Portable Ii Personal Computer Maintenance and Service Guide
Total Page:16
File Type:pdf, Size:1020Kb
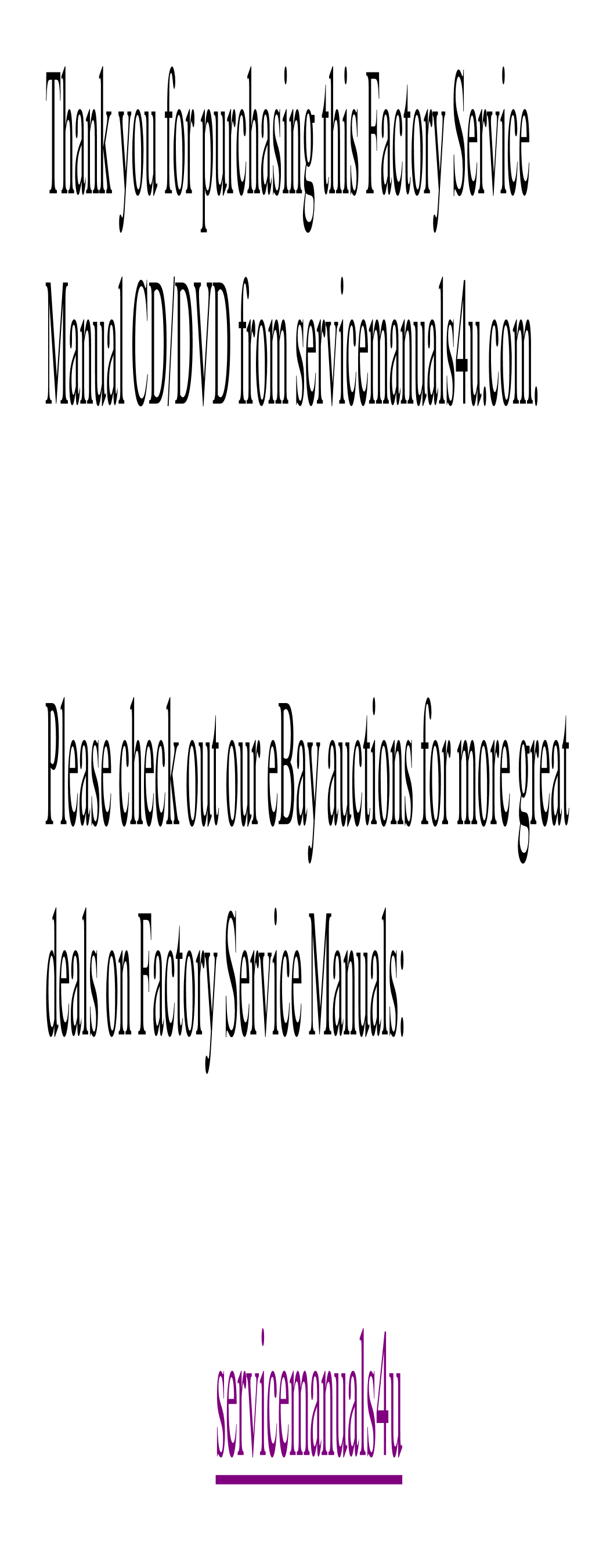
Load more
Recommended publications
-
Compaq Alphaserver ES45 Client/Server System Using Oracle9i, R2 Enterprise Edition for Tru64 UNIX ® and Compaq Tru64 UNIX 5.1A®
TPC Benchmark C® Full Disclosure Report Compaq AlphaServer ES45 Client/Server System Using Oracle9i, R2 Enterprise Edition for Tru64 UNIX ® and Compaq Tru64 UNIX 5.1A® Company System Name Database Software Operating System Name Software Compaq CompaqAlphaServer ES45 Oracle9i, R2 Enterprise Compaq Computer 4 CPU Client/Server System Edition Tru64 UNIX V5.1A Corporation for Tru64 UNIX Availability Date: May 9, 2002 Total System Cost TPC-C Throughput Price Performance Sustained maximum throughput - Hardware of systemrunning TPC Total systemcost/ - Software Benchmark C expressed in TPC-C® throughput 3-Years Maintenance transactions per minute $763,829 50,117 $15.24 I First Printing - January 2002 Compaq Computer Corporation believes that the information in this document is accurate as of its publication date; such information is subject to change without notice. Compaq Computer Corporation is not responsible for any inadvertent errors. Compaq conducts its business in a manner that conserves the environment and protects the safety and health of its employees, customers, and the community. The performance information in this document is for guidance only. System performance is highly dependent on many factors, including systemhardware, systemand user software, and user application characteristics. Customerapplications must be carefully evaluated before estimating performance. Compaq Computer Corporation does not warrant or represent that a user can or will achieve similar performance expressed in transactions per minute (tpmC) or normalized price/performance ($/tpmC). No warranty on system performance or price/performance is expressed or implied in this document. Copyright © 2002 Compaq Computer Corporation All Rights Reserved. Printed in U.S.A. Permission is hereby granted to reproduce this document in whole or in part provided the copyright notice printed above is set forth in full text on the title page of each itemreproduced. -
Compaq/Conner CP341 IDE/ATA Drive
Compaq/Conner CP341 IDE/ATA Drive 1987 Compaq/Conner CP341 IDE/ATA Drive Emergence of IDE/ATA as widely used interface. Why it's important The IDE/ATA (Integrated Drive Electronics/AT Attachment) interface, now known as PATA (Parallel ATA) and SATA (Serial ATA), became the dominant hard disk drive (HDD) interface for IBM compatible PCs, initially because of its low cost and simplicity of integration. Today it is supported by most operating systems and hardware platforms and is incorporated into several other peripheral devices in addition to HDDs. As an intelligent drive interface universally adopted on personal computers, IDE/ATA was an enabler of the acceleration of disk drive capacity that began in the early 1990s. Discussion: The IDE interface development was initially conceived by Bill Frank of Western Digital (WD) in the fall of 1984 as a means of combining the disk controller and disk drive electronics, while maintaining compatibility with the AT and XT controller attachments to a PC without changes to the BIOS or drivers. WD floated that idea by its largest customers, IBM, DEC, and Compaq in the winter and spring of 1985. Compaq showed interest, so Bill Frank collaborated with Ralph Perry and Ken Bush of Compaq to develop the initial specification. WD formed a Tiger team in the spring of 1985 to build such a drive, using externally purchased 3.5” HDAs (Head Disk Assemblies), but initially just provided IDE to ST506 controller boards that Compaq hard-mounted to 10MB and 20MB 3.5” Miniscribe ST506 drives for their Portable II computer line, announced in February 1986 [3, 15, 20]. -
Timeline of Computer History
Timeline of Computer History By Year By Category Search AI & Robotics (55) Computers (145)(145) Graphics & Games (48) Memory & Storage (61) Networking & The Popular Culture (50) Software & Languages (60) Bell Laboratories scientist 1937 George Stibitz uses relays for a Hewlett-Packard is founded demonstration adder 1939 Hewlett and Packard in their garage workshop “Model K” Adder David Packard and Bill Hewlett found their company in a Alto, California garage. Their first product, the HP 200A A Called the “Model K” Adder because he built it on his Oscillator, rapidly became a popular piece of test equipm “Kitchen” table, this simple demonstration circuit provides for engineers. Walt Disney Pictures ordered eight of the 2 proof of concept for applying Boolean logic to the design of model to test recording equipment and speaker systems computers, resulting in construction of the relay-based Model the 12 specially equipped theatres that showed the movie I Complex Calculator in 1939. That same year in Germany, “Fantasia” in 1940. engineer Konrad Zuse built his Z2 computer, also using telephone company relays. The Complex Number Calculat 1940 Konrad Zuse finishes the Z3 (CNC) is completed Computer 1941 The Zuse Z3 Computer The Z3, an early computer built by German engineer Konrad Zuse working in complete isolation from developments elsewhere, uses 2,300 relays, performs floating point binary arithmetic, and has a 22-bit word length. The Z3 was used for aerodynamic calculations but was destroyed in a bombing raid on Berlin in late 1943. Zuse later supervised a reconstruction of the Z3 in the 1960s, which is currently on Operator at Complex Number Calculator (CNC) display at the Deutsches Museum in Munich. -
Quickspecs Cluster Monitor Version 1.0
RETIRED: Retired products sold prior to the November 1, 2015 separation of Hewlett-Packard Company into Hewlett Packard Enterprise Company and HP Inc. may have older product names and model numbers that differ from current models. Compaq Insight Manager XE - QuickSpecs Cluster Monitor Version 1.0 MODELS Compaq Insight Manager XE – Cluster Monitor Version 1.0 New for Version 1.0 • Web Based Monitor for NT MSCS clusters • Support for all ProLiant Cluster kits • Monitor for cluster events and system hardware alerts • Selectable cluster configuration views for ease of control • Drill down to cluster nodes via Web tools for fast problem determination and resolution • Optional integration with Compaq Intelligent Cluster Administrator Version 1.5 (122284-B22 or 122284-292) • Y2K Compliant Ordering Information: Compaq Insight Manager console and the Compaq Server Management Agents are distributed as part of the Compaq Server Setup and Management package included with every Compaq server. Compaq Insight Manager XE may be requested via the Web at http://www.compaq.com/sysmanage. Latest Compaq Insight Manager console and the Compaq Server Management Agents may be downloaded from www.compaq.com/sysmanage. OVERVIEW Compaq Insight Manager XE - Cluster Monitor is a web-based subsystem that monitors the operation of Compaq ProLiant Clusters using Microsoft Cluster Server option of NT Enterprise Edition Version 4.0. Insight Manager XE has been extended to include Compaq ProLiant cluster support, providing a common interface for all management operations that previously required two or more interfaces. Compaq Insight Manager XE’s value has been enhanced to give system administrators additional control through its visual interface, comprehensive fault and configuration management and industry-leading, web based management for clusters, as well as its stand-alone systems. -
13 Critical Machines
THEBIRTHOFTHENOTEBOOK History has a way of reinventing itself. Like modern computer. Oh, and it weighed 2 pounds. Michael Jackson, the past makes strange and The only catch was that the Dynabook didn’t exist. The sometimes hideous transformations — and, as technology it required simply hadn’t been invented yet. At with Jacko, it’s not always easy to fi gure out what the time, only primitive LCD and plasma displays were being exactly happened. tinkered with, and the technology for one wireless modem took THEBIRTHOF Who invented the telephone? Was it Alexander Graham up half of an Econoline van. Bell or Elisha Gray? The Wright brothers made the fi rst fl ight The closest Kay ever got to building the Dynabook was a in a passenger plane, but what about Otto Lilienthal, whose cardboard mock-up fi lled with lead pellets. gliders infl uenced the brothers in their quest? From the game of chess to the pinball machine to the fortune cookie, the THE MINIATURE MAINFRAME THENOTEBOOK birth of countless famous products is a matter for debate. One of the factors keeping Xerox from working on the Dynabook And so it is with the portable computer. Who’s responsible was the market, which at the time could be summed up in one Mobile PC takes you on the strange and harrowing for pioneering the biggest shift in PC technology since the word: IBM. The computing giant had swallowed an astonishing punch card gave way to the magnetic disk? 81-percent share of the computer market by 1961, quashing journey to the origins of portable computing It depends on whom you ask. -
Quickspecs Tru64 UNIX Operating System V5.1A
RETIRED: Retired products sold prior to the November 1, 2015 separation of Hewlett-Packard Company into Hewlett Packard Enterprise Company and HP Inc. may have older product names and model numbers that differ from current models. QuickSpecs Tru64 UNIX Operating System V5.1A Overview Introduction The Compaq Tru64 UNIX Operating System is a 64-bit advanced kernel architecture based on Carnegie-Mellon University's Mach V2.5 kernel design, with components from Berkeley Software Distribution (BSD) 4.3 and 4.4, UNIX System V, and other sources. Tru64 UNIX is the Compaq Computer Corporation implementation of The Open Group's OSF/1 R1.0, R1.1, and R1.2 technology, and the Motif graphical user interface and programming environment. Tru64 UNIX provides symmetric multiprocessing (SMP), real-time support, and numerous features to assist application programmers in developing applications that use shared libraries, multithread support, and memory-mapped files. The full features of the X Window System, Version 11, Release 6.5 (X11R6.5) from The Open Group are supported. Tru64 UNIX complies with other standards and industry specifications, including major standards sponsored by The Open Group, POSIX, FIPS, and the System V Interface Definition (SVID). By providing support for SVID, Tru64 UNIX supports System V applications. The Tru64 UNIX Operating System is compatible with Berkeley 4.3 programming interfaces. DA - 11938 Worldwide — Version 1 — April 8, 2004 Page 1 RETIRED: Retired products sold prior to the November 1, 2015 separation of Hewlett-Packard Company into Hewlett Packard Enterprise Company and HP Inc. may have older product names and model numbers that differ from current models. -
Potential Final Exam Questions 2009.Pdf
Final Exam Questions 1. What are three characteristics of embedded systems? 2. What are 3 common design metrics for embedded systems? 3. List the benefits and drawbacks of the PLD: 4. Offer at least one financial reason why embedded systems are so prevalent in today’s world, from a financial standpoint. 5. What are the 4 phases of the RUP? 6. What are 7 examples of Embedded Systems? 7. Give a short explanation for the three key technologies for embedded systems. 8. Provide an overview of C# and its features. 9. Which term is not specific to communication protocol from the list below? • Port • Delegate • Socket • TCP 9. What are the main restrictions in developing a GUI using the .NET Compact Framework? 10. What does RUP stand for? 11. Define time‐to‐market and give the average time‐to‐market constraint. 12. List 5 examples of embedded systems. 13. Define the frequency‐hopping spread spectrum. 14. List and describe the two Bluetooth stacks. 15. Define IEEE 802.11 technology and name the 3 frequency bands it operates in. 16. The NetworkStream Class constructor takes 3 parameters. What are they? 17. What does WPAN stand for? 18. List the 3 key technologies for embedded systems. 19. What documents are included into a RUP Phase X Report (where X is replaced by the current phase number)? 20. What does Moore’s Law state? 21. What does RUP stand for? 22. List one thing that is not in the .NET Compact Framework. 23. __________is similar to an interface, but specifies just one signature for a single method. -
System Support Addendum
System Support Addendum PRODUCT NAME: PATHWORKS for DOS, Version 4.0 SSA 55.07.1 G-A (Formerly DECnet PCSA Client for DOS) HARDWARE REQUIREMENTS Maximum disk space required for the installation of all PATHWORKS for DOS software is 12MB of tree disk Systems, components, and peripherals specified be space (or 23,000 blocks on a VMS server). low are supported except as noted for specific software components: Other configurations, using selected components, may require less disk space. • An Intel® 8086-, 8088-, 80286-, 80386-, 80486- based personal computer from the Supported Base Systems Chart. OPnONALHARDWARE • A minimum of 640KB system memory. Expanded Memory Specification Version 4.0 Support • One network connection, either asynchronous or via PATHWORKS for DOS software supports the use of Ex an Ethernet controller. Refer to the Supported Base panded Memory Specification (EMS) applications that Systems Chart at the end of this document for a list are EMS, Version 4.0 compliant. The PATHWORKS for of supported Ethernet controllers in the various sup DOS networking software that can be loaded into EMS ported systems. More than one communications de requires 144KB of memory. vice may be installed in a system subject to system limitations. If use of another device is required, the Digital Printers system may need to be rebooted. A device cannot typically be shared with other communications prod PATHWORKS for DOS software supports the following ucts. Digital printers which can be connected to the PC: • In a PC local area network, at least one base system LA75 LA75P must have one diskette drive capable of reading 5.25 LA50 LA210 inch (360KB) diskettes or 3.50 inch (720KB) diskettes W250 W252 to load the distribution media. -
Compaq Desktop Computers, 1984
Now I -.ou ever dreamed o It sjmply works better. -1 Computer dreams. COMPAQB combined the best features of the best desktop computers. And then added exclusives you won't find on others. Today, they're together in one personal computer. The COMPAQ DESKPROTM. It's the most expandable desktop you can buy-inside instead ofout-so memory, additional functions and storage can grow as your needs grow. Without extra peripherals cluttering your desk. It's the most rugged desktop-with shock mounts and a steel shell so that it can live in the real world. It's the most compatible desktop, giving you full soft- ware and hardware compatibility with the industry's most popular personal computers. The COMPAQ DESKPRO runs thousands of programs written for the IBM@PC and XTright off the shelf. And it's two to three times faster than the industry standard to save you time. In fact, it's the fastest truly compatible computer you can buy. Dream computer. But there's more. The COMPAQ DESKPRO offers exclusives not found on any other personal computer. For instance, a dual-mode high-resolution monitor (amber or green) displays high-quality text and graphics with equal brilliance, saving you the cost and clutter of a second monitor. And a unique fixed disk drive baclzup device helps protect your valuable data. The list con- tinues. COMPAQ had the most successful first year in the history of American business. The fit, the finish, the culture of quality and attention to detail that made the COMPAQ@Portable and COMPAQ PLUSTMsuccesses are all evident in the COMPAQ DESKPRO. -
Installing Microsoft Windows 98 on Compaq Portable Products 2
White Paper Publication date: November 1998 PRT011B0998 Installing Microsoft Windows 98 Prepared by Software Marketing on Compaq Portable Products Compaq Computer Corporation Summary ....................................3 Abstract: This White Paper focuses on the steps necessary for the Installation Requirements and Dependencies......................3 successful installation of Microsoft Windows 98 on select Compaq Terms and Assumptions............4 Armada portable products. The steps outlined herein will provide the Installation Scripts .....................5 user with complete installation procedures for a clean installation or New Installation ........................5 an upgrade installation over Windows 3.1x/Windows 95. Upgrading from Windows 95 .....9 Upgrading from Windows Compaq has made available the Windows 98 specific installation 3.1x ........................................14 instructions and software enhancements (BIOS, hardware-enabling Installing Compaq Drivers and Enhancements...................19 drivers, and software applications) for the Armada 1100, 1500, Compaq Drivers and Support 1700, 3500, 4100, 4200, 7300, 7400, 7700, 7800, SB families, and Software .................................19 LTE 5000 families. This white paper instructs you on installing the SoftPaq Installation operating system and Compaq enhancements. Procedures .............................22 Appendix 1: Downloading Although Compaq will support customers that upgrade to Windows Software from the Compaq 98 on the Armada 6500, doing so at this time -
COMPAQ DESKPRO 386 Personal Computer MAINTENANCE and SERVICE GUIDE
COMPAQ DESKPRO 386 Personal Computer MAINTENANCE AND SERVICE GUIDE NOTICE The information in this guide is subject to change without notice. COMPAQ COMPUTER CORPORATION SHALL NOT BE LIABLE FOR TECH- NICAL OR EDITORIAL ERRORS OR OMISSIONS CONTAINED HEREIN; NOR FOR INCIDENTAL OR CONSEQUENTIAL DAMAGES RESULTING FROM THE FURNISHING, PERFORMANCE, OR USE OF THIS MATERIAL. This guide contains information protected by copyright. No part of this guide may be photocopied or reproduced in any form without prior written consent from Compaq Computer Corporation. © Copyright 1988 by Compaq Computer Corporation. All rights reserved. Printed in the U.S.A. COMPAQ®, COMPAQ DESKPRO®, COMPAQ DESKPRO 286®, COMPAQ PORTABLE II®, COMPAQ DESKPRO 386®, COMPAQ PORTABLE III®, COMPAQ DESKPRO 386/20®, COMPAQ PORTABLE 386®, COMPAQ DESKPRO 386s®, COMPAQ DESKPRO 386/25, COMPAQ DESKPRO 386/20e, and COMPAQ SLT/286 are trademarks of Compaq Computer Corporation. The software described in this guide is furnished under a license agreement of nondisclosure. The software may be used or copied only in accordance with the terms of the agreement. Microsoft®, MS®, and MS-DOS® are trademarks of Microsoft Corporation. MS® OS/2 is a product of Microsoft Corporation. Product names mentioned herein are used for identification purposes only and may be trademarks and/or registered trademarks of their respective companies. MAINTENANCE AND SERVICE GUIDE COMPAQ DESKPRO 386 Personal Computer Third Edition (February 1988) Second Edition (June 1987) First Edition (August 1986) Assembly Number 108033-003 Text Number 108035-003 Addendum 108431-001 (November 1988) Compaq Computer Corporation ® Registered United States Patent and Trademark Office. ii WARNING This equipment has been certified to comply with the limits for a Class B computing device, pursuant to Subpart J of Part 15 of FCC Rules. -
PORTABLE 386T and COMPAQ PORTABLE IIITM Are Trademarks of Compaq Computer Corporation
F: CONTENTS Introduction . 2 Standard Interfaces ........................ 6 Standard Models and Options . 2 Plasma Display ........................... 6 Features Illustration .......................... 3 Monitor and Video Boards ................... 6 Features/Functions/Benefits ....................4 Physical Characteristics ..................... 7 Microprocessor ........................... 4 Convenience Options ....................... 7 Expansion Unit ........................... 4 Software ................................ 7 Random-Access Memory .................... 4 Documentation ........................... 7 Clock .................................. 5 Memory Expansion ........................... 8 Mass Storage Devices ....................... 5 Technical Specifications ....................... 10 Tape Backup Expansion Unit ................. 5 Physical Measurements ....................... 13 Power Supply ............................ 5 Questions and Answers ....................... 15 Keyboard ...............................6 NOTICE THE INFORMATION CONTAINED IN THIS DOCUMENT IS SUBJECT TO CHANGE WITHOUT NOTICE. COMPAQ COMPUTER CORPORATION SHALL NOT BE LIABLE FOR TECHNICAL OR EDITORIAL ERRORS OR OMISSIONS MADE HEREIN; NOR FOR THE INCIDENTAL OR CONSEQUENTIAL DAMAGES RESULTING FROM THE FURNISHING, PERFORMANCE, OR USE OF THIS MATERIAL. Copyright © 1987, Compaq Computer Corporation. All Rights Reserved. COMPAQ is a Registered Trademark of Compaq Computer Corporation. COMPAQ PORTABLE 386T and COMPAQ PORTABLE IIITM are Trademarks of Compaq Computer