(12) Patent Application Publication (10) Pub. No.: US 2006/0020077 A1 Miyoshi Et Al
Total Page:16
File Type:pdf, Size:1020Kb
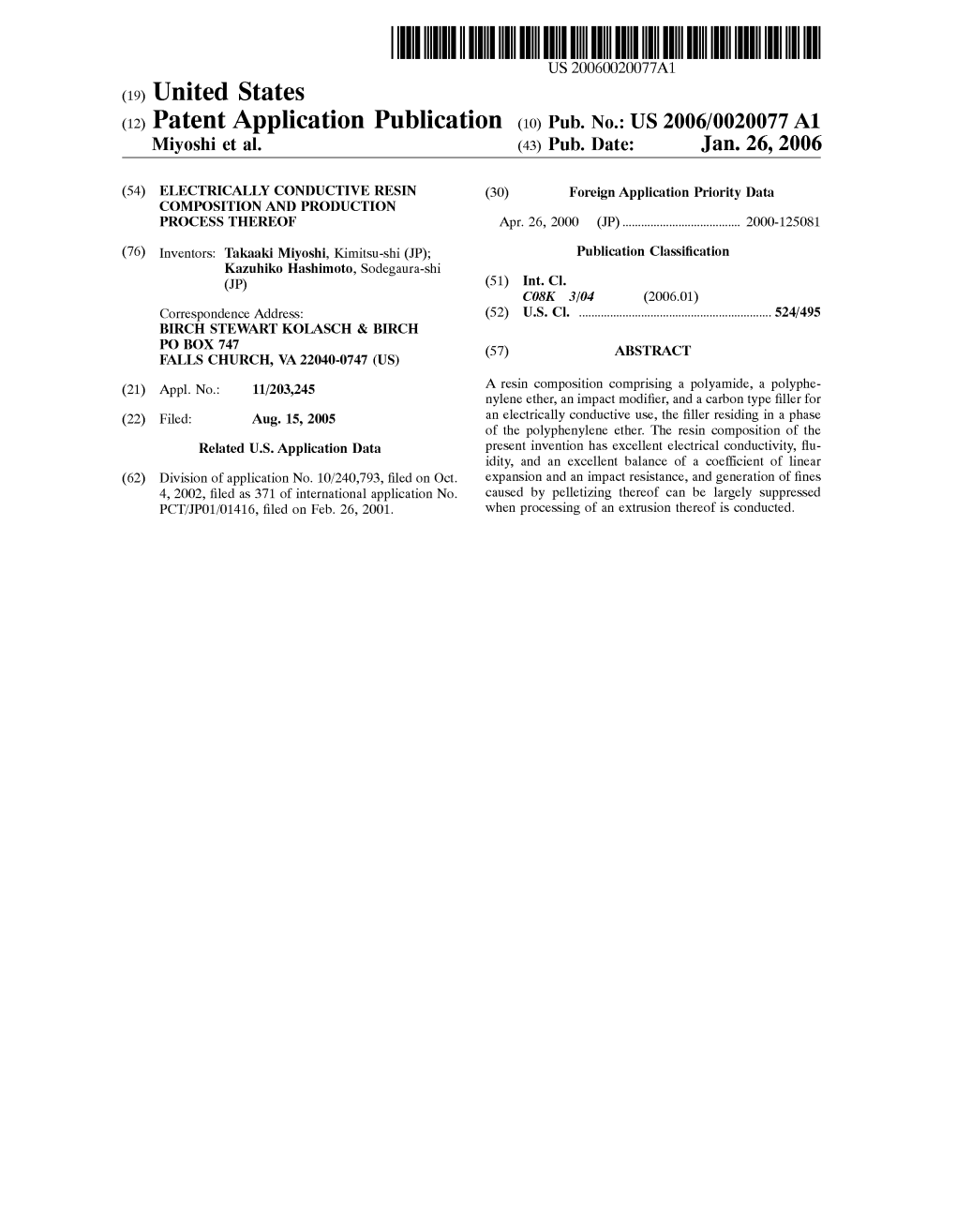
Load more
Recommended publications
-
A Simple, Fast, and Reliable LC-MS/MS Method for Determination and Quantification of Phthalates in Distilled Beverages
A Simple, Fast, and Reliable LC-MS/MS Method for Determination and Quantification of Phthalates in Distilled Beverages Dimple Shah and Jennifer Burgess Waters Corporation, Milford, MA, USA APPLICATION BENEFITS INTRODUCTION ■■ Separation and detection of 7 phthalates Phthalates, esters of phthalic acid, are often used as plasticizers for polymers such in 11 minutes. as polyvinylchloride. They are widely applicable in various products including personal care goods, cosmetics, paints, printing inks, detergents, coatings, ■■ Simple, quick “dilute and shoot” sample preparation method for routine applications and food packaging. These phthalates have been found to leach readily into the where high sample throughput is required. environment and food as they are not chemically bound to plastics. As such they are known to be ubiquitously present in our environment. ■■ Elimination of major phthalate contamination using the ACQUITY UPLC® Isolator Column. Phthalates have been reported to show a variety of toxic effects related to reproduction in animal studies, which has resulted in these compounds being ■■ Selective mass spectra obtained for all seven considered as endocrine disruptors. Screening food and beverages for phthalates phthalates with dominant precursor ion. contamination is required by many legislative bodies, although regulations vary ■■ Low limits of quantification achieved using from country to country in regards to acceptable daily tolerances and specific Waters® ACQUITY UPLC H-Class System migration limits. and Xevo® TQD. Traditionally, phthalates have been analyzed by gas chromatography-mass ■■ Single and robust method for a variety spectrometry (GC-MS), where derivatization and/or extraction and sample of distilled beverages. preparation is often required to improve chromatographic separation.1 The ■■ Maintain consumer confidence and resulting GC-EI-MS spectra can lack selectivity, where the base ion, used for ensure compliance in market. -
162 Part 175—Indirect Food Addi
§ 174.6 21 CFR Ch. I (4–1–19 Edition) (c) The existence in this subchapter B Subpart B—Substances for Use Only as of a regulation prescribing safe condi- Components of Adhesives tions for the use of a substance as an Sec. article or component of articles that 175.105 Adhesives. contact food shall not be construed as 175.125 Pressure-sensitive adhesives. implying that such substance may be safely used as a direct additive in food. Subpart C—Substances for Use as (d) Substances that under conditions Components of Coatings of good manufacturing practice may be 175.210 Acrylate ester copolymer coating. safely used as components of articles 175.230 Hot-melt strippable food coatings. that contact food include the fol- 175.250 Paraffin (synthetic). lowing, subject to any prescribed limi- 175.260 Partial phosphoric acid esters of pol- yester resins. tations: 175.270 Poly(vinyl fluoride) resins. (1) Substances generally recognized 175.300 Resinous and polymeric coatings. as safe in or on food. 175.320 Resinous and polymeric coatings for (2) Substances generally recognized polyolefin films. as safe for their intended use in food 175.350 Vinyl acetate/crotonic acid copoly- mer. packaging. 175.360 Vinylidene chloride copolymer coat- (3) Substances used in accordance ings for nylon film. with a prior sanction or approval. 175.365 Vinylidene chloride copolymer coat- (4) Substances permitted for use by ings for polycarbonate film. 175.380 Xylene-formaldehyde resins con- regulations in this part and parts 175, densed with 4,4′-isopropylidenediphenol- 176, 177, 178 and § 179.45 of this chapter. -
Proposed Designation of Butyl Benzyl Phthalate As a High-Priority
United States Office of Chemical Safety and Environmental Protection Agency Pollution Prevention Proposed Designation of Butyl Benzyl Phthalate (CASRN 85-68-7) as a High-Priority Substance for Risk Evaluation August 22, 2019 Table of Contents List of Tables ................................................................................................................................ iii Acronyms and Abbreviations ..................................................................................................... iv 1. Introduction ............................................................................................................................... 1 2. Production volume or significant changes in production volume ........................................ 3 Approach ..................................................................................................................................... 3 Results and Discussion ............................................................................................................... 3 3. Conditions of use or significant changes in conditions of use ............................................... 3 Approach ..................................................................................................................................... 3 CDR Tables ................................................................................................................................. 4 CDR and TRI Summary and Additional Information on Conditions of Use ............................. 6 -
Four Plastics Exempted from CPSIA Third Party Testing of Phthalates
Issue No.: 05/16/TCD Four Plastics Exempted from CPSIA Third Party Testing of Phthalates A Notice of Proposed Rulemaking exempting four plastics from phthalates testing under the CPSIA was approved by the Consumer Product Safety Commission (CPSC) on 9 August 2016. The decision came following a research conducted by the Toxicology Excellence for Risk Assessment (TERA) and other similar researches by the CPSC on the presence of eleven phthalates in four plastics used in children’s toys and child care articles. Once the rule has been approved, manufacturers shall not be required to conduct third-party testing in assuring compliance with the phthalate prohibitions for these four plastics. These four exempted plastics are: ¾ Polypropylene (PP) ¾ Polyethylene (PE) ¾ High Impact Polystyrene (HIPS) ¾ Acrylonitrile Butadiene Styrene (ABS) However, products made from the above plastics must continue to comply with Section 108 of CPSIA in which the “accessible plasticized component parts and other component parts made of materials that may contain phthalates” shall not contain any of the prohibited phthalates in concentration greater than 0.1% in children’s toys and child care articles. The six prohibited phthalates are: CPSIA Section 108 Phthalates Limit Permanent ban for use in children’s DEHP: di-(2-ethylhexyl) phthalate 0.1% toys or child care articles DBP: dibutyl phthalate 0.1% BBP: benzyl butyl phthalate 0.1% Interim ban for use in toys that can be DINP: diisononyl phthalate 0.1% put in the mouth or child care articles DIDP: diisodecyl phthalate 0.1% DnOP: di-n-octyl phthalate 0.1% Phthalates are generally used as plasticizers or softener of certain plastics. -
Toxicity Review of Diisobutyl Phthalate (DIBP)
identification, that is, a review of the available toxicity data for the chemical under consideration and a determination of whether the chemical is considered “toxic”. Chronic toxicity data (including carcinogenicity, neurotoxicity, and reproductive and developmental toxicity) are assessed by the CPSC staff using guidelines issued by the Commission (CPSC, 1992). If it is concluded that a substance is “toxic” due to chronic toxicity, then a quantitative assessment of exposure and risk is performed to evaluate whether the chemical may be considered a “hazardous substance”. This memo represents the first step in the risk assessment process; that is, the hazard identification step. * This report was prepared for the Commission pursuant to contract CPSC-D-06-0006. It has not been reviewed or approved by, and may not necessarily reflect the views of, the Commission. Page 2 of 2 FINAL TOXICITY REVIEW FOR DIISOBUTYL PHTHALATE (DiBP, CASRN 84-69-5) Contract No. CPSC-D-06-0006 Task Order 012 Prepared by: Versar Inc. 6850 Versar Center Springfield, VA 22151 SRC, Inc. 7502 Round Pond Road North Syracuse, NY 13212 Prepared for: Kent R. Carlson, Ph.D. U.S. Consumer Product Safety Commission 4330 East West Highway Bethesda, MD 20814 July 14, 2011 * This report was prepared for the Commission pursuant to contract CPSC-D-06-0006. It has not been reviewed or approved by, and may not necessarily reflect the views of, the Commission. TABLE OF CONTENTS TOXICITY REVIEW FOR DIISOBUTYL PHTHALATE APPENDICES .............................................................................................................................. -
CAS 84-69-5 Diisobutyl Phthalate (DIBP)
CAS 84-69-5 Diisobutyl phthalate (DIBP) Toxicity The European Union classified DIBP as a reproductive Substance of Very High Concern (SVHC).1 A 2011 study observed decreased testicular testosterone in male rats fed DIBP for 4 days.2 Borch et al. 2006 found male offspring of female rats exposed to DIBP from gestation day 7 to gestation day 20 or 21 had significantly reduced anogenital distance.3 The Chronic Hazard Advisory Panel (CHAP) determined, due to toxicological profile similarities to Dibutyl phthalate (DBP), exposure to DIBP contributes to a cumulative antiandrogenic effect with other phthalates and should be permanently banned in children’s toys and child care articles at levels greater than 0.1 percent.4 In 2017 the CPSC permanently banned DIBP in children’s toys and childcare articles at levels greater than 0.1 percent.5 Exposure The 2015 National Health and Nutrition Examination Survey (NHANES) monitored a metabolite of DIBP in human urine, and the levels appear to be increasing.6 Metabolites of DIBP were detected in the urine of pregnant Danish women in a 2010-2012 study.7 A significant correlation was found between DIBP metabolite concentrations in the urine of Danish children and increased levels of DIBP in bedroom dust and day care centers.8 Other DIBP is used as a substitute ingredient to di-n-butyl phthalate (DBP) due to structural similarities, therefore, its’ presence in products may increase.3 References 1. European Commission, Endocrine disruptor priority list. Retrieved from: http://ec.europa.eu/environment/chemicals/endocrine/strategy/substances_en.htm 2. Hannas, B.R., Lambright, C.S., Furr, J., Howdeshell, K.L., Wilson, V.S., Gray, L.E., Jr. -
Benzyl Butyl Phthalate Or BBP)
Toxicity Review for Benzylnbutyl Phthalate (Benzyl Butyl Phthalate or BBP) Introduction Benzyl butyl phthalate (BBP) is a man‐made phthalate ester that is mostly used in vinyl tile (CERHR, 2003). BBP can also be found as a plasticizer in polyvinyl chloride (PVC) for the manufacturing of conveyor belts, carpet, weather stripping and more. It is also found in some vinyl gloves and adhesives. BBP is produced by the sequential reaction of butanol and benzyl chloride with phthalic anhydride (CERHR, 2003). The Monsanto Company is the only US producer of BBP (IPCS, 1999). When BBP is added during the manufacturing of a product, it is not bound to the final product. However, through the use and disposal of the product, BBP can be released into the environment. BBP can be deposited on and taken up by crops for human and livestock consumption, resulting in its entry into the food chain (CERHR, 2003). Concentrations of BBP have been found in ambient and indoor air, drinking water, and soil. However, the concentrations are low and intakes from these routes are considered negligible (IPCS, 1999). Exposure to BBP in the general population is based on food intake. Occupational exposure to BBP is possible through skin contact and inhalation, but data on BBP concentrations in the occupational environment is limited. Unlike some other phthalates, BBP is not approved by the U.S. Food and Drug Administration for use in medicine or medical devices (IPCS, 1999; CERHR, 2003). Based on the National Toxicology Program (NTP) bioassay reports of increased pancreatic lesions in male rats, a tolerable daily intake of 1300 µg/kg body weight per day (µg/kg‐d) has been calculated for BBP by the International Programme on Chemical Safety (IPCS) (IPCS, 1999). -
Labware Chemical Resistance Table
Labware Chemical Resistance Table Interpretation of Chemical Resistance The Chemical Resistance Chart that follows is a general guide only. Because so many factors can affect the chemical resistance of a given product, you should test under your own conditions. Effects of Chemicals on Plastics Chemicals can affect the strength, flexibility, surface appearance, color, dimensions or weight of plastics. The basic modes of interaction which cause these changes are: (1) chemical attack on the polymer chain, with resultant reduction in physical properties, including oxidation; reaction of functional groups in or on the chain; and depolymerization; (2) physical change, including absorption of solvents, resulting in softening and swelling of the plastic; permeation of solvent through the plastic; dissolution in a solvent; and (3) stress cracking from the interaction of a “stress cracking agent” with internal or external stresses. Mixing and/or dilution of certain chemicals can be potentially dangerous. The reactive combination of different chemicals or compounds of two or more classes may cause an undesirable chemical effect or result in an increased temperature, which can affect chemical resistance (as temperature increases, resistance to attack decreases). Other factors affecting chemical resistance include pressure and internal or external stresses (e.g. centrifugation), length of exposure, and concentra tion of the chemical. 608 www.thermoscientifi c.com appendix Environmental Stress Cracking Environmental stress cracking is the failure of a plastic material in the presence of certain types of chemicals. This failure is not a result of chemical attack. Simultaneous presence of three factors causes stress cracking: tensile stress, a stress cracking agent and the inherent susceptability of the plastic to stress cracking. -
Determination of Six Phthalates in Polypropylene Consumer Products by Sonication-Assisted Extraction/Gc-Ms Methods
The Malaysian Journal of Analytical Sciences, Vol 15 No 2 (2011): 167 - 174 DETERMINATION OF SIX PHTHALATES IN POLYPROPYLENE CONSUMER PRODUCTS BY SONICATION-ASSISTED EXTRACTION/GC-MS METHODS (Penentuan Enam Ftalat dalam Produk-Produk Konsumer Polipropilena dengan Kaedah Ekstraksi Bantuan-Sonikasi/GCMS) Chong Kian Wei*, Loke Chui Fung and Michelle Pang Chemistry and Biology Division, School of Arts and Science, Tunku Abdul Rahman College, Jalan Genting Kelang, Setapak, 53300 Kuala Lumpur, Malaysia *Corresponding author: [email protected] Abstract Studies on determination of six kinds of phthalates, i.e. dimethyl phthalate (DMP), diethyl phthalate (DEP), dibutyl phthalate (DBP), benzyl butyl phthalate (BBP), di-(2-ethylhexyl) phthalate (DEHP), and di-n-octyl phthalate (DnOP), in three kinds of plastic containers for food use, including food container, instant noodle cup and snack container, by gas chromatography in combination with mass spectrometry detector (GC-MS) in electronic ionization mode with selected-ion monitoring (SIM) acquisition method (GC-MS(EI-SIM)) have been carried out. Extraction, clean-up and analysis methods have been developed and optimized. Determination of samples were performed after sonication-assisted extraction with 1:9 toluene and dichloromethane, clean-up with Bio-Beads S-X8 gel-permeation column and analyzed by GC-MS methods. The characteristic ions, 163, 194 for DMP; 149, 177, 222 for DEP; 149, 233, 251 for DBP; 91, 149, 206 for BBP; 149, 176, 193 for DEHP; 149, 167, 279 for DNOP were chosen for quantitative studies. These techniques are possible to detect phthalates at the level of 1-70 mg/kg. The overall recoveries were 79.2-91.1% with relative standard deviation (R.S.D.) values at 3.1-11.3%. -
Phthalate Release from Plastic Fragments and Degradation in Seawater Andrea Paluselli, Vincent Fauvelle, François Galgani, Richard Sempere
Phthalate Release from Plastic Fragments and Degradation in Seawater Andrea Paluselli, Vincent Fauvelle, François Galgani, Richard Sempere To cite this version: Andrea Paluselli, Vincent Fauvelle, François Galgani, Richard Sempere. Phthalate Release from Plastic Fragments and Degradation in Seawater. Environmental Science and Technology, American Chemical Society, 2019, 53 (1), pp.166-175. 10.1021/acs.est.8b05083. hal-01974368 HAL Id: hal-01974368 https://hal.archives-ouvertes.fr/hal-01974368 Submitted on 8 Jan 2019 HAL is a multi-disciplinary open access L’archive ouverte pluridisciplinaire HAL, est archive for the deposit and dissemination of sci- destinée au dépôt et à la diffusion de documents entific research documents, whether they are pub- scientifiques de niveau recherche, publiés ou non, lished or not. The documents may come from émanant des établissements d’enseignement et de teaching and research institutions in France or recherche français ou étrangers, des laboratoires abroad, or from public or private research centers. publics ou privés. Article Cite This: Environ. Sci. Technol. 2019, 53, 166−175 pubs.acs.org/est Phthalate Release from Plastic Fragments and Degradation in Seawater Andrea Paluselli,† Vincent Fauvelle,† Francoiş Galgani,‡ and Richard Semperé *́ ,† †Aix-Marseille University; Université de Toulon, CNRS, IRD, Mediterranean Institute of Oceanography (M I O), 13288 Marseille, France ‡IFREMER, Laboratoire Environnement Ressources, Provence Azur Corse (LER/PAC), Ifremer Centre de Mediterrané e,́ ZP de Bregaillon, -
Priority Chemical List
PRIORITY CHEMICAL LIST Policy Number BBBPO-0017 Implementation 2019 Revision Date: Date: Bed Bath & Beyond Inc. and its subsidiaries (collectively, the “Company”) are committed to providing customers with safe, high quality products. To that end, the Company is issuing the below Priority Chemical List, which is a subset of its Restricted Substances List (“RSL”), to further reduce the use of certain chemicals of concern in household cleaning, personal care, and cosmetic products. In addition, the Company is responding to customers’ growing interest in ingredient disclosures by committing to ingredient transparency in certain private label products. It is the Company’s expectation that vendors of all household cleaning, personal care, and cosmetic products will remove, or at minimum, reduce the use of Priority Chemicals in their products, including parabens, phthalates, formaldehyde donors, NPEs, Toluene, and Triclosan. In moving to eliminate these chemicals from formulations, the Company expects suppliers to select ingredients identified as Safer Chemicals by the U.S. Environmental Protection Agency (EPA) Safer Choice program, or to use EPA Safer Choice criteria or the safer alternatives Marketplace to evaluate and select safe substitutions. See https://www.epa.gov/saferchoice/safer-ingredients. The Company also encourages all vendors of household cleaning, personal care, and cosmetic products to include ingredient disclosures on product packaging. The Company is particularly committed to eliminating Priority Chemicals from private label baby personal care products. The Company is working collaboratively with suppliers to evaluate private label baby personal care products and to reformulate where necessary to eliminate intentionally added Priority Chemicals from those products, including in fragrances, by the end of 2020. -
Breast Cancer Fund's Faqs About Phthalates
PHTHALATES FREQUENTLY ASKED QUESTIONS What are phthalates? Phthalates are odorless, colorless chemicals that are added to plastic to make it soft and flexible. Phthalates are a family of chemicals that include diethyl phthalate (DEP), diethylhexyl phthalate (DEHP), dibutyl phthalate (DBP), butyl benzyl phthalate (BBP), diisodecyl phthalate (DIDP), diisononyl phthalate (DINP), di-n-octyl phthalate (DNOP), and many other distinct types. The polyvinyl chloride (PVC) plastics industry uses phthalates as additives to improve the flexibility of its products, including home vinyl siding, flooring, furniture, food packaging, toys, clothing, car interiors, and medical equipment, including IV bags. In addition, other manufacturers use phthalates in personal care products such as soap, shampoo, deodorant, hand lotion, nail polish, cosmetics, and perfume, as well as industrial products like solvents, lubricants, glue, paint, sealants, insecticides, and detergent.1,2 How long have we known about the problems phthalates can pose? Scientists began studying the toxicity of several phthalates as early as the 1950s and discovered significant evidence of environmental and human contamination in the early 1970s, including the leaching of phthalates into human blood from PVC bags used in hospitals.3 As noted by the Worldwatch Institute,4 NASA scientists warned against using PVC in the space program in 1971 because of poor physical properties and the presence of phthalates. They noted that “substitute polymers . are available and in many cases they have far superior physical properties at a small sacrifice in immediate cost.5” Nonetheless, phthalates remain in wide use today. Why are phthalates such a problem? Phthalates are known endocrine disruptors and can affect normal hormonal processes.