DC Motor and Controller Primer 1 DC Motor and Controller Primer
Total Page:16
File Type:pdf, Size:1020Kb
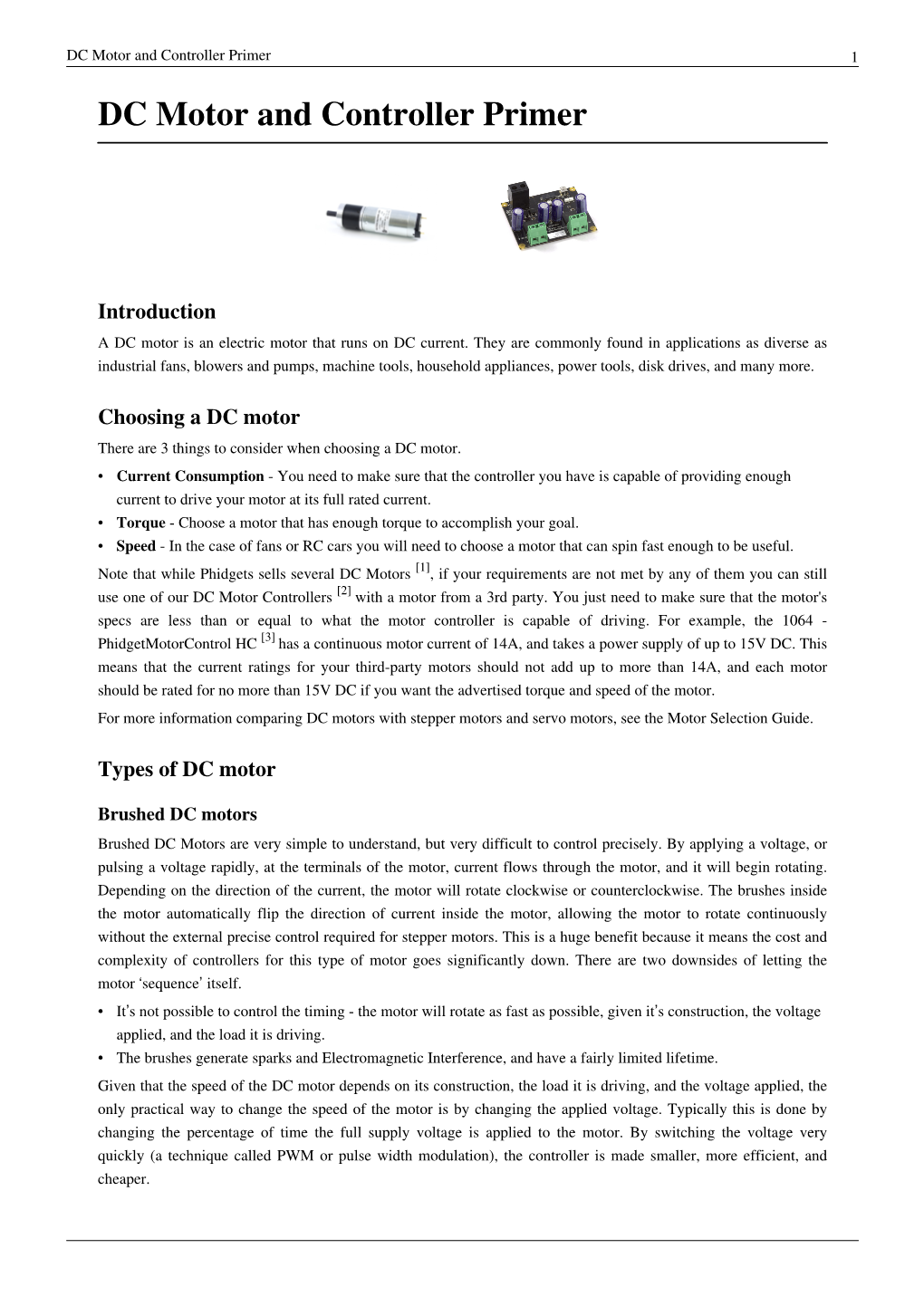
Load more
Recommended publications
-
A Motor Primer - Part 5
A MOTOR PRIMER - PART 5 Copyright Material IEEE Paper No. PCIC 2005-9 Bryan Oakes Gary Donner Senior Member, IEEE Fellow, IEEE Rockwell Automation Shell Oil Products US 101 Reliance Road 2101 E Pacific Coast Hwy Kings Mountain, NC 28086 Wilmington, CA 90748 USA USA [email protected] [email protected] Steve Evon Wayne Paschall Senior Member, IEEE Member, IEEE Rockwell Automation Rockwell Automation 6040 Ponders Ct. 101 Reliance Road Greenville, SC 29615 Kings Mountain, NC 28086 USA USA [email protected] [email protected] Abstract - In recent years much has been written II. WHAT PURPOSE DOES PERFORMING A about motors concerning efficiencies, vibration TORSIONAL ANALYSIS SERVE AND WHEN IS and resonance conditions as they relate to the IT REQUIRED? WHAT OCCURS DURING A American Petroleum Institutes (API) Standard TORSIONAL RESONANT CONDITION? 541 and motor diagnostics. Most of these papers and articles assume that the reader has Torsional vibration is an oscillatory twisting of significant knowledge of motor theory and the shaft. A motor by design applies a torsional operation. However, this assumption is overly force to the driven equipment and the driven optimistic, considering that only a few colleges equipment applies an equal and opposite force teach motor theory today and that application back to the motor. The shaft system deflects in experience at motor user locations has been torsion or twists away from the free position. At reduced in recent years. free vibration, and at its natural frequencies, the twist is free to unwind, twisting back to the free Index Terms – AC Induction Motors, position and, if undamped, twist an equal amount Efficiency, Torsional, Lateral Critical Speed, in the opposite direction. -
Motors / Electrical Supplies
MOTORS / ELECTRICAL SUPPLIES SUBJECT INDEX Page # Page # A L A.O. SMITH............................................................155 LAU Fan Blades..............................................167-169 ACME-MIAMI.....................................27, 162, 170-171 Light Bulbs...............................................................13 Anti-Ice Control.........................................................11 LiquidTite Conduit and Fittings.................................13 ASPEN Pumps...................................................24-25 LITTLE GIANT....................................................23-27 B Low Ambient Controls..............................................11 Bearings.........................................................171-173 M Belts, V............................................................174-175 MAGNETEK UNIVERSAL Motors....27, 151-159, 162 Blades, Fan.....................................................167-171 Monitors Blower Shaft...........................................................171 3-Phase Voltage.....................................................1 Blowers Phase Loss/Reversal..............................................1 Centrifugal......................................................86-87 Motors Axial Fans........................................................88-89 3.3” Diameter...................................................35-43 Fireplace.........................................................94-97 3.5” Diameter............................................44-46, 151 Flue Exhaust...................................................90-92 -
Fasco Facts-98561
MARS-FASCO facts:Layout 1 3/10/10 1:46 PM Page 1 FASCO FACTS Distributed by ® Time-saving motor replacement tips www.marsm-a.com MARS-FASCO facts:Layout 1 3/10/10 1:46 PM Page 2 INTRODUCTION This edition of the long-standing informative Fasco Facts booklet has been prepared by Fasco Distributing Company as a helpful guide for the motor replacement serviceman. The goal of this booklet is to provide a better working knowledge of electric motors and related disciplines. Being better informed provides a better foundation for successful motor and blower replacement. We encourage every service person to take basic precautions for their own safety as well as their customers when installing or servicing motors. Power to the equipment must be disconnected while the unit is being serviced, and all electric motors should be grounded. The National Electrical Code and local electrical and safety regulations should be followed at all times. Keep in mind that even though this booklet provides an abundance of information, there is much more information available on motors from other sources such as your local library. Depending on how much you wish to learn about motors, the library can be an invaluable source for the extended information. The only question is, how much do you want to learn? Have fun. There are several types of fractional horsepower motors. Each type performs certain jobs better than the other types. The characteristics of a motor designed to move air are completely different than those of a motor used to drive a grinder, a pump, or even a belt-driven application. -
WOODWORKING CATALOG Table of Contents
WOODWORKING CATALOG TABLE OF CONTENTS TABLESAWS .................. 3–11 SHAPERS .....................70-73 BANDSAWS ..................12-21 DRILLING .....................74-78 JOINTERS AND PLANERS ......22-35 SPECIALTY ACCESSORIES .........79 DUST MANAGEMENT ..........36-47 WORKHOLDING .............. 80–84 SANDERS AND ABRASIVES ....48-59 WARRANTY .....................85 GRINDING AND BUFFING ......60-62 AUTHORIZED SERVICE CENTERS .................... 86–90 WOODTURNING ...............63-69 ® JetTools.com 12" XACTA TABLESAW TABLESAWS A E E C D B 708536PK Massive cast iron components and trunnions A. Exclusive XACTA® Fence II D. Industrial Magnetic Controls B. Large Handwheel E. Solid Cast Iron Wings C. Sheet Metal Hinged Motor Cover FEATURES SPECIFICATIONS • EXCLUSIVE 50" commercial XACTA® Fence II with See Available Packages Stock Number T-square design Below • Cast iron wings for a large, flat work surface Model Number JTAS-12 • Three matched V-belts deliver full power to the blade Blade Diameter (in.) 12 Arbor Diameter (in.) 1 • Rail-mounted magnetic switch is easy to reach and provides overload protection Arbor Speed (RPM) 4200 • One-piece closed stand channels dust through a 4" port for fast, Max. Depth of Cut (in.) 4 clean dust collection Max. Depth of Cut at 45 Degrees (in.) 2-7/8 • Large, heavy-duty handwheels help you make precise adjustments Max. Rip Right of Blade (in.) 50 with less effort Max. Rip Left of Blade (in.) 13 • See-through blade guard with splitter and anti-kickback pawls helps Table in Front of Saw Blade at Max. Depth of Cut (in.) 12 protect operator while giving a clear view of the material being cut Max. Width of Dado (in.) 13/16 • Deluxe miter gauge with adjustable positive stops provides large Max. -
Reconditioning Services
February 2019 RECONDITIONING SERVICES We race condition any brand armature. Every armature is ultrasonically cleaned, diamond trued, and precision rebalanced. We take the lightest cut possible to true your commutator and we calibrate our machine for each armature. Please include your name, address, phone number and email address so we can contact you during normal business hours for payment and shipping options. o Armature Reconditioning $4.50 o When sending 10 or more armatures $4.00 o Engraving $.50 o Grind stacks up to .010 reduction $1.00 o Grind stacks greater than .010 reduction $2.00 o Remagnetize ceramic magnets in or out of the can, including R/C Magnets $1.25 ADDITIONAL SERVICES o Resistance and Induction readings done on each armature and marked on the tubes $1.50 VISIT OUR WEBSITE FOR, ARTICLES AND NEW PRODUCT INFORMATION http://www.proslot.com ProSlot LLC. – 12 West Main St. - Hartford, MI 49057 PH: (616) 897-6000 Motor Rebuilding Program PS-725 Dragmaster SPEC motor……………………… $25.00 Includes: Ultrasonic cleaning, re-zapping, recondition armature, new Goldust brushes, springs, bushings (if needed) & reseal the motor. Additional charges for replacement parts may apply PS-748-12, PS-748-20 & PS-733 Dragmaster Motors… $25.00 Includes: Ultrasonic cleaning, re-zapping, recondition armature, new Goldust brushes, springs, shunt wire & new bushings if needed. Additional charges for replacement parts may apply All MK1 Series, C-can & D-can Motors…………….. $25.00 Includes: Ultra sonic cleaning, re-zapping, recondition armature, new Goldust brushes, springs & new bushings if needed. Additional charges for replacement parts may apply Pro Slot VR Neo Motors………………………………. -
Capacitor-Driven Railgun: Magnetic Fields Doing Work 1 Problem
Capacitor-Driven Railgun: Magnetic Fields Doing Work Kirk T. McDonald Joseph Henry Laboratories, Princeton University, Princeton, NJ 08544 (December 28, 2015; updated October 13, 2017) 1Problem Discuss force, work and energy in a capacitor-drive railgun, as illustrated on the left below (from [229]),1 and in the original conception due to Amp`ere and de La Rive (1822) [26] as illustrated on the right below.2 Examples like these are used to illustrate the claim that “magnetic forces do no work” [133, 136, 235, 236, 244], which implies that some other force(s) than magnetism are “at work” here. Consider also the variant shown below3 in which the railgun circuit is initially super- conducting with current I0 and fixed (superconducting) crosspiece), but at time t =0the crosspiece goes normal, takes on electrical resistance R,andissetfreetomove.4 1As this note has an historical flavor, it seemed appropriate that the references be listed in chronological order, by date of submission for publication. 2A railgun was patented by Birkeland in 1902 [89, 185]. For another contribution of Birkeland, see [243]. The literature on railguns is now vast. A sample is [135, 218, 237, 245]. 3A railgun was discussed by Maxwell in Arts. 594-596 of [71], as sketched on in the figure on right. 4A simple railgun variant is now featured at sites such as http://sci-toys.com/scitoys/scitoys/electro/railgun/railgun.html In this, the magnetic field that provides the Lorentz force is due to strong permanent magnets that form the wheels of a rolling crosspiece. The direction of the axial field in the two wheels must be opposite (such that a single rolling magnet wouold not suffice). -
Control Or Regulation of Electric Motors, Electric Generators Or Dynamo-Electric Converters; Controlling Transformers, Reactors Or Choke Coils
CPC - H02P - 2017.08 H02P CONTROL OR REGULATION OF ELECTRIC MOTORS, ELECTRIC GENERATORS OR DYNAMO-ELECTRIC CONVERTERS; CONTROLLING TRANSFORMERS, REACTORS OR CHOKE COILS Definition statement This place covers: Arrangements for • starting, • regulating, • electronically commutating, • braking, or otherwise controlling: • motors, • generators, • dynamo-electric converters, clutches, brakes, gears, • transformers, • reactors or choke coils, of the types classified in the relevant subclasses, e.g. H01F, H02K. References Limiting references This place does not cover: Arrangements for merely turning on an electric motor to drive a machine A47L 9/28, F02N 11/00 or device, e.g.: vacuum cleaner, vehicle starter motor Hybrid vehicle, conjoint control, arrangements for mounting B60K, B60W Arrangements for controlling electric generators for charging batteries H02J 7/00 Arrangements for starting, regulating, electronically commutating, H02N braking, or otherwise controlling electric machines not otherwise provided for, e.g. machines using piezo-electric effects Informative references Attention is drawn to the following places, which may be of interest for search: Curtain A47H Hand hammers, drills B25D 17/00 Printers B41J Power steering B42D 5/00 Heating cooling ventilating B60H 1/00 Electrically propelled vehicles, current collector, maglev B60L Lighting B60Q 1/00 Electric circuits for vehicle B60R, H02J Wiper control B60S 1/00 Marine B63H 1 H02P (continued) CPC - H02P - 2017.08 Elevator B66B Washing machines, household appliances D06F 39/00 Sliding -
IMESA-Product-Catalog.Pdf
PRODUCT CATALOG 3.3” Shaded Pole Motors FOR COMMERCIAL REFRIGERATION AND VENTILATION C AB Enclosure: Open. Service Factor: 1.0 Work Ambient: 40°C - 60°C Bearings: Sleeve bearing, or ball bearing. Service: Continuos Duty. Fig. 1 Dwg 1 RPM: 1550. C AB Mounting: 2 or 3 or 4 studs on a 2.84” diameter. Shaft Dimensions: 5/16” diameter. Leads: #18 GA, 125°C, 600V. Fig. 2 Dwg 2 HP Model Voltage Amp. Rot. A B C Fig. Dwg. Protection A/5 127 0.55 CCW 2.150 0.938 0.475 1 1 ZP or Aut. A/5E 127 0.55 CCW 2.150 0.938 0.475 2 2 ZP or Aut A/5-2 220 0.26 CCW 2.150 0.938 0.475 1 1 ZP or Aut A/5-2E 220 0.26 CCW 2.150 0.938 0.475 2 2 ZP or Aut 1/100 A/6 127 0.55 CW 2.150 0.938 0.475 1 1 ZP or Aut. A/6E 127 0.55 CW 2.150 0.938 0.475 2 2 ZP or Aut A/6-2 220 0.26 CW 2.150 0.938 0.475 1 1 ZP or Aut A/6-2E 220 0.26 CW 2.150 0.938 0.475 2 2 ZP or Aut B/5 127 0.77 CCW 2.275 0.938 0.350 1 1 ZP or Aut. B/5E 127 0.77 CCW 2.275 0.938 0.350 2 2 ZP or Aut B/5-2 220 0.45 CCW 2.275 0.938 0.350 1 1 ZP or Aut B/5-2E 220 0.45 CCW 2.275 0.938 0.350 2 2 ZP or Aut 1/70 B/6 127 0.77 CW 2.150 0.813 0.475 1 1 ZP or Aut. -
CPC Notice of Changes 323-DP0171 (H02P)
EUROPEAN PATENT OFFICE U.S. PATENT AND TRADEMARK OFFICE CPC NOTICE OF CHANGES 323 DATE: JANUARY 1, 2017 PROJECT DP0171 The following classification changes will be effected by this Notice of Changes: Action Subclass Group(s) New/modified/deleted Definitions: H02P 5/00 H02P 5/485 H02P 5/505 H02P 5/51 H02P 5/60 H02P 5/68 H02P 5/74 H02P 6/00 H02P 6/04 H02P 6/08 H02P 6/10 H02P 6/15 H02P 6/16 H02P 6/185 H02P 6/20 H02P 6/21 H02P 6/28 H02P 6/30 H02P 7/00 H02P 7/281 H02P 7/291 H02P 7/293 H02P 7/32 H02P 7/34 H02P 21/00 H02P 21/32 H02P 21/04 H02P 21/16 H02P 23/00 H02P 23/0004 H02P 23/04 H02P 23/16 H02P 23/18 H02P 23/183 H02P 23/186 H02P 23/26 H02P 23/30 H02P 25/00 H02P 25/026 H02P 25/034 H02P 25/083 CPC Form – v.4 CPC NOTICE OF CHANGES 323 DATE: JANUARY 1, 2017 PROJECT DP0171 Action Subclass Group(s) H02P 25/089 H02P 25/098 H02P 25/10 H02P 25/14 H02P 27/00 H02P 29/00 H02P 29/02 H02P 29/50 H02P 29/60 No other subclasses/groups are impacted by this Notice of Changes. This Notice of Changes includes the following [Check the ones included]: 1. CLASSIFICATION SCHEME CHANGES A. New, Modified or Deleted Group(s) B. New, Modified or Deleted Warning Notice(s) C. New, Modified or Deleted Note(s) D. New, Modified or Deleted Guidance Heading(s) 2. -
MOTOR / GENERATOR SET – Hand Driven Cat: EM1758-001 Hand Driven Motor/Generator
INSTRUCTION SHEET MOTOR / GENERATOR SET – hand driven Cat: EM1758-001 hand driven motor/generator DESCRIPTION: The IEC hand driven Motor / Generator is a precision, ball bearing motor with a 2 pole rotor and a 2 bar commutator. It can be run as a DC motor or it can be hand driven to be a DC generator. All parts of the motor are easily visible and the operation of the commutator and brushes can be studied. The commutator is self-lubricating to avoid squeaking and wear. It is strong and is designed to have a long life in the hands of students. When connected as a generator, an MES lamp is provided to illuminate as power is created. To create the magnetic field through the motor, use the Ucore that forms part of the IEC Electricity Kit EM1763-001, the IEC ‘Hodson” Induction Kit EM1973-001 or the IEC Small Dissectible Transformer EM4089-001. The motor/generator can be used also with permanent magnets. EM1758-001 HAND DRIVEN MOTOR/GENERATOR MOTOR/GENERATOR EM1758-001 ///////// Ucore and coil from an IEC Electricity Kit or a “Hodson” Induction Kit Physical size: 18x10x10mm LxWxH Weight: 0.5 kg. INDUSTRIAL EQUIPMENT & CONTROL PTY.LTD. 61-65 McClure St. Thornbury. 3071 Melbourne. Australia Tel: 61 (0)3 9497 2555 Fax: 61 (0)3 9497 2166 em1758-001.doc 21-Jun-07 1 INSTRUCTION SHEET MOUNTING THE MOTOR/GENERATOR:: The motor/generator is designed to slide between the legs of the standard IEC ‘Hodson’ Induction Kit iron Ucore fitted with a single 600 turn coil. This Coil and Ucore creates the field for the motor. -
Pricing List
PRICE LIST Last Updated: Friday, June 11th 2021 REFRIGERATION SUPPLIES DISTRIBUTOR MANUFACTURER PRODUCT DESCRIPTION LIST PRICE Acme 3001 5/16 In Aluminum Hub; 5.58 Acme 31005 10 In 40 Deg Aluminum Fan Blade CW; 14.14 Acme 31015 10 In 40 Deg Aluminum Fan Blade CCW; 14.14 Acme 3106 10 In 27 Deg Aluminum Fan Blade CW; 12.64 Acme 3106-31 10 In 31 Deg Aluminum Fan Blade CW; 12.64 Acme 3116 10 In 27 Deg Aluminum Fan Blade CCW; 12.64 Acme 3116-31 10 In 31 Deg Aluminum Fan Blade CCW; 12.64 Acme 3706-31 7 In 31 Deg Aluminum Fan Blade CW; 7.98 Acme 3806 8 In 25 Deg Aluminum Fan Blade CW; 9.36 Acme 3806-31 8 In 31 Deg Aluminum Fan Blade CW; 9.36 Acme 3816 8 In 25 Deg Aluminum Fan Blade CCW; 9.36 Acme 3816-31 8 In 31 Deg Aluminum Fan Blade CCW; 9.36 Acme 3906-31 9 In 31 Deg Aluminum Fan Blade CW; 10.60 Acme BB-700 Revesible C Frame Ball Bearing Motor 115 Volt; 50.90 AO Smith FEH1036SF Cond Fan Motor 1/3 HP 460 Volt PSC 1075 RPM REV 5.6" Dia BB TEV; 502.26 AO Smith FEH1056S Condenser Fan Motor 1/2 HP 460 Volt PSC 1050 RPM Ball Brg REV TE 5.6" Dia; 436.78 AO Smith GF2024D Blower Motor 1/4 HP 115/230 Volt 1725 RPM REV 48/56 Frame w/Base 4680; 471.82 AO Smith H1050AV1 1 HP 208-230/460 3PH 1140 1SP Rev 56H BB Inverter Duty; 698.92 AO Smith H1051AV1 1-1/2 HP 208-230/460 3PH 1140 1SP Rev 56H BB Inverter Duty; 765.00 AO Smith H1052AV1 2 HP 208-230/460 3PH 1140 1SP Rev 56H BB Inverter Duty; 833.56 AO Smith VB2074V1 Blower Motor 3/4 HP 115 Volt 1725 RPM 1 Speed CCW 56Z Frame Evap Cooler; 290.54 Appion G5 TWIN Recovery Machine G5 Twin R410a Rated; 1,516.10 -
Ball-Bearing Motor Kirk T
Ball-Bearing Motor Kirk T. McDonald Joseph Henry Laboratories, Princeton University, Princeton, NJ 08544 (May 17, 2011; updated June 1, 2020) 1Problem Discuss the principle of operation of a so-called ball-bearing motor, a popular form of which is sketched below (from [2]).1 The motor can start from rest (although not all observers report this [1]-[24]), and rotates in either sense, if the current (AC or DC!) is large enough. 2Solution The discovery/invention of the ball-bearing motor is attributed to Milroy [1]. It has been discussed several times, with conflicting explanations [2]-[24].2,3 This solution is a much simplified version of that given in [10], and is based on the Lorentz force. 1Numerous videos of variants of this device are available on YouTube. 2Most authors except Marinov [7] suppose the torque to be due to a Lorentz force, whereas he stated (without supporting argument) that the torque results from thermal expansion of the bearings. It is generally agreed that the first attempt at an electromagnetic explanation, [2], was wrong. Also, the explanation in [11] was later retracted by its author. 3Refs. [6, 19, 22, 23] associate ball-bearing motors with the “Huber effect”, after [25]. See also Appendix A below, and [26]-[29]; the last paper reviews the Russian literature on this topic. Huber considered a kind of railgun in which the crosspiece, a sphere or cylinder, rolled along tracks, supposedly propelled by the Lorentz force on the current in the crosspiece. However, [26] reported sparking between the wheels and the rails on the trailing side of the motion, which could imply that thermal effects, rather than the Lorentz force, are important here.