Aug. 21, 1962 R
Total Page:16
File Type:pdf, Size:1020Kb
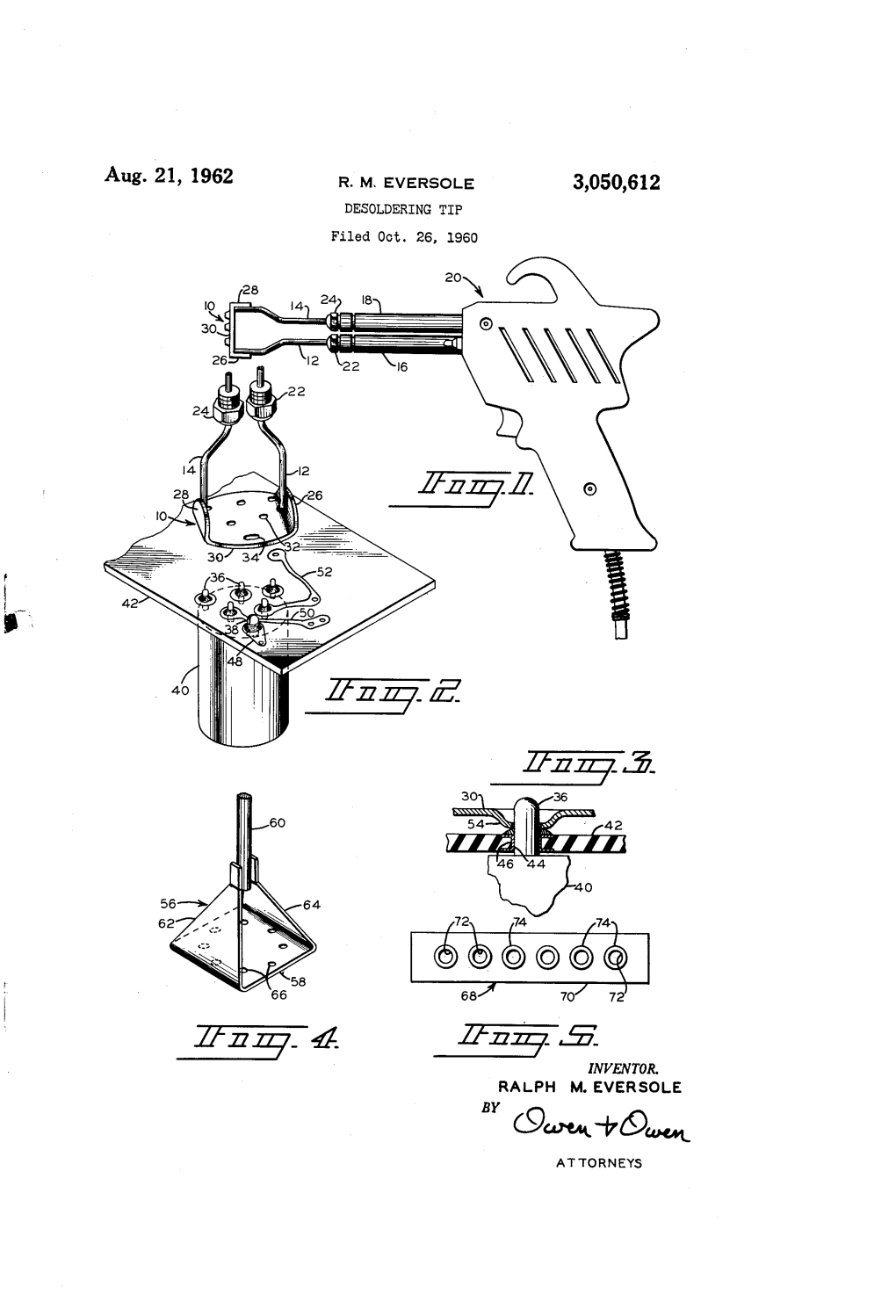
Load more
Recommended publications
-
AN-1448 Application Note
AN-1448 APPLICATION NOTE One Technology Way • P. O. Box 9106 • Norwood, MA 02062-9106, U.S.A. • Tel: 781.329.4700 • Fax: 781.461.3113 • www.analog.com Recommended Rework Procedure for PBGA Packages By Ramon Navarro INTRODUCTION component, such as heating the component beyond the This application note provides a recommended procedure for specified peak temperature or overexposure to heat, can lead to removing a plastic ball grid array package (PBGA) from a package delamination or external physical damage (see Figure 2 printed circuit board (PCB). and Figure 3). For a component that must undergo further analysis, delamination caused by improper component removal PACKAGE DESCRIPTION makes identifying the true failure mechanism more difficult. The PBGA is a package format with a main distinguishing Consequently, proper removal of the defective component is characteristic of an array of solder balls as a mode of interacting necessary to conduct effective failure analysis. with the substrate (such as a PCB). This feature gives the PBGA an advantage over other package formats with different pin configurations (such as single, dual in line, and quad types) in terms of achieving higher pin count density. Interconnection inside the PBGA package is implemented through wire bonding or flip chip technology. The die for the PBGA, which contains the integrated circuit, is encapsulated in mold compound. 15521-001 Figure 1. Illustration of a PBGA Component REWORK FOR PGBA COMPONENTS If defects are present after attaching the PBGA component to the PCB, rework to remove the defective component and replace it with a functioning device. Before removing the device, apply 15521-002 heat on the defective component until the solder joints are Figure 2. -
Recommendations for Assembly of Infineon to Packages
Additional Information, DS1, March 2008 Recommendations for Assembly of Infineon TO Packages Edition 2008-03 Published by Infineon Technologies AG 81726 München, Germany © 2008 Infineon Technologies AG All Rights Reserved. Legal Disclaimer The information given in this document shall in no event be regarded as a guarantee of conditions or characteristics. With respect to any examples or hints given herein, any typical values stated herein and/or any information regarding the application of the device, Infineon Technologies hereby disclaims any and all warranties and liabilities of any kind, including without limitation, warranties of non-infringement of intellectual property rights of any third party. Information For further information on technology, delivery terms and conditions and prices, please contact the nearest Infineon Technologies Office (www.infineon.com). Warnings Due to technical requirements, components may contain dangerous substances. For information on the types in question, please contact the nearest Infineon Technologies Office. Infineon Technologies components may be used in life-support devices or systems only with the express written approval of Infineon Technologies, if a failure of such components can reasonably be expected to cause the failure of that life-support device or system or to affect the safety or effectiveness of that device or system. Life support devices or systems are intended to be implanted in the human body or to support and/or maintain and sustain and/or protect human life. If they fail, it is reasonable to assume that the health of the user or other persons may be endangered. Assembly & Interconnect Technology Table of Contents 1 Package Description and Thermal Performance . -
Copper Tin Intermetallic Crystals and Their Role in the Formation of Microbridges Between the Leads of Hand Reworked Fine Pitch Components
As originally published in the IPC proceedings. Copper Tin Intermetallic Crystals and Their Role in the Formation of Microbridges between the Leads of Hand Reworked Fine Pitch Components Jeff Kukelhan BAE Systems Electronics, Intelligence, & Support Fort Wayne, Indiana Abstract Wave soldering is a mature manufacturing process that metallurgically joins component and PWB termination features by passing them together across the flowing surface of a molten solder reservoir. During this exposure, copper from through holes, surface mount lands, and component leads, continually dissolves into the molten solder. Unless the solder in the reservoir is regularly changed, the dissolved copper eventually reaches a point of saturation, and orthorhombic Cu6Sn5 crystals begin to precipitate out of the molten solder, causing it to become gritty and sluggish. Solder drawn from such a saturated wave solder pot can solidify into joints whose surface finish exhibits many needle like metallic protrusions. These protrusions are in fact orthorhombic Cu6Sn5 crystals. Recently, BAE Systems has determined that this same phenomenon is responsible for the formation of nearly invisible intermetallic microbridges between fine pitch surface mount component leads. They form when a solder bridge from a surface mount paste reflow operation is hand reworked with a soldering iron and copper desoldering braid. This paper documents several short circuit failures caused by this phenomenon, the investigation that identified the root cause of the problem, and the rework techniques that can be used to prevent its occurrence. Introduction BAE Systems’ Fort Wayne, Indiana facility manufactures electronic hardware for use in both commercial and military avionics applications. The hardware typically contains surface mount assemblies, which are made with one of two solder paste alloys: Sn63/Pb37 and Sn62/Pb36/Ag2. -
United States Patent (19) 11) Patent Number: 5,054,681 Kim 45 Date of Patent: * Oct
United States Patent (19) 11) Patent Number: 5,054,681 Kim 45 Date of Patent: * Oct. 8, 1991 (54) COMPONENT DESOLDERING TOOL FOREIGN PATENT DOCUMENTS 76) Inventor: Henry I. Kim, 12665 Salmon River 260999 7/1988 France .................................. 228/51 Rd., San Diego, Calif. 92129 1 i3172 5/1989 Japan ..................................... 228/51 * Notice: The portion of the term of this patent OTHER PUBLICATIONS subsequent to Jan. 23, 2007 has been disclaimed. IBM Technical Disclosure Bulletin, "Soldering Iron Tip', vol. 1, No. 2, p. 18, Aug. 1958. 21 Appl. No.: 557,451 Research Disclosure, "Hot Air Deflector . ', Kenneth Mason Publications Ltd., England, No. 281, 22 Fied: Jul. 25, 1990 Jul. 1988. 51 Int. Cl. ................................................ B23K 3/02 52 U.S. Cl. ...................................... 228/191; 228/51; Primary Examiner-Samuel M. Heinrich 228/55 Attorney, Agent, or Firm-Ralph S. Branscomb 58) Field of Search ..................... 228/19, 180.2, 191, 57 ABSTRACT 228/.264, 51, 55; 29/764 A tool for desoldering quadrilateral surface-mount (56) References Cited components such as integrated circuits which have a row of leads on each of the four sides, the tool compris U.S. PATENT DOCUMENTS ing a metallic hood with a depending skirt which 1,297,245 3/1919 Reddicliffe ... a 228/55 contacts the rows of leads when the hood is snapped 1,881,698 10/1932 Kuriyama ... - 228/55 over the component. The hood is heated with a hot air 2,724,041 1/1955 Anton .................. - - - - a 228/55 gun or a heating element, and conducts the heat to the 3,393,857 7/1968 Taylor, Jr. -
SMD Soldering Workshop Ñ Rule 3: the Point on the Iron-Tip Is NOT the Hottest Part
SMD Soldering Workshop ñ Rule 3: The point on the iron-tip is NOT the hottest part. This takes some getting used to. Learn to use SMD Soldering the side of the tip near the point. It's all about get- ting the heat to flow from the iron to the joint. If 1 Overview you sit in one spot for a long period of time and We want to share with you some soldering tech- nothing is flowing, take a step back, clean your tip, niques that will allow you to solder 0.5mm pitch de- add a bit a solder to the tip, and try soldering the vices and small 0603 components. This is by no means a joint again. certification course! There is a lot of information, train- ñ Rule 4: The soldering iron is only there for heat, not ing, and practice that goes into proper soldering. We solder. You use the iron to heat two things - the just want to show you the basics. part and the board, and then you add solder to the This packet with associated tutorial videos is available two heated parts. You do not add a glob of solder to online at: the tip and then rub this mess against the two things you're trying to solder together. Use the side http://www.sparkfun.com/commerce/ of the iron (remember, not the point) to heat the present.php?p=BEE-6-SolderingBasics two parts while adding solder from the opposite side. ñ Rule 5: Perfectionism kills. If you solder a joint, Soldering is the act of heating up a pad on a PCB and it looks alright, let it be. -
Application Note
AN4388 Quad Flat Package (QFP) Rev. 3.0 — 15 August 2019 Application note Document information Information Content Keywords quad flat package QFP Abstract This application note provides guidelines for the handling and board mounting of NXP's QFP packages including recommendations for printed-circuit board (PCB) design, board mounting, and rework. NXP Semiconductors AN4388 Quad Flat Package (QFP) 1 Introduction This application note provides guidelines for the handling and board mounting of NXP's QFP packages. Included in this application note are recommendations for the design of Printed Circuit Boards (PCB), board mounting, and rework. Generic information of package properties, such as Moisture Sensitivity Level (MSL) rating, board level reliability, mechanical and thermal resistance data are also provided. Because semiconductor components are electrically and mechanically sensitive devices, proper precautions for handling, packing and processing QFP packages are described. AN4388 All information provided in this document is subject to legal disclaimers. © NXP B.V. 2019. All rights reserved. Application note Rev. 3.0 — 15 August 2019 2 / 40 NXP Semiconductors AN4388 Quad Flat Package (QFP) 2 Scope This application note contains generic information about various QFP packages assembled at NXP and NXP's assembly and test vendors. Refer to Section 9 "Downloading package information from the NXP website" for step-by-step instructions for retrieving package information. For more details about NXP products, visit www.nxp.com or contact the appropriate product application team. Development efforts are required to optimize the board assembly process and application design per individual product requirements. Additionally, industry standards (such as IPC and JEDEC), and prevalent practices in the board assembly environment are good references. -
The Basic Soldering Guide Photo Gallery
The Basic Soldering Guide Photo Gallery (Left) Printed circuit board copper tracks must be clean to begin with, especially if they're not previously "tinned" with solder. Clean any raw p.c.b. copper tracks gently with e.g. an abrasive rubber block available from electronics suppliers. (Right) Clean the iron "bit" (soldering iron tip) using a damp sponge. The soldering iron featured is an Ungar Concept 2100 Soldering Station. Other popular brands of soldering equipment include Weller and Antex. (Left) A useful product is Multicore's Tip Tinner Cleaner (TTC) - a 15 gramme tin of special paste which cleans and "tins" the soldering iron iron, in one go. New tips must be tinned immediately when used for the first time. (Right) Insert components and splay the leads so that the part is held in place. (Left) It's usually best to snip the electronic component wires to length prior to soldering. This helps prevent transmitting mechanical shocks to the copper foil.(Right) Apply a clean soldering iron tip to the copper solder pad and the component lead, in order to heat both items at the same time. (Left) Continue heating and apply a few millimetres of solder. Remove the iron and allow the solder joint to cool naturally. (Right) It only takes a second or two, to make the perfect joint, which should be nice and shiny. Check the Guide for troubleshooting help. An example of a "dry" or "gray" soller joint - the solder failed to flow, and instead beaded to form globules around the wire. The Basic De-soldering Guide Photo Gallery (and Black Museum of Bad Soldering) (Left) The two solder joints to be desoldered, to enable a faulty electrolytic capacitor to be removed from the printed circuit board. -
Solder Reflow Guide for Surface Mount Devices
Solder Reflow Guide for Surface Mount Devices Technical Note FPGA-TN-02041 Version 3.8 November 2017 Solder Reflow Guide for Surface Mount Devices Technical Note Contents Acronyms in This Document ................................................................................................................................................. 3 1. Introduction ................................................................................................................................................................... 4 2. Reflow ........................................................................................................................................................................... 4 3. Inspection ..................................................................................................................................................................... 4 4. Cleaning Recommendations ......................................................................................................................................... 4 5. Rework Recommendations ........................................................................................................................................... 4 6. BGA Reballing ............................................................................................................................................................... 5 7. Pb-Free/Halogen-Free (RoHS-Compliant) Products ..................................................................................................... -
Printed Circuit Board Rework - Pad Preparation
Printed Circuit Board Rework - Pad Preparation Our thanks to Weller Division of Cooper Tools for allowing us to reprint the following. Claude W. “Bubba” Powers, Manager, Technical Services Cooper Tools – Professional Tools Group, Weller® Division Rework Process After each successful component removal process, it is imperative that the printed circuit board pads be properly prepped so that the new device can be placed down with a high degree of accuracy and repeatability. The pads should be completely level so that all leads or solder balls of the device being replaced make full contact with the cleaned pads. Tools of the Trade To do this, there are certain tools that every technician should have to properly perform the cleaning process. This application will normally require the use of several different types of tools and subsequent materials. Below Solder Pad Excavation is a list of materials that can be found on most rework benches. Begin by using the vacuum desoldering tool with a tiplet designed to match the pad dimension for the component • Temperature controlled rework system with being reworked. The desoldering tiplet should be slightly vacuum and hot air capabilities larger than the pad being cleaned, but not too large • Vacuum desoldering iron with tiplet (20% larger than pad is the maximum). A tiplet that is too large may damage the surrounding solder mask or • Soldering iron with standard tip adjacent pads and components. • Blade style tip (width of blade to match On the rework station, select a temperature for the component dimensions) desoldering tool that closely matches the process • Wire cored solder (solder and flux should match temperature when the PC Board was originally original soldering process criteria) assembled. -
Iot Security-Part 13 (Introduction to Hardware Recon)
⌂ Home › ☷ All Blogs › ✍ Shakir › IoT Security-Part 13 (Introduction To Hardware Recon) Shakir 1-September-2020 IoT Security Part 13 (Introduction to Hardware Recon) This blog is part of the IoT Security series where we discuss the basic concepts pertaining to the IoT/IIoT eco-system and its security. If you have not gone through the previous blogs in the series, I would urge you to go through those first. In case you are only interested in the basics of Hardware recon, feel free to continue. IoT Security - Part 1 (101 - IoT Introduction And Architecture) IoT Security - Part 12 (MQTT Broker Security - 101) In this blog, we will discuss how to perform reconnaissance on hardware. The hardware comprises physical electronics components that include micro-controller, microprocessor, resistor, capacitor, LEDs, etc. which make a device work. The hardware reconnaissance process consists of several steps like device disassembly, looking at the various components, debug ports like UART, JTAG/SWD, identifying the chips, finding the respective datasheet, and finding the information from the datasheet. so let’s get into each of them. Importance of Hardware Recon During the process of pentesting or security research in general, before starting to attack the target we have to have a complete understanding of the system even if it is a blackbox. The recon process helps in identifying different components that make up the system so we can gear our attacks towards what we know and what loopholes we have identified while understanding the system. During the recon, we identify pieces and connect those pieces to derive intelligent information that will help in compromising the security of the system. -
Soldering and Desoldering
Soldering Step-by-step instructions and for making (and unmaking) Desoldering the perfect solder joint. By Joe Grand The two key parts of soldering are good heat distribution and cleanliness of the soldering surface and component. With practice, you’ll become comfortable and experienced with the process. In this primer, I’ll explain how to solder a component onto a printed circuit board (PCB). I’ll also provide desoldering tips and show you how to remove a surface-mount component from a printed circuit board using a Chip Quik kit. And I’ll show you how to remove a component by removing the solder in a way that won’t damage the components or the circuit board. Reprinted with permission from Hardware Hacking, copyright 2004, Syngress Publishing, ISBN: 1-932266-83-6, pp. 34–40. Joe Grand by Photography 50 Make: Workshop+Tool Guide p050-53_SIP_SolderPrimer_F1.indd 50 10/11/10 10:46:01 AM overvIew toolS AND tips Tools of the Trade The Chip Quik SMD Removal Kit Soldering iron You could pay Chip Quik SMD Removal Kit The Chip Quik SMD Removal as little as $10 or as much as Allows you to remove surface Kit allows you to quickly $1,000 for a soldering iron. mount components quickly and and easily remove surface- I recommend a fine-tip, 700°F, easily. Chipquik.com offers the mount components such 50W soldering stick iron. kit for $16. as PlCC, SOIC, TSOP, QFP, A good general-purpose iron and discrete packages. The for hardware hacking is the Sandpaper A very fine-grit main component of the kit Weller W60P Controlled-Output sandpaper is useful for remov- is a low-melting-temperature Soldering Iron, which sells ing oxidation from component solder (requiring less than for under $70. -
United States Patent [19] [111 3,874,443 Bayer [45] Apr
United States Patent [19] [111 3,874,443 Bayer [45] Apr. 1, 1975 [54] HEAT DISSIPATOR Primary Examiner-Charles Sukalo Attorney, Agent, or Firm-—Torres & Berryhill [76] lnventor: Joseph V. Bayer; 2214 Monterrey ‘ Dr., Kemah, Tex. 77565 [57] ABSTRACT [22] Filed: July 16, 1973 Disclosed is a heat dissipator for use in soldering or [21] Appl.No.:379,343 desoldering dual-inline-pin integrated circuits com prising two identical heat dissipation clip members [52] US. Cl .................... .. 165/47, 165/80, 165/185, each having a notch forming a jaw. The clip members 174/15, 269/254 R, 81/417 are pivotably fastened together and biased by a spring [51] Int. Cl. ............................................ .. F24h 3/00 such that the jaw clamps over the integrated circuit {58] Field of Search .... .. 165/47, 80, 185; 174/15 R, when in use. l74/D1G. 5; 228/46; 81/417; 269/254 CS, In an alternate embodiment, the heat dissipator may 254 MW, 254 DF, 254 D, 254 R be modified to function as an extractor for removing or inserting an integrated circuit on a printed circuit [56] References Cited board, as well as functioning as a heat sink. The UNITED STATES PATENTS modi?ed embodiment includes an adaptor member 3.552.630 1/1971 Dean ........ .. .i 223/46 attached to each clip member having a plurality of 3,566,958 3/1971 Zelina .......... i. 174/DIG. 5 ?ngers to engage the integrated circuit. 3.652.903 3/1972 Eriksson ............................. .. 165/30 8 Claims, 6 Drawing Figures PATENTED APR 1 I975 5.874.443 \l, / HEl IWVHKIJBZ/IOICU.