LM5-Valve Gear and Motion
Total Page:16
File Type:pdf, Size:1020Kb
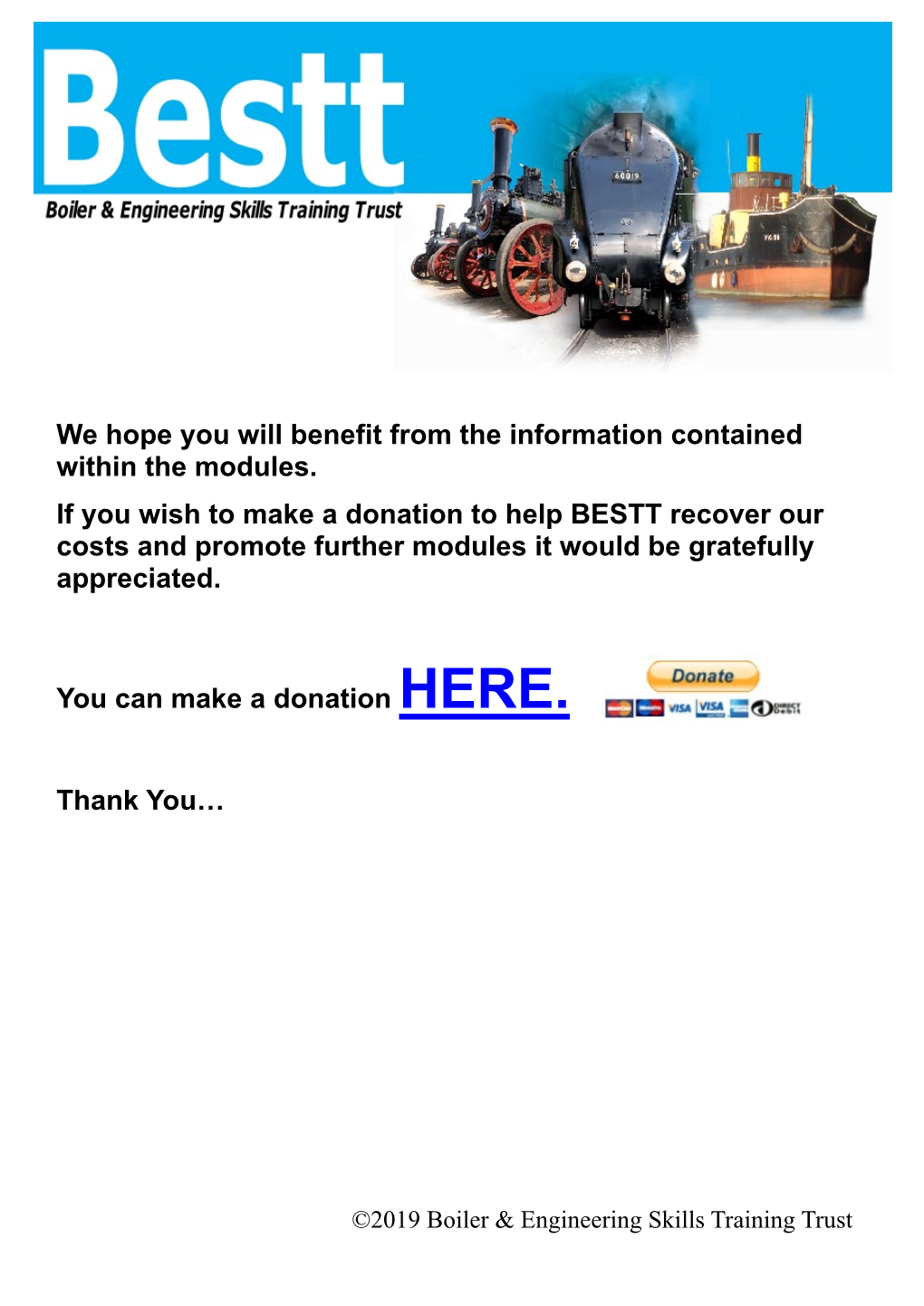
Load more
Recommended publications
-
Engine Components and Filters: Damage Profiles, Probable Causes and Prevention
ENGINE COMPONENTS AND FILTERS: DAMAGE PROFILES, PROBABLE CAUSES AND PREVENTION Technical Information AFTERMARKET Contents 1 Introduction 5 2 General topics 6 2.1 Engine wear caused by contamination 6 2.2 Fuel flooding 8 2.3 Hydraulic lock 10 2.4 Increased oil consumption 12 3 Top of the piston and piston ring belt 14 3.1 Hole burned through the top of the piston in gasoline and diesel engines 14 3.2 Melting at the top of the piston and the top land of a gasoline engine 16 3.3 Melting at the top of the piston and the top land of a diesel engine 18 3.4 Broken piston ring lands 20 3.5 Valve impacts at the top of the piston and piston hammering at the cylinder head 22 3.6 Cracks in the top of the piston 24 4 Piston skirt 26 4.1 Piston seizure on the thrust and opposite side (piston skirt area only) 26 4.2 Piston seizure on one side of the piston skirt 27 4.3 Diagonal piston seizure next to the pin bore 28 4.4 Asymmetrical wear pattern on the piston skirt 30 4.5 Piston seizure in the lower piston skirt area only 31 4.6 Heavy wear at the piston skirt with a rough, matte surface 32 4.7 Wear marks on one side of the piston skirt 33 5 Support – piston pin bushing 34 5.1 Seizure in the pin bore 34 5.2 Cratered piston wall in the pin boss area 35 6 Piston rings 36 6.1 Piston rings with burn marks and seizure marks on the 36 piston skirt 6.2 Damage to the ring belt due to fractured piston rings 37 6.3 Heavy wear of the piston ring grooves and piston rings 38 6.4 Heavy radial wear of the piston rings 39 7 Cylinder liners 40 7.1 Pitting on the outer -
Walschaerts Valve-Gear 2 Return Cranks with Steel Screws & Nuts
This pack contains the following parts: - Walschaerts Valve-Gear 2 Return Cranks with steel screws & nuts. 2 Expansion links with bushes & This kit contains parts to construct 2BA nuts. a set of Walschaerts type valve- 2 Lifting arms with grub screws & Allen key. gear as used on ROUNDHOUSE 2 Lifting links. locomotives. It is of a simplified 4 M2 steel screws & nuts. design, which does not use a 6 5BA steel washers. combination lever and is intended 2 Radius rods. for use with the ROUNDHOUSE 2 Weigh shaft brackets 1 Weigh shaft. Cylinder set. 2 Starlock washers 2 Roll pins. NOTE:- Frames, Cylinders, 6 Short crank pins. Coupling Rods, Connecting Rods, 2 Plain crank pins Axles and Outside Cranks are not included with this set of parts. 1 Push Rod Connector, Screw & Starlock. 1 Stainless Steel spring & Long Crank Pin. 1 Reversing lever handle. 1 Reversing lever base. 3 M2 screws and nuts. 2 M3 mounting screws. 1 Steel push rod & quicklink connector. Roundhouse Engineering Co. Ltd 2 Eccentric rods. Units 6 to 9, Churchill Business Park, Churchill Road, Wheatley, Doncaster. DN1 2TF. England. Tel 01302 328035 Fax 01302 761312 Email: [email protected] www.roundhouse-eng.com 1 Walschaerts Valve-Gear Part Number WVG Assembly of Walschaerts type valve-gear 1). Radius Rod. 2). Lifting Link. 3). Lifting Arm. Diagram4). Expansion showing Linkgeneral Bush. arrangement 5). Weigh of Walschaerts Shaft Bracket valve (Penguin). gear. NOTE:- Frames, Coupling rods, connecting rods and outside cranks are not included6). Weigh with this Shaft. set of 7). parts. Starlock Washer. 8). 2BA Nut. -
Overview of Materials Used for the Basic Elements of Hydraulic Actuators and Sealing Systems and Their Surfaces Modification Methods
materials Review Overview of Materials Used for the Basic Elements of Hydraulic Actuators and Sealing Systems and Their Surfaces Modification Methods Justyna Skowro ´nska* , Andrzej Kosucki and Łukasz Stawi ´nski Institute of Machine Tools and Production Engineering, Lodz University of Technology, ul. Stefanowskiego 1/15, 90-924 Lodz, Poland; [email protected] (A.K.); [email protected] (Ł.S.) * Correspondence: [email protected] Abstract: The article is an overview of various materials used in power hydraulics for basic hydraulic actuators components such as cylinders, cylinder caps, pistons, piston rods, glands, and sealing systems. The aim of this review is to systematize the state of the art in the field of materials and surface modification methods used in the production of actuators. The paper discusses the requirements for the elements of actuators and analyzes the existing literature in terms of appearing failures and damages. The most frequently applied materials used in power hydraulics are described, and various surface modifications of the discussed elements, which are aimed at improving the operating parameters of actuators, are presented. The most frequently used materials for actuators elements are iron alloys. However, due to rising ecological requirements, there is a tendency to looking for modern replacements to obtain the same or even better mechanical or tribological parameters. Sealing systems are manufactured mainly from thermoplastic or elastomeric polymers, which are characterized by Citation: Skowro´nska,J.; Kosucki, low friction and ensure the best possible interaction of seals with the cooperating element. In the A.; Stawi´nski,Ł. Overview of field of surface modification, among others, the issue of chromium plating of piston rods has been Materials Used for the Basic Elements discussed, which, due, to the toxicity of hexavalent chromium, should be replaced by other methods of Hydraulic Actuators and Sealing of improving surface properties. -
Assessing Steam Locomotive Dynamics and Running Safety by Computer Simulation
TRANSPORT PROBLEMS 2015 PROBLEMY TRANSPORTU Volume 10 Special Edition steam locomotive; balancing; reciprocating; hammer blow; rolling stock and track interaction Dāvis BUŠS Institute of Transportation, Riga Technical University Indriķa iela 8a, Rīga, LV-1004, Latvia Corresponding author. E-mail: [email protected] ASSESSING STEAM LOCOMOTIVE DYNAMICS AND RUNNING SAFETY BY COMPUTER SIMULATION Summary. Steam locomotives are preserved on heritage railways and also occasionally used on mainline heritage trips, but since they are only partially balanced reciprocating piston engines, damage is made to the railway track by dynamic impact, also known as hammer blow. While causing a faster deterioration to the track on heritage railways, the steam locomotive may also cause deterioration to busy mainline tracks or tracks used by high speed trains. This raises the question whether heritage operations on mainline can be done safely and without influencing the operation of the railways. If the details of the dynamic interaction of the steam locomotive's components are examined with computerised calculations they show differences with the previous theories as the smaller components cannot be disregarded in some vibration modes. A particular narrow gauge steam locomotive Gr-319 was analyzed and it was found, that the locomotive exhibits large dynamic forces on the track, much larger than those given by design data, and the safety of the ride is impaired. Large unbalanced vibrations were found, affecting not only the fatigue resistance of the locomotive, but also influencing the crew and passengers in the train consist. Developed model and simulations were used to check several possible parameter variations of the locomotive, but the problems were found to be in the original design such that no serious improvements can be done in the space available for the running gear and therefore the running speed of the locomotive should be limited to reduce its impact upon the track. -
Heyside Signals and Locomotives Three Etched Brass Footbridge Kits
The Lancashire & Yorkshire Railway Society The Lancashire & Yorkshire Railway Society sections; Cynric did the CAD work, and a short while later, I was presented with Heyside signals and locomotives three etched brass footbridge kits. Since the article on the 7mm scale layout Heyside in Magazine 251 there have been continuing The footbridge made up exactly as developments, both on the signalling side and in additions to the locomotive fleet, as its owner intended, fitting the space perfectly, RICHARD LAMBERT, who also took the layout photographs, explains… and providing a sound base to mount the signals. The signals themselves are made from wood, with etched and cast components from Scale Signal Supply for the fittings. The decking was made of copper-clad strip, stanchions from nickel- coated brass lace pins and the various brackets and smoke shields from brass sheet. The operating wire is 0.4mm nickel silver and the operation is by servos mounted under the baseboard. The gantry This was felt to be the signature piece of the layout with five dolls and nine arms. It is based on the gantry outside Victoria East Junction signal box and illustrations in the Society’s Focus on Signalling (No.3). The legs are made of wood, with brass ‘X’ pieces, while the support for the decking is four strips of brass. The decking itself is made from 84 P4 copper-clad sleepers, while the spandrels were commissioned by me from Scale Signal Supply. The dolls and hardware were built as before, but it was in the operation of the signals that most thought had to be given. -
Steamboating Guide Edition 2 2010
Steamboating SampleGuide Pages Second Edition Steamboating Guide Edition 2 2010 Edited by Roger Calvert and Rob van Es The contributors and editors of this publication have made every effort to ensure the accuracy and relevance of the data presented and the validity and appropriateness of the recommendations made. It is, however, ultimately the responsibility of the owner of a boat to check the data and take the final decisions, in the context of the proposed design. If necessary, appropriate professional advice should be sought. Neither the contributors, the editors, nor the SBA can accept responsibility for any direct or indirect consequences arising from the use of the data or from following the recommendationsSample of this publication. Pages Copying of parts or the whole of this document by members of the SBA is permitted, subject to the terms published on the SBA web site. Otherwise, copying is not permitted without the permission of the SBA, except as allowed under copyright law. Table of Contents Preface Section A – Introduction 1 Hulls 1-1 2 Boiler Types 2-1 3 Engine Types 3-1 4 Fuels 4-1 Section B – Steamboat Operations 5 Boiler Fittings 5-1 6 Steam Plant Installation 6-1 7 Boiler Operation and Maintenance 7-1 8 Steam Ancillaries 8-1 9 Boat Handling Advice 9-1 10 Boiler Inspection and Testing 10-1 11 Trailers and Towing 11-1 Section C – Technical 12 Propulsion 12-1 13 Valve Setting 13-1 14 Data and Performance 14-1 15 Boiler Design Considerations 15-1 16 Workshop Techniques 16-1 Glossary 17-1 Index 18-1 Sample Pages Preface The aims and objects of the Steam Boat Association are: (i) To foster and encourage steam boating and the building, development, preservation and restoration of steam boats and steam machinery, by all possible means. -
Swampʼs Diesel Performance Tips to Help Remove and Install Power
Injectors-Chips-Clutches-Transmissions-Turbos-Engines-Fuel Systems Swampʼs Diesel Performance Competition Parts For Your Diesel 304-A Sand Hill Rd. La Vergne, TN 37086 Tel 615-793-5573 or (866) 595-8724/ Fax 615-793-5572 Email: [email protected] Tips to help remove and install Power Stroke injectors. Removal: After removing the valve covers and the valve cover gaskets, but before removing any injectors, drain the oil rails by removing the drain plugs inside the valve cover. On 94-97 trucks theyʼre just under where the electrical connectors are on the gasket. These plugs are very tight; give them a sharp blow with a hammer and punch to help break them loose, then use a 1/8" Allen wrench. The oil will drain out into the valve train area and from there into the crankcase. Donʼt drop the plugs down the push rod holes! Also remove one of the plugs on top of each oil rail, (beside where the lines from the High Pressure Oil Pump enter) for a vent to allow air to enter so the oil can drain. The plugs are 5/8”. Inspect the plug O-rings and replace if necessary. If the plugs under the covers leak, it will cause a substantial loss of performance. When removing the injectors, oil and fuel from the passages in the cylinder head drains down through the injector bore into the cylinders. If not removed, this can hydro-lock the engine when cranking. There is a ~40cc dish in the center of each piston. Fluid accumulates in it, as well as in the corner on the outside of the piston between the piston top and the cylinder wall, due to the 45* slope of the cylinder bank. -
See 1912/1913 Bulletin 8-4 (Pdf Images
.· ' ·. _--Series VIII. _' N~mber iv. BlJLLETlN. THE_ -OF . ·-. • • j • • University. - g · of l.\lotre Dame ---_ I\lOTRE . DAME~ II'JDIANA -j : • , : .. -. ·. , , . ( · . ' ·. ! . ·. _.! . i I ' : : ~ : - _.· . .; .· ·. ·- .:. · GENERAL CATALOGUE -. _ __.. ' l9J2·:·J 9J3 - . _- . .. - ·PUBLISHED QUARTERLY AT -NOTRE Dl\.ME '•· :- - _ f. THE U~I"VERSITY PRESS -. , APRIL,. J9'J3 · .-·- Entered. at th~ Postoffice, N~tr ~ Dame~ Indiana, ~s sec~!'ld~das s m attertl tl[y 17, J 90.5 :- ... _, -~ ,- .... UNIVERSITY OF NOTRE DAM E Noire Damn, Imliana Series VIII* Ntmifeer IV* BULLETIN OF THE University of Notre Dame NOTRE DAME, INDIANA GENERAL CATALOGUE 1912-1913 PUBLISHED QUARTERLY AT NOTRE DAME THE UNIVERSITY PRESS APRIL, 1913 Entered at the Postoffice, Notre Dame, Indiana, as second-class m atter, July 17, i 9 0 s 2 BULLETIN OF THE DIRECTORY OF THE UNIVERSITY The FACULTY—Address: THB UNIVERSITY OF NOTRB DAM#, NOTRE DAME, INDIANA. The STUDENTS—Address: As for the Faculty, except that the name of the H a l l in which the student lives should be added. A Postoffice, a Telegraph Office, a Long Distance Tel ephone, and an Bxpress Office are at the University. The University is two miles from the city of South Bend, Indiana, and about eighty miles east of Chicago. The Lake Shore and Michigan Southern, the Grand Trunk, the Vandalia, the Indiana, Illinois & Iowa, the Chicago and Indiana Southern, and the Michigan Cen tral railways run directly into South Bend. A trolley line runs cars from South Bend to the University every fifteen minutes. The Latitude of the University is 41 degrees, 43 minutes, and 12.7 seconds North, and 86 degrees, 14 minutes and 19.3 seconds W est of Greenwich. -
Lima 2-8-0 “Consolidation”, Developed for TS2013, by Smokebox
Union Pacific 4000 Class 4884-1 "Big Boy" circa 1948-49 Developed by Smokebox TM for Dovetail Games' Train Simulator © Smokebox 2021, all rights reserved Issue 1 Union Pacific 4000 Class 4884-1 "Big Boy" Steam Locomotive Page 2 Contents Introduction ....................................................................................................................................................... 7 32- and 64-bit TS ................................................................................................................................................ 7 Expert or Simple Controls mode, HUD and Automatic Fireman ....................................................................... 7 "All-in-one" .................................................................................................................................................... 7 Standard TS Automatic Fireman .................................................................................................................... 8 F4 HUD ........................................................................................................................................................... 8 High Detail (HD) and Standard Detail (SD) ........................................................................................................ 8 Recommended Settings ..................................................................................................................................... 9 Cab Layout ...................................................................................................................................................... -
Station Sign 64” 2 14 Bennet
Boston & Maine Railroad Historical Society Inc. Hardware Collection Tag No. File No: Inventory: Size: Donor: 1 14 West Hollis – Station sign 64” 2 14 Bennett Hall – Station sign 69” Arnold Wilder 3 14 Fitchburg “Wood” Station sign 56” Arnold Wilder 4 14 Woburn “Wood” Station sign 30” Charles Smith 5 14 Danville Junction – Station Sign 96” Anonymous 6 14 West Fitchburg – Station sign 92” Arnold Wilder 7 14 West Hollis – Station sign 72” Arnold Wilder 8 14 Scheghticoke – Station sign 76” Arnold Wilder 9 14 Hubbardston – Station sign 76” Arnold Wilder 10 14 Winchester “Wood” Station sign 68” 11 14 Wedgmere “Wood” Station Sign 56” 12 14 Salem – Station sign 48” 13 14 Whately – Station sign 52”x 11” 14 14 Mt Tom – Station sign 42”x 10 ½” 15 14 Middlesex “Wood” Station sign 54” Carl Byron 16 15 Railway Express Agency - sign 72” 17 15 B&MRR Passenger Waiting Room - sign 32”x 11” 18 15 B&M Outing - sign 23”x 14” 19 15 Yard Limit – sign 16”x 14” 20 15 Notice no Deliveries “Wood” – sign 18”x 24” 21 15 Private Crossing “Plastic” – sign 18”x 6” 22 15 Free Parking “Wood” – sign 24 ½”x 8” 23 15 Railroad Crossing – Sign 36”x 36” 24 15 2 Tracks sign “White /w Black lettering (2 each) 27”x 18” 25 15 Railroad Crossbuck /w reflectors (2 each) 26 14 Lowell Station – sign reproduction Property of the Boston & Maine Railroad Historical Society Boston & Maine Railroad Historical Society Inc. Hardware Collection Tag No. File No: Inventory: Size: Donor: 27 15 Hand Held Stop – sign Donald S. -
The Evolution of the Steam Locomotive, 1803 to 1898 (1899)
> g s J> ° "^ Q as : F7 lA-dh-**^) THE EVOLUTION OF THE STEAM LOCOMOTIVE (1803 to 1898.) BY Q. A. SEKON, Editor of the "Railway Magazine" and "Hallway Year Book, Author of "A History of the Great Western Railway," *•., 4*. SECOND EDITION (Enlarged). £on&on THE RAILWAY PUBLISHING CO., Ltd., 79 and 80, Temple Chambers, Temple Avenue, E.C. 1899. T3 in PKEFACE TO SECOND EDITION. When, ten days ago, the first copy of the " Evolution of the Steam Locomotive" was ready for sale, I did not expect to be called upon to write a preface for a new edition before 240 hours had expired. The author cannot but be gratified to know that the whole of the extremely large first edition was exhausted practically upon publication, and since many would-be readers are still unsupplied, the demand for another edition is pressing. Under these circumstances but slight modifications have been made in the original text, although additional particulars and illustrations have been inserted in the new edition. The new matter relates to the locomotives of the North Staffordshire, London., Tilbury, and Southend, Great Western, and London and North Western Railways. I sincerely thank the many correspondents who, in the few days that have elapsed since the publication: of the "Evolution of the , Steam Locomotive," have so readily assured me of - their hearty appreciation of the book. rj .;! G. A. SEKON. -! January, 1899. PREFACE TO FIRST EDITION. In connection with the marvellous growth of our railway system there is nothing of so paramount importance and interest as the evolution of the locomotive steam engine. -
RED RAVEN, the LINKED-BOGIE PROTOTYPE Ara Mekhtarian, Joseph Horvath, C.T. Lin Department of Mechanical Engineering, California
RED RAVEN, THE LINKED-BOGIE PROTOTYPE Ara Mekhtarian, Joseph Horvath, C.T. Lin Department of Mechanical Engineering, California State University, Northridge California, USA Abstract RedRAVEN is a pioneered autonomous robot utilizing the innovative Linked-Bogie dynamic frame, which minimizes platform tilt and movement, and improves traction while maintaining all the vehicle’s wheels in contact with uneven surfaces at all times. Its unique platform design makes the robot extremely maneuverable since it allows the vehicle’s horizontal center of gravity to line up with the center of its differential-drive axle. Where conventional differential-drive vehicles use one or more caster wheels either in front or in the rear of the driving axle to balance the vehicle’s platform, the Linked-Bogie design utilizes caster wheels both in the front and in the rear of the driving axle. Without using any springs or shock absorbers, the dynamic frame allows for compensation of uneven surfaces by allowing each wheel to move independently. The compact and lightweight ground vehicle also features a driving-wheel neutralizing mechanism, a rigid aluminum frame, and a translucent polycarbonate weatherproofing shell. INTRODUCTION 1. Horizontal Center of Gravity Red RAVEN, the grand award (HCG) winner of the 2011 Intelligent Ground Vehicle (IGV) Competition, is mechanically Unless a differential drive vehicle designed to navigate through an autonomous can balance the weight of its platform on the course fast and efficiently. The Cal State two driving wheels similar to a Segway, an Northridge IGV Team designed the vehicle additional and floating or caster wheel is with the innovative Linked-Bogie dynamic required to support the platform weight.