Approaches for Modelling the Physical Behavior of Technical Systems on the Example of Wind Turbines
Total Page:16
File Type:pdf, Size:1020Kb
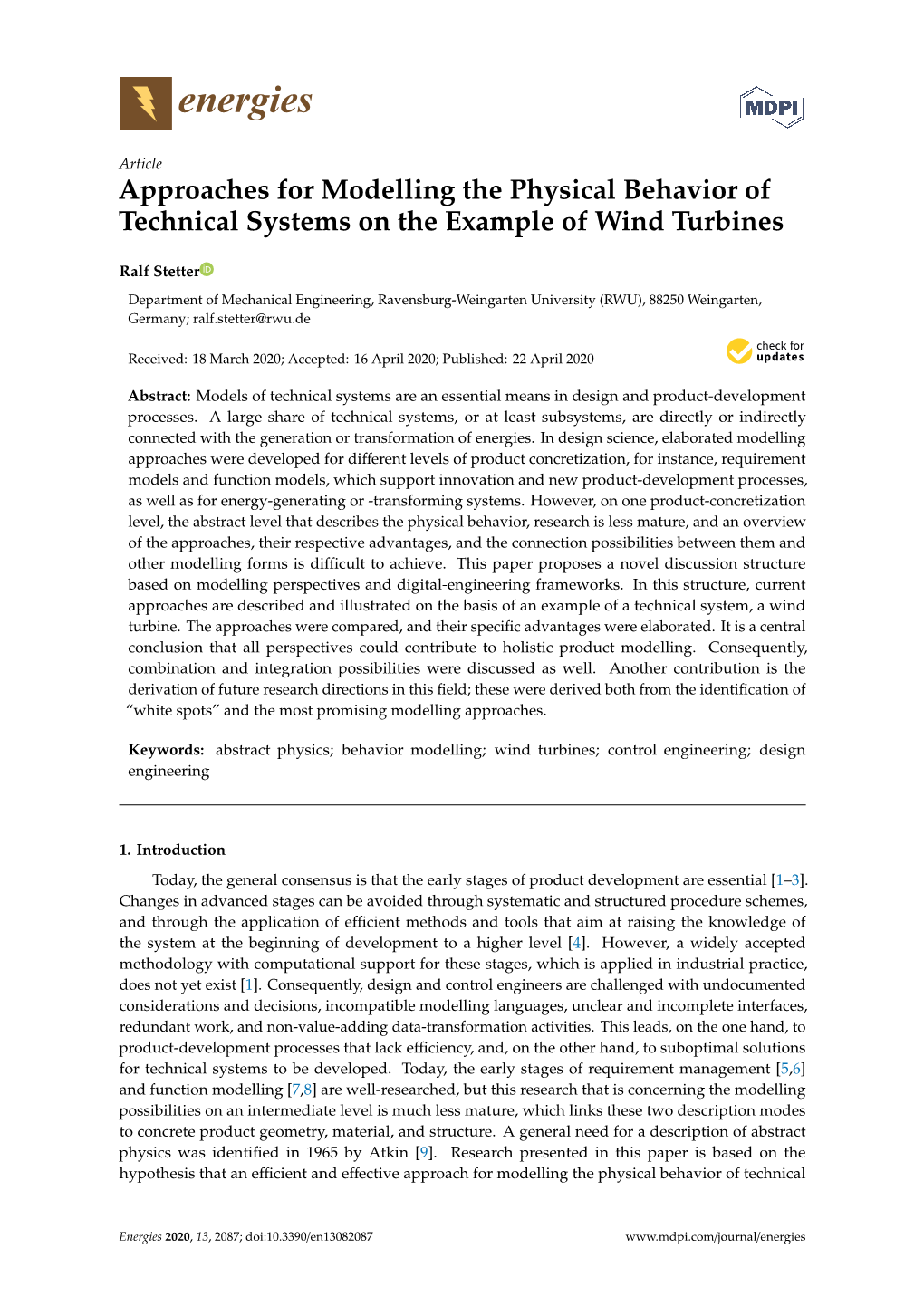
Load more
Recommended publications
-
ESI's Simulationx
by ESI‘s SimulationX Courses and Contents SimulationX is a registered trademark of ESI ITI GmbH Dresden. © ESI ITI GmbH, Dresden, Germany, 2019. All rights reserved. Doc. Vers. 08/2019 Preface Dear Sir or Madam, with the continuous development of SimulationX we provide you with the necessary resources for a targeted and sustain- able work in the field of system simulation. You will learn the efficient use of the software and its innovations in group and individual training courses at ESI or directly at your site. The highly practical nature of our courses and the professional Your personal contact: expertise of our tutors guarantee a quick and successful learn- ing process. We look forward to passing on our knowledge and would be happy to discuss new solutions with you. Antje Richter T + 49 (0) 351 260 50 - 120 With best regards on behalf of the ESI team, F + 49 (0) 351 260 50 - 155 [email protected] Antje Richter, Content 1 ESI ITI Academy 1.1 Introduction 07 1.2 Course Overview 08 1.3 Conditions of Participation 09 1.4 Registration 10 2 Introduction to SimulationX 2.1 Fundamentals 11 2.2 Advanced Modeling 12 2.3 Methods for Calculation and Analyses 13 3 Physical Domains 3.1 Mechanics (1D) 14 3.2 Planar Mechanics 15 3.3 Multi-Body Systems 16 3.4 Hydraulics 17 3.5 Thermal 18 3.6 Pneumatics 19 3.7 Acoustics (1D) 20 3.8 Electronics, Electromagnetics, Electromechanics 21 3.9 Electrical Power & Communications Analysis (1D) 22 3.10 Control Engineering 23 Content 4 Applications 4.1 Drive Systems 24 4.1 Drive Systems 25 4.2 Hybrid -
Simulationx를 이용한 기계, 유체, 전기 통합 시스템 모델링 및 해석 Simulationx, Multi-Domain Simulation and Modeling Tool for the Design, Analysis, and Optimization of Complex Systems
기술해설 SimulationX를 이용한 기계, 유체, 전기 통합 시스템 모델링 및 해석 SimulationX, Multi-domain Simulation and Modeling tool for the Design, Analysis, and Optimization of Complex systems 윤영환, 장주섭 Y. H. Yoon and J. S. Jang 1. 서 론 SimulationX의 사용상 장점은 다음과 같다. 1) 각기 다른 분야의 엔지니어들이 각자의 방식대 컴퓨터의 성능 발달로 인하여 이것을 활용한 시 로 부품이나 시스템을 모델링 할 수 있고, 이를 뮬레이션의 활용도가 높아지고 있고, 그 결과 복잡 서로 공유함으로써 복합적인 시스템 전체의 해 한 시스템을 실제 시스템처럼 모사가 가능하다. 이 석을 가능하게 하여 Multi-Domain Simulation 러한 CAE(Computer Aided Engineering) 기술 활 S/W라고 한다. 용은 비용 절감 및 개발 기간의 단축이라는 점에서 2) 상호 작용 및 피드백을 포함하는 다양한 도메 매우 중요하며, 현재 많은 제품 개발에 해석 기술이 인 부품들의 상호 작용을 모델링 할 수 있다. 활용되고 있다.1-4) 3) 시스템 개발에 있어서 공통적인 모델링 및 해 SimulationX는 독일의 드레스덴(Dresden)에 본사 석 환경을 이용함으로써 모든 관계자들 간 상 를 두고 있는 ITI GmbH에서 개발한 Multi-Domain 호 이해의 기반을 다질 수 있다. 시뮬레이션 프로그램으로서, 어떤 시스템을 구성하 4) 시제품(prototype) 제작 및 테스트 기간을 단축 고 있는 부품들의 상호 작용을 해석하고 평가할 수 하고 개발 비용을 절감할 수 있다. 있는 대표적인 소프트웨어(Software, S/W)이다. 5) 실제로 측정이 어렵거나 불가능한 모델에 대한 SimulationX를 가장 많이 시용하는 업체로는 유 관찰이 가능하여 시스템 전반에 대한 이해도를 럽의 BMW, Benz와 같은 자동차산업의 선두그룹으 높여 준다. 로 독일 자동차 회사들이 왜 세계 최고의 제품을 SimulationX의 조작 화면(GUI)은 그림 1과 같이 만드는지 알 수 있을 정도로 잘 만들어진 S/W이다. 왼쪽의 각종 물리적인 모델을 포함하고 있는 라이 SimulationX는 이미 라이브러리 화 되어있는 기 브러리, 오른쪽 위에 이러한 모델들을 배치하고 서 계(1D mechanics, 3D multi-body systems), 유압 로 연결하여 시스템 전체의 회로도를 작성하는 (Hydraulics), 공압(Pneumatics), 제어(Controls), 전 Model view외 각 모델의 물리적 특성 파라미터의 기, 전자(Electric, Electronics), 자장(Magnetics), 파 표시 및 조정, 해석과 관련된 사항을 조정하는 워트레인(Power transmission 1D, 3D), 전기 기계 Model explorer로 구성되어 있다. -
Modelling and Control Methods with Applications to Mechanical Waves
Digital Comprehensive Summaries of Uppsala Dissertations from the Faculty of Science and Technology 1174 Modelling and Control Methods with Applications to Mechanical Waves HANS NORLANDER ACTA UNIVERSITATIS UPSALIENSIS ISSN 1651-6214 ISBN 978-91-554-9023-2 UPPSALA urn:nbn:se:uu:diva-229793 2014 Dissertation presented at Uppsala University to be publicly examined in room 2446, ITC, Lägerhyddsvägen 2, Uppsala, Friday, 17 October 2014 at 10:15 for the degree of Doctor of Philosophy. The examination will be conducted in English. Faculty examiner: Prof. Jonas Sjöberg (Chalmers). Abstract Norlander, H. 2014. Modelling and Control Methods with Applications to Mechanical Waves. Digital Comprehensive Summaries of Uppsala Dissertations from the Faculty of Science and Technology 1174. 72 pp. Uppsala: Acta Universitatis Upsaliensis. ISBN 978-91-554-9023-2. Models, modelling and control design play important parts in automatic control. The contributions in this thesis concern topics in all three of these concepts. The poles are of fundamental importance when analyzing the behaviour of a system, and pole placement is an intuitive and natural approach for control design. A novel parameterization for state feedback gains for pole placement in the linear multiple input case is presented and analyzed. It is shown that when the open and closed loop poles are disjunct, every state feedback gain can be parameterized. Other properties are also investigated. Hammerstein models have a static non-linearity on the input. A method for exact compensation of such non-linearities, combined with introduction of integral action, is presented. Instead of inversion of the non-linearity the method utilizes differentiation, which in many cases is simpler. -
Design Analysis Method for Multidisciplinary Complex Product Using Sysml
MATEC Web of Conferences 139, 00014 (2017) DOI: 10.1051/matecconf/201713900014 ICMITE 2017 Design Analysis Method for Multidisciplinary Complex Product using SysML Jihong Liu1,*, Shude Wang1, and Chao Fu1 1 School of Mechanical Engineering and Automation, Beihang University, 100191 Beijing, China Abstract. In the design of multidisciplinary complex products, model-based systems engineering methods are widely used. However, the methodologies only contain only modeling order and simple analysis steps, and lack integrated design analysis methods supporting the whole process. In order to solve the problem, a conceptual design analysis method with integrating modern design methods has been proposed. First, based on the requirement analysis of the quantization matrix, the user’s needs are quantitatively evaluated and translated to system requirements. Then, by the function decomposition of the function knowledge base, the total function is semi-automatically decomposed into the predefined atomic function. The function is matched into predefined structure through the behaviour layer using function-structure mapping based on the interface matching. Finally based on design structure matrix (DSM), the structure reorganization is completed. The process of analysis is implemented with SysML, and illustrated through an aircraft air conditioning system for the system validation. 1 Introduction decomposition and function modeling, function structure mapping and evaluation, and structure reorganization. In the process of complex product design, system The whole process of the analysis method is aimed at engineering is a kind of development methods which providing designers with an effective analysis of ideas covers a wide range of applications across from system and theoretical support to reduce the bad design and requirements analysis, function decomposition to improve design efficiency. -
Understanding the Rational Function Model: Methods and Applications
UNDERSTANDING THE RATIONAL FUNCTION MODEL: METHODS AND APPLICATIONS Yong Hu, Vincent Tao, Arie Croitoru GeoICT Lab, York University, 4700 Keele Street, Toronto M3J 1P3 - {yhu, tao, ariec}@yorku.ca KEY WORDS: Photogrammetry, Remote Sensing, Sensor Model, High-resolution, Satellite Imagery ABSTRACT: The physical and generalized sensor models are two widely used imaging geometry models in the photogrammetry and remote sensing. Utilizing the rational function model (RFM) to replace physical sensor models in photogrammetric mapping is becoming a standard way for economical and fast mapping from high-resolution images. The RFM is accepted for imagery exploitation since high accuracies have been achieved in all stages of the photogrammetric process just as performed by rigorous sensor models. Thus it is likely to become a passkey in complex sensor modeling. Nowadays, commercial off-the-shelf (COTS) digital photogrammetric workstations have incorporated the RFM and related techniques. Following the increasing number of RFM related publications in recent years, this paper reviews the methods and key applications reported mainly over the past five years, and summarizes the essential progresses and address the future research directions in this field. These methods include the RFM solution, the terrain- independent and terrain-dependent computational scenarios, the direct and indirect RFM refinement methods, the photogrammetric exploitation techniques, and photogrammetric interoperability for cross sensor/platform imagery integration. Finally, several open questions regarding some aspects worth of further study are addressed. 1. INTRODUCTION commercial companies, such as Space Imaging (the first high- resolution satellite imagery vendor), to adopt the RFM scheme A sensor model describes the geometric relationship between in order to deliver the imaging geometry model has also the object space and the image space, or vice visa. -
Efficient Software Tools in the Renewable Energy Domain: Maple and Maplesim
EnviroInfo 2013: Environmental Informatics and Renewable Energies Copyright 2013 Shaker Verlag, Aachen, ISBN: 978-3-8440-1676-5 Efficient software tools in the renewable energy domain: Maple and MapleSim Ji ří H řebí ček 1, Jaroslav Urbánek 1,2 Abstract There are presented efficient software tools Maple and MapleSim for solving technical problems in the renewable energy domain using mathematics-based modelling. MapleSim represents the simulation environment, which has a graphical interface for interconnecting system components. The system models are then processed by the Maple (symbolic computation system) mathematics engine, and finally the differential-algebraic equations describing the solved systems are simulated numerically to produce and 2-D, 3-D visualise output results. Maple allows users to quickly focus and reliably solve problems with easy access to over 5000 algorithms and functions developed over 30 years of cutting-edge research and development. In the paper there are presented two solved problems in the renewa- ble energy domain, which are freely downloadable from the web of the Canadian company Maplesoft developing above software tools. 1. Introduction The Canadian company Maplesoft 3 has developed simple and friendly used software tools Maple® 4 and MapleSim® 5 which reduce the cost and effort of developing high-fidelity models of power generation and energy storage systems, including gas and steam turbine generator sets; wind, wave, and solar energy sys- tems and batteries. Maple information technology has been trusted as a cutting edge mathematical and technical tool for over 30 years. In that time, millions of users from around the world have used and relied on the power of Maple for their research, testing, analysis, design, teaching, and schoolwork (Gander/Hřebí ček 2004), (Lynch 2009), (Borwein/Skerritt 2011), (Fox 2011), (Hřebí ček et al 2011), (Hřebí ček 2012). -
Reliability Block Diagram (Rbd)
RELIABILITY BLOCK DIAGRAM (RBD) 1. System performance 2. RBD definition 3. Structure function Master ISMP Master ISMP - Castanier 4. Reliability function of a non repairable complex system 5. Reliability metrics for a repairable complex system 59 System performance Problem: Individual definition of the failure modes and components What about the global performance of the « system »? Master ISMP Master ISMP - Castanier 60 Reliability Block Diagram definition Definition A Reliability Block Diagram is a success-oriented graph which illustrates from a logical perspective how the different functional blocks ensure the global mission/function of the system. The structure of the reliability block diagram is mathematically described through structure functions which allow to assess some reliability measures of the (complex) Master ISMP Master ISMP - Castanier system. Function model EThe valve can be closed S and stop the flow SDV1 61 Reliability Block Diagram definition Decomposition of a complex system in functional blocks Component 1 8 9 4 4 2 7 8 10 Master ISMP Master ISMP - Castanier 5 6 3 9 10 Functional block 1 62 Reliability Block Diagram definition The classical architectures « Serie » structure A system which is operating if and only of all of its components are operating is called a serie structure/system. « Parallel » structure A system which is operating if at least one of its components is Master ISMP Master ISMP - Castanier operating is called a parallel structure/system. « oo » structure A system which is operating if at least of its component are operating is called a over structure/system 63 Reliability Block Diagram definition Example Let consider 2 independent safety-related valves V1 and V2 which are physically installed in series. -
A Model-Driven Data-Analysis Architecture Enabling Reuse and Insight in Open Data
A model-driven data-analysis architecture enabling reuse and insight in open data Robin Hoogervorst July 2018 Master's Thesis Master of Computer Science Specialization Software Technology University of Twente Faculty of Electrical Engineering, Mathematics and Computer Science Supervising committee: dr. Luis Ferreira Pires dr.ir. Maurice van Keulen prof.dr.ir. Arend Rensink Abstract The last years have shown an increase in publicly available data, named open data. Organisations can use open data to enhance data analysis, but tradi- tional data solutions are not suitable for data sources not controlled by the organisation. Hence, each external source needs a specific solution to solve accessing its data, interpreting it and provide possibilities verification. Lack of proper standards and tooling prohibits generalization of these solutions. Structuring metadata allows structure and semantics of these datasets to be described. When this structure is properly designed, these metadata can be used to specify queries in an abstract manner, and translated these to dataset its storage platform. This work uses Model-Driven Engineering to design a metamodel able to represent the structure different open data sets as metadata. In addition, a function metamodel is designed and used to define operations in terms of these metadata. Transformations are defined using these functions to generate executable code, able to execute the required data operations. Other transformations apply the same operations to the metadata model, allowing parallel transformation of metadata and data, keeping them synchronized. The definition of these metamodels, as well as their transformations are used to develop a prototype application framework able to load external datasets and apply operations to the data and metadata simultaneously. -
S C H U L U N G S K a T a L O G 2 0
SCHULUNGSKATALOG 2021 ENGINEERING SYSTEM INTERNATIONAL GMBH www.esi-group.com DIVE INTO THE WORLD OF ZERO TESTS, ZERO PROTOTYPES, ZERO DOWNTIME Seit der Gründung im Jahre 1973 hat ESI die Vision, reale und praxisnahe Konstruk- tionsprobleme verschiedener Industriezweige zu lösen. Diese Simulationslösungen, die auf der Materialphysik basieren, erzielten 1985 eine Weltpremiere: Zum ersten Mal wurde ein virtueller Crash-Test für Volkswagen durchgeführt, der den Weg für den umfangreichen Einsatz virtueller Lösungen in Entwicklungsprozessen eb- nete und neue Sicherheitsstandards etablierte. Ein neues Paradigma, die Outcome Economy Die zunehmende Komplexität stellt alle Branchen vor Herausforderungen. Die Herstel- ler stehen vor vielen neuen Aufgaben, um die Bedürfnisse der Kunden in Hinblick auf Qualität, Zuverlässigkeit, Sicherheit und pünktlicher Lieferung zu erfüllen. Die Outcome Economy erschwert die Erfüllung der wichtigen Leistungsindikatoren, da der Erfolg an der Leistung und nicht am Produkt selbst gemessen wird. Die Industrien müssen Wach- stum erzielen bei gleichzeitiger Aufrechterhaltung der Innovation. Daher entschei- den sie sich für eine digitale Transformation, die sie zu Initiativen ohne nachgewiesene Ergebnisse führen könnte. Courtesy of Volkswagen AG 2 Transformations-Reise Die von der ESI Group angebotenen Lösungen – das Ergebnis aus 45 Jahren Erfahrung – bringen die technologische Kompetenz mit, sich effizient und zuversichtlich zu entwickeln. Als Kernstück des ESI-Geschäftsmodells ermöglicht Virtual Proto- typing seinen globalen Kunden die Herstellung, Montage und das Verhalten ih- rer Produkte in verschiedenen Umgebungen zu validieren und so ihre Kos- ten und die Markteinführungszeit zu minimieren, ohne Abstriche bei Sicher- heit und Qualität zu machen. Um diese Ziele zu erreichen, begleitet ESI seine Kunden auf dem Weg hin zu Zero Tests, Zero Prototypes und Zero Downtime. -
Integration Definition for Function Modeling (IDEF0)
NIST U.S. DEPARTMENT OF COMMERCE PUBLICATIONS £ Technology Administration National Institute of Standards and Technology FIPS PUB 183 FEDERAL INFORMATION PROCESSING STANDARDS PUBLICATION INTEGRATION DEFINITION FOR FUNCTION MODELING (IDEFO) » Category: Software Standard SUBCATEGORY: MODELING TECHNIQUES 1993 December 21 183 PUB FIPS JK- 45C .AS A3 //I S3 IS 93 FIPS PUB 183 FEDERAL INFORMATION PROCESSING STANDARDS PUBLICATION INTEGRATION DEFINITION FOR FUNCTION MODELING (IDEFO) Category: Software Standard Subcategory: Modeling Techniques Computer Systems Laboratory National Institute of Standards and Technology Gaithersburg, MD 20899 Issued December 21, 1993 U.S. Department of Commerce Ronald H. Brown, Secretary Technology Administration Mary L. Good, Under Secretary for Technology National Institute of Standards and Technology Arati Prabhakar, Director Foreword The Federal Information Processing Standards Publication Series of the National Institute of Standards and Technology (NIST) is the official publication relating to standards and guidelines adopted and promulgated under the provisions of Section 111 (d) of the Federal Property and Administrative Services Act of 1949 as amended by the Computer Security Act of 1987, Public Law 100-235. These mandates have given the Secretary of Commerce and NIST important responsibilities for improving the utilization and management of computer and related telecommunications systems in the Federal Government. The NIST, through its Computer Systems Laboratory, provides leadership, technical guidance, -
Hosted by Indian Institute of Science, Bangalore
Hosted by Indian Institute of Science, Bangalore 29 November 2018 30 November 2018 Modelica Tutorials – Beginners and 1st Modelica Users’ Meet – India Intermediate level with Hands on (MUMI 2018) Venue Class Room – 222, ICER, IISc, Bangalore Register here https://tinyurl.com/isadigitaltwins Silver Sponsor Bronze Sponsor About Modelica A non-proprietary, object-oriented, equation based language to conveniently model complex multi- domain systems used by many Industries for Modeling and Simulation Control Edge Designer MIKE from OpenModelica from from Bosch Rexroth DHI OSMC SimulationX from ESI ITI Technologies GmbH, Dresden, Germany. Simcenter Amesim from Siemens PLM Software SystemModeler from Wolfram Research, Sweden CATIA Systems Engineering Dymola from Dassault from Dassault Systèmes Systèmes Altair Activate from Altair OPTIMICA Compiler solidThinking Toolkit from Modelon AB ABB OPTIMAX PowerFit Twin Builder MapleSim from JModelica from from ABB Group from ANSYS Waterloo Maple Modelon with academia Application Tool Modelica Tutorial Modelica Users’ Meet India, 2018 Keynote: Dr Peter Fritzson Presenters from Professor and Research Director of the Programming Altair India Private Limited Environment Laboratory at Linköping University BMSCE Bangalore Director of the Open Source Modelica Consortium Dymola Director of the MODPROD center for model-based IISc Bangalore product development IIT Bombay Vice chairman of the Modelica Association ModeliCon InfoTech LLP Modelon Engineering Private Limited Tutorial Agenda SASTRA Deemed University -
NI Tools for Automated Testing
Agenda ▪ Introduction to NI ▪ Real-Time Test ▪ NI Solutions for Real-Time Test ▪ SW ▪ HW ▪ Standardizing the signal path ▪ SLSC ▪ ASAM XIL Mission Statement NI equips engineers and scientists with systems that accelerate productivity, innovation, and discovery. ni.com ONE-PLATFORM APPROACH NI SERVICES AND SUPPORT THIRD-PARTY SOFTWARE THIRD-PARTY HARDWARE WEB SERVICES NI PRODUCTIVE ARDUINO PYTHON DEVELOPMENT SOFTWARE ETHERNET C USB The MathWorks, Inc. MATLAB® GPIB .NET SERIAL VHDL NI MODULAR HARDWARE LXI/VXI AND MORE AND MORE MATLAB® is a registered trademark of The MathWorks, Inc. ONE PLATFORM APPROACH NI SERVICES AND SUPPORT Community THIRD PARTY HARDWARE Support 300,000+ Online Members 700+ Field Engineers 450+ User Groups NI PRODUCTIVE 700+ Support Engineers 9,000+ Code Examples DEVELOPMENT SOFTWARE 50+ Worldwide Offices NI ECOSYSTEM Academic Add-Ons 8,000+ Universities Worldwide 400+ Software Add-Ons 5M+ Tools Network Downloads NI ECOSYSTEM Partners NI MODULAR HARDWARE Open Connectivity 1,000+ Alliance Partners THIRD PARTY SOFTWARE 10,000+ Instrument and Device Drivers Industry-Leading Technology Partners 1,000+ Sensor and Motor Drivers Flexible Software Protects Your Investments NI TestStand NI VeriStand NI DIAdem NI InsightCM Enterprise NI Multisim LabWindows/CVI Measurement Studio Third Party Software Our Customers’ Success Electronics and Industrial Machinery Aerospace and Defense Semiconductor Academic and Research Electronics and Industrial Machinery Aerospace and Defense Semiconductor Academic and Research Transportation and Automotive Wireless Heavy Equipment Energy Transportation and Automotive Wireless Heavy Equipment Energy AEROSPACE AND DEFENSE “Through the use of advanced software architecture and NI hardware, G Systems was able to provide Lockheed Martin Aeronautics with a highly-configurable, expandable system to meet current and future requirements of the F-35 VSIF.” — Michael Fortenberry, G Systems, Inc.