(12) Patent Application Publication (10) Pub. No.: US 2010/0217022 A1 Abraham Et Al
Total Page:16
File Type:pdf, Size:1020Kb
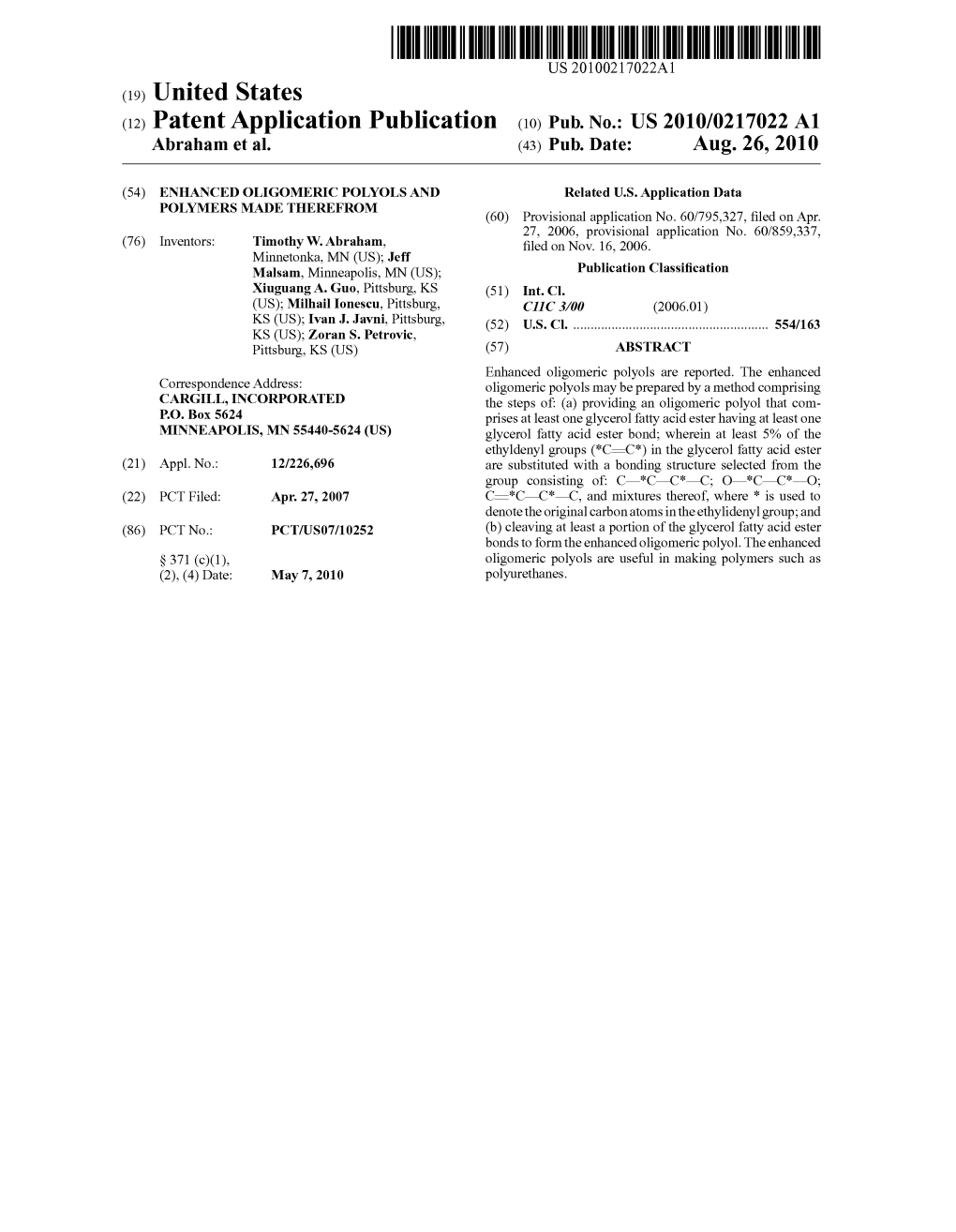
Load more
Recommended publications
-
Achieving Performance and Sustainability Objectives with Biobased Polyols
AS SEEN IN Paint Coatings Industry Globally Serving Liquid and Powder Manufacturers and Formulators Achieving Performance and Sustainability Objectives with Biobased Polyols By Mark Anater, Chemist, Research & Technology Aliphatic polyester polyols are typically produced based – Polyols, and Eric Geiger, Technology Manager – on petrochemical-derived adipic acid, which is expe- Polyols, Emery Oleochemicals LLC, Cincinnati, OH riencing environmental pressure due to the potential for NOx emissions. Biobased adipic acid is not currently commercially available. However, there are alternative chieving sustainability objectives has biobased diacids available, such as the nine carbon increased in importance for those in the chain diacid, azelaic acid, which can offer end products coatings industry. This includes the use of with equivalent or improved performance with the biobased raw materials in the production of added benefit of sustainability. Aresins. The use of biobased materials in coatings is cer- Physical properties of a, w-alkane dicarboxylic acids tainly not new; shellac is based on a resin secreted from are dependent upon the carbon chain length, and physical the lac bug, and some of the first polyurethane chemistry characteristics can be quite different if the diacid has an practiced was based on castor oil, both of which are still even or an odd number of carbons, as outlined in Table 1. in use. The key limitation with such natural products Diacids with an even number of carbons have much higher was often performance. As application performance melting points and lower boiling points than the adjacent demands increased, more “engineered” solutions were odd carbon numbered acids. The even-odd effect can also developed based upon materials that were typically be seen in water solubility, but here chain length masks the derived from petrochemicals. -
Bio-Based Chemicals Overview
Bio-Based Chemicals Overview 2019 PCA International Conference Vancouver, B.C., Canada, 23 - 24 September 2019 Doris de Guzman Senior Consultant – Biomaterials [email protected] OUR CORE STRENGTHS Intermediates, Fibres & Specialty Resins Soda Ash Epichlorohydrin Epoxy Resins Bisphenol A Caustic Soda EDC VCM PVC Acetone Phenol Isocyanates Chlorine Peroxy PO Polyols Polyurethanes Polyester Film Chlorohydrin PO PET Resin Bio-Materials Derivatives EO Derivatives Ethylene Oxide MEG Polyester Fibre Acetic Acid PTA Polyester Polypropylene Fibre Paraxylene Vinyl Acetate Monomer DMT Caprolactam Acrylic Fibre Acrylonitrile Adiponitrile HMDA Polyamide 6 Polyamide Fibre Adipic Acid AH Salt Polyamide 66 Polyamide Resin Polyacetal ABS & SAN PBT Polycarbonate Methanol Isodecanol DIDP Orthoxylene Styrene Methyl Acrylate Isononanol DINP Phthalic Anhydride 1,4-Butanediol Ethyl Acrylate 2-PH DPHP Acrylic Acid Unsaturated Maleic Anhydride Polyester Resin 2-Ethylhexyl Acrylate 2-EH DOP Butyl Acrylate Butanols 2 BIO-MAT E R IAL S & INT E R ME DIAT E S A monthly publication reporting market trends, pricing, and feedstock for Bio-based chemicals and their Petrochemicals counterpart Started in 2007 & Inspired by an unwavering belief that we can and will do better www.greenchemicalsblog.com 3 Value additions of Bio-based Industry to US Economy Forest Products $364bn Bio-based $22bn Chemicals $3.5bn $45bn (NA) $106bn Enzymes Textiles Agriculture $35bn and $1.11bn Forestry Biorefining Bioplastic $506m bottles and packaging Source: USDA, PCA 4 Value additions -
Synthesis of Lipid Based Polyols from 1-Butene Metathesized Palm Oil for Use in Polyurethane Foam Applications
Synthesis of Lipid Based Polyols from 1-butene Metathesized Palm Oil for Use in Polyurethane Foam Applications A Thesis Submitted to the Committee on Graduate Studies in Partial Fulfillment of the Requirements for the Doctor of Philosophy in the Faculty of Arts and Science TRENT UNIVERSITY Peterborough, Ontario, Canada © Copyright by Prasanth Kumar Sasidharan Pillai 2015 Materials Science PhD. Graduate Program January 2016 Abstract Synthesis of Lipid Based Polyols from 1-Butene Metathesized Palm Oil for Use in Polyurethane Foam Applications Prasanth Kumar Sasidharan Pillai This thesis explores the use of 1-butene cross metathesized palm oil (PMTAG) as a feedstock for preparation of polyols which can be used to prepare rigid and flexible polyurethane foams. PMTAG is advantageous over its precursor feedstock, palm oil, for synthesizing polyols, especially for the preparation of rigid foams, because of the reduction of dangling chain effects associated with the omega unsaturated fatty acids. 1-butene cross metathesis results in shortening of the unsaturated fatty acid moieties, with approximately half of the unsaturated fatty acids assuming terminal double bonds. It was shown that the associated terminal OH groups introduced through epoxidation and hydroxylation result in rigid foams with a compressive strength approximately 2.5 times higher than that of rigid foams from palm and soybean oil polyols. Up to 1.5 times improvement in the compressive strength value of the rigid foams from the PMTAG polyol was further obtained following dry and/or solvent assisted fractionation of PMTAG in order to reduce the dangling chain effects associated with the saturated components of the PMTAG. -
Polyurethanes Technical Conference 2016
Polyurethanes Technical Conference 2016 Baltimore, Maryland, USA 26 - 28 September 2016 ISBN: 978-1-5108-3172-8 Printed from e-media with permission by: Curran Associates, Inc. 57 Morehouse Lane Red Hook, NY 12571 Some format issues inherent in the e-media version may also appear in this print version. Copyright© (2016) by American Chemistry Council All rights reserved. Printed by Curran Associates, Inc. (2016) For permission requests, please contact American Chemistry Council at the address below. American Chemistry Council 700 Second St., NE Washington, DC 20002 USA Phone: (202) 249-7000 Fax: (202) 249-6100 www.americanchemistry.com Additional copies of this publication are available from: Curran Associates, Inc. 57 Morehouse Lane Red Hook, NY 12571 USA Phone: 845-758-0400 Fax: 845-758-2633 Email: [email protected] Web: www.proceedings.com TABLE OF CONTENTS PAPERS AUTOMOTIVE I Vehicle Interior Air Quality - VDA 278 and Beyond..........................................................................................................1 Caroline Widdowson, Ilaria Ferrante, Massimo Santoro Aldehyde Emissions from Flexible Molded Foam...............................................................................................................5 Jennifer Al-Rashid, Torsten Panitzsch, Jackson Su, Gauri Sankar Lal, Allen Arnold L-Shaped Air Flush Spray Mixing Heads for the Production of Lightweight Automotive Components..................... 16 Andrea Bartolini, Alessandro Colella AUTOMOTIVE II Enabling Automotive Light Weighting by Reducing -
PDF ( 832.9 Kb )
Boost your sustainability profile Sovermol® – natural oil-based, performance driven polyols Boost your sustainability profile 2 Sovermol® – natural oil-based, performance driven polyols Performance-driven polyols for 2K PU systems based on natural oil Sovermol® by BASF BASF’s Sovermol® range of green polyols has been specially designed for use in coating, adhesive and putty applications. These natural oil-based polyols help you to comply with environmental standards while meeting even the toughest production regulations. What’s more, improving the environmental profile of your processes will make you more attractive to both existing and new customers. Sovermol® is part of our 2K PU offering containing the crosslinker (Basonat® − NCO) and acrylic polyol (Joncryl®). Natural-oil polyols are polyfunctional alcohols based on exhibit excellent hydrolysis resistance, chemical resistance renewable raw materials like rapeseed oil, castor oil, soybean and UV resistance, as well as low viscosity. This latter oil and palm kernel oil. The practical advantages of these characteristic is especially important in spraying applications. products include good adhesion, excellent workability and The modular system of our Sovermol® product group includes good weathering properties. They can also be used on a other important features, such as being 100 % solid, good wide variety of different substrates. gloss development and good pigment wetting characteristics. The latest generation of BASF Sovermol® products combines Polyols based on natural oils have a very pronounced sustainability with performance, thus meeting the requirements hydrophobic character. For this reason, oleochemical of today’s producers and consumers. Hardness can be polyols create significantly less carbon dioxide as a result regulated without using plasticizers and they feature excellent of the side reaction of the isocyanate. -
Method of Obtaining Environment-Friendly Polyols from Waste Left After Transesterification of Plant Oils, and Method of Obtaining Rigid Polyurethane Foams
(19) TZZ ¥_T (11) EP 2 957 583 A1 (12) EUROPEAN PATENT APPLICATION (43) Date of publication: (51) Int Cl.: 23.12.2015 Bulletin 2015/52 C08G 18/48 (2006.01) C08J 11/10 (2006.01) C08J 11/12 (2006.01) C08G 65/34 (2006.01) (2006.01) (21) Application number: 14460111.9 C08G 18/36 (22) Date of filing: 16.12.2014 (84) Designated Contracting States: (72) Inventors: AL AT BE BG CH CY CZ DE DK EE ES FI FR GB • Haponiuk, Józef T. GR HR HU IE IS IT LI LT LU LV MC MK MT NL NO 80-344 Gdansk (PL) PL PT RO RS SE SI SK SM TR • Piszczyk, Lukasz Designated Extension States: 80-107 Gdansk (PL) BA ME • Danowska, Magdalena 80-266 Gdansk (PL) (30) Priority: 18.06.2014 PL 40861014 • Strankowsku, Michal 80-177 Gdansk (PL) (71) Applicant: Novapur Sp. z o.o. 80-233 Gdansk (PL) (54) Method of obtaining environment-friendly polyols from waste left after transesterification of plant oils, and method of obtaining rigid polyurethane foams (57) Method of obtaining environment-friendly poly- phuric acid pH 4.5 to 9, preferably from 6.5 to 7.5. Next, ols from waste left after transesterification of plant oils is the reaction mixture is heated under reduced pressure characterized in that the said waste is heated to a tem- to a temperature between 100 and 120°C until water perature in the range between 160 and 240°C, preferably stops to appear. Polyols are also produced from polyg- between 175 and 185°C, under reduced pressure in or- lycols extended with fatty acids and modified fatty acids. -
Life Cycle Inventory
Table of Contents List of Tables and Figures ....................................................................................................... 3 Abstract ................................................................................................................................ 4 Introduction .......................................................................................................................... 5 Scope and System Boundary .................................................................................................. 5 Life Cycle Inventory ............................................................................................................... 6 Soy Farming and Land Conversion ..................................................................................................................... 7 Soybean Oil Processing ...................................................................................................................................... 8 Crude Oil Extraction and Process Impacts .......................................................................................................... 9 Polyol Process .................................................................................................................................................... 9 Foaming Process .............................................................................................................................................. 11 End of Use Recycling ....................................................................................................................................... -
Bio-Based and Recycled Content Polyols
Bio-Based and Recycled Content Polyols Product Brochure Pioneering natural-based Your preferred innovations for 175 years partner in sustainable Emery Oleochemicals is a leading solutions provider in polyurethanes renewable-based specialty chemicals with global operations spanning Asia, Europe and the U.S. Dedicated to providing Transforming market needs into innovative customers with best-in-class products derived from natural products through our EMEROX® sources, we pride ourselves on having a diverse portfolio known renewable and INFIGREEN® recycled for its performance, economics, and environmentally responsible content polyols, our Eco-Friendly Polyols properties. are poised to provide the polyurethanes industry with custom solutions providing Guided by an inventive spirit that goes beyond providing high value-added performance benefits that performance solutions, we are able to assist your business cope can be integrated economically into with the challenges of markets that are going greener by the day. sustainable products and processes. Our combined strengths in cutting-edge research, technology, and development and in-depth knowledge and understanding Creating polyols that enhance your of markets and customer needs, allow us to expand the formulations and end-products to go boundaries of science and advance sustainable solutions. Our beyond performance requirements, competitive advantage is translated into a wide-ranging portfolio optimize processing parameters, and of target markets including Eco-friendly Polyols, Agro Green, be environmentally responsible. These Bio-Lubricants, Green Polymer Additives, Home and Personal are excellent raw materials for use in Wellness and OleoBasics. the manufacture of insulation, furniture, automotive applications, major appliances Working with customers to build a resource-efficient way of life and coatings, adhesives, sealants & makes us your preferred natural-based chemical solutions partner. -
A Study Assessing the Opportunities and Potential of Soybean Based Products and Technologies
A Study Assessing the Opportunities and Potential of Soybean Based Products and Technologies Developed by For The Agricultural Utilization Research Institute August 2009 Page i TABLE OF CONTENTS I. EXECUTIVE SUMMARY.................................................................................... 1 A. RENEWABLE DIESEL .......................................................................................... 1 B. ENZYMATIC TRANSESTERIFICATION ..................................................................... 1 C. SOY-BASED POLYOLS........................................................................................ 2 D. EPICHLOROHYDRIN ............................................................................................ 2 E. SOY-BASED WOOD ADHESIVE ............................................................................ 3 F. HIGH-OIL SOYBEANS ......................................................................................... 3 G. HIGH STABILITY OIL SOYBEANS .......................................................................... 4 H. AQUACULTURE FEED ......................................................................................... 4 II. INTRODUCTION ................................................................................................ 6 A. REPORT LAYOUT ............................................................................................... 6 B. PROJECT METHODOLOGY AND PROCESS FLOW ................................................... 6 1. Demand/Market Potential: .......................................................................... -
(12) United States Patent (10) Patent No.: US 8,097,739 B2 Luo Et Al
USO08097739B2 (12) United States Patent (10) Patent No.: US 8,097,739 B2 Luo et al. (45) Date of Patent: Jan. 17, 2012 (54) PROCESS FOR THE MANUFACTURE OF 2006/0276609 A1* 12/2006 Lysenko et al. ................. 528.44 NATURAL OIL HYDROXYLATES 2007/O123725 A1 5/2007 Lorenz 2007/0173632 A1 7, 2007 Odaka (75) Inventors: Ning Luo, Fayetteville, AR (US); Trevor FOREIGN PATENT DOCUMENTS Newbold, Freeport (BS) CN 1837.180 A 9, 2006 CN 1837181 A 9, 2006 (73) Assignee: BioBases Technologies, LLC, GB 1248919 10, 1971 WO WO2004/099227 11, 2004 Springdale, AR (US) WO WO2005 123798 12/2005 WO WO2006/094227 A2 9, 2006 (*) Notice: Subject to any disclaimer, the term of this patent is extended or adjusted under 35 OTHER PUBLICATIONS U.S.C. 154(b) by 461 days. Fornol et, al. in Fornol, A.R.; Onah, E., Ghosh, S.; Frazier, C.E.; Sohn, S.; Wilkes, G.L.; and Long, T.E., Synthesis and Characteriza (21) Appl. No.: 12/082,808 tion on Triglyceride-Based polyols and Tack-Free 15 Coatings Via The Air Oxidation of Soy Oil. J. Appl. Poly. Sci. (2006), 102:690 (22) Filed: Apr. 15, 2008 697.* Guo, A.; Javni, I; Petrovic, Z. Rigid Polyurethane Foams Based on (65) Prior Publication Data Soybean Oil. J. Appl. Poly. Sci. (2000), 77:467-473.* Zlatanic, A.; Lava, C.; Zhang, W.; Petrovic, Z. S. Effect of Structure US 2008/O262259 A1 Oct. 23, 2008 on Properties of Polyols and Polyurethanes Based on Different Veg etable Oils, 15 J. Poly. Sci.: Part B: Polymer Physics (2004), 42: Related U.S. -
Polyurethane Networks from Different Soy-Based Polyols by the Ring Opening of Epoxidized Soybean Oil with Poly(Ethylene Glycol)S
Polyurethane Networks from Different Soy-Based Polyols by the Ring Opening of Epoxidized Soybean Oil with Poly(ethylene glycol)s 1Miray Sakarya and 1*Sennur Deniz 1Yıldız Technical University, Chemical Engineering Department, Davutpaşa cd. Nr:127, 34210, Esenler-Istanbul, Turkey Abstract Epoxidized vegetable oils have drawn much attention in recent years, especially in the polymer industry as they are economical, available, environmentally friendly, non-noxious and renewable. Epoxidized soybean based polyols are a great alternative for the polyurethane industry in applications where hydrophobicity, hardness, flexibility, and mechanical and chemical resistance are needed: foams, coatings and floorings. In this study, PEG400-ESO soy-based polyols with a range of hydroxyl numbers based on epoxidized soybean oil (ESO) are prepared by oxirane ring opening with poly(ethylene glycol) (PEG400) having the molecular weight of 400g/mol in the presence of tetrafluoroboric acid catalyst. These epoxy ring opening reactions give a range of different structures, which when converted to polyurethanes imparted different properties to the final products. Rigid polyurethane foams are prepared by reacting with synthesized soy-based polyols and polymeric methylene diphenyl diisocyanate (MDI). The effects of reaction temperature and catalyst amount on the PEG400-ESO soy-based polyols were investigated by spectroscopic, chemical and physical methods. Key words: Epoxidized soybean oils, soy-based polyols, polyurethane, polyethylene glycol 1. Introduction The new interest in utilization of vegetable oils for industrial use is the result of the public awareness and insistence on sustainability and the need to save the environment. Vegetable oils have been successfully used for polyols in the polyurethane industry [1]. -
WO 2009/020774 Al
(12) INTERNATIONAL APPLICATION PUBLISHED UNDER THE PATENT COOPERATION TREATY (PCT) (19) World Intellectual Property Organization International Bureau (43) International Publication Date (10) International Publication Number 12 February 2009 (12.02.2009) PCT WO 2009/020774 Al (51) International Patent Classification: (74) Agent: HUSEBO, Lars; Intellectual Property Law, P.O. C08G 18/36 (2006.01) C08G 18/66 (2006.01) Box 1967, Midland, Michigan 48641-1967 (US). C08G 18/48 (2006.01) (81) Designated States (unless otherwise indicated, for every kind of national protection available): AE, AG, AL, AM, (21) International Application Number: AO, AT,AU, AZ, BA, BB, BG, BH, BR, BW, BY, BZ, CA, PCT/US2008/071048 CH, CN, CO, CR, CU, CZ, DE, DK, DM, DO, DZ, EC, EE, EG, ES, FI, GB, GD, GE, GH, GM, GT, HN, HR, HU, ID, (22) International Filing Date: 24 July 2008 (24.07.2008) IL, IN, IS, JP, KE, KG, KM, KN, KP, KR, KZ, LA, LC, LK, LR, LS, LT, LU, LY,MA, MD, ME, MG, MK, MN, MW, (25) Filing Language: English MX, MY, MZ, NA, NG, NI, NO, NZ, OM, PG, PH, PL, PT, RO, RS, RU, SC, SD, SE, SG, SK, SL, SM, ST, SV, SY,TJ, (26) Publication Language: English TM, TN, TR, TT, TZ, UA, UG, US, UZ, VC, VN, ZA, ZM, ZW (30) Priority Data: 60/963,704 August 2007 (06.08.2007) US (84) Designated States (unless otherwise indicated, for every kind of regional protection available): ARIPO (BW, GH, GM, KE, LS, MW, MZ, NA, SD, SL, SZ, TZ, UG, ZM, (71) Applicant (for all designated States except US): DOW ZW), Eurasian (AM, AZ, BY, KG, KZ, MD, RU, TJ, TM), GLOBAL TECHNOLOGIES INC.