Influence of Isolation Condition on Structure of Milled Wood Lignin Characterized by Quantitative 13C Nuclear Magnetic Resonance Spectroscopy
Total Page:16
File Type:pdf, Size:1020Kb
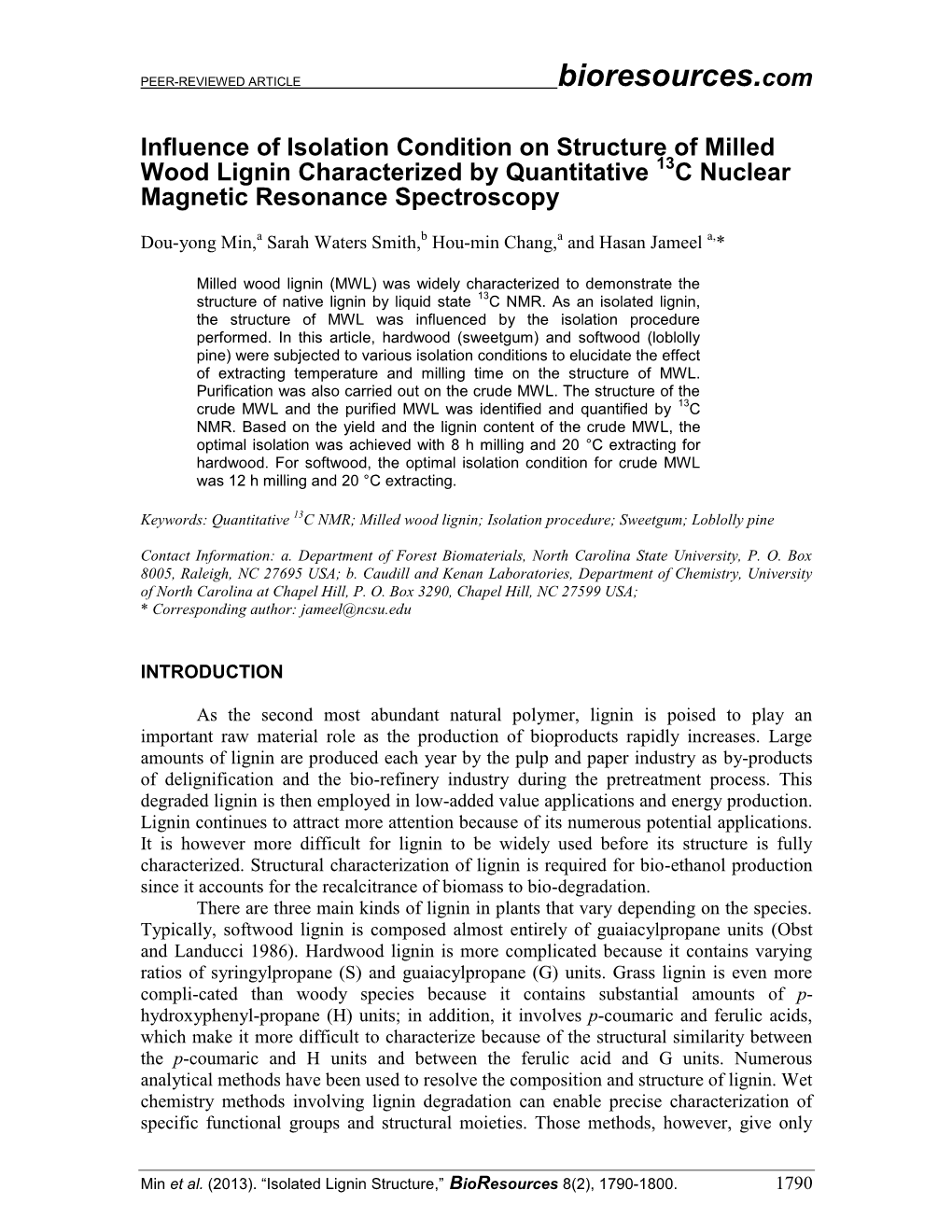
Load more
Recommended publications
-
Lignin Utilization Technology Session Review Area: Biochemical Conversion & Lignin Utilization PI: Gregg T
Lignin Utilization Technology Session Review Area: Biochemical Conversion & Lignin Utilization PI: Gregg T. Beckham, National Renewable Energy Laboratory From Davis et al. NREL Design Report 2013; Project overview Corona et al. Green Chem. 2018 Goal: Develop industrially-relevant processes and tools for Heilmeier Catechism: viable lignin valorization – contribute $2-3/gge to MFSP • Aim: develop lignin depolymerization catalysts and • Develop deconstruction catalysts for C–C bonds in lignin analytics for accurate process metrics • Provide deconstructed lignin to bioconversion efforts • Today: lignin combusted for heat, C–C bonds are • Develop lignin analytics and model compound syntheses major hurdle, analytics mostly monomers only • Support lignin projects in the BETO/DOE portfolio • Important: lignin key for biorefinery TEA and LCA (Biological Lignin Valorization (BLV), LigFirst, ORNL • Risks: C–C cleavage and quantitative lignin project, SepCon, Bioenergy Research Centers, etc.) analytics are both challenging NREL | 2 Management Task 1: Analytics and Synthesis • Experts in synthesis (R. Katahira) and analytics (B. Black) • Milestones: lignin characterization tool development, model compound synthesis • Collaborate with multiple projects – support BETO lignin portfolio for analytics and models Task 2: Depolymerization • Experts in oxidation catalysis (X. Du, C. Palumbo, K. Sullivan) and chemical engineering (J. Kruger) • Milestones: usable monomer yield from oxidative catalytic deconstruction processes • Milestones: reaction/process engineering, -
Structural Characterization of Lignin and Lignin-Carbohydrate Complex (LCC) from Ginkgo Shells (Ginkgo Biloba L.) by Comprehensive NMR Spectroscopy
polymers Article Structural Characterization of Lignin and Lignin-Carbohydrate Complex (LCC) from Ginkgo Shells (Ginkgo biloba L.) by Comprehensive NMR Spectroscopy Bo Jiang 1, Yu Zhang 1, Tianyu Guo 1, Huifang Zhao 1,2 and Yongcan Jin 1,* 1 Jiangsu Co-Innovation Center of Efficient Processing and Utilization of Forest Resources, Nanjing Forestry University, Nanjing 210037, China; [email protected] (B.J.); [email protected] (Y.Z.); [email protected] (T.G.); [email protected] (H.Z.) 2 Institute of Botany, Jiangsu Province and the Chinese Academy of Sciences, Nanjing 210014, China * Correspondence: [email protected]; Tel.: +86-025-8542-8163 Received: 13 June 2018; Accepted: 2 July 2018; Published: 4 July 2018 Abstract: Lignin and lignin-carbohydrate complexes are important polymers for lignocellulosic biorefinery and functional materials, but those in ginkgo shells are not effectively analyzed and exploited. Based on this background, milled wood lignins (MWLML and MWLFZ) and lignin- carbohydrate complexes (LCCML and LCCFZ) were isolated from the shells of Ginkgo biloba L. cv. Damaling (ML) and Ginkgo biloba L. cv. Dafozhi (FZ) correspondingly, and were structurally characterized by comprehensive NMR spectroscopy. The results showed that ginkgo shells exhibited higher lignin (42%) and xylan (20%) content than general softwood species. Isolated MWLs were rich in guaiacyl units with the presence of ferulates and p-coumarates, and the molecular formula was C9H7.93O2.73(OCH3)0.81 and C9H7.87O2.76(OCH3)0.88 for MWLML and MWLFZ, respectively. Phenolic hydroxyl of MWLML (1.38 mmol/g) and MWLFZ (1.23 mmol/g) in ginkgo shells was much less than that in general softwoods, suggesting a higher etherification and condensation degree of ginkgo shells lignin, and b-50, a-O-40, and 4-O-50 bonds were the main condensed structures. -
Lignin Transformation and Characterization of Pyrolytic Products Eric Amo Boakye South Dakota State University
South Dakota State University Open PRAIRIE: Open Public Research Access Institutional Repository and Information Exchange Theses and Dissertations 2017 Lignin Transformation and Characterization of Pyrolytic Products Eric Amo Boakye South Dakota State University Follow this and additional works at: http://openprairie.sdstate.edu/etd Part of the Chemistry Commons Recommended Citation Boakye, Eric Amo, "Lignin Transformation and Characterization of Pyrolytic Products" (2017). Theses and Dissertations. 1185. http://openprairie.sdstate.edu/etd/1185 This Dissertation - Open Access is brought to you for free and open access by Open PRAIRIE: Open Public Research Access Institutional Repository and Information Exchange. It has been accepted for inclusion in Theses and Dissertations by an authorized administrator of Open PRAIRIE: Open Public Research Access Institutional Repository and Information Exchange. For more information, please contact [email protected]. i LIGNIN TRANSFORMATION AND CHARACTERIZATION OF PYROLYTIC PRODUCTS BY ERIC AMO BOAKYE A dissertation submitted in partial fulfilment of the requirement for the Doctor of Philosophy Major in Chemistry South Dakota State University 2017 iii AKNOWLEDGEMENTS My sincere gratitude to my advisor, Dr. Douglas Raynie for his continuous encouragement, support, and selfless and faithful guidance offered to me throughout my entire time in graduate school. Many thanks also go to my committee members for their uncommon guidance and directions. To my green chemistry lab members, my friends, and all the people at SDSU who made my stay here a very memorable one. Thank you to all of you for your constant support. Thank you to Doctors Wei, Zhang, Gu and all your students for opening your labs to me all the time. -
Lignin–Carbohydrate Complexes: Properties, Applications, Analyses, and Methods of Extraction: a Review Dmitry Tarasov1,2, Mathew Leitch2 and Pedram Fatehi1*
Tarasov et al. Biotechnol Biofuels (2018) 11:269 https://doi.org/10.1186/s13068-018-1262-1 Biotechnology for Biofuels REVIEW Open Access Lignin–carbohydrate complexes: properties, applications, analyses, and methods of extraction: a review Dmitry Tarasov1,2, Mathew Leitch2 and Pedram Fatehi1* Abstract The complexity of lignin and hemicellulose segmentation has been known since the middle of the ninetieth century. Studies confrmed that all lignin units in coniferous species and 47–66% of lignin moieties in deciduous species are bound to hemicelluloses or cellulose molecules in lignin–carbohydrate complexes (LCC). Diferent types and propor- tions of lignin and polysaccharides present in biomass lead to the formation of LCC with a great variety of composi- tions and structures. The nature and amount of LCC linkages and lignin substructures afect the efciency of pulping, hydrolysis, and digestibility of biomass. This review paper discusses the structures, compositions, and properties of LCC present in biomass and in the products obtained via pretreating biomass. Methods for extracting, fractionating, and analyzing LCC of biomass, pulp, and spent pulping liquors are critically reviewed. The main perspectives and chal- lenges associated with these technologies are extensively discussed. LCC could be extracted from biomass follow- ing varied methods, among which dimethyl sulfoxide or dioxane (Björkman’s) and acetic acid (LCC-AcOH) processes are the most widely applied. The oxidation and methylation treatments of LCC materials elucidate the locations and frequency of binding sites of hemicelluloses to lignin. The two-dimensional nuclear magnetic resonance analysis allows the identifcation of the structure and the quantity of lignin–carbohydrate bonds involved in LCC. -
A Critical Review on the Analysis of Lignin Carbohydrate Bonds in Plants
Green Chemistry A Critical Review on the Analysis of Lignin Carbohydrate Bonds in Plants Journal: Green Chemistry Manuscript ID GC-CRV-11-2018-003606.R2 Article Type: Critical Review Date Submitted by the 14-Feb-2019 Author: Complete List of Authors: Giummarella, Nicola; Wallenberg Wood Science Center Pu, Yunqiao; Oak Ridge National Laboratory, Joint Institute of Biological Science, Biosciences Division Ragauskas, Arthur; University of Tennessee, Lawoko, Martin; Wallenberg Wood Science Center (WWSC), Fiber and Polymer Technology Page 1 of 26 Please Greendo not Chemistry adjust margins Green Chemistry Critical Review A Critical Review on the Analysis of Lignin Carbohydrate Bonds Nicola Giummarella,a Yunqiao Pu,b,c Arthur J. Ragauskas*b,c,d,e and Martin Lawoko*a Received 00th January 20xx, Accepted 00th January 20xx Replacing fossil-based resources with renewable alternatives is generally acknowledged as a critical component to address several of today's environmental concerns. In this context, lignocellulosic biomass is an attractive, sustainable resource. DOI: 10.1039/x0xx00000x However, the constitutional biopolymers of interest are locked in the structural complexity of the plant cell walls, which www.rsc.org/ defines their properties and contributes to fractionation recalcitrance. One of the key suspects restricting fractionation of the biopolymers in high yield is the presence of lignin-carbohydrate bonds forming a matrix referred to as Lignin- Carbohydrate Complexes (LCC). Nevertheless, covalent bonds between lignin and carbohydrates, remain one of the most controversial topics in lignocellulose chemistry. This challenge can be attributed to the slow progress made in their research, which also forms the basis for this review. Herein, we will critically discuss the literature with a particular focus on the latest characterization and analytical techniques. -
Preparation and Characterization of Lignin
The Pennsylvania State University The Graduate School College of Agricultural Sciences PREPARATION AND CHARACTERIZATION OF LIGNIN- PROTEIN COVALENT LINKAGES A Dissertation in Biorenewable Systems by Brett Galen Diehl ©2014 Brett Galen Diehl Submitted in Partial Fulfillment of the Requirements for the Degree of Doctor of Philosophy May 2014 The dissertation of Brett Galen Diehl was reviewed and approved* by the following: Nicole R. Brown Associate Professor of Wood Chemistry Dissertation Adviser Chair of Committee John E. Carlson Professor of Molecular Genetics Jeffrey M. Catchmark Associate Professor of Agricultural and Biological Engineering Emmanuel Hatzakis Director of NMR facility John Ralph Special Member Professor of Biochemistry University of Wisconsin at Madison Paul Smith Head of Biorenewable Systems department *Signatures are on file in the Graduate School. ii Abstract Lignin is a natural aromatic polymer that is bio-synthesized in the cell walls of almost all land plants. Great strides have been made in understanding lignin’s biological origins and chemical and physical properties. However, many unanswered questions remain. For example, the extent to which lignin interacts with other cell wall components, such as proteins, is largely unknown. In order to help address this question, the preparation and characterization of lignin- protein covalent linkages is reported here for the first time. Chapter 1 provides a more detailed introduction, justification, and literature review. Chapter 2 focuses on the preparation of low molecular weight lignin-protein model compounds. The compounds were not prepared under biomimetic conditions. Instead, the primary focus of this study was on the characterization of the model compounds, leading to the identification of diagnostic lignin-protein NMR chemical shifts. -
Study of New Chemical Derivatization Techniques for Lignin Analysis by Size Exclusion Chromatography Esakkiammal Sudha Esakkimuthu
Study of new chemical derivatization techniques for lignin analysis by size exclusion chromatography Esakkiammal Sudha Esakkimuthu To cite this version: Esakkiammal Sudha Esakkimuthu. Study of new chemical derivatization techniques for lignin analysis by size exclusion chromatography. Material chemistry. Université Grenoble Alpes [2020-..], 2020. English. NNT : 2020GRALI004. tel-02612598 HAL Id: tel-02612598 https://tel.archives-ouvertes.fr/tel-02612598 Submitted on 19 May 2020 HAL is a multi-disciplinary open access L’archive ouverte pluridisciplinaire HAL, est archive for the deposit and dissemination of sci- destinée au dépôt et à la diffusion de documents entific research documents, whether they are pub- scientifiques de niveau recherche, publiés ou non, lished or not. The documents may come from émanant des établissements d’enseignement et de teaching and research institutions in France or recherche français ou étrangers, des laboratoires abroad, or from public or private research centers. publics ou privés. THÈSE Pour obtenir le grade de DOCTEUR DE L'UNIVERSITE GRENOBLE ALPES Spécialité : 2MGE : Matériaux, Mécanique, Génie civil, Electrochimie Arrêté ministériel : 25 mai 2016 Présentée par Esakkiammal Sudha ESAKKIMUTHU Thèse dirigée par Gérard MORTHA, Professeur, Grenoble INP et Co-encadrée par Nathalie MARLIN, Maître de Conférences, Grenoble INP préparée au sein du Laboratoire Génie des Procédés Papetiers (LGP2) dans l'École Doctorale I-MEP2 - Ingénierie - Matériaux, Mécanique, Environnement, Energétique, Procédés, Production Étude -
Extraction, Modification and Characterization of Lignin from Oil Palm Fronds As Corrosion Inhibitors for Mild Steel in Acidic Solution Mohd Hazwan Bin Hussin
Extraction, modification and characterization of lignin from oil palm fronds as corrosion inhibitors for mild steel in acidic solution Mohd Hazwan Bin Hussin To cite this version: Mohd Hazwan Bin Hussin. Extraction, modification and characterization of lignin from oil palm fronds as corrosion inhibitors for mild steel in acidic solution. Food and Nutrition. Université de Lorraine, 2014. English. NNT : 2014LORR0135. tel-01750984 HAL Id: tel-01750984 https://hal.univ-lorraine.fr/tel-01750984 Submitted on 29 Mar 2018 HAL is a multi-disciplinary open access L’archive ouverte pluridisciplinaire HAL, est archive for the deposit and dissemination of sci- destinée au dépôt et à la diffusion de documents entific research documents, whether they are pub- scientifiques de niveau recherche, publiés ou non, lished or not. The documents may come from émanant des établissements d’enseignement et de teaching and research institutions in France or recherche français ou étrangers, des laboratoires abroad, or from public or private research centers. publics ou privés. AVERTISSEMENT Ce document est le fruit d'un long travail approuvé par le jury de soutenance et mis à disposition de l'ensemble de la communauté universitaire élargie. Il est soumis à la propriété intellectuelle de l'auteur. Ceci implique une obligation de citation et de référencement lors de l’utilisation de ce document. D'autre part, toute contrefaçon, plagiat, reproduction illicite encourt une poursuite pénale. Contact : [email protected] LIENS Code de la Propriété Intellectuelle. articles L 122. 4 Code de la Propriété Intellectuelle. articles L 335.2- L 335.10 http://www.cfcopies.com/V2/leg/leg_droi.php http://www.culture.gouv.fr/culture/infos-pratiques/droits/protection.htm Faculté des Sciences et Technique U.F.R. -
( 12 ) United States Patent
US009988412B2 (12 ) United States Patent ( 10 ) Patent No .: U 8 , 412 B2 Jansen et al. ( 45 ) Date of Patent : Jun . 5 , 2018 (54 ) METHODS FOR PREPARING THERMALLY 58 ) Field of Classification Search STABLE LIGNIN FRACTIONS CPC combination set ( s ) only. See application file for complete search history . Applicant : Virdia , Inc ., Raceland , LA (US ) ( 71) ( 56 ) References Cited ( 72 ) Inventors : Robert Jansen , Collinsville , IL (US ) ; James Alan Lawson , Ellsworth , ME U . S . PATENT DOCUMENTS (US ) ; Noa Lapidot , Mevaseret Zion 2 , 380 , 448 A 7 / 1945 Katzen ( IL ) ; Bassem Hallac, Jerusalem ( IL ) ; 2 , 772 , 965 A 12 / 1956 Gray et al. Perry Rotem , Bazra ( IL ) 3 , 808 , 192 A 4 / 1974 Dimitri M 4 , 111 , 928 A 9 / 1978 Holsopple et al. 4 ,237 , 110 A 12 / 1980 Forster et al. ( 73 ) Assignee : VIRDIA , INC ., Raceland, LA (US ) 4 ,277 ,626 A 7 / 1981 Forss et al . 4 ,470 ,851 A 9 / 1984 Paszner et al. ( * ) Notice : Subject to any disclaimer , the term of this 4 ,520 , 105 A 5 / 1985 Sinner et al. patent is extended or adjusted under 35 4 ,740 , 591 A 4 / 1988 Dilling et al . U . S . C . 154 ( b ) by 0 days. days . 4 ,797 ,457 A 1 / 1989 Guiver et al . 4 , 946 , 946 A 8 / 1990 Fields et al . (21 ) Appl. No. : 15 /593 , 752 ( Continued ) ( 22 ) Filed : May 12 , 2017 FOREIGN PATENT DOCUMENTS 2812685 A1 3 /2012 (65 ) Prior Publication Data 101143881 A 3 / 2008 US 2018 /0079766 A1 Mar . 22 , 2018 ( Continued ) Related U . S . Application Data OTHER PUBLICATIONS (63 ) Continuation of application No . -
Understanding Lignin Fractionation and Characterization From
Research Article Cite This:ACS Sustainable Chem. Eng.2018, 6, 6612−6623 pubs.acs.org/journal/ascecg Understanding Lignin Fractionation and Characterization from Engineered Switchgrass Treated by an Aqueous Ionic Liquid Enshi Liu,†Mi Li,‡Lalitendu Das,†Yunqiao Pu,‡Taylor Frazier,§Bingyu Zhao,§Mark Crocker,∥,⊥ Arthur J. Ragauskas,‡,# and Jian Shi*,† †Biosystems and Agricultural Engineering, University of Kentucky, 115 C.E. Barnhart Building, Lexington, Kentucky 40546, United States ‡Joint Institute of Biological Science, Center for BioEnergy Innovation, Biosciences Division, Oak Ridge National Laboratory, Oak Ridge, Tennessee 37831, United States §Department of Horticulture, Virginia Tech, Blacksburg, Virginia 24061, United States ∥Center for Applied Energy Research, University of Kentucky, Lexington, Kentucky 40511, United States ⊥Department of Chemistry, University of Kentucky, Lexington, Kentucky 40506, United States #Department of Chemical & Biomolecular Engineering, Center for Renewable Carbon, and Department of Forestry, Wildlife, and Fisheries, University of Tennessee, Knoxville, Tennessee 37996, United States *S Supporting Information ABSTRACT:Aqueous ionic liquids (ILs) have received increasing interest because of their high efficacy in fractionating and pretreating lignocellulosic biomass while at the same time mitigating several challenges associated with IL pretreatment such as IL viscosity, gel formation during pretreatment, and the energy consumption and costs associated with IL recycling. This study investigated the fate of -
Characterization and Utilization of Hot-Water Extracted Lignin for Formaldehyde-Free Resin Applications
SUNY College of Environmental Science and Forestry Digital Commons @ ESF Dissertations and Theses Spring 4-23-2018 CHARACTERIZATION AND UTILIZATION OF HOT-WATER EXTRACTED LIGNIN FOR FORMALDEHYDE-FREE RESIN APPLICATIONS Prajakta Dongre [email protected] Follow this and additional works at: https://digitalcommons.esf.edu/etds Recommended Citation Dongre, Prajakta, "CHARACTERIZATION AND UTILIZATION OF HOT-WATER EXTRACTED LIGNIN FOR FORMALDEHYDE-FREE RESIN APPLICATIONS" (2018). Dissertations and Theses. 58. https://digitalcommons.esf.edu/etds/58 This Open Access Dissertation is brought to you for free and open access by Digital Commons @ ESF. It has been accepted for inclusion in Dissertations and Theses by an authorized administrator of Digital Commons @ ESF. For more information, please contact [email protected], [email protected]. CHARACTERIZATION AND UTILIZATION OF HOT-WATER EXTRACTED LIGNIN FOR FORMALDEHYDE-FREE RESIN APPLICATIONS by Prajakta Dongre A dissertation submitted in partial fulfillment of the requirements for the Doctor of Philosophy Degree State University of New York College of Environmental Science and Forestry Syracuse, New York April 2018 Department of Paper and Bioprocess Engineering Approved by: Biljana Bujanovic, Major Professor Thomas Amidon, Co-Major Professor Robert W. Malmsheimer, Chair, Examining Committee Bandaru V. Ramarao, Faculty Chair S. Scott Shannon, Dean, The Graduate School Gary M. Scott, Director, Division of Engineering © 2018 Copyright Prajakta Dongre All rights reserved Acknowledgements I would like to thank my advisor Dr. Biljana Bujanovic for her constant guidance and continually encouraging me to push boundaries. Dr. Amidon, for his ever-ready helping hand and understanding. I appreciate Dr. Arthur Stipanovic for his support on thermal analysis, Dr. -
Structural and Thermal Characterization of Novel Organosolv Lignins from Wood and Herbaceous Sources
processes Article Structural and Thermal Characterization of Novel Organosolv Lignins from Wood and Herbaceous Sources Anna Trubetskaya 1,*,† , Heiko Lange 2,*,† , Bernd Wittgens 3, Anders Brunsvik 3, Claudia Crestini 4 , Ulrika Rova 5 , Paul Christakopoulos 5, J. J. Leahy 1 and Leonidas Matsakas 5,*,† 1 Bernal Center, University of Limerick, V94 T9PX Castletroy, Ireland; [email protected] 2 Department of Pharmacy, University of Naples ’Federico II’, 80131 Naples, Italy 3 SINTEF Industry, Richard Birkelands vei 2B, 7034 Trondheim, Norway; [email protected] (B.W.); [email protected] (A.B.) 4 Department of Molecular Science and Nanosystems, University of Venice Ca’ Foscari, Via Torino 155, 30170 Venice Mestre, Italy; [email protected] 5 Biochemical Process Engineering, Division of Chemical Engineering, Department of Civil, Environmental and Natural Resources Engineering, Luleå University of Technology, 97187 Luleå, Sweden; [email protected] (U.R.); [email protected] (P.C.) * Correspondence: [email protected] (A.T.); [email protected] (H.L.); [email protected] (L.M.) † These authors contributed equally to this work. Received: 26 June 2020; Accepted: 13 July 2020; Published: 17 July 2020 Abstract: This study demonstrates the effects of structural variations of lignins isolated via an organosolv process from different woody and herbaceous feedstocks on their thermal stability profiles. The organosolv lignins were first analysed for impurities, and structural features were determined using the default set of gel permeation chromatography, FT-IR spectroscopy, quantitative 31P NMR 1 13 spectroscopy and semi-quantitative H- C HSQC analysis. Pyrolysis-, O2- and CO2-reactivity of the organosolv lignins were investigated by thermogravimetric analysis (TGA), and volatile formation in various heating cycles was mapped by head-space GC-MS analysis.