The Effect of Organosolv Pretreatment Variables on Enzymatic Hydrolysis of Sugarcane Bagasse
Total Page:16
File Type:pdf, Size:1020Kb
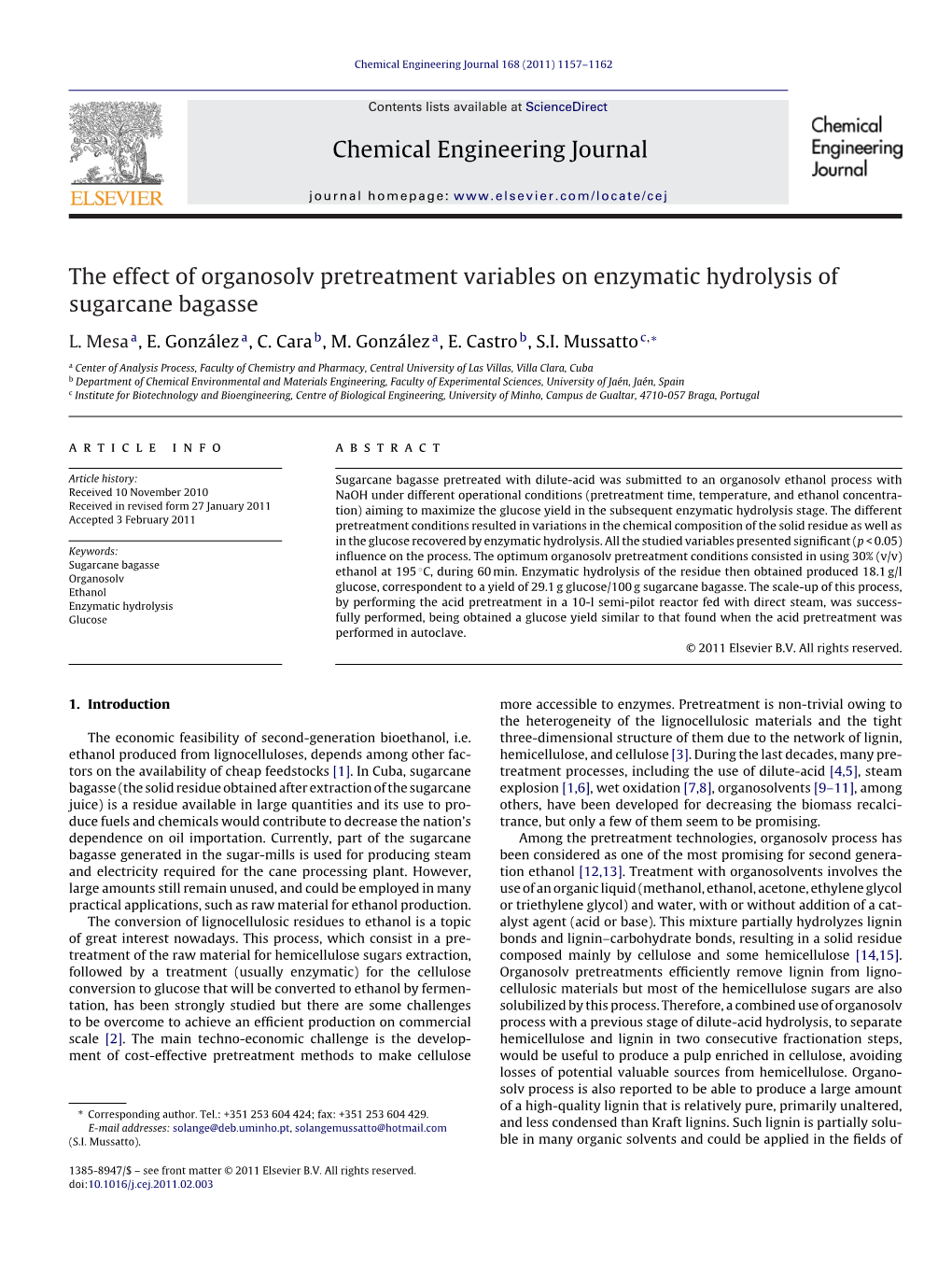
Load more
Recommended publications
-
Making! the E-Magazine for the Fibrous Forest Products Sector
PAPERmaking! The e-magazine for the Fibrous Forest Products Sector Produced by: The Paper Industry Technical Association Volume 5 / Number 1 / 2019 PAPERmaking! FROM THE PUBLISHERS OF PAPER TECHNOLOGY Volume 5, Number 1, 2019 CONTENTS: FEATURE ARTICLES: 1. Wastewater: Modelling control of an anaerobic reactor 2. Biobleaching: Enzyme bleaching of wood pulp 3. Novel Coatings: Using solutions of cellulose for coating purposes 4. Warehouse Design: Optimising design by using Augmented Reality technology 5. Analysis: Flow cytometry for analysis of polyelectrolyte complexes 6. Wood Panel: Explosion severity caused by wood dust 7. Agriwaste: Soda-AQ pulping of agriwaste in Sudan 8. New Ideas: 5 tips to help nurture new ideas 9. Driving: Driving in wet weather - problems caused by Spring showers 10. Women and Leadership: Importance of mentoring and sponsoring to leaders 11. Networking: 8 networking skills required by professionals 12. Time Management: 101 tips to boost everyday productivity 13. Report Writing: An introduction to report writing skills SUPPLIERS NEWS SECTION: Products & Services: Section 1 – PITA Corporate Members: ABB / ARCHROMA / JARSHIRE / VALMET Section 2 – Other Suppliers Materials Handling / Safety / Testing & Analysis / Miscellaneous DATA COMPILATION: Installations: Overview of equipment orders and installations since November 2018 Research Articles: Recent peer-reviewed articles from the technical paper press Technical Abstracts: Recent peer-reviewed articles from the general scientific press Events: Information on forthcoming national and international events and courses The Paper Industry Technical Association (PITA) is an independent organisation which operates for the general benefit of its members – both individual and corporate – dedicated to promoting and improving the technical and scientific knowledge of those working in the UK pulp and paper industry. -
( 12 ) United States Patent
US009902815B2 (12 ) United States Patent ( 10 ) Patent No. : US 9 ,902 , 815 B2 Tamminen et al. ( 45 ) Date of Patent: Feb . 27 , 2018 ( 54 ) FUNCTIONALIZED LIGNIN AND METHOD ( 58 ) Field of Classification Search OF PRODUCING THE SAME ??? . .. C07G 1 / 00 See application file for complete search history . @(71 ) Applicant : Teknologian tutkimuskeskus VTT , VTT (FI ) ( 56 ) References Cited U . S . PATENT DOCUMENTS @(72 ) Inventors : Tarja Tamminen , Espoo (FI ) ; Jarmo Ropponen , Espoo (FI ) ; Eva - Lena Hult , 2 ,429 , 102 A 10 / 1947 Lewis et al. Espoo ( FI) ; Kristiina Poppius- Levlin , 3 , 149 , 085 A 9 / 1964 Ball et al . Espoo (FI ) 4 ,017 ,430 A * 4 / 1977 Briggs .. .. .. 530 / 502 5 ,773 , 590 A * 6 / 1998 Hart 530 / 500 6 ,172 ,204 B1 * 1 /2001 Sarkanen et al. 530 /500 @(73 ) Assignee : Teknologian tutkimuskeskus VTT Oy, 2010 /0105798 A1 * 4 /2010 Hasegawa . .. .. 522 / 99 Espoo (FI ) 2010 /0152428 A1* 6 / 2010 Gifford et al . .. .. .. 530 / 504 2010 / 0204368 A1 * 8 / 2010 Benko et al. .. .. .. .. .. .. .. 524 / 73 ( * ) Notice : Subject to any disclaimer, the term of this 2010 / 0331531 A1 * 12 / 2010 Mykytka .. .. 530 / 501 patent is extended or adjusted under 35 2011/ 0263836 A1 * 10 / 2011 Vuorenpalo et al. .. .. 530 / 500 U . S . C . 154 ( b ) by 33 days. 2012 /0012035 A1 * 1 / 2012 Blank et al. .. .. 106 / 802 ( 21) Appl. No. : 14 /348 , 904 OTHER PUBLICATIONS (22 ) PCT Filed : Oct. 8 , 2012 Holmbom ( Journal of the American Oil Chemists Society , 1977 , p . 289 - 293 ) . * Stenberg et al . (Surface Coatings International Part B : Coatings ( 86 ) PCT No. : PCT/ FI2012 /050965 Transactions , vol. 88 , B2 , 83 - 156 , 2005 ) . -
What Happens to Cellulosic Fibers During Papermaking and Recycling? a Review
PEER-REVIEWED REVIEW ARTICLE ncsu.edu/bioresources WHAT HAPPENS TO CELLULOSIC FIBERS DURING PAPERMAKING AND RECYCLING? A REVIEW Martin A. Hubbe,* Richard A. Venditti, and Orlando J. Rojas Both reversible and irreversible changes take place as cellulosic fibers are manufactured into paper products one or more times. This review considers both physical and chemical changes. It is proposed that by understanding these changes one can make better use of cellulosic fibers at various stages of their life cycles, achieving a broad range of paper performance characteristics. Some of the changes that occur as a result of recycling are inherent to the fibers themselves. Other changes may result from the presence of various contaminants associated with the fibers as a result of manufacturing processes and uses. The former category includes an expected loss of swelling ability and decreased wet-flexibility, especially after kraft fibers are dried. The latter category includes effects of inks, de-inking agents, stickies, and additives used during previous cycles of papermaking. Keywords: Paper recycling, Drying, Deinking, Hornification, Inter-fiber bonding, Refining, Fines, Fiber length, Conformability Contact information: Department of Forest Biomaterials Science and Engineering, Box 8005, North Carolina State University, Raleigh, NC 27695-8005, USA; *Corresponding author: [email protected] INTRODUCTION Cellulosic fibers can change significantly when formed into a wet web of paper and subsequently subjected to such processes as pressing, drying, printing, storage, repulping, and deinking. Some of the changes can be subtle. Often it is possible to substitute recovered fibers in place of virgin fibers used for the production of paper or paperboard. On the other hand, characteristic differences between recycled fibers and virgin fibers (fresh from pulping wood, not recycled) can be expected; many of these can be attributed to drying. -
Fungal Pretreatment for Organosolv Pulping and Dissolving Pulp Production
13 Fungal Pretreatment for Organosolv Pulping and Dissolving Pulp Production ANDRÉ FERRAZ, LYUDMIL CHRISTOV, AND MASOOD AKHTAR INTRODUCTION Biopulping is the fungal pretreatment of wood chips, designed as a solid-state fer- mentation process, for production of mechanical or chemical pulps (cf. Chapters 10 and 12). The concept of biopulping is based on the ability of some white-rot fungi to colonize and degrade selectively the lignin in wood, thereby leaving the cellulose relatively intact. This chapter presents an evaluation of biopulping and biobleaching with white-rot fungi as pretreatment steps in organosolv pulping and in dissolving pulp production. Fungal-organosolv pulping is focused mainly on chemical and topo- chemical bases for the combination of biopulping and organosolv processes. Experi- mental data are presented to illustrate the potential of this fungal-chemical method to produce wood pulps. Biopulping and biobleaching with selected white-rot fungi are also evaluated as potential methods for production of dissolving pulp. A report in part has been submitted for publication in Enzyme and Microbial Technology. This chapter is based mainly on the work from a collaborative project between the Department of Microbiology and Biochemistry, The University of Orange Free State, of Bloemfontein South Africa and the USDA Forest Products Laboratory in Madison, Wisconsin. Fungal-organosolv pulping methods are based mainly on the work developed at the Department of Biotechnology in Lorena, Brazil, and the Renewable Resource Laboratory in Concepcion, Chile. ORGANOSOLV PULPING Background The need to find new technologies for pulp and paper production that cause less environmental impact has contributed to an increase in the number of studies on Environmentally Friendly Technologies for the Pulp and Paper Industry, edited by Raymond A. -
Value Chains for Production of Renewable Transportation Fuels Using Intermediates - Case Studies for Bio-Oils in Refinery Applications and Bio-Sng
REPORT f3 2016:05 VALUE CHAINS FOR PRODUCTION OF RENEWABLE TRANSPORTATION FUELS USING INTERMEDIATES - CASE STUDIES FOR BIO-OILS IN REFINERY APPLICATIONS AND BIO-SNG Report from an f3 project June 2016 Authors: Marie Anheden, Christian Ehn & Valeria Lundberg, INNVENTIA AB Karin Pettersson, Chalmers University of Technology Malin Fugelsang & Carl Johan Hjerpe, ÅF Industri AB Åsa Håkansson, Preem AB Ingemar Gunnarsson, Göteborg Energi AB VALUE CHAINS FOR PRODUCTION OF RENEWABLE TRANSPORTATION FUELS USING INTERMEDIATES PREFACE This report is the result of a collaborative project within the Swedish Knowledge Centre for Renewa- ble Transportation Fuels (f3). f3 is a networking organization, which focuses on development of envi- ronmentally, economically and socially sustainable renewable fuels, and Provides a broad, scientifically based and trustworthy source of knowledge for industry, gov- ernments and public authorities, Carries through system oriented research related to the entire renewable fuels value chain, Acts as national platform stimulating interaction nationally and internationally. f3 partners include Sweden’s most active universities and research institutes within the field, as well as a broad range of industry companies with high relevance. f3 has no political agenda and does not con- duct lobbying activities for specific fuels or systems, nor for the f3 partners’ respective areas of inter- est. The f3 centre is financed jointly by the centre partners, the Swedish Energy Agency and the region of Västra Götaland. f3 also receives funding from Vinnova (Sweden’s innovation agency) as a Swedish advocacy platform towards Horizon 2020. Chalmers Industriteknik (CIT) functions as the host of the f3 organization (see www.f3centre.se). The project is financed and carried out within the f3 - Energimyndigheten (Swedish Energy Agency) collaborative research program “Förnybara drivmedel och system” (Renewable transportation fuels and systems). -
CNC) from Eucalyptus Published: Xx Xx Xxxx Hardwood Renli Zhang & Yun Liu
www.nature.com/scientificreports OPEN High energy oxidation and organosolv solubilization for high yield isolation of cellulose Received: 23 April 2018 Accepted: 18 October 2018 nanocrystals (CNC) from Eucalyptus Published: xx xx xxxx hardwood Renli Zhang & Yun Liu Cellulose nanocrystals (CNC) have been widely used as responsive materials, chiral templates, and tough nano-composites due to its unparalleled properties. Acid and enzyme hydrolyses are extensively employed to prepare CNC. These traditional approaches exhibit inherent limitations of corrosion hazards, time-consuming process, and/or low yield. Herein, irradiation oxidation and organosolv solubilization are conducted to cause rapid degradation with simultaneous crystallization of cellulose to achieve approx. 87% yield of CNC. The morphology, spectroscopic, and stability properties of the as-prepared CNC are characterized through UV-vis spectroscopy, zetal potential, XRD, TEM, DLS, GPC, FT-IR and TGA techniques. The resultant CNC suspension presents unique property with high stability after 9 months storage at 4 °C. Moreover, CNC liquid crystal phase is successfully generated by addition of anions or cations solution to the CNC aqueous dispersion without stirring. The innovative approach in this work opens an avenue to obtain CNC directly from lignocellulosic biomass through irradiation oxidation and organosolv solubilization without acid hydrolysis and washing procedure. Cellulose, lignin and hemicellulose are the three principal structural components of lignocellulosic biomass. -
USE of NONWOOD PLANT FIBERS for PULP and PAPER INDUSTRY in ASIA: POTENTIAL in CHINA by Mudit Chandra Dr
USE OF NONWOOD PLANT FIBERS FOR PULP AND PAPER INDUSTRY IN ASIA: POTENTIAL IN CHINA By Mudit Chandra Degree Paper Submitted to the Faculty of Virginia Polytechnic Institute and State University in Partial Fulfillment of the Requirements for the Degree of MASTER OF FORESTRY IN WOOD SCIENCE AND FOREST PRODUCTS APPROVED: A. L. Hammett, Chairman J. D. Dolan C. D. West August, 1998 Blacksburg, Virginia USE OF NONWOOD PLANT FIBERS FOR PULP AND PAPER INDUSTRY IN ASIA: POTENTIAL IN CHINA by Mudit Chandra Dr. A. L. Hammett, Chairman Department of Wood Science and Forest Products (ABSTRACT) The pulp and paper industry around the world has been growing rapidly. As a result there has been a huge demand for pulp and paper making raw material. Recent years have seen a spurt in use of nonwood fibers being used as a raw material for this purpose. Although some of the nonwood fibers used for papermaking are used because of their fine paper making qualities, majority of nonwood fibers is used to overcome the shortage of wood fibers. As a result their use is more widespread in countries with shortage of wood. The use of nonwood fibers in pulp and paper industry is fraught with problems. Right from supply of raw material to the properties of finished paper, majority of nonwood raw material has proven to be economically inferior to wood. But over the last few years, technological breakthrough in almost all the fields of papermaking have made nonwood more competitive with wood as a raw material for papermaking. Although till recently, use of nonwood fibers for pulp and paper making was concentrated in countries with limited wood supply, it is now showing an increasing trend even in countries with adequate wood supply due to environmental considerations. -
Pretreatment Options for Refining Lignocelluloses
Pretreatment Options for Refining Lignocelluloses Juergen Puls vTI-Institute for Wood Technology and Wood Biology Hamburg IEA Task 42 Workshop on Biorefineries Outline 1. Raw material basis 2. Lignocellulose composition 3. Pulping processes for biorefineries? 4. Pretreatment processes with options for component separation 5. Lignocellulose biorefinery based on organosolv pretreatment 6. Lignin as the high-value product of the lignocellulose biorefinery 7. Conclusion J. Puls: IEA Task 42 Workshop on Biorefineries Storage of Wood in Forest (billion m³) 3.0 2.5 Germany 2.0 Annual increment: 60 mill. m³ Annual harvest: 42 mill. m³ 1.5 1.0 0.5 0 s d nd a France Finlan Belaru Norway Germany Sweden Switzerl J. Puls: IEA Task 42 Workshop on Biorefineries Characteristic differences between softwood, hardwood, and residues of annual plants Softwood Hardwood Annual plants 1.) Galactoglucomannan (15-20%) Acetyl-4-0-MeGluA-Xylan (20-30%) Feruloyl- & p-Coumaroyl (Hexosane) (Pentosane) substituted Arabino-4-0- • Partly high acetyl content MeGluA-Xylan (18-35%) (Beech: 6% acetic acid) (Pentosane) 2.) Ara-4-0-MeGluA-Xylan (8-12%) (Pentosane) • Partly high proportion of extractives • Partly high ash content • Small acetyl content Strongly cross-linked lignin (28-30%) Less cross-linked lignin (18-22%) Least cross-linked lignin (10-22%) J. Puls: IEA Task 42 Workshop on Biorefineries Pulp Mills and Pulp Production in Germany Capacity Mill Process Raw material Integration (t / year) Alfeld (SAPPI) Mg-Sulphite Spruce 75.000 yes Beech 40.000 Ehingen (SAPPI) Mg-Sulphite Buche 100.000 yes Spruce 30.000 Mannheim (SCA) Mg-Sulphite Spruce 180.000 yes Beech 40.000 Stockstadt (SAPPI) Mg-Sulphite Beech 140.000 yes Blankenstein (Mercer) Kraft Spruce/ 300.000 no Pine Stendal (Mercer) Kraft Pine/ 550.000 no Spruce/ total capacity (t / year) 1,455.000 J. -
A Review on the Lignin Biopolymer and Its Integration in the Elaboration of Sustainable Materials
sustainability Review A Review on the Lignin Biopolymer and Its Integration in the Elaboration of Sustainable Materials Francisco Vásquez-Garay 1,*, Isabel Carrillo-Varela 2, Claudia Vidal 2, Pablo Reyes-Contreras 1 , Mirko Faccini 1 and Regis Teixeira Mendonça 2,3 1 Centro de Excelencia en Nanotecnología (CEN), Santiago 7500724, Chile; [email protected] (P.R.-C.); [email protected] (M.F.) 2 Laboratorio de Recursos Renovables, Centro de Biotecnología, Universidad de Concepción, Concepción 4030000, Chile; [email protected] (I.C.-V.); [email protected] (C.V.); [email protected] (R.T.M.) 3 Facultad de Ciencias Forestales, Casilla 160-C, Universidad de Concepción, Concepción 4030000, Chile * Correspondence: [email protected] Abstract: Lignin is one of the wood and plant cell wall components that is available in large quantities in nature. Its polyphenolic chemical structure has been of interest for valorization and industrial application studies. Lignin can be obtained from wood by various delignification chemical processes, which give it a structure and specific properties that will depend on the plant species. Due to the versatility and chemical diversity of lignin, the chemical industry has focused on its use as a viable alternative of renewable raw material for the synthesis of new and sustainable biomaterials. However, its structure is complex and difficult to characterize, presenting some obstacles to be integrated into mixtures for the development of polymers, fibers, and other materials. The objective of this review is to present a background of the structure, biosynthesis, and the main mechanisms of lignin recovery Citation: Vásquez-Garay, F.; from chemical processes (sulfite and kraft) and sulfur-free processes (organosolv) and describe the Carrillo-Varela, I.; Vidal, C.; different forms of integration of this biopolymer in the synthesis of sustainable materials. -
IEA Bioenergy Task42 Biorefining Deals with Knowledge Building and Exchange Within the Area of Biorefining, I.E
IEA Bioenergy is an international collaboration set-up in 1978 by the International Energy Agency (IEA) to improve international co-operation and information exchange between national bioenergy RD&D programmes. Its Vision is that bioenergy is, and will continue to be a substantial part of the sustainable IEA BIOENERGY use of biomass in the BioEconomy. By accelerating the sustainable production and use of biomass, particularly in a Task42 Biorefining approach, the economic and environmental impacts will be optimised, resulting in more cost-competitive BIOREFINING bioenergy and reduced greenhouse gas emissions. Its Mission is facilitating the commercialisation and market deployment of environmentally sound, socially acceptable, and cost-competitive bioenergy systems and technologies, and to advise policy and industrial decision makers accordingly. Its Strategy is to provide platforms for international FOOD FEED collaboration and information exchange, including the development of networks, dissemination of information, and provision of science-based technology BIOENERGY (FUELS, POWER, HEAT) analysis, as well as support and advice to policy makers, involvement of industry, and encouragement of membership by countries with a strong bioenergy CHEMICALS MATERIALS infrastructure and appropriate policies. Gaps and barriers to deployment will be addressed to successfully promote sustainable bioenergy systems. The purpose of this brochure is to provide an unbiased, authoritative statement on biorefining in general, and of the specific activities -
Modified Organosolv As a Fractionation Process of Lignocellulosic Biomass for Co-Production of Fuels and Chemicals
Confidential Modified organosolv as a fractionation process of lignocellulosic biomass for co-production of fuels and chemicals W.J.J. Huijgen R.R. van der Laan J.H. Reith ECN-M--08-034 MAY 2008 ECN-M--08-034 Confidential 2 MODIFIED ORGANOSOLV AS A FRACTIONATION PROCESS OF LIGNOCELLULOSIC BIOMASS FOR CO- PRODUCTION OF FUELS AND CHEMICALS Huijgen W.J.J.*, Van der Laan R.R. & Reith J.H. Energy research Centre of the Netherlands (ECN), Biomass, Coal & Environmental Research unit P.O. Box 1, 1755 ZG Petten, The Netherlands. * Corresponding author: Wouter Huijgen, Phone: +31 224 568162, Fax: +31 224 568487, E-mail: [email protected] ABSTRACT: Modified organosolv is a process by which lignocellulosic biomass can be fractionated into its three main constituents, i.e. hemicellulose, cellulose and lignin. In the process, lignocellulosic biomass is brought into contact with an organic solvent-water mixture at elevated temperature and pressure. Thus, lignin is extracted from the biomass and hemicellulose is hydrolysed, while the solid residue (mainly cellulose) is made more accessible for enzymatic hydrolysis in the subsequent process step. The goal is to achieve full fractionation of all biomass fractions, including lignin, in a sufficient quality for production of (bio)chemicals. In this work, the effect of process conditions applied, type of organic solvent and the use of catalysts is explored. Keywords: biomass pre-treatment, biorefining, lignin. 1 INTRODUCTION Previously, we presented the first results of our work In the biorefinery approach, the aim is to make on a modified organosolv process using willow wood, optimal use of the existing chemical functionalities in ethanol-water mixtures in combination with the use of biomass by fractionation of the main constituents for CO2 as a catalyst [5]. -
Structural and Compositional Changes in Sugarcane Bagasse Subjected to Hydrothermal and Organosolv Pretreatments and Their Impac
Industrial Crops & Products 113 (2018) 64–74 Contents lists available at ScienceDirect Industrial Crops & Products journal homepage: www.elsevier.com/locate/indcrop Structural and compositional changes in sugarcane bagasse subjected to T hydrothermal and organosolv pretreatments and their impacts on enzymatic hydrolysis Melissa Espirito Santoa, Camila A. Rezendeb, Oigres D. Bernardinellia, Nei Pereira Jr.c, ⁎ Antonio A.S. Curvelod, Eduardo R. deAzevedoa, Franscisco E.G. Guimarãesa, Igor Polikarpova, a Department of Physics and Interdisciplinary Science, São Carlos Institute of Physics, University of São Paulo, Av. Trabalhador São-carlense, 400, São Carlos, SP, 13566- 590, Brazil b Institute of Chemistry, University of Campinas, P.O. Box 6154, Campinas, SP, 13083-970, Brazil c Biochemical Engineering Department, School of Chemistry, Federal University of Rio de Janeiro (UFRJ), Block E, Room 121, Ilha do Fundão, 21949-900, Rio de Janeiro, RJ, Brazil d Department of Physical-Chemistry, Institute of Chemistry of São Carlos, University of São Paulo, Av. Trabalhador Sãocarlense, 400, São Carlos, SP, 13566-590, Brazil ARTICLE INFO ABSTRACT Keywords: Economical sustainability of cellulosic ethanol technology still requires considerable improvements in efficacies Sugarcane bagasse of both pretreatment and enzymatic hydrolysis steps. In this work a number of physical techniques were applied Enzymatic hydrolysis to characterize sugarcane bagasse samples that underwent hydrothermal and/or organosolv pretreatments under Bioethanol variable conditions and to correlated the observed changes with the efficiency of enzymatic hydrolysis. Confocal Pretreatments and field emission scanning electron microscopy studies revealed morphological changes in lignin distribution in Biophysical investigations the plant cell wall. The hydrothermal pretreatment caused a disorder in the arrangement of the lignin, whereas organosolv pretreatment partially removed lignin from bagasse and fraction of it redeposited at the surfaces of cellulose fibers.