(12) Patent Application Publication (10) Pub. No.: US 2011/0129683 A1 Ahn Et Al
Total Page:16
File Type:pdf, Size:1020Kb
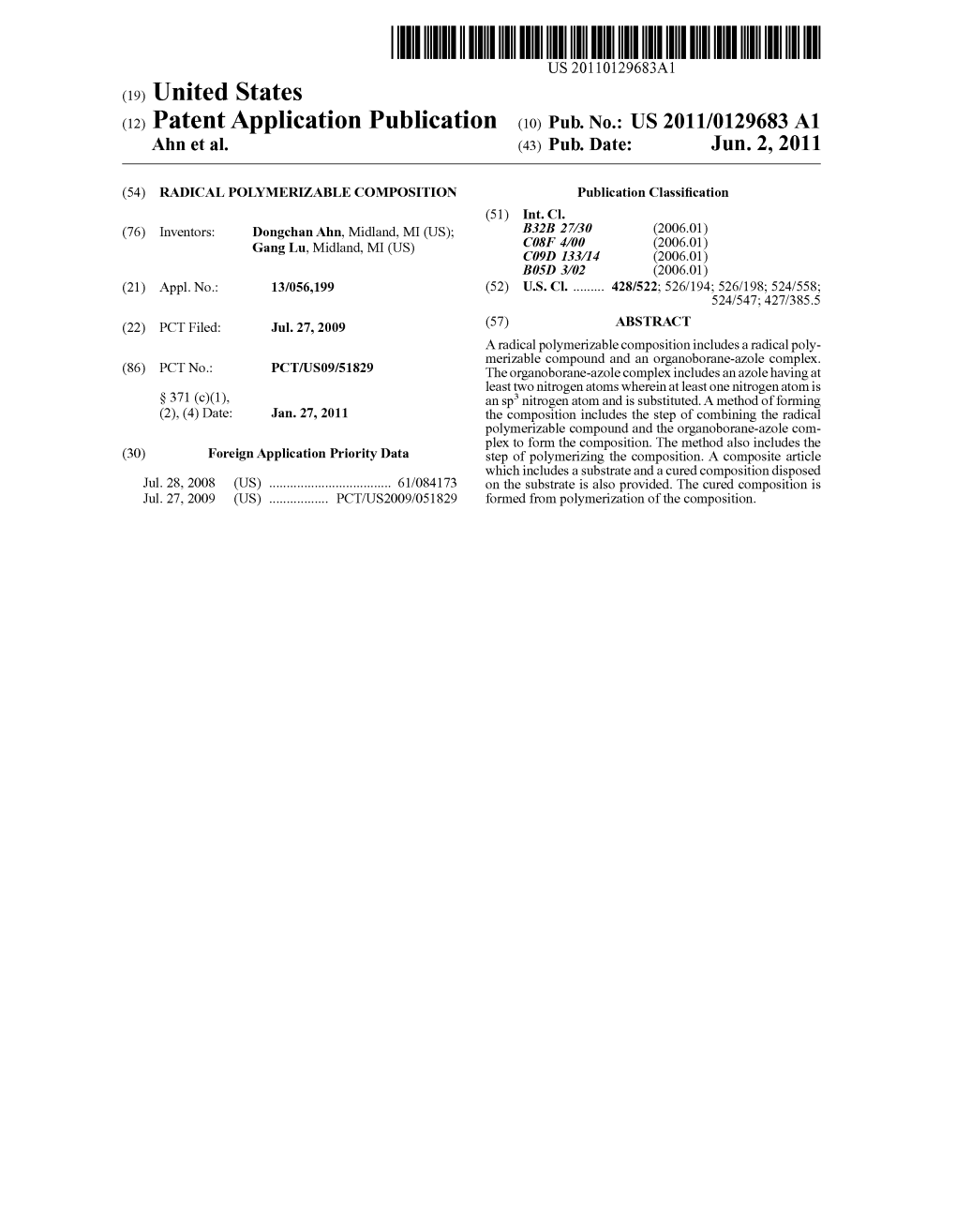
Load more
Recommended publications
-
The Application of Semiempirical Methods in Drug Design
THE APPLICATION OF SEMIEMPIRICAL METHODS IN DRUG DESIGN By MARTIN B. PETERS A DISSERTATION PRESENTED TO THE GRADUATE SCHOOL OF THE UNIVERSITY OF FLORIDA IN PARTIAL FULFILLMENT OF THE REQUIREMENTS FOR THE DEGREE OF DOCTOR OF PHILOSOPHY UNIVERSITY OF FLORIDA 2007 1 c 2007 Martin B. Peters 2 For Jane 3 ACKNOWLEDGMENTS Words cannot describe my Jane. She is everything I can could ask for. She has stood by me even when I left Ireland to pursue my dream of getting my PhD. Thank you honey for your love, support and the sacrifices you have made for us. I thank my mother for always giving me tremendous support and for her words of wisdom and encouragement. I would also like to thank my two brothers, Patrick and Francis, and my two sisters, Marian and Deirdre, for all their encouragement and support. Kennie thank you for giving me the opportunity to work with you; I have truly enjoyed the experience. I would like to express my gratitude to all Merz group members especially Kaushik, Andrew, Ken, Kevin, and Duane for their support and friendship. Also I would like to acknowledge the effort of Mike Weaver who helped by editing this dissertation. 4 TABLE OF CONTENTS page ACKNOWLEDGMENTS ................................. 4 LIST OF TABLES ..................................... 8 LIST OF FIGURES .................................... 11 LIST OF ABBREVIATIONS ............................... 15 ABSTRACT ........................................ 19 CHAPTER 1 INTRODUCTION .................................. 21 2 THEORY AND METHODS ............................. 25 2.1 Receptor-Ligand Binding Free Energy ..................... 28 2.2 Computational Drug Design .......................... 30 2.3 Molecular Mechanics .............................. 32 2.4 Quantum Mechanics .............................. 33 2.5 Ligand Based Drug Design .......................... -
Non-Empirical Calculations on the Electronic Structure of Olefins and Aromatics
NON-EMPIRICAL CALCULATIONS ON THE ELECTRONIC STRUCTURE OF OLEFINS AND AROMATICS by Robert H. Findlay, B.Sc. Thesis presented for the Degree of Doctor of philosophy University of Edinburgh December 1973 U N /),, cb CIV 3 ACKNOWLEDGEMENTS I Wish to express my gratitude to Dr. M.H. Palmer for his advice and encouragement during this period of study. I should also like to thank Professor J.I.G. Cadogan and Professor N. Campbell for the provision of facilities, and the Carnegie Institute for the Universities of Scotland for a Research Scholarship. SUMMARY Non-empirical, self-consistent field, molecular orbital calculations, with the atomic orbitals represented by linear combinations of Gaussian-type functions have been carried out on the ground state electronic structures of some nitrogen-, oxygen-, sulphur- and phosphorus-containing heterocycles. Some olefins and olefin derivatives have also been studied. Calculated values of properties have been compared with the appropriate experimental quantities, and in most cases the agreement is good, with linear relationships being established; these are found to have very small standard deviations. Extensions to molecules for which there is no experimental data have been made. In many cases it has been iôtrnd possible to relate the molecular orbitals to the simplest member of a series, or to the hydrocarbon analogue. Predictions of the preferred geometry of selected molecules have been made; these have been used to predict inversion barriers and reaction mechanisms. / / The extent of d-orbital participation in molecules containing second row atoms has been investigated and found to be of trivial importance except in molecules containing high valence states of the second row atoms. -
Isocyclicc Com- Poundscompounds
The Chemistry of Heterocycles Structure, Reactions, Syntheses, and Applications Mohammad Jafarzadeh Faculty of Chemistry, Razi University The Chemistry of Heterocycles, (Second Edition). By Theophil Eicher and Siegfried Hauptmann, Wiley-VCH Veriag GmbH, 2003 1 1 The Structure of Heterocyclic Compounds 1. The Structure of Heterocyclic Compounds • Molecules are defined by the type and number of atoms as well as by the covalent bonding within Mosthemt chemica. Therel arecompoundtwo mains consistypes tof ostructuref molecules: . The classification of such chemical compounds is base— Thed onatoms the structurform ae chainof thes-ealiphatic molecules(acyclic), whichcompounds is defined by the type and number of atoms as well as b—y thThee covalenatomst formbondina ringg withi- cyclicn themcompounds. There are two main types of structure: — The a t o m s form a chain - aliphatic (acyclic) compounds — The a t o m s form a ring - cyclic compounds CycliCyclicc compoundcompoundss iinn whicwhichh ththee rinringg isis madmadee upup ofof atomatomss ofof ononee elemenelementt onlonlyy areare callecalledd isocycliisocyclicc com- poundscompounds. If th.eIf rintheg consistring consistss of C-atomof C-atomss only,only, then thenwe speawe speakk of a carbocycliof a carbocyclicc compoundcompound,, e.g.: e.g.: NMe? O (4 - dimethylaminophenyl) pentazole cyclopenta -1,3 - diene isocyclic isocyclic und carbocyclic 2 Cyclic compounds with at least two different atoms in the ring (as ring atoms or members of the ring) are known as heterocyclic compounds. The ring itself is called a heterocycle. If the ring contains no C-atom, then we speak of an inorganic heterocycle, e.g.: MeO 2,4 - bis (4 - methoxyphenyl) - 1,3 - dithiadiphosphetan -2,4 - disulfide borazine (Lawesson - Reagent) If at least one ring atom is a C-atom, then the molecule is an organic heterocyclic compound. -
Complexes of CO2 with the Azoles: Tetrel Bonds, Hydrogen Bonds and Other Secondary Interactions
molecules Article Complexes of CO2 with the Azoles: Tetrel Bonds, Hydrogen Bonds and Other Secondary Interactions Janet E. Del Bene 1,* ID , José Elguero 2 and Ibon Alkorta 2,* ID 1 Department of Chemistry, Youngstown State University, Youngstown, OH 44555, USA 2 Instituto de Química Médica (IQM-CSIC), Juan de la Cierva, 3, E-28006 Madrid, Spain; [email protected] * Correspondence: [email protected] (J.E.D.B.); [email protected] (I.A.); Tel.: +1-330-609-5593 (J.E.D.B.); +34-91-562-29-00 (I.A.) Academic Editor: Steve Scheiner Received: 31 March 2018; Accepted: 11 April 2018; Published: 14 April 2018 Abstract: Ab initio MP2/aug’-cc-pVTZ calculations have been performed to investigate the complexes of CO2 with the azoles pyrrole, pyrazole, imidazole, 1,2,3- and 1,2,4-triazole, tetrazole and pentazole. Three types of complexes have been found on the CO2:azole potential surfaces. These include ten complexes stabilized by tetrel bonds that have the azole molecule in the symmetry plane of the complex; seven tetrel-bonded complexes in which the CO2 molecule is perpendicular to the symmetry plane; and four hydrogen-bonded complexes. Eight of the planar complexes are stabilized by Nx···C tetrel bonds and by a secondary interaction involving an adjacent Ny-H bond and an O atom of CO2. The seven perpendicular CO2:azole complexes form between CO2 and two adjacent N atoms of the ring, both of which are electron-pair donors. In three of the four hydrogen-bonded complexes, the proton-donor Nz-H bond of the ring is bonded to two C-H bonds, thereby precluding the planar and perpendicular complexes. -
Synthesis and Characterization of Metal Complexes Containing
Wayne State University Wayne State University Dissertations 1-1-2010 Synthesis And Characterization Of Metal Complexes Containing Tetrazolate, Poly(tetrazolyl)borate, And Aryl Pentazole Ligands As High Energy Density Materials Dongmei Lu Wayne State University Follow this and additional works at: http://digitalcommons.wayne.edu/oa_dissertations Part of the Inorganic Chemistry Commons Recommended Citation Lu, Dongmei, "Synthesis And Characterization Of Metal Complexes Containing Tetrazolate, Poly(tetrazolyl)borate, And Aryl Pentazole Ligands As High Energy Density Materials" (2010). Wayne State University Dissertations. Paper 68. This Open Access Dissertation is brought to you for free and open access by DigitalCommons@WayneState. It has been accepted for inclusion in Wayne State University Dissertations by an authorized administrator of DigitalCommons@WayneState. SYNTHESIS AND CHARACTERIZATION OF METAL COMPLEXES CONTAINING TETRAZOLATE, POLY(TETRAZOLYL)BORATE, AND ARYL PENTAZOLE LIGANDS AS HIGH ENERGY DENSITY MATERIALS by DONGMEI LU DISSERTATION Submitted to the Graduate School of Wayne State University, Detroit, Michigan in partial fulfillment of the requirements for the degree of DOCTOR OF PHILOSOPHY 2010 MAJOR: CHEMISTRY (Inorganic) Approved by: ______________________________ Advisor Date ______________________________ ______________________________ ______________________________ DEDICATION To my parents ii ACKNOWLEDGMENTS I would like to express my sincere gratitude to my advisor, Professor Charles H. Winter, for his guidance and support though the years at Wayne State University. I am grateful to my committee members, Professor Stephanie L. Brock, Professor Jin K. Cha, and Professor Mark Ming-Cheng Cheng, for reviewing my thesis and giving valuable comments and suggestions. I would like to thank Dr. Mary Jane Heeg for determining all the crystal structures, and Dr. Bashar Ksebati for his help with the NMR experiments. -
Glossary of the Key Notions in Bionics and Beyond
Glossary of the key notions in Bionics and beyond Created by XMLmind XSL-FO Converter. Glossary of the key notions in Bionics and beyond Publication date PPKE ITK, Budapest, 2011 Copyright © 2011 Pázmány Péter Catholic University Created by XMLmind XSL-FO Converter. Table of Contents A. Glossary of the key notions in Bionics and beyond ....................................................................... 1 Preface ................................................................................................................................................ ii 1. Resources ........................................................................................................................................ 4 2. Glossary .......................................................................................................................................... 5 1. 1 ............................................................................................................................................ 5 2. 2 ............................................................................................................................................ 5 3. 6 ............................................................................................................................................ 5 4. A ............................................................................................................................................ 5 5. B ......................................................................................................................................... -
Synthesis of Polyheteroatomic Heterocycles: Relevance of Microwave-Assisted Reactions
Synthesis of polyheteroatomic heterocycles: relevance of microwave-assisted reactions Daniele Canestrari Dissertação para obtenção do Grau de Mestre em Química Orientadores: Prof. Pedro Paulo de Lacerda e Oliveira Santos Prof. Enrico Marcantoni Júri Presidente: Profª. Maria Matilde Soares Duarte Marques Vogais: Prof. Pedro Paulo de Lacerda e Oliveira Santos Prof. Corrado Bacchiochi Doutora Alexandra Maria Moita Antunes Maio de 2014 Abstract Heterocyclic structures, components of a large number of molecules, have been studied since the mid- 1800s due to their wide occurrence in nature, such as in the Heme and Chlorophyll A, and the discovery of their usefulness in organic chemistry, creating an interesting new branch, which continues today. From the first applications of simple heterocycles in main fields of research, such as in medicine, pharmaceutical, agrochemical and energy materials, polyheteroatomic heterocycles have achieved a remarkable position in the development of new products for clinical use with most advantageous features that allow different interactions with the biological target, not always possible with a simple heterocyclic ring. And this is the real aim of this thesis, based on a new research project on particular polyheteroatomic heterocyclic systems, namely 1,2,5-oxadiazoles, also called furazans, five-membered rings likely to be useful for the architectural structure of new drugs. Furthermore, this work wants to propose possible innovative methods to synthesize furazans from acyclic substrates in order to obtain specific heterocycles with particular substituents on the ring. Even more importantly, our attention has focused on the possibility to exploit microwave-assisted organic synthesis (MAOS) for its ability to optimize strategies both from the point of view of the time and of the yield. -
Pentazole-Based Energetic Ionic Liquids:•› a Computational Study
View metadata, citation and similar papers at core.ac.uk brought to you by CORE provided by Digital Repository @ Iowa State University Chemistry Publications Chemistry 1-2007 Pentazole-Based Energetic Ionic Liquids: A Computational Study Ian S. O. Pimienta Iowa State University Sherrie Elzey Iowa State University Jerry A. Boatz Air Force Research Laboratory Mark S. Gordon Iowa State University, [email protected] Follow this and additional works at: http://lib.dr.iastate.edu/chem_pubs Part of the Chemistry Commons The ompc lete bibliographic information for this item can be found at http://lib.dr.iastate.edu/ chem_pubs/491. For information on how to cite this item, please visit http://lib.dr.iastate.edu/ howtocite.html. This Article is brought to you for free and open access by the Chemistry at Iowa State University Digital Repository. It has been accepted for inclusion in Chemistry Publications by an authorized administrator of Iowa State University Digital Repository. For more information, please contact [email protected]. Pentazole-Based Energetic Ionic Liquids: A Computational Study Abstract The trs uctures of protonated pentazole cations (RN5H+), oxygen-containing anions such as N(NO2)2-, NO3-, and ClO4- and the corresponding ion pairs are investigated by ab initio quantum chemistry calculations. The ts ability of the pentazole cation is explored by examining the decomposition pathways of several monosubstituted cations (RN5H+) to yield N2 and the corresponding azidinium cation. The heats of formation of these cations, which are based on isodesmic (bond-type conserving) reactions, are calculated. The proton-transfer reaction from the cation to the anion is investigated. -
Excipients USA, Undesired Substances
To whom it may concern Dr. Gabriele Müller Director Quality MEGGLE USA Date of issue: 08.02.2021 Page 1/2 Doc.-No. EIP-0065 -USA Revision 5 Undesired Substances MEGGLE Products: - Lactose Monohydrate (USP-NF / Ph. Eur. / JP): GranuLac® 70 US, GranuLac® 140 US, GranuLac® 200 US - Anhydrous Lactose (USP-NF / Ph. Eur. / JP): DuraLac® H The mentioned substances mentioned in the list on page 2 are neither used as ingredients and technical aids nor are contained in ingredients or technical aids as intentionally added substances. Manufacturing includes refining whereby processing aids (activated carbon and inorganic filter auxiliaries) are added to a hot solution of the unrefined lactose. With cooling, the desired crystals grow and the regular structure of the crystal tends to favour the desired material and exclude other kinds of particles and impurities. Thus, refining is a purification process leading to a higher purity. Best regards MEGGLE USA inc. Dr. Gabriele Müller MEGGLE USA Inc., 592 Route 22, Suite 2B, Pawling, NY 12564, USA Telephone +1 845 289 0264, [email protected] www.meggle-pharma.com Date of issue: 08.02.2021 Page 2/2 Doc.-No. EIP-0065 -USA Revision 5 Undesired Substance1 List Alkyl phenols and their ethoxylates Flavourings, perfumes Phenylalanine Amines Flavouring substances2 Phthalates Antioxidants Formaldehyde and its donor substances Polybrominated Diphenyl Ethers Asbestos Fruits and vegetables, all types Polychlorinated Biphenyls Azo dyes Fumaric acid and its esters Polychlorinated Phenoxyphenols Azoles3 Fungi -
Crystalline Hydro-Nitrogens at High Pressure
Pentazole and Ammonium Pentazolate: Crystalline Hydro-Nitrogens at High Pressure Brad A. Steele and Ivan I. Oleynik∗ Department of Physics, University of South Florida, 4202 E. Fowler Ave., Tampa, FL 33620 E-mail: [email protected] Abstract Two new crystalline compounds, pentazole (N5H) and ammonium pentazolate (NH4)(N5), both featuring cyclo-N5− are discovered using first principles evolution- ary search of the nitrogen-rich portion of the hydro-nitrogen binary phase diagram (N H , x y) at high pressures. Both crystals consist of the pentazolate N− anion x y ≥ 5 + + and ammonium NH4 or hydrogen H cations. These two crystals are predicted to be thermodynamically stable at pressures above 30 GPa for (NH4)(N5) and 50 GPa for pentazole N5H. The chemical transformation of ammonium azide (NH4)(N3) mixed with di-nitrogen (N2) to ammonium pentazolate (NH4)(N5) is predicted to become energetically favorable above 12.5 GPa. To assist in identification of newly synthesized compounds in future experiments, the Raman spectra of both crystals are calculated and mode assignments are made as a function of pressure up to 75 GPa. arXiv:1702.04326v1 [cond-mat.mtrl-sci] 14 Feb 2017 Introduction Pentazole N5H, a hydro-nitrogen molecule containing all-nitrogen aromatic ring N5, has been in the focus of intensive experimental efforts of synthetic chemists for at least a century1–4. 1 Although theory predicted its existence as a metastable species with a local minimum on the potential energy surface confined by a large activation barrier5, this planar pentagon of N atoms connected to one H atom is short-lived in the gas phase, making the synthesis of this last member of azole series very difficult6–8. -
NBO Applications, 2008
NBO 2008 (Jan-Dec) - 910 references Compiled by Emily Wixson; Updated by Ariel Neff 4/16/13 Adalsteinsson, H.; Debusschere, B. J.; Long, K. R.; Najm, H. N. Components for atomistic-to-continuum multiscale modeling of flow in micro- and nanofluidic systems Scientific Programming, (16): 297-313 2008. Adcock, W.; Trout, N. A. Diastereofacial selectivity in some 4-substituted (X) 2-adamantyl derivatives: electronic versus steric effects Journal of Physical Organic Chemistry, (21): 68-72 2008. Agapito, F.; Nunes, P. A.; Costa Cabral, B. J.; Borges dos Santos, R. A.; Martinho Simoes, J. A. Energetic differences between the five- and six-membered ring hydrocarbons: Strain energies in the parent and radical molecules Journal of Organic Chemistry, (73): 6213-6223 2008. Aguilar-Castro, L.; Tlahuextl, M.; Mendoza-Huizar, L. H.; Tapia-Benavides, A. R.; Tlahuext, H. Hydrogen bond studies in substituted N-(2-hydroxyphenyl)-2-[(4- methylbenzenesulfonyl)amino]acetamides Arkivoc: 210-226 2008. Alajarin, M.; Cabrera, J.; Pastor, A.; Sanchez-Andrada, P.; Bautista, D. Polar hetero-Diels-alder reactions of 4-alkenylthiazoles with 1,2,4-triazoline-3,5-diones: An experimental and computational study Journal of Organic Chemistry, (73): 963-973 2008. Albertin, G.; Antoniutti, S.; Baldan, D.; Castro, J.; Garcia-Fontan, S. Preparation of benzyl azide complexes of iridium(III) Inorganic Chemistry, (47): 742-748 2008. Alcoba, D. R.; Ona, O. Determination of energies and electronic densities of functional groups according to partitionings in the physical space Journal of Physical Chemistry A, (112): 10023-10028 2008. Alia, J. D.; Vlaisavljevich, B. Prediction of molecular properties including symmetry from quantum-based molecular structural formulas, VIF Journal of Physical Chemistry A, (112): 9784-9795 2008. -
The Synthesis and Characterisation of Halogen and Nitro Phenyl Azide
Dissertation zur Erlangung des Dokorgrades der Fakultät für Chemie und Pharmazie der Ludwig-Maximilans-Universität München The synthesis and characterisation of halogen and nitro phenyl azide derivatives as highly energetic materials. von David Adam aus Glasgow , Schottland 2001 Index Acknowledgements 1 Abstract 3 1. Introduction 4 1.1 Azides 4 1.2 Nitro compounds 13 1.3 Nitrocarbons 16 1.4 Explosives 18 1.5 Theoretical Calculations 20 1.6 Pentazoles 23 2 Halogen substitued phenyl azides 27 2.1 2,4,6-tribromophenyl azide 27 2.2 2,4,6-trichlorophenyl azide 35 2.3 2,5,6-trichlorophenyl azide 42 2.4 2,4-dibromophenyl azide 43 2.5 2,4-dichlorophenyl azide 44 2.6 2,4,6-trifluorophenyl azide 44 2.7 2,3,4,5,6-pentafluorophenyl azide 47 2.8 2,6-diiodo-4-nitrophenyl azide 50 2.9 2,3,4,5,6-pentachlorophenyl azide 59 3. Nitro compounds 65 3.1 o-nitrophenyl azide 65 3.2 m-nitrophenyl azide 68 3.3 2,4-dinitrophenyl azide 70 3.4 2,4,6-trintrophenyl azide 72 3.5 1,3,5-triazido-2,4-dinitrobenzene 94 3.6 1,3,5-triazido-2,4,6-trinitrobenzene 100 3.7 hexakis (azidomethyl) benzene. 106 3.8 hexakis (methylnitrate) benzene 108 4. Decomposition and explosion experiments 111 4.1 Thermal decomposition of TNMA , DNTA and TNTA 111 4.2 Computational Aspects 118 4.3 Thermal decomposition of halogen substituted phenyl azides 121 4.4 Thermal decomposition of hexakis (azidomethyl) benzene 122 4.5 Drophammer Tests of TNMA, DNTA and TNTA 125 4.6 Calculation of the detonation velocity from molecular formula and structure for TNMA , DNTA and TNTA 133 4.7 Calculation of the detonation velocity from molecular formula and structure for a series of azido and nitro substituted benzenes 135 5 Calculation of compounds of the type C6 (NO2)6-n (N3)n 138 5.1 Structural discussion 144 5.2 Molecular structures 145 6.