Simulation of High-Voltage Discharge Channel in Waterat Electro-Hydraulic Forming Using LS-DYNA®
Total Page:16
File Type:pdf, Size:1020Kb
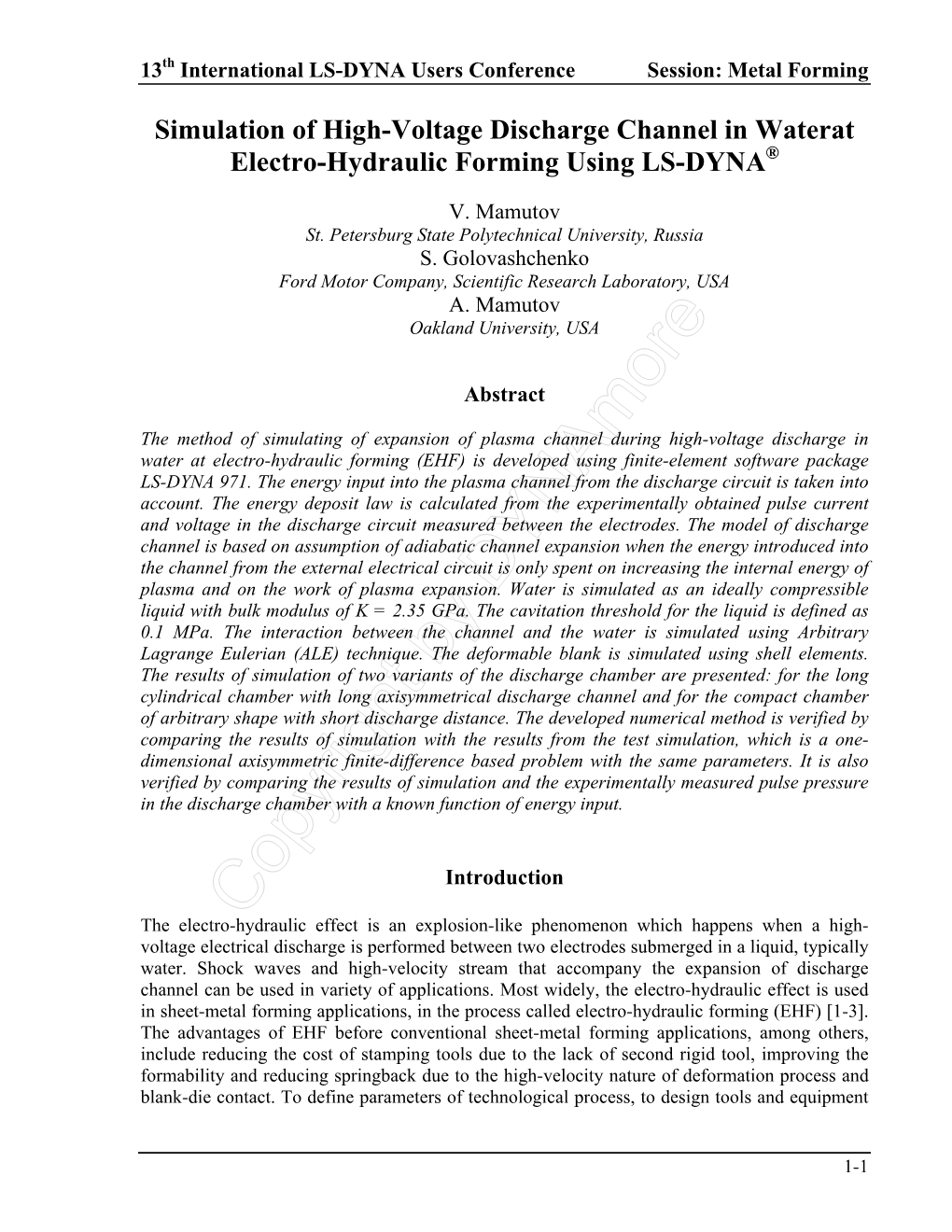
Load more
Recommended publications
-
First Results of Srf Cavity Fabrication by Electro-Hydraulic Forming at Cern S
THAA05 Proceedings of SRF2015, Whistler, BC, Canada FIRST RESULTS OF SRF CAVITY FABRICATION BY ELECTRO-HYDRAULIC FORMING AT CERN S. Atieh, A. Amorim Carvalho, I. Aviles Santillana, F. Bertinelli, R. Calaga, O. Capatina, G. Favre, M. Garlasché, F. Gerigk, S.A.E. Langeslag, K.M. Schirm, N. Valverde Alonso, CERN, Geneva, Switzerland G. Avrillaud, D. Alleman, J. Bonafe, J. Fuzeau, E. Mandel, P. Marty, A. Nottebaert, H. Peronnet, R. Plaut Bmax, Toulouse, France Abstract and combination of techniques: spinning, deep drawing, necking and hydroforming. In the framework of many accelerator projects relying on RF superconducting technology, shape conformity and processing time are key aspects for the optimization of niobium cavity fabrication. An alternative technique to traditional shaping methods, such as deep-drawing and spinning, is Electro-Hydraulic Forming (EHF). In EHF, cavities are obtained through ultra-high-speed deformation of blank sheets, using shockwaves induced in water by a pulsed electrical discharge. With respect to traditional methods, such a highly dynamic process can yield valuable results in terms of effectiveness, Figure 1: SPL 704 MHz elliptical cavity. repeatability, final shape precision, higher formability and reduced spring-back. In this paper, the first results of EHF on copper prototypes and ongoing developments for niobium for the Superconducting Proton Linac studies at CERN are discussed. The simulations performed in order to master the embedded multi-physics phenomena and to steer process parameters are also presented. INTRODUCTION Several projects at CERN require developments of new or spare superconducting RF cavities, in particular for the LHC consolidation, the LHC High Luminosity upgrade (HL-LHC), the Superconducting Proton Linac (SPL) and the Future Circular Collider (FCC) studies. -
Factors Effecting Electromagnetic Flat Sheet Forming Using the Uniform Pressure Coil
FACTORS EFFECTING ELECTROMAGNETIC FLAT SHEET FORMING USING THE UNIFORM PRESSURE COIL A THESIS Presented in Partial Fulfillment of the Requirements for the Degree of Master of Science in the Graduate School of The Ohio State University By Kristin E. Banik, B.S. ***** The Ohio State University 2008 Master’s Examination Committee: Approved by Professor Glenn S. Daehn, Adviser Professor Kathy Flores _______________________________ Adviser Graduate Program in Materials Science and Engineering ABSTRACT Electromagnetic forming is a possible alternative to sheet metal stamping. There are multiple limitations to the incumbent stamping methods including: complex alignment, changes to component shapes, and ductility issues, which often limits available formed geometry. Electromagnetic forming allows for the avoidance of some of these issues, but introduces a few other issues. In this thesis, the issues with electromagnetic forming will be discussed in conjunction with the application of the uniform pressure coil. Also, the effects on properties of the electromagnetically formed samples in comparison to the traditional samples will be presented. These properties include hardness, formability and interface issues. Lastly, discussed in this paper is the implementation of the Photon Doppler Velocimetry (PDV) system, a velocity measurement system used to determine the velocity of the workpiece and compare it to physics-based models of the process. ii Dedicated to my parents. iii ACKNOWLEDGMENTS I want to thank my adviser, Dr. Glenn Daehn for his support and guidance throughout graduate school and in running experiments and writing my thesis. I would also like to thank John Bradley, Steve Hatkevich and Allen Jones for their support of the work in our group as well as electromagnetic forming. -
Mechanical and Electrohydraulic Forming Processes
Process reliability and reproducibility of pneumo- mechanical and electrohydraulic forming processes W. Homberg1, E. Djakow1, O. Damerow1 1 Chair of Manufacturing and Forming Technology (LUF), Paderborn University, Paderborn Germany Abstract A sufficiently high process reliability and reproducibility is mandatory if a high-speed forming process is to be used in industrial production. A great deal of basic research work into pneumo-mechanical and electrohydraulic forming has been successfully performed in different institutions in the past. There, the focus has been more on process related correlations, such as the influence and interaction of different parameters on the course and result of those processes. The aspects of reliability and reproducibility have not been examined to a sufficient extent. Hence, in the case of pneumo-mechanical forming, insufficient investigations have been conducted into the effect that key parameters like the kinetic energy level, the filling height of the working media or the conditions inside the acceleration tube have on the reproducibility and course of the process. For electrohydraulic forming, the repeatability has worsened on occasions up to now. To improve the forming results and, in particular, the reputability of the process, it is necessary to examine the tool parameters associated with the electrodes and the working media. That is why research of this type is currently ongoing at the LUF. One important issue here is examining the options that exist for visualising the way the spark takes hold in the discharge chamber. Keywords High Speed Forming, Pneumo-mechanical Forming, Electrohydraulic Forming 1 Introduction The global trend towards the sustainable use of rare resources and the increasing demands of consumers for security items for products, for example, are leading to more complex components that are subject to high quality requirements. -
31St Daaam International Symposium on Intelligent Manufacturing and Automation
31ST DAAAM INTERNATIONAL SYMPOSIUM ON INTELLIGENT MANUFACTURING AND AUTOMATION DOI: 10.2507/31st.daaam.proceedings.055 TECHNOLOGIES OF HIGH-VELOCITY FORMING Darko Sunjic, Stipo Buljan & E. Gomes This Publication has to be referred as: Sunjic, D[arko]; Buljan, S[tipo] & Gomes, E[duarda] (2020). Technologies of High-Velocity Forming, Proceedings of the 31st DAAAM International Symposium, pp.0403-0407, B. Katalinic (Ed.), Published by DAAAM International, ISBN 978-3-902734-29-7, ISSN 1726-9679, Vienna, Austria DOI: 10.2507/31st.daaam.proceedings.055 Abstract Technologies of high-velocity forming are mostly used for forming workpieces in which conventional technologies do not have a good effect. It is not possible to form certain workpieces with conventional technologies due to the complexity of the surfaces and shapes, type of materials, dimensions of the workpiece or other technical parameters of the workpiece. Increased market demands, especially in the automotive, aerospace and military industries, have expedited the development of new technologies and thus high-velocity technologies. Some of the technologies which are included in this are explosive forming, electromagnetic forming, electrohydraulic forming, and others. The paper describes these technologies and gives their advantages and disadvantages. Keywords: unconventional technologies; explosive forming; electromagnetic forming; high-velocity forming; forming 1. Introduction The paper describes the technologies that are best known and the technologies that are most used in high-velocity forming. High-velocity forming or high energy rate forming include technologies that use a large amount of energy in a very short time interval. The reason for these needs as well as the division itself are explained in the paper. -
Multi-Scale Characterization of Hyperplasticity and Failure in Dual Phase Steels Subject to Electrohydraulic Forming
University of Windsor Scholarship at UWindsor Electronic Theses and Dissertations Theses, Dissertations, and Major Papers 2013 Multi-scale Characterization of Hyperplasticity and Failure in Dual Phase Steels Subject to Electrohydraulic Forming Javad Samei University of Windsor Follow this and additional works at: https://scholar.uwindsor.ca/etd Recommended Citation Samei, Javad, "Multi-scale Characterization of Hyperplasticity and Failure in Dual Phase Steels Subject to Electrohydraulic Forming" (2013). Electronic Theses and Dissertations. 4929. https://scholar.uwindsor.ca/etd/4929 This online database contains the full-text of PhD dissertations and Masters’ theses of University of Windsor students from 1954 forward. These documents are made available for personal study and research purposes only, in accordance with the Canadian Copyright Act and the Creative Commons license—CC BY-NC-ND (Attribution, Non-Commercial, No Derivative Works). Under this license, works must always be attributed to the copyright holder (original author), cannot be used for any commercial purposes, and may not be altered. Any other use would require the permission of the copyright holder. Students may inquire about withdrawing their dissertation and/or thesis from this database. For additional inquiries, please contact the repository administrator via email ([email protected]) or by telephone at 519-253-3000ext. 3208. Multi-scale Characterization of Hyperplasticity and Failure in Dual Phase Steels Subject to Electrohydraulic Forming By Javad Samei A Dissertation Submitted to the Faculty of Graduate Studies through Materials Engineering in Partial Fulfillment of the Requirements for the Degree of Doctor of Philosophy at the University of Windsor Windsor, Ontario, Canada ©2013 Javad Samei Multi-scale Characterization of Hyperplasticity and Failure in Dual Phase Steels Subject to Electrohydraulic Forming by Javad Samei APPROVED BY: ________________________________________________________ Dr. -
1. Introduction 2. Experimental Procedure Microstructural And
Materials Research. 2015; 18(4): 843-852 © 2015 DOI: http://dx.doi.org/10.1590/1516-1439.000314 Microstructural and Micromechanical Effects of Cold Roll-forming on High Strength Dual Phase Steels Meritxell Ruiz-Andresa, Ana Condea, Juan de Damboreneaa, Ignacio Garciaa* aCentro Nacional de Investigaciones Metalúrgicas – CENIM-CSIC, Madrid, Spain Received: June 18, 2015; Revised: June 29, 2015 In this work correlation between the 1000 MPa dual phase (DP) steel microstructure and the strain gained after roll-forming process have been studied by both microstructural and micromechanical analysis. The scanning electron microscope (SEM) inspection in the bent area reveals changes in the ferrite-martensitic microstructure. The plastic deformation of DP steels originates defects at the edges of bent sheet make them partly responsible for the damage caused. In addition, electron backscatter diffraction (EBSD) measurements have been carried out for an in-depth characterization after roll-forming. A high density of misorientation of the crystal lattice within the ferrite strained grains is observed, mainly concentrated in the ferrite/martensite grain boundaries. Furthermore, the ultramicrohardness tests exhibit little dependence between mechanical parameters and the material properties. Keywords: dual phase steel, roll-forming, EBSD, ultramicrohardness, microstructure 1. Introduction High strength low alloy (HSLA) steels, specifically dual or cup drawing. Luo & Wierzbicki15 analysed the failure phase (DP) steels, are widely used in the automotive industry behaviour of DP steels during stretch-bending operations due to the necessity of improving fuel efficiency1-3, with its and summarized the typical damage accumulation in this subsequent energy saving and environmental protection4. area. Wu-rong et al.8 found that DP steels show competitive In addition, these DP steels have been developed to increase formability after cup drawing tests, despite encountering the highly demanding collision safety standards5 in the consistent shear cracks on the damage surfaces. -
Esr (Electro Slag Refining)
ESR (ELECTRO SLAG REFINING) ESR has been known since the 1930s, but it took approx 30 years before it became an acknowledged process for mass production of high-quality ingots. The ESR technology is of interest not only for the production of smaller weight ingots of tool steels and super alloys, but also of heavy forging ingots up to raw ingot weights of 165 tons. 1 It is a process of remelting and refining steel and other alloys for mission-critical applications in aircraft, thermal power stations, nuclear power plants, military technology. 2 The consumable electrods are as cast or forged cylindrical parts made of an alloy to be remelt. An electroslag remelting process (ESR) starts when the lower tip of a consumable electrode is immersed into a pool of molten slag. The premelted slag possessing electrical conductivity is located on the water-cooled mold base connected to a power supply. The electric current (commonly AC) passing through the the slag keeps it at high temperature, which is about (200ºC) higher than the melting point of the remelted metal. 3 The electrode tip is heated by the hot slag and starts to melt forming droplets of liquid metal, which disconnect from the electrode and sink through the slag layer. The slag composition is based on calcium fluoride (CaF2), lime (CaO) and alumina (A The molten steel in form of both liquid film on the electrode tip and descending droplets contacts with the slag and get refined due to desulfurization and removal of non-metallic inclusions ( Sulfides and Oxides ). l2O3). 4 The droplets enters the molten steel pool, bottom of which is progressively solidifying. -
Technology of Metal Working − Part 2
Textbook for Vocational Training − Technology of Metal Working − Part 2 Table of Contents Textbook for Vocational Training − Technology of Metal Working − Part 2................................................1 Preface...................................................................................................................................................1 5. Manufacturing Method of Separating..................................................................................................2 5.1. Dividing.....................................................................................................................................3 5.2. Chip−detaching.......................................................................................................................10 5.3. Erosion....................................................................................................................................94 6. Manufacturing Method of Joining....................................................................................................102 6.1. Joining by Pressing On and In..............................................................................................105 6.2. Joining by Initial Shaping......................................................................................................120 6.3. Joining by Forming................................................................................................................124 6.4. Joining by Uniting Substances..............................................................................................131 -
ME477: Manufacturing Processes Introduction Manufacturing
Concept Introduction Design • Manufacturing? Organization Make or Buy – Making goods and articles ME477: – Shaping and treating Materials Virtual Product to perform desirable functions Organization • Manufacturing Processes Manufacturing Processes – Casting – Powder Processing (Shape, Raw Materials Material, – Forming Tolerance Patrick Kwon – Machining & Cost) Manufacturing – Surface processing Process Department of Mechanical Engineering – Joining Michigan State University • To make good and articles - A Manufacturing sequence of processes must be Process East Lansing, Michigan chosen, based on shape, material, tolerance and cost Manufacturing • Before MFG, a Make or Buy Process decision – Process Design 1 – Production Systems Part 2 Manufacturing as a set of Manufacturing processes • Manufacturing: 20% of U.S. GNP Power Management • Service sector: 70% of U.S. GNP (retail, transportation, banking, education, Labor Facility Machine communication, insurance and government). • Agriculture, Construction etc.: 10% of U.S. GNP • Manufacture comes from the Latin words manus A set Raw Materials Part (hand) and factus (make). of Processes • Definition: the application of physical and Concurrent or chemical processes to alter the geometries, Simultaneous Waste properties and appearance of a starting material Engineering in order to make and assemble it into a product. 3 4 Manufacturing Processes More Manufacturing Processes Deformation Processing Machining Polymer Processing Composite Processing Microelectronic Processing Casting Process Open -
Technology Reference Guide for Radioactively Contaminated Media (Guide) As a Reference for Technologies That Can Effectively Treat Radioactively Contaminated Sites
DISCLAIMER This Technology Guide, developed by USEPA, is meant to be a summary of information available for technologies demonstrated to be effective for treatment of radioactively contaminated media. Inclusion of technologies in this Guide should not be viewed as an endorsement ofeither the technology or the vendor by USEPA. Similarly, exclusion of any technology should not be viewed as not being endorsed by USEPA; it merely means that the information related to that technology was not so readily available during the development of this Guide. Also, the technology-specific performance and cost data presented in this document are somewhat subjective as they are from a limited number of demonstration projects and based on professional judgment. In addition, all images used in this document are from public domain or have been used with permission. FORWARD The Technology Reference Guidance for Radioactively Contaminated Media (Guide) is intended to aid in the selection of treatment technologies for remediation of radioactively contaminated media. The Guide is designed to help site managers, Remedial Program Managers (RPM), On-Scene Coordinators (OSC), their contractors and others to identify and understand technologies that are potentially useful in the remediation of radioactively contaminated media. This Guide is designed to give easy access to critical information on applied technologies that address radioactive contamination in solid and liquid media. The solid media includes soils, sediments, sludge and solid waste, but does not include buildings and structures. The liquid media includes groundwater, surface water, leachate and waste water. The Guide is an update of the 1996 document "Technology Screening Guide for Radioactively Contaminated Site," EPA-402-R-96-017. -
ASM Handbook Volume 14B Metalworking: Sheet Forming Contents Introduction
ASM Handbook_ Volume 14B Metalworking: Sheet Forming Contents Introduction ........................................................................................... 1 Introduction to Sheet-Forming Processes S.L. Semiatin ........................................................................................ 3 Historical Perspective .............................................................. 3 Classification of Sheet-Forming Processes ............................. 3 Process-Related Developments ............................................... 4 Rapid Prototyping and Flexible Manufacturing Techniques ........................................................................... 6 Materials-Related Developments ............................................ 7 Process Simulation, Design, and Control ................................ 8 Future Outlook ......................................................................... 9 Design for Sheet Forming Howard Kuhn .................................................................................... 11 Hole Punching ....................................................................... 11 Flanging ................................................................................. 12 Beads and Ribs ...................................................................... 14 Large Recesses ...................................................................... 14 Scrap Reduction .................................................................... 18 Shearing, Cutting, Blanking, and Piercing ...................................... -
Bell-Etal-ESAFORM-2016-Research
Research Directions in Hydroforming Technology Colin Bell1, a), Dr Saeed Tamimi2, b), Prof Jonathan Corney1, c), David Savings3, d), Nicola Zuelli2, e) 1Design, Manufacture and Engineering Management, University of Strathclyde, 75 Montrose St, Glasgow G1 1XJ 2Advanced Forming Research Centre (AFRC), University of Strathclyde, 85 Inchinnan Drive, Inchinnan PA49LJ 3Rolls-Royce plc, PO Box 31, Derby DE24 8BJ a)[email protected] b)[email protected] c)[email protected] d)[email protected] e)[email protected] Abstract. This paper both summarizes and explores the literature published between 1995 and 2015 on enhancing and extending hydroforming technology. Many different research areas have been proposed, all of which try to enhance the well-established manufacturing process by either improving formability or reducing costs. Each of the technological variations are first described and then their uses, benefits, drawbacks, and applications are discussed and summarized. BACKGROUND Hydroforming is a near net shape manufacturing process that uses large amounts of hydraulic pressure to form metal from readily available “blank” shapes into net or near net shape geometries. While the first examples of hydroforming can be traced all the way back to the 1890s and the first patent was issued in 1940, most of the technological development has taken place after 1950 (Zhang & Danckert, 1998). Hydroforming’s benefits stem from two key physical phenomena; the first is the ability of fluids to exert pressure on a surface completely evenly and in all directions and the second is the capacity to have a complicated pressure loading cycle which can vary pressure over a predetermined and optimized timeframe.