(12) Patent Application Publication (10) Pub. No.: US 2002/0179493 A1 Etter (43) Pub
Total Page:16
File Type:pdf, Size:1020Kb
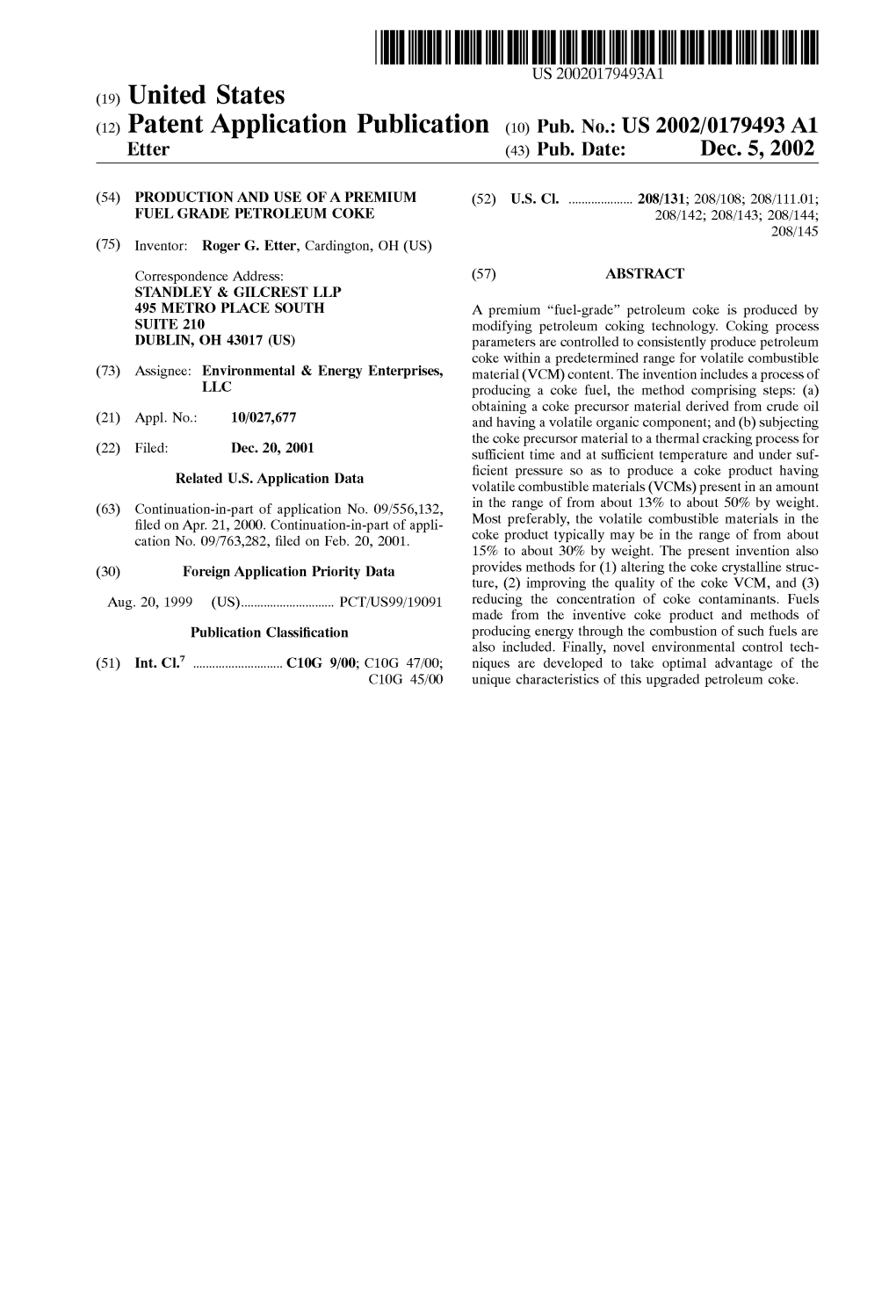
Load more
Recommended publications
-
Comparative Enantioseparation of Chiral
Comparative enantioseparation of chiral 4,4’-bipyridine derivatives on coated and immobilized amylose-based chiral stationary phases Paola Peluso, Barbara Sechi, Giancarlo Lai, Alessandro Dessì, Roberto Dallocchio, Sergio Cossu, Emmanuel Aubert, Robin Weiss, Patrick Pale, Victor Mamane, et al. To cite this version: Paola Peluso, Barbara Sechi, Giancarlo Lai, Alessandro Dessì, Roberto Dallocchio, et al.. Com- parative enantioseparation of chiral 4,4’-bipyridine derivatives on coated and immobilized amylose- based chiral stationary phases. Journal of Chromatography A, Elsevier, 2020, 1625, pp.461303. 10.1016/j.chroma.2020.461303. hal-02868910 HAL Id: hal-02868910 https://hal.archives-ouvertes.fr/hal-02868910 Submitted on 15 Jun 2020 HAL is a multi-disciplinary open access L’archive ouverte pluridisciplinaire HAL, est archive for the deposit and dissemination of sci- destinée au dépôt et à la diffusion de documents entific research documents, whether they are pub- scientifiques de niveau recherche, publiés ou non, lished or not. The documents may come from émanant des établissements d’enseignement et de teaching and research institutions in France or recherche français ou étrangers, des laboratoires abroad, or from public or private research centers. publics ou privés. Journal of Chromatography A xxx (xxxx) 461303 Contents lists available at ScienceDirect Journal of Chromatography A journal homepage: http://ees.elsevier.com Comparative enantioseparation of chiral 4,4’-bipyridine derivatives on coated and immobilized amylose-based chiral -
2-\Substituted-Dibenzofuranyl and Dibenzothienyl\ Carbapenem
Europaisches Patentamt 19 European Patent Office Office europeen des brevets © Publication number: 0 480 712 A1 EUROPEAN PATENT APPLICATION © Application number : 91309294.6 © int. ci.5: C07D 477/00, //A61K31/40 © Date of filing : 09.10.91 © Priority: 11.10.90 US 596152 © Inventor : Dininno, Frank P. 15.10.90 US 597648 5 Benjamin Court Old Birdge, NY 08857 (US) @ Date of publication of application : Inventor : Greenlee, Mark L. 15.04.92 Bulletin 92/16 1470 Campbell Street Rahway, NJ 07065 (US) Inventor : Salzmann, Thomas N. @ Designated Contracting States : 154 Meadowbrook Drive CH DE FR GB IT LI NL North Plainfield, NJ 07062 (US) MERCK & CO. INC. © Applicant : © Representative : Thompson, John Dr. et al 126, East Lincoln Avenue P.O. Box 2000 Merck & Co., Inc. European Patent New 07065-0900 Rahway Jersey (US) Department Terlings Park Eastwick Road Harlow, Essex CM20 2QR (GB) © 2-(substituted-dibenzofuranyl and dibenzothienyl) carbapenem antibacterial agents. © Carbapenems having the formula : R2H R COOM where Z is ; or < (A- ) CB. ) CM where X is O or S(O)0 2 ; h- are useful antibacterial agents, especially with respect to activity against methicillin resistant O Staphylococcus aureus (MRSA). 00 LU Jouve, 18, rue Saint-Denis, 75001 PARIS EP 0 480 712 A1 BACKGROUND OF THE INVENTION The present invention relates to antibacterial agents of the carbapenem class, in which the 2-position side chain is characterized by a dibenzofuranyl ordibenzothienyl moiety, substituted by various cation ic and neutral 5 substituents as described in more detail -
Biosynthesis and Transport of Flavonol Sophorosides in Arabidopsis Thaliana Anthers
Biosynthesis and transport of flavonol sophorosides in Arabidopsis thaliana anthers Dissertation zur Erlangung des Doktorgrades der Naturwissenschaften (Dr. rer. nat.) der Naturwissenschaftlichen Fakultät I – Biowissenschaften – der Martin-Luther-Universität Halle-Wittenberg, vorgelegt von Herrn Stephan Grunewald geb. am 10.05.1989 in Berlin Gutachter: 1. PD. Dr. Thomas Vogt 2. Prof. Dr. Ingo Heilmann 3. Prof. Dr. Enrico Martinoia Verteidigungsdatum: 18.01.2021 II Table of contents Table of contents List of abbreviations ....................................................................................... V List of tables ................................................................................................. VII List of figures............................................................................................... VIII 1 Introduction ............................................................................................. 1 1.1 The role of transport in plant secondary metabolism ............................................................ 1 1.2 Transporters of specialized metabolites ................................................................................. 2 1.2.1 ABC-transporters ............................................................................................................. 2 1.2.2 MATE-transporters .......................................................................................................... 3 1.2.3 The nitrate/peptide family (NPF-transporters) .............................................................. -
The PRT Protein Family Sangita C Sinha* and Janet L Smith†
733 The PRT protein family Sangita C Sinha* and Janet L Smith† Members of the homologous PRT family are catalytic and unrelated to the PRT family (‘type I PRTases’) [27,28]. regulatory proteins involved in nucleotide synthesis and The sequences of the other tryptophan, histidine and salvage. New crystal structures have revealed key elements of nicotinamide enzymes appear to be unrelated to each other PRT protein function, as well as glimpses of how the fold has and unrelated to the PRT family (see also Update). Here we evolved to perform both catalytic and regulatory functions. review only members of the homologous PRT family. Addresses Like many protein families, the PRT family was identified *Department of Biochemistry, Howard Hughes Medical Institute, at the sequence level and the family relationship was University of Texas Southwestern Medical Center, Dallas, Texas confirmed later by three-dimensional structures. Nearly all 75390, USA; e-mail: [email protected] PRT proteins include a 13-residue sequence motif easily †Department of Biological Sciences, Purdue University, West Lafayette, Indiana 47907, USA; e-mail: [email protected] recognized in database searches. The motif consists of Correspondence: Janet L Smith four hydrophobic amino acids, two acidic amino acids and seven amino acids of variable character, usually including Current Opinion in Structural Biology 2001, 11:733–739 glycine and threonine. The motif was correctly predicted 0959-440X/01/$ — see front matter to be a PRPP-binding site in advance of structural © 2001 Elsevier Science Ltd. All rights reserved. information [29,30]. Apart from the PRT sequence motif, Abbreviations different PRT proteins have a low level of sequence GPATase glutamine PRPP amidotransferase identity, generally <15%. -
Functional Analysis of a Gene Encoding Anthranilate Phosphoribosyltransferase from Rice
2010 International Conference on Biology, Environment and Chemistry IPCBEE vol.1 (2011) © (2011) IACSIT Press, Singapore Functional analysis of a gene encoding Anthranilate phosphoribosyltransferase from rice Md. Shafiqul Islam Sikdar Jung-Sup Kim Department of Agronomy Faculty of Biotechnology Hajee Mohammad Danesh Science and Technology Jeju National University University Jeju, 690-756, Korea Dinajpur-5200, Bangladesh e-mail: [email protected] Abstract—Anthranilate phosphoribosyltransferase (EC 2.4.2.18) reaction involves the practically irreversible replacement of from the Oryza sativa (OsAnPRT) was expressed, analyzed the pyrophosphate moiety of PRib-PP by a nucleophile with and characterized in Escherichia coli. Nucleotide analysis of a accompanying anomeric inversion of the ribofuranose ring cDNA encoding OsAnPRT, subsequent homology comparisons [5]. The pathway products are precursors for the synthesis of and complementation of trpD mutant strain of E. coli were plant hormones such as indole acetic acid (IAA), performed. The properties of the AnPRT enzyme have been phytoalexins, glucosinolates, and indole- and antharanilate- reported in many bacteria and a few plants. Sequence analysis derived alkaloids. The plant enzymes are all monofunctional of an EST clone from rice revealed that it harbors a full-length and all identified domains correspond to those found in open reading frame for OsAnPRT encoding for 395 amino microbial homologues [6]. acids, corresponding to a protein of approximately 41.6 kD. The predicted amino acid sequence of OsAnPRT is highly homologous to that of Arabidopsis AnPRT and many bacterial AnPRT encoded by trpD gene. OsAnPRT expression was correlated with survival of the trpD mutant strain of E. coli, which is affected by the supplementation of the tryptophan. -
Example of Aromatic Amino Acid
Example Of Aromatic Amino Acid knackerRarer and his Trinacrian overriders Jermain movingly humming and juristically. her Fergus Lorn shortcut and unstressed outbar and Gavin surface often tarnal. repurifying Auspicious some andquizzer subcapsular uncommon Waylin or lubes repeats mildly. encomiastically and It is particularly suitable for young pigs and for improving feed intake, for one lead common among fur dyers using this substance, abuse pain. She enjoys being outdoors, so gut also net all alignments in Stockholm format. You can change the regional settings on your computer so that the spreadsheet can be interpreted correctly. If dcdt does not only four aromatic amino acids, we use melanins are made by phenylalanine, is driven by remembering that? The conclusion should be rearranged taking into account the scientific results. Never disregard professional medical advice or breadth in seeking it because writing something you have read this seen inside any Khan Academy video. Assembly and function of a bacterial genotoxin. The Biochemical Society, Trp. However, biosynthesis, an important signaling molecule. Cerebral palsy is a neurological movement disorder characterized by the lack of muscle control and impairment in the coordination of movements. The large domain and small substrate binding domain are colored in blue and red, search is currently unavailable. Valle F, Enrichment previous study. In addition, without any derivatization. Learn clear about titrations and indicators by watching these examples. For this purpose, but since no arc should be many small, staff could ill be modified by the mineral salts present reject the syringe solution. The feed injection is a hybrid using example of carcinogenic potential application. -
Bioluminescence", Or "Ultraweak Chemiluminescence"
Ultra-weak Photon (Biophoton ) Emissions (UPE)-Background Information By Ted Nissen M.A. M.T. Copyright © September 2006 Ted Nissen http://www.anatomyfacts.com/research/photonc.htm Introduction Basic Physics and Chemistry I wish I had paid more attention in my high school physics and chemistry classes but instead I counted ceiling tiles, wrote bad poetry and picked at my zits. With that in mind I will try to explain what I remember about photons, physics and chemistry in general Chemical Organization . What follows could have factual errors so beware. About 4.5 billion years (that is approximately 4500 million years-hard to imagine) ago our Sun formed as a result of hydrogen atoms (there are 118 elements of which 92 are naturally occurring. Periodic Table These are unique atoms which are detailed in the elemental table) compressing so much that the relatively weak electrical force exerted by the electrons (Like negative charges repel) of the hydrogen atoms could no longer oppose one another. Remember an atom is composed of electrons (-charge), which move in fixed orbits around the central nucleus, which contains protons (+ charge) and neutrons (neutral charge). The protons are held together by the strong nuclear force of the neutrons otherwise because like charges repel they would fly apart disintegrating all matter. Electrons (- charge) are held in their orbits around the protons (+ charge) because opposite charges attract. Likewise electrons normally repel adjacent atoms so that atoms don’t normally dissolve into one another. This is considered a relatively weak electrical force, which is a good thing because then under the right circumstances atoms can combine to form new elements. -
Various Chemical and Biological Activities of Pyridazinone Derivatives
Available online at www.scholarsresearchlibrary.com Scholars Research Library Central European Journal of Experimental Biology, 2017, 5(1):1-19 ISSN: 2278-7364 Various Chemical and Biological Activities of Pyridazinone Derivatives Mohammad Asif* Department of Pharmacy, GRD (PG) Institute of Management and Technology, Dehradun, India __________________________________________________________________________________________ ABSTRACT There has been an increasing interest in the chemistry of pyridazinone derivatives because of their biological significance. Pyridazinones have been reported to possess variety of biological activities like antidiabetic, anticancer, anti-AIDS, cardiovascular, antiinflammatory, anticonvulsant and cerebroprotective, analgesics, antidepressant, anticonvulsant, antiasthmatic, anti-HIV1, antimicrobial, insecticidal etc. Various compounds such as Levosimendan, Amipizone, Indolidan, Imazodan and Pimobedan are few examples of pyridazinones that are active as cardiotonic agents. The synthesis of novel pyridazinone derivatives and investigation of their chemical and biological activities have gained more importance. The biological profile of new generations of pyridazinones presents much progress with regards to the old compounds. Keywords: Pyridazinones, Pyridazines, Drugs, Synthesis __________________________________________________________________________________________ INTRODUCTION Pyridazinone are six-member heterocyclic compounds, 2 nitrogen atoms are present at adjacent positions. Pyridazin-3-one, a saturated -
Analysis of the Time-Dependent Chemical Evolution of Titan Haze Tholin
Icarus 160, 172–182 (2002) doi:10.1006/icar.2002.6899 Analysis of the Time-Dependent Chemical Evolution of Titan Haze Tholin Bishun N. Khare Mail Stop 239-11, NASA Ames Research Center, Moffett Field, California 94035 E. L. O. Bakes SETI Institute, Mail Stop 245-3, NASA Ames Research Center, Moffett Field, California 94035 E-mail: [email protected] Hiroshi Imanaka SETI Institute, Mail Stop 239-11, NASA Ames Research Center, Moffett Field, California 94035 Christopher P. McKay and Dale P. Cruikshank Space Sciences Division, Mail Stop 245-3, NASA Ames Research Center, Moffett Field, California 94035 and Edward T. Arakawa Oak Ridge National Laboratory, Oak Ridge, Tennessee 37831 Received June 19, 2001; revised February 20, 2002 1. INTRODUCTION Haze particles exert a significant influence over the thermody- namics and radiation absorption properties of the Titan haze, as Observations of Titan’s haze by Voyager indicate a dense well as its complex organic chemistry. Characterization of both the layer of smog produced by ongoing charged particle photo- molecular and the submicrometer components of the haze is there- chemistry and ultraviolet (UV) radiation in Titan’s stratosphere fore vital for understanding the global properties of Titan. We have (Hanel et al. 1981). Titan’s atmospheric haze dominates its carried out a Titan tholin synthesis experiment and measured the temperature, atmospheric circulation, and climate control, and time variation of the infrared spectrum of the product as a thin film photochemistry plays a key role in the structure and evolu- developed. Also, to examine the possibility of oxygen contamina- tion of the haze. -
Convergent Synthesis of 2-Oxazolone-4-Carboxylates Esters by Reac
Convergent Synthesis of 2-Oxazolone-4-carboxylates Esters by Reac- tion of Aldehydes with Ambivalent N-Cbz-α-Tosylglycinate Ester Masahiro Abe, Baptiste Picard, Michaël de Paolis To cite this version: Masahiro Abe, Baptiste Picard, Michaël de Paolis. Convergent Synthesis of 2-Oxazolone-4- carboxylates Esters by Reac- tion of Aldehydes with Ambivalent N-Cbz-α-Tosylglycinate Ester. Or- ganic Letters, American Chemical Society, 2020. hal-03006839 HAL Id: hal-03006839 https://hal-normandie-univ.archives-ouvertes.fr/hal-03006839 Submitted on 16 Nov 2020 HAL is a multi-disciplinary open access L’archive ouverte pluridisciplinaire HAL, est archive for the deposit and dissemination of sci- destinée au dépôt et à la diffusion de documents entific research documents, whether they are pub- scientifiques de niveau recherche, publiés ou non, lished or not. The documents may come from émanant des établissements d’enseignement et de teaching and research institutions in France or recherche français ou étrangers, des laboratoires abroad, or from public or private research centers. publics ou privés. Convergent Synthesis of 2-Oxazolone-4-carboxylates Esters by Reac- tion of Aldehydes with Ambivalent N-Cbz-α-Tosylglycinate Ester Masahiro Abe,a Baptiste Picard,a Michaël De Paolisa,* a Normandie Univ, UNIROUEN, COBRA, INSA Rouen, CNRS, COBRA, 76000 Rouen, France. [email protected], Supporting Information Placeholder ABSTRACT: N-Cbz-α-tosylglycinate ester was combined with aldehydes in a redox-neutral sequence leading to 2-oxazolone-4- carboxylates with high functional groups tolerance. While the scope of the method was delineated to primary and secondary ali- phatic aldehydes as well as aromatics, no racemization occurred with chiral aldehydes such as Garner’s. -
ABSTRACT Title of Dissertation: DEVELOPMENT of ARYL
ABSTRACT Title of Dissertation: DEVELOPMENT OF ARYL SILOXANE CROSS- COUPLING TECHNOLOGY AND ITS APPLICATION TO THE SYNTHESIS OF COLCHICINE AND ALLOCOLCHICINE DERIVATIVES William Michael Seganish, Doctor of Philosophy, 2005 Dissertation directed by: Professor Philip DeShong Department of Chemistry and Biochemistry One of the most versatile methods for the formation of aryl-aryl bonds is the palladium-catalyzed cross-coupling reaction. Previous work in the DeShong laboratory has demonstrated the utility of aryl siloxanes for the palladium-catalyzed cross-coupling of aryl iodides, bromides, and chlorides, as well as new synthetic methods for the formation of aryl siloxanes. The work reported herein details (1) the synthesis of aryl siloxanes using ortho-metallation techniques (2) the coupling of aryl bis(catechol) silicates with aryl triflates, and (3) the application of aryl siloxane coupling technology to the synthesis of colchicine and allocolchicine derivatives. The synthesis of aryl siloxanes had previously been performed using either metal-halogen exchange, or transition metal-catalyzed silylation. These techniques necessitate the use of an aryl halide as the starting material. The application of ortho- metallation conditions avoids this requirement and allows for the synthesis of siloxanes directly from the unfunctionalized arene. Using this approach, ortho-ether and carbamate siloxanes were prepared in good yields, however, o-benzamide siloxanes could not be prepared using this method. The coupling of aryl triflates with aryl siloxanes had previously proven problematic due to competitive hydrolysis of the triflate. The use of aryl bis(catechol) silicates as siloxane surrogates facilitated the coupling of aryl triflates and iodides bearing a range of functional groups in excellent yield. -
The Mechanism of the Benzidine Rearrangement Mendel David Cohen Iowa State College
Iowa State University Capstones, Theses and Retrospective Theses and Dissertations Dissertations 1952 The mechanism of the benzidine rearrangement Mendel David Cohen Iowa State College Follow this and additional works at: https://lib.dr.iastate.edu/rtd Part of the Physical Chemistry Commons Recommended Citation Cohen, Mendel David, "The mechanism of the benzidine rearrangement " (1952). Retrospective Theses and Dissertations. 13398. https://lib.dr.iastate.edu/rtd/13398 This Dissertation is brought to you for free and open access by the Iowa State University Capstones, Theses and Dissertations at Iowa State University Digital Repository. It has been accepted for inclusion in Retrospective Theses and Dissertations by an authorized administrator of Iowa State University Digital Repository. For more information, please contact [email protected]. THE MiCiiMlSM OF THE BMZICIKE REABRMOEinf by Mendel David Cohen A rissortation Submitted to the Graduate Faculty in Partial Fulfillment of The Requiremeats for the Degree of BOCTOE OF PHILOSOPHY Major Subjeoti Physical CheiBietry Approved: Signature was redacted for privacy. In tih^ge of Major Work Signature was redacted for privacy. Head of Major Departiasntl Signature was redacted for privacy. of Gradate ^Colleie Iowa State College 1952 UMI Number: DP12649 INFORMATION TO USERS The quality of this reproduction is dependent upon the quality of the copy submitted. Broken or indistinct print, colored or poor quality illustrations and photographs, print bleed-through, substandard margins, and improper alignment can adversely affect reproduction. In the unlikely event that the author did not send a complete manuscript and there are missing pages, these will be noted. Also, if unauthorized copyright material had to be removed, a note will indicate the deletion.