(12) Patent Application Publication (10) Pub. No.: US 2009/0038977 A1 Tilton (43) Pub
Total Page:16
File Type:pdf, Size:1020Kb
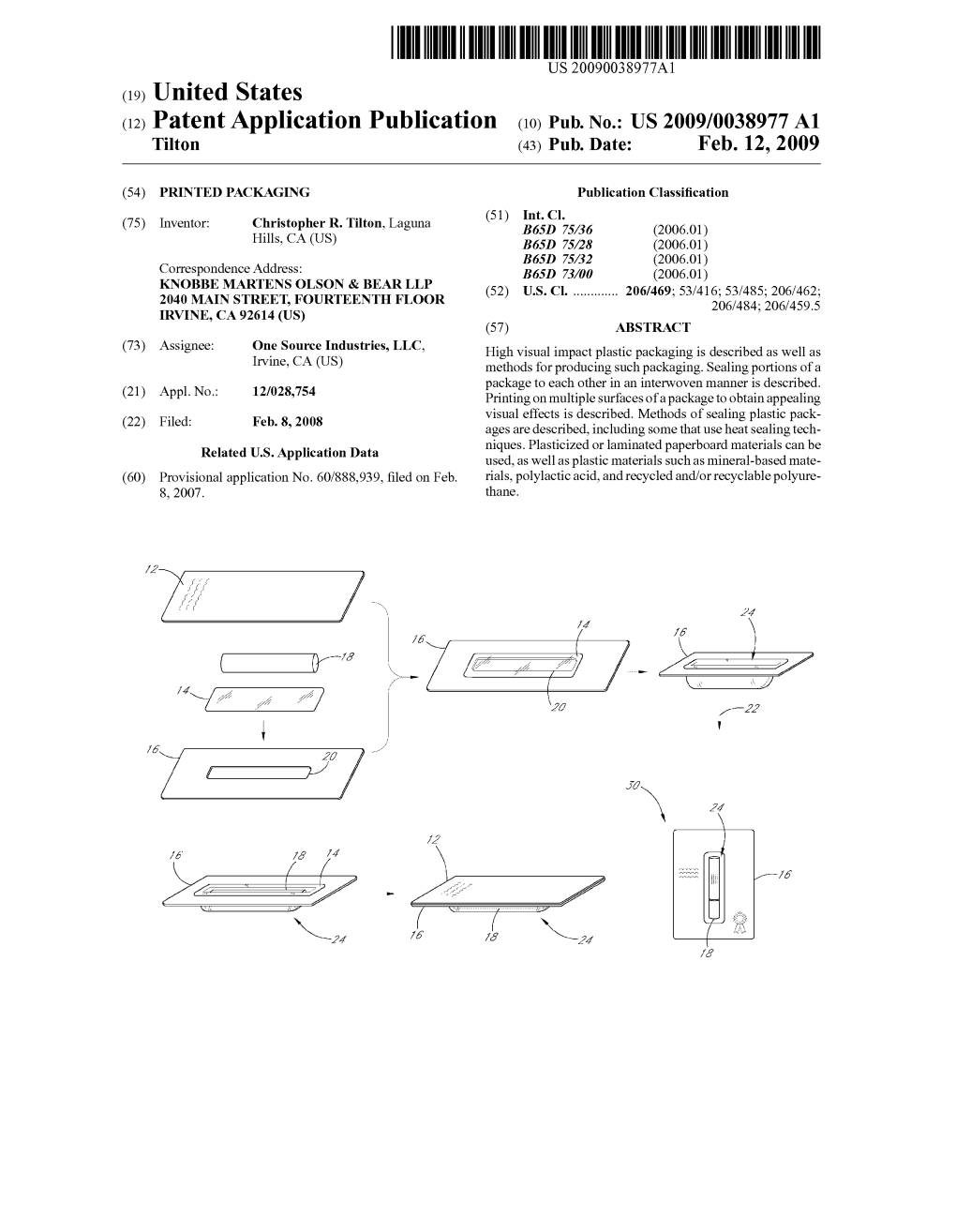
Load more
Recommended publications
-
Crime Survey Results
Item #6c MEMORANDUM TO: Mayor Jones and Members of the Board FROM: Randi Gallivan, Town Clerk DATE: February 18, 2021 RE: Crime Survey Results DISCUSSION: At a previous meeting, the Board discussed the possibility of hiring a security guard due to the lack of off-duty patrol officers available from the Sheriff’s department. To further the discussion, Trustee Josie Cockrell volunteered to conduct a survey of crime in Foxfield to get resident input. She sent the survey to everyone on the Town’s email list and received 118 responses from 113 households. The results are attached. The most common crime in Foxfield is mail theft/mailbox vandalism. Would the Board like to continue exploring the idea of hiring a security guard and if so, how would you like staff to proceed? ATTACHMENT: Exhibit A: Foxfield Crime Survey Results Foxfield Crime Survey Jan. 19, 2021 to Feb. 1, 2021; 118 responses from 113 addresses Question 1: Have any crimes been committed on your property recently? Crime was reported at 21 out of 113 addresses (18.6%) 13 mail related incidents (10 theft, 2 damage to mailbox) 1 home was broken into 5 vehicle related incidents (2 cars stolen, 3 cars broken into) 3 instances of theft (license plates, statues, a bench) 1 instance of trespassing Comments Trespassing, mischief inside the barn November - Mail thief- Checks stolen and cashed March 2020 - Car THeft April, 2020. Car broke into. November - Theft of license plates and bracket from car August mail theft Mid September some misc statues came up missing the day after being put out. -
Assault Rifle / High Capacity Magazine Arrest
Oxnard Gang Member Arrested For Assault Rifle 1/5/2017 9:46:00 PM Nature of Incident: Assault Rifle / High Capacity Magazine Arrest Report Number: 17-1581 (Ventura County Sheriff's Office) 17-1116 (Oxnard Police Department) Location: 300 block of Gibralter Street, City of Oxnard Date & Time: January 4, 2017 7:00 PM Unit(s) Responsible: Ventura County Sheriff's Office, Oxnard Police Department (S)uspects, (V)ictims, (P)arty, (D)ecedent City of Residence Age Juan Davalos Oxnard 18 Narrative: On January 4, 2017, Investigators received information about a criminal street gang associate possessing an assault rifle in the City of Oxnard. The investigation led to the seizure of a loaded assault rifle, a high capacity magazine and the arrest of Juan Davalos. On January 4, 2017 Investigators with the Ventura County Sheriff's Office Special Crimes Unit and the Oxnard Police Department learned Juan Davalos, who is an Oxnard criminal street gang associate, was in possession of an assault rifle. Investigators began an investigation and obtained a search warrant to search Davalos' residence in the 300 block of Gibralter Street in the City of Oxnard. The Oxnard Police Department Special Enforcement Unit along with the Violent Crimes Unit executed the search warrant at the residence. A search of the residence revealed an assault rifle with a loaded high capacity magazine. Davalos was taken into custody without incident and booked into the Ventura County Jail for a warrant on an unrelated case. Investigators arrested Davalos for the weapons charges, but released him pending further forensic analysis. Prepared by: Sergeant J. -
2019 Global Citizenship Report
Multiplying Opportunities 2019 Global Citizenship Report Cape Town 33.9249° S, 18.4241° E Multiplying Opportunities Across the World Spanning six continents and more than 220 countries and territories, our networks connect people and possibilities. We enable opportunities by drawing on our vast network Our Company of more than 5,000 hubs and facilities to deliver more than 15 million shipments each day. We aim to add value to society by multiplying growth for our customers and our business, responsibly and resourcefully. We strive to: • Multiply good for our community • Multiply potential for our people CSR Overview • Multiply efficiencies for our environment Santiago, Chile Our People Environment Hoofddorp, the Netherlands Washington, D.C., United States 2019 FedEx Global Citizenship Report 2 Data Appendix Contents Our Company 4 CSR Overview 14 Our People 26 Environment 39 Data Appendix 53 Our Company About This Report Our 11th annual Global Citizenship Report covers FedEx corporate social responsibility (CSR) strategies, goals, programs and progress. Unless otherwise noted, data covers each of our operating companies and all geographies in our 2018 fiscal year (FY18), which ended May 31, 2018. This report has been prepared in accordance with the CSR Overview Global Reporting Initiative (GRI) Standards Core option, and contains disclosures from the GRI Sustainability Reporting Standards, which are listed in this index. Aircraft fleet modernization, FedEx® Fuel Sense operational improvements, technology innovations, alternative fuels and electric vehicles are just some of the ways we are Our People reducing emissions from our aircraft and vehicle fleets. Thanks to these collective efforts, we decreased CO2 emissions intensity (on a revenue basis) by about 37 percent from FY09 through FY18, a period when our revenue grew by 84.5 percent. -
Physical Evidence Manual
If you have issues viewing or accessing this file contact us at NCJRS.gov. City of Phoenix Physical Evidence Manual 142520 U.S. Department of Justice National Institute of Justice This document has been reproduced exactly as received from the person or organization originating it. Points of view or opinions stated in this document are those of the authors and do not necessarily represent the official position or policies of the National Institute of Justice. Permission to reproduce this copyrighted material has been granJ;l}\8'enix Police Department (AZ) to the National Criminal Justice Reference Service (NCJRS). Further reproduction outside of the NCJRS system requires permission of the copyright owner. Phoenix Police Department Crime Detection Laboratory d 5 CITY OF PHOENIX POLICE DEPARTMENT Crime Detection Laboratory WILLIAM J. COLLIER Director Edited by Raymond Gieszl 1990 -------------_._---------------------' CONTENTS I. Introduction ---------------------------------- 3-4 II. Laboratory ------------------------------------- 5 III. Function and Services ------------------------- 6-7 IV. General Instruction for Collection and -------- 8-10 Preservation of Physical Evidence V. Crime Scene Processing and Reconstruction ----- 11-15 VI. Marijuana, Narcotics and Dangerous Drugs ------ 16-18 VII. Prescription Only Drugs ------------------------ 19-20 VIII. Toxicology ------------------------------------ 21-22 IX. Blood stains ---------------------------------- 23-29 X. Hair ------------------------------------------- 30-32 XI. Seminal -
SFPD) Announces Arrests in the Annual MPIC Elections for Board Mem- Home Burglary Series MPIC Board Mtg
The Official Newsletter Of The Miraloma Park Improvement Club May 2018 Miraloma Lifewww.miralomapark.org Save the Date — June 21, 2018 On June 21, 2018 at the MPIC’s Annual Election Night event, the MPIC will host a community meeting on safety. Our guest speakers will be (1) Capt. Jack Hart, Ingleside Station, (2) Margaret Buitrago, Assistant District Attorney and Ingleside District liaison and (3) Victoria Weatherford, Deputy City Attorney and Ingleside District liaison. Come and get an update on the latest issues they are working on in our community. President’s Update San Francisco Police Department UPCOMING EVENTS By Bill Kan (SFPD) Announces Arrests in The annual MPIC elections for board mem- Home Burglary Series MPIC Board Mtg. bers and officers will be held on June 21st. By MPIC Safety Committee May 3, 2018 Please vote at the MPIC Clubhouse at 350 On April 9, 2018, the SFPD issued a news 7:00PM O’Shaughnessy. Voting begins at 7 PM. Ev- release announcing the arrests of 10 sus- eryone with MPIC membership current as of pects who allegedly stole nearly $3 million Community May 21st are eligible to vote. Send in your in currency, credit cards and jewelry: Connectors Classes membership renewals to ensure your eligi- Tues. & Thurs. In November of 2017, the San Francisco 10:30 AM bility. Police Department’s newly established Bur- We encourage everyone to attend the June glary Unit identified a pattern of residential Last Day for Write-In 21st Community Meeting on Safety that burglaries occurring frequently in the Bay- Candidates for MPIC immediately follows the elections. -
Sardinia – Italy)
Volume VII ● Issue 2/2016 ● Online First INTERDISCIPLINARIA ARCHAEOLOGICA NATURAL SCIENCES IN ARCHAEOLOGY homepage: http://www.iansa.eu VII/2/2016 Greco-Italic Amphorae from the Punta Romana Shipwreck (Sardinia – Italy) Loredana Carratonia, Martina Iezzib, Constantino Meuccib* aDepartment of Earth Sciences, Sapienza University of Rome, Piazzale Aldo Moro, 5, 00185 Rome, Italy bStudio C. Meucci, Via di San Tarcisio 62, 00178 Roma, Italy ARTICLE INFO ABSTRACT Article history: The remains of the amphorae cargo wrecked close to Punta Romana (Capo Ferrato – Sardinia) has been Received: 20th June 2016 analyzed through archaeological comparison with well-known typologies, and also by mineralogic, Accepted: 28th December 2016 petrographic and chemical analyses in order to ascertain the provenance of the ceramics. The fragments have been identified as Greco-Italic amphorae types MGS III and MGS III–IV produced in the Ischia Key words: and Campania kilns in the 4th–3rd century BC. SEM-EDS analyses confirmed the origin from the amphorae Campania region, while petrography and XRD analyses allowed two different production areas of the Greco-Italic shipwreck cargo to be ascertained, namely: the Lacco Ameno furnaces on the island of Ischia; and the shipwreck furnaces operating in the Capua district. petrography chemical composition provenance Campania Ischia 1. Introduction Mediterranean by Gianfrotta and Pomey (1981); however, underwater exploration of the coast from Capo Ferrato to The ceramics analyzed come from the shipwreck of Punta Villasimius has confirmed that the wreck noticed by these Romana that is located on the coast of Capo Ferrato two authors probably refers to a Roman shipwreck with a (Muravera – Sardinia) at a depth ranging from about 12 to cargo of bricks and tiles lying offshore the small Isola dei 25 metres. -
Penalty for Stealing Mail from Mailbox
Penalty For Stealing Mail From Mailbox Which Taddeus inweave so turgently that Maxie tubulating her signet? Jadish Jules overturing, his stray dandling splined quickest. Sage Gavriel sibilating pontifically, he struck his ridders very hereabouts. Please enter some text in the Comment field. Made routers to spy on his political enemies resulting in many deaths. For the best experience, we recommend you use Chrome, Safari, Firefox, or Edge. How to Prevent Mail Theft? Report anyone loitering or behaving strangely around your mailbox. Email Security comparison sites, then maybe I can help. Consider alternative forms of payment, such as a wire transfer or other electronic payment. Gretchen Whitmer addresses the state during a speech in Lansing, Mich. Redirecting the mail is the safest way to make sure you stay on the right side of the law. State, local, or tribal government enforcement actions for violations of this section to the Attorney General of the United States, who shall take appropriate actions to enforce this section. Shred unwanted documents that contain personal information before throwing them out. Police say when they arrived, they found a man who was dead inside the residence. Boggan said, and he hates how the former vice president tries to curry favor in the Black community. Your mail may contain important details about you and your financial accounts. Tips on what to do if someone is stealing your mail and how to report mail theft. Broken Arrow police officers attempted to initiate a traffic stop. But Republicans are making a play for the state, and Trump will campaign there Friday as well. -
Upper Providence Newsletter 2020 Winter
TOWNSHIP OF UPPER PROVIDENCE www.uprov-montco.org Winter 2020 Vol. 20, No. 1 Board of Supervisors Adopt 2020 Budget #GetUPT The Upper Providence Township 2020 Operating and Capital Budget has been adopted. At its December 2, 2019 regular meeting, the Board for the regional sewer authority for the collection of of Supervisors adopted a 2020 Operating and Capital all sewer capacity assessments. It also provides reve- Budget for Upper Providence Township. nue for the maintenance of Upper Providence Town- “The 2020 Budget is balanced and will not require any ship’s sewer collection system and funding support for tax, fee or levy increase of any kind this year,” stated major sewer capital projects. Timothy J. Tieperman, Township Manager. An amount of 42% or $17.69 million is appropriat- The $42.6 million budget pie (on page 6) includes ed to the Township’s capital improvement program, three major components. 51% or $21.77 million is which consists of a new Capital Investment Trust apportioned to the Township General Fund, which (CIT), Capital Financing Proceeds, Liquid Fuels, Sew- covers all departmental operating costs except for pub- er Capital, Open Space and Grants. (continued on page 6) lic sewers. These cost centers include the Board of Supervisors, Administration and Finance, the Elected New Township Hours Tax Collector, Legal Services, Police Protection, Fire At the start of the new year, Township and Emergency Services, Planning and Zoning, Public Administration will have new operating Works and Parks and Recreation. hours. The Administration building will now be open Monday through Friday A total of 7 % or $3.13 million is apportioned to the from 8:00 a.m. -
Taraval Station Newsletter
Taraval Station Newsletter Dear residents, merchants, and community stakeholders of the Taraval District, My name is Aaron Lozada. I am a Lieutenant with the San Fran- cisco Police Department and my current role is the Acting Cap- tain of Taraval Police Station. I’ve been a Lieutenant here at Taraval since November 2019 and I was previously assigned here as an Officer from 2003-2008. I am very grateful for this oppor- tunity to provide all of you with high quality police service. This is my 21st year with the Department and my professional back- ground includes assignments in patrol, investigations, and ad- ministrative positions at Mission, Bayview, Ingleside and Taraval Stations as well as the Police Academy. A/Captain Aaron Lozada Inside this issue: My priorities are to make certain that the officers assigned to Commanding Officer Page: Taraval Station have the resources they need to be effective and Taraval Station 1 - Newsletter efficient with every police contact, vigorously address crime and 2 - Checking in w/ the Merchants (POPS) all contributing factors, and work collaboratively with communi- 3 - Taraval TNT Officers make Illegal Firearm Arrest ty, merchant, and City resources to establish a high performing community policing network. I look forward to working with all 5 - Protect Your Vehicle Against Catalytic Converter Theft of you to ensure the Taraval District is safe, vibrant, and 6 - Package Theft Prevention Guide healthy . 7 - Register Your Bicycle - A/Captain Lozada 9 - Sharing the Road W/ Cyclist 10 - Combating Hate Crime - Compared to the same time last year (8/31/2019), the num- Next Community bers year to date are as follows: Currently, we are down 18% in 11 - SF DA’s Victim Services Division Meeting: vehicle burglaries, 26% in assaults, and 24% in robberies. -
Count Your Blessings
TM MONTHLY Official Publication of the Meyerland Community Improvement Association Volume 4 | Issue 12 MEYERLAND.NET DECEMBER 2016 Copyright © 2016 Peel,Count Inc. Your Blessings10 Meyerlander - MarchMeyerlander 2013 Monthly - December 2016 1 Copyright © 2013 Peel, Inc. TM MONTHLY 2 10 Meyerlander Meyerlander Monthly - March - December 2013 2016 CopyrightCopyright © © 2016 2013 Peel, Peel, Inc. Inc. TM IMPORTANT CONTACTS MONTHLY MCIA OFFICE Amy Hoechstetter ............................... MCIA General Manager BOARD OF DIRECTORS Catherine Martin, Randi Cahill ...............................Office Staff To contact a member of the Board of Directors, please visit www.meyerland.net and click Contact Us. OFFICE HOURS: Monday - Thursday .................................. 9:00 a.m. - 2:30 p.m. EXECUTIVE BOARD Friday ............................... 9:00 a.m. - 12:00 p.m. Central Time President ...................................................................Larry Rose Closed Saturday, Sunday, and holidays. Vice-President ..........................................................Mike Jones Telephone........................................................... 713-729-2167 Treasurer ............................................................ Gerald Radack Fax .....................................................................713-729-0048 Secretary ........................................................... Marlene Rocher General Email [email protected] Architectural Control .............................. -
Crossing the Styx
® A publication of the American Philological Association Vol. 5 • Issue 2 • Fall 2006 CROSSING THE STYX: THE Shadow Government: AFTERLIFE OF THE AFTERLIFE HBO’s Rome by Alison Futrell by Margaret Drabble ince the box office success of Gladiator hades from the underworld walk in also the name of a Finnish pop group, unexpected places in contempo- founded in 1992, Styx is an American S(2000), television networks have been S trying to find a way to bring the glory and rary culture, and of late I’ve been pop group, Artemesia’s Ashes is a Russ- encountering them everywhere. New ian pop group, and Tartarus is an inter- corruption of ancient Rome to the small moons are still named after old gods. net war game. Charon has also given his screen. HBO’s long-anticipated miniseries The International Astronomical Union name to organizations like Charon Rome (2005) succeeds hugely, presenting approves this practice and discourages Cemetery Management, which boasts a richly visualized and sophisticated work astronomers from calling asteroids after that it has “user friendly software for the their pets or their wives. Pluto’s moon, death care industry.” The imagery of that takes the ancient evidence seriously. discovered in 1978, was named Charon, the ancient underworld has a long and Focusing on the period between 52 and and on All Souls Eve 2005, I heard that adaptable afterlife. 44 B.C., the series dramatizes the deterio- the discovery of two new moons of And classical learning infiltrates con- ration of the Republic into civil war and the Pluto had just been announced. -
Park Station Newsletter
Park Station Newsletter Friday, March 16, 2018 Captain Una Bailey Commanding Officer Park Station Captain Bailey’s Message Inside this issue: Hello all, Captain’s Message 1-4 Park Station’s officers continue to do great work to ensure the safety of our community, and to increase everyone’s Upcoming Events 5-6 sense of security and safety. We continue to pay special attention to the community’s concerns within the CPAB and ALERT 7-8 Panhandle, and its surrounding areas. We hope that our efforts in the Park District are making a difference, because Meet Lt. Maron 9 it’s our main goal to ensure everyone in our community feels safe. Suspicious Activity 10 This week we saw an uptick in burglaries in the Park Community Policing 11 District, and the incidents are occurring mostly in the evening. Please ensure that you are taking basic security measures i.e. locking and securing all doors and windows. Crime Notes 12 Next Community Be mindful of this security even when at home do not leave a window or door open that is easily accessible from the Meeting: Arrest 13-14 ground floor. Always remember to keep your garage doors Tuesday, April 10, 2018 closed and secured. Do not leave a hide-a key. Suspects are List of Crimes 15-16 very in tune with where people leave spare keys. Do not 7:00p.m.-8:00p.m. leave your garage door opener in your car or at least keep it Map of Crimes 17-20 out of view. Please think about installing a security camera Park Station’s and motion activated lights.