OA09 Creation of Microstructered Polymers with Defined Micro And
Total Page:16
File Type:pdf, Size:1020Kb
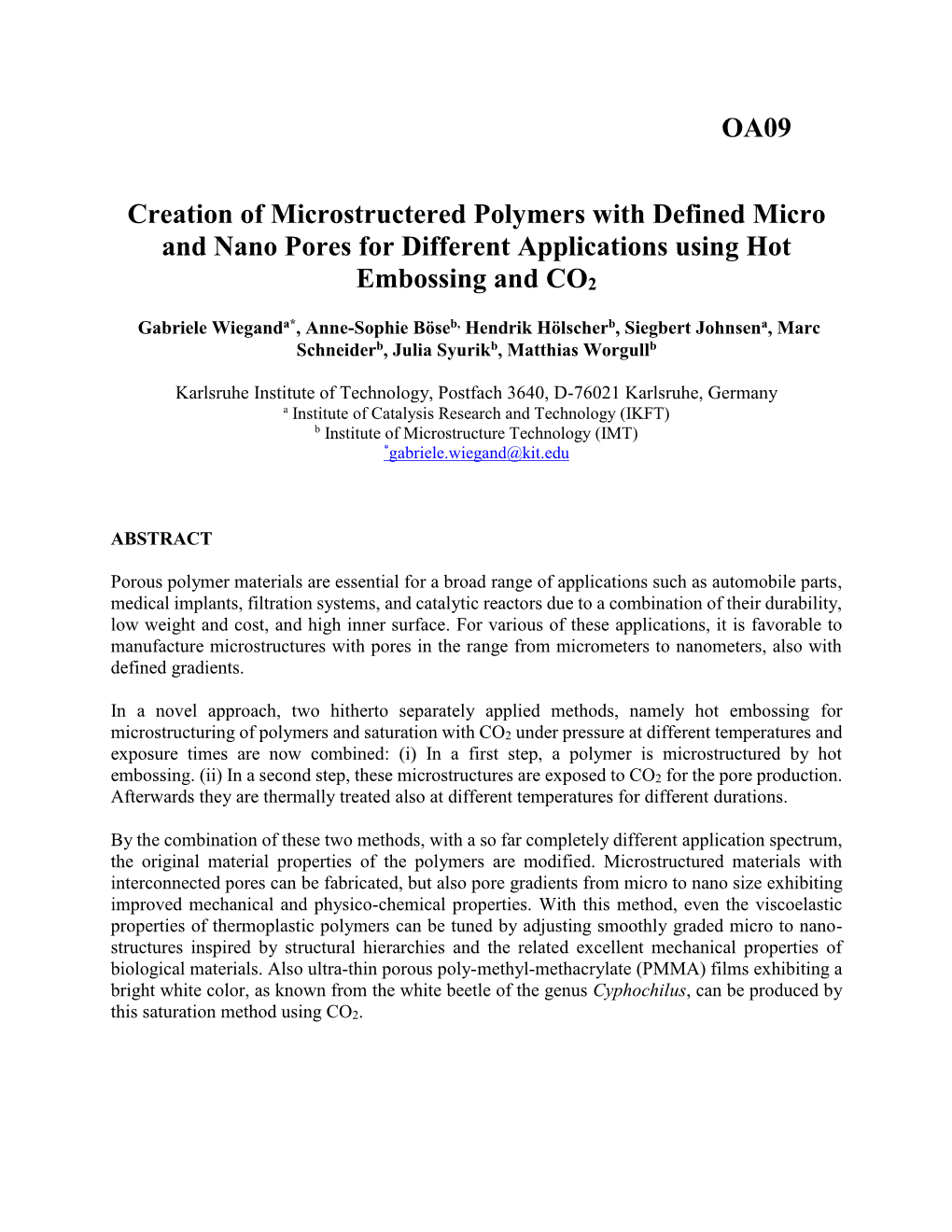
Load more
Recommended publications
-
Bright-White Beetle Scales Optimise Multiple Scattering of Light
OPEN Bright-White Beetle Scales Optimise SUBJECT AREAS: Multiple Scattering of Light OPTICAL PHYSICS Matteo Burresi1,2, Lorenzo Cortese1,3, Lorenzo Pattelli1,3, Mathias Kolle4, Peter Vukusic5, OPTICS AND PHOTONICS Diederik S. Wiersma1,3, Ullrich Steiner6 & Silvia Vignolini6,7 BIOLOGICAL PHYSICS BIOPHYSICS 1European Laboratory for Non-linear Spectroscopy (LENS), Universita` di Firenze, 50019 Sesto Fiorentino (FI), Italy, 2Istituto Nazionale di Ottica (CNR-INO), Largo Fermi 6, 50125 Firenze (FI), Italy, 3Universita` di Firenze, Dipartimento di Fisica e Astronomia, 50019 Sesto Fiorentino (FI), Italy, 4School of Engineering and Applied Sciences Harvard University 29 Oxford St., Received Cambridge, MA, 02138, USA and Department of Mechanical Engineering, Massachusetts Institute of Technology, 77 28 January 2014 Massachusetts Avenue, Cambridge, MA 02139, USA, 5Thin Film Photonics, School of Physics, Exeter University, Exeter EX4 4QL, UK, 6Cavendish Laboratory, Department of Physics, University of Cambridge, J. J. Thomson Avenue, Cambridge CB3 0HE, U.K, Accepted 7Department of Chemistry, University of Cambridge Lensfield Road, Cambridge CB2 1EW UK. 4 July 2014 Published Whiteness arises from diffuse and broadband reflection of light typically achieved through optical scattering 15 August 2014 in randomly structured media. In contrast to structural colour due to coherent scattering, white appearance generally requires a relatively thick system comprising randomly positioned high refractive-index scattering centres. Here, we show that the exceptionally bright white appearance of Cyphochilus and Lepidiota stigma Correspondence and beetles arises from a remarkably optimised anisotropy of intra-scale chitin networks, which act as a dense requests for materials scattering media. Using time-resolved measurements, we show that light propagating in the scales of the beetles undergoes pronounced multiple scattering that is associated with the lowest transport mean free should be addressed to path reported to date for low-refractive-index systems. -
An Introduction to Biomimetic Photonic Design
feaTureS biomimeTiC PHoToniC deSign An introduction to biomimetic photonic design I S.M. Luke and P. Vukusic - DOI: 10.1051/epn/2011302 I College of Engineering, Mathematics and Physical Sciences, University of Exeter, Stocker Road, Exeter EX4 4QL, UK. nature uses a large number of optical Highly saturated colours, such as those found on the phenomena to create a vast array of coloured blue wings of many Morpho butterflies, oen result appearances. The brightest colours and most from coherent scattering [1]. is arises when light is scattered from periodically-arranged discrete changes dazzling optical effects are often those which in refractive index. A strongly scattered reflection maxi - are created through the use of intricate mum arises at a given wavelength and therefore with a microstructures that manipulate light. distinctive colour. e colour depends on the periodi - Bio-inspired designs are increasingly city, the refractive indices of the materials and the leading to improvements in diverse arrays angles of illumination and observation. Multilayer structures that offer such periodicity are of products for which manipulation of common in nature. ey are oen found in brightly light and appearance is important. coloured beetle species such as the buprestid C hrysoch - roa raja (shown in figure 1) [2]. In this species a 1.5 µm layer on the wing casing surface contains alternating he natural world exhibits many examples of layers of two materials, each with a thickness of efficient design and specialised functionality. approximately 100 nm. e characteristic reflection Scientists have long sought inspiration from from this structure is the bright green colour seen at T the natural world; biomimetic design is res - normal incidence. -
Scarabaeidae, Melolonthinae, Melolonthini) with Consideratiton of Divisions of the Subtribe Melolonthina
Elytra, Tokyo, 38(2): 239ῌ247, November 13, 2010 Taxonomic Study on the Genus Psilopholis BG:CH@: (Scarabaeidae, Melolonthinae, Melolonthini) with Consideratiton of Divisions of the Subtribe Melolonthina Takeshi MATSUMOTO Nishi-miyahara 2ῌ6ῌ20ῌ102, Yodogawa-ku, Osaka, 532ῌ0004 Japan Abstract AnewspeciesofthegenusPsilopholis is described from the moun- tainous areas of Borneo, East Malaysia under the name of P. gigantea. Tricholepis vestita is synonymized with Psilopholis grandis,thetypespeciesofthisgenus.So-called generic characters of the genus Psilopholis are scrutinized. Division of the subtribe Melolonthina into two lineages by only the di#erence in the number of segments of the antennal club is not sustainable. The subtribe Melolonthina cannot be reasonably divided into the two lineages by any other morphological characters. Up to the present, the melolonthine genus Psilopholis has been monotypical, represented by the species, Psilopholis grandis alone, which has been known from the Malay Peninsula to Borneo via Java. In the course of my activities for collecting SE Asian melolonthines, I have accumulated a series of remarkably large specimens closely resembling the type species from Borneo. Lately, I searched for accounts that fit for these large specimens, but was unable to find any. I have noticed from these scrutinies that this species belongs to a new species. Therefore, I decided to describe it herein. Because neither BG:CH@: nor the succeeding researchers pointed out the generic characteristics in detail, I would like to describe them at this place. Furthermore, I will synonymize a S=6GE’s species with P. grandis. The subtribe Melolonthina has been divided into two lineages only by the di#erence in the number of segments of the antennal club by European and American researchers as in L¨D7A &SB:I6C6 (2006) without adequate discussions. -
Investigation of the Selective Color-Changing Mechanism
www.nature.com/scientificreports OPEN Investigation of the selective color‑changing mechanism of Dynastes tityus beetle (Coleoptera: Scarabaeidae) Jiyu Sun1, Wei Wu2, Limei Tian1*, Wei Li3, Fang Zhang3 & Yueming Wang4* Not only does the Dynastes tityus beetle display a reversible color change controlled by diferences in humidity, but also, the elytron scale can change color from yellow‑green to deep‑brown in specifed shapes. The results obtained by focused ion beam‑scanning electron microscopy (FIB‑SEM), show that the epicuticle (EPI) is a permeable layer, and the exocuticle (EXO) is a three‑dimensional photonic crystal. To investigate the mechanism of the reversible color change, experiments were conducted to determine the water contact angle, surface chemical composition, and optical refectance, and the refective spectrum was simulated. The water on the surface began to permeate into the elytron via the surface elemental composition and channels in the EPI. A structural unit (SU) in the EXO allows local color changes in varied shapes. The refectance of both yellow‑green and deep‑brown elytra increases as the incidence angle increases from 0° to 60°. The microstructure and changes in the refractive index are the main factors that infuence the process of reversible color change. According to the simulation, the lower refectance causing the color change to deep‑brown results from water infltration, which increases light absorption. Meanwhile, the waxy layer has no efect on the refection of light. This study lays the foundation to manufacture engineered photonic materials that undergo controllable changes in iridescent color. Te varied colors of nature have a great visual impact on human beings. -
Workshop on Supercritical Fluids and Energy
workshop on supercritical fl uids and energy ESTA OBRA FOI IMPRESSA EM PAPEL RECICLATO 75% PRÉ-CONSUMO, 25 % PÓS-CONSUMO, A PARTIR DE IMPRESSÕES E TIRAGENS SUSTENTÁVEIS. CUMPRIMOS NOSSO PAPEL NA EDUCAÇÃO E NA PRESERVAÇÃO DO MEIO AMBIENTE. workshop on supercritical fl uids and energy Dados Internacionais de Catalogação na Publicação (CIP) (Câmara Brasileira do Livro, SP, Brasil) Workshop em fluídos supercríticos e energia / M. Angela A. Meireles e Erdogan Kiran. (organizadores). – Campinas, SP : Mercado de Letras, 2013. – (Mercado de Letras Temas) ISBN 978-85-7591-301-7 1. Biocombustíveis 2. Energia – Fontes alternativas 3. Fluídos supercríticos I. Meireles, M. Angela A. II. Kiran, Erdogan III. Série. 13-12026 CDD-541.34 Índices para catálogo sistemático: 1. Fluídos supercríticos e energia 541.34 Capa e Projeto Gráfico: Vande Rotta Gomide Layout e Editoração: André S. Tavares da Silva Revisão: Gabriela Lopes Adami DIREITOS RESERVADOS PARA A LÍNGUA INGLESA: © MERCADO DE LETRAS EDIÇÕES E LIVRARIA LTDA. Rua João da Cruz e Souza, 53 Telefax: (19) 3241-7514 – CEP 13070-116 Campinas SP Brasil www.mercado-de-letras.com.br [email protected] 1a edição dezembro/2013 IMPRESSÃO DIGITAL IMPRESSO NO BRASIL Esta obra está protegida pela Lei 9610/98. É proibida sua reprodução parcial ou total sem a autorização prévia do Editor. O infrator estará sujeito às penalidades previstas na Lei. CONTENTS Preface. 7 Presentation . .13 Goals . 15 Committee . 17 OVERVIEW/PLENARy LECTURES ON ThE ROLE OF SUPERCRITICAL FLUIDS AND TEChNOLOGy (SCFs&T) State of SCFs&T — Future Directions and Progress in Commercialization. .19 SCFs&T for Bio-based Fuel processes . -
Evolutionary-Optimized Photonic Network Structure in White Beetle Wing Scales
Evolutionary-Optimized Photonic Network Structure in White Beetle Wing Scales Bodo D. Wilts#,∗, Xiaoyuan Sheng∗, Mirko Holler, Ana Diaz, Manuel Guizar-Sicairos, J¨orgRaabe, Robert Hoppe, Shu-Hao Liu, Richard Langford, Olimpia D. Onelli, Duyu Chen, Salvatore Torquato, Ullrich Steiner, Christian G. Schroer, Silvia Vignolini, and Alessandro Sepe# Whiteness arises from the random scattering of inci- of the diffusion approximation is limited, since sin- dent light from disordered structures.[1] Opaque white gle scattering elements are difficult to be identified.[7] materials have to contain a sufficiently large num- To fully understand the correlation between the struc- ber of scatterers and therefore usually require thicker, ture and (optical) properties of complex materials, the material-rich nanostructures than structural color aris- detailed real-space structure in combination with a ing from the coherent interference of light.[2,3] In na- suitable model unravels this relationship. In optics, ture, bright white appearance arises from the dense these include finite-element modeling (FEM) or finite- arrays of pterin pigments in pierid butterflies,[4] gua- difference time-domain (FDTD) techniques, which can nine crystals in spiders,[5] or leucophore cells in the be employed for materials with arbitrary structures.[11] [6] flexible skin of cuttlefish. A striking example of such Distortion-free three-dimensional imaging of biolog- whiteness is found in the chitinous networks of white ical tissue with sub-micrometer resolution in a large [7{9] beetles, -
Light Manipulation Principles in Biological Photonic Systems
© 2013 Science Wise Publishing & DOI 10.1515/nanoph-2013-0015 Nanophotonics 2013; 2(4): 289–307 Review article Tim Starkey* and Pete Vukusic Light manipulation principles in biological photonic systems Abstract: The science of light and colour manipulation wavelength-selective absorption of light by chromo- continues to generate interest across a range of disci- phores, the name given to colour-producing molecules plines, from mainstream biology, across multiple phys- [1]. If white light is incident upon a pigment, the resulting ics-based fields, to optical engineering. Furthermore, the scattered light will have some proportion of the light sub- study of light production and manipulation is of signifi- tracted from the incident spectrum. The molecular struc- cant value to a variety of industrial processes and com- ture of a pigment determines the wavelength band over mercial products. Among the several key methods by which it absorbs strongly. Pigmentary colour of a biologi- which colour is produced in the biological world, this cal species is usually synthesised by their physiological review sets out to describe, in some detail, the specifics processes, although some animals obtain these absorbing of the method involving photonics in animal and plant molecules through their diet [2]. Pigments that are synthe- systems; namely, the mechanism commonly referred to sised by many insects include melanins, pterins, ommo- as structural colour generation. Not only has this theme chromes, tetrapyrroles, papiliochromes and quinomes, been a very rapidly growing area of physics-based inter- while carotenoid and flavonoid pigments are generally est, but also it is increasingly clear that the biological obtained from their diet [2]. -
Las 4 Fuerzas Que Rigen El Universo – Jordi Pereyra
El mundo será un poco distinto cuando acabes de leer este prólogo. No mucho, por supuesto, ni siquiera te vas a dar cuenta, pero a tu alrededor habrán ocurrido una cantidad inimaginable de cosas que habrán cambiado un poco el aspecto de nuestro planeta. Millones de toneladas de agua se habrán evaporado a través de los 361.000.000 km2 de superficie oceánica, quedando suspendidas en el aire en forma de nubes. La erosión provocada por los ríos, el viento y las mareas moverá una cantidad aún más vertiginosa de material de un lado a otro y algunos volcanes añadirán nuevas rocas a la superficie en forma de lava. En el núcleo del Sol, miles de millones de toneladas de hidrógeno se habrán convertido en helio, proporcionándole a nuestra estrella la energía que necesita para brillar y permitir que, en la cara iluminada de la Tierra, los árboles y las plantas hayan crecido un poco más utilizando la fotosíntesis para fijar en su estructura el carbono contenido en la atmósfera. Y no sólo tus alrededores: tu propio cuerpo habrá cambiado. Los microorganismos que viven en tu sistema digestivo te ayudarán a descomponer parte de lo que has comido, tu corazón habrá estado llevando oxígeno y nutrientes a tus células a través del torrente sanguíneo y muchas de ellas habrán terminado de reproducirse mientras lees estas líneas, creando tejidos nuevos. Más aún: estos mismos procesos habrán ocurrido en el interior de cada uno de los 7.000 millones de habitantes del planeta, además de en los otros seres vivos que... ¡Vale, vale, lo he captado! ¡Ve al grano, por favor te lo pido! Perdona, voz cursiva, la emoción me había hecho entrar en bucle. -
UTAH PESTS Staff
UTAH PESTS News Utah Plant Pest Diagnostic Laboratory and USU Extension Vol. VIII, Fall 2014 First Report of Elm Seed Bug in Utah What’s Inside School IPM Workshops Bacterial Spot of Pepper Raspberry Horntail Research Summary Billbug Management Fruit/Vegetable Monitoring Report 2014 Update on Invasive Pests IPM in the News In July 2014, the UPPDL received multiple on elm fruits (samara) and young nymphs submissions of a small, brown and black emerge in mid-to-late May. The nymphs insect. We identified it, with confirmation progress through 5 growth stages before News Highlights from USDA APHIS, as elm seed bug becoming a winged adult. There can be (Arocatus melanocephalus), marking its first many overlapping life stages present during WELCOME TO NEW official appearance in the state. A native of the summer, but in Italy, the insects have one VEGETABLE IPM Europe, the elm seed bug was first identified generation per year. Invasions of buildings ASSOCIATE in the U.S. in Idaho in 2012 and then in have occurred anytime between late May Bonnie Oregon in 2013. While the Utah sample and late September and were seen to Bunn submissions came from Salt Lake County, I coincide with peak summer temperatures. recently also collected and identified this insect in joined the Cache County around the same time. It is Control of elm seed bug with insecticides Utah Pests possible that the elm seed bug is already may be difficult due to their mobile team to widely distributed along the Wasatch Front. behavior. Italian entomologists report that conduct outreach city governments attempted control with in vegeta- As a member of the family Lygaeidae, or etofenprox, pyrethrum, and rotenone, but ble integrated pest manage- the seed bugs, this insect feeds primarily on only etofenprox showed efficacy. -
Taxonomic Notes on the Genus Cyphochilus (Coleoptera: Scarabaeoidea: Melolonthinae) (Part 3) with Description of Three New Species from Indochina
Acta Soc. Zool. Bohem. 84: 51–65, 2020 ISSN 1211-376X Taxonomic notes on the genus Cyphochilus (Coleoptera: Scarabaeoidea: Melolonthinae) (part 3) with description of three new species from Indochina Guido Sabatinelli Muséum d’histoire naturelle, Case Postale 6434, CH–1211 Genève 6, Switzerland; e-mail: [email protected] Received 11 November 2020; accepted 30 October 2020 Published 28 December 2020 Abstract. Cyphochilus backy sp. nov., C. dongkinh sp. nov., and C. genevievae sp. nov. are described after the study of 795 specimens from Indochina. These species are largely distributed in Thailand, Laos, and Vietnam, marginally in southern China and Myanmar. They were confused until today with C. tonkinensis Brenske, 1903 for which the lectotype is designated. The parameres and distribution of the four species treated are illustrated. The use of Cyphochilus dongkinh sp. nov. as human food is documented in northern Laos. Key words. Systematics, taxonomy, lectotype designation, geographic distribution, China, Thailand, Laos, Vietnam, Myanmar, Arthropoda, Scarabaeidae, edible insects. INTRODUCTION The members of the genus Cyphochilus Waterhouse, 1867 are quite exceptional among Melo- lonthinae having relatively uniform external morphology in contrast with a much diversified morphology of paramera. This offers an extraordinary reading lens to easily identify of species and formulate hypothesis on interspecific relationships based on morphological affinities. The first use of paramera for the identification of a species was by Frey (1971) followed by Nomura (1977). Since 2000, I started gathering specimens of the genus Cyphochilus, documenting the types of all species described. Thus, 19 new species were described and the paramera of their sibling species illustrated (Sabatinelli 2020a, b). -
Volume 9 Numéro 18 Juin 2021 Revue De Faunistique
Faunitaxys Revue de Faunistique, Taxonomie et Systématique morphologique et moléculaire Volume 9 ISSN : 2269 - 6016 Juin 2021 Numéro 18 Dépôt légal : Juin 2021 Faunitaxys Revue de Faunistique, Taxonomie et Systématique morphologique et moléculaire ZooBank : http://zoobank.org/79A36B2E-F645-4F9A-AE2B-ED32CE6771CC Directeur de la publication, rédacteur, conception graphique et PAO : Lionel Delaunay Cette revue ne peut pas être vendue Elle est distribuée par échange aux institutions (version papier) et sur simple demande aux particuliers (format PDF) à l’adresse suivante : AFCFF (Association française de Cartographie de la Faune et de la Flore) 28, rue Voltaire, F- 42100 Saint Etienne E-mail : [email protected] Elle est disponible librement au téléchargement à partir du site : http ://faunitaxys.fr/ La parution de Faunitaxys est apériodique Faunitaxys est indexé dans / Faunitaxys is indexed in: - Zoological Record Articles and nomenclatural novelties are referenced by: - ZooBank (http://zoobank.org) Imprimée sur les presses de SPEED COPIE 6, rue Tréfilerie, F- 42100 Saint-Etienne Imprimé le 10 juin 2021 Faunitaxys, 9(18), 2021 : 1 – 8. 1 On the genus Cyphochilus Waterhouse, 1867 from Hainan Island, China (Coleoptera: Scarabaeidae: Melolonthinae) MING-ZHI ZHAO College of Plant Protection, South China Agricultural University, Guangzhou, 510642, P. R. China. - [email protected] - ZooBank : http://zoobank.org/4C58E8BF-E3AE-4246-BF20-DE92C6DBF1CE Keywords : Abstract. – The genus Cyphochilus Waterhouse, 1867 from Hainan Island of southern China Scarabaeoidea; hlai; is revised. Cyphochilus linpinchaoi sp. nov., C. qiujianyueae sp. nov., C. lixunae sp. nov., Melolonthinae; taxonomy; C. hainanensis sp. nov. and C. pseudopodicalis sp. nov. are described. The variability of Leucopholini; new species; Cyphochilus hlai Sabatinelli, 2021 is improved. -
Adma.202001215.Pdf
PROGRESS REPORT www.advmat.de Light Management with Natural Materials: From Whiteness to Transparency Gianni Jacucci, Lukas Schertel, Yating Zhang, Han Yang,* and Silvia Vignolini* for inhomogeneous materials, light trans- The possibility of structuring material at the nanoscale is essential to control port is a bulk phenomenon. Therefore, light–matter interactions and therefore fabricate next-generation paints and their appearance results from the interplay coatings. In this context, nature can serve not only as a source of inspiration between: 1) the single-scatterer proper- for the design of such novel optical structures, but also as a primary source ties as the scattering cross-section; 2) the ensemble properties as the filling frac- of materials. Here, some of the strategies used in nature to optimize light– tion (i.e., the volume percentage occupied matter interaction are reviewed and some of the recent progress in the by the scatterers), the average orienta- production of optical materials made solely of plant-derived building blocks is tion of the scatterers, and the structure highlighted. In nature, nano- to micrometer-sized structured materials made factor (i.e., the spatial organization of the [6,7] from biopolymers are at the origin of most of the light-transport effects. How scatterers). The appearance of a disordered mate- natural photonic systems manage light scattering and what can be learned rial (which is defined as system where from plants and animals to produce photonic materials from biopolymers the structure factor does not exhibit long- are discussed. Tuning the light-scattering properties via structural variations range order) is directly determined by the allows a wide range of appearances to be obtained, from whiteness to optical thickness (OT).