(12) United States Patent (10) Patent No.: US 8.258,180 B2 Nip (45) Date of Patent: Sep
Total Page:16
File Type:pdf, Size:1020Kb
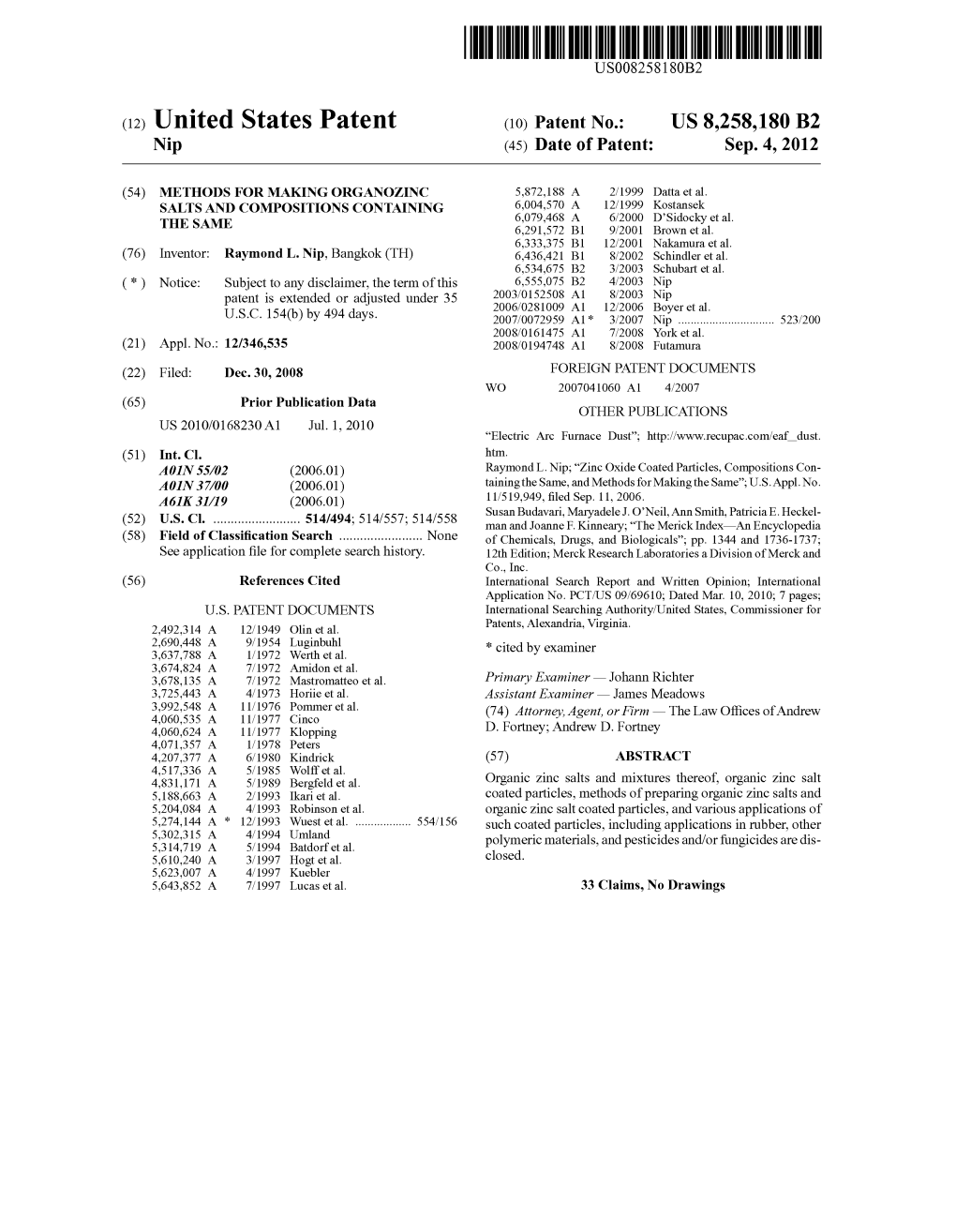
Load more
Recommended publications
-
Disability Classification System
CLASSIFICATION SYSTEM FOR STUDENTS WITH A DISABILITY Track & Field (NB: also used for Cross Country where applicable) Current Previous Definition Classification Classification Deaf (Track & Field Events) T/F 01 HI 55db loss on the average at 500, 1000 and 2000Hz in the better Equivalent to Au2 ear Visually Impaired T/F 11 B1 From no light perception at all in either eye, up to and including the ability to perceive light; inability to recognise objects or contours in any direction and at any distance. T/F 12 B2 Ability to recognise objects up to a distance of 2 metres ie below 2/60 and/or visual field of less than five (5) degrees. T/F13 B3 Can recognise contours between 2 and 6 metres away ie 2/60- 6/60 and visual field of more than five (5) degrees and less than twenty (20) degrees. Intellectually Disabled T/F 20 ID Intellectually disabled. The athlete’s intellectual functioning is 75 or below. Limitations in two or more of the following adaptive skill areas; communication, self-care; home living, social skills, community use, self direction, health and safety, functional academics, leisure and work. They must have acquired their condition before age 18. Cerebral Palsy C2 Upper Severe to moderate quadriplegia. Upper extremity events are Wheelchair performed by pushing the wheelchair with one or two arms and the wheelchair propulsion is restricted due to poor control. Upper extremity athletes have limited control of movements, but are able to produce some semblance of throwing motion. T/F 33 C3 Wheelchair Moderate quadriplegia. Fair functional strength and moderate problems in upper extremities and torso. -
Library of Congress Classification
R MEDICINE (GENERAL) R Medicine (General) Periodicals. Societies. Serials 5 International periodicals and serials 10 Medical societies Including aims, scope, utility, etc. International societies 10.5.A3 General works 10.5.A5-Z Individual societies America English United States. Canada 11 Periodicals. Serials 15 Societies British West Indies. Belize. Guyana 18 Periodicals. Serials 20 Societies Spanish and Portuguese Latin America 21 Periodicals. Serials 25 Societies 27.A-Z Other, A-Z 27.F7 French Europe English 31 Periodicals. Serials 35 Societies Dutch 37 Periodicals. Serials 39 Societies French 41 Periodicals. Serials 45 Societies German 51 Periodicals. Serials 55 Societies Italian 61 Periodicals. Serials 65 Societies Spanish and Portuguese 71 Periodicals. Serials 75 Societies Scandinavian 81 Periodicals. Serials 85 Societies Slavic 91 Periodicals. Serials 95 Societies 96.A-Z Other European languages, A-Z 96.H8 Hungarian Asia 97 English 97.5.A-Z Other European languages, A-Z 97.7.A-Z Other languages, A-Z Africa 98 English 98.5.A-Z Other European languages, A-Z 98.7.A-Z Other languages, A-Z 1 R MEDICINE (GENERAL) R Periodicals. Societies. Serials -- Continued Australasia and Pacific islands 99 English 99.5.A-Z Other European languages, A-Z 99.7.A-Z Other languages, A-Z Indexes see Z6658+ (101) Yearbooks see R5+ 104 Calendars. Almanacs Cf. AY81.M4 American popular medical almanacs 106 Congresses 108 Medical laboratories, institutes, etc. Class here papers and proceedings For works about these organizations see R860+ Collected works (nonserial) Cf. R126+ Ancient Greek and Latin works 111 Several authors 114 Individual authors Communication in medicine Cf. -
Reframing Sport Contexts: Labeling, Identities, and Social Justice
Reframing Sport Contexts: Labeling, Identities, and Social Justice Dr. Ted Fay and Eli Wolff Sport in Society Disability in Sport Initiative Northeastern University Critical Context • Marginalization (Current Status Quo) vs. • Legitimatization (New Inclusive Paradigm) Critical Context Naturalism vs. Trans-Humanism (Wolbring, G. (2009) How Do We Handle Our Differences related to Labeling Language and Cultural Identities? • Stereotyping? • Prejudice? • Discrimination? (Carr-Ruffino, 2003, p. 1) Ten Major Cultural Differences 1) Source of Control 2) Collectivism or Individualism 3) Homogeneous or Heterogeneous 4) Feminine or Masculine 5) Rank Status 6) Risk orientation 7) Time use 8) Space use 9) Communication Style 10) Economic System (Carr – Ruffino, 2003, p.27) Rationale for Inclusion • Divisioning by classification relative to “fair play” and equity principles • Sport model rather than “ism” segregated model (e.g., by race, gender, disability, socio-economic class, sexual orientation, look (body image), sect (religion), age) • Legitimacy • Human rights and equality Social Dynamics of Inequality Reinforce and reproduce Social Institutions Ideology Political (Patriarchy) Economic Educational Perpetuates Religious Prejudice & Are institutionalized by Discrimination Cultural Practices (ISM) Sport Music Art (Sage, 1998) Five Interlinking Conceptual Frameworks • Critical Change Factors Model (CCFM) • Organizational Continuum in Sport Governance (OCSG) • Criteria for Inclusion in Sport Organizations (CISO) • Individual Multiple Identity Sport Classifications Index (IMISCI) • Sport Opportunity Spectrum (SOS) Critical Change Factors Model (CCFM) F1) Change/occurrence of major societal event (s) affecting public opinion toward ID group. F2) Change in laws, government and court action in changing public policies toward ID group. F3) Change in level of influence of high profile ID group role models on public opinion. -
Yerkes Observatory Received August 20, I960
8IB .3 .5. THE SPECTRUM OF RHO CASSIOPEIAE. I* Wallace R. Beardsley! Yerkes Observatory 196lApJS. Received August 20, I960; revised September 16, 1960 ABSTRACT This paper constitutes an analysis of an extensive series of spectrograms of p Cassiopeiae taken by several observers principally with the 82-inch telescope of the McDonald Observatory both during and after the deep minimum in light of 1946. Identification measures by Tai and Thackeray before the minimum have been combined with detailed measures by the writer during and after the minimum, to form a catalogue of the spectral lines as seen on plates of medium dispersion. A group of 23 selected zero-volt lines were analyzed for radial-velocity and intensity changes. Although no change in radial velocity was detected, marked changes in intensity did occur. The hydrogen lines in p Cas in 1936 were found to be as strong as, or even stronger than, in ô CMa. Weakness of the hydrogen lines as early as 1939 may be evidence of spectral change leading up to the 1946 minimum. Evidence is cited for an over- lying shell in which the TiO is formed. Unlike RV Tauri stars, the spectral type from line ratios at minimum light was also M3. The spectral type after minimum varied progressively from K5p to G5p, even reaching F8p during the “flare-up” of 1950. The behavior of emission in the hydrogen and Ca I X 4227 lines is discussed, as well as the presence of a sharp absorption core in Ca I. This core also was probably due to an overlying shell. -
Field Indicators of Hydric Soils
United States Department of Field Indicators of Agriculture Natural Resources Hydric Soils in the Conservation Service United States In cooperation with A Guide for Identifying and Delineating the National Technical Committee for Hydric Soils Hydric Soils, Version 8.2, 2018 Field Indicators of Hydric Soils in the United States A Guide for Identifying and Delineating Hydric Soils Version 8.2, 2018 (Including revisions to versions 8.0 and 8.1) United States Department of Agriculture, Natural Resources Conservation Service, in cooperation with the National Technical Committee for Hydric Soils Edited by L.M. Vasilas, Soil Scientist, NRCS, Washington, DC; G.W. Hurt, Soil Scientist, University of Florida, Gainesville, FL; and J.F. Berkowitz, Soil Scientist, USACE, Vicksburg, MS ii In accordance with Federal civil rights law and U.S. Department of Agriculture (USDA) civil rights regulations and policies, the USDA, its Agencies, offices, and employees, and institutions participating in or administering USDA programs are prohibited from discriminating based on race, color, national origin, religion, sex, gender identity (including gender expression), sexual orientation, disability, age, marital status, family/parental status, income derived from a public assistance program, political beliefs, or reprisal or retaliation for prior civil rights activity, in any program or activity conducted or funded by USDA (not all bases apply to all programs). Remedies and complaint filing deadlines vary by program or incident. Persons with disabilities who require alternative means of communication for program information (e.g., Braille, large print, audiotape, American Sign Language, etc.) should contact the responsible Agency or USDA’s TARGET Center at (202) 720-2600 (voice and TTY) or contact USDA through the Federal Relay Service at (800) 877-8339. -
Pocket Filters Made of Non-Woven Synthetic Fibres – Type
PFS 6.2 – X XPFStestregistrierung Pocket filters made of non- woven synthetic fibres Type PFS Prefilters or final filters in ventilation systems Pocket filters for the separation of fine dust Filter classes M5, M6, F7 Performance data tested to EN 779 AIR FILTERS CLASS M5-F9 Eurovent certification for fine dust filters Meets the hygiene requirements of VDI 6022 Non-woven synthetic fibres, welded 6 Eurovent certification Enlarged filter area due to filter pockets Low initial differential pressure and high dust holding capacity Variable number of pockets and pocket depth H Quick installation and filter changing times due to easy, safe handling ISC GE N TE IE S T Fitting into standard cell frames for filter walls (type SIF) or into universal G E Y T H casings (type UCA) for duct installation Optional equipment and accessories V 2 DI 602 Front frame made of plastic or galvanised sheet steel Tested to VDI 6022 09/2013 – DE/en K7 – 6.2 – 1 Pocket filters made of non-woven synthetic fibres General information PFS Type Page PFS General information 6.2 – 2 Order code 6.2 – 3 Dimensions and weight 6.2 – 4 Specification text 6.2 – 5 Basic information and nomenclature 10.1 – 1 Description Application Materials and surfaces – Pocket filter made of non-woven synthetic – Filter media made of non-woven synthetic fibres type PFS for the separation of fine dust fibres – Fine dust filter: Prefilter or final filter in – Frame made of plastic or galvanised sheet ventilation systems steel Classification Standards and guidelines – Eurovent certification for -
Pocket Filter Rigid RS
Pocket Filter Rigid RS Rigid Pocket Filter for Automotive Application G Silicon free filter G Progressive density synthetic media G Self-supporting construction G High dust holding capacity G Classifications F5, F6, F7 and F8 G Optionally available with Plastic Header Rigid Pocket Filter Type RS The Type RS rigid pocket filter is Standard Type Filter area m2 Rated air flow designed for use in automotive air dimensions (mm) Rigid RS 650 mm m3/h handling units. The filter features a high quality thermally bonded synthetic F5 F5 F5 F5 media with a strong galvanized steel 592x592x650 45/6 5 3400 header. The media has a progressive 490x592x650 45/5 4,2 2830 density construction which allows dust 287x592x650 45/3 2,5 1700 particles to penetrate deeper into the 287x287x650 45/3H 1,25 850 media before they are trapped. As the F6 F6 back of the media loads, particles are F6 F6 592x592x660 65/8 6,9 3400 caught progressively closer to the surface. 490x592x660 65/6 5,2 2830 This design eliminates faceloading, 287x592x660 65/4 3,5 1700 increases dust holding capacity and 287x287x660 65/41/ 1,8 850 ensures cleaner air. The materials used to 4 make the filter are silicon free. Available F7 F7 F7 F7 in classifications F5 thru F8 in 592x592x660 85/8 6,9 3400 accordance with EN779. 490x592x660 85/6 5,2 2830 287x592x660 85/4 3,5 1700 To ensure an optimum airflow through 287x287x660 85/4 1,8 850 the filter and minimium media resistance, each pocket is separated from F8 F8 F8 F8 the other by three diamond shaped 592x592x660 95/8 6,9 3400 pocket separators. -
RULES 2004 Final Amended
INTERNATIONAL PARALYMPIC COMMITTEE ATHLETICS SECTION COMBINED RULES 2004 PREAMBLE For competition at Paralympics and I.P.C. World Championships, this book shall be used, along with the current I.A.A.F. Handbook. It contains all the rules, which govern an I.P.C. Athletics competition, written in a way, which is compatible with the rules of the governing body for athletics, the International Association of Athletics Federations (I.A.A.F.). In this way, officials, coaches and athletes may find rules to cover any event in a single document, rather than having to refer to separate books for each group. The rules must be read in conjunction with the I.A.A.F. rules, contained in the Handbook of that Association. For the period including the 2004 Athens Paralympics, the version of the I.A.A.F. Handbook to which this book refers is the 2004-2005 edition. The rules concerned are the Technical Rules of Competition as described herein, and additional rules as shown. The reference to the I.A.A.F. Handbook does not confer any responsibility onto the I.A.A.F. for the I.P.C. Rules. Each of the I.O.S.D.’s has its own cycle of rule changes, and this volume does not intend to change any rules so decided. It is quite simply a means of simplifying the task of reading the rules for those concerned. NOTES This Rule Book will remain in force until the publication of the next I.A.A.F. Handbook, at which time a new edition will be published to take account of any new I.A.A.F. -
The ICD-10 Classification of Mental and Behavioural Disorders Diagnostic Criteria for Research
The ICD-10 Classification of Mental and Behavioural Disorders Diagnostic criteria for research World Health Organization Geneva The World Health Organization is a specialized agency of the United Nations with primary responsibility for international health matters and public health. Through this organization, which was created in 1948, the health professions of some 180 countries exchange their knowledge and experience with the aim of making possible the attainment by all citizens of the world by the year 2000 of a level of health that will permit them to lead a socially and economically productive life. By means of direct technical cooperation with its Member States, and by stimulating such cooperation among them, WHO promotes the development of comprehensive health services, the prevention and control of diseases, the improvement of environmental conditions, the development of human resources for health, the coordination and development of biomedical and health services research, and the planning and implementation of health programmes. These broad fields of endeavour encompass a wide variety of activities, such as developing systems of primary health care that reach the whole population of Member countries; promoting the health of mothers and children; combating malnutrition; controlling malaria and other communicable diseases including tuberculosis and leprosy; coordinating the global strategy for the prevention and control of AIDS; having achieved the eradication of smallpox, promoting mass immunization against a number of other -
Hexagonal Logic of the Field F8 As a Boolean Logic with Three Involutive Modalities
Preliminary version of a paper published in: A. Koslow and A. Buchbaum (eds.) The Road to Universal Logic. Festschrift for 50th Birthday of Jean-Yves Béziau, Vol. I, Series: Studies in Universal Logic, 2015, XII, 191-220. Hexagonal Logic of the Field F8 as a Boolean Logic with Three Involutive Modalities René Guitart In friendly homage to Jean-Yves Béziau, on the occasion of his 50th birthday Abstract. We consider the Post-Malcev full iterative algebra P8 of all functions of all finite arities on a set 8 with 8 elements, e.g. on the Galois field F8. We prove that P8 is generated by the logical operations of a 3 canonical boolean structure on F8 = F2, plus three involutive F2-linear transvections A; B; C, related by circular relations and generating the group GL3(F2). It is known that GL3(F2) = PSL2(F7) = G168 is the unique simple group of order 168, which is the group of automorphisms of the Fano plane. Also we obtain that P8 is generated by its boolean logic plus the three cross product operations R×, S×, I×. Especially our result could be understood as a hexagonal logic, a natural setting to study the logic of functions on a hexagon; precisely it is a hexagonal presentation of the logic of functions on a cube with a selected diagonal. Mathematics Subject Classification (2010). 00A06, 03B45, 03B50, 03G05, 06Exx, 06E25, 06E30, 11Txx. Keywords. Hexagon of opposition, borromean object, specular logic, boolean algebra, modality, many-valued logics, finite fields, Fano plane. 1. Introduction: How and why to generate functions on 8 ? Our concrete result is formulated in elementary terms in Theorem 8.1. -
Functional Connectivity and Classification of Actual and Imaginary Motor Movement
International Journal of Engineering and Advanced Technology (IJEAT) ISSN: 2249 – 8958, Volume-9 Issue-2, December, 2019 Functional Connectivity and Classification of Actual and Imaginary Motor Movement Nilima Salankar, Anjali Mishra, Pratikshya Mishra Abstract— Imaginary Motor movement is an utmost In this study author have studied the different patterns of important for the designing of brain computer interface to assist connectivity between the actual ,imaginary motor movement the individual with physically disability. Brain signals associated and no motor movement with eyes open and eyes closed, it with actual motor movement include the signal for muscle would help to design brain computer interface to help to activity whereas in case of imaginary motor movement actual survive the physically challenged people. In this study muscle movement is not present .Authors have investigated the similarity/dissimilarity between the eeg signals generated in both authors has identified the most activated portion of the brain the cases along with the baseline activity. To instruct the brain in the form of lobes frontal, temporal, parietal and occipital. computer interface signals generated by electrodes of EEG must Electroencephalography is a non-invasive technique to resemble with actual motor movement. Selection of electrodes record brain signals; various signal processing techniques placement plays an important role for this purpose. In this study can give insight into the mental state, emotional condition of major four regions of the brain has been covered frontal, the person and motion intents. In literature, experiments for temporal, parietal and occipital region of the scalp and features recognition or detection of imaginary motion are available are extracted from the signals are standard deviations, kurtosis, with different accuracy and relevance. -
Deep Learning for EEG-Based Preference Classification In
applied sciences Article Deep Learning for EEG-Based Preference Classification in Neuromarketing Mashael Aldayel 1,2,*,† , Mourad Ykhlef 1,† and Abeer Al-Nafjan 3,† 1 Information System Department, College of Computer and Information Sciences, King Saud University, Riyadh 11543, Saudi Arabia; [email protected] 2 Information Technology Department, College of Computer and Information Sciences, King Saud University, Riyadh 11543, Saudi Arabia 3 Computer Science Department, College of Computer and Information Sciences, Imam Muhammad bin Saud University, Riyadh 11432, Saudi Arabia; [email protected] * Correspondence: [email protected] † Current address: Riyadh 11432, Saudi Arabia. Received: 14 January 2020; Accepted: 19 February 2020; Published: 24 February 2020 Featured Application: This article presents an application of deep learning in preference detection performed using EEG-based BCI. Abstract: The traditional marketing methodologies (e.g., television commercials and newspaper advertisements) may be unsuccessful at selling products because they do not robustly stimulate the consumers to purchase a particular product. Such conventional marketing methods attempt to determine the attitude of the consumers toward a product, which may not represent the real behavior at the point of purchase. It is likely that the marketers misunderstand the consumer behavior because the predicted attitude does not always reflect the real purchasing behaviors of the consumers. This research study was aimed at bridging the gap between traditional market research, which relies on explicit consumer responses, and neuromarketing research, which reflects the implicit consumer responses. The EEG-based preference recognition in neuromarketing was extensively reviewed. Another gap in neuromarketing research is the lack of extensive data-mining approaches for the prediction and classification of the consumer preferences.