Optimization-Based Energy Management for Multi-Energy Maritime Grids Springer Series on Naval Architecture, Marine Engineering, Shipbuilding and Shipping
Total Page:16
File Type:pdf, Size:1020Kb
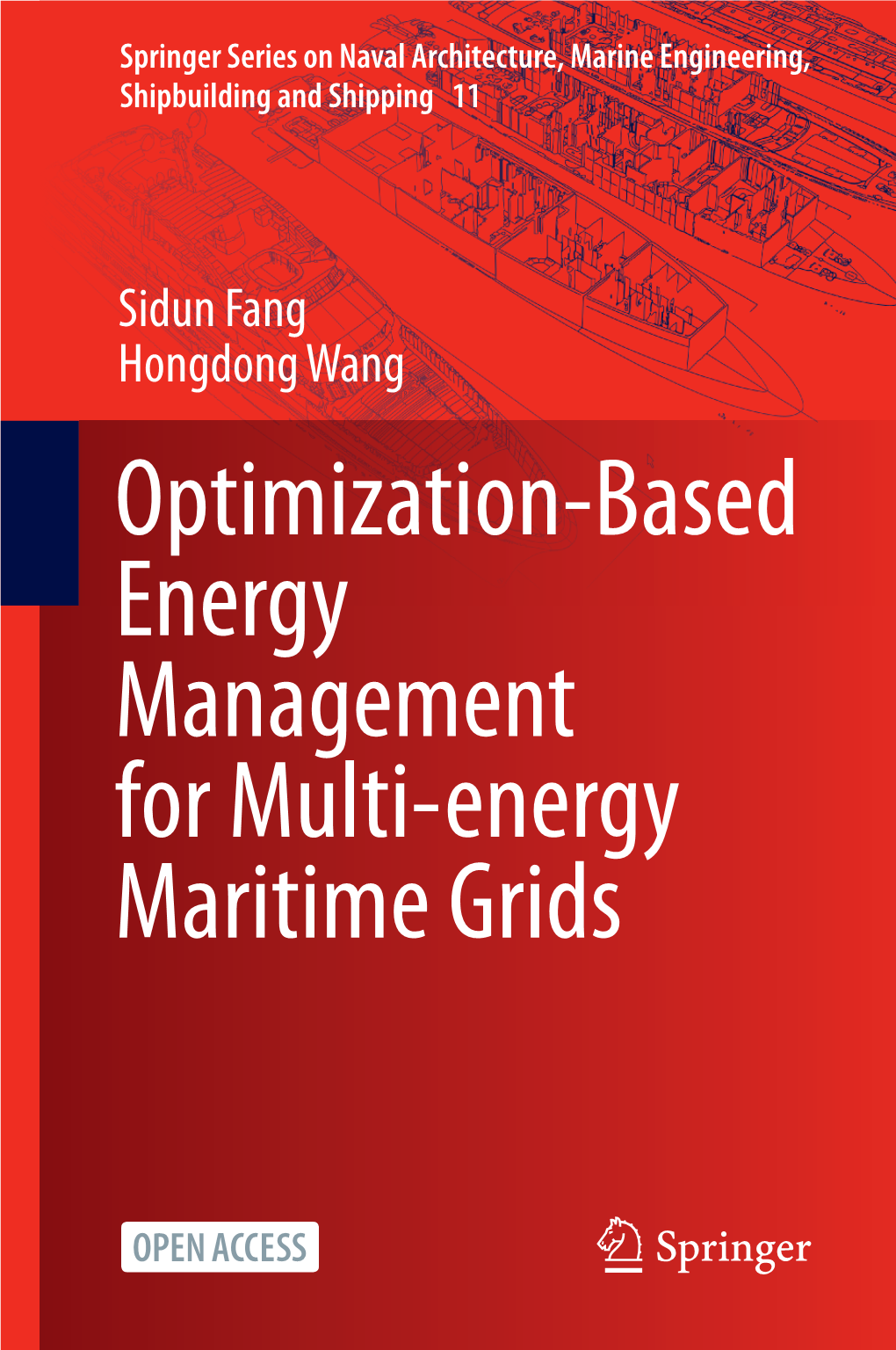
Load more
Recommended publications
-
Disposal Mandate in Relation to the Future Disposal of Ordinary Shares of Norwegian Cruise Line Holdings Ltd
THIS CIRCULAR IS IMPORTANT AND REQUIRES YOUR IMMEDIATE ATTENTION If you are in any doubt as to any aspect of this circular or as to the action to be taken, you should consult your licensed securities dealer, bank manager, solicitor, professional accountant or other professional adviser. If you have sold or transferred all your shares in Genting Hong Kong Limited, you should at once hand this circular to the purchaser or to the bank, licensed securities dealer or other agent through whom the sale or transfer was effected for transmission to the purchaser or transferee. Hong Kong Exchanges and Clearing Limited and The Stock Exchange of Hong Kong Limited take no responsibility for the contents of this circular, make no representation as to its accuracy or completeness and expressly disclaim any liability whatsoever for any loss howsoever arising from or in reliance upon the whole or any part of the contents of this circular. Genting Hong Kong Limited (Continued into Bermuda with limited liability) (Stock Code: 678) DISPOSAL MANDATE IN RELATION TO THE FUTURE DISPOSAL OF ORDINARY SHARES OF NORWEGIAN CRUISE LINE HOLDINGS LTD. POSSIBLE VERY SUBSTANTIAL DISPOSAL AND NOTICE OF SPECIAL GENERAL MEETING The notice convening the special general meeting (“SGM”) of Genting Hong Kong Limited (the “Company”) to be held at Suite 1501, Ocean Centre, 5 Canton Road, Tsimshatsui, Kowloon, Hong Kong SAR on Friday, 15 June 2018 at 11:30 a.m. (or as soon as practicable immediately after the conclusion or adjournment of the annual general meeting of the Company convened to be held at 11:00 a.m. -
BLÜCHER Marine References
BLÜCHER Marine References Country Project Shipyard Owner Vessel Type Hull no. Year Argentina Frigate Naval Shipyard Frigate Frigate Refitting 2005 Australia Australian Customs and Austal Ships Australian Customs and Border Cape Class Patrol Boat 361 2013 Border Protection Service Protection Service Australia Australian Customs and Austal Ships Australian Customs and Border Cape Class Patrol Boat 362 2013 Border Protection Service Protection Service Australia Australian Customs and Austal Ships Australian Customs and Border Cape Class Patrol Boat 363 2013 Border Protection Service Protection Service Australia Australian Customs and Austal Ships Australian Customs and Border Cape Class Patrol Boat 364 2013 Border Protection Service Protection Service Australia Australian Customs and Austal Ships Australian Customs and Border Cape Class Patrol Boat 365 2014 Border Protection Service Protection Service Australia Australian Customs and Austal Ships Australian Customs and Border Cape Class Patrol Boat 366 2014 Border Protection Service Protection Service Australia Australian Customs and Austal Ships Australian Customs and Border Cape Class Patrol Boat 367 2014 Border Protection Service Protection Service Australia Australian Customs and Austal Ships Australian Customs and Border Cape Class Patrol Boat 368 2014 Border Protection Service Protection Service Australia Australian Defence Civmec/ASC Australian Defence OPV OPV1 2019 Australia Australian Defence - ASC Shipyard Australian Defence Air Warfare Destroyer 2012 AWD Australia Australian Defence - LHD BAE Systems Australian Defence Landing Helicpoter 2012 Dock Australia Dick Smith Tenix Dick Smith Ocean Research Ulysses Blue 2005 Vessel Australia Esso West Tuna Esso Platform 1996 Australia HMAS Arunta BAE Systems Australian Defence ANZAC Frigate ANZAC 2019 Australia Jean de la Valette - Virtu Austal Ships Virtu Ferries High Speed Ferry 248 2010 Ferries Australia RNZN Tenix RNZN Ocean Research 42826 2006 Vessel Australia Taylor Bros. -
Carbon Emissions MANAGEMENT PLAN
Carbon Emissions MANAGEMENT PLAN Prepared for SWACO February 2020 prepared by Contents Section 1.0 Introduction .........................................................1 A Changing Climate . .. 1 SWACO’s Commitment . 2 Using this Plan . 2 Section 2.0 Carbon Footprint Evaluation .......................................3 Footprint Definition . 3 Methodology . 3 Monitoring . 4 Section 3.0 Benchmarking ..............................................5 Section 4.0 Goal Setting ..............................................6 Methodology . 6 Organization-wide Goal . 6 Section 5.0 Implementing .........................................7 Landfill Gas Emissions Management . 7 Vehicle and Equipment Fuel Management . 8 Building Energy Management . 8 Waste Management . 8 Section 6.0 Future Considerations ............................9 Appendices Appendix A: Benchmarking Assessment . 11 Appendix B: Carbon Management Strategic Initiatives Matrix . 15 Appendix C: Strategic Initiative Decision Trees . 17 Photo Caption LIST OF ACRONYMS CH4 GWP SBTI Methane Global Warming Science-Based Potential Target Initiative CO2 IPCC SWACO Carbon Dioxide Intergovernmental Solid Waste Authority Panel on Climate of Central Ohio Control CO2e N2O Carbon Dioxide Nitrous Oxide Equivalent Introduction SECTION 1.0 Introduction A CHANGING CLIMATE In the atmosphere, carbon dioxide (CO2), methane above 1.5°C (2.7°F) will result in increasingly significant (CH4), nitrous oxide (N2O), and certain fluorinated impacts of climate change. To limit the increase to gases, collectively referred -
A Citizen's Guide to BOEM's Renewable Energy Authorization Process
A Citizen’s Guide TO THE BUREAU OF OCEAN ENERGY MANAGEMENT’S RENEWABLE ENERGY AUTHORIZATION PROCESS December 2016 Overview This guide is intended to help the public understand the Bureau of Ocean Energy Management’s (BOEM) process for overseeing renewable energy projects on the Outer Continental Shelf (OCS) and to highlight opportunities for public involvement. About BOEM BOEM is the Bureau within the U.S. Department of the Interior responsible for managing development of the nation’s offshore energy resources in an environmentally and economically responsible way. BOEM promotes energy independence, environmental protection, and economic development through responsible, science-informed management of offshore energy resources. Introduction The United States is experiencing increased interest in the development of marine energy projects using wind, wave, and ocean current technologies. These types of renewable energy sources can provide densely populated coastal communities with a clean source of electrical power while helping to diversify the U.S. electrical supply. For additional information on offshore renewable energy technology, see BOEM’s “Offshore Renewable Energy Guide” at http://www.boem.gov/Offshore- Renewable-Energy-Guide/. In 2016, the U.S. Department of Energy (DOE) estimated 10,800 gigawatts (GW) of offshore wind energy could be accessed within the 200 nautical miles (nm) Exclusive Economic Zone (EEZ) boundary. DOE estimates offshore wind energy capacity recoverable given current technical capabilities to be 2,058 GW, with an energy generation potential almost double the electricity consumption of the United States. 2 | A Citizen’s Guide to the Bureau of Ocean Energy Management’s Renewable Energy Authorization Process BOEM’s Regulatory Authority for Renewable Energy Activities BOEM is the federal agency responsible for issuing leases, easements, and rights-of-way for renewable energy projects on the OCS. -
List of Registered Vessels Effective Date for EPD Reg
Environmental Protection Department Extended Port Facilities and Light Dues Incentive Scheme List of Registered Vessels Effective date for EPD Reg. registration Vessel Name IMO No. Call Sign Type of Vessel Nationality of Vessel Remarks No. (DD/MM/YYYY) N00001 1/7/2015 MAGNAVIA 9122447 A8BI5 CONTAINER LIBERIA N00002 1/7/2015 KARIN 9220433 A8IK5 CONTAINER LIBERIA N00003 1/7/2015 UNI ASSENT 9130585 3FBD9 CONTAINER PANAMA N00004 1/7/2015 UNI ASPIRE 9130573 3FVN8 CONTAINER PANAMA N00005 1/7/2015 UNI POPULAR 9202209 3FZG9 CONTAINER PANAMA N00006 1/7/2015 EVER PRIDE 9249233 VQGH8 CONTAINER UNITED KINGDOM OF GREAT BRITAIN N00007 1/7/2015 EVER UNITED 9116589 9V7957 CONTAINER SINGAPORE N00008 1/7/2015 EVER DYNAMIC 9142198 3FUB8 CONTAINER PANAMA N00009 1/7/2015 VANTAGE 9628192 9HA3435 CONTAINER MALTA N00010 1/7/2015 KARMEN 8906731 A8XJ9 CONTAINER LIBERIA N00011 1/7/2015 EVER UNIFIC 9168843 9V7961 CONTAINER SINGAPORE N00012 1/7/2015 ITAL MODERNA 9349629 ICAM CONTAINER ITALY N00013 1/7/2015 EVER PRIMA 9249245 VQUK5 CONTAINER UNITED KINGDOM OF GREAT BRITAIN N00014 1/7/2015 EVER DEVELOP 9142174 3FLF8 CONTAINER PANAMA N00015 1/7/2015 VALUE 9628166 9HA3355 CONTAINER MALTA N00016 1/7/2015 EVER LENIENT 9604146 2HDF9 CONTAINER UNITED KINGDOM OF GREAT BRITAIN N00017 1/7/2015 ITAL UNIVERSO 9196993 IBSP CONTAINER ITALY N00018 1/7/2015 UNI PACIFIC 9202156 3FCE9 CONTAINER PANAMA N00019 1/7/2015 EVER SMILE 9300415 MLTH5 CONTAINER UNITED KINGDOM OF GREAT BRITAIN N00020 1/7/2015 EVER SMART 9300403 MLBD9 CONTAINER UNITED KINGDOM OF GREAT BRITAIN N00021 1/7/2015 EVER -
Water Power for a Clean Energy Future
WATERWIND & POWER WATER PROGRAM POWER PROGRAM WATER POWER FOR A CLEAN ENERGY FUTURE March 2016 WATER POWER PROGRAM Building a Clean Energy Economy Leading the world in clean energy is critical to strengthening the American economy. Targeted investments in clean en- ergy research and development jumpstart private sector innovation critical to our long-term economic growth, energy security, and international competitiveness. The U.S. Department of Energy (DOE) Water Power Program (the Pro- gram) is strengthening the nation’s global position by funding cutting-edge research to produce the next generation of hydropower and marine and hydrokinetic (MHK) technologies, and by accelerating the development of markets for those technologies. Currently, the hydropower industry employs 200,000–300,000 workers in the United States, making it not only the longest-running, but also the largest renewable electricity production workforce in the nation. However, there has been a lack of consistent hydropower educational programs in the United States. In an effort to increase our nation’s knowledge and skills in this area, the Program has sponsored new graduate research opportunities to train the next generation of hydropower specialists and engineers. The newly emerging MHK industry holds tremendous potential for job growth as MHK technologies progress to- wards commercial readiness. The Program invests in fellowships that fund graduate-level training and sends U.S. researchers to advanced European research facilities to establish partnerships, boost innovation, and facilitate knowledge sharing. By capitalizing on water power’s significant potential for sustainable growth, the United States can add thousands of clean energy jobs while building a sustainable, renewable energy future. -
Norwegian Cruise Line
NORWEGIAN CRUISE LINE February 20, 2019 1 THE INNOVATOR IN CRUISING Freedom and Flexibility - 52 years of innovation in dining, entertainment, recreation and more - 16 ships - 2 resort destinations - 36 global ports - 300 destinations worldwide Youngest Fleet with a Global Presence Award-Winning Entertainment Exclusive Experiences (Jersey Boys on Norwegian Bliss) (Race track on Norwegian Joy and Bliss) 2 THE INNOVATOR IN CRUISING First to offer branded entertainment at sea Leader in innovative activities (Kinky Boots to debut on Norwegian Encore) (Open-air laser tag arena on Norwegian Bliss) First to offer Studios Innovator offering Bringing guests closer to the -Designed/priced for single traveler- Freestyle Dining & Entertainment majesty of the ocean (Studio on Norwegian Bliss) (27 Restaurant and Bar Options) (The Waterfront Promenade) 3 EXPERIENCES & DESTINATIONS First Private Island Experience Exclusive Hawaii Offering Authentic Alaska Experience (Great Stirrup Cay, Bahamas) (Pride of America) (Icy Strait Point) Overnights in Havana, Cuba Immersive Itineraries Private Resort Destination (Norwegian Sun & Sky) (Three-day excursion to Machu Picchu) (Harvest Caye, Belize) 4 PORT PARTNERSHIP/INVESTMENT Bell Street Pier, Seattle (2017) Icy Strait Point, Alaska (2020) Tortola, British Virgin Islands (2015) 5 THE PEARL OF MIAMI New Terminal B at PortMiami (2020) ❑ 166,500 square feet ❑ Up to 5,000 guests ❑ LEED-Silver standards ❑ State-of-the-art technology ❑ Expedited embarkation 6 NORWEGIAN EDGE® PROGRAM 2018 Norwegian Sun Norwegian Star -
Deloitte Resources 2017 Study Energy Management: Sustainability and Progress Contents
Deloitte Resources 2017 Study Energy management: Sustainability and progress Contents About the study 3 Executive summary 5 Residential consumer views on energy management 7 Detailed residential consumer findings 8 Business views on energy management 25 Detailed business findings 26 Concluding thoughts 46 Endnotes 49 Contacts 50 2 About the study Deloitte1, with strategy and market research firm Harrison The 2017 Study was conducted in March 2017, and thus, Group, a YouGov company, has completed its seventh largely reflects attitudes and practices related to the annual nationwide Resources Study (the “2017 Study” or year 2016. The Study captures two views: a residential “Study”) to provide insights that can be useful in helping consumer perspective and a business perspective. The energy companies and businesses make energy-related residential consumer portion is based on more than 1,500 investment and business decisions. The Study aims to demographically balanced online interviews with household answer questions such as: decision-makers for utility services. The business portion of the Study is based on more than 700 online interviews • What are US residential consumers and businesses with business decision-makers responsible for energy doing to manage their energy usage? management practices at companies with more than • Which energy issues matter most to them? 250 employees across all industries. To facilitate in-depth • What motivates them to reduce their energy analysis, business survey respondents are segmented consumption and what would impel them to take by industry sector and company size. Please see Figure 1 additional action? and Figure 2 for definitions of these segments. In addition, Deloitte interviewed several subject matter specialists and/ • Are they receptive to clean technologies? or providers of energy management products and services • How can electricity suppliers and energy service in order to obtain greater context and potential clarity providers better meet their needs? around key business findings. -
Energy Management and Optimization
Energy Management and Optimization Keith Masters Business Manager, Pulp and Paper Systems, ABB Westerville, OH Abstract Energy Management and Optimization solutions can help reduce energy costs while improving mill operational performance. Real time data from process monitoring systems, automation systems and production planning systems is used for planning and scheduling to help optimize energy use, procurement and generation. This mill information coupled with the price and energy availability information from energy providers/market is used to calculate optimal production and power generation plan, and to get the best price for the energy you require. Reporting tools provide energy consumption, costs and efficiency monitoring. Introduction There are many different ways to implement Energy Management and Optimization. This paper will describe a computer software program that includes planning and scheduling tools to help optimize energy use and supply, energy balance management tools to help energy procurement at the best price, and reporting tools to help monitor energy consumption, costs, efficiency and other energy-related information. The program is based on real time data from process monitoring systems, automation systems, production planning systems coupled with the price and energy availability information from energy providers/market. The continued rise in energy prices puts a squeeze on margin and profits. Margin ? Energy Cost Figure 1 Energy costs impact on margin In order to maintain margin, energy cost must be managed. -
Community Energy Management Best Practices
COMMUNITY ENERGY MANAGEMENT - BEST PRACTICES Community Energy Management Best Practices Index Program Overview Best Practice One: Community Plans and Public Outreach 1.1 Energy Plan 1.2 Public Participation Best Practice Two: Zoning Regulations 2.1 Zoning Regulations Best Practice Three: Project Review Process 3.1 Project Review Policy and Procedures 3.2 Guide to Energy Efficiency and Renewable Energy Projects Best Practice Four: Recruitment and Education 4.1 Recruitment and Orientation 4.2 Education and Training Best Practice Five: Clean Energy Communities 5.1 Clean Energy Sites 5.2 Community Energy Management Best Practice Six: Community Prosperity 6.1 Economic Development Strategy 6.2 Marketing and Promotion Glossary Acknowledgements COMMUNITY ENERGY MANAGEMENT - BEST PRACTICES Program Overview Local governments across Michigan struggle with economic constraints and seek tools to secure their financial health and identify sources of stable on-going funding for their critical services. Energy costs for the operation of municipal buildings and infrastructure are a rising expense for communities. Fortunately, energy costs also represent one of the easiest places where cost savings can be realized. However, local governments frequently lack the technical expertise and staff capacity to pursue those savings. Even when staff members are interested in pursuing energy savings, determining where the necessary information is and how to prioritize improvements is an ongoing challenge. This is where the services of a Community Energy Manager (CEM) -
Energy-Efficient Product Procurement for Federal Agencies (Brochure)
FEDERAL ENERGY MANAGEMENT PROGRAM Energy-Efficient Product Procurement for Federal Agencies The U.S. Department of Energy (DOE) Federal Energy Management Program (FEMP) supports Federal agencies in identifying energy- and water-efficient products that meet Federal acquisi- tion requirements, conserve energy, save taxpayer dollars, and reduce environmental impacts. This is achieved through technical assistance, guidance, FEMP helps Federal agencies evaluate energy-consuming products to select the most and efficiency requirements for energy- efficient, life-cycle cost effective options.Photo credit: iStock 11881809 efficient, water-efficient, and low standby power products. • EPAct 2005 mandates Federal agen- DOE and the U.S. Environmental cies to incorporate energy efficiency Protection Agency (EPA) sponsor four Federal Mandates criteria into relevant contracts and programs with the authority to identify Recognizing the benefits of energy-effi- specifications. appropriate product types and set cient products, Congress and multiple performance levels according to these Presidents passed several laws and • The Energy Independence and requirements. These programs include regulations mandating their purchase Security Act (EISA) of 2007 [amend- FEMP-designated products, ENERGY by Federal agencies, including: ing NECPA Section 8259b], E.O. STAR, low standby power products, 13423, and E.O. 13221 require and WaterSense labeled products. A • The Energy Policy Act (EPAct) of Federal agencies to purchase energy- 2005 [amending the National Energy -
ICHRIE-SECSA 2020 Conference Proceedings
Innovations in SECSA Hospitality and Tourism Research Volume 5, No. 1 Innovations is the research proceedings of the SECSA Federation of International Council of Hotel, Restaurant, and Institutional Education. ICHRIE-SECSA 2020 Conference Proceedings Chief Editor and Reviewer Lionel Thomas, Jr. PhD, MPM, CDM, CFPP Associate Professor International Hospitality, Hotels and Event Management Donald R. Tapia School of Business Saint Leo University, FL ICHRIE-SECSA Director of Research Assistant Editor Dr. Andrea White-McNeil, Ed. D., CHE, CHIA Assistant Professor Bob Billingslea School of Hospitality Management Bethune-Cookman University, FL ICHRIE-SECSA Director of Education Special Thank You to: Dr. Martin O’Neill, Horst Schulze Endowed Professor of Hospitality Management and Head of Department Nutrition, Dietetics and Hospitality Management, Auburn University for hosting our 5th Annual SECSA Conference. A special thank you to Dr. Imran Rahman (host conference chair) for his time, effort, and dedication to ensure a successful conference. Cover Art by Shaniel Bernard, Graduate Student, Department Nutrition, Dietetics and Hospitality Management, Auburn University Innovations in SECSA Hospitality and Tourism Research Volume 5, No. 1 ICHRIE-SECSA BOARD OF DIRECTORS 2019-2020 Immediate Past President President Vice-President Miranda Kitterlin-Lynch, PhD Ruth Smith, EdD Faizan Ali, PhD Associate Professor & Coco-Cola Assistant Professor Assistant Professor Endowed Professor Bob Billingslea School of College of Hospitality & Chaplin School of Hospitality & Hospitality Management Tourism Leadership Tourism Management Bethune-Cookman University University of South Florida Florida International University, FL [email protected] Sarasota-Manatee, FL [email protected] [email protected] Secretary Treasurer Director of Research Marissa Orlowski, PhD Yvette Green, PhD Lionel Thomas Jr., PhD Assistant Professor Interim Director, Associate Professor Rosen College of Hospitality Undergraduate & Graduate Donald R.