United States Patent C Patented Oct
Total Page:16
File Type:pdf, Size:1020Kb
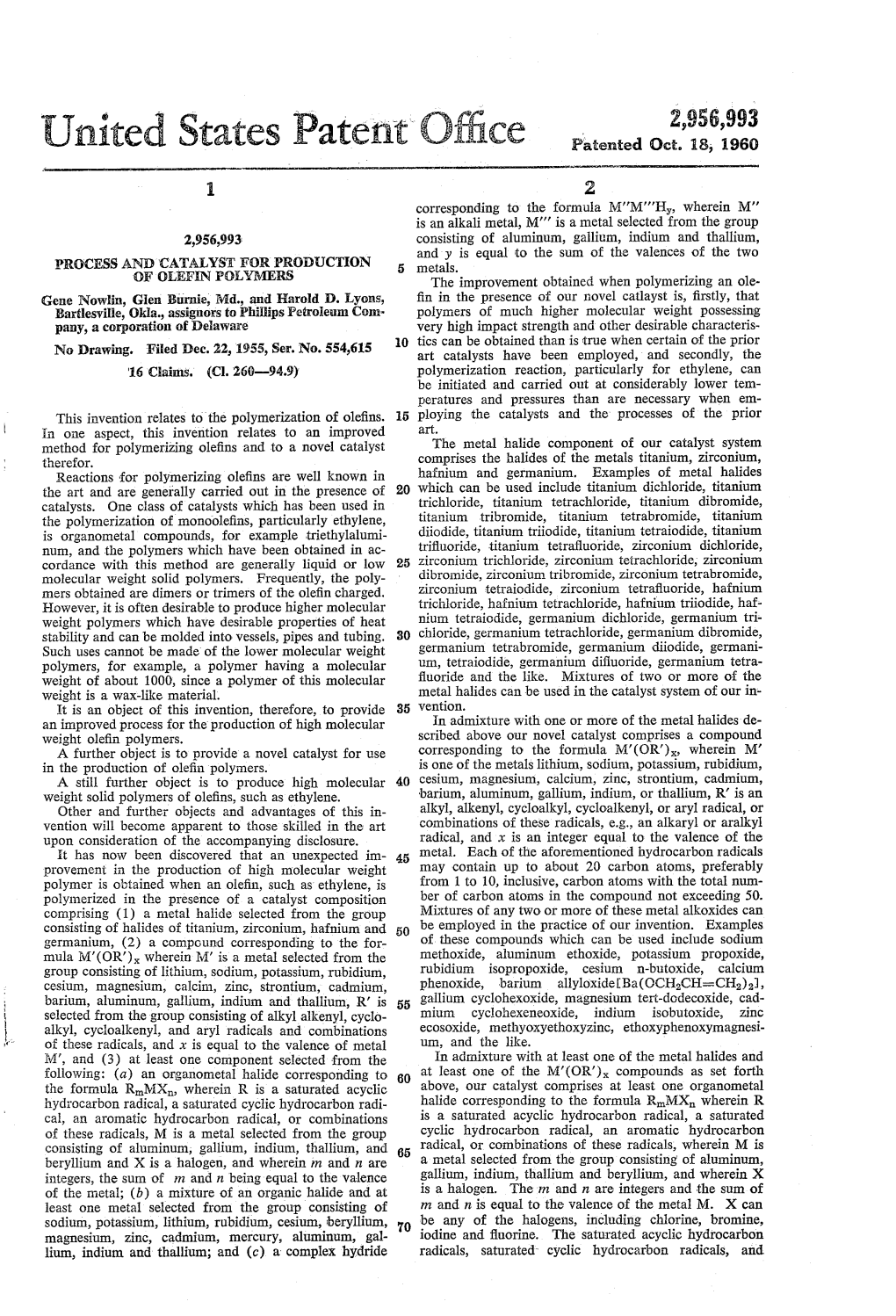
Load more
Recommended publications
-
Organometallic Compounds Suitable for Use in Vapor Deposition Processes
Europäisches Patentamt *EP001464724A2* (19) European Patent Office Office européen des brevets (11) EP 1 464 724 A2 (12) EUROPEAN PATENT APPLICATION (43) Date of publication: (51) Int Cl.7: C23C 16/22, C07F 7/30, 06.10.2004 Bulletin 2004/41 C07F 7/02 (21) Application number: 04251948.8 (22) Date of filing: 01.04.2004 (84) Designated Contracting States: (72) Inventors: AT BE BG CH CY CZ DE DK EE ES FI FR GB GR • Shenai-Khatkhate, Deodatta Vinayak HU IE IT LI LU MC NL PL PT RO SE SI SK TR Danvers Massachusetts 01923 (US) Designated Extension States: • Power, Michael Brendan AL HR LT LV MK Newburyport Massachusetts 01950 (US) (30) Priority: 05.04.2003 US 460791 P (74) Representative: Kent, Venetia Katherine 22.10.2003 US 513476 P Rohm and Haas (UK) Ltd European Patent Department (71) Applicant: Rohm and Haas Electronic Materials, 28th. Floor, City Point L.L.C. One Ropemaker Street Marlborough, Massachusetts 01752 (US) London EC2Y 9HS (GB) (54) Organometallic compounds suitable for use in vapor deposition processes (57) Organometallic compounds suitable for use as metallic precursors are also provided. Such Group IV vapor phase deposition precursors for Group IV metal- metal-containing films are particularly useful in the man- containing films are provided. Methods of depositing ufacture of electronic devices. Group IV metal-containing films using certain organo- EP 1 464 724 A2 Printed by Jouve, 75001 PARIS (FR) EP 1 464 724 A2 Description Background of the Invention 5 [0001] The present invention relates generally to the field of organometallic compounds. -
(12) Patent Application Publication (10) Pub. No.: US 2004/0194703 A1 Shenai-Khatkhate Et Al
US 2004O194703A1 (19) United States (12) Patent Application Publication (10) Pub. No.: US 2004/0194703 A1 Shenai-Khatkhate et al. (43) Pub. Date: Oct. 7, 2004 (54) ORGANOMETALLIC COMPOUNDS Related U.S. Application Data (75) Inventors: Deodatta Vinayak Shenai-Khatkhate, (60) Provisional application No. 60/460,791, filed on Apr. Danvers, MA (US); Michael Brendan 5, 2003. Provisional application No. 60/513,476, filed Power, Newburyport, MA (US) on Oct. 22, 2003. Correspondence Address: Publication Classification S. Matthew Cairns (51) Int. Cl." .............................. C23C 16/00; CO8F 4/44 EDWARDS & ANGELL, LLP U.S. Cl. ....................... 118/715; 427/252; 427/248.1 P.O. BOX 55874 (52) Boston, MA 02205 (US) (57) ABSTRACT (73) Assignee: Rohm and Haas Electronic Materials, Organometallic compounds Suitable for use as vapor phase L.L.C., Marlborough, MA deposition precursors for Group IV metal-containing films are provided. Methods of depositing Group IV metal-con (21) Appl. No.: 10/817,618 taining films using certain organometallic precursors are also provided. Such Group IV metal-containing films are (22) Filed: Apr. 2, 2004 particularly useful in the manufacture of electronic devices. US 2004/O194703 A1 Oct. 7, 2004 ORGANOMETALLIC COMPOUNDS Sition. These precursors are difficult to handle and have high Vapor preSSures. For example, germane decomposes Vio BACKGROUND OF THE INVENTION lently at 280 C., which is below the temperature used to grow germanium films. Accordingly, processes employing 0001. The present invention relates generally to the field either germane or Silane require extensive Safety procedures of organometallic compounds. In particular, the present and equipment. Germane typically requires film growth invention relates to the certain organometallic compounds temperatures of approximately 500 C. -
Structural and Physical Investigations of Novel Germanium Compounds: Aryloxides, Nanomaterials, and Photolysis of Oligogermanes
STRUCTURAL AND PHYSICAL INVESTIGATIONS OF NOVEL GERMANIUM COMPOUNDS: ARYLOXIDES, NANOMATERIALS, AND PHOTOLYSIS OF OLIGOGERMANES By AARON C. SCHRICK Bachelor of Science in Chemistry Midwestern State University Wichita Falls, Texas 2009 Submitted to the Faculty of the Graduate College of the Oklahoma State University in partial fulfillment of the requirements for the Degree of DOCTOR OF PHILOSOPHY May, 2014 STRUCTURAL AND PHYSICAL INVESTIGATIONS OF NOVEL GERMANIUM COMPOUNDS: ARYLOXIDES, NANOMATERIALS, AND PHOTOLYSIS OF OLIGOGERMANES Dissertation Approved: Dr. Charles S. Weinert Dissertation Adviser Dr. Allen Apblett Dr. Nicholas Materer Dr. Richard A. Bunce Dr. John Veenstra ii Name: AARON C. SCHRICK Date of Degree: MAY, 2014 Title of Study: STRUCTURAL AND PHYSICAL INVESTIGATIONS OF NOVEL GERMANIUM COMPOUNDS: ARYLOXIDES, NANOMATERIALS, AND PHOTOLYSIS OF OLIGOGERMANES Major Field: CHEMISTRY Abstract: The work described in this dissertation will explore the synthesis and characterization of novel germanium containing compounds in order to gain a better understanding of the organometallic chemistry of germanium. These compounds include germanium bisamides, aryloxogermylenes, polyfunctional aryloxides such as calix[n]arenes and binaphthoxogermanium compounds, and oligogermanes containing up to four germanium atoms. We have found that the germanium bisamides can be trapped using the germylene trapping agent benzil and we have fully characterized those products. The germanium bisamides can also be used as starting materials to synthesize germanium aryloxides via protonolysis of a phenol that contains one or more phenolic groups. Using this method we have prepared the t germanium(IV) aryloxides [Ge(OC6H3Ph2-2,6)2(R)(I)] (R = Bu or Me) where the R = Me derivative was then converted to the triaryloxo species [Ge(OC6H3Ph2-2,6)3(Me)] upon reaction of the iodine containing compound with an extra equivalent of 2,6-diphenylphenol. -
Durham E-Theses
Durham E-Theses Chemical and mass spectrometric studies on organogermanes Carrick, A. How to cite: Carrick, A. (1967) Chemical and mass spectrometric studies on organogermanes, Durham theses, Durham University. Available at Durham E-Theses Online: http://etheses.dur.ac.uk/9048/ Use policy The full-text may be used and/or reproduced, and given to third parties in any format or medium, without prior permission or charge, for personal research or study, educational, or not-for-prot purposes provided that: • a full bibliographic reference is made to the original source • a link is made to the metadata record in Durham E-Theses • the full-text is not changed in any way The full-text must not be sold in any format or medium without the formal permission of the copyright holders. Please consult the full Durham E-Theses policy for further details. Academic Support Oce, Durham University, University Oce, Old Elvet, Durham DH1 3HP e-mail: [email protected] Tel: +44 0191 334 6107 http://etheses.dur.ac.uk CHEMICAL and MASS SPECTROMETRIC STUDIES on ORGANOGERMANES A. CARRICK CHEMICAL AND MASS SPECTRQMETRIC STUDIES ON ORGANDGERMANES by A. CARRICK, B.Sc. Hatfield College A Thesis in candidature for the Degree of Doctor of Philosophy in the University of Durham, July,1967. for Patricia Plato The work described was carried out in the University of Durham between September 1964 and June 1967. It has not been submitted for any other degree and is the original work of the author except where acknowledged by reference. A portion of this work has been the subject of two publications with F. -
Solid-State Nuclear Magnetic Resonance Spectroscopy of Unreceptive Quadrupolar Nuclei in Inorganic Materials
Western University Scholarship@Western Electronic Thesis and Dissertation Repository 4-23-2012 12:00 AM Solid-State Nuclear Magnetic Resonance Spectroscopy of Unreceptive Quadrupolar Nuclei in Inorganic Materials Andre Sutrisno The University of Western Ontario Supervisor Dr. Yining Huang The University of Western Ontario Graduate Program in Chemistry A thesis submitted in partial fulfillment of the equirr ements for the degree in Doctor of Philosophy © Andre Sutrisno 2012 Follow this and additional works at: https://ir.lib.uwo.ca/etd Part of the Inorganic Chemistry Commons, Materials Chemistry Commons, Materials Science and Engineering Commons, and the Physical Chemistry Commons Recommended Citation Sutrisno, Andre, "Solid-State Nuclear Magnetic Resonance Spectroscopy of Unreceptive Quadrupolar Nuclei in Inorganic Materials" (2012). Electronic Thesis and Dissertation Repository. 460. https://ir.lib.uwo.ca/etd/460 This Dissertation/Thesis is brought to you for free and open access by Scholarship@Western. It has been accepted for inclusion in Electronic Thesis and Dissertation Repository by an authorized administrator of Scholarship@Western. For more information, please contact [email protected]. Solid-State Nuclear Magnetic Resonance Spectroscopy of Unreceptive Quadrupolar Nuclei in Inorganic Materials (Spine Title: Solid-State NMR Studies of Unreceptive Quadrupolar Nuclei) (Thesis format: Integrated-Article) By Andre Sutrisno Graduate Program in Chemistry A thesis submitted in partial fulfillment of the requirements for the degree of Doctor of Philosophy The School of Graduate and Postdoctoral Studies The University of Western Ontario London, Ontario, Canada © Andre Sutrisno 2012 ii THE UNIVERSITY OF WESTERN ONTARIO School of Graduate and Postdoctoral Studies CERTIFICATE OF EXAMINATION Supervisor Examiners _________________________________ ______________________________ Dr. -
New Polyether Complexes of Germanium(II) and Tin(II): Synthesis, Structural Characterization and Reactivity
University of Windsor Scholarship at UWindsor Electronic Theses and Dissertations Theses, Dissertations, and Major Papers 4-30-2018 New Polyether Complexes of Germanium(II) and Tin(II): Synthesis, Structural Characterization and Reactivity Alina Maria Secara University of Windsor Follow this and additional works at: https://scholar.uwindsor.ca/etd Recommended Citation Secara, Alina Maria, "New Polyether Complexes of Germanium(II) and Tin(II): Synthesis, Structural Characterization and Reactivity" (2018). Electronic Theses and Dissertations. 7449. https://scholar.uwindsor.ca/etd/7449 This online database contains the full-text of PhD dissertations and Masters’ theses of University of Windsor students from 1954 forward. These documents are made available for personal study and research purposes only, in accordance with the Canadian Copyright Act and the Creative Commons license—CC BY-NC-ND (Attribution, Non-Commercial, No Derivative Works). Under this license, works must always be attributed to the copyright holder (original author), cannot be used for any commercial purposes, and may not be altered. Any other use would require the permission of the copyright holder. Students may inquire about withdrawing their dissertation and/or thesis from this database. For additional inquiries, please contact the repository administrator via email ([email protected]) or by telephone at 519-253-3000ext. 3208. New Polyether Complexes of Germanium(II) and Tin(II): Synthesis, Structural Characterization and Reactivity By Alina Maria Secara A Thesis Submitted to the Faculty of Graduate Studies through the Department of Chemistry and Biochemistry in Partial Fulfillment of the Requirements for the Degree of Master of Science at the University of Windsor Windsor, Ontario, Canada 2018 © 2018 Alina M. -
Coordination Compounds of Germanium(IV) Formed with Soft and Hard Donor Atoms : a Look Into the Past and Present Work
Coordination Compounds of Germanium(IV) Formed with Soft and Hard Donor Atoms : A Look into the Past and Present Work R.V. Singh'*, Pratibha Gupta1, Pratibha Chaudhary' and C.N. Deshmukh2 'Department of Chemistry, University of Rajasthan, Jaipur - 302 004, India E-mail: kudiwal(a>dataii\fosys.net; Fax : +91-141-2708621 Department of Chemistry, Vidyabharti Mahavidyalaya, Amravati - 444 602. ABSTRACT An account of approximately hundred germanium and organogermanium derivatives have been included in this review. The unimolar and bimolar substitution products have been characterized by elemental analyses, conductance measurements, molecular weight determinations and spectral studies, viz., IR, 'H NMR, 13C NMR, U.V. and mass spectra. Thermal stability has been explained on the basis of TGA data. From the analyses of these studies the donor sites of the ligands are located and geometries of the donor environment around the Ge(IV) acceptor centre have been proposed. Based on these studies, trigonal bipyramidal and octahedral geometries have been proposed for the resulting derivatives. The resulting coloured solids are soluble in most of the common organic solvents. These were found to be monomers, as evidenced by their molecular weight determinations. The low values of molar conductance of the resulting metal complexes in anhydrous DMF show them to be non-electrolytes in nature. The spectral data suggested that the ligands act in monofunctional bidentate, bifunctional tridentate and Afunctional tetradentate manners, coordinating through the hard nitrogen and soft sulfur atoms. All such important aspects, including the biological properties about the germanium complexes synthesized in our laboratory as well as other laboratories, are discussed in brief. -
Studies Towards the Synthesis of a Heterobimetallic Zirconium Germanium Complex from Imidozirconocenes, Germanimines and Germylenes
Studies towards the Synthesis of a Heterobimetallic Zirconium Germanium Complex from Imidozirconocenes, Germanimines and Germylenes By Peter Chapple A thesis Submitted to Victoria University of Wellington In partial fulfilment of the requirements for the degree of Masters of Science In Chemistry Victoria University of Wellington 2018 Abstract Early-late transition metal heterobimetallic complexes with direct metal to metal interactions are desirable synthetic targets due to the complementary reactivity of the two different metals present in these compounds. The electron-rich late transition metal (often Rh, Ir, Fe, or Mo), and electron-poor early transition metal create an ideal environment for heterolytic bond cleavage in what is often termed ‘cooperative reactivity’. This project aimed to synthesise a zirconium-germanium heterobimetallic complex based on a known heterobimetallic ligand scaffold; 1. The synthesis of the desired heterobimetallic 1 was attempted using two different synthetic approaches. The first involved the investigating the reactivity between an unsaturated zirconium nitrogen bond (an imidozirconocene) and a germanium(II) source with a lone pair of electrons (known as a germylene). The second approach investigated the reactivity between an unsaturated germanium nitrogen bond (a germanimine) and a zirconium(II) source. In order to have the highest chance of success, a wide range of germanium and zirconium complexes were synthesised. TMS TMS Mes) The novel germylenes include [Ge(NAPH )] (NAPH = [1,8-((CH3)3Si)N)2C10H6]) and [Ge(BIAN ] Mes (BIAN = [((2,4,6-Me(C6H2)N)2)C12H6)]). These proved to be unreactive towards the imidozirconium t species [Cp2Zr(NAr*)(THF)] and [Cp2Zr(NDipp)(THF)] (Ar* = (2,6-(C6H5)2CH)-4-( Bu)C6H2), Dipp = (2,6- ((CH3)2CH)C6H3)) as well as other amidozirconocenes.