US5137780.Pdf
Total Page:16
File Type:pdf, Size:1020Kb
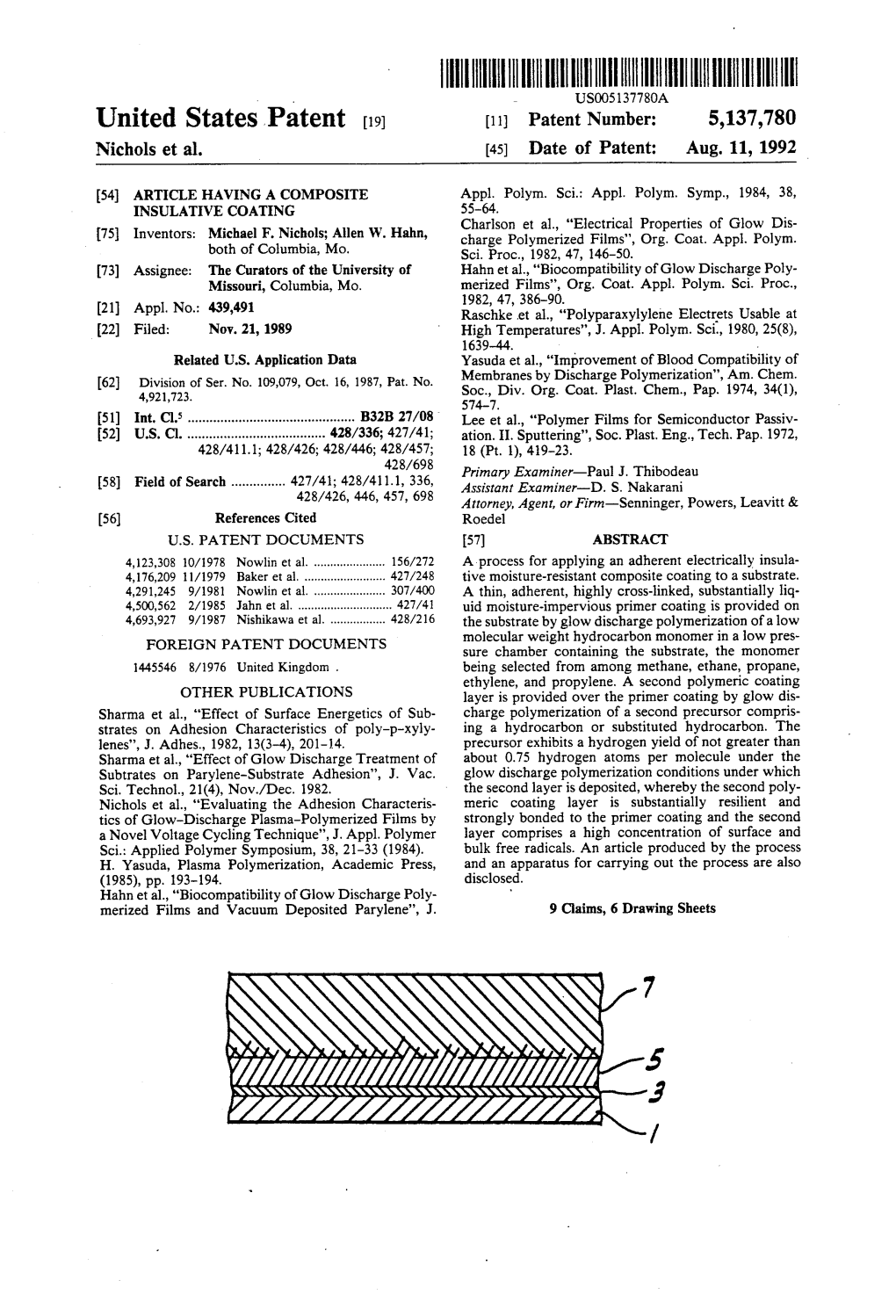
Load more
Recommended publications
-
The Parylene Deposition Process
History of Parylene Parylene development started in 1947, when Michael Szwarc discovered the polymer as one of the thermal decomposition products of a common solvent p-xylene at temperatures exceeding 1000 °C. Szwarc first postulated the monomer to be para-xylylene which he confirmed by reacting the vapors with iodine and observing the para-xylylene di-iodide as the only product. The reaction yield was only a few percent, and a more efficient route was found later by William F. Gorham at Union Carbide. The Parylene Deposition Process Parylene coating is applied through a vapor deposition process onto the substrate or material that is being coated. Depending on the coating type and required thickness, typical parylene deposition rates are about .2/mils per hour, so machine runs can vary from as little as 1 hour to over 24 hours. The process begins with raw dimer in solid state (these are: Parylene C, Parylene N, Parylene D, Parylene AF-4, or other variants) being placed into a loading boat, which is then inserted into the vaporizer. The raw dimer is heated between 100-150º C. At this time, the vapor is pulled, under vacuum into the furnace and heated to very high temperatures which allows for sublimation and the splitting of the molecule into a monomer. The monomer gas continues to be drawn by vacuum one molecule at a time onto the desired substrate at ambient temperatures in the coating chamber. The final stage of the parylene deposition process is the cold trap. The cold trap is cooled to between -90º and -120º C and is responsible for removing all residual parylene materials pulled through the coating chamber. -
Lens Array by Electrostatic Patterning of Dielectric Microspheres in a Parylene-C Well Template H
LENS ARRAY BY ELECTROSTATIC PATTERNING OF DIELECTRIC MICROSPHERES IN A PARYLENE-C WELL TEMPLATE H. Yang*, M. Cornaglia and Martin A. M. Gijs Laboratory of Microsystems, École Polytechnique Fédérale de Lausanne, Switzerland ABSTRACT We present the fabrication of a microlens array which can be integrated into a microfluidic device. In the demonstrated technique, a microwell array is firstly fabricated in a Parylene-C layer by a standard cleanroom process. Afterwards, the optically transparent dielectric microspheres with high refractive index are patterned inside the well template by utilizing an electrostatic technique. The mechanism of microsphere patterning is studied, and the lens effect of the microsphere is experimentally verified in a water-based medium. We also present a detailed two-dimensional numerical optical simulation study on the patterned microspheres using the Finite Element Method (FEM). KEYWORDS: Microlens array, Dielectric microspheres, Microfabrication, Parylene-C INTRODUCTION Microlenses that are integrated on microfluidic chips enable several important optical features, such as profiting from a large local numerical aperture (NA) and high light collection efficiency, so that, for example, the optical read-out in an immunoassay is facilitated and the detection limit decreased [1]. Optically transparent microspheres with high refractive index act as ball lenses and show strong capability in focusing light. Using microspheres to build a compact system integrated with microfluidics inevitably will be of benefit to the field of life sciences, diagnostics or environmental monitoring. In this study, an electrostatic technique for fabrication of a microlens array by printing single dielectric microspheres into a patterned microwell template is proposed. The immobilized microspheres can focus the illumination, such as the optical signal originating from the presence of fluorescent markers beneath a microlens, into a very narrow region with high optical intensity, which is also known as a ‘photonic nanojet’ [2]. -
Formation of Three-Dimensional Parylene C Structures Via Thermoforming
Journal of Micromechanics and Microengineering J. Micromech. Microeng. 24 (2014) 065003 (9pp) doi:10.1088/0960-1317/24/6/065003 Formation of three-dimensional Parylene C structures via thermoforming BJKim1, B Chen2,MGupta2 and E Meng1,3 1 Department of Biomedical Engineering, University of Southern California, 1042 Downey Way, DRB-140, Los Angeles, CA 90089-1111, USA 2 Mork Family Department of Chemical Engineering and Materials Science, University of Southern California, Los Angeles, CA 90089-1211, USA 3 Ming Hsieh Department of Electrical Engineering, University of Southern California, 3740 McClintock Ave., EEB-100, Los Angeles, CA 90089-2560, USA E-mail: [email protected] Received 14 January 2014, revised 19 March 2014 Accepted for publication 31 March 2014 Published 25 April 2014 Abstract The thermoplastic nature of Parylene C is leveraged to enable the formation of three-dimensional structures using a thermal forming (thermoforming) technique. Thermoforming involves the heating of Parylene films above its glass transition temperature while they are physically confined in the final desired conformation. Micro and macro scale three-dimensional structures composed of Parylene thin films were developed using the thermoforming process, and the resulting chemical and mechanical changes to the films were characterized. No large changes to the surface and bulk chemistries of the polymer were observed following the thermoforming process conducted in vacuum. Heat treated structures exhibited increased stiffness by a maximum of 37% depending on the treatment temperature, due to an increase in crystallinity of the Parylene polymer. This study revealed important property changes resulting from the process, namely (1) the development of high strains in thermoformed areas of small radii of curvature (30–90 µm) and (2) 1.5% bulk material shrinkage in thermoformed multilayered Parylene–Parylene and Parylene–metal–Parylene∼ films. -
Study on the Surface Characteristics of Parylene-C Films in Inductively Coupled O2/CF4 Gas Plasma
P2-44 / Y. -H. Ham Study on the surface characteristics of parylene-C films in inductively coupled O2/CF4 gas plasma Yong-hyun Ham1, Kyu-Ha Baek1, Kun-Sik Park1, Hong-sik Shin1, Ho-jin Yun1, Kwang-Ho Kwon2 , and Lee-Mi Do1 1 Electronics and Telecommunications Research Institute (ETRI), 138 Gajeongdong, Yuseong-gu, Daejeon 305-700, Korea Tel.:82-2-860-5776, E-mail: [email protected] 2 Dept. Control and Instrumentation Engineering, Korea University, Jochiwon-eup, Yeongi-gun, chungnam 339-700, Korea Keywords: Parylene-C, O2/CF4, Plasma treatment, ICP Abstract surface.[4] As a result, functional groups lead to In this article, we reported the results of etching poly- degradation of transistor performance. Hence, monochloro-para-xylylene (parylene-C) thin films using preventing the functional groups is essential to inductively coupled plasma and CF4/O2 gas mixture. The improve the OTFTs’ performance. Research in this CF4 gas fraction increased up to the approximately 16 %, field has been so far studied by many researching the polymer etch rate increased in the range of 277 – 373 groups. However, various gas chemistries have not nm/min. It confirmed that the etch rate of the parylene-C been widely examined to reduce the formation of the mainly depended on the O radical density in the plasma. Using a contact angle measurement, the contact angle functional groups, even though the reaction of the polymer with the plasma-created species makes a increased with increasing the CF4 fraction. Moreover, the contact angle was highly related a CFx functional group on large effect on the formation of the functional groups. -
Techniques and Considerations in the Microfabrication of Parylene C Microelectromechanical Systems
micromachines Review Techniques and Considerations in the Microfabrication of Parylene C Microelectromechanical Systems Jessica Ortigoza-Diaz 1, Kee Scholten 1 ID , Christopher Larson 1 ID , Angelica Cobo 1, Trevor Hudson 1, James Yoo 1 ID , Alex Baldwin 1 ID , Ahuva Weltman Hirschberg 1 and Ellis Meng 1,2,* 1 Department of Biomedical Engineering, University of Southern California, Los Angeles, CA 90089, USA; [email protected] (J.O.-D.); [email protected] (K.S.); [email protected] (C.L.); [email protected] (A.C.); [email protected] (T.H.); [email protected] (J.Y.); [email protected] (A.B.); [email protected] (A.W.H.) 2 Ming Hsieh Department of Electrical Engineering, University of Southern California, Los Angeles, CA 90089, USA * Correspondence: [email protected]; Tel.: +1-213-740-6952 Received: 31 July 2018; Accepted: 18 August 2018; Published: 22 August 2018 Abstract: Parylene C is a promising material for constructing flexible, biocompatible and corrosion- resistant microelectromechanical systems (MEMS) devices. Historically, Parylene C has been employed as an encapsulation material for medical implants, such as stents and pacemakers, due to its strong barrier properties and biocompatibility. In the past few decades, the adaptation of planar microfabrication processes to thin film Parylene C has encouraged its use as an insulator, structural and substrate material for MEMS and other microelectronic devices. However, Parylene C presents unique challenges during microfabrication and during use with liquids, especially for flexible, thin film electronic devices. In particular, the flexibility and low thermal budget of Parylene C require modification of the fabrication techniques inherited from silicon MEMS, and poor adhesion at Parylene-Parylene and Parylene-metal interfaces causes device failure under prolonged use in wet environments. -
Parylene-Coated PTFE-Membrane-Based Portable Urea Sensor for Use in Fast Flow Conditions
Preprints (www.preprints.org) | NOT PEER-REVIEWED | Posted: 26 September 2019 doi:10.20944/preprints201909.0297.v1 Peer-reviewed version available at Sensors 2019, 19, 4560; doi:10.3390/s19204560 Article Parylene-Coated PTFE-Membrane-Based Portable Urea Sensor for Use in Fast Flow Conditions Min Park 1,2,3, JeeYoung Kim 1,2,3, Kyounghee Kim 1,2,3, Jae-Chul Pyun 4 and Gun Yong Sung 1,2,3,* 1 Major in Materials Science and Engineering, Hallym University, Chuncheon, Gangwon-do, 24252 Rep. of Korea; [email protected](M.P.); [email protected](J.K.); [email protected](K.K.) 2 Cooperative course of Nano-Medical Device Engineering, Hallym University, Chuncheon, Gangwon-do, 24252 Rep. of Korea 3 Integrative Materials Research Institute, Hallym University, Chuncheon, Gangwon-do, 24252 Rep. of Korea 4 Department of Materials Science and Engineering, Yonsei University, Seoul, 03722 Rep. of Korea; [email protected](J.-C.P.) * Correspondence: [email protected]; Tel.: +82-33-248-2361 Abstract: A portable urea sensor for use in the fast flow condition was fabricated using porous polytetrafluoroethylene (PTFE) membranes coated with amine-functionalized parylene, parylene- A, by vapor deposition. To generate a specific electrochemical sensor signal from urea, the urea- hydrolyzing enzyme urease was immobilized on the parylene-A-coated PTFE membranes via chemical crosslinking using glutaraldehyde. The urease-immobilized membranes were assembled in a polydimethylsiloxane (PDMS) fluidic chamber, and a screen-printed carbon three-electrode system was used for electrochemical measurements. The success of urease immobilization was confirmed using fluorescence microscopy, scanning electron microscopy, and Fourier-transform infrared spectroscopy. -
Comparing Parylene to Liquid Conformal Coatings
Comparing Parylene to Liquid Conformal Coatings By: Sean Horn Diamond-MT, Inc. 213 Chestnut Street Johnstown, Pa 15906 +1 (814) 535 3505 phone +1 (814) 535 2080 fax www.paryleneconformalcoating.com [email protected] Conformal Coatings: A Quick Primer Consisting of various polymeric materials, conformal coatings preserve the operational integrity of electrical and mechanical assemblies, insulating the substrate, improving performance and extending product lifecycle. Conformal coatings provide printed circuit boards (PCBs) and similar electric devices with a protective, non-conductive dielectric layer, safeguarding these assemblies from: 1. Abrasion resulting from contact with acids, chemicals, solvents or, bodily fluids, in the case of medical equipment. 2. Conductor electro-migration, corrosion, dendritic growth, and electronic short-circuits. 3. Exposure to extreme changes in temperatures and humidity, working conditions requiring prolonged operation, or harsh physical environments. They also provide superior insulation and stress-relief to assure ongoing functionality. Major conformal coating types are composed of acrylic, epoxy, parylene, silicone and urethane. The type of coating material used depends upon such circumstances as: the precise character of the assembly/product being coated, the operational environment of the item's intended use, the coating substance's ability to provide appropriate protection, and the coating's process-requirements and cost relative to other coating materials. Four of the five types of conformal coating — acrylic, epoxy, polyurethane, and silicone — are applied by liquid methods, by either brushing, spraying, or dipping the coating on the substrate, then letting it dry on the surface of the designated assembly. Parylene is the major exception, employing a unique chemical vapor deposition (CVD) polymerization process, which generates superior performance for most uses, compared to liquid coatings. -
I. Composite Polymer Coatings Prepared in Supercritical Carbon Dioxide
University of Massachusetts Amherst ScholarWorks@UMass Amherst Doctoral Dissertations 1896 - February 2014 1-1-2006 I. Composite polymer coatings prepared in supercritical carbon dioxide. II. Chemical modification of atomic force microscope probes. III. Liquid mobility on surfaces with patterned chemistry and topography. Kevin A. Wier University of Massachusetts Amherst Follow this and additional works at: https://scholarworks.umass.edu/dissertations_1 Recommended Citation Wier, Kevin A., "I. Composite polymer coatings prepared in supercritical carbon dioxide. II. Chemical modification of atomic force microscope probes. III. Liquid mobility on surfaces with patterned chemistry and topography." (2006). Doctoral Dissertations 1896 - February 2014. 1088. https://scholarworks.umass.edu/dissertations_1/1088 This Open Access Dissertation is brought to you for free and open access by ScholarWorks@UMass Amherst. It has been accepted for inclusion in Doctoral Dissertations 1896 - February 2014 by an authorized administrator of ScholarWorks@UMass Amherst. For more information, please contact [email protected]. University of Massachusetts Amherst I B R A R Y 1 : 5 ! ) I This is an authorized facsimile, made from the microfilm master copy of the original dissertation or master thesis published by UMI. The bibliographic information for this thesis is contained in UMFs Dissertation Abstracts database, the only central source for accessing almost every doctoral dissertation accepted in North America since 1861. ® Dissertation UMI Services From:Pro(jsuest COMPANY 300 North Zeeb Road P.O. Box 1346 Ann Arbor, Michigan 48106-1346 USA 800.521.0600 734.761.4700 web www.il.proquest.com Printed in 2006 by digital xerographic process on acid-free paper I. COMPOSITE POLYMER COATINGS PREPARED IN SUPERCRITICAL CARBON DIOXIDE II. -
Photoluminescent Quantum-Dot Light Emitting Devices Controlled by Electric Field Induced Quenching Melissa Li
Photoluminescent Quantum-Dot Light Emitting Devices Controlled by Electric Field Induced Quenching by Melissa Li B.S. in Physics and Electrical Engineering, Massachusetts Institute of Technology (2017) Submitted to the Department of Electrical Engineering and Computer Science in partial fulfillment of the requirements for the degree of Master of Engineering in Electrical Engineering and Computer Science at the MASSACHUSETTS INSTITUTE OF TECHNOLOGY June 2019 ○c Massachusetts Institute of Technology 2019. All rights reserved. Author................................................................ Department of Electrical Engineering and Computer Science May 24, 2019 Certified by. Vladimir Bulović Professor Thesis Supervisor Accepted by . Katrina LaCurts Chair, Master of Engineering Thesis Committee 2 Photoluminescent Quantum-Dot Light Emitting Devices Controlled by Electric Field Induced Quenching by Melissa Li Submitted to the Department of Electrical Engineering and Computer Science on May 24, 2019, in partial fulfillment of the requirements for the degree of Master of Engineering in Electrical Engineering and Computer Science Abstract Colloidal quantum dots (QDs) have been promising luminophores due to their bright, pure, and tunable colors. The ability to control the emission properties of QDs has far-reaching potential applications for a new generation of display and lighting technologies. The emission control of QDs in a QD light-emitting device (LED) is usually achieved by changing the injection current density. However, these devices face issues with lifetime and stability as well as low external quantum efficiency (EQE) at high biases. In this thesis, we demonstrate a unique approach in operating a QD device that avoids these limitations. The device is a photoluminescent LED (PL-LED) where the emission from the LED is from optical excitation. -
Effect of Thermal and Deposition Processes on Surface Morphology, Crystallinity, and Adhesion of Parylene-C
Sensors and Materials, Vol. 20, No. 2 (2008) 087–102 MYU Tokyo S & M 0707 Effect of Thermal and Deposition Processes on Surface Morphology, Crystallinity, and Adhesion of Parylene-C Jui-Mei Hsu1,*, Loren Rieth2, Sascha Kammer3, Mike Orthner2, and Florian Solzbacher1,2,4 1Department of Materials Science and Engineering, University of Utah, Salt Lake City, UT 84112, USA 2Department of Electrical Engineering, University of Utah, Salt Lake City, UT 84112, USA 3Department Medical Engineering and Neuroprosthetics Group, Fraunhofer Institute for Biomedical Engineering, Germany 4Department of Bioengineering, University of Utah, Salt Lake City, UT 84112, USA (Received October 4, 2007; accepted February 4, 2008) Key words: CVD thin film, adhesion, surface morphology, crystallinity, Parylene-C Neural interface devices have been developed for neural science and neuroprosthetics applications to record and stimulate neural signals. Chemical-vapor-deposited Parylene-C films were studied as an encapsulation material for such an implantable device. The surface morphology of an implant affects its biocompatibility; thus, the Parylene-C surface morphology was investigated as a function of the precursor sublimation rate by atomic force microscopy. We found that high precursor sublimation rates resulted in slightly higher root-mean-square surface roughnesses (from 5.78 to 9.53 nm for deposition rates from 0.015 to 0.08 g/min). The crystallinity affects the physical properties of semicrystalline polymers, and various heat treatments were found to modify the crystallinity of Parylene-C films, as assessed by X-ray diffraction (XRD). The XRD peak at 2θ = ~14.5° increased in intensity and decreased in full width at half maximum with increasing annealing temperature, indicating an increase in film crystallinity. -
Flexible Quantum Dot Light-Emitting Diodes for Next-Generation Displays
www.nature.com/npjflexelectron REVIEW ARTICLE OPEN Flexible quantum dot light-emitting diodes for next-generation displays Moon Kee Choi1,2, Jiwoong Yang1,2, Taeghwan Hyeon1,2 and Dae-Hyeong Kim1,2 In the future electronics, all device components will be connected wirelessly to displays that serve as information input and/or output ports. There is a growing demand of flexible and wearable displays, therefore, for information input/output of the next- generation consumer electronics. Among many kinds of light-emitting devices for these next-generation displays, quantum dot light-emitting diodes (QLEDs) exhibit unique advantages, such as wide color gamut, high color purity, high brightness with low turn-on voltage, and ultrathin form factor. Here, we review the recent progress on flexible QLEDs for the next-generation displays. First, the recent technological advances in device structure engineering, quantum-dot synthesis, and high-resolution full-color patterning are summarized. Then, the various device applications based on cutting-edge quantum dot technologies are described, including flexible white QLEDs, wearable QLEDs, and flexible transparent QLEDs. Finally, we showcase the integration of flexible QLEDs with wearable sensors, micro-controllers, and wireless communication units for the next-generation wearable electronics. npj Flexible Electronics (2018) 2:10 ; doi:10.1038/s41528-018-0023-3 INTRODUCTION Bendable displays can be utilized as foldable tablets whose screen Flexible displays have received significant attention owing to their sizes are tunable (Fig. 1e). Moreover, transparent flexible displays potential applications to mobile and wearable electronics1,2 such can be used for smart windows or digital signage, which can as smartphones, automotive displays, and wearable smart devices. -
Parylene News Spring 2015
Parylene News Spring 2015 Parylene Variants - Know Your Options There are four commercially available Parylene variants. All four Parylene D has two chlorine atoms on the benzene ring, a higher are ultra-thin, pinhole-free and absolutely conformal, with excellent degree of thermal stability, and superior physical and electrical moisture, chemical and dielectric barrier properties. However, there properties at high temperatures. It is most frequently selected are significant differences between them that make it important to for applications involving mechanical substrates undergoing select the optimum grade for a given application. thermal cycling. Parylenes N, C and D - the readily available commercial formula- Finally, Parylene F (or HT) carries fluorine atoms on the benzene tions - account for more than 90 percent of Parylene coating ring rather than hydrogen atoms, resulting in a higher continuous uses across electronic, industrial, medical device, automotive, service temperature, greater UV stability, and reduced dielectric military and aerospace applications. Each of these coatings constant and dissipation factor values. Parylene F is more costly, exhibits particular strengths, enabling users to meet specialized and requires specialized equipment and processing. Parylene F requirements. The fourth variant, Parylene F (or HT*), is more may be required for substrates that are directly exposed to costly, and delivers selective advantages. sunlight and function at low electric currents. Parylene N is the primary or precursor form of Parylene, In some cases, users may specify Parylene F unnecessarily characterized by particularly high dielectric strength and low where an alternative material could satisfy special requirements. dielectric constant, suiting it to high frequency uses. Its measured For example, Parylene D, with its extended temperature range, rate of deposition allows for excellent crevice penetration on may be a practical and more cost-effective coating option for mechanically complex substrates.