Sago Int.Indd
Total Page:16
File Type:pdf, Size:1020Kb
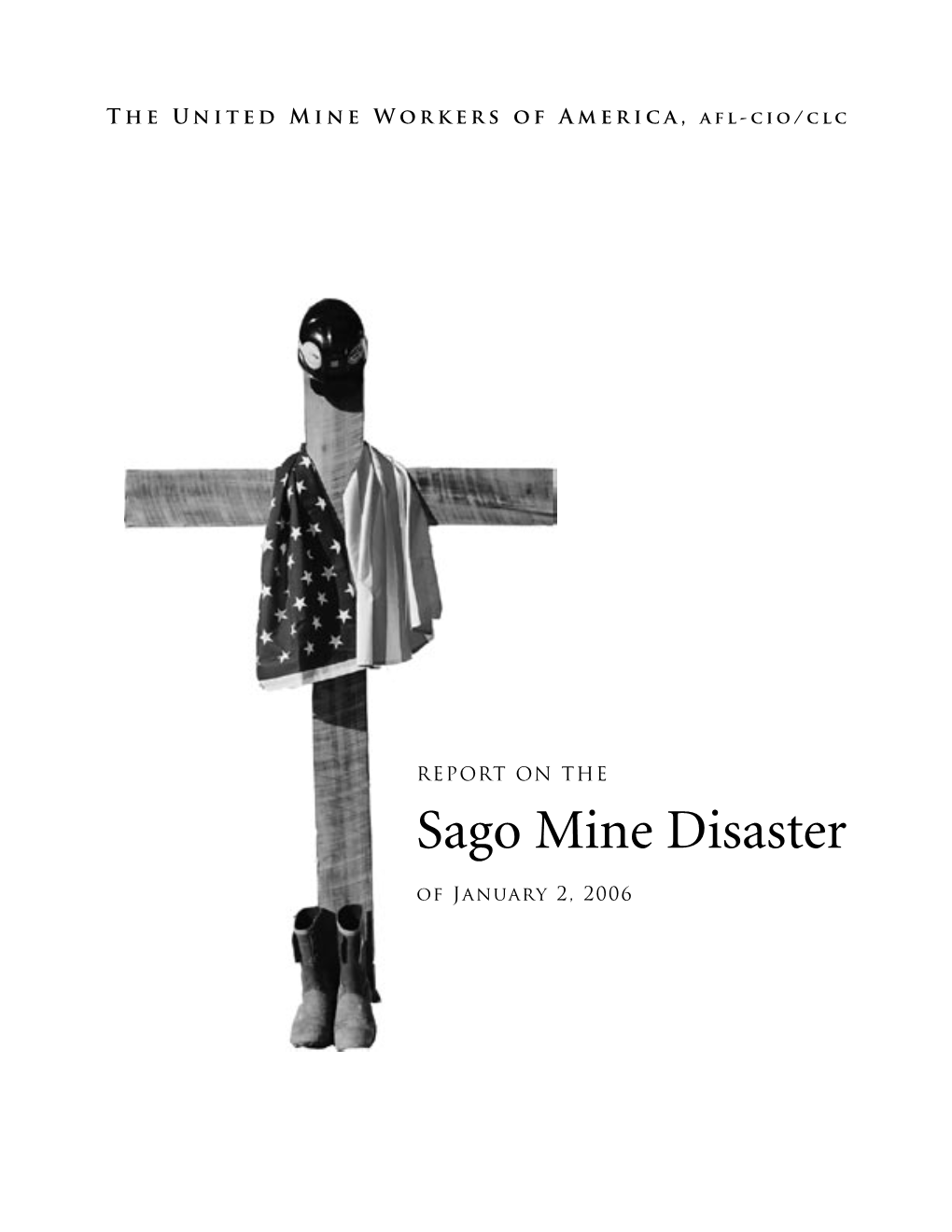
Load more
Recommended publications
-
WL Ross and Co., and the Anker Coal Disaster
Click here for Full Issue of EIR Volume 33, Number 4, January 27, 2006 subpoena both witnesses and documents, it now almost never does. It is instead interviewing witnesses behind closed doors, Interview: Mark Reutter making employer intimidation of miner witnesses more pos- sible. This lack of rigor by MHSA makes immediate Congres- sional hearings even more urgent. Sen. Robert Byrd (D- WLRoss and Co., and W.Va.) has attempted to schedule immediate hearings in a subcommittee of the Senate Appropriations Committee; whether these take place in the week of Jan. 23, or are put off, The Anker Coal Disaster is not clear at this writing. Sen. Jay Rockefeller (D-W.Va.) on Jan. 12, called for Mark Reutter is the author of Making Steel: Sparrows Point hearings in the Senate Health, Education, Labor, and Pensions and the Rise and Ruin of American Industrial Might (2004), Committee, signed by 11 other Senators of both parties, from which examines the bankruptcy proceedings of Bethlehem Kentucky, West Virginia, Pennsylvania, Indiana, and Ala- Steel and the company’s takeover by Wilbur L. Ross (see bama. Pressure is high on Committee Chairman Rick Enzi www.makingsteel.com for more), who controls the Sago coal (R-Wyo.) to schedule the hearings. In the Education and the mine. Reutter was interviewed by Paul Gallagher on Jan. 18. Workforce Committee on the House side, ranking Democrats George Miller (Calif.) and Major Owens (N.Y.) are pressing EIR: Twelve miners died and one was critically injured in a chairman John Boehner (R-Ohio) for hearings. Jan. 2 explosion at the Sago mine of Anker West Virginia If hearings are held soon and probe carefully this “Ross/ Coal, in Upshur County, West Virginia. -
As Filed with the Securities and Exchange Commission on May 5
As filed with the Securities and Exchange Commission on May 5, 2020 UNITED STATES OF AMERICA BEFORE THE SECURITIES AND EXCHANGE COMMISSION FIRST AMENDED AND RESTATED APPLICATION FOR AN ORDER PURSUANT TO SECTION 3(b)(2) OF THE INVESTMENT COMPANY ACT OF 1940, AS AMENDED, DECLARING THAT ARCH COAL, INC. IS PRIMARILY ENGAGED IN A BUSINESS OTHER THAN THAT OF INVESTING, REINVESTING, OWNING, HOLDING, OR TRADING IN SECURITIES In the Matter of ARCH COAL, INC. File No. 812-15085 Please send all communications to: Robert G. Jones, Esq. Arch Coal, Inc. One CityPlace Drive, Suite 300 St. Louis, Missouri 63141 (314) 994-2700 Nabil Sabki, Esq. Latham & Watkins LLP 330 North Wabash Avenue, Suite 2800 Chicago, Illinois 60611 (312) 876-7700 This Application (including Exhibits) consists of 22 pages. 1 UNITED STATES OF AMERICA BEFORE THE SECURITIES AND EXCHANGE COMMISSION In the Matter of FIRST AMENDED AND RESTATED APPLICATION FOR AN ORDER PURSUANT TO SECTION 3(b)(2) OF THE INVESTMENT ARCH COAL, INC. COMPANY ACT OF 1940, AS AMENDED, DECLARING THAT One CityPlace Drive, Suite 300 ARCH COAL, INC. IS PRIMARILY ENGAGED IN A BUSINESS St. Louis, Missouri 63141 OTHER THAN THAT OF INVESTING, REINVESTING, OWNING, HOLDING, OR TRADING IN SECURITIES. File No. 812-15085 I. SUMMARY OF RELIEF REQUESTED Arch Coal, Inc. (“Arch Coal” or the “Company”),1 a Delaware corporation listed on the New York Stock Exchange (NYSE: ARCH) with its principal executive office in St. Louis, Missouri, is one of the world’s largest coal producers. Arch Coal hereby files this amended and restated application (this “Application”) and applies for an order (the “Requested Order”) of the U.S. -
Independent Report on Sago
The Sago Mine Disaster A preliminary report to Governor Joe Manchin III J. Davitt McAteer and associates July • 2006 The Sago Mine Disaster A preliminary report to Governor Joe Manchin III J. Davitt McAteer and associates: Thomas N. Bethell Celeste Monforton Joseph W. Pavlovich Deborah Roberts Beth Spence JULY • 2006 Buckhannon, West Virginia On January 12, 2006, West Virginia Senate President Earl Ray Tomblin (D-Chapmanville) and House Speaker Bob Kiss (D-Raleigh) appointed Senators Don Caruth (R-Mercer), Jeff Kessler (D-Marshall) and Shirley Love (D-Fayette) and Delegates Mike Caputo (D-Marion), Eustace Frederick (D-Mercer) and Bill Hamilton (R-Upshur) to conduct an inquiry into the Sago disaster. At the request of Governor Joe Manchin III, their inquiry was conducted jointly with our investigation. These legislators have worked diligently with us in seeking answers to this West Virginia tragedy. This report, as well as additional related information, is available at: www.wvgov.org and www.wju.edu Front cover photo: Memorial ribbons on the Sago Mine security fence, January 2006 Jeff Swensen / Getty Images Back cover photo: Mourners praying at the funeral of Jerry Groves, January 2006 Haraz Ghanbari / AP Images Contents Letter of transmittal ..........................................................2 Dedication........................................................................4 1. Executive Summary .......................................................7 2. Recommendations ...................................................... -
Saratoga Advantage Trust, Et Al. V. International Coal Group, Inc., Et Al
4. F I LED IN THE UNITED STATES DISTRICT COU ' • 7...— MN FOR THE SOUTHERN DISTRICT OF WEST VI' A AT CHARLESTON 47e, RESAL. DEPPNER, CLERK US. District Court District of West Virginia SARATOGA ADVANTAGE TRUST, On ) Southern Behalf Of Themselves And All Others ) Civil Action No. a . 06- 00 Similarly Situated, ) ) CLASS ACTION COMPLAINT ) FOR VIOLATION OF FEDERAL Plaintiff, ) SECURITIES LAWS vs. ) ) ) ICG, INC. a/Ida INTERNATIONAL COAL ) DEMAND FOR JURY TRIAL GROUP, INC., WILBUR L. ROSS, ) BENNETT K. HATFIELD, WENDY L. TERAMOTO , WILLIAM D. CAMPBELL, ))',/,1 501 ) Defendants. ) ) ) Plaintiff Saratoga Advantage Trust, by their undersigned attorney, individually and on behalf of the Class described below, makes the following allegations based upon, inter alia, the investigation of Plaintiffs counsel, which investigation included analysis of publicly available news articles, press releases and reports, public filings, securities analysts' reports and advisories about ICG, Inc., a/k/a International Coal Group, Inc. ("ICG" or the "Company"), press releases and other public statements issued by, and media reports about the Company, and believing that substantial additional support exists for the allegations set forth herein upon a reasonable opportunity for discovery. NATURE OF THE ACTION 1. This is a securities class action on behalf of all persons and entities who purchased securities of ICG between April 28, 2005 and June 8, 2006, inclusive (the "Class Period") against ICG seeking to pursue remedies under the Securities Exchange Act of 1934 (the "Exchange Act") [15 U.S.C. §§78j(b) and 78(a)], and Rule 10b-5 promulgated thereafter by the SEC [17 C.F.R. -
Risky Business: a Pentadic Analysis of Two West Virginia Coal Mining
Risky business: A pentadic analysis of two West Virginia coal mining disasters Nathan Zachary Sowder Thesis submitted to the faculty of the Virginia Polytechnic Institute and State University in partial fulfillment of the requirements for the degree of Master of Arts in Communication Rachel L. Holloway, Chair Buddy W. Howell Damion M. Waymer May 8, 2013 Blacksburg, Virginia Keywords: coal, Burke, pentad, West Virginia Risky business: A pentadic analysis of two West Virginia coal mining disasters Nathan Zachary Sowder ABSTRACT: In just five years West Virginia was rocked with two devastating disasters in the coal mining industry. Despite the disasters, West Virginians could not just walk away from the mines, as they depended on the coal industry for jobs and tax revenue. West Virginia had built a purpose-driven orientation towards the coal industry through a historical and current dependency on coal. However, the two disasters had a chance to alter that dominant orientation. In order to understand how or if the coal orientation was altered, by the disaster or the discourse that followed, a pentadic analysis was completed. The analysis revealed that the coal companies constantly battled a tension between the elements of agency and purpose, while trying to overcome a scene that made safety challenging. In the end, one mining company altered the purpose-driven orientation, as the other reinforced the orientation. As both of the situations offered different orientations towards coalmining, their orientations showed that coal companies can be purpose-driven providers but also a responsible provider, understanding not only that miners need a paycheck, but also safety. -
Saratoga Advantage Trust, Et Al. V. International Coal Group, Inc., Et
UNITED STATES DISTRICT COURT SOUTHERN DISTRICT OF WEST VIRGINIA AT CHARLESTON SARATOGA ADVANTAGE TRUST and ) THEODORE HYER, On Behalf of ) Civil Action No. 2:08-ev-0011 Themselves and All Others Similarly ) Situated, ) FIRST AMENDED CLASS ACTION ) COMPLAINT FOR VIOLATION Plaintiffs, ) OF FEDERAL SECURITIES LAWS vs. ) ) ) ICG, INC. a/k/a INTERNATIONAL COAL ) DEMAND FOR JURY TRIAL GROUP, INC., WILBUR L. ROSS, ) BENNETT K. HATFIELD, WENDY L. ) TERAMOTO, and WILLIAM D. ) CAMPBELL, ) ) Defendants. ) ) Lead Plaintiff Saratoga Advantage Trust, and co-plaintiff Theodore Hyer, by their undersigned attorneys, individually and on behalf of the Class described below, makes the following allegations in support of their First Amended Class Action Complaint based upon, inter alia, the investigation of Plaintiffs' counsel, that included: an analysis of publicly available news articles, press releases and reports, public filings, securities analysts' reports and advisories about ICG, Inc., a/lc/a International Coal Group, Inc. ("ICG" or the "Company"); press releases and other public statements issued by, and media reports about the Company; and, the belief that substantial additional support exists for the allegations set forth herein upon a reasonable opportunity for discovery. NATURE OF THE ACTION 1. This is a securities class action on behalf of all persons and entities who purchased securities of ICG between April 28, 2005 and June 6, 2006, inclusive (the "Class Period"), against ICG seeking to pursue remedies under the Securities Exchange Act of 1934 (the "Exchange Act") [15 U.S.C. §§78j(b) and 78(a)], and Rule 10b-5 promulgated thereunder by the SEC [17 C.F.R. §240.10b-5]. -
Improving Mine Safety: One Year After Sago and Alma
S. HRG. 110–464 IMPROVING MINE SAFETY: ONE YEAR AFTER SAGO AND ALMA HEARING BEFORE A SUBCOMMITTEE OF THE COMMITTEE ON APPROPRIATIONS UNITED STATES SENATE ONE HUNDRED TENTH CONGRESS FIRST SESSION SPECIAL HEARING FEBRUARY 28, 2007—WASHINGTON, DC Printed for the use of the Committee on Appropriations ( Available via the World Wide Web: http://www.gpoaccess.gov/congress/index.html U.S. GOVERNMENT PRINTING OFFICE 43–819 PDF WASHINGTON : 2008 For sale by the Superintendent of Documents, U.S. Government Printing Office Internet: bookstore.gpo.gov Phone: toll free (866) 512–1800; DC area (202) 512–1800 Fax: (202) 512–2250 Mail: Stop SSOP, Washington, DC 20402–0001 COMMITTEE ON APPROPRIATIONS ROBERT C. BYRD, West Virginia, Chairman DANIEL K. INOUYE, Hawaii THAD COCHRAN, Mississippi PATRICK J. LEAHY, Vermont TED STEVENS, Alaska TOM HARKIN, Iowa ARLEN SPECTER, Pennsylvania BARBARA A. MIKULSKI, Maryland PETE V. DOMENICI, New Mexico HERB KOHL, Wisconsin CHRISTOPHER S. BOND, Missouri PATTY MURRAY, Washington MITCH MCCONNELL, Kentucky BYRON L. DORGAN, North Dakota RICHARD C. SHELBY, Alabama DIANNE FEINSTEIN, California JUDD GREGG, New Hampshire RICHARD J. DURBIN, Illinois ROBERT F. BENNETT, Utah TIM JOHNSON, South Dakota LARRY CRAIG, Idaho MARY L. LANDRIEU, Louisiana KAY BAILEY HUTCHISON, Texas JACK REED, Rhode Island SAM BROWNBACK, Kansas FRANK R. LAUTENBERG, New Jersey WAYNE ALLARD, Colorado BEN NELSON, Nebraska LAMAR ALEXANDER, Tennessee CHARLES KIEFFER, Staff Director BRUCE EVANS, Minority Staff Director SUBCOMMITTEE ON DEPARTMENTS OF LABOR, HEALTH AND HUMAN SERVICES, AND EDUCATION, AND RELATED AGENCIES TOM HARKIN, Iowa, Chairman DANIEL K. INOUYE, Hawaii ARLEN SPECTER, Pennsylvania HERB KOHL, Wisconsin THAD COCHRAN, Mississippi PATTY MURRAY, Washington JUDD GREGG, New Hampshire MARY L. -
Sago Mine Disaster and an Overview of Mine Safety Hearing
S. HRG. 109–534 SAGO MINE DISASTER AND AN OVERVIEW OF MINE SAFETY HEARING BEFORE A SUBCOMMITTEE OF THE COMMITTEE ON APPROPRIATIONS UNITED STATES SENATE ONE HUNDRED NINTH CONGRESS SECOND SESSION SPECIAL HEARING JANUARY 23, 2006—WASHINGTON, DC Printed for the use of the Committee on Appropriations ( Available via the World Wide Web: http://www.gpoaccess.gov/congress/index.html U.S. GOVERNMENT PRINTING OFFICE 27–461 PDF WASHINGTON : 2006 For sale by the Superintendent of Documents, U.S. Government Printing Office Internet: bookstore.gpo.gov Phone: toll free (866) 512–1800; DC area (202) 512–1800 Fax: (202) 512–2250 Mail: Stop SSOP, Washington, DC 20402–0001 COMMITTEE ON APPROPRIATIONS THAD COCHRAN, Mississippi, Chairman TED STEVENS, Alaska ROBERT C. BYRD, West Virginia ARLEN SPECTER, Pennsylvania DANIEL K. INOUYE, Hawaii PETE V. DOMENICI, New Mexico PATRICK J. LEAHY, Vermont CHRISTOPHER S. BOND, Missouri TOM HARKIN, Iowa MITCH MCCONNELL, Kentucky BARBARA A. MIKULSKI, Maryland CONRAD BURNS, Montana HARRY REID, Nevada RICHARD C. SHELBY, Alabama HERB KOHL, Wisconsin JUDD GREGG, New Hampshire PATTY MURRAY, Washington ROBERT F. BENNETT, Utah BYRON L. DORGAN, North Dakota LARRY CRAIG, Idaho DIANNE FEINSTEIN, California KAY BAILEY HUTCHISON, Texas RICHARD J. DURBIN, Illinois MIKE DEWINE, Ohio TIM JOHNSON, South Dakota SAM BROWNBACK, Kansas MARY L. LANDRIEU, Louisiana WAYNE ALLARD, Colorado J. KEITH KENNEDY, Staff Director TERRENCE E. SAUVAIN, Minority Staff Director SUBCOMMITTEE ON DEPARTMENTS OF LABOR, HEALTH AND HUMAN SERVICES, AND EDUCATION, AND RELATED AGENCIES ARLEN SPECTER, Pennsylvania, Chairman THAD COCHRAN, Mississippi TOM HARKIN, Iowa JUDD GREGG, New Hampshire DANIEL K. INOUYE, Hawaii LARRY CRAIG, Idaho HARRY REID, Nevada KAY BAILEY HUTCHISON, Texas HERB KOHL, Wisconsin TED STEVENS, Alaska PATTY MURRAY, Washington MIKE DEWINE, Ohio MARY L.