Rotorcraft Research at the NASA Vertical Motion Simulator
Total Page:16
File Type:pdf, Size:1020Kb
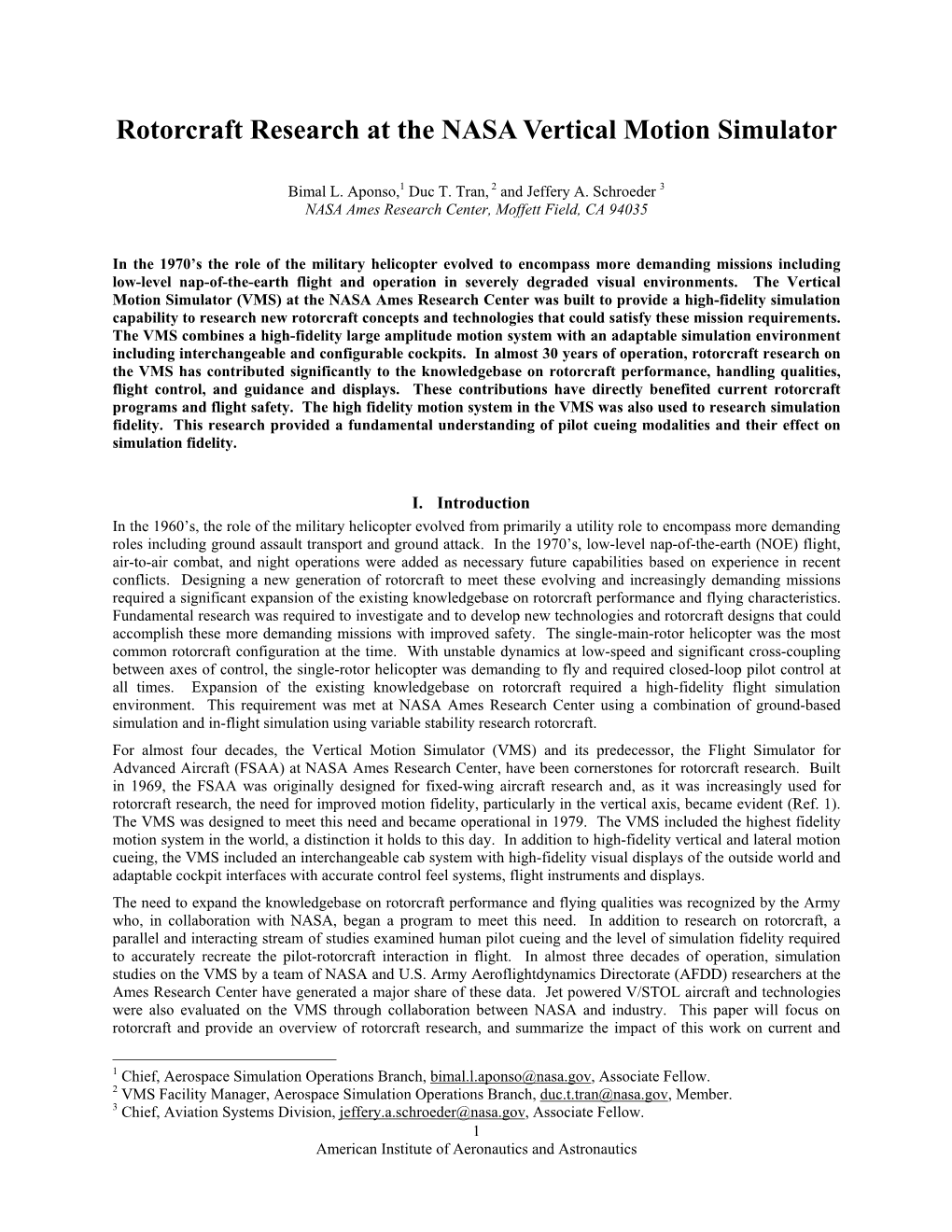
Load more
Recommended publications
-
1.1.3 Helicopters
Information on the Company’s Activities / 1.1 Presentation of the Company 1.1.3 Helicopters Airbus Helicopters is a global leader in the civil and military The HIL programme, for which the Airbus Helicopters’ H160 rotorcraft market, offering one of the most complete and modern was selected in 2017, was initially scheduled for launch range of helicopters and related services. This product range in 2022 by the current military budget law. Launching the currently includes light single-engine, light twin-engine, medium programme earlier will enable delivery of the fi rst H160Ms to and medium-heavy rotorcraft, which are adaptable to all kinds of the French Armed Forces to be advanced to 2026. The H160 mission types based on customer needs. See “— 1.1.1 Overview” was designed to be a modular helicopter, enabling its military for an introduction to Airbus Helicopters. version, with a single platform, to perform missions ranging from commando infi ltration to air intercept, fi re support, and anti-ship warfare in order to meet the needs of the army, the Strategy navy and the air force through the HIL programme. The new fi ve-bladed H145 is on track for EASA and FAA Business Ambition certifi cation in 2020. To ensure these certifi cations, two fi ve- bladed prototypes have clocked more than 400 fl ight hours Airbus Helicopters continues to execute its ambition to lead the in extensive fl ight test campaigns in Germany, France, Spain, helicopter market, build end-to-end solutions and grow new Finland, and in South America. First deliveries of the new H145 VTOL businesses, while being fi nancially sound. -
United Nations Peacekeeping Missions Military Aviation Unit Manual Second Edition April 2021
UN Military Aviation Unit Manual United Nations Peacekeeping Missions Military Aviation Unit Manual Second Edition April 2021 Second Edition 2019 DEPARTMENT OF PEACE OPERATIONS DEPARTMENT OF OPERATIONAL SUPPORT UN Military Aviation Unit Manual Produced by: Office of Military Affairs, Department of Peace Operations UN Secretariat One UN Plaza, New York, NY 10017 Tel. 917-367-2487 Approved by: Jean-Pierre Lacroix, Under-Secretary-General for Peace Operations Department of Peace Operations (DPO). Atul Khare Under-Secretary-General for Operational Support Department of Operational Support (DOS) April 2021. Contact: PDT/OMA/DPO Review date: 30/ 04 / 2026 Reference number: 2021.04 Printed at the UN, New York © UN 2021. This publication enjoys copyright under Protocol 2 of the Universal Copyright Convention. Nevertheless, governmental authorities or Member States may freely photocopy any part of this publication for exclusive use within their training institutes. However, no portion of this publication may be reproduced for sale or mass publication without the express consent, in writing, of the Office of Military Affairs, UN Department of Peace Operations. ii UN Military Aviation Unit Manual Foreword We are delighted to introduce the United Nations Peacekeeping Missions Military Aviation Unit Manual, an essential guide for commanders and staff deployed in peacekeeping operations, and an important reference for Member States and the staff at United Nations Headquarters. For several decades, United Nations peacekeeping has evolved significantly in its complexity. The spectrum of multi-dimensional UN peacekeeping operations includes challenging tasks such as restoring state authority, protecting civilians and disarming, demobilizing and reintegrating ex-combatants. In today’s context, peacekeeping missions are deploying into environments where they can expect to confront asymmetric threats and contend with armed groups over large swaths of territory. -
Global Military Helicopters 2015-16 Market Report Contents
GLOBAL MILITARY HELICOPTERS 2015-16 MARKET REPORT CONTENTS MARKET OVERVIEW 2 MILITARY HELICOPTER KEY REQUIREMENTS 4 EUROPE 5 NORTH AMERICA 10 LATIN AMERICA & THE CARIBBEAN 12 AFRICA 15 ASIA-PACIFIC 16 MIDDLE EAST 21 WORLD MILITARY HELICOPTER HOLDINGS 23 EUROPE 24 NORTH AMERICA 34 LATIN AMERICA & THE CARIBBEAN 36 AFRICA 43 ASIA-PACIFIC 49 MIDDLE EAST 59 EVENT INFORMATION 65 Please note that all information herein is subject to change. Defence IQ endeavours to ensure accuracy wherever possible, but errors are often unavoidable. We encourage readers to contact us if they note any need for amendments or updates. We accept no responsibility for the use or application of this information. We suggest that readers contact the specific government and military programme offices if seeking to confirm the reliability of any data. 1 MARKET OVERVIEW Broadly speaking, the global helicopter market is currently facing a two- pronged assault. The military helicopter segment has been impacted significantly by continued defense budgetary pressures across most traditional markets, and a recent slide in global crude oil prices has impacted the demand for new civil helicopters as well as the level of activity for existing fleets engaged in the offshore oil & gas exploration sector. This situation has impacted industry OEMs significantly, many of which had been working towards strengthening the civil helicopter segment to partially offset the impact of budgetary cuts on the military segment. However, the medium- to long-term view of the market is promising given the presence of strong fundamentals and persistent, sustainable growth drivers. The market for military helicopters in particular is set to cross a technological threshold in the form of next-generation compound helicopters and tilt rotorcraft. -
Development of Modern Control Laws for the AH-64D in Hover/Low Speed Flight
Development of Modern Control Laws for the AH-64D in Hover/Low Speed Flight Jeffrey W. Harding 1 Scott J. Moody Geoffrey J. Jeram 2 Aviation Engineering Directorate U.S. Army Aviation and Missile Research, Development, and Engineering Center Redstone Arsenal, Alabama M. Hossein Mansur 3 Mark B. Tischler Aeroflightdynamics Directorate U.S. Army Aviation and Missile Research, Development, and Engineering Center Moffet Field, California ABSTRACT Modern control laws are developed for the AH-64D Longbow Apache to provide improved handling qualities for hover and low speed flight in a degraded visual environment. The control laws use a model following approach to generate commands for the existing partial authority stability augmentation system (SAS) to provide both attitude command attitude hold and translational rate command response types based on the requirements in ADS-33E. Integrated analysis tools are used to support the design process including system identification of aircraft and actuator dynamics and optimization of design parameters based on military handling qualities and control system specifications. The purpose is to demonstrate the potential for improving the low speed handling qualities of existing Army helicopters with partial authority SAS actuators through flight control law modifications as an alternative to a full authority, fly-by-wire, control system upgrade. NOTATION INTRODUCTION ACAH attitude command attitude hold The AH-64 Apache was designed in the late 70’s and went DH direction hold into service as the US Army’s most advanced day, night DVE degraded visual environment and adverse weather attack helicopter in 1986. The flight HH height hold control system was designed to meet the relevant handling HQ handling qualities qualities requirements based on MIL-F-8501 (Ref. -
Assessment of Navy Heavy-Lift Aircraft Options
THE ARTS This PDF document was made available from www.rand.org as a public CHILD POLICY service of the RAND Corporation. CIVIL JUSTICE EDUCATION Jump down to document ENERGY AND ENVIRONMENT 6 HEALTH AND HEALTH CARE INTERNATIONAL AFFAIRS The RAND Corporation is a nonprofit research NATIONAL SECURITY POPULATION AND AGING organization providing objective analysis and effective PUBLIC SAFETY solutions that address the challenges facing the public SCIENCE AND TECHNOLOGY and private sectors around the world. SUBSTANCE ABUSE TERRORISM AND HOMELAND SECURITY TRANSPORTATION AND INFRASTRUCTURE Support RAND WORKFORCE AND WORKPLACE Purchase this document Browse Books & Publications Make a charitable contribution For More Information Visit RAND at www.rand.org Explore RAND National Defense Research Institute View document details Limited Electronic Distribution Rights This document and trademark(s) contained herein are protected by law as indicated in a notice appearing later in this work. This electronic representation of RAND intellectual property is provided for non- commercial use only. Permission is required from RAND to reproduce, or reuse in another form, any of our research documents for commercial use. This product is part of the RAND Corporation documented briefing series. RAND documented briefings are based on research briefed to a client, sponsor, or targeted au- dience and provide additional information on a specific topic. Although documented briefings have been peer reviewed, they are not expected to be comprehensive and may present preliminary findings. Assessment of Navy Heavy-Lift Aircraft Options John Gordon IV, Peter A. Wilson, Jon Grossman, Dan Deamon, Mark Edwards, Darryl Lenhardt, Dan Norton, William Sollfrey Prepared for the United States Navy Approved for public release; unlimited distribution The research described in this report was prepared for the United States Navy. -
Boeing's Mesa Site Is Humming with Apache Production—And That's Not
Boeing’s Mesa site is humming with Apache production—and that’s not all By Eric Fetters-Walp and photos by Bob Ferguson PHOTO: Boeing and U.S. Army aviators put two AH-64D Apache Longbow attack helicopters through their paces over the Arizona desert. NOVEMBER 2011 BOEING FRONTIERS / COVER STORY 21 byMesa the numbers 1 ranking of Boeing Mesa’s business among all Arizona manufacturers 382 acres (155 hectares) comprising the Mesa site 576 number of Boeing suppliers or vendors in Arizona 1982 year Mesa site was established by Hughes Helicopters 4,500 approximate number of employees 8,300 hours volunteered by employees in 2010 he hot desert air above Mesa, making a growing array of components Ariz., frequently pulses with the for multiple Boeing aircraft. 1,900,000 T sound of Apache attack helicop- “We’ve gone from producing Block II ters as the intimidating machines are put Apaches two years ago to having three dollars given by Boeing Mesa and through their paces after emerging from and soon four production lines here today,” employees in charitable contributions the Boeing production line. first of the next-generation Apache Block III said Dave Koopersmith, Boeing Military during 2010 It’s a sound that’s become familiar over production models this fall. The U.S. Army Aircraft’s vice president of Attack Helicopter the nearly 30 years that the Mesa site has plans to order nearly 700 newly built or Programs and Mesa senior site executive, built Apaches for the U.S. Army and a remanufactured Block III helicopters, which referring to the two Apache production 2,000,000 growing number of international customers. -
Over Thirty Years After the Wright Brothers
ver thirty years after the Wright Brothers absolutely right in terms of a so-called “pure” helicop- attained powered, heavier-than-air, fixed-wing ter. However, the quest for speed in rotary-wing flight Oflight in the United States, Germany astounded drove designers to consider another option: the com- the world in 1936 with demonstrations of the vertical pound helicopter. flight capabilities of the side-by-side rotor Focke Fw 61, The definition of a “compound helicopter” is open to which eclipsed all previous attempts at controlled verti- debate (see sidebar). Although many contend that aug- cal flight. However, even its overall performance was mented forward propulsion is all that is necessary to modest, particularly with regards to forward speed. Even place a helicopter in the “compound” category, others after Igor Sikorsky perfected the now-classic configura- insist that it need only possess some form of augment- tion of a large single main rotor and a smaller anti- ed lift, or that it must have both. Focusing on what torque tail rotor a few years later, speed was still limited could be called “propulsive compounds,” the following in comparison to that of the helicopter’s fixed-wing pages provide a broad overview of the different helicop- brethren. Although Sikorsky’s basic design withstood ters that have been flown over the years with some sort the test of time and became the dominant helicopter of auxiliary propulsion unit: one or more propellers or configuration worldwide (approximately 95% today), jet engines. This survey also gives a brief look at the all helicopters currently in service suffer from one pri- ways in which different manufacturers have chosen to mary limitation: the inability to achieve forward speeds approach the problem of increased forward speed while much greater than 200 kt (230 mph). -
Naval Postgraduate School Thesis
NAVAL POSTGRADUATE SCHOOL MONTEREY, CALIFORNIA THESIS A STUDY OF THE RUSSIAN ACQUISITION OF THE FRENCH MISTRAL AMPHIBIOUS ASSAULT WARSHIPS by Patrick Thomas Baker June 2011 Thesis Advisor: Mikhail Tsypkin Second Reader: Douglas Porch Approved for public release; distribution is unlimited THIS PAGE INTENTIONALLY LEFT BLANK REPORT DOCUMENTATION PAGE Form Approved OMB No. 0704-0188 Public reporting burden for this collection of information is estimated to average 1 hour per response, including the time for reviewing instruction, searching existing data sources, gathering and maintaining the data needed, and completing and reviewing the collection of information. Send comments regarding this burden estimate or any other aspect of this collection of information, including suggestions for reducing this burden, to Washington headquarters Services, Directorate for Information Operations and Reports, 1215 Jefferson Davis Highway, Suite 1204, Arlington, VA 22202-4302, and to the Office of Management and Budget, Paperwork Reduction Project (0704-0188) Washington DC 20503. 1. AGENCY USE ONLY (Leave blank) 2. REPORT DATE 3. REPORT TYPE AND DATES COVERED June 2011 Master‘s Thesis 4. TITLE AND SUBTITLE 5. FUNDING NUMBERS A Study of the Russian Acquisition of the French Mistral Amphibious Assault Warships 6. AUTHOR(S) Patrick Thomas Baker 7. PERFORMING ORGANIZATION NAME(S) AND ADDRESS(ES) 8. PERFORMING ORGANIZATION Naval Postgraduate School REPORT NUMBER Monterey, CA 93943-5000 9. SPONSORING /MONITORING AGENCY NAME(S) AND ADDRESS(ES) 10. SPONSORING/MONITORING N/A AGENCY REPORT NUMBER 11. SUPPLEMENTARY NOTES The views expressed in this thesis are those of the author and do not reflect the official policy or position of the Department of Defense or the U.S. -
Aircraft Collection
A, AIR & SPA ID SE CE MU REP SEU INT M AIRCRAFT COLLECTION From the Avenger torpedo bomber, a stalwart from Intrepid’s World War II service, to the A-12, the spy plane from the Cold War, this collection reflects some of the GREATEST ACHIEVEMENTS IN MILITARY AVIATION. Photo: Liam Marshall TABLE OF CONTENTS Bombers / Attack Fighters Multirole Helicopters Reconnaissance / Surveillance Trainers OV-101 Enterprise Concorde Aircraft Restoration Hangar Photo: Liam Marshall BOMBERS/ATTACK The basic mission of the aircraft carrier is to project the U.S. Navy’s military strength far beyond our shores. These warships are primarily deployed to deter aggression and protect American strategic interests. Should deterrence fail, the carrier’s bombers and attack aircraft engage in vital operations to support other forces. The collection includes the 1940-designed Grumman TBM Avenger of World War II. Also on display is the Douglas A-1 Skyraider, a true workhorse of the 1950s and ‘60s, as well as the Douglas A-4 Skyhawk and Grumman A-6 Intruder, stalwarts of the Vietnam War. Photo: Collection of the Intrepid Sea, Air & Space Museum GRUMMAN / EASTERNGRUMMAN AIRCRAFT AVENGER TBM-3E GRUMMAN/EASTERN AIRCRAFT TBM-3E AVENGER TORPEDO BOMBER First flown in 1941 and introduced operationally in June 1942, the Avenger became the U.S. Navy’s standard torpedo bomber throughout World War II, with more than 9,836 constructed. Originally built as the TBF by Grumman Aircraft Engineering Corporation, they were affectionately nicknamed “Turkeys” for their somewhat ungainly appearance. Bomber Torpedo In 1943 Grumman was tasked to build the F6F Hellcat fighter for the Navy. -
Military Use Handbook
National Interagency Fire Center Military Use Handbook 2021 This publication was produced by the National Interagency Coordination Center (NICC), located at the National Interagency Fire Center (NIFC), Boise, Idaho. This publication is also available on the Internet at http://www.nifc.gov/nicc/logistics/references.htm. MILITARY USE HANDBOOK 2021 INTRODUCTION ................................................................................................. ………………… ..................................................................................................................................................... CHAPTER 10 – GENERAL ........................................................................................................ 1 10.1 Purpose ............................................................................................................... 1 10.2 Overview .............................................................................................................. 1 10.3 Ordering Requirements and Procedures .............................................................. 1 10.4 Authorities/Responsibilities .................................................................................. 2 10.5 Billing Procedures ................................................................................................ 3 CHAPTER 20 – RESOURCE ORDERING PROCEDURES FOR MILITARY ASSETS ............... 4 20.1 Ordering Process ................................................................................................. 4 20.2 Demobilization -
The Rotating Wing Aircraft Meetings of 1938 and 1939 Were the First
The Rotating Wing Aircraft Meetings of 1938 and 1939 This advertisement showing Pitcairn’s 1932 Tandem landing at an were the first national conferences on rotorcraft. They marked estate was typical of their strategy to market to the wealthy. “If yours a transition from a technological focus on the Autogiro to the is such an estate or if you will select a neighboring field, a Pitcairn representative will gladly demonstrate the complete practicality of helicopter. In addition, these important meetings helped to this modern American scene.” With the Great Depression wearing lay the groundwork for the founding of the American Heli- on, however, the Autogiro business was moribund by the late 1930s. copter Society. – Ed. he Rotating Wing Aircraft Meeting of October 28 This was a significant gathering for the future of – 29, 1938 at the Franklin Institute in Philadel- rotary wing flight in America, coming at a time when T phia, PA, sponsored by the Philadelphia Chapter the Autogiro movement was moribund and helicopter of the Institute of the Aeronautical Sciences (IAS, the development was just about to receive a boost with forerunner of the American Institute of Aeronautics and commencement of the just-passed Dorsey-Logan Bill. Astronautics, or AIAA), was an historic gathering of And, perhaps of greater importance, those attending – those involved, committed to and researching Autogiro, including many of the leading developers of rotary wing convertiplane and helicopter flight. It was, as described flight – were actively speculating as to the future that in the preface to the conference proceedings, “the first rotary wing flight might take. -
Current Health Trends in U.S. Military Helicopter and Tiltrotor Pilots: a Triservice Epidemiological Study
Current Health Trends in U.S. Military Helicopter and Tiltrotor Pilots: A Triservice Epidemiological Study John S. Crowley MD MPH US Army Aeromedical Research Laboratory Angelia Cost PhD William Dodson MD MPH Dustin Huber PhD Armed Forces USAF School of Aerospace Medicine Naval Medical Research Unit Health Surveillance Branch Dayton Disclaimers Disclaimer The opinions, interpretations, conclusions, and recommendations are those of the presenter and are not necessarily endorsed by the U.S. Army and/or the U.S. Department of Defense. Citation of trade names in this presentation does not constitute an official Department of the Army endorsement or approval of the use of such commercial items. The authors have no conflicts of interest to declare. 2 Helicopters are different… “Like all novices we began with the helicopter but soon saw it had no future and dropped it. The helicopter does, with great labor, only what the balloon does without labor…The helicopter is much easier to design than an airplane, but it is worthless when done.” -Wilbur Wright 3 …Helicopter pilots are different too… Helicopter pilots are complicated… The stress of being first… » Helicopter pilots were the first to » Hover » Fly with NVGs » Use the aircraft HMD as primary flight display …Along with all the unique & common stresses of helicopter flight: » Disorientation » Vibration » Head supported mass » Altitude » Hypoxia » G forces » Posture » Fatigue » Workload » Technology 2017 Congressional Tasking SEC. 750. STUDY ON HEALTH OF HELICOPTER AND TILTROTOR PILOTS. (a) STUDY REQUIRED.—The Secretary of Defense shall carry out a study of career helicopter and tiltrotor pilots to assess potential links between the operation of helicopter and tiltrotor aircraft and acute and chronic medical conditions experienced by such pilots.