Red Bull Air Racer
Total Page:16
File Type:pdf, Size:1020Kb
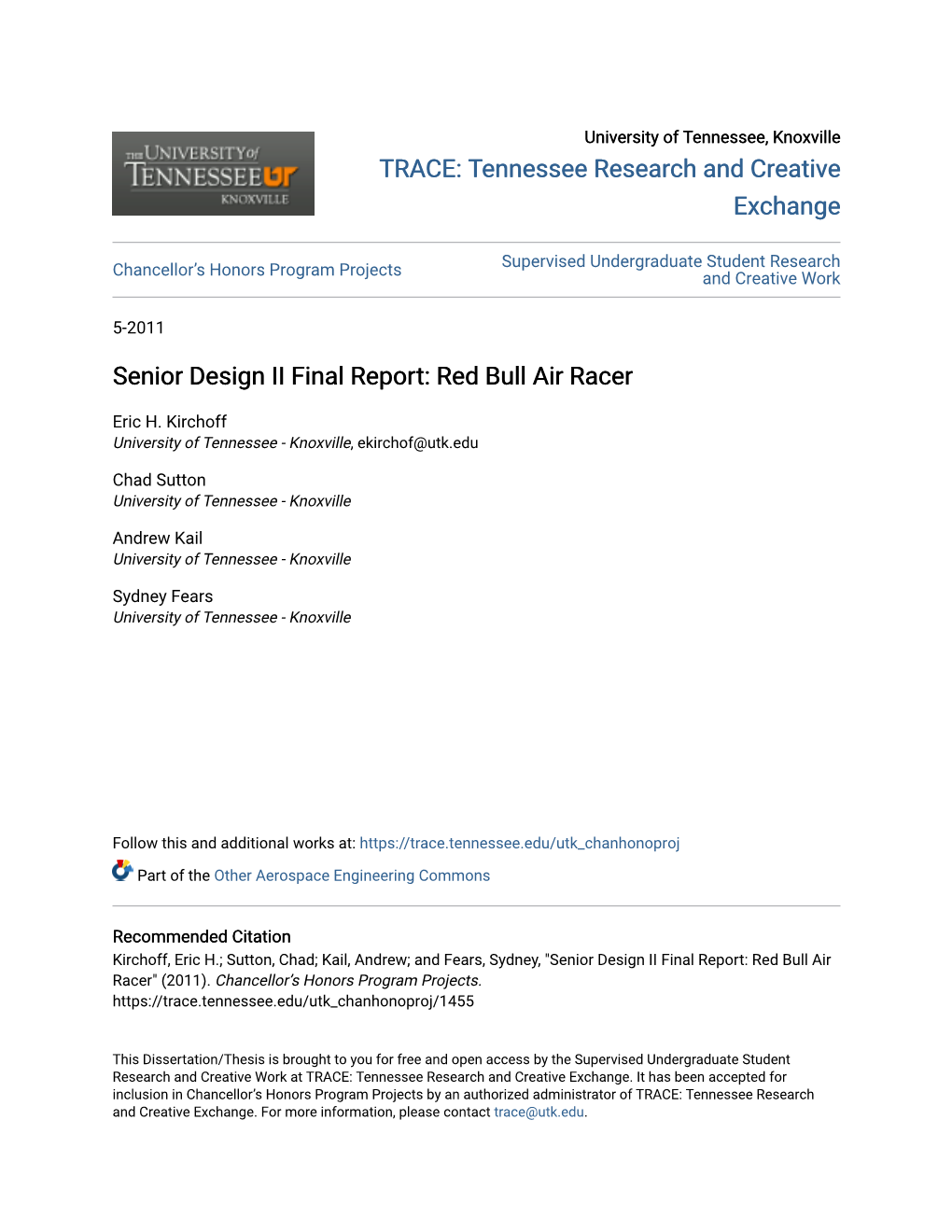
Load more
Recommended publications
-
A Numerical Approach for Implementing Air Intakes in a Canard Type Aircraft for Engine Cooling Purposes
https://doi.org/10.1590/jatm.v13.1192 ORIGINAL PAPER A Numerical Approach for Implementing Air Intakes in a Canard Type Aircraft for Engine Cooling Purposes Odenir de Almeida1,* , Pedro Correa Souza1 , Erick Cunha2 1.Universidade Federal de Uberlândia – Faculdade de Engenharia Mecânica – Centro de Pesquisa em Aerodinâmica Experimental – Uberlândia/MG – Brazil. 2.Fábrica Brasileira de Aeronaves – Uberlândia/MG – Brazil *Corresponding author: [email protected] ABSTRACT This work presents selected results of an unconventional aircraft development campaign. Engine installation at the rear part of the fuselage imposed design constraints for air intakes that should be used for cooling purposes. Trial and error flight tests increased the development cost and time which required a more sophisticated analysis through computational fluid dynamics (CFD) techniques and robust semiempirical approach. The carried-out investigation of the air intakes started with an empirical approach from guidelines for designing NACA and scoops. Numerical studies via computational fluid dynamics were performed with the air intakes installed in the aircraft fuselage. An analysis based on the air intake efficiency, drag and the effect of angle of attack are detailed in this work. Different air intakes designs, such as scoops of different shapes, were evaluated seeking for improved air intake efficiency and low drag while providing enough air for cooling the engine compartment. The results showed that the numerical approach used herein decreased the development cost and time of the aircraft, providing a reasonable low-cost approach and leading to a design selection more easily. Based on the current approach the canard airplane geometry was changed to account for the new selected air intake for engine cooling purposes. -
Orientation Sheet for Horizon Updated: 2017-Apr-21
Orientation Sheet for Horizon Updated: 2017-Apr-21 General • All voyages should be documented in the ship’s log book. Report any damage or deficiencies to [email protected] and to boat manager [email protected] / 410-203-2673 Specifications Registration #: MD 5596 AC Hull#: XLY 595267 Make: Islander 36 Year: 1977 Engine: Perkins 4.108; 4-cyl Diesel 48-HP Displacement: 13,450 lbs Draft: 5’ 02” Mast Height Fuel Capacity: 30 gal. Holding tank: 18 gal. (from waterline): 52’ 06” Water Capacity: 54 gal. 2 tanks, below Salon Settees LOA: 36’ 08" Batteries: House battery 1 and 2 (Starboard lazaret) LWL: 28’ 25” Starting Battery (under companionway steps) Beam: 11’ 17” Sails: Main, Genoa on furler, staysail with boom Safety Equipment First Aid Kit: Drawer port side Rescue Sling: Stern Rail PFDs: V-berth Fire Extinguishers: (2) – Starboard side cabin, Port quater berth Day/Night Flares: Aerial & Hand-held – Drawer port side above seats in salon Sounds (Horn, Bell & Whistle): Drawer port side above seats in salon Auto-Switched Bilge Pump: Wired directly to House Battery (must be switched to Auto when leaving boat). The switch is located on the starboard side inside the cabin above the galley sink Old Bilge Pump: Wired to Electric Panel on the engine compartment wall (manual mode only). Do not use this pump unless the other one is not working. Manual Bilge Pump: Cockpit Port side (handle located in drawer port side above seats) Anchors: Danforth (35 lbs) bow; Rode: 15’ of chain & 150’ of line (marked every 30’) Thru-hulls/Sea-cocks: Engine -
Gannet Electronics
Gannet Electronics A Summary of the Electronic Equipment Fitted to early Model R.A.N Gannet A.S.1 Aircraft Prepared by David Mowat Ex-L.R.E.M.(A) 21st. August 2003 Page 1 Page 2 GANNET ELECTRONIC EQUIPMENT Introduction The ‘Heart’ of the Gannet as a Weapons System was its Electronic Equipment. It contained a comprehensive range of electronic equipment to enable it to perform the various roles for which it was designed. Its Primary Role was to detect, locate, and destroy enemy submarines. For this Role, the Aircraft was fitted with a Search Radar and Sonobuoy Systems. Other electronic systems were also installed for Communications, both internal and external, and Navigation. The various equipments were allocated an ‘Aircraft Radio Installation’ (ARI) number, which specified the actual equipment used in each installation. These may vary between aircraft depending on the role that the particular aircraft was to perform. A cross- reference List of ARI’s is shown at Appendix ‘A’. The various equipments can be grouped into four major categories as follows: a.! Communications b.! Navigation c.! Warfare Systems d.! Stores Communications Equipment The Communications Equipment was used to enable the crew to talk to each other (internal communications) and other aircraft, ships or bases (external communications). They are as follows: a.! Audio Amplifier Type A1961 The Type A1921 was used to amplify the Microphone outputs from the three crew members and feed it back into the earphones. It was located on the port side of the rear cockpit at about seat height just forward of the Radio Operator. -
19750827-0 DC-3 5Y-AAF.Pdf
1 CAV/ACC/24/75 ACCIDENT IUVESTIGATION BRANCH CIVIL AIRCRAFT ACCIDEiiT Report on the Accident to Douglas DC-3 Aircraft Registration number 5Y-AAF which occurred on the 27th August,1975 At 0922 hours, at Mtwara Airport, Tanzania. E A S T A F R I CAN C 0 M M U NIT Y AOCIDEwr REPORT AOCIDE:~T INVESTIGATIOn BRAl'WH 'CIVIL ACCIDENT REPORT CAV/ACC/24/75 AIRCRAFT TYPE 8; HEGISTRATION: Douglas DC-::- 5Y-l~ ENGINE: Pratt & \filii tney R1830-90D REGISTERED OWlIJ]~R & OPERATOR: East African Airways Corporation, P.O. Box 19002, NAIROBI, Kenya. CREVf: CAPTAIN Gabriel Sebastian Turuka ) ) Uninjured FIJ:1ST OFFICER Steven Robert Wegoye ) PASSENGER: Sixteen - Uninjured. PLACE OF ACCIDEHT: ~,1twara Airport, Tanzania. DATE AND T1MB: 27th August, 1975, 0922 hours. ALL rrU'lES IN THIS REPORT ARE G.1VI. T. SUMMARY The aircraft was operating East African Airways Service flight number EC037 from Dar es Salaam to Nachingmea with an unscheduled refuelling stop at I1twara with 3 crew and 16 passengers on board. The flight from Dar es Salaam was uneventful and an approach and landing was made onto runway 19. After touch down the aircraft swung to the left and then to the right, after which it left the runway where both main landing gear assys collapsed causing substantial daLage to the centre section and nacelle structure. The report concludes that the most probable cause of the accident was the failure of the pilot to initiate corrective action to prevent the aircraft from turning off the runway. 1.1 HISTORY OF THE FLIGHT: The aircraft departed Dar es Salaam with three crew and 16 passengers. -
Vistara Soars Toward Expansion New Flight-Planning Technology Enhances Safety, Cuts Costs
MOBILITY ENGINEERINGTM AUTOMOTIVE, AEROSPACE, OFF-HIGHWAY A quarterly publication of and Vistara soars toward expansion New flight-planning technology enhances safety, cuts costs Base-engine value engineering Deriving optimum efficiency, performance Autos & The Internet of Things How the IoT is disrupting the auto industry Software’s expanding role Escalating software volumes shifting design, systems integration Volume 3, Issue 2 June 2016 ME Molex Ad 0616.qxp_Mobility FP 4/28/16 5:00 PM Page 1 Support Tomorrow’s Speeds with Proven Connectivity Simply Solved In Automotive, consumer demand is changing even faster than technology. When you collaborate with Molex, we can develop a complete solution that will support tomorrow’s data speeds, backed by proven performance. Together, we can simplify your design and manufacturing processes — while minimizing space and maximizing connectivity throughout the vehicle. www.molex.com/a/connectedvehicle/in CONTENTS Features 40 Base-engine value engineering 49 Agility training for cars for higher fuel efficiency and AUTOMOTIVE CHASSIS enhanced performance Chassis component suppliers refine vehicle dynamics at AUTOMOTIVE POWERTRAIN the high end and entry level with four-wheel steering and adaptive damping. Continuous improvement in existing engines can be efficiently achieved with a value engineering approach. The integration of product development with value 52 Evaluating thermal design of engineering ensures the achievement of specified targets construction vehicles in a systematic manner and within a defined timeframe. OFF-HIGHWAY SIMULATION CFD simulation is used to evaluate two critical areas that 43 Integrated system engineering address challenging thermal issues: electronic control units for valvetrain design and and hot-air recirculation. development of a high-speed diesel engine AUTOMOTIVE POWERTRAIN The lead time for engine development has reduced significantly with the advent of advanced simulation Cover techniques. -
Drivetrain 17 36 30 30 31 32 32 33 35 37 38 39 39 40 40 41 41 41 41 41 40 36-40
B Drivetrain ............................... 18 to 41 Drivetrain Struts Main .............................................................................18-19 Self-aligning gland type (with space) ................................. 30 Intermediate ...................................................................... 18 Heavy duty ..................................................................... 30 Sailboat ............................................................................. 19 Studs .................................................................................. 31 Port and starboard ............................................................ 20 Tournament (with space) ................................................ 32 Vee .................................................................................... 21 Self-aligning gland type (without space) ............................ 32 Universal ........................................................................... 21 Spud type Adjustable ....................................................................22-23 Tournament water cooled ............................................... 33 Cut off type ..................................................................... 22 Right hand thread ........................................................... 35 Swivel type ..................................................................... 23 Shaft logs..........................................................................36-40 Strut bolts ............................................................................. -
United States Patent (19) 11) Patent Number: 4,691,879 Greene 45) Date of Patent: Sep
United States Patent (19) 11) Patent Number: 4,691,879 Greene 45) Date of Patent: Sep. 8, 1987 54 JET AIRPLANE gravity. Full control of the airplane is possible under 76 Inventor: Vibert F. Greene, 19400 Sorenson high maneuverability conditions, extremely high accel Ave., Cupertino, Calif. 95014 erations and at large angles of attack. The delta nose wing creates swirling vortices that contribute substan 21 Appl. No.: 875,024 tially to the lift of the nose section. The winglet, an 22). Filed: Jun. 16, 1986 extension of the delta nose wing, allows the turbulent wake from the leading edge of the delta nose wing to 51 Int. Cl." .............................................. B64C39/08 flow over its upper surface to create additional lift while 52 U.S.C. .................................... 244/45 R; 24.4/13; the midspan wing causes the turbulent flow over its 244/45 A; 244/15 upper surface to form a turbulent wake at its leading 58 Field of Search .................. 244/45 R, 45 A, 4 R, edge. The V-tail delta wing with a V-shaped underside 244/15, 13 and blunt leading edge gives additional lift and control (56) References Cited to the airplane. A flow regulator helps to direct and U.S. PATENT DOCUMENTS control the flow field to the underside of the delta nose D. 138,538 8/1944 Clerc .................................. D12/331 wing and nose strake. There are eight pairs of control D. 155,569 10/1949 Bailey ............ ... D12/331 surfaces including an upper body stabilizer system for 3,447,76 6/1969 Whitener et al. ..................... 244/5 the control and stability of the airplane. -
The Design and Development of a Human-Powered
THE DESIGN AND DEVELOPMENT OF A HUMAN-POWERED AIRPLANE A THESIS Presented to the Faculty of the Graduate Division "by James Marion McAvoy^ Jr. In Partial Fulfillment of the Requirements for the Degree Master of Science in Aerospace Engineering Georgia Institute of Technology June _, 1963 A/ :o TEE DESIGN AND DETERMENT OF A HUMAN-POWERED AIRPLANE Approved: Pate Approved "by Chairman: M(Ly Z7. /q£3 In presenting the dissertation as a partial fulfillment of the requirements for an advanced degree from the Georgia Institute of Technology, I agree that the Library of the Institution shall make it available for inspection and circulation in accordance with its regulations governing materials of this type. I agree that permission to copy from, or to publish from, this dissertation may he granted by the professor under whose direction it was written, or, in his absence, by the dean of the Graduate Division when such copying or publication is solely for scholarly purposes and does not involve potential financial gain. It is under stood that any copying from, or publication of, this disser tation which involves potential financial gain will not be allowed without written permission. i "J-lW* 11 ACKNOWLEDGMENTS The author wishes to express his most sincere appreciation to Pro fessor John J, Harper for acting as thesis advisor, and for his ready ad vice at all times. Thanks are due also to Doctor Rohin B. Gray and Doctor Thomas W. Jackson for serving on the reading committee and for their help and ad vice . Gratitude is also extended to,all those people who aided in the construction of the MPA and to those who provided moral and physical sup port for the project. -
Water-Tunnel and Analytical Investigation of the Effect of Strake
https://ntrs.nasa.gov/search.jsp?R=19800019803 2020-03-21T17:02:56+00:00Z NASA TP " 1676 NASA Technical Paper 1676 ,.,I c. 1 Water-Tunneland Analytical Investigation of the Effect of Strake Design Variables on Strake VortexBreakdown. Characteristics Neal T. Frink and John E. Lamar AUGUST 1980 TECH LIBRARY KAFB, NM NASA Technical Paper 1676 Water-Tunnel andAnalytical Investigation of the Effect of Strake Design Variables on Strake VortexBreakdown Characteristics Neal T. Frink andJohn E. Lamar Lavzgley Research Cetzter Haznptorz, Virgivzia National Aeronautics and Space Administration Scientific and Technical Information Branch 1980 SUMMARY A systematic water tunnel study was made to determine the vortex breakdown characteristics of43 strakes, more than half of which were generated from a new analytical strake design method. The strakes were mountedon a l/2-scale model of a Langley Research Center general research fighter fuselage mode1 with a 44O leading-edge-sweep trapezoidal wing. This study develops, in conjunction with a common wing-body, a parametric set of strake data for use in establishing and verifying a new strake design procedure. To develop this parametric data base, several series of isolated strakes were designedon the basis of a simplified approach which relates pre- scribed suction and pressure distributions in a simplified flow field to plan- form shapes. The resulting planform shapes provided examples of the effects of the pri- mary design parameters of size, span, and slenderness on the vortex breakdown characteristics. These effects are analyzed in relation to the respective strake leading-edge suction distributions. Included are examples of the effects of detailed strake planform shaping for strakes with the same general size and slenderness. -
Bureau of Air Safety Investigation Report Basi
BUREAU OF AIR SAFETY INVESTIGATION REPORT BASI Report B/916/1017 Bell 214ST Helicopter VH-HOQ Timor Sea Latitude 12° 30' south Longitude 124° 25' east 22 November 1991 Bureau of Air Safety Investigation /i.:V Transport and Healonaf Development Department of Transport and Communications Bureau of Air Safety Investigation ACCIDENT INVESTIGATION REPORT B/916/1017 Bell 214ST Helicopter VH-HOQ Timor Sea Latitude 12° 30' south Longitude 124° 25' east 22 November 1991 Released by the Director of the Bureau of Air Safety Investigation under the provisions of Air Navigation Regulation 283 Bureau of Air Safety Investigation When the Bureau makes recommendations as a result of its investigations or research, safety, (in accordance with our charter), is our primary consideration. However, the Bureau fully recognises that the implementation of recommendations arising from its investigations will in some cases incur a cost to the industry. Consequently, the Bureau always attempts to ensure that common sense applies whenever recommendations are formulated. BASI does not have the resources to carry out a full cost- benefit analysis of every recommendation. The cost of any recommendation must always be balanced against its benefits to safety, and aviation safety involves the whole community. Such analysis is a matter for the CAA and the industry. ISBN 0642 193959 June 1993 This report was produced by the Bureau of Air Safety Investigation (BASI), PO Box 967, Civic Square ACT 2608. The Director of the Bureau authorised the investigation and the publication of this report pursuant to his delegated powers conferred by Air Navigation Regulations 278 and 283 respectively. -
Design Study of Technology Requirements for High Performance Single-Propeller- Driven Business Airplanes
3 1176 01346 2362 ! NASA Contractor Report 3863 NASA-CR-386319850007383 Design Study of Technology Requirements for High Performance Single-Propeller- Driven Business Airplanes David L. Kohlman and James Hammer CONTRACT NAS1-16363 JANUARY 1985 N/ A NASA Contractor Report 3863 Design Study of Technology Requirements for High Performance Single-Propeller- Driven Business Airplanes David L. Kohlman and James Hammer Flight Research Laboratory University of Kansas Center for Research, Inc. Lawrence, Kansas Prepared for Langley Research Center under Contract NAS1-16363 N/ A National Aeronautics and Space Administration Scientific and Technical InformationBranch 1985 TABLE OF CONTENTS Page i. INTRODUCTION .............................................. 1 2. NOMENCLATURE .............................................. 5 3. BASELINE CONFIGURATION ANALYSIS ........................... 7 3.1 Description of Baseline Configuration ................ 7 3.2 Effect of Aspect Ratio ............................... ii 3.3 Effect of Wing Loading ............................... 12 3.4 Effect of Wing Natural Laminar Flow .................. 15 3.5 Effect of Fuselage Drag .............................. 19 4. PROPULSION SYSTEM ANALYSIS ................................. 31 4.1 GATE Engine ........................................... 32 4.1.1 Description of Engine .......................... 32 4.1.2 GASP Engine Routine ............................ 33 4.2 Very Advanced Reciprocating Engine (Spark Ignited), (SIR) ............................... 36 4.3 Very Advanced Diesel -
WO 2015/012935 A2 29 January 2015 (29.01.2015) P O P C T
(12) INTERNATIONAL APPLICATION PUBLISHED UNDER THE PATENT COOPERATION TREATY (PCT) (19) World Intellectual Property Organization International Bureau (10) International Publication Number (43) International Publication Date WO 2015/012935 A2 29 January 2015 (29.01.2015) P O P C T (51) International Patent Classification: Bart Dean [US/US]; 2691 Daunet Ave., Simi Valley, Cali B64C 27/26 (2006.01) B64C 27/54 (2006.01) fornia 93065 (US). PARKS, William Martin [US/US]; B64C 5/02 (2006.01) B64C 39/02 (2006.01) 2805 North Woodrow Ave., Simi Valley, California 93065 B64C 9/00 (2006.01) G05D 1/08 (2006.01) (US). GANZER, David Wayne [US/US]; 4607 Kleberg B64C 25/00 (2006.01) B64C 29/00 (2006.01) St., Simi Valley, California 93063 (US). FISHER, Chris¬ topher Eugene [US/US]; 4 1 Los Vientos Dr., Thousand (21) International Application Number: Oaks, California 91320 (US). MUKHERJEE, Jason Sid- PCT/US20 14/036863 harthadev [US/US]; 605 Muirfield Ave., Simi Valley, (22) International Filing Date: California 93065 (US). KING, Joseph Frederick 5 May 2014 (05.05.2014) [US/US]; 10540 Gaviota Ave., Granada Hills, California 91344 (US). (25) Filing Language: English (74) Agent: DAWSON, James K.; 1445 E. Los Angeles Ave., English (26) Publication Language: Suite 108, Simi Valley, California 93065-2827 (US). (30) Priority Data: (81) Designated States (unless otherwise indicated, for every 3 May 2013 (03.05.2013) 61/819,487 US kind of national protection available): AE, AG, AL, AM, (71) Applicant: AEROVIRONMENT, INC. [US/US]; 181 W . AO, AT, AU, AZ, BA, BB, BG, BH, BN, BR, BW, BY, Huntington Drive, Suite 202, Monrovia, California 91016 BZ, CA, CH, CL, CN, CO, CR, CU, CZ, DE, DK, DM, (US).