Hopewell Village
Total Page:16
File Type:pdf, Size:1020Kb
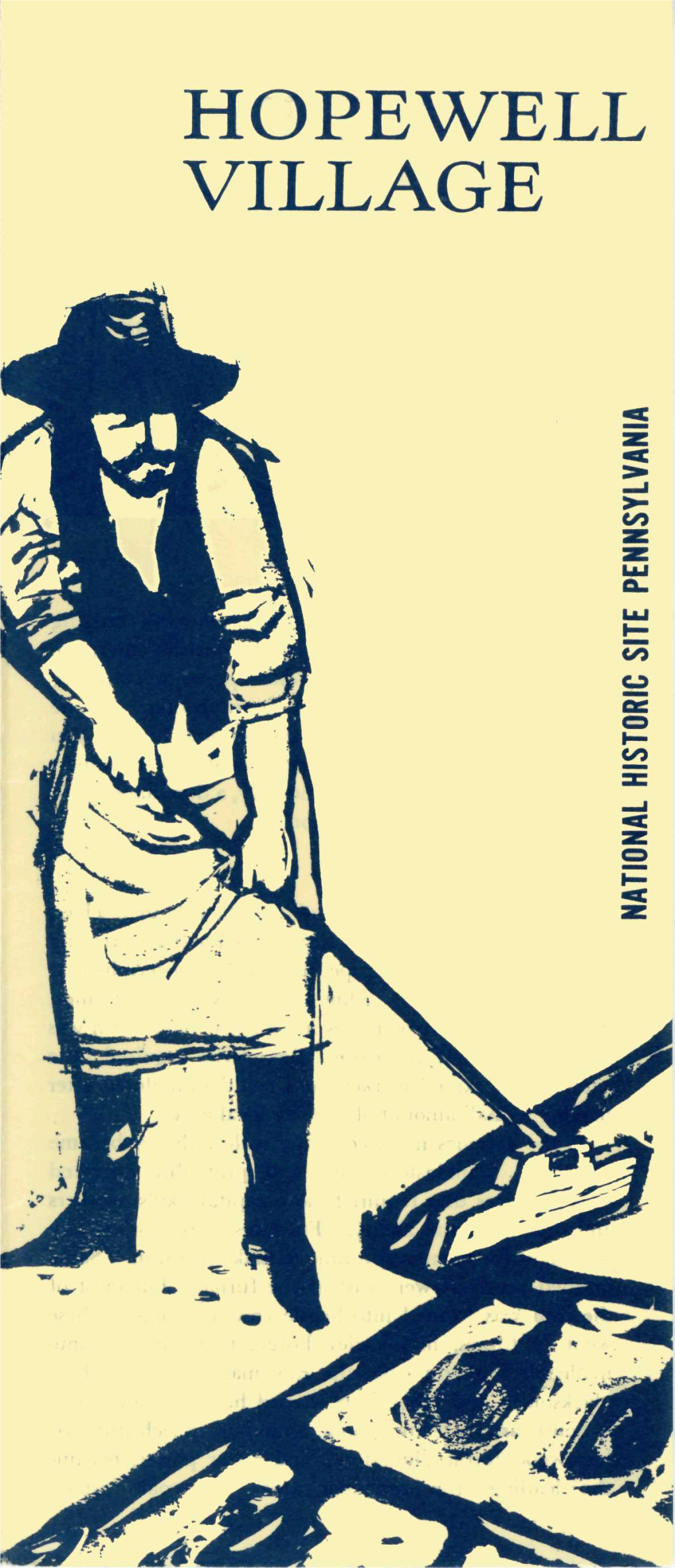
Load more
Recommended publications
-
National Register of Historic Places Multiple Property
NFS Form 10-900-b 0MB No. 1024-0018 (Jan. 1987) United States Department of the Interior National Park Service National Register of Historic Places Multipler Propertyr ' Documentation Form NATIONAL This form is for use in documenting multiple property groups relating to one or several historic contexts. See instructions in Guidelines for Completing National Register Forms (National Register Bulletin 16). Complete each item by marking "x" in the appropriate box or by entering the requested information. For additional space use continuation sheets (Form 10-900-a). Type all entries. A. Name of Multiple Property Listing ____Iron and Steel Resources of Pennsylvania, 1716-1945_______________ B. Associated Historic Contexts_____________________________ ~ ___Pennsylvania Iron and Steel Industry. 1716-1945_________________ C. Geographical Data Commonwealth of Pennsylvania continuation sheet D. Certification As the designated authority under the National Historic Preservation Act of 1966, as amended, J hereby certify that this documentation form meets the National Register documentation standards and sets forth requirements for the listing of related properties consistent with the National Register criteria. This submission meets the procedural and professional requiremerytS\set forth iri36JCFR PafrfsBOfcyid the Secretary of the Interior's Standards for Planning and Evaluation. Signature of certifying official Date / Brent D. Glass Pennsylvania Historical & Museum Commission State or Federal agency and bureau I, hereby, certify that this multiple -
Hopewell Village
IRONMAKING IN EARLY AMERICA the Revolutionary armies, is representative of (such as Valley Forge) to be made into the tougher the hundreds of ironmaking communities that and less brittle wrought iron. This was used to Hopewell In the early days of colonial America, iron tools supplied the iron needs of the growing nation. make tools, hardware, and horseshoes. and household items were brought over from Europe by the settlers or imported at a high cost. Until surpassed by more modern methods, cold- HOPEWELL FURNACE Village The colonists, early recognizing the need to manu blast charcoal-burning furnaces, such as that NATIONAL HISTORIC SITE • PENNSYLVANIA facture their own iron, set up a number of iron at Hopewell, supplied all the iron. These furnaces In an age when most businesses were operated by works, notably at Falling Creek, Va., and Saugus, consumed about 1 acre of trees a day for fuel, one or two men in a shop, Hopewell employed at Mass. Operations gradually spread throughout so they had to be located in rural areas close to least 65 men, with some responsible for two or the colonies, and by the end of the 1700's, south a timber supply. more jobs. As the nearest town was many miles eastern Pennsylvania had become the industry's away, the ironmaster built a store to supply his center. Hopewell Village, founded by Mark Bird Since the pig iron produced by these furnaces workers, many of whom lived in company-owned in 1770 in time to supply cannon and shot for had a limited use, much of it was sent to forges homes. -
CO2 Emission Reduction Potential in the Steel Industry by Integration of a Direct Reduction Process Into Existing Steel Mills Ab
Challenges for Petrochemicals and Fuels: Integration of Value Chains and Energy Transition DGMK Conference October 10 – 12, 2018 in Berlin, Germany CO2 Emission Reduction Potential in the Steel Industry by Integration of a Direct Reduction Process into Existing Steel Mills N. Müller, G. Herz, E. Reichelt, M. Jahn Fraunhofer IKTS, Dresden, Germany Abstract In the context of climate change, the reduction of greenhouse gas emissions in all economic sectors is considered to be an important factor in order to meet the demands of a sustainable energy system. The steel industry as one of the large industrial CO2 emitters is currently highly dependent on fossil resources. In order to reduce coke consumption and thereby CO2 emissions while still being able to further utilize existing blast furnaces, the possibility of in- cluding a direct reduction process (DRP) into a fully integrated steel mill was investigated. Therefore, a blast furnace model, derived from literature data and implemented in Aspen Plus, was used to analyze the impact of DRI in the blast furnace process. Furthermore, a state-of-the-art DRP was modeled to investigate the possibility of substituting the reducing agent natural gas with hydrogen. A sensitivity analysis was carried out in order to find the boundary percentage of hydrogen as a reducing agent without penalty to the DRI quality. Lastly, the two modeled process steps were combined to form a route of producing hot met- al. By varying boundary conditions of the DRP while recording the CO2 emissions of the two process steps, the overall potential for the reduction of CO2 emissions was estimated. -
What a Blast Furnace Is and How It Works
VOLUME II SATURDAY, NOVEMBER I, 1902 NUMBER 18 What a Blast Furnace Is and How It Works Popular Article for the Scientifically Uneducated on the Parts of a Furnace and How Pig Iron Is Made. 1 HE following article on the construc- may be accepted as an accurate statement of how tion and operations of blast furnaces pig iron is made. The editor wishes to take this was written especially for Camp and opportunity to thank these gentlemen for their Plant Mr. A of the by Harry Deuel, painstaking and careful work. Engineering Department of the Min- have articles nequa Works. It was afterwards Arrangements been madefor other carefully revised, and approved in all in "popular," though accurate, form, descriptive details by Mr R. H. Lee, superin- of other departments of the coal, coke, iron and tendent of the Blast Furnace Department, and steel industry. " Boiler House. Engine House. Furnace Stack. Stoves. Blast furnace B. Blast Furnace "A," Minnequa Steel Works, Pueblo. This view well illustrates the different external parts of "A" Furnace of which, except for minor modifica- tions, "D," "E" and "F" are duplicates Each of these furnaces is 20 feet x 95 feet, is fitted with automatic skip hoists and with the very b st and most modern equipment. This vi-w was taken, however, before the ore. coke and limestone bins, from which the skip is now automatically loaded, were installed. There are four stoves to each furnace. 21 feet in diameter by 106 feet high. Each of the tall draft stacks is 12 feet 6 inches in diameter in the clear, by 210 feet high. -
Using Cooled Mirror Hygrometers to Optimize Cold & Hot Blast Furnace
Application Note Using Cooled Mirror Hygrometers to optimize Cold & Hot Blast Furnace processes Application Background The purpose of a blast furnace is to chemically reduce and physically convert iron oxides into liquid iron. The blast furnace is a huge, steel stack lined with brick. Iron ore, coke and limestone are dumped into the top, and preheated “hot blast” air is blown into the bottom. The raw materials gradually descend to the bottom of the furnace where they become the final products of liquid slag and liquid iron. These liquid products are drained from the furnace at regular intervals. The hot air that was blown into the bottom of the furnace ascends to the top in 6 to 8 seconds after going through numerous chemical reactions. These hot gases exit the top of the blast furnace and proceed through gas cleaning equipment where Cold Blast, Hot blast & Stoves particulate matter is removed from the gas and the gas is cooled. This gas has a considerable energy value so it is burned as a fuel in the "hot blast stoves" which are used to preheat the air entering the blast furnace to become "hot blast". Any of the gas not burned in the stoves is sent to the boiler house and is used to generate steam which turns a turbo blower that generates the compressed air known as "cold blast" that comes to the stoves. Why is Moisture Critical? This process can be optimized by proper control of the flame temperature, which is in turn affected by the moisture content of the blast air. -
Refractory & Engineering
Refractory & Engineering Solutions for Hot Blast Stoves and Blast Furnace Linings Blast Furnace Technologies Refractory & Engineering The Company – The Program Paul Wurth Refractory & Engineering GmbH has been integrated into the Paul Wurth Group in ` Blast furnace linings for extended service life December 2004. This alliance offers, on a turnkey ` Blast furnace cooling systems basis, single source supply and procurement options for complete blast furnace plants. ` Turnkey hot blast stoves with internal or external combustion chamber Originally, Paul Wurth Refractory & Engineering ` Ceramic burners with ultra-low CO emission GmbH has been founded as DME in 1993 through the merger of departments of Didier-Werke AG ` Highly effective stress corrosion protection and Martin & Pagenstecher GmbH. Customers systems benefit from the unsurpassed experience and ` Complete hot blast main systems know-how that both companies have developed in the field of hot blast stove engineering, refractory ` Complete heat recovery systems lining design, and hot metal production. ` Refractory linings for smelting and direct reduction vessels Paul Wurth Refractory & Engineering GmbH is always striving for world class stove and refractory ` Refractory linings for coke dry quenching designs to meet demanding market requirements, ` Refractory linings for pellet plants such as larger production capacity, extended ser- vice life, optimized refractory selection, and high Highly experienced and motivated teams of engineers, energy efficiency. designers and project managers -
Hisarna Smelting Reduction
HISARNA SMELTING REDUCTION A SOLUTION FOR SUSTAINABLE HOT METAL PRODUCTION Jan van der Stel, Koen Meijer, Christiaan Zeilstra, Johan van Boggelen, Tim Peeters and Rod Dry (*) Tata Steel Research & Development, IJmuiden, The Netherlands (*) RIO TINTO Perth, Australia Reducing the carbon footprint of the steel industry, 19-20 April 1 ZaandamAll rights and reserved Petten - Reducing, theThe carbon Netherlands footprint of the steel industry - 19-20 April 2017 – Zaandam and Petten, The Netherlands Content 1. HIsarna development 2. Technology background 3. The HIsarna pilot plant 3.1. Milestones of the test campaigns 4. Forward program 4.1. Further experimental work in pilot plant 4.2. Industrial scale demonstration plant 5. Conclusions 6. Challenges 2 All rights reserved - Reducing the carbon footprint of the steel industry - 19-20 April 2017 – Zaandam and Petten, The Netherlands 1. HIsarna development • In 2004 several European steelmakers proactively started the ULCOS project with the objective to achieve 50 % reduction of the CO 2 emissions of steelmaking • HIsarna is one of the four process development that originate from the ULCOS project. • Since 2007 Tata Steel, Rio Tinto and ULCOS have been active developing this coal-based smelting reduction process. • To date over 80 mln Euro has been invested in this new technology. • The HIsarna process offers a combination of environmental and economical benefits. 3 All rights reserved - Reducing the carbon footprint of the steel industry - 19-20 April 2017 – Zaandam and Petten, The Netherlands 1.1 Comparison BF route - HIsarna Blast Furnace Iron ore Hot metal Coal Coking/Agglomeration Ironmaking HIsarna Iron ore Hot metal Direct use of fine ores and coal Coal (no agglomeration and coking) Ironmaking 4 All rights reserved - Reducing the carbon footprint of the steel industry - 19-20 April 2017 – Zaandam and Petten, The Netherlands 1.2. -
Blast Furnace Stove Dome and Hot Blast Main
BLAST FURNACE STOVE DOME AND HOT BLAST MAIN The quality and composition of iron produced in the blast furnace is directly related to the hearth temperature. This, in turn, is dependent on the temperature of the hot blast delivered from the blast furnace stoves. To maximise the efficiency of the stoves, they are operated at high temperatures, close to the safe working limit of the refractories. This makes it critical to carefully monitor the stove temperature. BLAST FURNACES AND STOVES Blast furnaces heat iron ore to a period of accumulation, flow is produce the iron required as a reversed, and the hot stove is used raw material for steel-making. For to preheat the incoming air. efficient operation, the air is heated Stoves are alternated, storing heat before being sent into the furnace. and dissipating heat on a regular This ‘hot blast’ technique – flow reversal plan. Many blast preheating air blown into the furnaces are serviced by three or blast furnace – dates back to the more stoves, so that while two are Industrial Revolution, and was being heated, the air blast can pass developed to permit higher through the regenerative chamber furnace temperatures, increasing of the third stove on its way to the the furnace capacity. furnace. Preheating the air intensifies and Accurate monitoring of the stove accelerates the burning of the temperature supports efficient coke. A blast furnace fed with operation – higher temperatures air preheated to between 900- are more efficient and, by reducing 1250oC (1652-2282oF) can generate coke consumption, are more cost- smelting temperatures of about effective. -
Inquiry Into the Development of Northern Australia Submission 6
Appendix 10 TATA STEEL CO NSULTING Provision of Technical A ssistance To East W est Line Parks Pty Ltd Bris ane! " L# ! A $stralia TSC Pro%ect Code & PIB' Pro%ect Iron Boo( eran) & Prefeasi ility *e+ort Tata Steel Consulting P.O. Box 30 Stephenson Street N ew port South W ales N P19 0RB U nite !ing o" #e$ruar% &01& CO N TEN TS 1. EXECUTIVE SUMMARY 4 2. OVERVIEW OF PROJECT IRON BOOMERANG 7 3. PURPOSE OF THIS REPORT 8 4. LIST OF ASSUMPTIONS 9 4.1 TECHNICAL & OPERATIONAL ASSUMPTIONS 9 4.1.1 Steel Complex Output 9 4.1.2 Indicative Iron Ore Chemistry 9 4.1.3 Indicative Coal Chemistry 9 4.1.4 Iron Making Production Philosophy 10 4.1.5 Indicative Iron Chemistry 11 4.1.6 Steel Making Philosophy 11 4.1.7 Indicative Steel Chemistry 12 4.1.8 Indicative product Mix 12 4.2 FINANCIAL ASSUMPTIONS 13 4.2.1 Capital Expenditure and Phasing 13 4.2.2 Capital Charges 15 4.2.3 Recurring Major Capital Expenditure 15 4.2.4 Raw Material Costs 15 4.2.5 Delivery of Slab 15 4.2.6 Inflation 16 4.2.7 Depreciation 16 4.2.8 Estimate Accuracy 16 5. TRENDS IN IRON AND STEELMAKING TECHNOLOGY 17 5.1 OPTIONS FOR IRONMAKING 17 5.1.1 Blast Furnace 17 5.1.2 Rotary Hearth Furnace 19 5.1.3 Rotary Kiln 23 5.1.4 HIsmelt 25 5.1.5 Corex/Midrex 28 5.1.6 Finex 30 5.1.7 Natural Gas Based Zero-Reforming HYL Process 31 5.1.8 Coal Based HYL Process 33 5.1.9 Electric Iron Furnace (EIF) 34 5.1.10 Submerged Arc Furnace (SAF) 36 5.1.11 HIsarna 40 5.1.12 Ausmelt 41 5.2 OPTIONS FOR STEELMAKING 41 5.2.1 Electric Arc Furnace 41 5.2.2 Basic Oxygen Steelmaking (BOS) 43 6. -
3. Classification 4. Owner of Property 5. Location of Legal Description 6
NATIONAL HISTORIC LANDMARK NPS Form 10-900 OMB No. 1024-0018 (3-82) Exp. 10-31-84 United States Department of the interior National Park Semes For NPS use only Of received date entered See instructions in How to Complete National Register Forms Type all entries—complete applicable sections historic CORNWALL IRON FURNACE NATIONAL HISTORIC LANDMARK DISTRICT and or common In irregular pattern along Rexmont Road and Boyd street & number street_________ _ _______ __________________—— no* city, town Cornwall Borough ——vicinity of state Pennsylvania code 42 county Lebanon code 075 3. Classification Category Ownership Status Present Use X district __ public X occupied agriculture _X_ museum building(s) private X unoccupied commercial park structure both work in progress educational _X_ private residence site Public Acquisition Accessible entertainment religious object in process yes: restricted government efiantifir being considered _X- yes: unrestricted X industrial transportation no military ...X other: 4. Owner of Property name Multiple - see continuation sheet street & number city, town __ vicinity of state 5. Location of Legal Description courthouse, registry of deeds, etc. T.P hanon County Courthouse street & number South 8th Street city, town Lebanon state PA 6. Representation in Existing Surveys title Historic Sites Survey has this property been determined eligible? yes no date 1966 _ federal county local depository for survey records National Park Service city, town Washington state D.C. 7. Description Condition Check one Check one X excellent deteriorated unaltered XL original site good ruins _X_ altered moved date fair unexposed Describe the present and original (if known) physical appearance The Cornwall Iron Furnace National Historic Landmark contains three interrelated major elements. -
NASSAWANGO IRON FURNACE Ca1828-1850 NEAR SNOW HILL, MARYLAND
NASSAWANGO IRON FURNACE ca1828-1850 NEAR SNOW HILL, MARYLAND A NATIONAL HISTORIC MECHANICAL ENGINEERING LANDMARK OCTOBER 19, 1991 The American Society of Mechanical Engineers FURNACE DelMarVa Group TOWN Nassawango Iron Furnace HISTORY OF NASSAWANGO IRON FURNACE Bog iron was first discovered in the swamps produced over 700 tons of pig iron per year at along Nassawango Creek in the 1780’s and in Nassawango; Spence was also credited with 1828 the Maryland Iron Company was the installation of the hot-blast stove on top of incorporated to extract and process it. In the furnace. 1830, the Company constructed a furnace along the creek at a point roughly four miles Iron was produced at Nassawango until 1847 northwest of its confluence with the when lack of labor and poor market Pocomoke River near Snow Hill, MD. Shortly conditions caused Spence (who fell into thereafter, the Nassawango furnace began financial ruin) to shut down the furnace. The producing pig iron by the cold-blast process. property sat idle from that time forward and was used by successive owners mostly for In 1836, two of the Company’s creditors, the timber rights. In 1962, the heirs of Arthur Milby and Joseph Waples, foreclosed Georgia Smith Foster donated the property to on the property; that same year they sold it to the Worcester County Historical Society Benjamin Jones, a Philadelphia ironmonger. which undertook a systematic long range Jones, who owned other furnaces and had a program to stabilize the furnace and cut back formidable business that bought and sold the plant growth of the previous 100 years. -
Blast Furnace Process: Is There Any Alternative?1
ISSN 2176-3135 BLAST FURNACE PROCESS: IS THERE ANY 1 ALTERNATIVE? 2 Ivan Kurunov Abstract Steel-making is globally based on hot metal refining in basic oxygen furnaces. At present and in perspective iron ore and coal remain the main primary materials for iron-making. Available processes of iron-making without a blast furnace are far behind the blast furnace process in terms of productivity and total through-out consumption of fuel for production of hot metal which includes the costs of coke and agglomerated raw materials production, hot blast and oxygen generation. Blast furnace process is the leader in terms of the amount of hot metal production with minimal production cost and in the near future can not only reserve the leading role but significantly reduce the cost for iron-making and the environmental impact. This possibility is related to the prospective use of self-reducing ore and coal briquettes made of concentrate and cheap coal-containing materials in blast furnaces. The process can also be further intensified by using oxygen and increasing the pressure within the furnace. Key words: Blast furnace process; Efficiency; Total fuel rate; Productivity, Alternative processes; Ore and coal briquettes. 1 6th International Congress on the Science and Technology of Ironmaking – ICSTI, 42nd International Meeting on Ironmaking and 13th International Symposium on Iron Ore, October 14th to 18th, 2012, Rio de Janeiro, RJ, Brazil. 2 Novolipetsk Steel, Chief Expert Ironmaking Division, Russia, e-mail: [email protected], tel. +79036437702 114 ISSN 2176-3135 1 INTRODUCTION At present steel is mostly made from hot metal, its percentage in the metallic charge of BOF vessels is 75-95 %, and in EAFs at integrated plants – up to 30-35 %.