6-4 7%. 6226. Agent
Total Page:16
File Type:pdf, Size:1020Kb
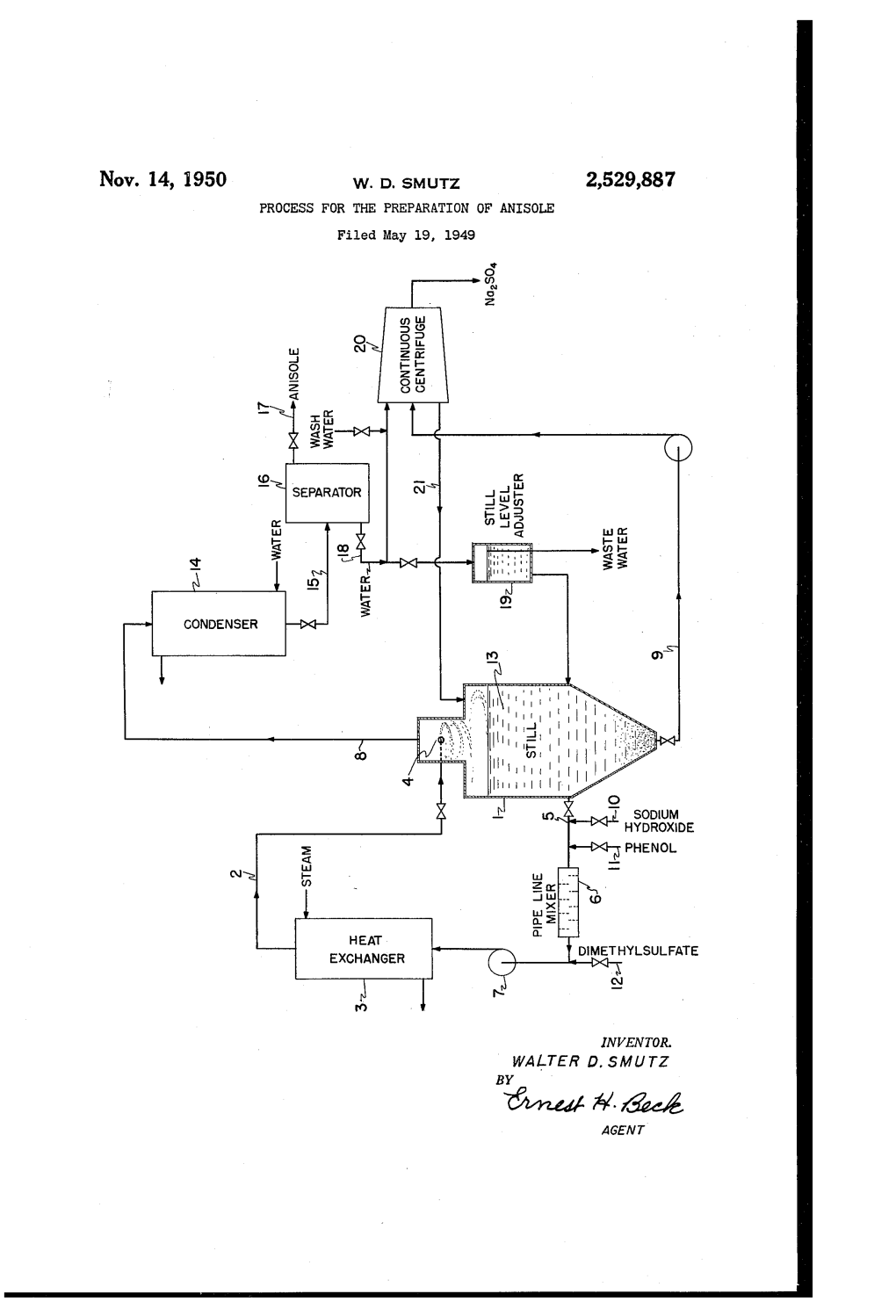
Load more
Recommended publications
-
Retention Indices for Frequently Reported Compounds of Plant Essential Oils
Retention Indices for Frequently Reported Compounds of Plant Essential Oils V. I. Babushok,a) P. J. Linstrom, and I. G. Zenkevichb) National Institute of Standards and Technology, Gaithersburg, Maryland 20899, USA (Received 1 August 2011; accepted 27 September 2011; published online 29 November 2011) Gas chromatographic retention indices were evaluated for 505 frequently reported plant essential oil components using a large retention index database. Retention data are presented for three types of commonly used stationary phases: dimethyl silicone (nonpolar), dimethyl sili- cone with 5% phenyl groups (slightly polar), and polyethylene glycol (polar) stationary phases. The evaluations are based on the treatment of multiple measurements with the number of data records ranging from about 5 to 800 per compound. Data analysis was limited to temperature programmed conditions. The data reported include the average and median values of retention index with standard deviations and confidence intervals. VC 2011 by the U.S. Secretary of Commerce on behalf of the United States. All rights reserved. [doi:10.1063/1.3653552] Key words: essential oils; gas chromatography; Kova´ts indices; linear indices; retention indices; identification; flavor; olfaction. CONTENTS 1. Introduction The practical applications of plant essential oils are very 1. Introduction................................ 1 diverse. They are used for the production of food, drugs, per- fumes, aromatherapy, and many other applications.1–4 The 2. Retention Indices ........................... 2 need for identification of essential oil components ranges 3. Retention Data Presentation and Discussion . 2 from product quality control to basic research. The identifi- 4. Summary.................................. 45 cation of unknown compounds remains a complex problem, in spite of great progress made in analytical techniques over 5. -
NIOSH Skin Notation Profiles Dimethyl Sulfate (DMS)
NIOSH Skin Notation Profiles Dimethyl Sulfate (DMS) IDSK [SK] SYS SYS (FATAL) DIR DIR (IRR) DIR (COR) SEN DEPARTMENT OF HEALTH AND HUMAN SERVICES Centers for Disease Control and Prevention SKNational Institute for Occupational Safety and Health This page intentionally left blank. NIOSH Skin Notation (SK) Profile Dimethyl Sulfate (DMS) [CAS No. 77-78-1] Naomi L. Hudson and G. Scott Dotson DEPARTMENT OF HEALTH AND HUMAN SERVICES Centers for Disease Control and Prevention National Institute for Occupational Safety and Health This document is in the public domain and may be freely copied or reprinted. Disclaimer Mention of any company or product does not constitute endorsement by the National Insti- tute for Occupational Safety and Health (NIOSH). In addition, citations to websites external to NIOSH do not constitute NIOSH endorsement of the sponsoring organizations or their pro- grams or products. Furthermore, NIOSH is not responsible for the content of these websites. Ordering Information To receive this document or information about other occupational safety and health topics, contact NIOSH: Telephone: 1-800-CDC-INFO (1-800-232-4636) TTY: 1-888-232-6348 E-mail: [email protected] or visit the NIOSH website: www.cdc.gov/niosh For a monthly update on news at NIOSH, subscribe to NIOSH eNews by visiting www.cdc.gov/niosh/eNews. Suggested Citation NIOSH [2017]. NIOSH skin notation profile: Dimethyl sulfate. By Hudson NL, Dotson GS. Cincinnati, OH: U.S. Department of Health and Human Services, Centers for Disease Control and Prevention, National Institute for Occupational Safety and Health, DHHS (NIOSH) Publi- cation No. 2017-189. -
RIFM Fragrance Ingredient Safety Assessment, 2-Isopropyl-4- Methylanisole, CAS Registry Number 31574-44-4
Food and Chemical Toxicology 110 (2017) S545eS551 Contents lists available at ScienceDirect Food and Chemical Toxicology journal homepage: www.elsevier.com/locate/foodchemtox Short review RIFM fragrance ingredient safety assessment, 2-isopropyl-4- methylanisole, CAS Registry Number 31574-44-4 * A.M. Api a, , D. Belsito b, D. Botelho a, D. Browne a, M. Bruze c, G.A. Burton Jr. d, J. Buschmann e, M.L. Dagli f, M. Date a, W. Dekant g, C. Deodhar a, M. Francis a, A.D. Fryer h, K. Joshi a,S.LaCavaa, A. Lapczynski a, D.C. Liebler i,D.O’Brien a, R. Parakhia a,A.Patela, T.M. Penning j, G. Ritacco a, J. Romine a, D. Salvito a, T.W. Schultz k, I.G. Sipes l, Y. Thakkar a, E.H. Theophilus a, A.K. Tiethof a, Y. Tokura m, S. Tsang a, J. Wahler a a Research Institute for Fragrance Materials, Inc., 50 Tice Boulevard, Woodcliff Lake, NJ 07677, USA b Columbia University Medical Center, Department of Dermatology, 161 Fort Washington Ave., New York, NY 10032, USA c Malmo University Hospital, Department of Occupational & Environmental Dermatology, Sodra Forstadsgatan 101, Entrance 47, Malmo SE-20502, Sweden d School of Natural Resources & Environment, University of Michigan, Dana Building G110, 440 Church St., Ann Arbor, MI 58109, USA e Fraunhofer Institute for Toxicology and Experimental Medicine, Nikolai-Fuchs-Strasse 1, 30625 Hannover, Germany f University of Sao Paulo, School of Veterinary Medicine and Animal Science, Department of Pathology, Av. Prof. dr. Orlando Marques de Paiva, 87, Sao Paulo CEP 05508-900, Brazil g University of Wuerzburg, Department of Toxicology, Versbacher Str. -
A Convenient and Safe O-Methylation of Flavonoids with Dimethyl Carbonate (DMC)
Molecules 2011, 16, 1418-1425; doi:10.3390/molecules16021418 OPEN ACCESS molecules ISSN 1420-3049 www.mdpi.com/journal/molecules Article A Convenient and Safe O-Methylation of Flavonoids with Dimethyl Carbonate (DMC) Roberta Bernini *, Fernanda Crisante and Maria Cristina Ginnasi Dipartimento di Agrobiologia e Agrochimica, Università degli Studi della Tuscia, Via S. Camillo De Lellis, 01100 Viterbo, Italy * Author to whom correspondence should be addressed; E-Mail: [email protected]. Received: 16 November 2010; in revised form: 23 January 2011 / Accepted: 27 January 2011 / Published: 9 February 2011 Abstract: Dietary flavonoids exhibit beneficial health effects. Several epidemiological studies have focused on their biological activities, including antioxidant, antibacterial, antiviral, anti-inflammatory and cardiovascular properties. More recently, these compounds have shown to be promising cancer chemopreventive agents in cell culture studies. In particular, O-methylated flavonoids exhibited a superior anticancer activity than the corresponding hydroxylated derivatives being more resistant to the hepatic metabolism and showing a higher intestinal absorption. In this communication we describe a convenient and efficient procedure in order to prepare a large panel of mono- and dimethylated flavonoids by using dimethyl carbonate (DMC), an ecofriendly and non toxic chemical, which plays the role of both solvent and reagent. In order to promote the methylation reaction under mild and practical conditions, 1,8-diazabicyclo[5.4.0]undec-7- ene (DBU) was added in the solution; methylated flavonoids were isolated in high yields and with a high degree of purity. This methylation protocol avoids the use of hazardous and high toxic reagents (diazomethane, dimethyl sulfate, methyl iodide). Keywords: methylated flavonoids; ecofriendly methylation reaction; dimethyl carbonate (DMC); green chemistry 1. -
TOXICOLOGY and EXPOSURE GUIDELINES ______(For Assistance, Please Contact EHS at (402) 472-4925, Or Visit Our Web Site At
(Revised 1/03) TOXICOLOGY AND EXPOSURE GUIDELINES ______________________________________________________________________ (For assistance, please contact EHS at (402) 472-4925, or visit our web site at http://ehs.unl.edu/) "All substances are poisons; there is none which is not a poison. The right dose differentiates a poison and a remedy." This early observation concerning the toxicity of chemicals was made by Paracelsus (1493- 1541). The classic connotation of toxicology was "the science of poisons." Since that time, the science has expanded to encompass several disciplines. Toxicology is the study of the interaction between chemical agents and biological systems. While the subject of toxicology is quite complex, it is necessary to understand the basic concepts in order to make logical decisions concerning the protection of personnel from toxic injuries. Toxicity can be defined as the relative ability of a substance to cause adverse effects in living organisms. This "relative ability is dependent upon several conditions. As Paracelsus suggests, the quantity or the dose of the substance determines whether the effects of the chemical are toxic, nontoxic or beneficial. In addition to dose, other factors may also influence the toxicity of the compound such as the route of entry, duration and frequency of exposure, variations between different species (interspecies) and variations among members of the same species (intraspecies). To apply these principles to hazardous materials response, the routes by which chemicals enter the human body will be considered first. Knowledge of these routes will support the selection of personal protective equipment and the development of safety plans. The second section deals with dose-response relationships. -
Arenechromium Tricarbonyl Complexes: Conformational
η6 – ARENECHROMIUM TRICARBONYL COMPLEXES: CONFORMATIONAL ANALYSIS, STEREOCONTROL IN NUCLEOPHILIC ADDITION AND APPLICATIONS IN ORGANIC SYNTHESIS by HARINANDINI PARAMAHAMSAN Submitted in partial fulfillment of the requirements for the degree of Doctor of Philosophy Thesis Advisor: Prof. Anthony J. Pearson Department of Chemistry CASE WESTERN RESERVE UNIVERSITY May 2005 CASE WESTERN RESERVE UNIVERSITY SCHOOL OF GRADUATE STUDIES We hereby approve the dissertation of Harinandini Paramahamsan candidate for the Ph.D. degree*. (signed) Prof. Philip P. Garner (Chair of the Committee, Department of Chemistry, CWRU) Prof. Anthony J. Pearson (Department of Chemistry, CWRU) Prof. Fred L. Urbach (Department of Chemistry, CWRU) Dr. Zwong-Wu Guo (Department of Chemistry, CWRU) Dr. Stuart J. Rowan (Department of Macromolecular Science and Engineering, CWRU) Date: 14th January 2005 *We also certify that written approval has been obtained for any propriety material contained therein. To Amma, Naina & all my Teachers Table of Contents List of Tables………………………………………………………………………..……iv List of Figures…………………………………………………………………….…........vi List of Schemes…………………………………………………………………….….….ix List of Equations………………………………………………………...……….……….xi Acknowledgements………………………………………………………….…..……….xii List of Abbreviations……………………………………………………………………xiv Abstract………………………………………………………………………………….xvi CHAPTER I........................................................................................................................ 1 I.1 Structure and Bonding ........................................................................................... -
Reactions of Aromatic Compounds Just Like an Alkene, Benzene Has Clouds of Electrons Above and Below Its Sigma Bond Framework
Reactions of Aromatic Compounds Just like an alkene, benzene has clouds of electrons above and below its sigma bond framework. Although the electrons are in a stable aromatic system, they are still available for reaction with strong electrophiles. This generates a carbocation which is resonance stabilized (but not aromatic). This cation is called a sigma complex because the electrophile is joined to the benzene ring through a new sigma bond. The sigma complex (also called an arenium ion) is not aromatic since it contains an sp3 carbon (which disrupts the required loop of p orbitals). Ch17 Reactions of Aromatic Compounds (landscape).docx Page1 The loss of aromaticity required to form the sigma complex explains the highly endothermic nature of the first step. (That is why we require strong electrophiles for reaction). The sigma complex wishes to regain its aromaticity, and it may do so by either a reversal of the first step (i.e. regenerate the starting material) or by loss of the proton on the sp3 carbon (leading to a substitution product). When a reaction proceeds this way, it is electrophilic aromatic substitution. There are a wide variety of electrophiles that can be introduced into a benzene ring in this way, and so electrophilic aromatic substitution is a very important method for the synthesis of substituted aromatic compounds. Ch17 Reactions of Aromatic Compounds (landscape).docx Page2 Bromination of Benzene Bromination follows the same general mechanism for the electrophilic aromatic substitution (EAS). Bromine itself is not electrophilic enough to react with benzene. But the addition of a strong Lewis acid (electron pair acceptor), such as FeBr3, catalyses the reaction, and leads to the substitution product. -
RIFM Fragrance Ingredient Safety Assessment, Anisyl Alcohol, CAS Registry T Number 105-13-5 A.M
Food and Chemical Toxicology 134 (2019) 110702 Contents lists available at ScienceDirect Food and Chemical Toxicology journal homepage: www.elsevier.com/locate/foodchemtox Short Review RIFM fragrance ingredient safety assessment, anisyl alcohol, CAS registry T number 105-13-5 A.M. Apia, D. Belsitob, S. Bisertaa, D. Botelhoa, M. Bruzec, G.A. Burton Jr.d, J. Buschmanne, M.A. Cancellieria, M.L. Daglif, M. Datea, W. Dekantg, C. Deodhara, A.D. Fryerh, S. Gadhiaa, L. Jonesa, K. Joshia, A. Lapczynskia, M. Lavellea, D.C. Liebleri, M. Naa, D. O'Briena, A. Patela, T.M. Penningj, G. Ritaccoa, F. Rodriguez-Roperoa, J. Rominea, N. Sadekara, D. Salvitoa, ∗ T.W. Schultzk, F. Siddiqia, I.G. Sipesl, G. Sullivana, , Y. Thakkara, Y. Tokuram, S. Tsanga a Research Institute for Fragrance Materials, Inc., 50 Tice Boulevard, Woodcliff Lake, NJ, 07677, USA b Member Expert Panel, Columbia University Medical Center, Department of Dermatology, 161 Fort Washington Ave., New York, NY, 10032, USA c Member Expert Panel, Malmo University Hospital, Department of Occupational & Environmental Dermatology, Sodra Forstadsgatan 101, Entrance 47, Malmo SE, 20502, Sweden d Member Expert Panel, School of Natural Resources & Environment, University of Michigan, Dana Building G110, 440 Church St., Ann Arbor, MI, 58109, USA e Member Expert Panel, Fraunhofer Institute for Toxicology and Experimental Medicine, Nikolai-Fuchs-Strasse 1, 30625, Hannover, Germany f Member Expert Panel, University of Sao Paulo, School of Veterinary Medicine and Animal Science, Department of Pathology, Av. Prof. dr. Orlando Marques de Paiva, 87, Sao Paulo, CEP 05508-900, Brazil g Member Expert Panel, University of Wuerzburg, Department of Toxicology, Versbacher Str. -
Working with Hazardous Chemicals
A Publication of Reliable Methods for the Preparation of Organic Compounds Working with Hazardous Chemicals The procedures in Organic Syntheses are intended for use only by persons with proper training in experimental organic chemistry. All hazardous materials should be handled using the standard procedures for work with chemicals described in references such as "Prudent Practices in the Laboratory" (The National Academies Press, Washington, D.C., 2011; the full text can be accessed free of charge at http://www.nap.edu/catalog.php?record_id=12654). All chemical waste should be disposed of in accordance with local regulations. For general guidelines for the management of chemical waste, see Chapter 8 of Prudent Practices. In some articles in Organic Syntheses, chemical-specific hazards are highlighted in red “Caution Notes” within a procedure. It is important to recognize that the absence of a caution note does not imply that no significant hazards are associated with the chemicals involved in that procedure. Prior to performing a reaction, a thorough risk assessment should be carried out that includes a review of the potential hazards associated with each chemical and experimental operation on the scale that is planned for the procedure. Guidelines for carrying out a risk assessment and for analyzing the hazards associated with chemicals can be found in Chapter 4 of Prudent Practices. The procedures described in Organic Syntheses are provided as published and are conducted at one's own risk. Organic Syntheses, Inc., its Editors, and its Board of Directors do not warrant or guarantee the safety of individuals using these procedures and hereby disclaim any liability for any injuries or damages claimed to have resulted from or related in any way to the procedures herein. -
1. A. the First Reaction Is a Friedel-Crafts Acylation (FCA), Where the Major Product Is the Para- Isomer (60% Isolated Yield)
1. a. The first reaction is a Friedel-Crafts Acylation (FCA), where the major product is the para- isomer (60% isolated yield). The second reaction is a nitration, where the incoming electrophile (nitronium ion) is directed to the ortho position of the methoxy group. The last reaction is a Wolff-Kishner reduction that converts the acetyl group into an ethyl group. The nitro group does not react under these conditions. OCH OCH OCH OCH3 3 3 3 NO2 NO2 N2H4/KOH CH3COCl/AlCl3 H2SO4/HNO3 0 oC O CH 3 O CH3 CH3 (A) Reaction 1 (B) Reaction 2 (C) Reaction 3 (P) b. The best solvent for the FC-acylation is dichloromethane. Tetrahydrofuran is a fairly strong Lewis base, which would react and deactivate the AlCl3 catalyst. Ethanol would also react with AlCl3 and form alcoholates, which are inactive at FCA catalyst. Dichloromethane is polar enough to dissolve all three compounds but does not form adducts with AlCl3. Thus, aluminum chloride maintains its Lewis acidity. 3+ c. As discussed in lecture, AlCl3*6 H2O is not suitable as catalyst because the Al is not a strong Lewis acid anymore. In addition, larger amounts of water would destroy the acetyl chloride as well (=hydrolysis, CH3COCl + H2O ---- > CH3COOH + HCl). Consequently, the reaction would not proceed in the desired fashion. 3+ OH2 H2O OH2 Al H2O OH2 OH2 d. In order to determine the yield, one has to calculate the number of moles of the reactant and the product. nA = 1.90 mL * 0.996 g/mL/108.14 g/mol = 17.5 mmol nCH3COCl = 2.49 mL * 1.104 g/mL/78.5 g/mol = 35.0 mmol nAlCl3 = 4.67 g/133.5 g/mol = 35.0 mmol Compound (A) is the limiting reagent. -
High Hazard Chemical Policy
Environmental Health & Safety Policy Manual Issue Date: 2/23/2011 Policy # EHS-200.09 High Hazard Chemical Policy 1.0 PURPOSE: To minimize hazardous exposures to high hazard chemicals which include select carcinogens, reproductive/developmental toxins, chemicals that have a high degree of toxicity. 2.0 SCOPE: The procedures provide guidance to all LSUHSC personnel who work with high hazard chemicals. 3.0 REPONSIBILITIES: 3.1 Environmental Health and Safety (EH&S) shall: • Provide technical assistance with the proper handling and safe disposal of high hazard chemicals. • Maintain a list of high hazard chemicals used at LSUHSC, see Appendix A. • Conduct exposure assessments and evaluate exposure control measures as necessary. Maintain employee exposure records. • Provide emergency response for chemical spills. 3.2 Principle Investigator (PI) /Supervisor shall: • Develop and implement a laboratory specific standard operation plan for high hazard chemical use per OSHA 29CFR 1910.1450 (e)(3)(i); Occupational Exposure to Hazardous Chemicals in Laboratories. • Notify EH&S of the addition of a high hazard chemical not previously used in the laboratory. • Ensure personnel are trained on specific chemical hazards present in the lab. • Maintain Material Safety Data Sheets (MSDS) for all chemicals, either on the computer hard drive or in hard copy. • Coordinate the provision of medical examinations, exposure monitoring and recordkeeping as required. 3.3 Employees: • Complete all necessary training before performing any work. • Observe all safety -
Dimethyl Sulfate Use CAS No
Report on Carcinogens, Fourteenth Edition For Table of Contents, see home page: http://ntp.niehs.nih.gov/go/roc Dimethyl Sulfate Use CAS No. 77-78-1 Dimethyl sulfate is used primarily as a methylating agent to convert compounds such as phenols, amines, and thiols to the correspond- Reasonably anticipated to be a human carcinogen ing methyl derivatives (IARC 1999). It is also used as a methylating or sulfating agent in the manufacture of methyl esters, ethers, and First listed in the Second Annual Report on Carcinogens (1981) amines in dyes, drugs, perfumes, pesticides, phenol derivatives, fab- OO ric softeners, polyurethane-based adhesives, and other organic chem- icals. Dimethyl sulfate is also used as a solvent for the separation of H3C S CH3 O O mineral oils, for the analysis of auto fluids, and with boron to sta- Carcinogenicity bilize liquid sulfur trioxide (HSDB 2009). It was formerly used as a chemical weapon. Dimethyl sulfate is reasonably anticipated to be a human carcino- Production gen based on sufficient evidence of carcinogenicity from studies in experimental animals. Dimethyl sulfate has been produced commercially since at least the 1920s (IARC 1974, 1999). One production method is continuous re- Cancer Studies in Experimental Animals action of dimethyl ether with sulfur trioxide (IARC 1974). In 2009, Dimethyl sulfate caused tumors in rats at several different tissue sites dimethyl sulfate was produced by 33 manufacturers worldwide, in- and by several different routes of exposure. Inhalation exposure to cluding 1 in the United States, 14 in China, 5 in India, 5 in Europe, 6 dimethyl sulfate caused cancer of the nasal cavity (squamous-cell car- in East Asia, and 2 in Mexico (SRI 2009), and was available from 44 cinoma) and other local tumors.