Principles of Machining Processes
Total Page:16
File Type:pdf, Size:1020Kb
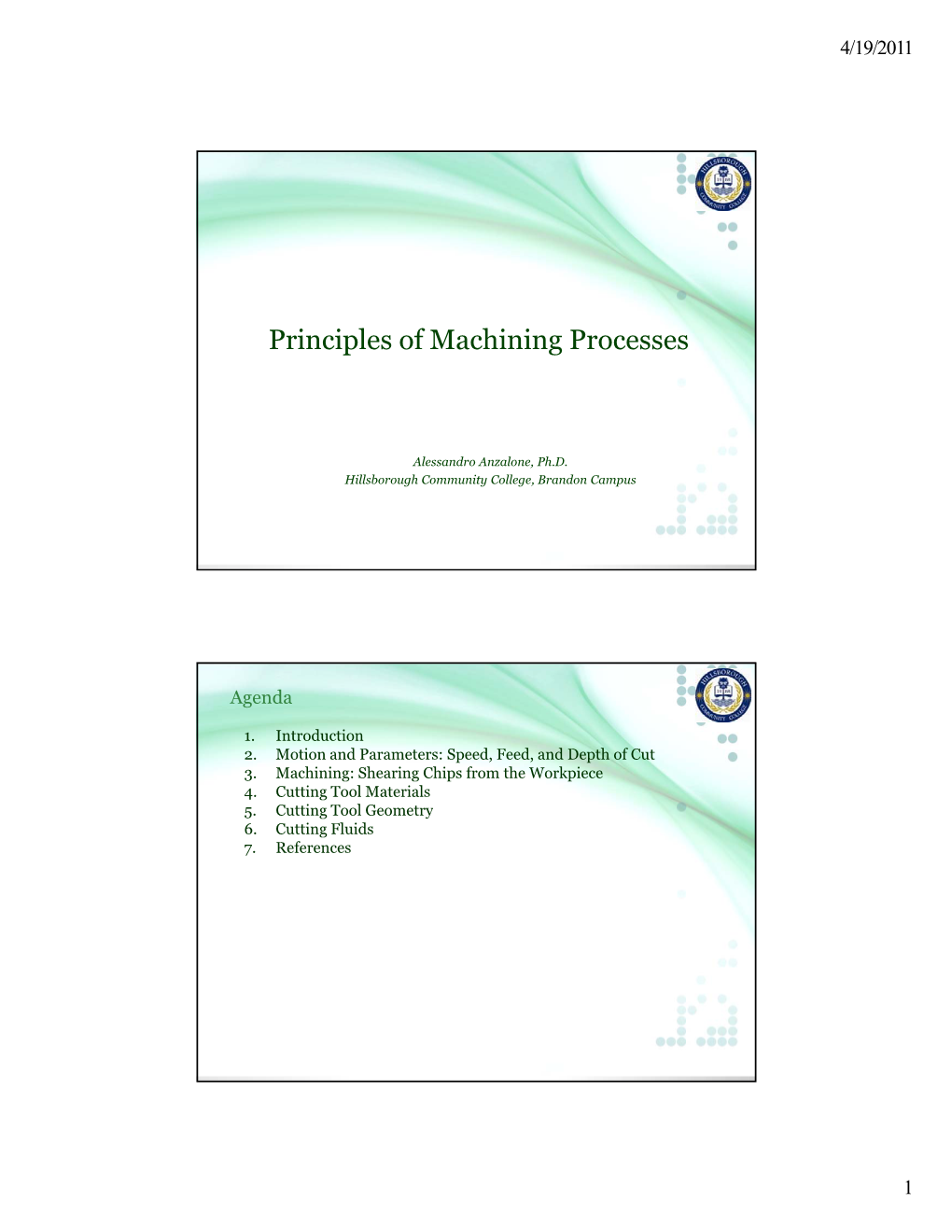
Load more
Recommended publications
-
Cutting Tools — Trends of Functional Upgrading, Resource Saving Technologies and New Products —
Prefatory Note Special Issue: Cutting Tools — Trends of Functional Upgrading, Resource Saving Technologies and New Products — Yoshihiro Minato Executive Officer and General Manager Advanced Materials R&D Laboratories Of all the tools used for cutting ferrous metals and non- made by sintering CBN, using a specially prepared ceramic ferrous metals, about 90% are cemented carbide or coated binder whose affinity with steel is extremely low. Subse- cemented carbide tools. Cemented carbide (WC-Co) is a quently, another type of CBN sintered body was developed composite material of a tungsten carbide (WC) phase and a by coating specially sintered CBN base material with a highly cobalt (Co) binder phase. It was invented in Germany in wear-resistant ceramic film. Coated CBN sintered body tools 1923 and put on the market in 1927 by the German corpo- are widely used today to cut hardened steels that are ex- ration Krupp AG under the trade name “WIDIA.” Subse- tremely difficult to cut in place of grinding. quently, Sumitomo Electric Industries, Ltd. succeeded in its Metal cutting technology has progressed and developed test manufacture of a cemented carbide wire-drawing die in in conjunction with three elements: tool materials, tool de- 1928, and commercialized a cemented carbide tool in 1931. sign/geometry, and machine tools. Among the above ele- This tool has been marketed under the brand name of ments, Sumitomo Electric has promoted the development of “IGETALLOY” ever since. In 2011, Sumitomo Electric cele- advanced tool materials and tool design/geometry. In the brated 80 years of marketing this product. In the early 1900s, very competitive market environment surrounding cutting high-speed steel tools were used for steel cutting operations. -
Coatings of Cutting Tools and Their Contribution to Improve Mechanical Properties: a Brief Review
International Journal of Applied Engineering Research ISSN 0973-4562 Volume 13, Number 14 (2018) pp. 11653-11664 © Research India Publications. http://www.ripublication.com Coatings of Cutting Tools and Their Contribution to Improve Mechanical Properties: A Brief Review Noor Atiqah Badaluddin1, Wan Fathul Hakim W Zamri1*, Muhammad Faiz Md Din2, Intan Fadhlina Mohamed1 and Jaharah A Ghani1 1Centre for Materials Engineering and Smart Manufacturing (MERCU), Faculty of Engineering and Built Environment, Universiti Kebangsaan Malaysia, 43600 Bangi, Selangor, Malaysia. 2 Faculty of Engineering, Universiti Pertahanan Nasional Malaysia, Kem Sungai Besi, 57000 Kuala Lumpur, Wilayah Persekutuan Kuala Lumpur, Malaysia. (Corresponding Author *) Abstract types of coating structures and materials can be combined to produce high-performance cutting tools. The coating not only Cutting is an important process in the manufacturing industry. functions to extend the lifetime of the cutting tool but it also It is necessary to use good quality cutting tools in order to acts as a protection against wear, especially against abrasions maintain the quality of a product. The coating on a cutting and adhesions, in cutting tool applications. The strength of the tool has a great impact in terms of the mechanical and coating is dependent on the material used for the coating, but tribological properties as well as the end results of the studies have shown that a more layered structure will further product. A cutting tool can made of various types of materials, enhance the hardness of the coating and increase its resistance but the most commonly used material in the industry today is to wear. Currently, a combination of various materials such as cemented tungsten carbide as its characteristics meet the TiALN/TiN, TiCN/TiSiN/TiAlN and many more are being requirements of manufacturers. -
Contents Cutting Tools and Cutting Materials
CONTENTS 1. Cutting tools and cutting materials 1.1 cutting tools- various types of single point cutting tools and their uses, single point cutting too geometry, tool signature and its effect, heat produced during cutting and its effect, cutting speed, feed and depth of cut and their effect 1.2 Cutting tool materials- properties of cutting tool material, study of various cutting tool materials viz. high-speed steel, tungsten carbide, cobalt steel cemented carbides, satellite, ceramics and diamond CUTTING TOOLS AND CUTTING MATERIALS 1.1 INTRODUCTION Cutting material are shaped with the help of cutting tool into usable forms through various processes. The work pieces of most different shapes and sizes and of different materials are worked. 1.2 CUTTING TOOLS The tools which are used for the purpose of cutting the metals in the desired shape and size are called cutting tools. 1.2.1 Classification of cutting tools: Cutting tools are classified into groups. 1. Single point cutting tool. 2. Multi point cutting tool. 1.2.2 Various types of single point cutting tools: Tools for lathe machines On a lathe machine to perform different operations different tools are required. i. Turning tool ii. Facing tool iii. Chamfering tool iv. External threading tool v. Internal threading tool vi. Boring tool vii. Grooving tool, etc. Tool for planer The planer tools are made of high speed steel. Cemented carbide tipped tools are also used. The shape of the tool depends on the type of operation to be performed. Different single point cutting tools are given below: i. Straight and bent roughing tools ii. -
Cutting Performance and Wear/Damage Characteristics of PCBN Tool in Hard Milling
applied sciences Article Cutting Performance and Wear/Damage Characteristics of PCBN Tool in Hard Milling Haining Gao *, Xianli Liu and Zhitao Chen School of Mechanical and Power Engineering, Harbin University of Science and Technology, Harbin 150080, China; [email protected] (X.L.); [email protected] (Z.C.) * Correspondence: [email protected]; Tel.: +136-5466-2869 Received: 6 January 2019; Accepted: 19 February 2019; Published: 22 February 2019 Abstract: In the intermittent machining of hardened steel for the die and mold industry, determining how to reduce the wear of PCBN (Polycrystalline Cubic Boron Nitride) tools and improve their machining efficiency and quality is an important subject. This study investigated the intermittent machining of hardened steel (Cr12MoV, 59HRC (Rockwell hardness)) using uncoated PCBN tools to determine the cutting performance (cutting force, chip morphology, surface quality, tool life, cutting temperature) and the wear/damage characteristics of the tools. The results showed that the cutting performance of a PCBN tool was better than that of a cemented carbide tool. The wear mechanism on the PCBN tool flank was diffusion wear, adhesive wear, and oxidation wear. The main failure modes of the PCBN tool in the machining process of hardened steel at low speed were tool micro-chipping, the conchoidal damage of the rake face, and the larger damaged area of the flank face. The main failure modes of the PCBN tool in the machining process of hardened steel at high speed were flank wear and high-rate fatigue damage. Keywords: cutting performance; wear characteristics; damage characteristics; PCBN tool; low-rate damage 1. Introduction PCBN is a cutting tool material most widely used in the machining of hardened steel due to its higher hardness, strength, thermal and chemical stability, and thermal conductivity, and lower friction coefficient than other tool materials at high temperature [1–3]. -
Cutting Tool Materials for High Speed Machining*
PROGRESS IN NATURAL SCIENCE Vol .15 , N o .9 , September 2005 Cutting tool materials for high speed machining* LIU Zhanqiang ** and AI Xing (School of Mechanical Engineering , S handong University , Jinan 250061 , China) Received Feb ruary 22 , 2005 ;revised March 28 , 2005 Abstract High speed machining (HSM)is one of the emerging cutting processes, w hich is machining at a speed significantly higher than the speed commonly in use on the shop floor .In the last tw enty years, high speed machining has received g reat attentions as a technological solution for high productivity in manufactu ring .This article review s the developments of tool materials in high speed ma- chining operations, and the properties, applications and prospective developments of tool materials in HSM are also presented . Keywords: tool materials, high speed machining. High speed machining processes can produce plications fo r each type of the material . more accurate parts , as well as reduce the costs asso- ciated w ith assembly and fixture storage by allow ing several procedures to be combined into a mo nolithic one[ 1] .There has been a stro ng resurgence of interest in high speed machining technology , so that it has become one of the most promising advanced manufac- turing technologies in the last tw enty years .Hig h speed machining technology has already been applied to many manufacturing industries such as the aviation and aerospace industry , automobile industry , mould industry to cut steel , cast iron and its alloys , alu- minum and magnesium alloys , super alloy s of nickel- based , cobalt-based , ferrous-based , titanium-based , Fig .1 . -
History of Development of Cemented Carbides and Cermet Pdf 1.5 MB
FEATURED TOPIC History of Development of Cemented Carbides and Cermet Keiichi TSUDA ---------------------------------------------------------------------------------------------------------------------------------------------------------------------------------------------------------------------------------------------------------- Cemented carbide was first commercialized by our company in 1928 for use in wire drawing dies. It has since been developed as a base material for cutting tools. First, titanium carbide was added to make the tools suitable for steel cutting, and then the ACE layer technology was developed in order to toughen the cemented carbide substrate. Zirconium was added to cemented carbide substrates in response to user requests for efficient machining. Meanwhile, cermet, base material that consists of a hard titanium phase and was originally created for use in jet engines, was developed for cutting tools because of their low reactivity with steel and fine cutting surface. Although toughness was an issue with cermet, it was solved by nitrogen doping. The subsequently developed surface hardening technology further improved their toughness and wear resistance, and thereby cutting performance. This paper details the history of the development of Igetalloy cemented carbide and cermet. ---------------------------------------------------------------------------------------------------------------------------------------------------------------------------------------------------------------------------------------------------------- -
Carbide Materials Brazed Tools
Carbide Materials Carbide Materials Brazed Tools Tools Brazed K1 to K13 K K K Carbide Material Features and Applications …… K2 Plate Blanks ………………………………………… K4 Rod Blanks …………………………………………… K5 Special Rod Blanks ………………………………… K6 JIS Type Inserts for Carbide Tool Holders ……… K8 JIS Type Carbide Tool Holders …………………… K9 Jig Boring Tools IJB Type ……………………… K12 D D mark: Standard stocked item * mark: Semi-standard stock (please confirm stock availability) Stock Markings and Symbols D mark: To be replaced with the new item featured on the same page S mark: Stock or planned stock (please confirm stock availability) F mark: To be replaced by a new product, made to order, or discontinued Blank: Made-to-order item (please confirm stock availability). - mark: Not available K1 Cemented Carbide Material Features and Applications D Stringent selection of high purity and high quality raw materials D Consistent quality and shorter delivery with the latest production facilities and techniques D Fully equipped with a system that ensures the highest quality D Constant R&D to develop the latest grades Grade Map D Hardness and Transverse Rupture Strength D Co Content vs Hardness Brazed Tools Brazed Carbide Materials Good 5 Good 94 AFU F0 AF1 XF1 KH15 AF0 XF1 AF0 KH12 93 4 AFU H1 ZF16A K EH10 ZF16A AF1 A1 KH05 EH10 KH12 3 92 KH15 KH03 KH03 A1 2 Resistance Wear 91 H1 F0 Fracture Resistance Fracture KH05 (HRA) 90 (GPa) 90 91 92 93 94 6912 15 TRS Hardness (HRA) Wear Resistance Good Good Rigidity Co content (wt%) Hardness Hardness Grade Properties and Features -
The Critical Raw Materials in Cutting Tools for Machining Applications: a Review
materials Review The Critical Raw Materials in Cutting Tools for Machining Applications: A Review Antonella Rizzo 1,*, Saurav Goel 2,3 , Maria Luisa Grilli 4 , Roberto Iglesias 5 , Lucyna Jaworska 6,7, Vjaceslavs Lapkovskis 8 , Pavel Novak 9, Bogdan O. Postolnyi 10,11 and Daniele Valerini 1 1 ENEA–Italian National Agency for New Technologies, Energy and Sustainable Economic Development, Brindisi Research Centre, S.S. 7 Appia–km 706, 72100 Brindisi, Italy; [email protected] 2 School of Engineering, London South Bank University, 103 Borough Road, London SE1 0AA, UK; saurav.goel@cranfield.ac.uk 3 School of Aerospace, Transport and Manufacturing, Cranfield University, Cranfield MK4 30AL, UK 4 ENEA–Italian National Agency for New Technologies, Energy and Sustainable Economic Development, Casaccia Research Centre, Via Anguillarese 301, 00123 Rome, Italy; [email protected] 5 Department of Physics, University of Oviedo, Federico Garcia Lorca 18, ES-33007 Oviedo, Spain; [email protected] 6 Łukasiewicz Research Network, Institute of Advanced Manufacturing Technology, 30-011 Krakow, Poland; [email protected] 7 Faculty of Non-Ferrous Metals, AGH University of Science and Technology, 30-059 Krakow, Poland 8 Faculty of Civil Engineering, Scientific Laboratory of Powder Materials/Faculty of Mechanical Engineering, Institute of Aeronautics, 6A Kipsalas str, lab. 110, LV-1048 Riga, Latvia; [email protected] 9 Department of Metals and Corrosion Engineering, University of Chemistry and Technology, Prague, Technická 5, 166 28 Prague -
TABLE of CONTENTS 974 CUTTING SPEEDS and FEEDS 978 Cutting Tool Materials 982 Cutting Speeds 983 Cutting Conditions 983 Selectin
TABLE OF CONTENTS MACHINING OPERATIONS CUTTING SPEEDS AND FEEDS ESTIMATING SPEEDS AND MACHINING POWER 978 Cutting Tool Materials 982 Cutting Speeds 1044 Planer Cutting Speeds 983 Cutting Conditions 1044 Cutting Speed and Time 983 Selecting Cutting Conditions 1044 Planing Time 983 Tool Troubleshooting 1044 Speeds for Metal-Cutting Saws 985 Cutting Speed Formulas 1044 Turning Unusual Material 987 RPM for Various Cutting Speeds 1046 Estimating Machining Power and Diameter 1046 Power Constants SPEED AND FEED TABLES 1047 Feed Factors 1048 Tool Wear Factors 991 Introduction 1050 Metal Removal Rates 991 Feeds and Speeds Tables 1051 Estimating Drilling Thrust, 995 Speed and Feed Tables for Turning Torque, and Power 1000 Tool Steels 1053 Work Material Factor 1001 Stainless Steels 1053 Chisel Edge Factors 1002 Ferrous Cast Metals 1054 Feed Factors 1004 Turning-Speed Adjustment 1055 Drill Diameter Factors Factors MACHINING ECONOMETRICS 1004 Tool Life Factors 1005 Adjustment Factors for HSS 1056 Tool Wear And Tool Life Tools Relationships 1006 Copper Alloys 1056 Equivalent Chip Thickness (ECT) 1007 Titanium and Titanium Alloys 1057 Tool-life Relationships 1008 Superalloys 1061 The G- and H-curves 1009 Speed and Feed Tables for Milling 1062 Tool-life Envelope 1012 Slit Milling 1065 Forces and Tool-life 1013 Aluminium Alloys 1067 Surface Finish and Tool-life 1014 Plain Carbon and Alloy Steels 1069 Shape of Tool-life Relationships 1018 Tool Steels 1070 Minimum Cost 1019 Stainless Steels 1071 Production Rate 1021 Ferrous Cast Metals 1071 The Cost Function -
Machining Nickel Alloys
NiDl Nickel Development Institute Machining nickel alloys A Nickel Development Institute Reference Book, Series No 11 008 Table of Contents Acknowledgments ............................................................................................ i Abbreviation key ............................................................................................... i Introduction ...................................................................................................... ii Nickel alloys and machinability ......................................................................1 Basic principles applicable to all machining operations .............................3 Work hardening .....................................................................................3 Choice of cutting tools ...........................................................................3 Lubricants and coolants ........................................................................4 Recommendations for machining ..................................................................5 Turning, boring and grooving ................................................................5 High speed steel tooling ....................................................................5 Carbide tooling ...................................................................................6 Ceramic tooling ..................................................................................7 Insert selection and method of use ....................................................9 Taking -
ASM Specialty Handbook: Tool Materials Copyright © 1995 ASM International® Joseph R
ASM Specialty Handbook: Tool Materials Copyright © 1995 ASM International® Joseph R. Davis, Editor All rights reserved www.asminternational.org General Guidelines for Selecting Cutting Tool Materials SELECTING Tiffi PROPER CUTIING Because of the wide range of conditions and • TYpe, capability, and condition of the machine TOOL MATERIAL for a specific machining ap requirements, no single cutting tool material tool to be used plication can provide substantial advantages, in meets the needs of all machining applications. • Rigidity of the tool and workpiece cluding increased productivity, improved quality, Each tool material has its own combination of • Production requirements influencing the and reduced costs (Ref 1). Increased productivity properties that makes it best for a specific opera~ speeds and feeds selected can be obtained by increasing cutting speeds tion. The fol1owing factors affect the selection of • Operating conditions, such as cutting forces and/or feed rates. Increasing the speeds and feeds, a cutting tool material for a specific application and temperatures however, is limited by the capability of the cUt (Ref 1): • Tool cost per part machined, including initial ting tool material and machine tool. Speeds and tool cost, grinding cost, tool life, frequency of feeds must be kept low enough to provide an • Hardness and condition of the workpiece rna~ regrinding or replacement, and labor cost. The terial acceptable tool life. Otherwise, tool changing and most economical tool is not necessarily the one • Operations to be performed (optimum tool se~ grinding costs can outweigh the advantages of providing the longest life or having the lowest lection may reduce the number of operations faster machining rates by increasing the cost per initial cost. -
Dry Turning of Tempered Martensitic Stainless Tool Steel Using Coated Cermet and Coated Carbide Tools M.Y
View metadata, citation and similar papers at core.ac.uk brought to you by CORE provided by Universiti Teknologi Malaysia Institutional Repository Journal of Materials Processing Technology 185 (2007) 83–90 Dry turning of tempered martensitic stainless tool steel using coated cermet and coated carbide tools M.Y. Noordin ∗, V.C. Venkatesh, S. Sharif Department of Manufacturing and Industrial Engineering, Faculty of Mechanical Engineering, Universiti Teknologi Malaysia, 81310 UTM Skudai, Malaysia Abstract Turning trials were performed under dry cutting conditions with constant depth of cut in order to investigate the usability of coated TiCN based cermet (KT 315) and coated carbide (KC 9110) cutting tools to turn tempered martensitic stainless tool steel with hardness in the 43–45 HRC range. Cutting speed, feed and the side cutting edge angle (SCEA) of the tool were the independent variables considered. Regardless of the cutting tool material, cutting speed and feed expectedly have an effect on tool wear and tool life. Additionally, the SCEA is found to influence the tool life where the tool life increases, as the SCEA was changed from 0◦ to −5◦. The longest tool life was attainable when cutting with KT 315 at low cutting speed and feed rate when using −5◦ SCEA. However, in all other instances, KC 9110 outperforms KT 315. This is particularly evident at medium and high cutting speeds and feed. The constant and exponent for the various Taylor tool life equations have been determined. Flank wear, end clearance wear and catastrophic failure were the main types of tool failure mode determining tool life. The wear mechanisms for the various tool failure modes were suggested.