Solid Oxide Electrochemical Systems: Material Degradation Processes and Novel Mitigation Approaches
Total Page:16
File Type:pdf, Size:1020Kb
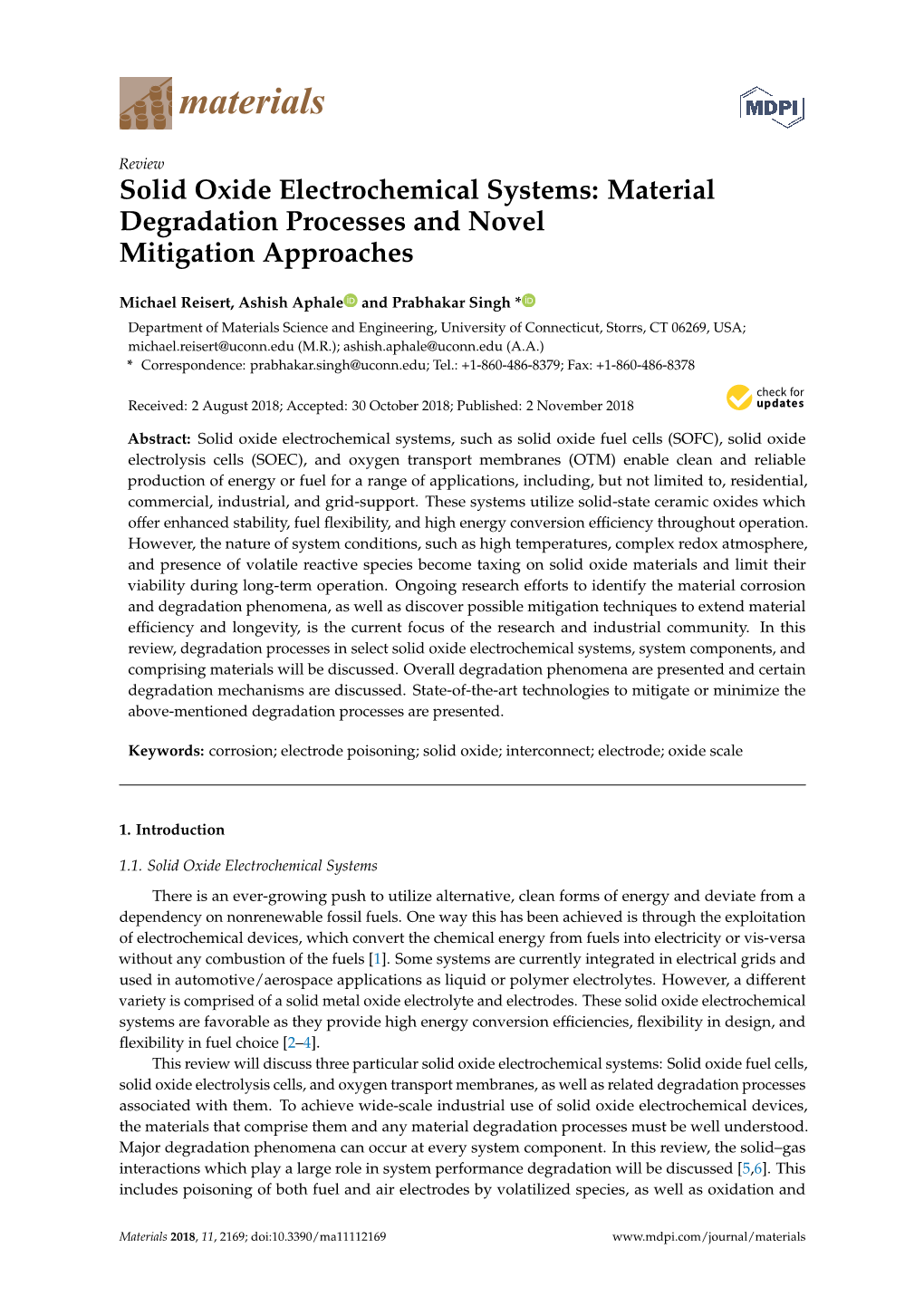
Load more
Recommended publications
-
1 Three-Dimensional Analysis of Solid Oxide Fuel Cell Ni-YSZ
Three-Dimensional Analysis of Solid Oxide Fuel Cell Ni-YSZ Anode Interconnectivity James R. Wilson,a Marcio Gameiro,b Konstantin Mischaikow,b William Kalies,c Peter W. Voorhees,a and Scott A. Barnetta a Department of Materials Science, Northwestern University, Evanston, IL 60208 b Department of Mathematics, Rutgers University, Piscataway, NJ 08854 c Department of Mathematics, Florida Atlantic University, Boca Raton, FL 33431 Abstract A method is described for quantitatively analyzing the level of interconnectivity of solid-oxide fuel cell (SOFC) electrode phases. The method was applied to the three-dimensional microstructure of a Ni – Y2O3-stabilized ZrO2 (Ni-YSZ) anode active layer measured by focused ion beam scanning electron microscopy. Each individual contiguous network of Ni, YSZ, and porosity was identified and labeled according to whether it was contiguous with the rest of the electrode. It was determined that the YSZ phase was 100% connected, whereas at least 86% of the Ni and 96% of the pores were connected. Triple- phase boundary (TPB) segments were identified and evaluated with respect to the contiguity of each of the three phases at their locations. It was found that 11.6% of the TPB length was on one or more isolated phases, and hence was not electrochemically active. 1 1. Introduction Attempts to understand solid oxide fuel cell (SOFC) electrode performance have often been limited by the lack of quantitative data describing the complex electrode microstructure. For example, composite electrodes such as Ni-YSZ (YSZ = 8 mol% Y2O3- stabilized ZrO2) typically consist of three phases – an electronically-conducting solid (e.g., Ni), an ionically-conducting solid (e.g., YSZ), and a pore phase. -
YSZ Electrodes
materials Article Analysis of Performance Losses and Degradation Mechanism in Porous La2−X NiTiO6−δ:YSZ Electrodes Juan Carlos Pérez-Flores 1,* , Miguel Castro-García 1 , Vidal Crespo-Muñoz 1, José Fernando Valera-Jiménez 1, Flaviano García-Alvarado 2 and Jesús Canales-Vázquez 1,* 1 3D-ENERMAT, Renewable Energy Research Institute, ETSII-AB, University of Castilla-La Mancha, 02071 Albacete, Spain; [email protected] (M.C.-G.); [email protected] (V.C.-M.); [email protected] (J.F.V.-J.) 2 Chemistry and Biochemistry Dpto., Facultad de Farmacia, Universidad San Pablo-CEU, CEU Universities, Boadilla del Monte, 28668 Madrid, Spain; fl[email protected] * Correspondence: [email protected] (J.C.P.-F.); [email protected] (J.C.-V.) Abstract: The electrode performance and degradation of 1:1 La2−xNiTiO6−δ:YSZ composites (x = 0, 0.2) has been investigated to evaluate their potential use as SOFC cathode materials by combining electrochemical impedance spectroscopy in symmetrical cell configuration under ambient air at 1173 K, XRD, electron microscopy and image processing studies. The polarisation resistance values increase notably, i.e., 0.035 and 0.058 Wcm2 h−1 for x = 0 and 0.2 samples, respectively, after 300 h under these demanding conditions. Comparing the XRD patterns of the initial samples and after long-term exposure to high temperature, the perovskite structure is retained, although La2Zr2O7 and NiO appear as secondary phases accompanied by peak broadening, suggesting amorphization or Citation: Pérez-Flores, J.C.; reduction of the crystalline domains. SEM and TEM studies confirm the ex-solution of NiO with time Castro-García, M.; Crespo-Muñoz, V.; in both phases and also prove these phases are prone to disorder. -
Triple-Phase Boundary and Power Density Enhancement in Thin Solid Oxide Fuel Cells by Controlled Etching of the Nickel Anode
Ebrahim et al. Nanoscale Research Letters 2014, 9:286 http://www.nanoscalereslett.com/content/9/1/286 NANO EXPRESS Open Access Triple-phase boundary and power density enhancement in thin solid oxide fuel cells by controlled etching of the nickel anode Rabi Ebrahim1,2*, Mukhtar Yeleuov4, Ainur Issova4, Serekbol Tokmoldin4 and Alex Ignatiev1,2,3,4 Abstract Fabrication of microporous structures for the anode of a thin film solid oxide fuel cell (SOFC(s)) using controlled etching process has led us to increased power density and increased cell robustness. Micropores were etched in the nickel anode by both wet and electrochemical etching processes. The samples etched electrochemically showed incomplete etching of the nickel leaving linked nickel islands inside the pores. Samples which were wet- etched showed clean pores with no nickel island residues. Moreover, the sample with linked nickel islands in the anode pores showed higher output power density as compared to the sample with clean pores. This enhancement is related to the enlargement of the surface of contact between the fuel-anode-electrolyte (the triple-phase boundary). Keywords: Thin film; Solid oxide; Fuel cell; Triple-phase boundaries; YSZ; LSCO Background high operating temperature of the SOFCs, it has been The world's extensive use of petroleum increased dras- proposed to reduce electrolyte thickness and/or use a tically in the last decades causing not only a sharp drop higher ion conducting electrolyte material. The fabrication in the world reserves but also resultant environmental of ultra-thin film SOFCs (10- to 15-μmcellthickness) concerns. Natural gas and other high hydrogen content built on microporous thin metallic foil substrates has fuels are better replacement candidates because of their already shown considerable reduction of the operating lower environmental effects [1-3]. -
Microfluidic Microbial Fuel Cells for Microstructure Interrogations By
Microfluidic Microbial Fuel Cells for Microstructure Interrogations by Erika Andrea Parra A dissertation submitted in partial satisfaction of the requirements for the degree of Doctor of Philosophy in Engineering - Mechanical Engineering in the Graduate Division of the University of California, Berkeley Committee in charge: Professor Liwei Lin, Chair Professor Carlos Fendandez-Pello Professor John D. Coates Fall 2010 Microfluidic Microbial Fuel Cells for Microstructure Interrogations Copyright 2010 by Erika Andrea Parra 1 Abstract Microfluidic Microbial Fuel Cells for Microstructure Interrogations by Erika Andrea Parra Doctor of Philosophy in Engineering - Mechanical Engineering University of California, Berkeley Professor Liwei Lin, Chair The breakdown of organic substances to retrieve energy is a naturally occurring process in nature. Catabolic microorganisms contain enzymes capable of accelerating the disintegration of simple sugars and alcohols to produce separated charge in the form of electrons and protons as byproducts that can be harvested extracellularly through an electrochemical cell to produce electrical energy directly. Bioelectrochemical energy is then an appealing green alternative to other power sources. However, a number of fundamental questions must be addressed if the technology is to become economically feasible. Power densities are low, hence the electron flow through the system: bacteria-electrode connectivity, the volumetric limit of catalyst loading, and the rate-limiting step in the system must be understood and optimized. This project investigated the miniaturization of microbial fuel cells to explore the scaling of the biocatalysis and generate a platform to study fundamental microstructure effects. Ultra- micro-electrodes for single cell studies were developed within a microfluidic configuration to quantify these issues and provide insight on the output capacity of microbial fuel cells as well as commercial feasibility as power sources for electronic devices. -
Electronic Transfer Within a Microbial Fuel Cell. Better Understanding of Experimental and Structural Parameters at the Interfac
Electronic transfer within a microbial fuel cell. Better understanding of Experimental and Structural Parameters at the Interface between Electro-active Bacteria and Carbon-based Electrodes David Pinto To cite this version: David Pinto. Electronic transfer within a microbial fuel cell. Better understanding of Experimental and Structural Parameters at the Interface between Electro-active Bacteria and Carbon-based Elec- trodes. Material chemistry. Université Pierre et Marie Curie - Paris VI, 2016. English. NNT : 2016PA066367. tel-01481318 HAL Id: tel-01481318 https://tel.archives-ouvertes.fr/tel-01481318 Submitted on 2 Mar 2017 HAL is a multi-disciplinary open access L’archive ouverte pluridisciplinaire HAL, est archive for the deposit and dissemination of sci- destinée au dépôt et à la diffusion de documents entific research documents, whether they are pub- scientifiques de niveau recherche, publiés ou non, lished or not. The documents may come from émanant des établissements d’enseignement et de teaching and research institutions in France or recherche français ou étrangers, des laboratoires abroad, or from public or private research centers. publics ou privés. Université Pierre et Marie Curie Ecole doctorale 397 − Physique et Chimie des Matériaux Laboratoire Chimie de la Matière Condensée de Paris Matériaux Hybride et Nanomatériaux TRANSFERT ELECTRONIQUE AU SEIN D’UNE PILE A COMBUSTIBLE MICROBIENNE Compréhension des Paramètres Expérimentaux et Structuraux à l’Interface entre une Bactérie électro-active et une Electrode carbonée Présentée par : David PINTO Thèse de doctorat de Chimie des Matériaux Dirigée par : Pr. Christel Laberty-Robert et Dr. Thibaud Coradin Présentée et soutenue publiquement le 14 Novembre 2016 Devant le jury composé de : Dr. -
Recent Advances in Zinc-Air Batteries
Chemical Society Reviews Recent Advances in Zinc -Air Batteries Journal: Chemical Society Reviews Manuscript ID: CS-REV-01-2014-000015.R2 Article Type: Review Article Date Submitted by the Author: 28-Apr-2014 Complete List of Authors: Li, Yanguang; Soochow University, Institute of Functional Nano & Soft Materials Dai, Hongjie; Chemistry Department, Stanford University Page 1 of 52 Chemical Society Reviews Recent Advances in Zinc-Air Batteries Yanguang Li 1* and Hongjie Dai 2* 1 Institute of Functional Nano & Soft Materials (FUNSOM) & Collaborative Innovation Center of Suzhou Nano Science and Technology, Soochow University, Suzhou 215123, China 2 Department of Chemistry, Stanford University, Stanford, CA 94305, USA Correspondence to: [email protected] ; [email protected] Abstract : Zinc-air is a century-old battery technology but has attracted revived interest recently. With larger storage capacity at a fraction of cost compared to lithium-ion, zinc-air batteries clearly represent one of the most viable future options to powering electric vehicles. However, some technical problems associated with them have yet to be resolved. In this review, we present the fundamentals, challenges and latest exciting advances related to zinc-air research. Detailed discussion will be organized around the individual components of the system − from zinc electrodes, electrolytes, separators to air electrodes and oxygen electrocatalysts in sequential order for both primary and electrically/mechanically rechargeable types. The detrimental effect of CO 2 on battery performance is also emphasized, and possible solutions summarized. Finally, other metal-air batteries are briefly overviewed and compared in favor of zinc-air. 1 Chemical Society Reviews Page 2 of 52 1. -
Characterization of Gas Diffusion Electrodes for Metal-Air Batteries
Characterization of gas diffusion electrodes for metal-air batteries Timo Dannera,b,∗, Santhana Eswarac,d, Volker P. Schulze, Arnulf Latza,b,f aInstitute of Engineering Thermodynamics, German Aerospace Center (DLR), Pfaffenwaldring 38-40, 70569 Stuttgart, Germany bHelmholtz Institute Ulm for Electrochemical Energy Storage (HIU), Helmholtzstraße 11, 89081 Ulm, Germany cElectron Microscopy Group of Materials Science, University of Ulm, Albert-Einstein-Allee 11, 89081 Ulm, Germany dAdvanced Instrumentation for Ion Nano-Analytics (AINA/MRT),Luxembourg Institute of Science and Technology, Rue du Brill 41, L-4422 Belvaux, Luxembourg eEngineering department, Baden-Wuerttemberg Cooperative State University Mannheim, Coblitzallee 1-9, 68163 Mannheim, Germany fInstitute of Electrochemistry, University of Ulm, Albert-Einstein-Allee 47, 89081 Ulm, Germany Abstract Gas diffusion electrodes are commonly used in high energy density metal- air batteries for the supply of oxygen. Hydrophobic binder materials ensure the coexistence of gas and liquid phase in the pore network. The phase distribution has a strong influence on transport processes and electrochem- ical reactions. In this article we present 2D and 3D Rothman-Keller type multiphase Lattice-Boltzmann models which take into account the hetero- geneous wetting behavior of gas diffusion electrodes. The simulations are performed on FIB-SEM 3D reconstructions of an Ag model electrode for predefined saturation of the pore space with the liquid phase. The resulting arXiv:1702.04670v1 [physics.flu-dyn] 30 Jan 2017 ∗Corresponding author: Email address: [email protected] (Timo Danner) URL: http://www.dlr.de/tt/en/ (Timo Danner) Preprint submitted to Journal of Power Sources February 16, 2017 pressure-saturation characteristics and transport correlations are important input parameters for modeling approaches on the continuum scale and allow for an efficient development of improved gas diffusion electrodes. -
Electrode Surface Activation and Nanostructuring Effects
ELECTRODE SURFACE ACTIVATION AND NANOSTRUCTURING EFFECTS ON FUEL CELL PERFORMANCE A DISSERTATION SUBMITTED TO THE DEPARTMENT OF MATERIALS SCIENCE AND ENGINEERING AND THE COMMITTEE ON GRADUATE STUDIES OF STANFORD UNIVERSITY IN PARTIAL FULFILLMENT OF THE REQUIREMENTS FOR THE DEGREE OF DOCTOR OF PHILOSOPHY Jason David Komadina December 2010 © 2011 by Jason David Komadina. All Rights Reserved. Re-distributed by Stanford University under license with the author. This work is licensed under a Creative Commons Attribution- Noncommercial 3.0 United States License. http://creativecommons.org/licenses/by-nc/3.0/us/ This dissertation is online at: http://purl.stanford.edu/zq508hs6390 ii I certify that I have read this dissertation and that, in my opinion, it is fully adequate in scope and quality as a dissertation for the degree of Doctor of Philosophy. Friedrich Prinz, Primary Adviser I certify that I have read this dissertation and that, in my opinion, it is fully adequate in scope and quality as a dissertation for the degree of Doctor of Philosophy. Yi Cui I certify that I have read this dissertation and that, in my opinion, it is fully adequate in scope and quality as a dissertation for the degree of Doctor of Philosophy. Paul McIntyre Approved for the Stanford University Committee on Graduate Studies. Patricia J. Gumport, Vice Provost Graduate Education This signature page was generated electronically upon submission of this dissertation in electronic format. An original signed hard copy of the signature page is on file in University Archives. iii Abstract Fuel cells are an attractive clean energy technology due to the low or zero emissions from operation and the potentially high efficiency. -
Direct-Hydrocarbon Proton-Conducting Solid Oxide Fuel Cells
sustainability Review Direct-Hydrocarbon Proton-Conducting Solid Oxide Fuel Cells Fan Liu and Chuancheng Duan * The Tim Taylor Department of Chemical Engineering, Kansas State University, Manhattan, KS 66506, USA; fl[email protected] * Correspondence: [email protected]; Tel.: +1-785-532-5587 Abstract: Solid oxide fuel cells (SOFCs) are promising and rugged solid-state power sources that can directly and electrochemically convert the chemical energy into electric power. Direct-hydrocarbon SOFCs eliminate the external reformers; thus, the system is significantly simplified and the capital cost is reduced. SOFCs comprise the cathode, electrolyte, and anode, of which the anode is of paramount importance as its catalytic activity and chemical stability are key to direct-hydrocarbon SOFCs. The conventional SOFC anode is composed of a Ni-based metallic phase that conducts electrons, and an oxygen-ion conducting oxide, such as yttria-stabilized zirconia (YSZ), which exhibits an ionic conductivity of 10−3–10−2 S cm−1 at 700 ◦C. Although YSZ-based SOFCs are being commercialized, YSZ-Ni anodes are still suffering from carbon deposition (coking) and sulfur poisoning, ensuing per- formance degradation. Furthermore, the high operating temperatures (>700 ◦C) also pose challenges to the system compatibility, leading to poor long-term durability. To reduce operating temperatures of SOFCs, intermediate-temperature proton-conducting SOFCs (P-SOFCs) are being developed as alternatives, which give rise to superior power densities, coking and sulfur tolerance, and durability. Due to these advances, there are growing efforts to implement proton-conducting oxides to improve durability of direct-hydrocarbon SOFCs. However, so far, there is no review article that focuses on direct-hydrocarbon P-SOFCs. -
UNIVERSITY of CALIFORNIA SAN DIEGO Fabrication of a Porous
UNIVERSITY OF CALIFORNIA SAN DIEGO Fabrication of a porous anode with continuous linear pores by using unidirectional carbon fibers as sacrificial templates to improve the performance of solid oxide fuel cell A Thesis submitted in partial satisfaction of the requirements for the degree Master of Science in Materials Science and Engineering by Carson Cheung Committee in charge: Professor Olivia A. Graeve, Chair Professor Javier E. Garay Professor Jian Luo 2018 The Thesis of Carson Cheung is approved, and it is acceptable in quality and form for publication on microfilm and electronically: ______________________________________________________________________________ ______________________________________________________________________________ ______________________________________________________________________________ Chair University of California San Diego 2018 iii DEDICATION I dedicate this thesis to my parents, Esther Cheung and Ken Cheung, for always giving me such loving support, Seongcheol Choi who has been a great mentor through my time in graduate school, and Olivia A. Graeve for this once in a lifetime opportunity to contribute a publication to society. iv TABLE OF CONTENTS SIGNATURE PAGE ..................................................................................................................... iii DEDICATION ............................................................................................................................... iv TABLE OF CONTENTS ............................................................................................................... -
Modeling of Solid Oxide Fuel Cells
Modeling of Solid Oxide Fuel Cells by Won Yong Lee B.S. Mechanical Engineering Seoul National University, 2001 SUBMITTED TO THE DEPARTMENT OF MECHANICAL ENGINEERING IN PARTIAL FULFILLMENT OF THE REQUIREMENTS FOR THE DEGREE OF MASTER OF SCIENCE IN MECHANICAL ENGINEERING AT THE MASSACHUSETTS INSTITUTE OF TECHNOLOGY SEPTEMBER 2006 C 2006 Massachusetts Institute of Technology. All rights reserved. The author hereby grants to MIT permission to reproduce and to distribute publicly paper and electronic copies of this thesis document in whole or in part in any medium now known or hereafter created. Signature of A uthor .......................................................... Department of Mechanical Engineering August 19, 2006 Certified by ............................... Ahmed F. Ghoniem Professor Thesis Supervisor A ccepted by................................................................. Lallit Anand Chairman, Department Committee on Graduate Students Modeling of Solid Oxide Fuel Cells By Won Yong Lee Submitted to the Department of Mechanical Engineering on 19 August 2006 in partial fulfillment of the requirements for the degree of Master of Science in Mechanical Engineering Abstract A comprehensive membrane-electrode assembly (MEA) model of Solid Oxide Fuel Cell (SOFC)s is developed to investigate the effect of various design and operating conditions on the cell performance and to examine the underlying mechanisms that govern their performance. We review and compare the current modeling methodologies, and develop an one-dimensional MEA model based on a comprehensive approach that include the dusty- gas model(DGM) for gas transport in the porous electrodes, the detailed heterogeneous elementary reaction kinetics for the thermo-chemistry in the anode, and the detailed electrode kinetics for the electrochemistry at the triple-phase boundary. -
Triple Phase Boundary Specific Pathway Analysis for Quantitative Characterization of Solid Oxide Cell Electrode Microstructure
Downloaded from orbit.dtu.dk on: Sep 28, 2021 Triple phase boundary specific pathway analysis for quantitative characterization of solid oxide cell electrode microstructure Jørgensen, Peter Stanley; Ebbehøj, Søren Lyng; Hauch, Anne Published in: Journal of Power Sources Link to article, DOI: 10.1016/j.jpowsour.2015.01.054 Publication date: 2015 Document Version Peer reviewed version Link back to DTU Orbit Citation (APA): Jørgensen, P. S., Ebbehøj, S. L., & Hauch, A. (2015). Triple phase boundary specific pathway analysis for quantitative characterization of solid oxide cell electrode microstructure. Journal of Power Sources, 279, 686- 693. https://doi.org/10.1016/j.jpowsour.2015.01.054 General rights Copyright and moral rights for the publications made accessible in the public portal are retained by the authors and/or other copyright owners and it is a condition of accessing publications that users recognise and abide by the legal requirements associated with these rights. Users may download and print one copy of any publication from the public portal for the purpose of private study or research. You may not further distribute the material or use it for any profit-making activity or commercial gain You may freely distribute the URL identifying the publication in the public portal If you believe that this document breaches copyright please contact us providing details, and we will remove access to the work immediately and investigate your claim. Triple Phase Boundary Specific Pathway Analysis for Quantitative Characterization of Solid Oxide Cell Electrode Microstructure P.S. Jørgensena,*, S. L. Ebbehøja A. Haucha, aDepartment of Energy Conversion and Storage, Technical University of Denmark, Risø Campus, Frederiksborgvej 399, 4000 Roskilde, Denmark.