Influence of the Type of Aggregate from Industrial Waste on Corrosion
Total Page:16
File Type:pdf, Size:1020Kb
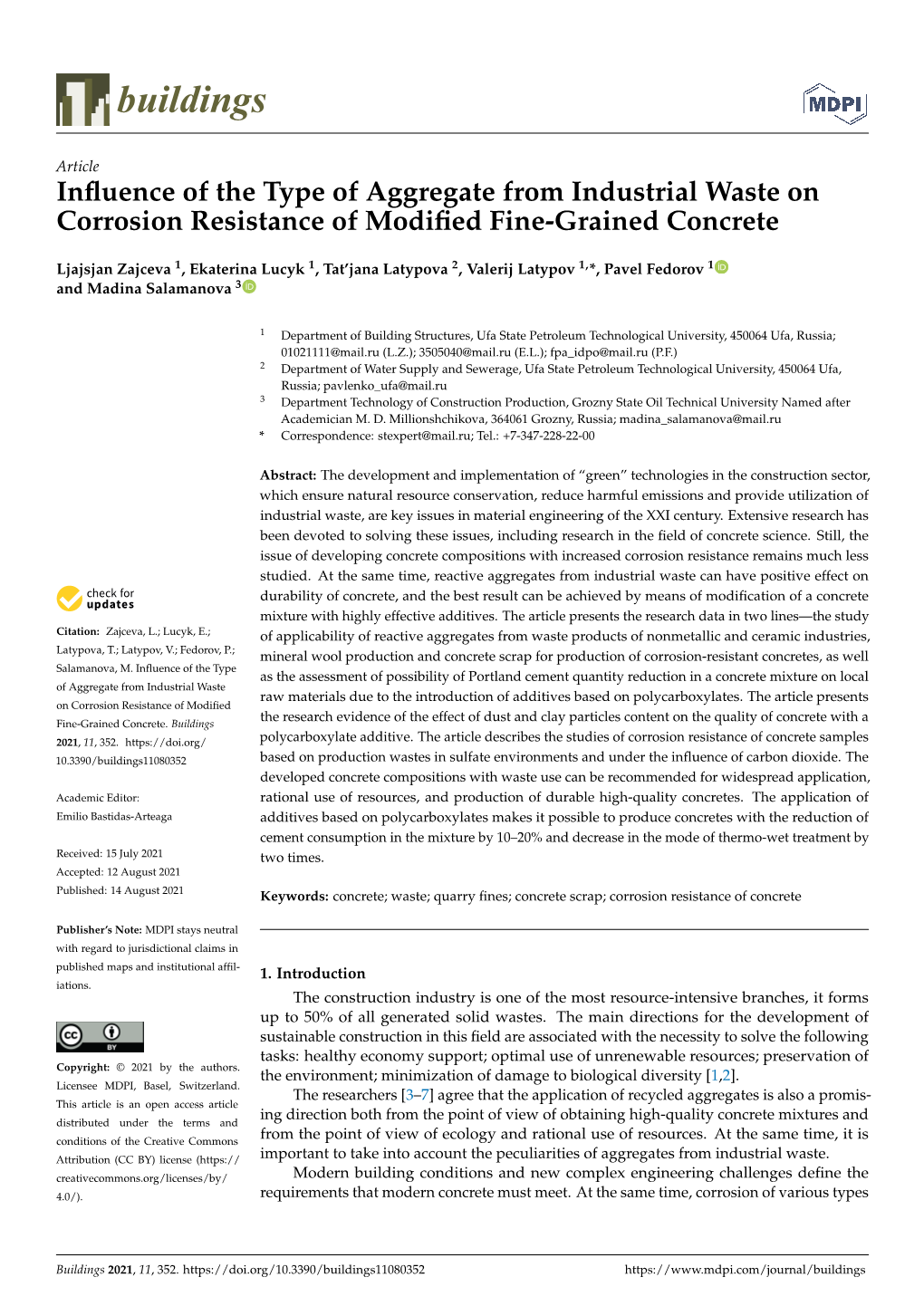
Load more
Recommended publications
-
The Manifest
VOLUME 3 | November 2017 THE MANIFEST I ntegrity - We have a strong moral compass, acting always inline with our core values. We honour our commitments and take ownership of issues. Abu Dhabi Cruise Terminal launches airport check-in Under this agreement Abu Dhabi Airports and the selected airline operators would be introducing on-ground services, including check-in counters that passengers arriving at Abu Dhabi Cruise Terminal can utilize to complete their airline check-in prior to their arrival to Abu Dhabi International Airport. Find out more here bmi Regional / Loganair begins codeshare routes bmi Regional and Loganair have become part of a new regional airline group, under newly appointed Chief Executive, Peter Simpson. The two airlines operate in clear niche markets in vital roles such as feeding traffic to mainline carrier networks like Lufthansa, Brussels Airlines and British Airways, with Loganair operating a successful franchise with major regional carrier Flybe. The code shares now cover: Aberdeen – Durham/Tees Valley Aberdeen – Kirkwall Aberdeen – Sumburgh Benbecula – Stornoway Edinburgh – Kirkwall Edinburgh – Sumburgh Edinburgh – Stornoway Edinburgh – Wick Glasgow – Kirkwall Glasgow – Manchester Glasgow – Stornoway Inverness – Manchester Norwich – Durham/Tees Valley Norwich – Manchester Did you know? We have the ability to provide various bespoke reporting options. To discuss your requirements please email: [email protected] Virgin Cancun Terminal move Virgin Atlantic customers departing from Cancun International Airport will be required to check in at Terminal 4, Zone D offering a enhanced experience for their customers. A brand new lounge will open in Terminal 4 in Spring 2018. Find out more here. Delta Introduces Auto Check-I n for App Users Delta Air Lines has added automatic check-in to the Fly Delta app to streamline the check-in experience for customers and take the guesswork out of accessing a boarding pass. -
Status and Protection of Globally Threatened Species in the Caucasus
STATUS AND PROTECTION OF GLOBALLY THREATENED SPECIES IN THE CAUCASUS CEPF Biodiversity Investments in the Caucasus Hotspot 2004-2009 Edited by Nugzar Zazanashvili and David Mallon Tbilisi 2009 The contents of this book do not necessarily reflect the views or policies of CEPF, WWF, or their sponsoring organizations. Neither the CEPF, WWF nor any other entities thereof, assumes any legal liability or responsibility for the accuracy, completeness, or usefulness of any information, product or process disclosed in this book. Citation: Zazanashvili, N. and Mallon, D. (Editors) 2009. Status and Protection of Globally Threatened Species in the Caucasus. Tbilisi: CEPF, WWF. Contour Ltd., 232 pp. ISBN 978-9941-0-2203-6 Design and printing Contour Ltd. 8, Kargareteli st., 0164 Tbilisi, Georgia December 2009 The Critical Ecosystem Partnership Fund (CEPF) is a joint initiative of l’Agence Française de Développement, Conservation International, the Global Environment Facility, the Government of Japan, the MacArthur Foundation and the World Bank. This book shows the effort of the Caucasus NGOs, experts, scientific institutions and governmental agencies for conserving globally threatened species in the Caucasus: CEPF investments in the region made it possible for the first time to carry out simultaneous assessments of species’ populations at national and regional scales, setting up strategies and developing action plans for their survival, as well as implementation of some urgent conservation measures. Contents Foreword 7 Acknowledgments 8 Introduction CEPF Investment in the Caucasus Hotspot A. W. Tordoff, N. Zazanashvili, M. Bitsadze, K. Manvelyan, E. Askerov, V. Krever, S. Kalem, B. Avcioglu, S. Galstyan and R. Mnatsekanov 9 The Caucasus Hotspot N. -
Download This Article in PDF Format
MATEC Web of Conferences 170, 01131 (2018) https://doi.org/10.1051/matecconf/201817001131 SPbWOSCE-2017 Renovation of industrial territories in single industry towns on the basis of industrial parks Vladimir Filatov1,*, Zhanna Dibrova1, Natalya Zhukova1 1Moscow State University of Technology and Management. K.G. Razumovsky, Zemlyanoy val st., 73, 109004, Moscow, Russia Abstract. The issues of renovation of industrial territories in single industry towns on the basis of industrial parks at the current stage are considered in this paper. The development of a new service industry - industrial parks – has started in Russia less than 10 years ago and gradually acquires a systemic character. However, the gap with the countries of America, Europe and Asia remains very significant. Dozens of new initiatives to create industrial parks of various forms of ownership have appeared in Russia in recent years. However, most areas of Russian industrial parks remain vacant against the backdrop of existing unmet demand for prepared sites and related services for the location of manufacturing plants. One of the main problems of the industry is that the quality of many industrial park projects announced in the country does not meet the requirements of investors - potential residents. 1 Introduction The issues of renovation of industrial territories are highly relevant for many Russian towns. In the conditions of the necessity to search for new drivers for the economic growth of towns, to improve the quality of the urban environment, and to increase the efficiency of the use of urban areas, an important task of finding and elaborating of innovation models for the development of industrial zones arises. -
Information for Persons Who Wish to Seek Asylum in the Russian Federation
INFORMATION FOR PERSONS WHO WISH TO SEEK ASYLUM IN THE RUSSIAN FEDERATION “Everyone has the right to seek and to enjoy in the other countries asylum from persecution”. Article 14 Universal Declaration of Human Rights I. Who is a refugee? According to Article 1 of the Federal Law “On Refugees”, a refugee is: “a person who, owing to well‑founded fear of being persecuted for reasons of race, religion, nationality, membership of particular social group or politi‑ cal opinion, is outside the country of his nationality and is unable or, owing to such fear, is unwilling to avail himself of the protection of that country”. If you consider yourself a refugee, you should apply for Refugee Status in the Russian Federation and obtain protection from the state. If you consider that you may not meet the refugee definition or you have already been rejected for refugee status, but, nevertheless you can not re‑ turn to your country of origin for humanitarian reasons, you have the right to submit an application for Temporary Asylum status, in accordance to the Article 12 of the Federal Law “On refugees”. Humanitarian reasons may con‑ stitute the following: being subjected to tortures, arbitrary deprivation of life and freedom, and access to emergency medical assistance in case of danger‑ ous disease / illness. II. Who is responsible for determining Refugee status? The responsibility for determining refugee status and providing le‑ gal protection as well as protection against forced return to the country of origin lies with the host state. Refugee status determination in the Russian Federation is conducted by the Federal Migration Service (FMS of Russia) through its territorial branches. -
Foreign Relations
Foreign relations STU MTF forms cooperation on the basis of good partnership relations which are typified by mutual cooperation, profit in the area of research activities, or experience in education. The active cooperation of our constitution, reflected in agreements concluded with foreign partners, is proof of the necessity for searching new partnerships and cooperation. Institutes which signed contracts of cooperation with the Faculty: Agreements on cooperation with Foreign Partners Foreign Partner Country City/Town Helmholtz-Zentrum Dresden Germany Rossendorf Technical University of Brandenburg Germany Cottbus Leibniz-Institute for Solid State and Materials Research Dresden Germany Dresden Anhlat University of Applied Sciences Germany Koethen Faculty of Machining, University in Ljubljana Slovenia Ljubljana St. Petersburg State University of Engineering and Electrotechnics Russia Saint-Petersburg Institute of Energy in Moscow Russia Moscow Buehler GmbH Germany Düsseldorf Ukrainian Academy of Engineering and Pedagogy Ukraine Charkov Faculty of Applied Informatics and Robotechnology, UGATU UFA Russia Ufa Faculty of Economics, Management and Finances UGATU UFA Russia Ufa National Institute of R & D for Materials Physics Romania Bucharest Faculty of Physics, University of Bucharest Romania Bucharest University of Science and Technology in Pohang South Korea Pohang Faculty of Organisation and Informatics, University of Zagreb Croatia Zagreb Bekaert Belgium Zwevegem Faculty of Machine Building, Technical University of Cluj-Napoca Romania Cluj-Napoca -
Investment Guide to the Republic of Bashkortostan | Ufa, 2017
MINISTRY OF ECONOMIC DEVELOPMENT OF THE REPUBLIC OF BASHKORTOSTAN Investment Guide to the Republic of Bashkortostan Ufa 2017 Introduction by Rustem Khamitov, Head of the Republic of Bashkortostan 3 Greetings from Dmitriy Chaban, Managing Partner of Deloitte Ufa 4 Address by Oleg Golov, General Director of the Development Corporation of the Republic of Bashkortostan 5 General information about the Republic of Bashkortostan 6 Seven reasons for doing business in the Republic of Bashkortostan 8 Top-priority sectors for development 16 Government support initiatives for investors 20 Fostering innovation 27 Development institutions 32 Summary of statistics on the economic position of the Republic of Bashkortostan 36 Contacts 38 Investment Guide to the Republic of Bashkortostan Introduction by Rustem Khamitov, Head of the Republic of Bashkortostan Dear Friends, Welcome to the Investment Guide to the Republic Federal mechanisms of investment activity development of Bashkortostan! Bashkortostan is among the leading are used extensively. There is effective cooperation with and dynamically developing regions of Russia. Its location Vnesheconombank and the Monocity Development Fund aimed at the intersection of main traffic arteries, abundant resource at diversifying the economy of the single-industry regions potential, well-developed industry and infrastructure, as well of the republic, as well as increasing the investment inflows as highly skilled labor force, attract investors to our region. to them. One significant event of 2016 was the creation of social and economic development areas in such monocities as Belebey In terms of total investment to subjects of the Russian Federation, and Kumertau, where additional business support tools are used. Bashkortostan today remains in the top ten. -
The Situation of Minority Children in Russia
The Situation of Children Belonging to Vulnerable Groups in Russia Alternative Report March 2013 Anti- Discrimination Centre “MEMORIAL” The NGO, Anti-Discrimination Centre “MEMORIAL”, was registered in 2007 and continued work on a number of human rights and anti-discrimination projects previously coordinated by the Charitable Educational Human Rights NGO “MEMORIAL” of St. Petersburg. ADC “Memorial‟s mission is to defend the rights of individuals subject to or at risk of discrimination by providing a proactive response to human rights violations, including legal assistance, human rights education, research, and publications. ADC Memorial‟s strategic goals are the total eradication of discrimination at state level; the adoption of anti- discrimination legislation in Russia; overcoming all forms of racism and nationalism; Human Rights education; and building tolerance among the Russian people. ADC Memorial‟s vision is the recognition of non-discrimination as a precondition for the realization of all the rights of each person. Tel: +7 (812) 317-89-30 E-mail: [email protected] Contributors The report has been prepared by Anti-discrimination Center “Memorial” with editorial direction of Stephania Kulaeva and Olga Abramenko. Anti-discrimination Center “Memorial” would like to thank Simon Papuashvili of International Partnership for Human Rights for his assistance in putting this report together and Ksenia Orlova of ADC “Memorial” for allowing us to use the picture for the cover page. Page 2 of 47 Contents Executive Summary ........................................................................................................................ 4 Summary of Recommendations ..................................................................................................... 7 Overview of the legal and policy initiatives implemented in the reporting period ................. 11 Violations of the rights of children involving law enforcement agencies ............................... -
Kyiv and Vatican Reaffirm That Pope's Visit Is on Track Kuchma Dismisses
INSIDE:• Ukraine and Russia sign pact on military cooperation — page 3. • Malanky: New York- and Toronto-style — page 10. • Non-profit organization promotes publishing in Ukraine — page 13. Published by the Ukrainian National Association Inc., a fraternal non-profit association Vol. LXIX HE KRAINIANNo. 4 THE UKRAINIAN WEEKLY SUNDAY, JANUARY 28, 2001 EEKLY$1/$2 in Ukraine UkrainianT CatholicU bishops convene Kuchma dismissesW Tymoshenko synod to elect primate of Church Former vice PM vows to continue fight by R.L. Chomiak Church worldwide. by Roman Woronowycz Yuschenko until January 23 to announce Special to The Ukrainian Weekly It was Metropolitan Sheptytsky who Kyiv Press Bureau that he had issued his own governmental reformed, renewed and globalized the decree. LVIV – The Synod of Bishops of the Church that until his tenure had been limit- KYIV – President Leonid Kuchma Mr. Kuchma said in Berlin that he Ukrainian Greek-Catholic Church began its ed to a corner of the Austro-Hungarian brought the political axe down on Vice signed the order not only because of the work here on Wednesday, January 24, with empire known as Eastern Galicia. It was he Prime Minister Yulia Tymoshenko on investigation by Procurator General the principal topic on the agenda being the who started sending priests to the continents January 19 in connection with charges of Mykhailo Potebenko but also “for other election of a new primate for the Church, a where Ukrainian Catholics were settling; as smuggling, forgery and tax evasion that reasons,” according to Interfax-Ukraine, successor to Cardinal Myroslav Ivan a result, today there are 34 Ukrainian the country’s chief prosecutor has leveled which included Ms. -
Composition of Raw Milk from Conventional and Organic Dairy Farming
Biotechnology in Animal Husbandry 32 (2), p 133-143 , 2016 ISSN 1450-9156 Publisher: Institute for Animal Husbandry, Belgrade-Zemun UDC 637.07’62 DOI: 10.2298/BAH1602133K COMPOSITION OF RAW MILK FROM CONVENTIONAL AND ORGANIC DAIRY FARMING Denis Kučević1*, Snežana Trivunović1, Vladan Bogdanović2, Ksenija Čobanović1, Dobrila Janković1, Dragan Stanojević2 1University of Novi Sad, Faculty of Agriculture, Department of Animal Science, Trg D. Obradovica 8, Novi Sad, 21000 2University of Belgrade, Faculty of Agriculture, Department of Zootechniques, 11080 Zemun, Serbia *Corresponding author: E-mail: [email protected] Original scientific paper Abstract: Possible differences between composition of raw milk due to dairy farming system (organic vs conventional) as well as seasonal variations were investigated. The samples were analysed during one year. A total of 6.782 samples of raw milk were collected (4.496 from organic farming). Dairy farms were located in the northern part of Republic of Serbia (Province of Vojvodina). The principle of analysis of raw milk samples was in accordance with the methodology by mid- infrared spectrometry and flow cytometry. The fixed effect of system of farming and season (winter, spring, summer and fall) have shown a high statistical significance (P < 0.01) on all examined milk parameters except fat, total solids and somatic cell count, where the impact was slightly lower (P < 0.05). Significant difference wasn't found in number of bacterial colonies (P > 0.05). Composition of milk is also affected by a number of other factors, therefore it is recommended to involve factors such as nutrition of dairy cows, breed and farm management. -
16850 RHI67.Indb
The Success of the Anglo-Maikop Corporation Within the Fiasco of the Maikop “Oil Rush”* • AURÈLIA MAÑÉ ESTRADA GATE, University of Barcelona & School of History, University of East Anglia Introduction On the same page of the Nineteenth General Annual Report of the Board of Trade1 of 1909 we learn of the creation of two new British companies: the Anglo Persian Oil Company (APOC) and the Anglo Maikop Corporation (AMC). None of these belonged to the first wave of oil companies who had tried to find their place in the emerging international oil industry of the twen- tieth century. Both, however, were amongst the British free-standing compa- nies2 which proliferated at the beginning of the century only to disappear by * The present article is the result of a stage as a visiting fellow at the School of Histo- ry of the University of East Anglia (UK) during the year 2013-2014 and of my work with Dr Paul Warde. I am indebted mainly to him but also to my colleagues of the UEA, espe- cially Dr Cathie Carmichael and Dr Silvia Evengelisti, for their kind help throughout my re- search. I would like to thank chiefly, too, Kate and Jonathan Griffin, relatives of George Tweedy, who helped to check some of the information included in this article. My stay at UEA was possible thanks to the University of Barcelona, which granted a sab- batical, and the collaboration with the project “New spaces, actors and instruments in Spain’s foreign relations with the Arab and muslim worlds” (CSO2011-29438-C05-02). -
Argus Nefte Transport
Argus Nefte Transport Oil transportation logistics in the former Soviet Union Volume XVI, 5, May 2017 Primorsk loads first 100,000t diesel cargo Russia’s main outlet for 10ppm diesel exports, the Baltic port of Primorsk, shipped a 100,000t cargo for the first time this month. The diesel was loaded on 4 May on the 113,300t Dong-A Thetis, owned by the South Korean shipping company Dong-A Tanker. The 100,000t cargo of Rosneft product was sold to trading company Vitol for delivery to the Amsterdam-Rotter- dam-Antwerp region, a market participant says. The Dong-A Thetis was loaded at Russian pipeline crude exports berth 3 or 4 — which can handle crude and diesel following a recent upgrade, and mn b/d can accommodate 90,000-150,000t vessels with 15.5m draught. 6.0 Transit crude Russian crude It remains unclear whether larger loadings at Primorsk will become a regular 5.0 occurrence. “Smaller 50,000-60,000t cargoes are more popular and the terminal 4.0 does not always have the opportunity to stockpile larger quantities of diesel for 3.0 export,” a source familiar with operations at the outlet says. But the loading is significant considering the planned 10mn t/yr capacity 2.0 addition to the 15mn t/yr Sever diesel pipeline by 2018. Expansion to 25mn t/yr 1.0 will enable Transneft to divert more diesel to its pipeline system from ports in 0.0 Apr Jul Oct Jan Apr the Baltic states, in particular from the pipeline to the Latvian port of Ventspils. -
Russia's Muslims.PDF
111th CONGRESS Printed for the use of the 1st Session Commission on Security and Cooperation in Europe RUSSIA’S MUSLIMS DECEMBER 17, 2009 Briefing of the Commission on Security and Cooperation in Europe Washington: 2012 VerDate 0ct 09 2002 12:05 Sep 20, 2012 Jkt 000000 PO 00000 Frm 00001 Fmt 3191 Sfmt 3191 U:\WORK\121709 KATIE big-LOGO.EPS Commission on Security and Cooperation in Europe 234 Ford House Office Building Washington, DC 20515 202–225–1901 [email protected] http://www.csce.gov Legislative Branch Commissioners HOUSE SENATE ALCEE L. HASTINGS, FLORIDA, BENJAMIN L. CARDIN, MARYLAND, Co-Chairman Chairman EDWARD J. MARKEY, MASSACHUSETTS CHRISTOPHER J. DODD, CONNECTICUT LOUISE MCINTOSH SLAUGHTER, SHELDON WHITEHOUSE, RHODE ISLAND NEW YORK TOM UDALL, NEW MEXICO MIKE MCINTYRE, NORTH CAROLINA JEANNE SHAHEEN, NEW HAMPSHIRE G.K. BUTTERFIELD, NORTH CAROLINA SAM BROWNBACK, KANSAS CHRISTOPHER H. SMITH, NEW JERSEY SAXBY CHAMBLISS, GEORGIA ROBERT B. ADERHOLT, ALABAMA RICHARD BURR, NORTH CAROLINA JOSEPH R. PITTS, PENNSYLVANIA ROBERT F. WICKER, MISSISSIPPI DARRELL E. ISSA, CALIFORNIA Executive Branch Commissioners MICHAEL H. POSNER, DEPARTMENT OF STATE ALEXANDER VERSHBOW, DEPARTMENT OF DEFENSE MICHAEL C. CAMUN˜ EZ, DEPARTMENT OF COMMERCE (II) VerDate 0ct 09 2002 12:05 Sep 20, 2012 Jkt 000000 PO 00000 Frm 00002 Fmt 3193 Sfmt(2) 3193 U:\WORK\121709 KATIE ABOUT THE ORGANIZATION FOR SECURITY AND COOPERATION IN EUROPE The Helsinki process, formally titled the Conference on Security and Cooperation in Europe, traces its origin to the signing of the Helsinki Final Act in Finland on August 1, 1975, by the leaders of 33 European countries, the United States and Canada.