A Review on Lignin Liquefaction: Advanced Characterization of Structure and Microkinetic Modeling Evan Terrell, Lauren D
Total Page:16
File Type:pdf, Size:1020Kb
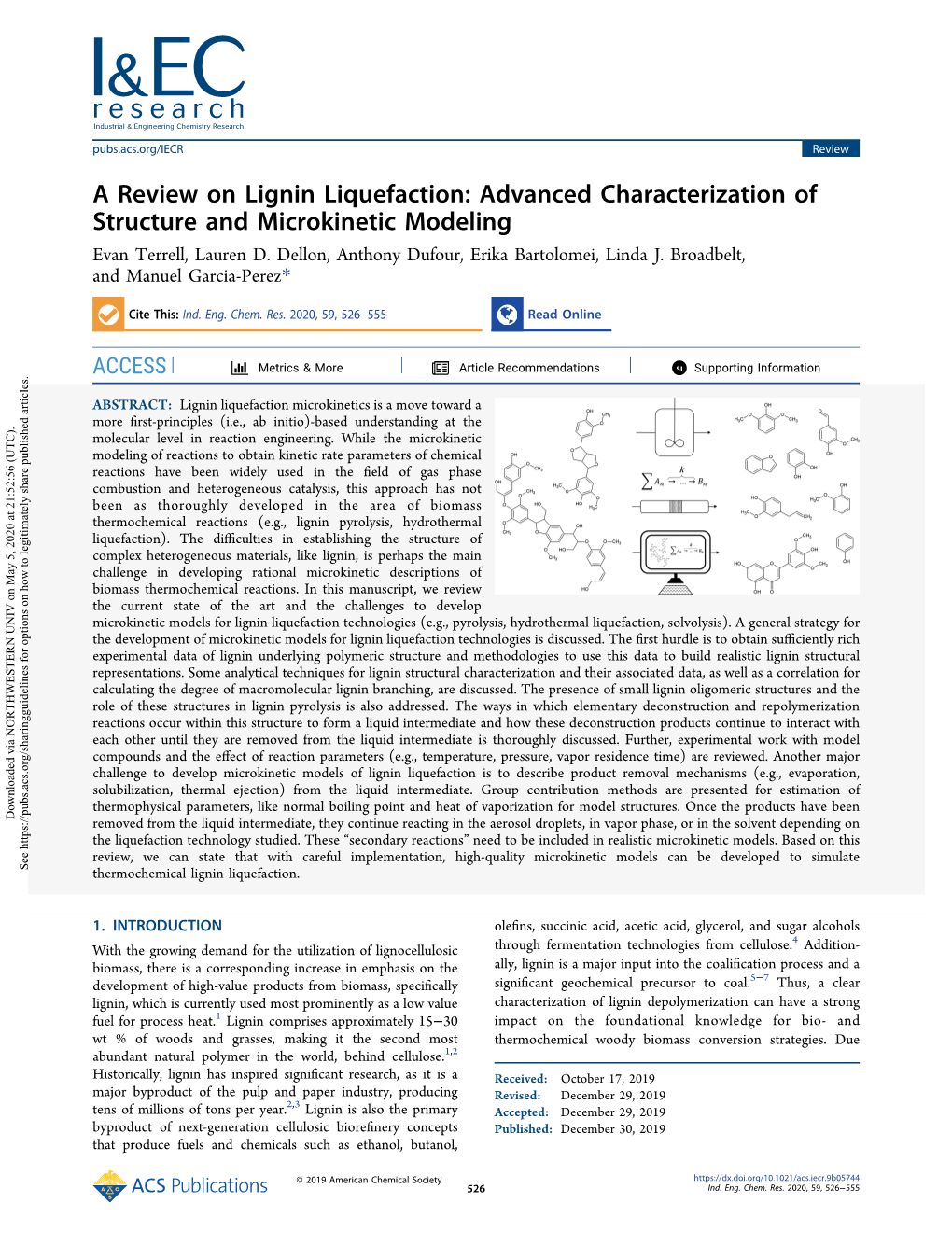
Load more
Recommended publications
-
2015 Plastics to Fuel Developer's Guide
2015 PLASTICS-TO-FUEL PROJECT DEVELOPER’S GUIDE Prepared For: The American Chemistry Council Prepared By: OCEAN RECOVERY ALLIANCE 20th Floor, Central Tower 28 Queen's Road Central Hong Kong TEL: (852) 2803-0018 c/o Malibu Foundation, 1471 S. Bedford St. #3, Los Angeles, Calif. 90035 TEL: (310)-614-5578 www.oceanrecov.org June 2015 1 Disclaimer: The 2015 Plastics-to-Fuel Project Developer’s Guide was prepared to educate prospective stakeholders on the current state of the plastics-to-fuel industry and offer considerations for developing a system. The views expressed here are those of the authors and should not be perceived as an endorsement of any technology provider or solution. Interested parties are advised to engage in direct consultation with technology providers to obtain additional, opportunity-specific costing and performance data when appropriate. The American Chemistry Council does not make any warranty or representation, either express or implied, with respect to the accuracy or completeness of the information contained in this report; nor does the American Chemistry Council assume any liability of any kind whatsoever resulting from the use of or reliance upon any information, conclusion, or options contained herein. The American Chemistry Council sponsored this report. About OCEAN RECOVERY ALLIANCE: OCEAN RECOVERY ALLIANCE (ORA) and the American Chemistry Council are working together to reduce plastic in the ocean environment. ORA is a 501c3 registered non- profit in California and a registered charitable organization in Hong Kong that seeks to introduce innovative projects and initiatives that will help improve our ocean environment by bringing together new ways of thinking, technologies, creativity and collaborations. -
Conversion Technologies for Advanced Biofuels – Bio-Oil Production
Conversion Technologies for Advanced Biofuels – Bio-Oil Production Report-Out Webinar David Dayton, Ph.D. February 9, 2012 RTI International 1 EnergyProgram Efficiency Name or &Ancillary Renewable Text Energy eere.energy.gov Bio-oil Production – Presenter Information Dr. David C. Dayton Director, Chemistry and Biofuels Center for Energy Technology RTI International 2007 – present RTI International 1993 – 2007 National Renewable Energy Laboratory 1991-1993 U.S. Army Research Laboratory • Ph.D., Biochemistry, University of Texas Health Science Center at San Antonio, 2000 • B.S., Biochemistry, cum laude, Washington State University, 1995 Over 18 years of project management and research experience in biomass thermochemical conversion R&D involving biomass combustion, gasification, and pyrolysis. Manage projects related to synthesis gas conversion, synthesis gas cleanup and conditioning, and catalytic biomass pyrolysis. Focus on expanding integrated biorefinery technology development activities for biofuels production. 2 Energy Efficiency & Renewable Energy eere.energy.gov State-of-Technology Current State-of-the-Art Bio-oil Production Gas – CO, CO2CxHy H H O, CO H H O, CO (C2) 2 2 2 2 2 2 Technology Options Fast Pyrolysis Biomass Flash Bio-oil Biofuel Hydroprocessing (Cin) Pyrolysis Stabilization (Cout) (0.1 MPa and ~500°C) Bio-oil Stabilization Char Coke Coke ° (C1) (C3) (C4) (10 MPa, 150-250 C) Hydroprocessing (20 MPa, 300-350°C) Next Generation Technology Catalytic Fast Pyrolysis (0.1 MPa and ~500°C) Gas – CO, CO2, CHxHy, 2 H2 H2O, -
Integrated Waste to Energy and Liquid Fuel Plants: Key to Sustainable Solid Waste Management
Integrated Waste to Energy and Liquid Fuel Plants: Key to Sustainable Solid Waste Management Bary Wilson, Ph.D. Barry Liss, Ph.D., P.E Brandon Wilson, Ph.D., P.E May 2019 EnviroPower Renewable, Inc. 7301A Palmetto Parkway Rd. Suite 206B Boca Raton, FL 33433 www.eprenewable.com EPR Doc. 05212019 © 2019 EPR All Rights Reserved 1 Table of Contents Executive Summary ................................................................................................................................... 3 Introduction .............................................................................................................................................. 4 Background ............................................................................................................................................... 4 Plastics................................................................................................................................................... 5 Plastics Recycling................................................................................................................................... 6 Diesel Fuels ........................................................................................................................................... 6 Premium Diesel ..................................................................................................................................... 7 Biodiesel and Renewable Diesel .......................................................................................................... -
Lignin Utilization Technology Session Review Area: Biochemical Conversion & Lignin Utilization PI: Gregg T
Lignin Utilization Technology Session Review Area: Biochemical Conversion & Lignin Utilization PI: Gregg T. Beckham, National Renewable Energy Laboratory From Davis et al. NREL Design Report 2013; Project overview Corona et al. Green Chem. 2018 Goal: Develop industrially-relevant processes and tools for Heilmeier Catechism: viable lignin valorization – contribute $2-3/gge to MFSP • Aim: develop lignin depolymerization catalysts and • Develop deconstruction catalysts for C–C bonds in lignin analytics for accurate process metrics • Provide deconstructed lignin to bioconversion efforts • Today: lignin combusted for heat, C–C bonds are • Develop lignin analytics and model compound syntheses major hurdle, analytics mostly monomers only • Support lignin projects in the BETO/DOE portfolio • Important: lignin key for biorefinery TEA and LCA (Biological Lignin Valorization (BLV), LigFirst, ORNL • Risks: C–C cleavage and quantitative lignin project, SepCon, Bioenergy Research Centers, etc.) analytics are both challenging NREL | 2 Management Task 1: Analytics and Synthesis • Experts in synthesis (R. Katahira) and analytics (B. Black) • Milestones: lignin characterization tool development, model compound synthesis • Collaborate with multiple projects – support BETO lignin portfolio for analytics and models Task 2: Depolymerization • Experts in oxidation catalysis (X. Du, C. Palumbo, K. Sullivan) and chemical engineering (J. Kruger) • Milestones: usable monomer yield from oxidative catalytic deconstruction processes • Milestones: reaction/process engineering, -
Deterioration in the Physico-Mechanical and Thermal Properties of Biopolymers Due to Reprocessing
polymers Article Deterioration in the Physico-Mechanical and Thermal Properties of Biopolymers Due to Reprocessing Jamileh Shojaeiarani 1,*, Dilpreet S. Bajwa 1, Chad Rehovsky 1, Sreekala G. Bajwa 2 and Ghazal Vahidi 1 1 Department of Mechanical Engineering, North Dakota State University, Fargo, ND 58108, USA; [email protected] (D.S.B.); [email protected] (C.R.); [email protected] (G.V.) 2 Department of Agriculture and Biosystem Engineering, North Dakota State University, Fargo, ND 58108, USA; [email protected] * Correspondence: [email protected]; Tel.: +1-701-799-7759 Received: 30 November 2018; Accepted: 18 December 2018; Published: 2 January 2019 Abstract: Biopolymers are an emerging class of materials being widely pursued due to their ability to degrade in short periods of time. Understanding and evaluating the recyclability of biopolymers is paramount for their sustainable and efficient use in a cost-effective manner. Recycling has proven to be an important solution, to control environmental and waste management issues. This paper presents the first recycling assessment of Solanyl, Bioflex, polylactic acid (PLA) and PHBV using a melt extrusion process. All biopolymers were subjected to five reprocessing cycles. The thermal and mechanical properties of the biopolymers were investigated by GPC, TGA, DSC, mechanical test, and DMA. The molecular weights of Bioflex and Solanyl showed no susceptible effect of the recycling process, however, a significant reduction was observed in the molecular weight of PLA and PHBV. The inherent thermo-mechanical degradation in PHBV and PLA resulted in 20% and 7% reduction in storage modulus, respectively while minimal reduction was observed in the storage modulus of Bioflex and Solanyl. -
An Analysis of Physico-Chemical Properties of the Next Generation Biofuels and Their Correlation with the Requirements of Diesel Engine
Chapter 16 An Analysis of Physico-Chemical Properties of the Next Generation Biofuels and Their Correlation with the Requirements of Diesel Engine Artur Malinowski, Joanna Czarnocka and Krzysztof Biernat Additional information is available at the end of the chapter http://dx.doi.org/10.5772/53685 1. Introduction There is a pressing need to haste developing advanced energy technologies to reduce dependency on crude oil and climate protection. Biofuels – liquid and gaseous fuels de‐ rived from organic matter – can play an important role in reducing of carbon dioxide (CO2) emissions in the transport, and can raise the energy security. By 2050, biofuels could provide 27% of total transport fuel. The use of biofuels could avoid around 2.1 gigatonnes (Gt) of CO2 emissions per year when produced sustainably. To meet this vi‐ sion, most conventional biofuel technologies need to improve conversion efficiency, cost and overall sustainability. Conventional biofuel technologies include well-established that are already producing biofuels on a commercial scale. These biofuels, commonly re‐ ferred to as first-generation, include sugar- and starch-based ethanol, oil-crop based bio‐ diesel and straight vegetable oil, as well as biogas gained through anaerobic digestion. The International Energy Agency has undertaken an effort to develop a series of global technology road maps covering 19 advanced technologies, commonly referred to as sec‐ ond- or third-generation. This new technologies are still in the research and develop‐ ment (R&D), pilot or demonstration phase [1].Significant decrease of fossil fuels and lack of new ones becomes the basis for the Olduvai theory, published by R.C. -
810International Conference
Chemicals and Products from Renewable Carbon International Conference St. Simons Island, Georgia, USA November 5 - November 8 Steering Committee0 Members Advisory Board Members8 2Nourredine Abdoulmoumine Gregg Beckham Dan Cosgrove National1 Renewable Energy Laboratory Pennsylvania State University Joseph Bozell Stephen Chmely Linda Broadbelt Roberto Rinaldi Northwestern University Imperial College London Nicole Labbé Kevin Edgar Andy Sutton Timothy Rials Virginia Polytechnic Institute and State Los Alamos National Laboratory Center for Renewable Carbon University The University of Tennessee Hosted By: CONFERENCE SCHEDULE MONDAY NOVEMBER 5, 2018 5:00pm-8:00pm Registration/Social Hour TUESDAY NOVEMBER 6, 2018 6:45am-7:40am Registration/Breakfast Plenary Session: Biorefinery Concepts Session Chair: Timothy Rials (The University of Tennessee) 7:45-8:00 Timothy Rials (The University of Tennessee) Welcome and Opening Remarks 8:00-8:40 Wilfred Vermerris (University of Florida) Genetic enhancement of bioenergy crops to support the bio-economy in the southeastern United States 8:40-9:20 Brigitte Chabbert (FARE laboratory, INRA, Université de Reims Champagne-Ardennes) Multimodal characterization of lignocelluloses in the frame of biofuel production 9:20-10:00 Jeremy Luterbacher (École Polytechnique Fédérale de Lausanne) Protect and serve: acetal formation during biomass fractionation as a toolkit for reducing degradation and introducing new reactivity 10:00am-10:30am Coffee Break 10:30-11:10 Roberto Rinaldi (Imperial College London) Lignin-first -
Structural Characterization of Lignin and Lignin-Carbohydrate Complex (LCC) from Ginkgo Shells (Ginkgo Biloba L.) by Comprehensive NMR Spectroscopy
polymers Article Structural Characterization of Lignin and Lignin-Carbohydrate Complex (LCC) from Ginkgo Shells (Ginkgo biloba L.) by Comprehensive NMR Spectroscopy Bo Jiang 1, Yu Zhang 1, Tianyu Guo 1, Huifang Zhao 1,2 and Yongcan Jin 1,* 1 Jiangsu Co-Innovation Center of Efficient Processing and Utilization of Forest Resources, Nanjing Forestry University, Nanjing 210037, China; [email protected] (B.J.); [email protected] (Y.Z.); [email protected] (T.G.); [email protected] (H.Z.) 2 Institute of Botany, Jiangsu Province and the Chinese Academy of Sciences, Nanjing 210014, China * Correspondence: [email protected]; Tel.: +86-025-8542-8163 Received: 13 June 2018; Accepted: 2 July 2018; Published: 4 July 2018 Abstract: Lignin and lignin-carbohydrate complexes are important polymers for lignocellulosic biorefinery and functional materials, but those in ginkgo shells are not effectively analyzed and exploited. Based on this background, milled wood lignins (MWLML and MWLFZ) and lignin- carbohydrate complexes (LCCML and LCCFZ) were isolated from the shells of Ginkgo biloba L. cv. Damaling (ML) and Ginkgo biloba L. cv. Dafozhi (FZ) correspondingly, and were structurally characterized by comprehensive NMR spectroscopy. The results showed that ginkgo shells exhibited higher lignin (42%) and xylan (20%) content than general softwood species. Isolated MWLs were rich in guaiacyl units with the presence of ferulates and p-coumarates, and the molecular formula was C9H7.93O2.73(OCH3)0.81 and C9H7.87O2.76(OCH3)0.88 for MWLML and MWLFZ, respectively. Phenolic hydroxyl of MWLML (1.38 mmol/g) and MWLFZ (1.23 mmol/g) in ginkgo shells was much less than that in general softwoods, suggesting a higher etherification and condensation degree of ginkgo shells lignin, and b-50, a-O-40, and 4-O-50 bonds were the main condensed structures. -
Effects of Hydrothermal Depolymerization and Enzymatic Hydrolysis of Algae Biomass on Yield of Methane Fermentation Process
Pol. J. Environ. Stud. Vol. 21, No. 2 (2012), 363-368 Original Research Effects of Hydrothermal Depolymerization and Enzymatic Hydrolysis of Algae Biomass on Yield of Methane Fermentation Process Anna Grala*, Marcin Zieliński, Marcin Dębowski, Magda Dudek Department of Environmental Protection Engineering, University of Warmia and Mazury in Olsztyn, Prawocheńskiego 1, 10-957 Olsztyn, Poland Received: 7 March 2011 Accepted: 23 August 2011 Abstract Our study was undertaken in order to determine the effects of preliminary hydrothermal depolymeriza- tion and enzymatic hydrolysis of macroalgae biomass originating from the Vistula Lagoon on yield of the methane fermentation process in terms of quantity and quality of produced biogas. The process of enzymatic hydrolysis was conducted with a mixture of enzymes: Cellulast 1.5 L, Novozym 188, and Hemicellulase. In turn, the process of hydrothermal depolymerization was run for 120 minutes at 200ºC under a pressure of 1.7 MPa. The processed plant substrate was next subjected to mesophilic fermentation. The application of enzy- matic hydrolysis contributed to an increased quantity of and improved qualitative composition of biogas pro- duced. Keywords: algae biomass, methane fermentation, enzymatic hydrolysis, hydrothermal depolymeriza- tion, biogas Introduction aquatic plants biomass from open water bodies enables us to accomplishing two objectives: the first linked directly Biological conversion of biomass to biogas in recent with the acquisition of energetic raw material, and the sec- years has become a popular research topic. Researchers ond with minimization of the eutrophication process. have studied the production of methane in almost 100 types Algae is a large and diverse group of simple autotroph- of fruits and vegetables, solid waste, leaves, trees, weeds, ic organisms, from unicellular to multicellular forms [3]. -
Lignin Transformation and Characterization of Pyrolytic Products Eric Amo Boakye South Dakota State University
South Dakota State University Open PRAIRIE: Open Public Research Access Institutional Repository and Information Exchange Theses and Dissertations 2017 Lignin Transformation and Characterization of Pyrolytic Products Eric Amo Boakye South Dakota State University Follow this and additional works at: http://openprairie.sdstate.edu/etd Part of the Chemistry Commons Recommended Citation Boakye, Eric Amo, "Lignin Transformation and Characterization of Pyrolytic Products" (2017). Theses and Dissertations. 1185. http://openprairie.sdstate.edu/etd/1185 This Dissertation - Open Access is brought to you for free and open access by Open PRAIRIE: Open Public Research Access Institutional Repository and Information Exchange. It has been accepted for inclusion in Theses and Dissertations by an authorized administrator of Open PRAIRIE: Open Public Research Access Institutional Repository and Information Exchange. For more information, please contact [email protected]. i LIGNIN TRANSFORMATION AND CHARACTERIZATION OF PYROLYTIC PRODUCTS BY ERIC AMO BOAKYE A dissertation submitted in partial fulfilment of the requirement for the Doctor of Philosophy Major in Chemistry South Dakota State University 2017 iii AKNOWLEDGEMENTS My sincere gratitude to my advisor, Dr. Douglas Raynie for his continuous encouragement, support, and selfless and faithful guidance offered to me throughout my entire time in graduate school. Many thanks also go to my committee members for their uncommon guidance and directions. To my green chemistry lab members, my friends, and all the people at SDSU who made my stay here a very memorable one. Thank you to all of you for your constant support. Thank you to Doctors Wei, Zhang, Gu and all your students for opening your labs to me all the time. -
Lignin–Carbohydrate Complexes: Properties, Applications, Analyses, and Methods of Extraction: a Review Dmitry Tarasov1,2, Mathew Leitch2 and Pedram Fatehi1*
Tarasov et al. Biotechnol Biofuels (2018) 11:269 https://doi.org/10.1186/s13068-018-1262-1 Biotechnology for Biofuels REVIEW Open Access Lignin–carbohydrate complexes: properties, applications, analyses, and methods of extraction: a review Dmitry Tarasov1,2, Mathew Leitch2 and Pedram Fatehi1* Abstract The complexity of lignin and hemicellulose segmentation has been known since the middle of the ninetieth century. Studies confrmed that all lignin units in coniferous species and 47–66% of lignin moieties in deciduous species are bound to hemicelluloses or cellulose molecules in lignin–carbohydrate complexes (LCC). Diferent types and propor- tions of lignin and polysaccharides present in biomass lead to the formation of LCC with a great variety of composi- tions and structures. The nature and amount of LCC linkages and lignin substructures afect the efciency of pulping, hydrolysis, and digestibility of biomass. This review paper discusses the structures, compositions, and properties of LCC present in biomass and in the products obtained via pretreating biomass. Methods for extracting, fractionating, and analyzing LCC of biomass, pulp, and spent pulping liquors are critically reviewed. The main perspectives and chal- lenges associated with these technologies are extensively discussed. LCC could be extracted from biomass follow- ing varied methods, among which dimethyl sulfoxide or dioxane (Björkman’s) and acetic acid (LCC-AcOH) processes are the most widely applied. The oxidation and methylation treatments of LCC materials elucidate the locations and frequency of binding sites of hemicelluloses to lignin. The two-dimensional nuclear magnetic resonance analysis allows the identifcation of the structure and the quantity of lignin–carbohydrate bonds involved in LCC. -
Renewable Bioplastics and Biocomposites from Biogas
Renewable Bioplastics and Biocomposites From Biogas Methane and Waste-Derived Feedstock: Development of Enabling Technology, Life Cycle Assessment, and Analysis of Costs California Department of Resources Recycling and Recovery August 2014 Contractor's Report Produced Under Contract By: Craig S. Criddle Sarah L. Billington Department of Civil and Environmental Engineering Stanford University Curtis W. Frank Department of Chemical Engineering Stanford University S T A T E O F C ALIFORNIA Edmund G. Brown Jr. Governor Matt Rodriquez Secretary, California Environmental Protection Agency DEPARTMENT OF RESOURCES RECYCLING AND RECOVERY Caroll Mortensen Director Department of Resources Recycling and Recovery Public Affairs Office 1001 I Street (MS 22-B) P.O. Box 4025 Sacramento, CA 95812-4025 www.calrecycle.ca.gov/Publications/ 1-800-RECYCLE (California only) or (916) 341-6300 Publication # DRRR-2014-1502 To conserve resources and reduce waste, CalRecycle reports are produced in electronic format only. If printing copies of this document, please consider use of recycled paper containing 100 percent postconsumer fiber and, where possible, please print images on both sides of the paper. Copyright © 2014 by the California Department of Resources Recycling and Recovery (CalRecycle). All rights reserved. This publication, or parts thereof, may not be reproduced in any form without permission. Prepared as part of contract number DRRR10020 / $1,874,328. The California Department of Resources Recycling and Recovery (CalRecycle) does not discriminate on the basis of disability in access to its programs. CalRecycle publications are available in accessible formats upon request by calling the Public Affairs Office at (916) 341-6300. Persons with hearing impairments can reach CalRecycle through the California Relay Service, 1-800-735-2929.