PATENT OFFICE 2,680,098 SILICON COMPOUNDS Ral B
Total Page:16
File Type:pdf, Size:1020Kb
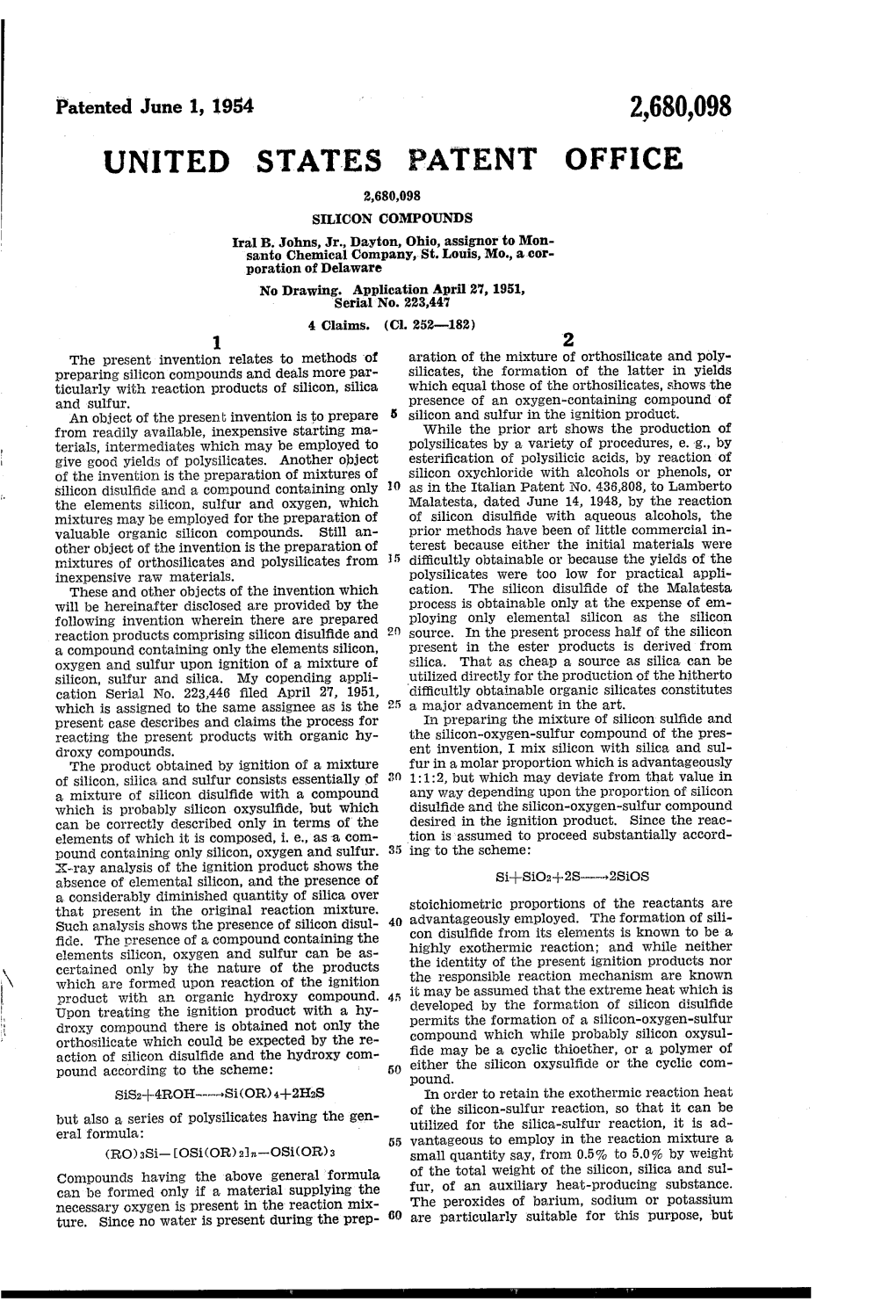
Load more
Recommended publications
-
Sulfur-Containing Radicals: from EPR Spectroscopic Studies to Synthetic Methodology
Sulfur-containing Radicals: From EPR Spectroscopic Studies to Synthetic Methodology A Thesis Presented to the University of London in Partial Fulfilment of the Requirements for the Degree of Doctor of Philosophy Alistair John Fielding February 2002 Christopher Ingold Laboratories Department of Chemistry University College London London WCIH OAJ UCL ProQuest Number: 10015687 All rights reserved INFORMATION TO ALL USERS The quality of this reproduction is dependent upon the quality of the copy submitted. In the unlikely event that the author did not send a complete manuscript and there are missing pages, these will be noted. Also, if material had to be removed, a note will indicate the deletion. uest. ProQuest 10015687 Published by ProQuest LLC(2016). Copyright of the Dissertation is held by the Author. All rights reserved. This work is protected against unauthorized copying under Title 17, United States Code. Microform Edition © ProQuest LLC. ProQuest LLC 789 East Eisenhower Parkway P.O. Box 1346 Ann Arbor, Ml 48106-1346 7 believe a leaf of grass is no less than the journey-work of the stars. ” Walt Whitman This thesis is dedicated to my late Auntie, Doreen Latter. 1930-2001 ABSTRACT A variety of novel homochiral silanethiols have been prepared and investigated as polarity-reversal catalysts for the enantioselective hydrosilylation of a prochiral alkene. The enantiomeric excesses of the products were disappointingly small. A computer modelling procedure, based on molecular mechanics, was applied in order to understand the results and quantitative agreement with experiment was reasonably good. Silanethiols have been oxidised to the corresponding disulfides and these have been investigated as photochemical sources of silanethiyl radicals. -
Material Safety Data Sheet
LTS Research Laboratories, Inc. Safety Data Sheet Silicon Sulfide ––––––––––––––––––––––––––––––––––––––––––––––––––––––––––––––––––––––––––––––––––––––––––––– 1. Product and Company Identification ––––––––––––––––––––––––––––––––––––––––––––––––––––––––––––––––––––––––––––––––––––––––––––– Trade Name: Silicon Sulfide Chemical Formula: SiS2 Recommended Use: Scientific research and development Manufacturer/Supplier: LTS Research Laboratories, Inc. Street: 37 Ramland Road City: Orangeburg State: New York Zip Code: 10962 Country: USA Tel #: 855-587-2436 / 855-lts-chem 24-Hour Emergency Contact: 800-424-9300 (US & Canada) +1-703-527-3887 (International) ––––––––––––––––––––––––––––––––––––––––––––––––––––––––––––––––––––––––––––––––––––––––––––– 2. Hazards Identification ––––––––––––––––––––––––––––––––––––––––––––––––––––––––––––––––––––––––––––––––––––––––––––– Signal Word: Danger Hazard Statements: H261: In contact with water releases flammable gas H300: Fatal if swallowed H315: Causes skin irritation H319: Causes serious eye irritation H335: May cause respiratory irritation Precautionary Statements: P231+P232: Handle under inert gas. Protect from moisture P261: Avoid breathing dust/fume/vapor P301+P310: IF SWALLOWED: Immediately call a POISON CENTER or doctor/physician P305+P351+P338: IF IN EYES: Rinse cautiously with water for several minutes. Remove contact lenses if present and easy to do – continue rinsing P405: Store locked up P501: Dispose of contents/container in accordance with local/regional/national/international regulations -
Creating New Layered Structures at High Pressures: Sis2 Dušan Plašienka1, Roman Martoňák1 & Erio Tosatti2,3
www.nature.com/scientificreports OPEN Creating new layered structures at high pressures: SiS2 Dušan Plašienka1, Roman Martoňák1 & Erio Tosatti2,3 Old and novel layered structures are attracting increasing attention for their physical, electronic, and Received: 27 September 2016 frictional properties. SiS2, isoelectronic to SiO2, CO2 and CS2, is a material whose phases known Accepted: 03 November 2016 experimentally up to 6 GPa exhibit 1D chain-like, 2D layered and 3D tetrahedral structures. We present Published: 25 November 2016 highly predictive ab initio calculations combined with evolutionary structure search and molecular dynamics simulations of the structural and electronic evolution of SiS2 up to 100 GPa. A highly stable CdI2-type layered structure, which is octahedrally coordinated with space group P31m surprisingly appears between 4 and up to at least 100 GPa. The tetrahedral-octahedral switch is naturally expected upon compression, unlike the layered character realized here by edge-sharing SiS6 octahedral units connecting within but not among sheets. The predicted phase is semiconducting with an indirect band gap of about 2 eV at 10 GPa, decreasing under pressure until metallization around 40 GPa. The robustness of the layered phase suggests possible recovery at ambient pressure, where calculated phonon spectra indicate dynamical stability. Even a single monolayer is found to be dynamically stable in isolation, suggesting that it could possibly be sheared or exfoliated from bulk P31m -SiS2. SiS2 is a member of an important family of group IV-VI AB2 compounds made of light elements including 1–14 15–22 23–27 28–31 well-known materials such as CO2 , SiO2 , GeO2 and CS2 . -
I DEVELOPING a SCIENCE UNIT PLAN THAT IS BOTH INTERESTING and EFFECTIVE for SECONDARY SCHOOLS a Thesis Submitted to the Kent St
DEVELOPING A SCIENCE UNIT PLAN THAT IS BOTH INTERESTING AND EFFECTIVE FOR SECONDARY SCHOOLS A thesis submitted to the Kent State University Honors College in partial fulfillment of the requirements for General Honors by Margaret Quinn Evans May, 2015 i Thesis written by Margaret Quinn Evans Approved by _______, Advisor ______________ _ , Director, School of Teaching, Learning and Curriculum Studies Accepted by , Dean, Honors College ii TABLE OF CONTENTS LIST OF TABLES . .iv ACKNOWLEDGEMENT . .v CHAPTER I. INTRODUCTION . 1 II. READY, SET, PLAN! . 3 Collaborative Teaching . 3 Determining Learning Objectives . 5 Appropriate and Essential Instruction and Activities . 6 III. ADAPTATIONS TO LESSON PLANS . 9 Accommodations for Students with Special Needs . 9 IV. SAMPLE UNIT PLAN . 14 Lesson 1: Charge It Elementally! . .20 Lesson 2: How Ionic – Predicting Ionic Compound Formulas . .39 Lesson 3: What’s In A Name? – Naming Ionic Compounds . 50 Lesson 4: Coo- Coo For Covalents – Naming Covalent Compounds . 70 Lesson 5: Reverse, Reverse! – Formula Writing From Name . 84 Unit Test . 96 WORKS CITED . .106 iii LIST OF TABLES Table 1. Collaboration with Other Teachers . 4 Table 2. Categories and Examples of Accommodations . 10 iv AKNOWLEDGMENTS First and foremost I would like to thank Dr. Lisa Borgerding for being such a crucial part of helping me write and edit this thesis. I would also like to take the time to thank Dr. Pritha Sumraminian, Dr. Paul Sampson, and Dr. Sarah Raven for taking the time to be a part of my defense committee. I would also like to thank my Fall 2013 and Spring 2013 Supplemental Instruction Classes for being the test dummies for my lesson activities. -
1. Give the Correct Names for Each of the Compounds Listed Below. A
1. Give the correct names for each of the compounds listed below. a) NaCl sodium chloride n) ZrS2 zirconium sulfide b) FrBr francium bromide o) AgI silver iodide c) KF potassium fluoride p) BaSe barium selenide d) RaS radium sulfide q) MgO magnesium oxide e) LiI lithium iodide r) LaBr3 lanthanum bromide f) Li3N lithium nitride s) Sr3N2 strontium nitride g) AlBr3 aluminum bromide t) Cd3As2 cadmium arsenide h) CdCl2 cadmium chloride u) Rb2Se rubidium selenide i) K2O potassium oxide v) Rb3N rubidium nitride j) InF3 indium fluoride w) BaF2 barium fluoride k) ZnO zinc oxide x) ZrTe2 zirconium telluride l) Y2O3 yttrium oxide y) Cs3P cesium phosphide m) CaTe calcium telluride z) Y2O3 yttrium oxide 2. Write the correct chemical formula for each of the following compounds. a) potassium bromide KBr n) potassium nitride K3N b) zinc bromide ZnBr2 o) aluminum bromide AlBr3 c) lithium iodide LiI p) zinc phosphide Zn3P2 d) scandium chloride ScCl3 q) magnesium sulfide MgS e) magnesium chloride MgCl2 r) hafnium chloride HfCl4 f) magnesium oxide MgO s) barium sulfide BaS g) hydrogen sulfide H2S t) tantalum oxide Ta2O5 h) gallium iodide GaI3 u) zirconium nitride Zr3N4 i) sodium oxide Na2O v) potassium selenide K2Se j) magnesium selenide MgSe w) germanium fluoride GeF4 k) calcium fluoride CaF2 x) francium phosphide Fr3P l) aluminum oxide Al2O3 y) zinc arsenide Zn3As2 m) beryllium chloride BeCl2 z) scandium telluride Sc2Te3 L. h. s. – Chemistry – Nomenclature – Answers – Page 1 3. Give the correct names for each of the compounds listed below. a) CaSO4 calcium -
THERMODYNAMIC PROPERTIES of INDIVIDUAL SUBSTANCES Fourth Edition
THERMODYNAMIC PROPERTIES OF INDIVIDUAL SUBSTANCES Fourth Edition Volume 2 Elements C, Si, Ge, Sn, Pb, and Their Compounds PartTwo Tables Editors L. V. Gurvich and I. V. Veyts Institute for High Temperatures USSR Academy of Sciences, Moscow C. B. Alcock University of Notre Dame, Notre Dame, Indiana Table Editor V. S. Iorish Institute for High Temperatures USSR Academy of Sciences, Moscow OHEMISPHERE PUBLISHING CORPORATION A member of the Taylor & Francis Group New York Washington Philadelphia London CONTENTS LIST OF TABLES Table No. Substance Pag 238 Carbon (graphite) C(cr, 1) 1 239 Carbon (diamond) C(cr) 2 240 Carbon C(g) 3 241 Carbon positive ion C+(g) 5 242 Carbon negative ion C_(g) 7 243 Dicarbon C2(g) 8 + 244 Dicarbon positive ion C2 (g) 10 245 Dicarbon negative ion C2~(g) 12 246 Tricarbon C3(g) 14 247 Tetracarbon C4(g) 16 248 Pentacarbon C5(g) 18 249 Carbon oxide CO(g) 20 250 Carbon oxide positive ion CO+(g) 22 251 Carbon dioxide C02(g) 24 + 252 Carbon dioxide positive ion C02 (g) 26 253 Dicarbon oxide CzO(g) 28 254 Tricarbon dioxide C302(g) 29 255 Methine CH(g) 30 256 Methine positive ion CH +(g) 32 257 Methylene CH2(g) 34 258 Methyl CH3(g) 35 259 Methane CH4(g) 36 260 Dicarbon hydride C2H(g) 37 261 Acetylene C2H2(g) 39 262 Dicarbon trihydride C2H3(g) 41 263 Ethylene C2H4(g) 42 264 Ethyl C2H5(g) 43 265 Ethane C2H6(g) 44 vi CONTENTS Table No. Substance Page 266 Formyl HCO 45 267 Carboxyl COOH(g) 46 268 Formaldehyde H2CO(g) 47 269 Formic acid HCOOH(g) 48 270 Cfa-Formic acid HCOOH[rä](g) 49 271 Trans-Formic acid HCOOH[trans](g) 50 272 -
Organic Seminar Abstracts
UNIVERSITY OF IILINOIS LIBRARY AT U ^.NA-CHAMPAIGN Digitized by the Internet Archive in 2012 with funding from University of Illinois Urbana-Champaign http://archive.org/details/organicsemi1979821univ 1 SEMINAR TOPICS X- I Semester 1979-80 — ^ Generation and Synthetic Utility of Carbanions Stabilized by Divalent Sulfur Peter Becker The Design, Synthesis, and Biology of Intercalating Agents David W. Robertson r HERTZBERG - NEW METHOD, INC. EAST VANDALIA ROAD, JACKSONVILLE, ILL. 62650 J - Q_ , TITUE NO. ACCOUNT NO. LOT AND TICKET NO. ...13 B ]• 22 : NRTK« 31 5>79~82*PT Q* 547*IG»L< 33 CLOTH COLOR CHARGING INFORMATION .... 36 STUBBING FRONT COVER HAND SEW NO TR IM THRU SEW PAGES LAMINATED THRU SEW ON TAPE EXTRA THICKNESS ... .46 HAND ADHESIVE MAP POCKET PAPER LENGTHWISE MAP POCKET CLOTH SPECIAL WORK AND PREP. FOREIGN TITLE SPECIAL WORK LINES OF LETTERING 56 Phosphorus uompouiiub Stephen D. Harper Vanadium- and Molybdenum-Catalyzed of Olefins with Epoxidations 59 Alkyl Hydroperoxides - John R. Hurst Characterization of Certain Detection and 68 Carbon Diradicals Via ESR and CIDNP... G. H. Slocum 76 Enzymic Catalysis in Organic Synthesis Venkatesalu Bakthavachalam in the Reactions of Regioselectivity 86 Hetero-Substituted Allylic Carbanions, Dale Kempf SEMINAR TOPICS I Semester 1979-80 - T* Generation and Synthetic Utility of Carbanions Stabilized by Divalent Sulfur 1 Peter Becker The Design, Synthesis, and Biology of Intercalating Agents 3 David W. Robertson Modification of Olefins with Organo- Selenium Reagents 13 Larry D. Boardman Synthetic Methods for the Preparation of Sterically Hindered Olefins 22 Ronald S. Michalak Mechanistic Considerations in 1,3-Dipolar Cycloadditions 31 Clark Cummins Applications of Lasers in Organic Chemistry 33 Rick Gdanski Magnetic Field Effects on Chemical Reactions in Solution 36 Paul Gelburd Synthetic Approaches to Biotin 46 Jack Muskopf Stable Hexacoordinate Organo- Phosphorus Compounds 56 Stephen D. -
An Introduction to Basic Silicone Chemistry By
[ 01 ft< 58449 > OU_1 [g ^ CD ^ C/) LI ' Call No. - ~L> Accession No. Author fidCJi*lO. Tak CL^v betew. This book should be re/Urned on or before the date last marked An Introduction to the CHEMISTRY of the SILICONES An Introduction to the CHEMISTRY of the SILICONES By EUGENE G. ROCHOW Research Laboratory, General Electric Company NEW YORK: JOHN WILEY & SONS, INC. LONDON: CHAPMAN & HALL, LIMITED COPYRIGHT, 1946 BY EUGENE G. ROCHOW AU Rights Reserved This book or any part thereof must not be reproduced in any form without the written permission of the publisher. SECOND PRINTING, MARCH, 1947 PRINTED IN THE UNITED STATES OF AMERICA To P. G. F. PREFACE The organic compounds of silicon, which have been the subject of many scholarly researches during the past 80 years, at last show promise of emerging from the laboratory and finding a place in industry. An understanding of the behavior of organosilicon materials is necessary to their intelligent use and, inasmuch as the chemistry of these substances ordinarily is not treated in our textbooks, it is possible that a compact yet comprehensive survey of our present knowledge in this field would be of service to chemists, engineers, and industrial designers. This volume has just such a purpose. The first few chapters review the silanes and their derivatives in some detail, in order to provide an understanding of the fundamental chemistry of the nonsilicate com- pounds of silicon. The later chapters emphasize the silicone polymers which have achieved commercial importance and deal with the methods for their preparation, their chemical and physical properties, and their possible usas. -
Combined Prohibited and Restricted Chemical Lists
Dedicated to protecting and improving the health and environment of the people of Colorado Combined Prohibited and Restricted Chemical Lists This document is a combined and alphabetized list of the Prohibited and Restricted Chemicals as defined and listed in the Rules and Regulations Governing Schools in the State of Colorado, 6 CCR 1010-6, Appendices A, B, and B2. This combined list can be used as a supplement to the Rules and Regulations and as a quick reference format when conducting such activities as a chemical inventory or during the chemical procurement process. Shelf life descriptions are provided for each chemical to assist in evaluating a timeframe for safe chemical use and storage. In general, chemical shelf life descriptions are as follows: POOR - less than 1 year; FAIR - 1 to 3 years; GOOD - 3 to 5 years; and EXCELLENT or INDEFINITE - greater than 5 years. Additional oversight for chemicals with a shelf life of less than 3 years is important to ensure that they are not stored or used past their shelf life or expiration date, at which point they may become unstable and dangerous. Completion of Table 2 on the Restricted Chemical Variance Application Form is required for any chemicals with a shelf life of less than 3 years and/or those chemicals that are known to have issues with container integrity or other hazards associated with their use and storage in a school environment. Please see "Limited Shelf Life – Table 2 Required?" column on this list before completing the variance application form. Please note that the hazard information and shelf life descriptions provided for the listed chemicals is not intended to address all safety concerns. -
NBO 2015 – 2008 References Compiled by Ariel Andrea on 8/31/2018
NBO 2015 – 2008 references Compiled by Ariel Andrea on 8/31/2018 Abbat, S.; Dhaked, D.; Arfeen, M.; Bharatam, P. V. Mechanism of the Paal-Knorr reaction: the importance of water mediated hemialcohol pathway RSC Advances, (5): 88353-88366. 2015. 10.1039/c5ra16246g Abdel-Azeim, S.; Jedidi, A.; Eppinger, J.; Cavallo, L. Mechanistic insights into the reductive dehydroxylation pathway for the biosynthesis of isoprenoids promoted by the IspH enzyme Chemical Science, (6): 5643-5651. 2015. 10.1039/c5sc01693b Abdel-Ghani, N. T.; Mansour, A. M.; El-Ghar, M. F. A.; El-Borady, O. M.; Shorafa, H. Co(II), Ni(II) and Cu(II) complexes of azo-aminopyrazole ligand: Spectroscopic, crystal structure and quantum chemical calculations Inorganica Chimica Acta, (435): 187-193. 2015. 10.1016/j.ica.2015.06.021 Abdulsattar, M. A. Molecular approach to hexagonal and cubic diamond nanocrystals Carbon Letters, (16): 192-197. 2015. 10.5714/cl.2015.16.3.192 Abdulsattar, M. A.; Almaroof, S. M. Electronic and spectroscopic properties of GeC superlattice nanocrystals: A first-principle study using diamondoid structures Superlattices and Microstructures, (79): 63-71. 2015. 10.1016/j.spmi.2014.12.011 Abedini, M.; Izadyar, M.; Nakhaipour, A. Different Aspects of Single Wall Carbon Nanotube Functionalization by Aniline Adsorption; Quantum Mechanics/Molecular Mechanics Study Journal of Nano Research, (32): 1-U21. 2015. 10.4028/www.scientific.net/JNanoR.32.1 Abyar, F.; Farrokhpour, H.; Tabrizchi, M. Gas phase ionization energies of some important unsaturated steroids Structural Chemistry, (26): 71-86. 2015. 10.1007/s11224-014-0469-4 Adhikari, D. A computational study to unravel the selectivity in an iron-catalysed 3+2 cycloaddition of aziridine and heterocumulenes RSC Advances, (5): 95379-95384. -
Writing Names and Formulas
Module 7 – Writing Names and Formulas Module 7 – Writing Names and Formulas Prerequisites: Complete Module 6 before starting Module 7. The other prior modules are not necessary for Module 7. * * * * * Lesson 7A: Naming Elements and Covalent Compounds Pretest: If you think you know this topic, try the last letter of each question in Practice A and Practice B. If you get those right, skip the lesson. * * * * * Systems for Naming Substances In chemistry, substances are identified by both a unique name and a chemical formula. For names and formulas that both identify and differentiate substances, a system for writing formulas and names is required. 1. The names of some compounds are non-systematic but familiar: Water (H2O) and ammonia (NH3) are examples. 2. Historically, chemical substances have been divided into two broad categories. Compounds containing carbon comprise organic chemistry, which has its own system for naming compounds. All other substances are part of inorganic chemistry, which is the focus of most first-year chemistry courses. 3. Different types of inorganic substances have different naming systems. We will begin with the rules for elements, binary covalent compounds, ions, and binary ionic compounds. Naming Elements An element is a substance that contains of only one kind of atom. The name of an element is simply the name of its atoms. Examples • The element comprised of atoms with 20 protons is called calcium. Formulas of metals are written as if they are monatomic elements. The formula for the element calcium is written Ca. • Chlorine atoms, at room temperature, are found in diatomic molecules. For the element chlorine, the formula is written Cl2. -
Academic Upgrading Chemistry 20 Placement Test Study Guide
Centre for Academic Learner Services Academic Upgrading Chemistry 20 Placement Test Study Guide Updated: June 2015 Academic Upgrading | Chemistry 20 Placement Test Study Guide | 2 Important Information about this Study Guide and the Placement Test This study guide is designed to prepare students for the Academic Upgrading Chemistry 20 Placement test. An answer key is included at the end of this guide. The test is taken in the Testing Centre (MC 221; see www.sait.ca/testing for hours, location and to book your test appointment). Contact Academic Upgrading to receive instructions for booking your testing appointment by emailing [email protected]. It is designed for Academic Upgrading placement purposes only. This test may not be used for admission to any SAIT program; that is, this is not a SAIT admission exam. In addition, the results cannot be used at any other educational institution. The time allotted for the Chemistry 20 Placement test is 2 hours. The tests consists of 54 questions and covers Grade 11 (Chemistry 20) material. A mark of 65% is required to pass and allows entrance into CHEM 182. Note: CHEM 182 is equivalent to Chemistry 30. CHEM 182 is accepted as an admission requirement at other post-secondary institutions in Alberta, but you should always check with the post-secondary institution you are interested in attending (if it is not SAIT) to confirm it will accept the course. Academic Upgrading | Chemistry 20 Placement Test Study Guide | 3 SAIT Academic Upgrading Course Sequence APSC 180 CHEM 181 CHEM 182 (Science Prep) (Chemistry 20 (Chemistry 30 equiv.) equiv.) Introduction: Chemistry 20 Study Guide Review the objectives, definitions, and practice exercises.