WHAM: a Simplified Energy Consumption for Water Heaters
Total Page:16
File Type:pdf, Size:1020Kb
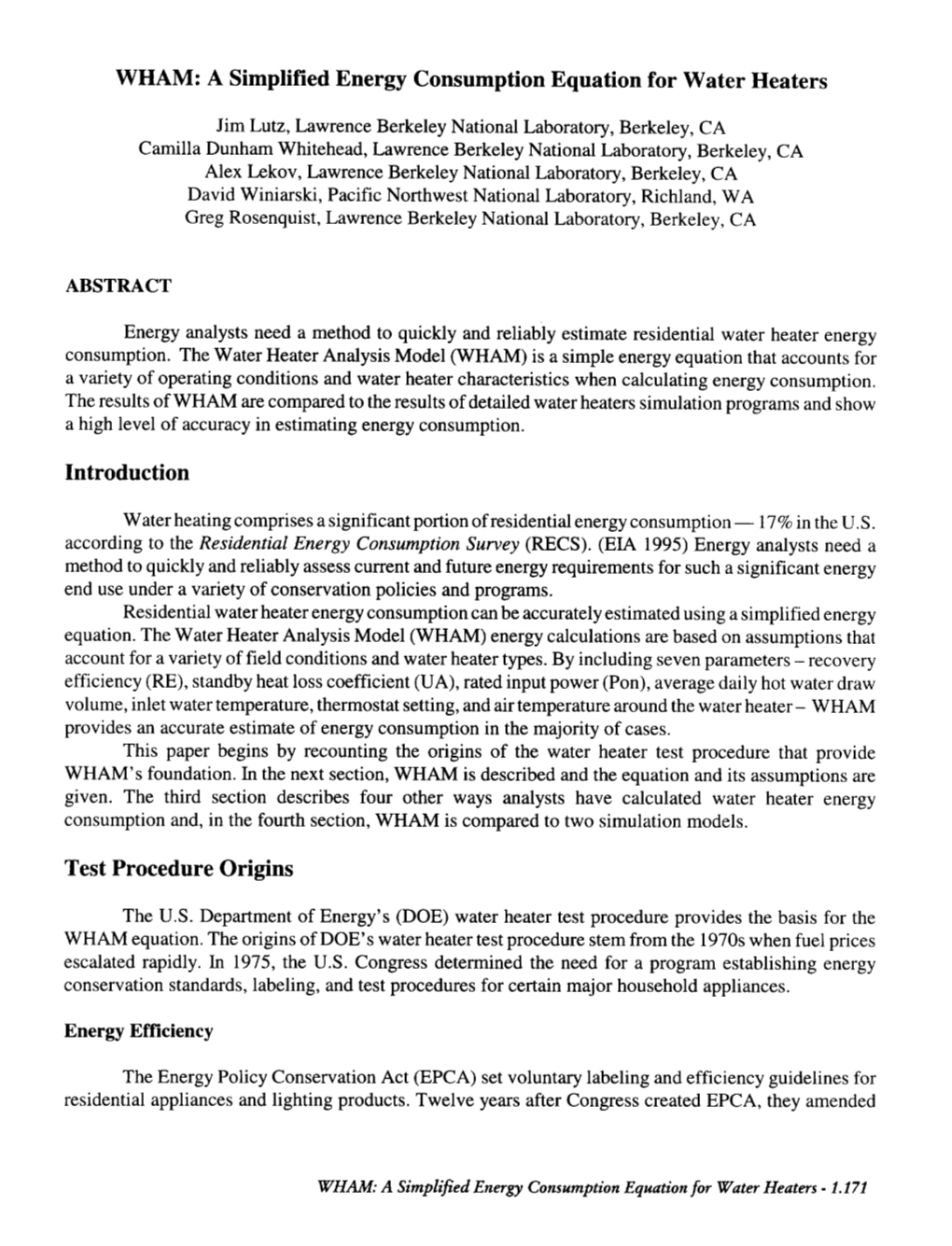
Load more
Recommended publications
-
GRID-INTERACTIVE EFFICIENT BUILDINGS TECHNICAL REPORT SERIES: Overview of Research Challenges and Gaps
Grid-interactive Efficient Buildings Technical Report Series Overview of Research Challenges and Gaps December 2019 (This page intentionally left blank) GRID-INTERACTIVE EFFICIENT BUILDINGS TECHNICAL REPORT SERIES: Overview of Research Challenges and Gaps Disclaimer This report was prepared as an account of work sponsored by an agency of the United States Government. Neither the United States Government, nor any agency thereof, nor any of their employees, nor any of their contractors, subcontractors, or their employees, makes any warranty, express or implied, or assumes any legal liability or responsibility for the accuracy, completeness, or usefulness of any information, apparatus, product, or process disclosed, or represents that its use would not infringe privately owned rights. Reference herein to any specific commercial product, process, or service by trade name, trademark, manufacturer, or otherwise, does not necessarily constitute or imply its endorsement, recommendation, or favoring by the United States Government or any agency, contractor, or subcontractor thereof. The views and opinions of authors expressed herein do not necessarily state or reflect those of the United States Government or any agency thereof. iii GRID-INTERACTIVE EFFICIENT BUILDINGS TECHNICAL REPORT SERIES: Overview of Research Challenges and Gaps Authors The authors of this report are: Monica Neukomm, U.S. Department of Energy (DOE) Valerie Nubbe, Navigant Consulting, Inc. Robert Fares, former American Association for the Advancement of Science (AAAS) fellow at DOE Acknowledgments The authors would like to acknowledge the valuable guidance and input provided during the preparation of this report. The authors are also grateful to the following list of contributors. Their feedback, guidance, and review proved invaluable in preparing this report. -
Heat Transfer in Flat-Plate Solar Air-Heating Collectors
Advanced Computational Methods in Heat Transfer VI, C.A. Brebbia & B. Sunden (Editors) © 2000 WIT Press, www.witpress.com, ISBN 1-85312-818-X Heat transfer in flat-plate solar air-heating collectors Y. Nassar & E. Sergievsky Abstract All energy systems involve processes of heat transfer. Solar energy is obviously a field where heat transfer plays crucial role. Solar collector represents a heat exchanger, in which receive solar radiation, transform it to heat and transfer this heat to the working fluid in the collector's channel The radiation and convection heat transfer processes inside the collectors depend on the temperatures of the collector components and on the hydrodynamic characteristics of the working fluid. Economically, solar energy systems are at best marginal in most cases. In order to realize the potential of solar energy, a combination of better design and performance and of environmental considerations would be necessary. This paper describes the thermal behavior of several types of flat-plate solar air-heating collectors. 1 Introduction Nowadays the problem of utilization of solar energy is very important. By economic estimations, for the regions of annual incident solar radiation not less than 4300 MJ/m^ pear a year (i.e. lower 60 latitude), it will be possible to cover - by using an effective flat-plate solar collector- up to 25% energy demand in hot water supply systems and up to 75% in space heating systems. Solar collector is the main element of any thermal solar system. Besides of large number of scientific publications, on the problem of solar energy utilization, for today there is no common satisfactory technique to evaluate the thermal behaviors of solar systems, especially the local characteristics of the solar collector. -
Heat Transfer (Heat and Thermodynamics)
Heat Transfer (Heat and Thermodynamics) Wasif Zia, Sohaib Shamim and Muhammad Sabieh Anwar LUMS School of Science and Engineering August 7, 2011 If you put one end of a spoon on the stove and wait for a while, your nger tips start feeling the burn. So how do you explain this simple observation in terms of physics? Heat is generally considered to be thermal energy in transit, owing between two objects that are kept at di erent temperatures. Thermodynamics is mainly con- cerned with objects in a state of equilibrium, while the subject of heat transfer probes matter in a state of disequilibrium. Heat transfer is a beautiful and astound- ingly rich subject. For example, heat transfer is inextricably linked with atomic and molecular vibrations; marrying thermal physics with solid state physics|the study of the structure of matter. We all know that owing matter (such as air) in contact with a heated object can help `carry the heat away'. The motion of the uid, its turbulence, the ow pattern and the shape, size and surface of the object can have a pronounced e ect on how heat is transferred. These heat ow mechanisms are also an essential part of our ventilation and air conditioning mechanisms, adding comfort to our lives. Importantly, without heat exchange in power plants it is impossible to think of any power generation, without heat transfer the internal combustion engine could not drive our automobiles and without it, we would not be able to use our computer for long and do lengthy experiments (like this one!), without overheating and frying our electronics. -
(CFD) Modelling and Application for Sterilization of Foods: a Review
processes Review Computational Fluid Dynamics (CFD) Modelling and Application for Sterilization of Foods: A Review Hyeon Woo Park and Won Byong Yoon * ID Department of Food Science and Biotechnology, College of Agricultural and Life Science, Kangwon National University, Chuncheon 24341, Korea; [email protected] * Correspondence: [email protected]; Tel.: +82-33-250-6459 Received: 30 March 2018; Accepted: 23 May 2018; Published: 24 May 2018 Abstract: Computational fluid dynamics (CFD) is a powerful tool to model fluid flow motions for momentum, mass and energy transfer. CFD has been widely used to simulate the flow pattern and temperature distribution during the thermal processing of foods. This paper discusses the background of the thermal processing of food, and the fundamentals in developing CFD models. The constitution of simulation models is provided to enable the design of effective and efficient CFD modeling. An overview of the current CFD modeling studies of thermal processing in solid, liquid, and liquid-solid mixtures is also provided. Some limitations and unrealistic assumptions faced by CFD modelers are also discussed. Keywords: computational fluid dynamics; CFD; thermal processing; sterilization; computer simulation 1. Introduction In the food industry, thermal processing, including sterilization and pasteurization, is defined as the process by which there is the application of heat to a food product in a container, in an effort to guarantee food safety, and extend the shelf-life of processed foods [1]. Thermal processing is the most widely used preservation technology to safely produce long shelf-lives in many kinds of food, such as fruits, vegetables, milk, fish, meat and poultry, which would otherwise be quite perishable. -
Recent Developments in Heat Transfer Fluids Used for Solar
enewa f R bl o e ls E a n t e n r e g Journal of y m a a n d d n u A Srivastva et al., J Fundam Renewable Energy Appl 2015, 5:6 F p f p Fundamentals of Renewable Energy o l i l ISSN: 2090-4541c a a n t r i DOI: 10.4172/2090-4541.1000189 o u n o s J and Applications Review Article Open Access Recent Developments in Heat Transfer Fluids Used for Solar Thermal Energy Applications Umish Srivastva1*, RK Malhotra2 and SC Kaushik3 1Indian Oil Corporation Limited, RandD Centre, Faridabad, Haryana, India 2MREI, Faridabad, Haryana, India 3Indian Institute of Technology Delhi, New Delhi, India Abstract Solar thermal collectors are emerging as a prime mode of harnessing the solar radiations for generation of alternate energy. Heat transfer fluids (HTFs) are employed for transferring and utilizing the solar heat collected via solar thermal energy collectors. Solar thermal collectors are commonly categorized into low temperature collectors, medium temperature collectors and high temperature collectors. Low temperature solar collectors use phase changing refrigerants and water as heat transfer fluids. Degrading water quality in certain geographic locations and high freezing point is hampering its suitability and hence use of water-glycol mixtures as well as water-based nano fluids are gaining momentum in low temperature solar collector applications. Hydrocarbons like propane, pentane and butane are also used as refrigerants in many cases. HTFs used in medium temperature solar collectors include water, water- glycol mixtures – the emerging “green glycol” i.e., trimethylene glycol and also a whole range of naturally occurring hydrocarbon oils in various compositions such as aromatic oils, naphthenic oils and paraffinic oils in their increasing order of operating temperatures. -
Solar Water Heating with Low-Cost Plastic Systems
FEDERAL ENERGY MANAGEMENT PROGRAM Two U.S.-manufactured low-cost plastic packaged systems are now available, including the SunCache system (above left) and the FAFCO system (above right). The manufacturers use plastic materials that reduce production and installation costs. Photos from Harpiris Energy and FAFCO Solar Water Heating with Low-Cost Plastic Systems Newly developed solar water heating technology can help Federal agencies more affordably meet the EISA requirements for solar water heating in new construction and major renovations. Federal buildings consumed over 392,000 billion Btu of site- is reasonably comparable, and these systems are capable delivered energy for buildings during FY 2007 at a total cost of meeting the statutory requirements of 30% solar power of $6.5 billion.[1] Earlier data indicate that about 10% of this efficiently and cost-effectively. is used to heat water.[2] Targeting energy consumption in Federal buildings, the Overcoming the Cost Barrier Energy Independence and Security Act of 2007 (EISA) Benefits and applications of solar water heating are well- requires new Federal buildings and major renovations to meet known, and have been covered in many publications found 30% of their hot water demand with solar energy, provided in the references. However, the single biggest market barrier it is cost-effective over the life of the system. In October for solar water heaters is cost. For single-family systems with 2009, President Obama expanded the energy reduction national-average water draw, paybacks with conventional and performance requirements of EISA and its subsequent solar water heaters often exceed expected system life of regulations with his Executive Order 13514. -
Convectional Heat Transfer from Heated Wires Sigurds Arajs Iowa State College
Iowa State University Capstones, Theses and Retrospective Theses and Dissertations Dissertations 1957 Convectional heat transfer from heated wires Sigurds Arajs Iowa State College Follow this and additional works at: https://lib.dr.iastate.edu/rtd Part of the Physics Commons Recommended Citation Arajs, Sigurds, "Convectional heat transfer from heated wires " (1957). Retrospective Theses and Dissertations. 1934. https://lib.dr.iastate.edu/rtd/1934 This Dissertation is brought to you for free and open access by the Iowa State University Capstones, Theses and Dissertations at Iowa State University Digital Repository. It has been accepted for inclusion in Retrospective Theses and Dissertations by an authorized administrator of Iowa State University Digital Repository. For more information, please contact [email protected]. CONVECTIONAL BEAT TRANSFER FROM HEATED WIRES by Sigurds Arajs A Dissertation Submitted to the Graduate Faculty in Partial Fulfillment of The Requirements for the Degree of DOCTOR 01'' PHILOSOPHY Major Subject: Physics Signature was redacted for privacy. In Chapge of K or Work Signature was redacted for privacy. Head of Major Department Signature was redacted for privacy. Dean of Graduate College Iowa State College 1957 ii TABLE OF CONTENTS Page I. INTRODUCTION 1 II. THEORETICAL CONSIDERATIONS 3 A. Basic Principles of Heat Transfer in Fluids 3 B. Heat Transfer by Convection from Horizontal Cylinders 10 C. Influence of Electric Field on Heat Transfer from Horizontal Cylinders 17 D. Senftleben's Method for Determination of X , cp and ^ 22 III. APPARATUS 28 IV. PROCEDURE 36 V. RESULTS 4.0 A. Heat Transfer by Free Convection I4.0 B. Heat Transfer by Electrostrictive Convection 50 C. -
THERMODYNAMICS, HEAT TRANSFER, and FLUID FLOW, Module 3 Fluid Flow Blank Fluid Flow TABLE of CONTENTS
Department of Energy Fundamentals Handbook THERMODYNAMICS, HEAT TRANSFER, AND FLUID FLOW, Module 3 Fluid Flow blank Fluid Flow TABLE OF CONTENTS TABLE OF CONTENTS LIST OF FIGURES .................................................. iv LIST OF TABLES ................................................... v REFERENCES ..................................................... vi OBJECTIVES ..................................................... vii CONTINUITY EQUATION ............................................ 1 Introduction .................................................. 1 Properties of Fluids ............................................. 2 Buoyancy .................................................... 2 Compressibility ................................................ 3 Relationship Between Depth and Pressure ............................. 3 Pascal’s Law .................................................. 7 Control Volume ............................................... 8 Volumetric Flow Rate ........................................... 9 Mass Flow Rate ............................................... 9 Conservation of Mass ........................................... 10 Steady-State Flow ............................................. 10 Continuity Equation ............................................ 11 Summary ................................................... 16 LAMINAR AND TURBULENT FLOW ................................... 17 Flow Regimes ................................................ 17 Laminar Flow ............................................... -
High Efficiency Boiler with Water Heating
High Efficiency Boiler with Water Heating Revolutionary Design High Efficiency Boiler: Works on Almost Any Residential Application Advanced Modulating Controls Ensure High Efficiency Output Available in LP and Natural Gas Built with Corrosion Resistant Stainless Steel Heat Exchanger for Longer Life Equipped with a Highly Innovative Gas Leak Detector Eco-Friendly and Low NOx Combustion System Heat Exchanger Bears the ASME “H” Stamp SCAQMD Rule 1146.2 SCAQMD Rule 1146.2 Save Energy • Save Money • Save Space • Save On Installation A CLOSER LOOk Exhaust Intake Automatic Air Vent DC Turbo Fan Modulating combustion blower Ceramic Fiber Burner The Eco Pre-mixed burner with high combustion efficiency Gas Valve and low NOx emissions Gas Input Fire Tube Heat Exchanger Hi-fin Heat Exchanger - Higher Main Control efficiency - Lower pressure drop - Multiple safety functions Compact storage size Built in dual stage anti-freezing mechanism Out In State of the Art Built-In Out Space Heating Water lines Gas Leak Detector In the event of a gas leak, the leak detector shuts the unit Domestic Hot Water lines down and activates alarm In Circulation Pump for Central Heating Condensate Out Air Pressure Sensor Indirect Fired Water Heater Circulation Pump for High quality stainless steel coil: Indirect Fired Water Heater Minimize calcium deposit Attached storage tank (Endless hot water & maintains Drain line stable temperature) 1. Horizontal Vent Terminations 1. HorizontaVENTl Vent Terminations TERMINATION 2. Vertical Vent Termination 2. Vertical Vent Termination Forced Draft Direct-Vent 2"(50ft), 3"(100ft), PVC, CPVC & PP Customized Temperature Control MULTIFUNCTION Maintain constant temperature with the user CONTROL PANEL friendly Flow Control, Flow Sensor and Heat Capacity Control. -
Forced Convection Heat Transfer Convection Is the Mechanism of Heat Transfer Through a Fluid in the Presence of Bulk Fluid Motion
Forced Convection Heat Transfer Convection is the mechanism of heat transfer through a fluid in the presence of bulk fluid motion. Convection is classified as natural (or free) and forced convection depending on how the fluid motion is initiated. In natural convection, any fluid motion is caused by natural means such as the buoyancy effect, i.e. the rise of warmer fluid and fall the cooler fluid. Whereas in forced convection, the fluid is forced to flow over a surface or in a tube by external means such as a pump or fan. Mechanism of Forced Convection Convection heat transfer is complicated since it involves fluid motion as well as heat conduction. The fluid motion enhances heat transfer (the higher the velocity the higher the heat transfer rate). The rate of convection heat transfer is expressed by Newton’s law of cooling: q hT T W / m 2 conv s Qconv hATs T W The convective heat transfer coefficient h strongly depends on the fluid properties and roughness of the solid surface, and the type of the fluid flow (laminar or turbulent). V∞ V∞ T∞ Zero velocity Qconv at the surface. Qcond Solid hot surface, Ts Fig. 1: Forced convection. It is assumed that the velocity of the fluid is zero at the wall, this assumption is called no‐ slip condition. As a result, the heat transfer from the solid surface to the fluid layer adjacent to the surface is by pure conduction, since the fluid is motionless. Thus, M. Bahrami ENSC 388 (F09) Forced Convection Heat Transfer 1 T T k fluid y qconv qcond k fluid y0 2 y h W / m .K y0 T T s qconv hTs T The convection heat transfer coefficient, in general, varies along the flow direction. -
Low Outgassing of Silicon-Based Coatings on Stainless Steel Surfaces for Vacuum Applications
Low Outgassing of Silicon-Based Coatings on Stainless Steel Surfaces for Vacuum Applications David A. Smith, Martin E. Higgins Restek Corporation, 110 Benner Circle Bellefonte, PA 16823, www.restekcoatings.com Bruce R.F. Kendall Elvac Laboratories 100 Rolling Ridge Drive, Bellefonte, PA 16823 Performance Coatings This presentation was developed through the collaborative efforts of Restek Performance Coatings and Bruce Kendall of Elvac Labs. Restek applied the coatings to vacuum components and Dr. Kendall developed, performed and interpreted the experiments to evaluate the coating performance. lit. cat.# RPC-uhv3 1 Objective Evaluate comparative outgassing properties of vacuum components with and without amorphous silicon coatings Performance Coatings lit. cat.# RPC-uhv3 2 Theoretical Basis – Heat Induced Outgassing • Outgassing rate (F) in monolayers per sec: F = [exp (-E/RT)] / t’ t’ = period of oscillation of molecule perp. to surface, ca. 10-13 sec E = energy of desorption (Kcal/g mol) R = gas constant source: Roth, A. Vacuum Technology, Elsevier Science Publishers, Amsterdam, 2nd ed., p. 177. • Slight elevation of sample temperature accelerates outgassing rate exponentially Performance Coatings The design of the first set of experiments allowed the isolation and direct comparison of outgassing rates with increasing temperature. By applying heat, the outgassing rates are exponentially increased for the purpose of timely data collection. These comparisons with experimental controls will directly illustrate the differences incurred by the applied coatings. lit. cat.# RPC-uhv3 3 Experimental Design – Heated Samples • Turbo pump for base pressures to 10-8 Torr – pumping rate between gauge and pump: 12.5 l/sec (pump alone: 360 l/sec) – system vent with dry N2 between thermal cycles • Comparative evaluation parts – a-silicon coated via CVD (Silcosteel®-UHV); 3D deposition – equally treated controls without deposition Performance Coatings The blue sample (left) was a standard coating commercially available through Restek. -
Connected in Various Ways and Pressure Environment
https://ntrs.nasa.gov/search.jsp?R=19700015462 2020-03-23T19:09:28+00:00Z X-327-69-524 PREPRI NT INTERNAL PRESSURES OF A SPACECRAFT OR OTHER SYSTEM OF COMPARTMENTS, CONNECTED IN VARIOUS WAYS AND INCLUDING OUTGASSING MATERIALS, IN A TIME-VARYING 1 PRESSURE ENVIRONMENT J. I. SCIALDONE / INTERNAL PRESSURES OF A SPACECRAFT OR OTHER SYSTEM OF COMPARmMENTS, CONNECTED IN VARIOUS WAYS &W INCLUDING OUTGASSING MATERIALS, IN A TLME-VARYING PRESSURE ENVIRONMENT John 3. Scialdone Test and Evaluation Division Systems Reliability Directorate August 1969 Goddard Space Flight t errter Greenbelt, Mary1ar.d. INTERNAL PRESSURES OF A SPACECMFT OR QTHER SYSTEM OF COMPARTMENTS, CONNECTED IN VARIOUS WAYS AND INCLUDING OUTGASSING MATERIALS, IN A TIME-VARYING PRESSURE E1'IRONMENT Prepared by: fohn Vcialdone Research and Technology Office Approved by hn H. Boeckel eputy Chief, Test and Evaluation Division PROJECT STATUS This report describes a method for calculating the pressure versus time inside each of a system of volumes containing outgassing materials. Authorization Test and Evaluation Charge No. 327-124-12-06-01 iii PRECEDlNG PAGE BLANK NOT FILMED. INTERNAL PRESSURES OF A SPACECRAFT OR OTFIER SYSTEM OF CBMPAR?%lEN'I'S, CONNECTED IN VARIOUS WAYS AND INCLUDING OUTGASSING MATERIAIS, IN A TIME-VARYING PRESSURE ENVIRONMENT John J. Scidd~ne Test and Evaluatim Division SUMMARY A method od calculating the pressure profile for eac:h com- partment of a multi-compartment system such as a spacecraft is presented. Thc method is applicable to volumes connected in series or in parallel or bothby passages of various sizes and geometries, where each volume may include several materials outgassing ac- cox~dingto known or assumed characteristics.