Development and Implementation of a Composite Material Shell-Element Model
Total Page:16
File Type:pdf, Size:1020Kb
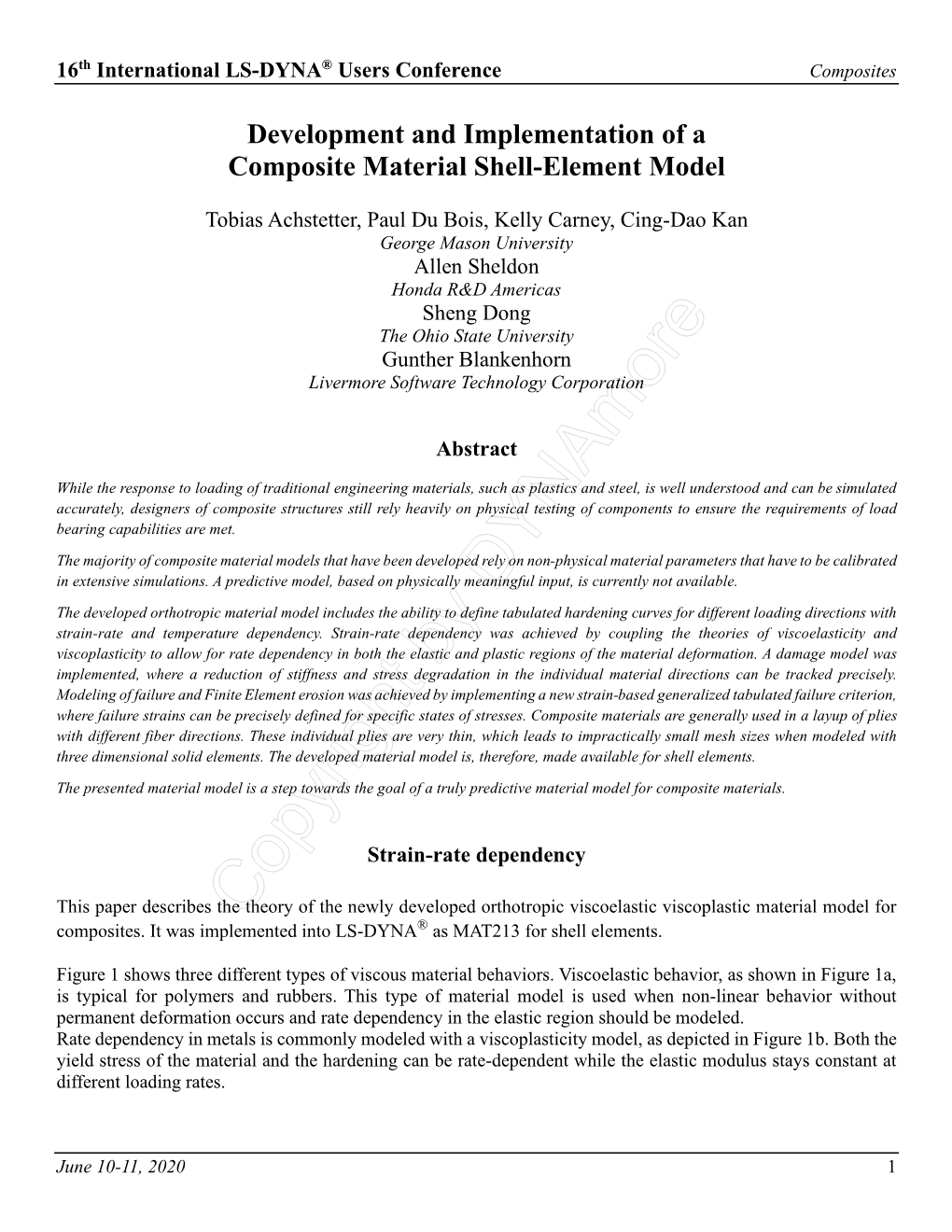
Load more
Recommended publications
-
V- 3 31 Finite Element Implementation of State Variable-Based
https://ntrs.nasa.gov/search.jsp?R=19910023209 2020-03-17T14:54:26+00:00Z View metadata, citation and similar papers at core.ac.uk brought to you by CORE provided by NASA Technical Reports Server ,,/v-_3 31 / NASA Contractor Report 187212 Finite Element Implementation of State Variable-Based Viscoplasticity Models (UA_A-CR-I_7212) FINITE ELEMENT N91-32523 IMPLEMENTATIL3N OF STATE VA&IABLF-_ASED VISCOPLA_TICITY MnOELS Final Report (Akron Univ.) 41 p CSCL 2OK G3/39 I. Iskovitz, T.Y.P. Chang, and A.F. Saleeb University of Akron Akron, Ohio September 1991 Prepared for Lewis Research Center Under Grant NAG3-901 National Aeronautics and Space Administration Finite Element Implementation of State Variable-Based Viscoplasticity Models I. Iskovitz, T.Y.P. Chang and A.F. Saleeb Department of Civil Engineering University of Akron Akron, Ohio 44325 Abstract Implementation of state variable-based viscoplasticity models is made in a general purpose finite element code for structural appli- cations of metals deformed at elevated temperature. Two consti- tutive models, i.e. Walker's and Robinson's models, are studied in conjunction with two implicit integration methods: the trapezoidal rule with Newton-Raphson iterations and an asymptotic integra- tion algorithm. A comparison is made between the two integration methods, and the latter method appears to be computationally more appealing in terms of numerical accuracy and CPU time. However, in order to make the asymptotic algorithm robust, it is necessary to include a self adaptive scheme with subincremental step control and error checking of the Jacobian matrix at the integration points. Three examples are given to illustrate the numerical aspects of the integration methods tested. -
Constitutive Behavior of Granitic Rock at the Brittle-Ductile Transition
CONSTITUTIVE BEHAVIOR OF GRANITIC ROCK AT THE BRITTLE-DUCTILE TRANSITION Josie Nevitt, David Pollard, and Jessica Warren Department of Geological and Environmental Sciences, Stanford University, Stanford, CA 94305 e-mail: [email protected] fracture to ductile flow with increasing depth in the Abstract earth’s crust. This so-called “brittle-ductile transition” has important implications for a variety of geological Although significant geological and geophysical and geophysical phenomena, including the mechanics processes, including earthquake nucleation and of earthquake rupture nucleation and propagation propagation, occur in the brittle-ductile transition, (Hobbs et al., 1986; Li and Rice, 1987; Scholz, 1988; earth scientists struggle to identify appropriate Tse and Rice, 1986). Despite the importance of constitutive laws for brittle-ductile deformation. This deformation within this lithospheric interval, significant paper investigates outcrops from the Bear Creek field gaps exist in our ability to accurately characterize area that record deformation at approximately 4-15 km brittle-ductile deformation. Such gaps are strongly depth and 400-500ºC. We focus on the Seven Gables related to the uncertainty in choosing the constitutive outcrop, which contains a ~10cm thick aplite dike that law(s) that govern(s) the rheology of the brittle-ductile is displaced ~45 cm through a contractional step transition. between two sub-parallel left-lateral faults. Stretching Rheology describes the response of a material to an and rotation of the aplite dike, in addition to local applied force and is defined through a set of foliation development in the granodiorite, provides an constitutive equations. In addition to continuum excellent measure of the strain within the step. -
Fracture Mechanics
Fracture Mechanics Introduction to Fracture Introduction to Fracture Presented by Calvin M. Stewart, PhD MECH 5390-6390 Fall 2020 Outline • Definition • Failure of Structures • Fracture Mechanics Approach to Design • Significance • Review of Approaches • Energy Approach, Stress Intensity Factor Approach, Crack Tip Plasticity, Fracture Toughness, The J Integral, Classification, Fatigue • Methods • Analytical, Experimental, Computational Definition of Fracture Mechanics • Fracture – field of study focused on characterizing the behavior of crack in cracked structures. • Notes: • Understanding how crack behaves equips engineers with the tools needed to design against the initiation and propagation of cracks • Fracture behavior is dependent on material, load/displacement, and geometric factors Failure of Structures Fracture Mechanics Approach to Design Significance In the nineteenth century, it was realized that pre-existing flaws could initiate cracking and fracture. It was discovered that brittle fracture in steels was promoted by low temperatures. Significance There was considerable development of new high strength alloys. In the 1950’s, it was recognized that although these materials are not intrinsically brittle, the energy required for fracture is comparatively low. The possibility, and indeed occurrence, of this low energy fracture in high strength materials stimulated the modern development of fracture mechanics. Significance Consider a structure containing pre-existing flaws and/or in which crack initiate in service. The crack may growth with time owing to various causes (fatigue, stress corrosion, creep, etc.) and will generally grow progressively faster. The residual strength of the structure, which is the failure strength as a function of crack size, decreases with increasing crack size. After a time, the residual strength becomes so low that the structure may failure in service. -
An Anisotropic Viscoplasticity Model for Shale Based on Layered Microstructure Homogenization
An anisotropic viscoplasticity model for shale based on layered microstructure homogenization Jinhyun Chooa,∗, Shabnam J. Semnanib, Joshua A. Whitec aDepartment of Civil Engineering, The University of Hong Kong, Hong Kong bDepartment of Structural Engineering, University of California, San Diego, United States cAtmospheric, Earth, and Energy Division, Lawrence Livermore National Laboratory, United States Abstract Viscoplastic deformation of shale is frequently observed in many subsurface applications. Many studies have sug- gested that this viscoplastic behavior is anisotropic—specifically, transversely isotropic—and closely linked to the layered composite structure at the microscale. In this work, we develop a two-scale constitutive model for shale in which anisotropic viscoplastic behavior naturally emerges from semi-analytical homogenization of a bi-layer mi- crostructure. The microstructure is modeled as a composite of soft layers, representing a ductile matrix formed by clay and organics, and hard layers, corresponding to a brittle matrix composed of stiff minerals. This layered microstructure renders the macroscopic behavior anisotropic, even when the individual layers are modeled with isotropic constitutive laws. Using a common correlation between clay and organic content and magnitude of creep, we apply a viscoplastic Modified Cam-Clay plasticity model to the soft layers, while treating the hard layers as a linear elastic material to minimize the number of calibration parameters. We then describe the implementation of the proposed model in a standard material update subroutine. The model is validated with laboratory creep data on samples from three gas shale formations. We also demonstrate the computational behavior of the proposed model through simulation of time-dependent borehole closure in a shale formation with different bedding plane directions. -
A Variational Framework for Nonlinear Viscoelastic and Viscoplastic Models in Finite Deformation Regime Laurent Stainier, E
A variational framework for nonlinear viscoelastic and viscoplastic models in finite deformation regime Laurent Stainier, E. Fancello, Jean-Philippe Ponthot To cite this version: Laurent Stainier, E. Fancello, Jean-Philippe Ponthot. A variational framework for nonlinear viscoelas- tic and viscoplastic models in finite deformation regime. Proc. of MECOM VIII, Argentinian Congress on Computational Mechanics, 2005, Buenos Aires, Argentina. hal-01007825 HAL Id: hal-01007825 https://hal.archives-ouvertes.fr/hal-01007825 Submitted on 27 Aug 2019 HAL is a multi-disciplinary open access L’archive ouverte pluridisciplinaire HAL, est archive for the deposit and dissemination of sci- destinée au dépôt et à la diffusion de documents entific research documents, whether they are pub- scientifiques de niveau recherche, publiés ou non, lished or not. The documents may come from émanant des établissements d’enseignement et de teaching and research institutions in France or recherche français ou étrangers, des laboratoires abroad, or from public or private research centers. publics ou privés. A VARIATIONAL FRAMEWORK FOR NONLINEAR VISCOELASTIC AND VISCOPLASTIC MODELS IN FINITE DEFORMATION REGIME Laurent Stainier∗, Eduardo A. Fancello†, and Jean-Philippe Ponthot∗ ∗Departement´ AeroSpatiale,´ Mecanique´ et mAteriaux´ Universite´ de Liege,` LTAS-MCT, 1 chemin des chevreuils, B-4000 Liege,` Belgium email: [email protected], web page: http://www.asma.ulg.ac.be †Departmento de Engenharia Mecanicaˆ Universidade Federal de Santa Catarina, Caixa Postal 476, Campus Universitario,´ Trindade, 88040-900 Florianopolis,´ SC, Brazil email: [email protected], web page: http://www.emc.ufsc.br Key Words: Constitutive Updates, Finite Viscoelasticity, Finite Viscoplasticity, Variational Formulation. Abstract. The goal of this work is to provide a general framework for constitutive viscoelastic and viscoplastic models based on the theoretical background proposed in Ortiz and Stainier, Comput. -
Robust Integration Schemes for Generalized Viscoplasticity with Internal-State Variables
Computers and Structures 74 (2000) 601±628 www.elsevier.com/locate/compstruc Robust integration schemes for generalized viscoplasticity with internal-state variables A.F. Saleeb*, T.E. Wilt, W. Li Department of Civil Engineering, The University of Akron, Akron, OH 44325, USA Received 11 July 1998; accepted 31 August 1998 Abstract This paper is concerned with the development of a general framework for the implicit time-stepping integrators for the ¯ow and evolution equations in complex viscoplastic models. The primary goal is to present a complete theoretical formulation, and to address in detail the algorithmic and numerical analysis aspects involved in its ®nite element implementation, as well as to critically assess the numerical performance of the developed schemes in a comprehensive set of test cases. On the theoretical side, we use the unconditionally stable, backward Euler dierence scheme. Its mathematical structure is of sucient generality to allow a uni®ed treatment of dierent classes of viscoplastic models with internal variables. Two speci®c models of this type, which are representatives of the present state-of-the-art in metal viscoplasticity, are considered in the applications reported here; i.e., generalized viscoplasticity with complete potential structure fully associative (GVIPS) and non-associative (NAV) models. The matrix forms developed for both these models are directly applicable for both initially isotropic and anisotropic materials, in three-dimensions as well as subspace applications (i.e., plane stress/strain, axisymmetric, generalized plane stress in shells). On the computational side, issues related to eciency and robustness are emphasized in developing the (local) iterative algorithm. In particular, closed-form expressions for residual vectors and (consistent) material tangent stiness arrays are given explicitly for the GVIPS model, with the maximum matrix sizes `optimized' to depend only on the number of independent stress components (but independent of the number of viscoplastic internal state parameters). -
Bounding Surface Elasto-Viscoplasticity: a General Constitutive Framework for Rate-Dependent Geomaterials
Center for Sustainable Engineering of Geological and Infrastructure Materials (SEGIM) Department of Civil and Environmental Engineering McCormick School of Engineering and Applied Science Evanston, Illinois 60208, USA Bounding Surface Elasto-Viscoplasticity: A General Constitutive Framework for Rate-Dependent Geomaterials Z. Shi, J. P. Hambleton and G. Buscarnera SEGIM INTERNAL REPORT No. 18-5/766B Submitted to Journal of Engineering Mechanics May 2018 1 Bounding Surface Elasto-Viscoplasticity: A General Constitutive 2 Framework for Rate-Dependent Geomaterials 1 2 3 Zhenhao Shi, Ph.D. A.M. ASCE , James P. Hambleton, Ph.D. A.M. ASCE , and Giuseppe 3 4 Buscarnera, Ph.D. M. ASCE 1 5 Department of Civil and Environmental Engineering, Northwestern University, Evanston, IL 6 60208, USA, with corresponding author email. Email: [email protected] 2 7 Department of Civil and Environmental Engineering, Northwestern University, Evanston, IL 8 60208, USA 2 9 Department of Civil and Environmental Engineering, Northwestern University, Evanston, IL 10 60208, USA 11 ABSTRACT 12 A general framework is proposed to incorporate rate and time effects into bounding surface (BS) 13 plasticity models. For this purpose, the elasto-viscoplasticity (EVP) overstress theory is combined 14 with bounding surface modeling techniques. The resulting constitutive framework simply requires 15 the definition of an overstress function through which BS models can be augmented without 16 additional constitutive hypotheses. The new formulation differs from existing rate-dependent 17 bounding surface frameworks in that the strain rate is additively decomposed into elastic and 18 viscoplastic parts, much like classical viscoplasticity. Accordingly, the proposed bounding surface 19 elasto-viscoplasticity (BS-EVP) framework is characterized by two attractive features: (1) the rate- 20 independent limit is naturally recovered at low strain rates; (2) the inelastic strain rate depends 21 exclusively on the current state. -
Parameter Identification in Viscoplasticity Using Transitional
Parameter Identification in Viscoplasticity using Transitional Markov Chain Monte Carlo Method Ehsan Adeli and Hermann G. Matthies Institute of Scientific Computing Technische Universitat¨ Braunschweig Braunschweig, Germany [email protected] June 2019 Abstract To evaluate the cyclic behavior under different loading conditions using the kinematic and isotropic hardening theory of steel, a Chaboche viscoplas- tic material model is employed. The parameters of a constitutive model are usually identified by minimization of the difference between model response and experimental data. However, measurement errors and differences in the specimens lead to deviations in the determined parameters. In this article, the Choboche model is used and a stochastic simulation technique is ap- plied to generate artificial data which exhibit the same stochastic behavior as experimental data. Then the model parameters are identified by apply- ing an estimation using Bayes’s theorem. The Transitional Markov Chain Monte Carlo method (TMCMC) is introduced and employed to estimate the model parameters in the Bayesian setting. The uniform distributions of the arXiv:1906.10647v1 [cs.CE] 21 Jun 2019 parameters representing their priors are considered which literally means no knowledge of the parameters is available. Identified parameters are com- pared with the true parameters in the simulation, and the efficiency of the identification method is discussed. In fact, the main purpose of this study is to observe the possibility of identifying the model and hardening parameters of a viscoplastic model as a very high non-linear model with only a surface displacement measurement vector in the Bayesian setting using TMCMC and evaluate the number of measurements needed for a very acceptable es- timation of the uncertain parameters of the model. -
Chapter 11. Elastic and Viscoplastic Properties
NEA/NSC/R(2015)5 Chapter 11. Elastic and viscoplastic properties R.A. Lebensohn Los Alamos National Laboratory, US Abstract In this chapter, we review crystal elasticity and plasticity-based self-consistent theories and apply them to the determination of the effective response of polycrystalline aggregates. These mean-field formulations, which enable the prediction of the mechanical behaviour of polycrystalline aggregates based on the heterogeneous and/or directional properties of their constituent single crystal grains and phases, are ideal tools to establish relationships between microstructure and properties of these materials, ubiquitous among fuels and structural materials for nuclear systems. Introduction Mean-field theories linking microstructure and properties of heterogeneous materials can be used for the development of efficient algorithms for the prediction of the elastic and plastic response of polycrystals. In this chapter, we will review crystal elasticity and crystal plasticity-based self-consistent theories, and show applications of these formulations to the prediction of microstructure-property relations of polycrystalline aggregates. The self-consistent (SC) approximation, one of the most commonly used homogenisation methods to estimate the mechanical response behaviour of polycrystals, was originally proposed by A.V. Hershey [3] for linear elastic materials. For nonlinear aggregates (as those formed by grains deforming in the viscoplastic regime), the several SC approximations that were subsequently proposed differ in the procedure used to linearise the local non-linear mechanical behaviour, but eventually all of them end up making use of the original linear SC theory. In general, SC estimates of the effective behaviour of heterogeneous materials are between the iso-strain upper-bound (i.e., Voigt and Taylor approximations in the elastic and viscoplastic regimes, respectively) and the iso-stress lower-bound (Reuss and Sachs approximations in the elastic and viscoplastic regimes, respectively). -
Microstructural Constitutive Model for Polycrystal Viscoplasticity in Cold and Warm Regimes Based on Continuum Dislocation Dynamics
Microstructural constitutive model for polycrystal viscoplasticity in cold and warm regimes based on continuum dislocation dynamics S. Amir H. Motaman*, Ulrich Prahl Department of Ferrous Metallurgy, RWTH Aachen University, Intzestr. 1, D-52072 Aachen, Germany ARTICLE INFO ABSTRACT Manuscript history: Viscoplastic flow of polycrystalline metallic materials is the result of motion Revised and interaction of dislocations, line defects of the crystalline structure. In the microstructural (physics-based) constitutive model presented in this paper, the main underlying microstructural processes influencing viscoplastic deformation and mechanical properties of metals in cold and warm regimes Keywords: are statistically described by the introduced sets of postulates/axioms for continuum dislocation continuum dislocation dynamics (CDD). Three microstructural (internal) dynamics; state variables (MSVs) are used for statistical quantifications of different microstructural types/species of dislocations by the notion of dislocation density. Considering constitutive modeling; the mobility property of dislocations, they are categorized to mobile and dislocation density; (relatively) immobile dislocations. Mobile dislocations carry the plastic strain thermo-micro-mechanical (rate), while immobile dislocations contribute to plastic hardening. Moreover, modeling; with respect to their arrangement, dislocations are classified to cell and wall polycrystal viscoplasticity; dislocations. Cell dislocations are those that exist inside cells/subgrains, and nonlocal -
Yielding Behaviour of Viscoplastic Materials
J. Ind. Eng. Chem., Vol. 12, No. 5, (2006) 653-662 REVIEW Yielding Behaviour of Viscoplastic Materials C. Tiu†, J. Guo, and P. H. T. Uhlherr Department of Chemical Engineering, Monash University, Clayton 3800, Australia Received September 4, 2006 Abstract: Complex fluids exhibiting a yield stress have extremely variable shear properties ranging from elasto-plastic behaviour below the yield stress to viscous behaviour beyond that. The progressive elastic to plastic transition of viscoplastic materials can be explored by a number of rheological techniques including stress sweep, stress ramp, creep and strain recovery. The non-linear behaviour of such materials under different loading conditions can be investigated using a large amplitude oscillatory shear flow (LAOS) combined with Fourier-Transform (FT) harmonic analysis. Results from these rheological measurements provide a char- acteristic “rheological fingerprint” for complex materials exhibiting yield stress. Keywords: yield stress, viscoplasticity, creep, recovery strain, large amplitude oscillatory shear Introduction responding to the transition between plastic deformation 1) and purely viscous flow [4-6]. Although the yielding Many industrial materials, such as filled polymers, response is conventionally interpreted in terms of a polymer gels, thickeners, foodstuffs, cosmetics, concen- “critical stress”, measurements with highly-filled suspen- trated mineral suspensions, electro-rheological and mag- sions such as ER fluids have shown that it is equally neto-rheological fluids behave rheologically in a manner possible to consider the existence of a critical strain at that varies between elastic solid and viscous liquid any level of stress [7,8]. A fundamental interpretation of depending upon the processing conditions. The exis- this transition with respect to processing conditions is of tence of a “yield stress” is traditionally recognised to be great importance to industrial applications. -
A Viscoplastic Model Including Damage for Argillaceous Rocks Mountaka Souley, K
A viscoplastic model including damage for argillaceous rocks Mountaka Souley, K. Su, Gilles Armand, Mehdi Ghoreychi To cite this version: Mountaka Souley, K. Su, Gilles Armand, Mehdi Ghoreychi. A viscoplastic model including damage for argillaceous rocks. 1. International Symposium on computational geomechanics (COMGEO 2009), Apr 2009, Juan-les-Pins, France. pp.146-157. ineris-00973339 HAL Id: ineris-00973339 https://hal-ineris.archives-ouvertes.fr/ineris-00973339 Submitted on 4 Apr 2014 HAL is a multi-disciplinary open access L’archive ouverte pluridisciplinaire HAL, est archive for the deposit and dissemination of sci- destinée au dépôt et à la diffusion de documents entific research documents, whether they are pub- scientifiques de niveau recherche, publiés ou non, lished or not. The documents may come from émanant des établissements d’enseignement et de teaching and research institutions in France or recherche français ou étrangers, des laboratoires abroad, or from public or private research centers. publics ou privés. A VISCOPLASTIC MODEL INCLUDING DAMAGE FOR ARGILLACEOUS ROCKS M. Souley Institut national de l’environnement industriel et des risques, Nancy, France K. Su Agence nationale de gestion des déchets radioactifs, France. Currently at Total, Pau, France G. Armand Agence nationale de gestion des déchets radioactifs, Bure, France M. Ghoreychi Institut national de l’environnement industriel et des risques, Verneuil, France ABSTRACT: Based on numerous studies of laboratory tests and in-situ observations, a macroscopic viscoplastic