Markov Models for Mixing of Powders in Static Mixers
Total Page:16
File Type:pdf, Size:1020Kb
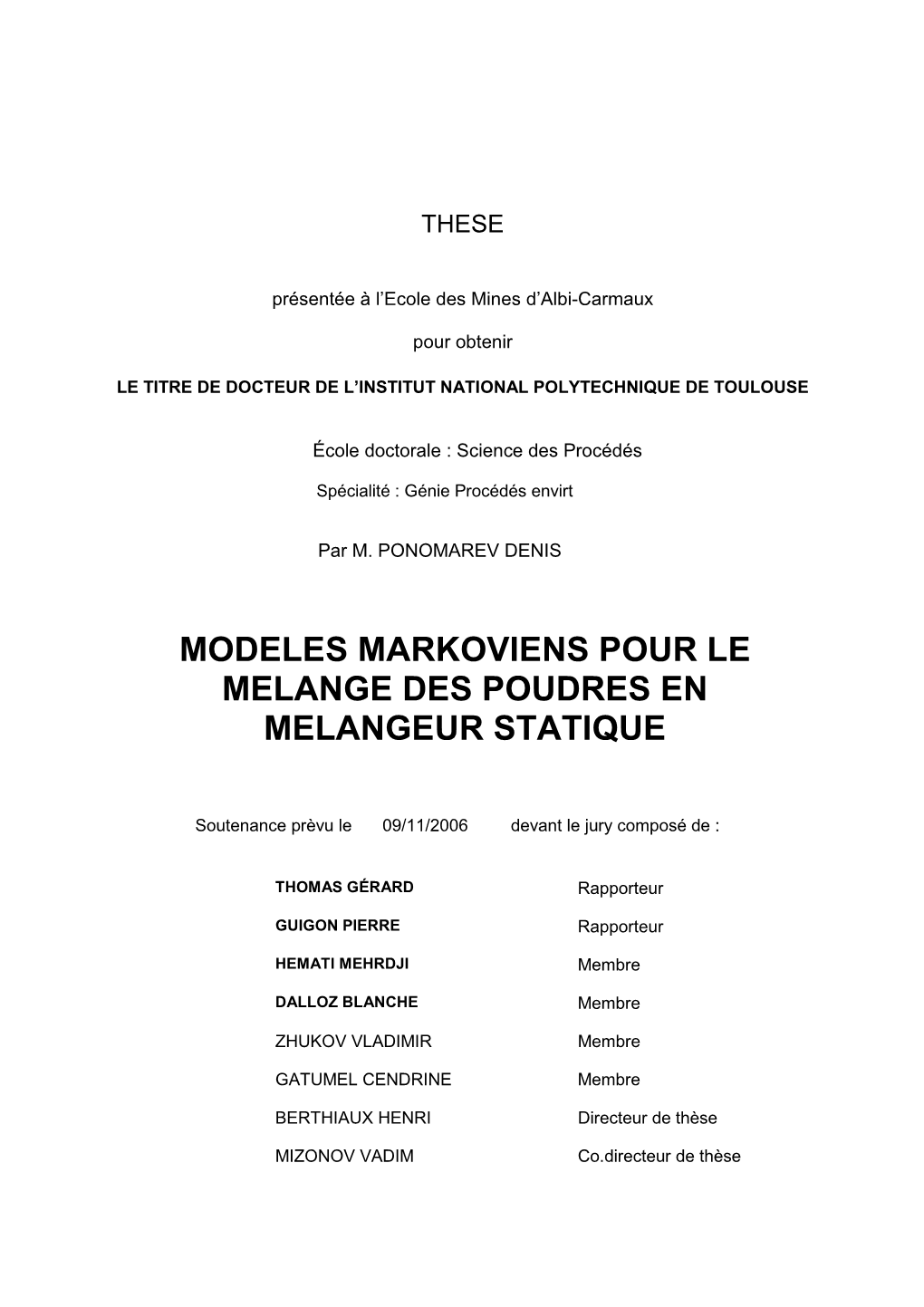
Load more
Recommended publications
-
How to Choose a Static Mixer to Properly Mix a 2-Component Adhesive"
"CHOOSING A STATIC MIXER" "HOW TO CHOOSE A STATIC MIXER TO PROPERLY MIX A 2-COMPONENT ADHESIVE" BY David W. Kirsch Choosing a static mixer requires more than reading a sales catalog and selecting a part number. Adhesive manufacturers and end users both should investigate many variables when evaluating mixer characteristics for specific applications. This article is a guide to help make the right decision when choosing a static mixer to properly mix a 2- component adhesive. A static mixer, which sometimes is called a motionless mixer, is a simple device with no moving parts, and consists of a series of internal baffles or elements within a plastic tube. Yet this seemingly elementary product is used to effectively mix 2 flowable liquids in what can be a very complicated process. As adhesive components are forced through the mixer, they are repeatedly divided and recombined, thus creating a complete and uniform mixture. Static mixer systems are frequently chosen when users encounter too many difficulties with conventional adhesive handling systems, such as when components are scooped into a cup, hand mixed and transferred to a dispensing container. Utilizing a static mixer provides many benefits, including consistency of mix and eliminating the introduction of air into the mixing. The latter is an essential precaution, since air represents a source of voids in cured bond lines and the possibility of a bonding failure. Overall, process control in hand mixing is difficult to maintain, which can create serious bonding problems, as well as problems with waste, cost, and safety. This overview will not evaluate or compare a static mixer vs. -
Motionless Mixers in Bulk Solids Treatments – a Review†
Motionless Mixers in Bulk Solids Treatments – A Review† J. Gyenis University of Kaposvar Research Institute of Chemical and Process Engineering* Abstract In this paper the general features, behavior and application possibilities of motionless mixers in mixing and treatments of bulk solids are overviewed, summarizing the results published during the last three decades. Working principles, mechanisms, performance, modeling and applications of these devices are described. Related topics, such as use in particle coating, pneumatic conveying, contacting, flow improvement, bulk volume reduction, and dust separation are also summarized. recombining of different parts of materials are com- 1. Introduction mon mechanisms in this respect, both in fluids and Motionless or static mixers are widely known and bulk solids. applied in process technologies for the mixing of liq- Motionless mixers eliminate the need for mechani- uids, especially for highly viscous materials, and to cal stirrers and therefore have a number of benefits: contact different phases to enhance heat and mass No direct motive power, driving motor and electrical transfer. Producing dispersions in two- and multi- connections are necessary. The flow of materials phase systems such as emulsions, suspensions, (even particulate flow) through them may be induced foams, etc., is also the common aim of using motion- either by gravity, pressure difference or by utilizing less mixers. Far less information is known on their the existing potential or kinetic energy. The space behavior, capabilities and applications in bulk solids requirement is small, allowing a compact design of treatments. Although investigations started more equipment in bulk solids treatments. Installation is than thirty years ago in this field, research and devel- easy and quick, e.g. -
The Development of a Colour 3D Food Printing System
Copyright is owned by the Author of the thesis. Permission is given for a copy to be downloaded by an individual for the purpose of research and private study only. The thesis may not be reproduced elsewhere without the permission of the Author. The Development of a Colour 3D Food Printing System A thesis presented in partial fulfilment of the requirements for the degree of Masters of Engineering In Mechatronics At Massey University, Palmerston North, New Zealand Caleb Ian Millen 2012 Abstract Foods are becoming more customised and consumers want food that tastes great, looks great and is healthy. Food printing, a method of distributing food in a personalised manner, is one way to satisfy this demand. The overarching goal of this research is to develop the ability to print coloured images with food, but this thesis focuses on a subsection of that research. It aims to establish a broad base for future research in the area of food printing, present the design and development of mixing techniques applicable to food printing and finally use image processing to examine the distribution of colour in images likely to be printed. By developing and testing various components and systems of the existing food printer and by performing a broad review of relevant literature, future researchers will be able to progress topics identified as essential in this field. Photographs of samples mixed using selected mixing techniques were analysed in order to produce qualitative and quantitative results. Six sample images were processed in such a way that colour distribution values were able to be used to estimate the average distances a food printing machine head would have to move between successive deposited volume elements while using discontinuous flow. -
PPG Semco® Packaging & Application Systems
PPG Semco® Packaging & Application Systems • • At PPG, we work every day to develop and deliver the paints, coatings and materials• that our customers have trusted for 135 years. Through dedication and creativity, we solve our customers’ biggest challenges, collaborating• closely to find the right path forward. With headquarters in Pittsburgh, we operate and innovate in more than 70 countries. • We serve customers in construction, consumer products, industrial and transportation markets and aftermarkets. We are a leader in all our markets: construction, consumer products, industrial and transportation markets and aftermarkets. Packaging & Application Systems Application support centers (ASCs) We have over 50 years of experience in handling the packaging and dispensing of a variety of materials. Our superior products are available through a global network of PPG application support centers. These facilities are strategically located to provide customers with local service and product support. In addition, each ASC location aims to stock material based on their customers' needs, so that we can deliver our products to your assembly line quickly, safely, and cost-effectively. Putting our expertise to the test Our application support center network was specifically created to provide our customers with the benefit of our knowledge and experience. Let our packaging experts put these skills to work for your company. They can help find ways to improve your manufacturing process using our products and services. We also offer a wide range of chemical packaging services (CPS) through our facilities. In our CPS business, we utilize PPG's trained personnel and aerospace quality standards to repackage third-party sealants, adhesives and other chemicals, both as a toll packager and for each end customer. -
Effect of Radiation on Polymerization, Microstructure, and Microbiological
University of Vermont ScholarWorks @ UVM Graduate College Dissertations and Theses Dissertations and Theses 2015 Effect of radiation on polymerization, microstructure, and microbiological properties of whey protein in model system and whey protein based tissue adhesive development Ning Liu University of Vermont Follow this and additional works at: https://scholarworks.uvm.edu/graddis Part of the Food Science Commons Recommended Citation Liu, Ning, "Effect of radiation on polymerization, microstructure, and microbiological properties of whey protein in model system and whey protein based tissue adhesive development" (2015). Graduate College Dissertations and Theses. 521. https://scholarworks.uvm.edu/graddis/521 This Thesis is brought to you for free and open access by the Dissertations and Theses at ScholarWorks @ UVM. It has been accepted for inclusion in Graduate College Dissertations and Theses by an authorized administrator of ScholarWorks @ UVM. For more information, please contact [email protected]. EFFECT OF RADIATION ON POLYMERIZATION, MICROSTRUCTURE, AND MICROBIOLOGICAL PROPERTIES OF WHEY PROTEINS IN MODEL SYSTEM AND WHEY PROTEIN BASED TISSUE ADHESIVE DEVELOPMENT A Thesis Presented by Ning Liu to The Faculty of the Graduate College of The University of Vermont In Partial Fulfillment of the Requirements for the Degree of Master of Science Specializing in Nutrition and Food Sciences May, 2015 Defense Date: March 10, 2015 Thesis Examination Committee: Mingruo Guo, Ph.D., Advisor Philip M.Lintilhac, Ph.D., Chairperson Stephen J. Pintauro, Ph.D. Cynthia J. Forehand, Ph.D., Dean of the Graduate College ABSTRACT Whey proteins are mainly a group of small globular proteins. Their structures can be modified by physical, chemical and other means to improve their functionality. -
The Assembly and Use of Continuous-Flow Systems for Chemical Synthesis
The Assembly and Use of Continuous Flow Systems for Chemical Synthesis The MIT Faculty has made this article openly available. Please share how this access benefits you. Your story matters. Citation Britton, Joshua, and Timothy F. Jamison. “The Assembly and Use of Continuous Flow Systems for Chemical Synthesis.” Nature Protocols, vol. 12, no. 11, Oct. 2017, pp. 2423–46. As Published http://dx.doi.org/doi:10.1038/nprot.2017.102 Publisher Nature Publishing Group Version Author's final manuscript Citable link http://hdl.handle.net/1721.1/114610 Terms of Use Article is made available in accordance with the publisher's policy and may be subject to US copyright law. Please refer to the publisher's site for terms of use. The Assembly and Use of Continuous-Flow Systems for Chemical Synthesis Dr. Joshua Britton and Prof. Dr. Timothy F. Jamison* Department of Chemistry, Massachusetts Institute of Technology, 77 Massachusetts Avenue, Cambridge, MA 02139 (USA) Abstract The adoption and opportunities in continuous-flow chemical synthesis (“flow chemistry”) have increased significantly over the past several years. Nevertheless, while several continuous-flow platforms are commercially available, ‘in-lab’ constructed systems provide researchers with a flexible, versatile, and cost-effective alternative. Herein, we describe how to assemble modular continuous-flow apparatus from readily available and affordable parts in as little as 30 minutes. Furthermore, our experiences in single- and multi-step continuous-flow synthesis have been documented to provide solutions to commonly encountered technical problems. Following this Protocol, a non-specialist can assemble a continuous-flow system from reactor coils, syringes, in-line liquid-liquid separators, drying columns, back pressure regulators, static mixers, and packed bed reactors. -
Biodiesel Production Using Static Mixers
BIODIESEL PRODUCTION USING STATIC MIXERS J. C. Thompson, B. B. He ABSTRACT. Static mixers, devices used for mixing immiscible liquids in a compact configuration, were found to be effective in carrying out initial transesterification reactions of canola oil and methanol. The objective of this study was to explore the possibilities of using static mixers as a continuous-flow reactor for biodiesel production. Biodiesel (canola methyl ester) was produced under varying conditions using a closed-loop static mixer system. Sodium methoxide was used as the catalyst. Process parameters of flow rate or mixing intensity, catalyst concentration, reaction temperature, and reaction time were studied. A full-factorial experimental design was employed, and samples were analyzed for unreacted glycerides as an indicator for biodiesel quality control. It was found that static mixers can be used for biodiesel production. In fact, given enough residence time, appropriate temperature, and high mixing rate, a reactor could consist solely of static mixers and pumps in a continuous-flow design. Temperature and catalyst concentration had the most influence on the transesterification reaction. The data clearly indicates separate inverse linear relationships between temperature and catalyst concentration verses total glycerin. The ASTM D6584 specification for total glycerin (0.24% wt, max.) was met at three of the four temperatures tested, utilizing two of the four catalyst concentrations. The most favorable conditions for completeness of reaction were at 60°C and 1.5% catalyst for 30 min. Keywords. Biodiesel, Continuous flow, Reactor, Sodium methoxide, Static mixer. lobal oil reserves are in decline, markets are be- that a high percentage, up to 80%, of the reaction was accom- coming more competitive, many of the oil-pro- plished in a short retention time (less than 5 min) in the static ducing countries are becoming unstable, and mixers placed prior to the RD column. -
Quantifying Mixing Using Magnetic Resonance Imaging
Journal of Visualized Experiments www.jove.com Video Article Quantifying Mixing using Magnetic Resonance Imaging Emilio J. Tozzi1, Kathryn L. McCarthy1, Lori A. Bacca2, William H. Hartt2, Michael J. McCarthy1 1 Dept. Food Science and Technology, University of California, Davis 2 Corporate Engineering and Technology Laboratory, Procter & Gamble Company Correspondence to: Michael J. McCarthy at [email protected] URL: https://www.jove.com/video/3493 DOI: doi:10.3791/3493 Keywords: Biophysics, Issue 59, Magnetic resonance imaging, MRI, mixing, rheology, static mixer, split-and-recombine mix Date Published: 1/25/2012 Citation: Tozzi, E.J., McCarthy, K.L., Bacca, L.A., Hartt, W.H., McCarthy, M.J. Quantifying Mixing using Magnetic Resonance Imaging. J. Vis. Exp. (59), e3493, doi:10.3791/3493 (2012). Abstract Mixing is a unit operation that combines two or more components into a homogeneous mixture. This work involves mixing two viscous liquid streams using an in-line static mixer. The mixer is a split-and-recombine design that employs shear and extensional flow to increase the interfacial contact between the components. A prototype split-and-recombine (SAR) mixer was constructed by aligning a series of thin laser- cut Poly (methyl methacrylate) (PMMA) plates held in place in a PVC pipe. Mixing in this device is illustrated in the photograph in Fig. 1. Red dye was added to a portion of the test fluid and used as the minor component being mixed into the major (undyed) component. At the inlet of the mixer, the injected layer of tracer fluid is split into two layers as it flows through the mixing section. -
Nanoparticles Using Static Mixers
University of Kentucky UKnowledge University of Kentucky Master's Theses Graduate School 2008 PROCESS FOR FORMATION OF CATIONIC POLY (LACTIC-CO- GLYCOLIC ACID) NANOPARTICLES USING STATIC MIXERS Yamuna Reddy Charabudla University of Kentucky Right click to open a feedback form in a new tab to let us know how this document benefits ou.y Recommended Citation Charabudla, Yamuna Reddy, "PROCESS FOR FORMATION OF CATIONIC POLY (LACTIC-CO-GLYCOLIC ACID) NANOPARTICLES USING STATIC MIXERS" (2008). University of Kentucky Master's Theses. 580. https://uknowledge.uky.edu/gradschool_theses/580 This Thesis is brought to you for free and open access by the Graduate School at UKnowledge. It has been accepted for inclusion in University of Kentucky Master's Theses by an authorized administrator of UKnowledge. For more information, please contact [email protected]. ABSTRACT OF THESIS PROCESS FOR FORMATION OF CATIONIC POLY (LACTIC-CO-GLYCOLIC ACID) NANOPARTICLES USING STATIC MIXERS Nanoparticles have received special attention over past few years as potential drug carriers for proteins/peptides and genes. Biodegradable polymeric poly (lactic-co-glycolic acid) (PLGA) nanoparticles are being employed as non-viral gene delivery systems for DNA. This work demonstrates a scalable technology for synthesis of nanoparticles capable of gene delivery. Cationic PLGA nanoparticles are produced by emulsion- diffusion-evaporation technique employing polyvinyl alcohol (PVA) as stabilizer and chitosan chloride for surface modification. A sonicator is used for the emulsion step and a static mixer is used for dilution in the diffusion step of the synthesis. A static mixer is considered ideal for the synthesis of PLGA nanoparticles as it is easily scalable to industrial production. -
Evaluating 3D Printing to Solve the Sample-To- Device
1. C h a p t e r 4 EVALUATING 3D PRINTING TO SOLVE THE SAMPLE-TO- DEVICE INTERFACE FOR LRS AND POC DIAGNOSTICS: EXAMPLE OF AN INTERLOCK METER-MIX DEVICE FOR METERING AND LYSING CLINICAL URINE SAMPLES E. Jue, N.G. Schoepp, D. Witters, and R.F. Ismagilov. 2016. Lab on a Chip. 16:1852-1860. doi:10.1039/c6lc00292g Abstract This chapter evaluates the potential of 3D printing, a semi-automated additive prototyping technology, as a means to design and prototype a sample-to-device interface, amenable to diagnostics in limited-resource settings, where speed, accuracy, and user-friendly design are critical components. As a test case, we built and validated an interlock meter-mix device for accurately metering and lysing human urine samples for use in downstream nucleic acid amplification. Two plungers and a multivalve generated and controlled fluid flow through the device and demonstrate the utility of 3D printing to create leak-free seals. Device operation consists of three simple steps that must be performed sequentially, eliminating manual pipetting and vortexing to provide rapid (5 to 10 s) and accurate metering and mixing. Bretherton's prediction was applied, using the Bond number to guide a design that prevents potentially biohazardous samples from leaking from the device. We employed multi-material 3D printing technology, which allows composites with rigid and elastomeric properties to be printed as a single part. To validate the meter-mix device with a clinically relevant sample, we used urine spiked with inactivated Chlamydia Trachomatis and Neisseria gonorrhoeae. A downstream nucleic acid amplification by quantitative PCR (qPCR) confirmed there was no statistically significant difference between samples metered and mixed using the standard protocol and those prepared with the meter-mix device, showing the 3D-printed device could accurately meter, mix, and dispense a human urine sample without loss of nucleic acids. -
Effects of Static Mixer Geometry on Polyurethane Properties
The University of Southern Mississippi The Aquila Digital Community Honors Theses Honors College 5-2021 Effects of Static Mixer Geometry on Polyurethane Properties Christian R. Dixon Follow this and additional works at: https://aquila.usm.edu/honors_theses Part of the Polymer and Organic Materials Commons Recommended Citation Dixon, Christian R., "Effects of Static Mixer Geometry on Polyurethane Properties" (2021). Honors Theses. 796. https://aquila.usm.edu/honors_theses/796 This Honors College Thesis is brought to you for free and open access by the Honors College at The Aquila Digital Community. It has been accepted for inclusion in Honors Theses by an authorized administrator of The Aquila Digital Community. For more information, please contact [email protected]. Effects of Static Mixer Geometry on Polyurethane Properties by Christian Robert Dixon A Thesis Submitted to the Honors College of The University of Southern Mississippi in Partial Fulfillment of Honors Requirements May 2021 iii Approved by: Jeffrey Wiggins, Ph.D., Thesis Advisor, School of Polymer Science and Engineering Derek Patton, Ph.D., Director, School of Polymer Science and Engineering Ellen Weinauer, Ph.D., Dean Honors College iii ABSTRACT The field of additive manufacturing has gained significant academic interest in the past few decades with a recently developed type of three-dimensional (3D) printing. Reactive extrusion additive manufacturing combines precursor materials within a static mixer (SM) head, where polymerization begins before deposition. Variable static mixer geometries currently exist, but the relationship between mixer geometry and post- polymerization mechanical properties is undefined. To elucidate this relationship, a series of experiments with identical chemistry was performed using a high shear SM, a low shear SM, and a comparative batch reaction. -
Automated In-Line Mixing System for Large Scale Production of Chitosan- Based Polyplexes
Journal of Colloid and Interface Science 500 (2017) 253–263 Contents lists available at ScienceDirect Journal of Colloid and Interface Science journal homepage: www.elsevier.com/locate/jcis Regular Article Automated in-line mixing system for large scale production of chitosan- based polyplexes Ashkan Tavakoli Naeini a, Ousamah Younoss Soliman a, Mohamad Gabriel Alameh a, Marc Lavertu b, ⇑ Michael D. Buschmann a,b, a Institute of Biomedical Engineering, Polytechnique Montreal, Montreal, Quebec, Canada b Department of Chemical Engineering, Polytechnique Montreal, Montreal, Quebec, Canada graphical abstract article info abstract Article history: Chitosan (CS)-based polyplexes are efficient non-viral gene delivery systems that are most commonly Received 5 February 2017 prepared by manual mixing. However, manual mixing is not only poorly controlled but also restricted Revised 5 April 2017 to relatively small preparation volumes, limiting clinical applications. In order to overcome these draw- Accepted 5 April 2017 backs and to produce clinical quantities of CS-based polyplexes, a fully automated in-line mixing platform Available online 07 April 2017 was developed for production of large batches of small-size and homogeneous CS-based polyplexes. Operational conditions to produce small-sized homogeneous polyplexes were identified. Increasing mix- Keywords: ing concentrations of CS and nucleic acid was directly associated with an increase in size and polydisper- In-line mixing sity of both CS/pDNA and CS/siRNA polyplexes. We also found that although the speed of mixing has a Chitosan siRNA negligible impact on the properties of CS/pDNA polyplexes, the size and polydispersity of CS/siRNA poly- Plasmid plexes are strongly influenced by the mixing speed: the higher the speed, the smaller the size and poly- Polyplex dispersity.