Mechanised Thinning with a Waratah Grapple Harvester and Timberjack Forwarder
Total Page:16
File Type:pdf, Size:1020Kb
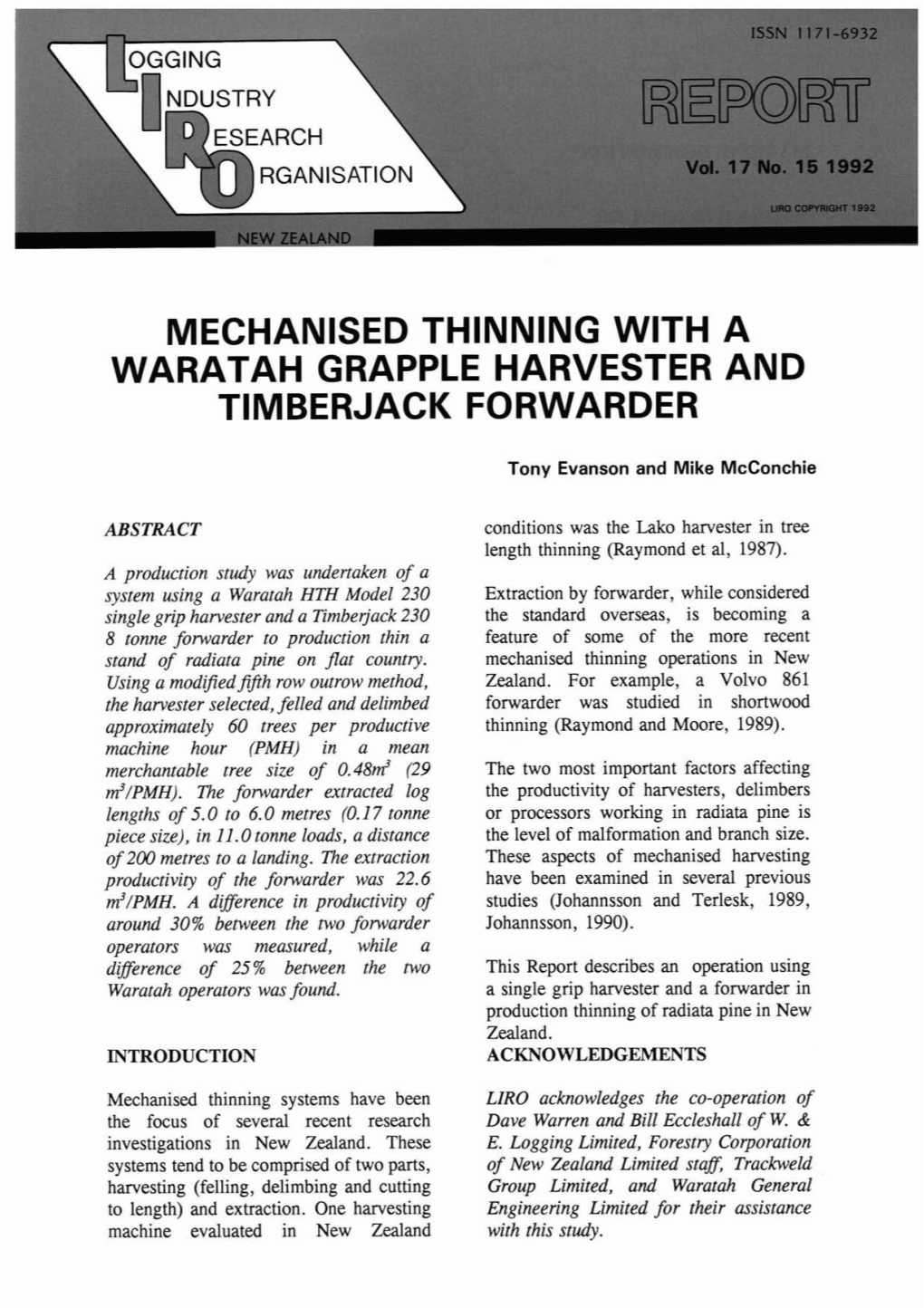
Load more
Recommended publications
-
2001 Pacific Logging Congress • in the Woods • Presidents Message •
2001 PACIFIC LOGGING CONGRESS • IN THE WOODS • PRESIDENTS MESSAGE • at $20 US per person or a 3-day pass at Greetings! $50 US per person. So register now and you will receive up-to-the-minute It's been four years since the last information on the 2001 "In the Pacific Logging Congress "In-The- Woods" show program and activities. Woods" Show in Washington State. On-site registration will be available at Mark your calendars for September the bus parking area. 19-22, 2001 for the 4th "In the Woods" Show passes include: show, which will be held on Longview •Access to all equipment demonstra- Fibre Timberland, 35 miles west of tion areas and exhibitor displays. downtown Portland on Hwy 26. The •Tickets to Thursday Hosted Benson Hotel will serve as the head- Hospitality events. quarter hotel. To make room reserva- You may also purchase tickets to tions call 888-523-6766, be sure to let the Reception and Banquet on Friday them know you are with the Pacific evening. Logging Congress group. To receive Please consider a contribution to the discount rate, please make reserva- Joel Olson the Pacific Logging Congress tions before August 18. Education Fund. PLC will host an The Pacific Logging Congress live Education Day on September 19th, "In-The-Woods" Show, is the largest Congress, "In-The-Woods" Show, is by inviting over 3,000 students and teach- active logging equipment show in the registration only. You must have a ers from Portland area schools to United States. Leading product lines paid ticket to attend. -
TOLL FREE: 1-800-669-5613 Matic Ad Taker Will Take Your Ads
Want To Place Your Classified Ad In IronWorks? Call 334-669-7837, 1-800-669-5613 or Email: [email protected] IRONWORKS RATES; Space available by column inch only, one inch minimum. Rate is $50 per inch, special typeset - ting, borders, photo inclusion, blind ads, $10 extra each. Deadlines: By mail, 15th of month prior to publication. Place your ad toll-free 24 hours a day from anywhere in the USA (except Alaska and Hawaii) 1-800-669-5613 ask for IRONWORKS Classifieds 8:30-5 pm CST. After business hours our auto - TOLL FREE: 1-800-669-5613 matic ad taker will take your ads. 9 0 2 ARMY 6X6 TRUCKS 6 1 2 ⁄2 Ton # 5 Ton # 10 Ton EQUIPMENT FINANCING IF YOU ARE A LOGGER, THEN THIS IS Pull Out Trucks YOUR PARTS RESOURCE CENTER • Preferred Good Credit Plans • Rough Credit Plans CHECK US OUT ON THE WEB. WE HAVE QUALITY USED (turned down, tax liens, bankruptcies) Loader Chassis TIGERCAT, JOHN DEERE, CAT, HYDRO-AX & PRENTICE PARTS AT AFFORDABLE PRICES. • Purchases • Refinance • Start-up Business Complete ** CAT 525C: 165-5509 Fuel Tank Assembly .$500 ** John Deere 648GIII: AT367621 DF Grapple - • Loans Against Military Truck Your Existing Equipment Boom .....................................................$3,000 Parts Inventory for QUICK CASH! ** Tigercat 720 Series: 9488B Dual Motor Trans 2-Hour Approvals! Gearbox ...........................................$3,000/Exc Low Monthly Payments Little or No Down Payments ** Tigercat 620: BH530 32" Suction Fan .......$250 ALL WHEEL DRIVE 15 Years In Business ** Tigercat 5000: 3112D Drive Shaft Spindle CALL NOW .......................................................$1,000/Exc 985-875-7373 MEMPHIS EQUIPMENT Fax: 985-867-1188 CONTACT: Email: [email protected] 766 S. -
Growinggoldsummer05.Pdf
KENTUCKY’S GROWING GOLD A PUBLICATION OF: KENTUCKY DIVISION OF FORESTRY FRANKFORT, KENTUCKY 40601 A SERVICE TO KENTUCKY’S FOREST PRODUCTS INDUSTRY AND TIMBERLAND OWNERS VOL. XLV, NO. 3 EDITOR: CHRISTOPHER G. NEVINS SUMMER 2005 THE FOLLOWING MARKED TIMBER FOR SALE IS A LISTING OF TIMBER MARKED BY THE KENTUCKY DIVISION OF FORESTRY FOR PRIVATE WOODLAND OWNERS. THE LIST WAS CURRENT AS OF DATE OF SUBMISSION TO THE PRINTERS. IF YOU WANT FURTHER INFORMATION ON MARKED TIMBER, PLEASE REFER TO THE "COUNTY GUIDE TO DISTRICT FORESTERS' OFFICES" INSIDE THE BACK COVER AND CALL THE APPROPRIATE DISTRICT FORESTER. MARKED TIMBER FOR SALE LOCATION SPECIES AND VOLUME CONTACT CENTRAL DISTRICT TRACT #1 ALLEN CO. RED OAK 15231 BEECH 2661 FRED OLIVER LOCATED NORTH OF YELLOW POPLAR 6115 MISC. OAKS 580 1437 LONGVIEW DR. SCOTTSVILLE, APPROX. 2 WHITE OAK 3881 CHERRY 248 BOWLING GREEN, KY 42104 MILES FROM JCT. OF HWY HARD MAPLE 3315 ASH 164 270-842-7137 31E &HWY 101, ON NORTH HICKORY 2985 BLACKGUM 120 SIDE OF HWY. 1332. TOTAL BF (DOYLE) 35300 29 ACRES 128 TREES MARKED TRACT #2 5 ACRES LOBLOLLY PINE 31340 119 TREES MARKED HART CO. YELLOW POPLAR 20249 SCARLET/SHINGLE OAK 2712 MITCHELL WADDELL LOCATED 10 MILES WEST RED OAK 14296 ASH 1894 3095 ROSEBURG RD. OF MUNFORDVILLE, ON WHITE OAK 9874 WALNUT/CHERRY 1468 CUB RUN, KY 42729 THE SOUTH SIDE OF HICKORY 4405 CHINKAPIN OAK 604 270-524-0113 HWY 88. HARD MAPLE 3880 MISCELLANEOUS 472 38 ACRES BEECH 3387 TOTAL BF (DOYLE) 63241 327 TREES MARKED www.kentuckyunbridledspirit.com 1 OCATION SPECIES AND VOLUME CONTACT CENTRAL DISTRICT NELSON CO. -
Mechanization in Short Rotation, Intensive Culture Forestry"; 1994 March 1-3; Mobile, AL
Proceedings of the IEA/BA Task IX, Activity 1 International Conference Mobile, Alabama USA March 1-3, 1994 Edited by Bryce J. Stokes and Timothy P. McDonald U.S.D.A. Forest Service DeVall Drive Auburn University, Alabama 36849 Hosted by Scott Paper Company Sponsored by IEA/BA Task IX, Activity 1 Electric Power Research Institute Oak Ridge National Laboratory U.S. Department of Energy Southern Forest Engineering Center Auburn University Southern Forest Experiment Station U.S.D.A. Forest Service Southeastern Regional Biomass Energy Program Demonstration Sponsored by Morbark Industries Table Of Contents Foreward Session I (Moderator - Jim Decosmo) Industrial short rotation intensive culture operations,Thomas H. Morgan, Jr Harvesting costs and utilization of hardwood plantations, Timothy P. McDonald and Bryce J. Stokes Short rotation forestry in loblolly pine, Alan P. Bruce Utilization of cottonwood plantations, C. Jeffrey Portwood Stand Establishment and Culture of Hybrid Poplars, Charles E. Kaiser, Donald E. Rice, and Kirk R. Wallace Development of a flail harvester for small diameter brush and coppiced trees to produce energy/chemical feedstock, Robert A. McLauchlan, Andrew Conkey, Greg Scherer, Peter Felker, and Stan Brown Mechanization of short rotation intensive-culture wood crops, William B. Stuart Growing Eucalyptus for Pulp and Energy, James A. Rydelius Session II (Moderator - Sam Foster) Management of irrigated hybrid poplar plantations in the Pacific Northwest, Charles A. Wierman Mechanization potential for industrial-scale fiber and energy plantations, Bruce Hartsough and Randall Richter Establishing and tending poplar plantations in the North-Central U.S., Dan Netzer and Ed Ward Hansen Silvicultural techniques for short rotation Eucalyptus plantations in Brazil, Ken McNabb The effects of whole tree harvesting on fuel quality and coppicing ability of SRIC willow crops, Juha Nurmi and Jyrki Hytönen Utilization of short rotation forestry from an effluent disposal scheme, Hamish T. -
LOGGING and LOG TRANSPORT in TROPICAL HIGH FOREST Log Extraction in Waterlogged Areas by Means of Blasted Ditches, Surinam
rv0D AND AGRICULTURE ORGANIZATION OF THE UNITED NATIONS As recorded information on methods, production and costs of logging and transport in the developing world - and especially in tropical high forest - is scarce, one of the main purposes· of this manual is to focus attention on the analytic approach needed to quantify output and costs data. An important element of tropical high forest logging is examined: the influence of physical and economic conditions on production. Production and cost data are presented, as far as available information permits, for the most commonly used logging methods adaptable to this. particular situation. LOGGING AND LOG TRANSPORT IN TROPICAL HIGH FOREST Log extraction in waterlogged areas by means of blasted ditches, Surinam. (Bubberman/Vink) FAO Forestry Development Paper No. 18 LOGGING AND LOG TRANSPORT IN TROPICAL HIGH FOREST A manual on production and costs FOOD AND AGRICULTURE ORGANIZATION OF THE UNITED NATIONS Rome, 1974 The copyright in this book is vested in the Food and Agri culture Organization of the United Nations. The book may not be translated, nor may it be reproduced, in whole or in part, by any method or process, without written permission from the copyright holder. Applications for such permis sion, with a statement of the purpose and extent of the reproduction desired, should be addressed to The Director, Publications Division, Food and Agriculture Organization of the United Nations, Via delle Terme di Caracalla, Rome, Italy. @ FAO 1974 Printed in Italy CONTENTS Introduction . 1 PURPOSE OF THE STUDY 1 SOURCES OF INFORMATION 2 Field studies - Questionnaires - Literature 1. Theoretical framework . 4 SELECTION OF FACTORS AFFECTING PRODUCTION 4 LIMITATIONS OF THE STUDY . -
Bailey's Logger Wear $17999 $19999
baileysonline.com 1-800-322-4539 Industrial Division 1-888-465-8227 7 am through 5 pm PST Your Complete Choice for Work Gear, Logging, Urban Forest Management & Tree Care. ¡Operador en Español disponible: 1-888-322-1215! Sale Ends June 9, 2020 Bailey’s Logger Wear Wild Ass Short Sleeve Classic Hickory Shirt Jean Sale! As Low As SALE From $ 99 $ 99 25 Item No 28 HSC 92 Reg From Reg From $3399 $2999 See page 28 for Complete Wild Ass Clothing Specials! Item No HSC 94 See page 26 for more details! Designed by Professional Arborists Boot Sale! Light • Comfortable • Durable Red Dawg is Bailey’s Only exclusive custom line of $ 99 premium work boots. 199 SALE From Smart asymmetrical design $ 99 offers extended protection on 179 the left side of legs, where Meets Reg From most injuries occur. ASTM Std.F-1897-2014 and $ 99 199 CAN/BNQ 1923-450-M91. UL Certified. See page 27 for more details! Item No BWP AP Available Only at Bailey’s Husqvarna Chainsaws Farm & Ranch Husqvarna is our top selling brand of chainsaws, and many chainsaw users will not run anything else. Husqvarna farm and ranch chainsaws have many of the 50cc Chainsaw with same features as their professional "XP" chainsaw line, without the big price tag. 445 II E-Series 16” or 18” Bar & Chain If you are a first time user, this is a great line of chainsaws to start with. We offer The 445 II E-Series is a powerful all around saw with many professional each of these Husqvarna chainsaw models in a variety of options, including features. -
Mechanised Harvesting and Processing
This Best Practice Guide is being reviewed. The future of Best Practice Guides will be decided during 2015. Best practice guidelines for Mechanised Harvesting and Processing V ision, knowledge, performance competenz.org.nz He Mihi Nga pakiaka ki te Rawhiti. Roots to the East. Nga pakiaka ki te Raki. Roots to the North. Nga pakiaka ki te Uru. Roots to the West. Nga pakiaka ki te Tonga. Roots to the South. Nau mai, Haere mai We greet you and welcome you. ki te Waonui~ o Tane To the forest world of Tane. Whaia te huarahi, Pursue the path, o te Aka Matua, of the climbing vine, i runga, I te poutama on the stairway, o te matauranga.~ of learning. Kia rongo ai koe So that you will feel, te mahana o te rangimarie.~ the inner warmth of peace. Ka kaha ai koe, Then you will be able, ki te tu~ whakaiti, to stand humbler, ki te tu~ whakahi.~ Yet stand proud. Kia Kaha, kia manawanui~ Be strong, be steadfast. Tena koutou katoa. First edition December 2002 Revised edition January 2005 This Best Practice Guideline is to be used as a guide to mechanical harvesting and processing. It does not supersede legislation in any jurisdiction or the recommendations of equipment manufacturers. FITEC believes that the information in the guideline is accurate and reliable; however, FITEC notes that conditions vary greatly from one geographical area to another; that a greater variety of equipment and techniques are currently in use; and other (or additional) measures may be appropriate in a given situation. Other Best Practice Guidelines included in the series: • Cable -
Free Loan Program
Videos of Life NORTHEAST HISTORIC in New England FILM FREE LOAN PROGRAM Members of Northeast Historic Film Borrow from our FREE loan collection of Videos of Life in New England. You can borrow up to three videos at a time and pay only $5 per shipment for postage. Pay by check, money order, Discover, Visa or Mastercard using the form on page 27. Also, please provide an alternate selection in case your rst choice is out. To join or borrow videos please call 800.639.1636, email: nhf@old lm.org , write Northeast Historic Film, PO Box 900, Bucksport, ME 04416 or to save on postage, stop by our o ce at 85 Main Street in Bucksport. www.old lm.org and click on “Borrow” to view this catalog online. Public Performance Certain videos are o ered as a reference service. Where possible, public performance rights are included. Please be sure to check each video’s status: PERF means public performance rights are included. Where there is no PERF, the video is for home use only, or face-to-face classroom instruction. We have also indicated PERF videos by bolding the title in the index. No admission may be charged for events where Videos of Life in New England are being shown. If you have a date in mind, call NHF at 207.469.0924 to ensure availability. Available Format Please check the description of each video for available format. Titles are available in DVD or VHS. Teachers and students should note the special listing of titles available on mini-dv for student and class projects. -
Logging Our Roots Are Deeply Planted in Repair
Logging Our roots are deeply planted in repair Logging and Forestry means demanding conditions for hydraulic seals, and Hercules has met those demands for decades with superior sealing products, customer service and technical assistance. Logging is a complex industry, with a wide array of heavy-duty needs. Hercules’ vast product offering exclusively for logging and for- estry includes seals, seal kits and cylinders for the various logging environments such as log loading, harvest- ing and hauling. Our products are field tested to assure maximum continuous performance as they withstand severe heat, pres- sure, speeds, friction and more in numerous logging equipment and environments. Your needs are unique, so count on Hercules’ expertise for the best custom solutions and products. For more information, quick quotations, expert consultation and responsive customer service CALL 800.777.5617 ORDER ONLINE www.HerculesUS.com BARKO CYLINDER REPAIR KITS CATERPILLAR (CONTINUED) Various Kits TRACK SKIDDER / GRAPPLE SKIDDERS MODELS 517, 527 BELL CYLINDER REPAIR KITS TRACK SKIDDER / GRAPPLE SKIDDERS TREE HARVESTERS MODELS 517, 527 MODELS SUPER T and ULTRA T TREE HARVESTERS CASE CYLINDER REPAIR KITS MODELS 518,550, 550B, 560B, 570, 570B, 580, 580, 950 MB4/94 WHEEL FELLER BUNCHERS MODEL 26C Backhoe, P80 Cable Plow, T70 MODELS 533, 543, TK370, TK380 WHEEL LOADERS (LOG FORK) CATERPILLAR CYLINDER REPAIR KITS MODELS 924G, 930, 944, 944A, 950, 966A, 966B, 966C 972G, 972H, CRAWLER LOADERS (LOG FORK) 980, 980B, 980C, 988B and 988G MODELS 951, 955, 955E. 955H, -
Download Our Master Catalog
Your Complete Choice for Work Gear, Logging, Urban Forest Management & Tree Care Prices are subject to change without notice $2.00 Volume 43 baileysonline.com | Consumer: 800-322-4539 | Bailey’s Industrial: 1-888-465-8227 | [email protected] “Ain’t noth’n ever been got that ain’t been went out after.” Welcome... Jack Terwilliger, (1914-2005) Welcome to our 2018 Master Catalog! This catalog represents the most comprehensive printed media we have ever produced. I encourage you to Online Resources thumb through and shop with confidence that we are offering one of the best selections of forestry and tree Our industry-leading care work gear available today. Chainsaw Part Selector, Chainsaw Bar Selector, Bailey’s is a leading authority when it comes to chainsaws, bars, and chain. We began selling Chipper Knife Selector, chainsaws back in 1975, and we offer the most Mower Blade Selector, comprehensive selection of chainsaw guide bars and Chainsaw Chain Selector saw chain in the industry. Whether you are a and PartFINDER will weekend firewood cutter, a seasoned logger, or help you find the right anything in between, we have you covered. I product quickly and encourage you to try our online bar and chain easily. Be sure to look for selector guides to see all of the options we offer. these icons located on Bailey’s is also your one stop shopping source for the right side of our portable sawmilling and wood processing equipment. home page. We offer a wide range of entry level sawmills from Granberg and Logosol, as well as the world famous Lucas Mill swing blade sawmills and dedicated slabbers. -
The Landing Magazine Summer 2021 Issue
6 HELPING YOU 10 RUN STRONG Graham Hinch, Director, Western Hemisphere Sales and Marketing Every day in the woods is an opportunity for you Th ey can recommend the right type and size of to not just meet the day’s quota but to take your machine, special confi gurations, and Precision operation to the next level. To help you accomplish Forestry solutions that fi t your business’s unique 18 this, we’ve developed an unrivaled lineup of forestry applications and needs. See your John Deere dealer machines, leading Precision Forestry technologies, for extended warranty and maintenance agreement and a top network of dealers backing your fl eet. options and fi nancing solutions to help you manage your ownership and operating costs. At John Deere, we believe you deserve the best equipment to help raise your game. Our new But our dealer support goes well beyond signing on John Deere 768L-II Bogie Skidder is a great example the dott ed line. From rapid service to preventative of how we listen to our customers to design and maintenance, your local dealer will help keep you manufacture machines that meet their unique and up and running. Th rough John Deere Connected CONTENTS changing needs. Loggers are increasingly looking Support™ enabled by JDLink™, with consent your for opportunities to harvest in diffi cult terrain. Th e dealer closely monitors your fl eet’s health, remotely 3 Loggers’ Round Table six-wheel 768L-II fi ts the bill perfectly, delivering diagnoses machine issues, and quickly responds Four loggers recently discussed the impact of technology on their operations outstanding traction, stability, and fl otation in wet with the appropriate part or solution. -
Time Study and Skidding Capacity of the Wheeled Skidder Timberjack 450C in Caspian Forests
JOURNAL OF FOREST SCIENCE, 54, 2008 (4): 183–188 Time study and skidding capacity of the wheeled skidder Timberjack 450C in Caspian forests F. K. Behjou1, B. Majnounian1, M. Namiranian1, J. Dvořák2 1Faculty of Natural Resources, University of Tehran, Tehran, Iran 2Faculty of Forestry and Wood Sciences, Czech University of Life Sciences Prague, Prague, Czech Republic ABSTRACT: This study was carried out in a steep and difficult terrain. Trees were logged downhill to the landing by a wheeled skidder Timberjack 450C. Selection cutting was performed on a 66-hectare tract with an average slope of 30%. The elemental time study method was applied to develop the skidding time predicting model. In this study 43 working cycles were included. The skidding cycle time was mainly affected by skidding distance, winching distance and interac- tion between skidding distance and slope. The gross and net production rate was 20.51 and 22.93 m3/h, respectively. The unit cost considering the gross and net production rate was 6.31 and 6.22 USD/m3, respectively. Keywords: wheeled skidder Timberjack 450C; working efficiency; init cost; skidding Due to the higher initial cost of harvesting ma- costs of harvesting stands under different machine chines, larger diameters and crowns of hardwoods and harvest prescriptions. and the relatively steep terrain in Caspian forests Jones (1983) conducted a time study on a 60-acre motomanual harvesting and a wheeled skidder are tract with three thinning treatments in the north of still the most commonly used system in this region. West Virginia. Time studies showed that the hourly Primary wood transportation is one of the most sen- felling production increased while the skidding sitive and the most expensive operations and a hard productivity decreased from the treatments 45% to level of forest utilization (Dvořák 2005).