UNIVERSITY of CALIFORNIA, IRVINE Spreading and Leidenfrost
Total Page:16
File Type:pdf, Size:1020Kb
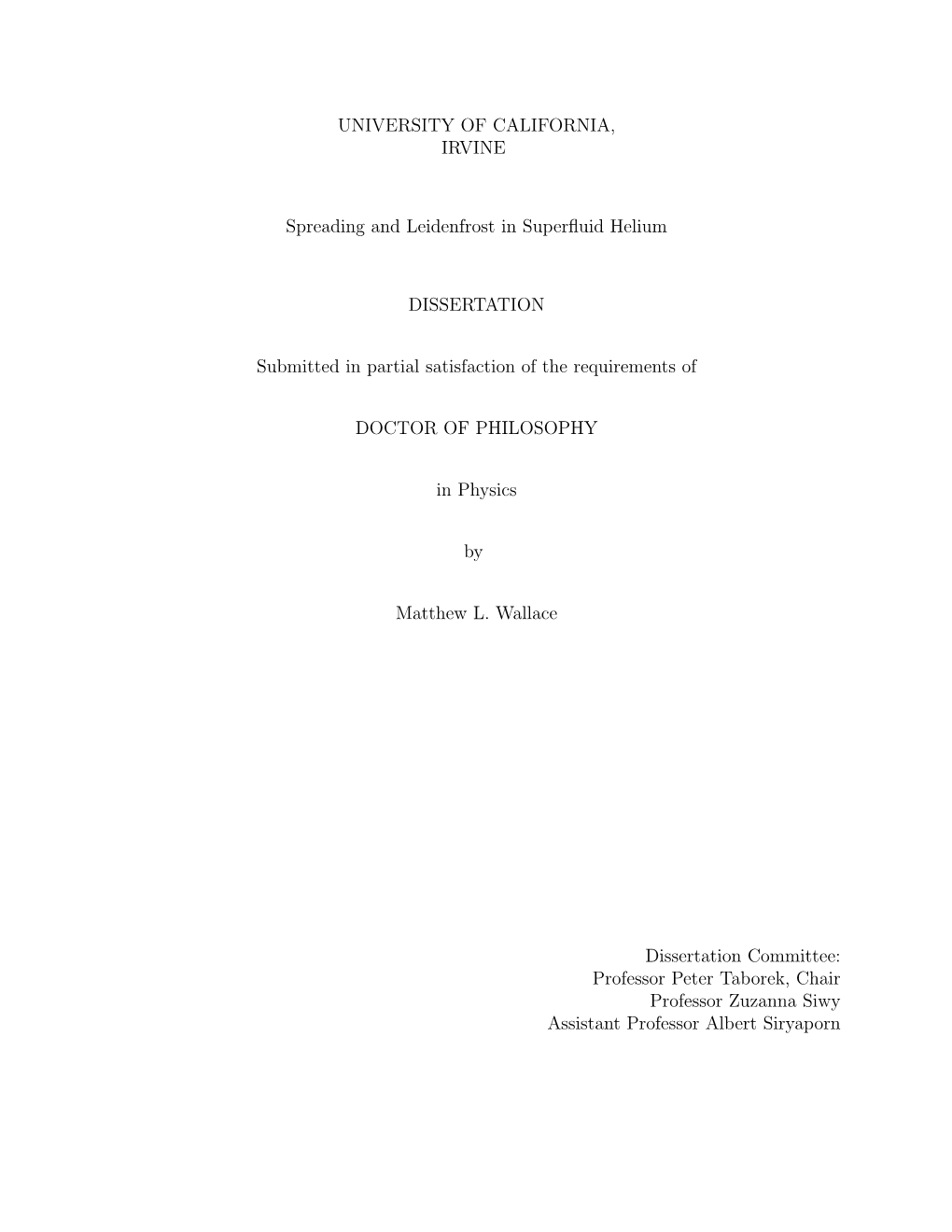
Load more
Recommended publications
-
Plasmofluidic Single-Molecule Surface-Enhanced Raman
ARTICLE Received 24 Feb 2014 | Accepted 9 Jun 2014 | Published 7 Jul 2014 DOI: 10.1038/ncomms5357 Plasmofluidic single-molecule surface-enhanced Raman scattering from dynamic assembly of plasmonic nanoparticles Partha Pratim Patra1, Rohit Chikkaraddy1, Ravi P.N. Tripathi1, Arindam Dasgupta1 & G.V. Pavan Kumar1 Single-molecule surface-enhanced Raman scattering (SM-SERS) is one of the vital applications of plasmonic nanoparticles. The SM-SERS sensitivity critically depends on plasmonic hot-spots created at the vicinity of such nanoparticles. In conventional fluid-phase SM-SERS experiments, plasmonic hot-spots are facilitated by chemical aggregation of nanoparticles. Such aggregation is usually irreversible, and hence, nanoparticles cannot be re-dispersed in the fluid for further use. Here, we show how to combine SM-SERS with plasmon polariton-assisted, reversible assembly of plasmonic nanoparticles at an unstructured metal–fluid interface. One of the unique features of our method is that we use a single evanescent-wave optical excitation for nanoparticle assembly, manipulation and SM-SERS measurements. Furthermore, by utilizing dual excitation of plasmons at metal–fluid interface, we create interacting assemblies of metal nanoparticles, which may be further harnessed in dynamic lithography of dispersed nanostructures. Our work will have implications in realizing optically addressable, plasmofluidic, single-molecule detection platforms. 1 Photonics and Optical Nanoscopy Laboratory, h-cross, Indian Institute of Science Education and Research, Pune 411008, India. Correspondence and requests for materials should be addressed to G.V.P.K. (email: [email protected]). NATURE COMMUNICATIONS | 5:4357 | DOI: 10.1038/ncomms5357 | www.nature.com/naturecommunications 1 & 2014 Macmillan Publishers Limited. All rights reserved. -
Generation and Stability of Size-Adjustable Bulk Nanobubbles
www.nature.com/scientificreports OPEN Generation and Stability of Size-Adjustable Bulk Nanobubbles Based on Periodic Pressure Received: 10 September 2018 Accepted: 18 December 2018 Change Published: xx xx xxxx Qiaozhi Wang, Hui Zhao, Na Qi, Yan Qin, Xuejie Zhang & Ying Li Recently, bulk nanobubbles have attracted intensive attention due to the unique physicochemical properties and important potential applications in various felds. In this study, periodic pressure change was introduced to generate bulk nanobubbles. N2 nanobubbles with bimodal distribution and excellent stabilization were fabricated in nitrogen-saturated water solution. O2 and CO2 nanobubbles have also been created using this method and both have good stability. The infuence of the action time of periodic pressure change on the generated N2 nanobubbles size was studied. It was interestingly found that, the size of the formed nanobubbles decreases with the increase of action time under constant frequency, which could be explained by the diference in the shrinkage and growth rate under diferent pressure conditions, thereby size-adjustable nanobubbles can be formed by regulating operating time. This study might provide valuable methodology for further investigations about properties and performances of bulk nanobubbles. Nanobubbles are gaseous domains which could be found at the solid/liquid interface or in solution, known as surface nanobubbles (SNBs)1,2 and bulk nanobubbles (BNBs)3, respectively. For BNBs, generally recognized as spherical bubbles with the diameter of less than 1μm surrounded by liquid, though it has been observed frstly in 19814, the existence of long-lived BNBs is still a controversial subject as it is contrary to the classical theory5,6. -
Review Article Importance of Molecular Interactions in Colloidal Dispersions
Hindawi Publishing Corporation Advances in Condensed Matter Physics Volume 2015, Article ID 683716, 8 pages http://dx.doi.org/10.1155/2015/683716 Review Article Importance of Molecular Interactions in Colloidal Dispersions R. López-Esparza,1,2 M. A. Balderas Altamirano,1 E. Pérez,1 and A. Gama Goicochea1,3 1 Instituto de F´ısica, Universidad Autonoma´ de San Luis Potos´ı, 78290 San Luis Potos´ı, SLP, Mexico 2Departamento de F´ısica, Universidad de Sonora, 83000 Hermosillo, SON, Mexico 3Innovacion´ y Desarrollo en Materiales Avanzados A. C., Grupo Polynnova, 78211 San Luis Potos´ı, SLP, Mexico Correspondence should be addressed to A. Gama Goicochea; [email protected] Received 21 May 2015; Accepted 2 August 2015 Academic Editor: Jan A. Jung Copyright © 2015 R. Lopez-Esparza´ et al. This is an open access article distributed under the Creative Commons Attribution License, which permits unrestricted use, distribution, and reproduction in any medium, provided the original work is properly cited. We review briefly the concept of colloidal dispersions, their general properties, and some of their most important applications, as well as the basic molecular interactions that give rise to their properties in equilibrium. Similarly, we revisit Brownian motion and hydrodynamic interactions associated with the concept of viscosity of colloidal dispersion. It is argued that the use of modern research tools, such as computer simulations, allows one to predict accurately some macroscopically measurable properties by solving relatively simple models of molecular interactions for a large number of particles. Lastly, as a case study, we report the prediction of rheological properties of polymer brushes using state-of-the-art, coarse-grained computer simulations, which are in excellent agreement with experiments. -
Inverted Leidenfrost-Like Effect During Condensation
Article pubs.acs.org/Langmuir Inverted Leidenfrost-like Effect during Condensation Ramchandra Narhe,†,‡ Sushant Anand,§ Konrad Rykaczewski,∥ Marie-Gabrielle Medici,†,⊥ Wenceslao Gonzalez-Viń ̃as,‡ Kripa K. Varanasi,§ and Daniel Beysens*,†,# † Physique et Mecaniqué des Milieux Hetérogé nes,̀ UnitéMixte de Recherches (UMR) 7636, École Superieuré de Physique et Chimie Industrielles ParisTech, UniversitéPierre et Marie Curie, UniversitéParis-Diderot, Centre National de la Recherche Scientifique (CNRS), 10 rue Vauquelin, 75231 Paris, France ‡ Department of Physics and Applied Mathematics, University of Navarra, 31008 Pamplona, Spain § Department of Mechanical Engineering, Massachusetts Institute of Technology, Cambridge, Massachusetts 02139, United States ∥ School for Engineering of Matter, Transport and Energy, Arizona State University, Tempe, Arizona 85281, United States ⊥ UniversitéNice Sophia Antipolis, CNRS, Laboratoire de Physique de la Mateierè Condensee-UMŔ 7336, Parc Valrose, 06100 Nice, France # Service des Basses Temperatures,́ CEA-Grenoble and UniversitéJoseph Fourier, 38041 Grenoble, France *S Supporting Information ABSTRACT: Water droplets condensing on solidified phase change materials such as benzene and cyclohexane near their melting point show in-plane jumping and continuous “crawling” motion. The jumping drop motion has been tentatively explained as an outcome of melting and refreezing of the materials surface beneath the droplets and can be thus considered as an inverted Leidenfrost-like effect (in the classical case vapor is generated from a droplet on a hot substrate). We present here a detailed investigation of jumping movements using high-speed imaging and static cross- sectional cryogenic focused ion beam scanning electron microscope imaging. Our results show that drop motion is induced by a thermocapillary (Marangoni) effect. The in-plane jumping motion can be delineated to occur in two stages. -
Colloidal Crystal: Emergence of Long Range Order from Colloidal Fluid
Colloidal Crystal: emergence of long range order from colloidal fluid Lanfang Li December 19, 2008 Abstract Although emergence, or spontaneous symmetry breaking, has been a topic of discussion in physics for decades, they have not entered the set of terminologies for materials scientists, although many phenomena in materials science are of the nature of emergence, especially soft materials. In a typical soft material, colloidal suspension system, a long range order can emerge due to the interaction of a large number of particles. This essay will first introduce interparticle interactions in colloidal systems, and then proceed to discuss the emergence of order, colloidal crystals, and finally provide an example of applications of colloidal crystals in light of conventional molecular crystals. 1 1 Background and Introduction Although emergence, or spontaneous symmetry breaking, and the resultant collective behav- ior of the systems constituents, have manifested in many systems, such as superconductivity, superfluidity, ferromagnetism, etc, and are well accepted, maybe even trivial crystallinity. All of these phenonema, though they may look very different, share the same fundamental signature: that the property of the system can not be predicted from the microscopic rules but are, \in a real sense, independent of them. [1] Besides these emergent phenonema in hard condensed matter physics, in which the interaction is at atomic level, interactions at mesoscale, soft will also lead to emergent phenemena. Colloidal systems is such a mesoscale and soft system. This size scale is especially interesting: it is close to biogical system so it is extremely informative for understanding life related phenomena, where emergence is origin of life itself; it is within visible light wavelength, so that it provides a model system for atomic system with similar physics but probable by optical microscope. -
Universality in Spectral Condensation Induja Pavithran1, Vishnu R
www.nature.com/scientificreports OPEN Universality in spectral condensation Induja Pavithran1, Vishnu R. Unni2*, Alan J. Varghese3, D. Premraj3, R. I. Sujith3,4*, C. Vijayan1, Abhishek Saha2, Norbert Marwan4 & Jürgen Kurths4,5,6 Self-organization is the spontaneous formation of spatial, temporal, or spatiotemporal patterns in complex systems far from equilibrium. During such self-organization, energy distributed in a broadband of frequencies gets condensed into a dominant mode, analogous to a condensation phenomenon. We call this phenomenon spectral condensation and study its occurrence in fuid mechanical, optical and electronic systems. We defne a set of spectral measures to quantify this condensation spanning several dynamical systems. Further, we uncover an inverse power law behaviour of spectral measures with the power corresponding to the dominant peak in the power spectrum in all the aforementioned systems. During self-organization, an ordered pattern emerges from an initially disordered state. In dynamical systems, a pattern can be any regularly repeating arrangements in space, time or both1. For example, a laser emits random wave tracks like a lamp until the critical pump power, above which the laser emits light as a single coherent wave track with high-intensity2. A macroscopic change is observed in the laser system as a long-range pattern emerges in time. Another example is the Rayleigh–Bénard system. For lower temperature gradients, the fuid parcels move randomly. As the temperature gradient is increased, a rolling motion sets in and the fuid parcels behave coherently to form spatially extended patterns. Te initial random pattern can be regarded as a superposition of a variety of oscillatory modes and eventually some oscillatory modes dominate, resulting in the emergence of a spatio-temporal pattern3,4. -
Surface Plasmon Resonance Study of the Purple Gold
SURFACE PLASMON RESONANCE STUDY OF THE PURPLE GOLD (AuAl2) INTERMETALLIC, pH-RESPONSIVE FLUORESCENCE GOLD NANOPARTICLES, AND GOLD NANOSPHERE ASSEMBLY Panupon Samaimongkol Dissertation submitted to the faculty of the Virginia Polytechnic Institute and State University in partial fulfillment of the requirements for the degree of Doctor of Philosophy In Physics Hans D. Robinson, Chair Giti Khodaparast Chenggang Tao Webster Santos June 22, 2018 Blacksburg, Virginia Keywords: Surface plasmons (SPs), Localized surface plasmon resonances (LSPRs), Kretschmann configuration, Surface plasmon-enhanced fluorescence (PEF) spectroscopy, Self-Assembly, Nanoparticles Copyright 2018, Panupon Samaimongkol i SURFACE PLASMON RESONANCE STUDY OF THE PURPLE GOLD (AuAl2) INTERMETALLIC, pH-RESPONSIVE FLUORESCENCE GOLD NANOPARTICLES, AND GOLD NANOSPHERE ASSEMBLY Panupon Samaimongkol ABSTRACT (academic) In this dissertation, I have verified that the striking purple color of the intermetallic compound AuAl2, also known as purple gold, originates from surface plasmons (SPs). This contrasts to a previous assumption that this color is due to an interband absorption transition. The existence of SPs was demonstrated by launching them in thin AuAl2 films in the Kretschmann configuration, which enables us to measure the SP dispersion relation. I observed that the SP energy in thin films of purple gold is around 2.1 eV, comparable to previous work on the dielectric function of this material. Furthermore, SP sensing using AuAl2 also shows the ability to measure the change in the refractive index of standard sucrose solution. AuAl2 in nanoparticle form is also discussed in terms of plasmonic applications, where Mie scattering theory predicts that the particle bears nearly uniform absorption over the entire visible spectrum with an order magnitude higher absorption than efficient light-absorbing carbonaceous particle also known a carbon black. -
Polymer Colloid Science
Polymer Colloid Science Jung-Hyun Kim Ph. D. Nanosphere Process & Technology Lab. Department of Chemical Engineering, Yonsei University National Research Laboratory Project the financial support of the Korea Institute of S&T Evaluation and Planning (KISTEP) made in the program year of 1999 기능성 초미립자 공정연구실 Colloidal Aspects 기능성 초미립자 공정연구실 ♣ What is a polymer colloids ? . Small polymer particles suspended in a continuous media (usually water) . EXAMPLES - Latex paints - Natural plant fluids such as natural rubber latex - Water-based adhesives - Non-aqueous dispersions . COLLOIDS - The world of forgotten dimensions - Larger than molecules but too small to be seen in an optical microscope 기능성 초미립자 공정연구실 ♣ What does the term “stability/coagulation imply? . There is no change in the number of particles with time. A system is said to be colloidally unstable if collisions lead to the formation of aggregates; such a process is called coagulation or flocculation. ♣ Two ways to prevent particles from forming aggregates with one another during their colliding 1) Electrostatic stabilization by charged group on the particle surface - Origin of the charged group - initiator fragment (COOH, OSO3 , NH4, OH, etc) ionic surfactant (cationic or anionic) ionic co-monomer (AA, MAA, etc) 2) Steric stabilization by an adsorbed layer of some substance 3) Solvation stabilization 기능성 초미립자 공정연구실 기능성 초미립자 공정연구실 Stabilization Mechanism Electrostatic stabilization - Electrostatic stabilization Balancing the charge on the particle surface by the charges on small ions -
Behavior of Self-Propelled Acetone Droplets in a Leidenfrost State on Liquid Substrates
CORE Metadata, citation and similar papers at core.ac.uk Provided by OIST Institutional Repository Behavior of self-propelled acetone droplets in a Leidenfrost state on liquid substrates Author Stoffel D. Janssens, Satoshi Koizumi, Eliot Fried journal or Physics of Fluids publication title volume 29 number 3 page range 032103 year 2017-03-14 Publisher AIP Publishing Author's flag publisher URL http://id.nii.ac.jp/1394/00000325/ doi: info:doi/10.1063/1.4977442 Creative Commons Attribution 4.0 International (http://creativecommons.org/licenses/by/4.0/) Behavior of self-propelled acetone droplets in a Leidenfrost state on liquid substrates Stoffel D. Janssens, Satoshi Koizumi, and Eliot Fried Citation: Physics of Fluids 29, 032103 (2017); doi: 10.1063/1.4977442 View online: https://doi.org/10.1063/1.4977442 View Table of Contents: http://aip.scitation.org/toc/phf/29/3 Published by the American Institute of Physics Articles you may be interested in Effect of interfacial slip on the deformation of a viscoelastic drop in uniaxial extensional flow field Physics of Fluids 29, 032105 (2017); 10.1063/1.4977949 Reversible self-propelled Leidenfrost droplets on ratchet surfaces Applied Physics Letters 110, 091603 (2017); 10.1063/1.4976748 Leidenfrost drops Physics of Fluids 15, 1632 (2003); 10.1063/1.1572161 The fate of pancake vortices Physics of Fluids 29, 031701 (2017); 10.1063/1.4977975 Spontaneous rotation of an ice disk while melting on a solid plate Physics of Fluids 28, 123601 (2016); 10.1063/1.4967399 On the shape memory of red blood cells Physics of Fluids 29, 041901 (2017); 10.1063/1.4979271 PHYSICS OF FLUIDS 29, 032103 (2017) Behavior of self-propelled acetone droplets in a Leidenfrost state on liquid substrates Stoffel D. -
Ways to Physically Separate a Mixture There Are 2 Types of Mixtures
Mixtures 12 Mixtures Homogenous Compare Heterogeneous compounds and Suspension Mixtures. Colloid Solution Differentiate Solute/Solvent between solutions, suspensions, and colloids Comparing Mixtures and Compounds Mixtures Compounds Made of 2 or more substances Made of 2 or more substances physically combined chemically combined Substances keep their own properties Substances lose their own properties Can be separated by physical means Can be separated only by chemical means Have no definite chemical composition Have a definite chemical composition What method is used to separate mixtures Ways to physically separate a Mixture based on boiling • Distillation – uses boiling point point? • Magnet – uses magnetism What method is used • Centrifuge – uses density to separate mixtures based on density? • Filtering – separates large particles from smaller ones What method is used There are 2 types of mixtures: to separate mixtures (1) Heterogeneous Mixtures: the parts mixed together can still be based on particle size? distinguished from one another...NOT uniform in composition Give examples of a heterogeneous Examples: chicken soup, fruit salad, dirt, sand in water mixture Mixtures 12 (2) Homogenous Mixtures: the parts mixed together cannot be distinguished from one another...completely uniform in composition. Give examples of a homogenous Examples: Air, Kool-aid, Brass, salt water, milk mixture Differentiate Types of Homogenous mixtures between a homogenous 1. Suspensions mixture and a i.e. chocolate milk, muddy water, Italian dressing heterogeneous mixture. They are cloudy (usually a liquid mixed with small solid particles) Identify an example of a suspension. Needs to be shaken or stirred to keep the solids from Will the solid settling particles settle in a suspension? The solids can be filtered out 2. -
Classification of Matter Section ●1 Composition of Matter
266_277_Ch15_RE_896315.qxd 3/23/10 3:04 AM Page 266 S-034 113:GO00492:GPS_Reading_Essentials_SE%0:XXXXXXXXXXXXX_SE:Application_Files_ chapter 15 Classification of Matter section ●1 Composition of Matter What You’ll Learn Before You Read ■ what substances and mixtures are Matter is all around you. You breathe matter, sit on it, and ■ how to identify drink it every day. What words would you use to describe elements and different kinds of matter? compounds ■ the difference between solutions, colloids, and suspensions Read to Learn Underline Look for different descriptions of matter Pure Substances as you read each paragraph. Underline these descriptions. Have you ever seen a print that looked like a real painting? Read the underlined descriptions Did you have to touch it to find out? The smooth or rough again after you’ve finished surface told you whether it was a painting or a print. Each reading the section. material has its own properties. The properties of materials can be used to classify them into categories. Each material is made of a pure substance or of a mix of substances. A substance is a type of matter that is always made of the same material or materials. A substance can be either an element or a compound. Some substances you might recognize are helium, aluminum, water, and salt. What are elements? All substances are made of atoms. A substance is an element if all the atoms in the substance are the same. The graphite in your pencil is an element. The copper coating on most pennies is an element, too. -
Alexandre Édouard Baudrimont: Crystallography, Colloids, Aqua Regia
Revista CENIC. Ciencias Químicas ISSN: 1015-8553 ISSN: 2221-2442 [email protected] Centro Nacional de Investigaciones Científicas Cuba Alexandre Édouard Baudrimont: Crystallography, colloids, aqua regia Wisniak, Jaime Alexandre Édouard Baudrimont: Crystallography, colloids, aqua regia Revista CENIC. Ciencias Químicas, vol. 49, no. 1, 2018 Centro Nacional de Investigaciones Científicas, Cuba Available in: https://www.redalyc.org/articulo.oa?id=181661081002 PDF generated from XML JATS4R by Redalyc Project academic non-profit, developed under the open access initiative Jaime Wisniak. Alexandre Édouard Baudrimont: Crystallography, colloids, aqua regia Articulos de Revision Alexandre Édouard Baudrimont: Crystallography, colloids, aqua regia Alexandre Édouard Baudrimont: Cristalografía, coloides, agua regia Jaime Wisniak a Redalyc: https://www.redalyc.org/articulo.oa? Ben-Gurion University of the Negev, Israel id=181661081002 [email protected] Received: 03 January 2018 Accepted: 15 February 2018 Abstract: Alexander Édouard Baudrimont (1806-1880) was a French physician and pharmacist that carried on fundamental research on a wide variety of subjects, among them, philosophy of science, linguistic, colloidal chemistry, cosmology, crystallography, mechanics of materials, etc. e same as Ampère, he proposed a new theory where only certain geometrical shapes were able to induce a chemical reaction. When atoms combined to form and integral molecule, they assumed an arrangement that if not regular, was at least symmetric. Chemical formulas did not represent the absolute number of atoms present; they represented only a number proportional to the real one. Crystalline particles were always small polyhedrons, which adapted one to the other without leaving empty spaces, a condition satisfied only by only cuboids, hexahedral prisms, and dodecahedrons.