(12) United States Patent 10
Total Page:16
File Type:pdf, Size:1020Kb
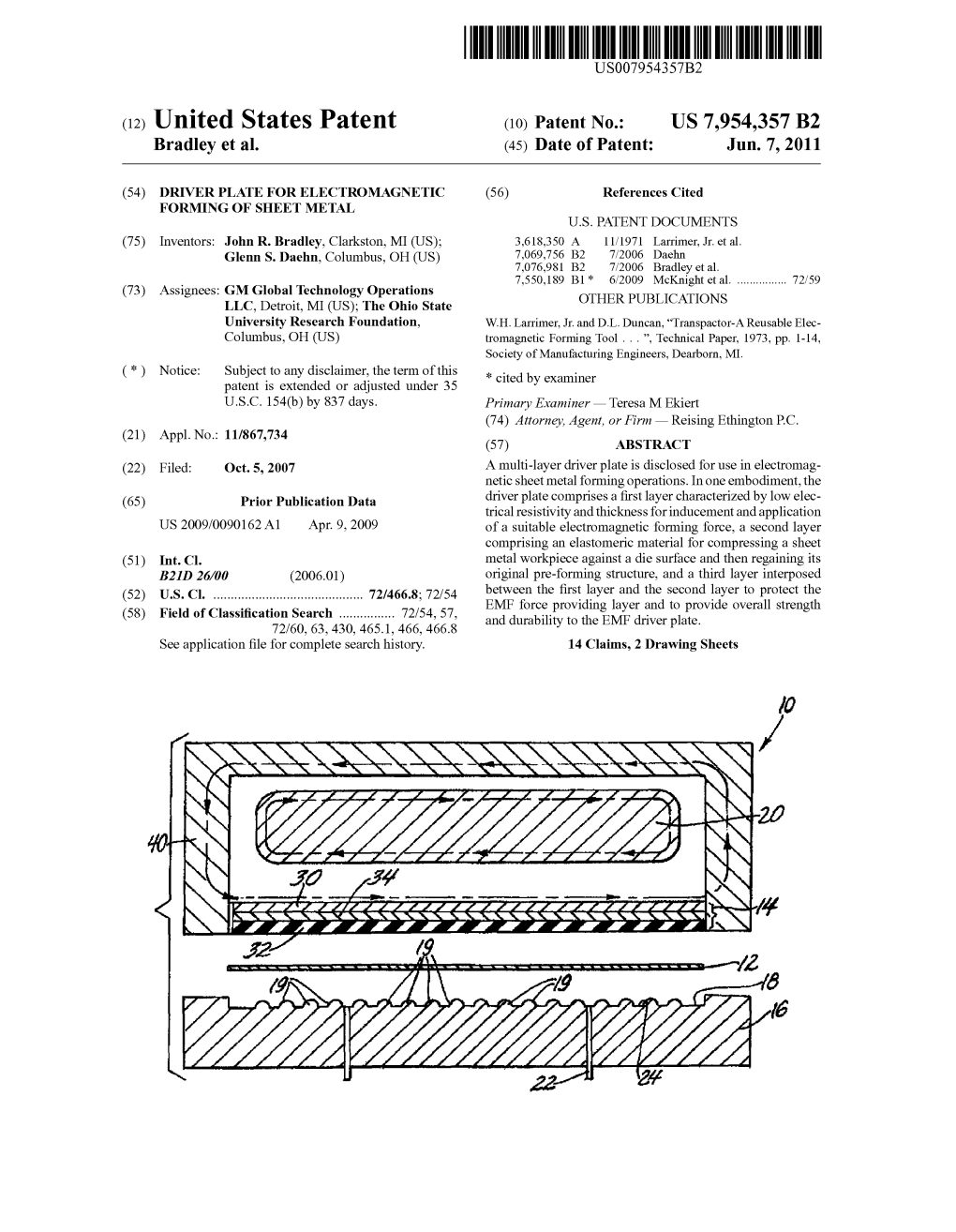
Load more
Recommended publications
-
Modification in Forming Die to Overcome Manufacturing Process
International Journal of Scientific & Engineering Research Volume 11, Issue 7, July-2020 ISSN 2229-5518 41 Modification in Forming Die to Overcome Manufacturing Process Limitation Prof.B.R.Chaudhari[1], PrathmeshKulkarni[2], Tejas Potdar[3], Omkar Pawar[4], Akhilesh Nikam[5] Abstract—Forming of sheet metal is common and vital process in manufacturing industry. Sheet metal forming is the plastic deformation of the work over an axis, creating a change in the parts geometry. Generally, there are two parts used in forming process; one of the part is punch which performs the stretching, bending and blanking operation and another is Die block which secularly clamps the workpiece and same operation as punch. Forming processes are particular manufacturing processes which make use of suitable stresses like compression, tension, shear, combined stresses which causes plastic deformation of the material to produce required shapes. During Forming process, no material is removed i.e. they are deformed and displaced. Some examples of forming processes are Forging, Sheet metal working, thread rolling, Electromagnetic forming, Explosive forming, rotary swaging, etc. Here the problem statement of the project is to combine these two parts design in one forming die which is now manufacturing separately on two different forming dies. Index Terms—Forming Die, Die Design, Blanking Process, Importance of Material Selection; ———————————————————— 1 INTRODUCTION heet metal is simply metal formed into thin and flat pieces. B. Plastic Deformation process: Bending, twisting, curling, S It is one of the fundamental forms used in metal forming deep drawing, necking, ribbing, seaming. can be cut and bent into variety of different shapes. -
10Th Int'l LS-DYNA® Users Conf
10th International LS-DYNA® Users Conference Metal Forming (3) Comparison Between Experimental and Numerical Results of Electromagnetic Forming Processes José Imbert*, Pierre L’eplattenier** and Michael Worswick* *Department of Mechanical and Mechatronics Engineering University of Waterloo, Waterloo, Ontario, Canada **LSTC, Livermore, California, USA Abstract Electromagnetic Forming (EMF) is a high speed metal forming process that is being studied with interest in both academia and industry as a way of improving existing sheet metal forming. The main thrust of the published research has been increasing the formability of aluminum alloys. Observing and measuring EMF process is made very difficult by the high speeds involved and the tooling used to obtain the final shapes. As with many other processes, numerical simulations can potentially be used to study the details of EMF; however, one limiting factor is the difficulty in modeling the process, since accurate models of both the structural and electromagnetic phenomena must be solved. Researchers have relied on simplifications that use analytical magnetic force distributions, on separate electromagnetic (EM) and structural codes or on in-house codes that can solve both problems simultaneously. In this paper, the predictive ability of the EM module of LS-DYNA® is assessed through a comparison between experimental and numerical results for samples formed by EMF. V-Channel and conical shaped samples were formed using two different EMF apparatuses. For the V-Channel samples a double rectangular coil was used and for the conical samples a spiral coil was used. Both processes were modeled using LS-DYNA®’s EM module. A comparison of the final experimental and numerical final shape and current profiles is presented. -
Advanced Manufacturing Processes Prof. Dr. Apurbba Kumar Sharma Department of Mechanical and Industrial Engineering Indian Institute of Technology, Roorkee
Advanced Manufacturing Processes Prof. Dr. Apurbba Kumar Sharma Department of Mechanical and Industrial Engineering Indian Institute of Technology, Roorkee Module - 5 Other Advanced Processes Lecture - 1 High Energy Rate Forming Processes Welcome to this new module on some new specialized material processing methods under the course advanced manufacturing processes. In the module 4, we have discussed about many advanced welding processes like solid state welding processes, laser welding processes, plasma arc welding processes etcetera. We have seen the working principles, advantages, limitations and applications of these processes. Moving on, let us see some new processes like high energy rate forming process, then rapid prototyping process and microwave material processing techniques. In the first of these techniques, let us consider high energy rate forming process. (Refer Slide Time: 01:50) The principle of these processes is like this. A number of methods have been developed to form metals through the application of large amounts of energy in a very short time interval. These processes are known as high energy rate forming processes. (Refer Slide Time: 02:13) Many metals tend to deform more rapidly under the ultra rapid load application rates used in these processes. Principle of high energy rate metal forming can be explained like this, if we have a ductile material, then this material can be deformed by working on it at a very faster speed and against a die of the shape required, the material can be shaped under the pressure of this applied energy. (Refer Slide Time: 02:57) Say for example, we have a sheet of metal which is of ductile in nature. -
Electromagnetic Forming Processes: Material Behaviour and Computational Modelling François Bay, Anne-Claire Jeanson, José-Rodolfo Alves Zapata
Electromagnetic Forming Processes: Material Behaviour and Computational Modelling François Bay, Anne-Claire Jeanson, José-Rodolfo Alves Zapata To cite this version: François Bay, Anne-Claire Jeanson, José-Rodolfo Alves Zapata. Electromagnetic Forming Processes: Material Behaviour and Computational Modelling. 11th International Conference on Technology of Plasticity, ICTP 2014, Oct 2014, Nagoya, Japan. pp.793-800, 10.1016/j.proeng.2014.10.078. hal- 01221105 HAL Id: hal-01221105 https://hal-mines-paristech.archives-ouvertes.fr/hal-01221105 Submitted on 27 Oct 2015 HAL is a multi-disciplinary open access L’archive ouverte pluridisciplinaire HAL, est archive for the deposit and dissemination of sci- destinée au dépôt et à la diffusion de documents entific research documents, whether they are pub- scientifiques de niveau recherche, publiés ou non, lished or not. The documents may come from émanant des établissements d’enseignement et de teaching and research institutions in France or recherche français ou étrangers, des laboratoires abroad, or from public or private research centers. publics ou privés. Available online at www.sciencedirect.com ScienceDirect Procedia Engineering 81 ( 2014 ) 793 – 800 11th International Conference on Technology of Plasticity, ICTP 2014, 19-24 October 2014, Nagoya Congress Center, Nagoya, Japan Electromagnetic forming processes: material behaviour and computational modelling François Baya , Anne-Claire Jeansona,b, Jose Alves Zapataa aCenter for Material Forming (CEMEF) Mines Paristech – UMR CNRS 7635 BP 207, F-06904 Sophia-Antipolis cedex, France bI-Cube Research, 30 Boulevard de Thibaud, F-31100 Toulouse, France Abstract Electromagnetic Forming is a very promising high-speed forming process. However, designing these processes remains quite intricate as it leads to deal with strongly coupled multiphysics process and thus requires the use of computational models. -
Factors Effecting Electromagnetic Flat Sheet Forming Using the Uniform Pressure Coil
FACTORS EFFECTING ELECTROMAGNETIC FLAT SHEET FORMING USING THE UNIFORM PRESSURE COIL A THESIS Presented in Partial Fulfillment of the Requirements for the Degree of Master of Science in the Graduate School of The Ohio State University By Kristin E. Banik, B.S. ***** The Ohio State University 2008 Master’s Examination Committee: Approved by Professor Glenn S. Daehn, Adviser Professor Kathy Flores _______________________________ Adviser Graduate Program in Materials Science and Engineering ABSTRACT Electromagnetic forming is a possible alternative to sheet metal stamping. There are multiple limitations to the incumbent stamping methods including: complex alignment, changes to component shapes, and ductility issues, which often limits available formed geometry. Electromagnetic forming allows for the avoidance of some of these issues, but introduces a few other issues. In this thesis, the issues with electromagnetic forming will be discussed in conjunction with the application of the uniform pressure coil. Also, the effects on properties of the electromagnetically formed samples in comparison to the traditional samples will be presented. These properties include hardness, formability and interface issues. Lastly, discussed in this paper is the implementation of the Photon Doppler Velocimetry (PDV) system, a velocity measurement system used to determine the velocity of the workpiece and compare it to physics-based models of the process. ii Dedicated to my parents. iii ACKNOWLEDGMENTS I want to thank my adviser, Dr. Glenn Daehn for his support and guidance throughout graduate school and in running experiments and writing my thesis. I would also like to thank John Bradley, Steve Hatkevich and Allen Jones for their support of the work in our group as well as electromagnetic forming. -
No 49, 1 May 1980, 1269
No. 49 1269 THE NEW ZEALAND GAZETTE Published by Authority WELLINGTON: THURSDAY, 1 MAY 1980 Revoking a Warrant Declaring an Area of Land in the Nelson 4. Paragraph 5 of the principal order is hereby amended Acclimatisation District to be a Wildlife Refuge by deleting the expression "$4.10 per acre" and substituting the expression "$10.15 per hectare". KEITH HOLYO AKE, Governor-General 5. Paragraph 6 of the principal order is hereby amended A PROCLAMATION by deleting the expression "$2.30 per acre-foot" and substi PURSUANT to section 14 of the Wildlife Act 1953, I, The tuting the expression '"$1.85 per 1,000 cubic metres". Right Honourable Sir Keith Jacka Holyoake, the Governor 6. The Third Schedule to the principal order is hereby General of New Zealand, hereby revoke the Warrant published amended by deleting those items following the item relating on 14 March 1963* notifying and declaring an area of land to the fifth season and substituting the following: to be a Wildlife Refuge. $ Given under the hand of His Excellency the Governor General, and issued under the Seal of New Zealand, Sixth season 6.09 per hectare. this 17th day of April 1980. Seventh season 7.11 per hectare. Eighth season 8.12 per hectare. D. A. HIGHET, Minister of Internal Affairs. Ninth season 9.14 per hectare. [L.S.] Goo SAVE THE QUEEN! Tenth season 10.15 per 'hectare. *New Zealand Gazette, No. 16 at page 331 P. G. MILLEN, Clerk of the Executive Council. (Wil. 34/10/5) (P.W. 64/7/1/15; D.O. -
Superplastic Forming, Electromagnetic Forming, Age Forming, Warm Forming, and Hydroforming
ANL-07/31 Innovative Forming and Fabrication Technologies: New Opportunities Final Report Energy Systems Division About Argonne National Laboratory Argonne is a U.S. Department of Energy laboratory managed by UChicago Argonne, LLC under contract DE-AC02-06CH11357. The Laboratory’s main facility is outside Chicago, at 9700 South Cass Avenue, Argonne, Illinois 60439. For information about Argonne, see www.anl.gov. Availability of This Report This report is available, at no cost, at http://www.osti.gov/bridge. It is also available on paper to the U.S. Department of Energy and its contractors, for a processing fee, from: U.S. Department of Energy Office of Scientific and Technical Information P.O. Box 62 Oak Ridge, TN 37831-0062 phone (865) 576-8401 fax (865) 576-5728 [email protected] Disclaimer This report was prepared as an account of work sponsored by an agency of the United States Government. Neither the United States Government nor any agency thereof, nor UChicago Argonne, LLC, nor any of their employees or officers, makes any warranty, express or implied, or assumes any legal liability or responsibility for the accuracy, completeness, or usefulness of any information, apparatus, product, or process disclosed, or represents that its use would not infringe privately owned rights. Reference herein to any specific commercial product, process, or service by trade name, trademark, manufacturer, or otherwise, does not necessarily constitute or imply its endorsement, recommendation, or favoring by the United States Government or any agency thereof. The views and opinions of document authors expressed herein do not necessarily state or reflect those of the United States Government or any agency thereof, Argonne National Laboratory, or UChicago Argonne, LLC. -
The University of Hull Solidification of Metal
THE UNIVERSITY OF HULL SOLIDIFICATION OF METAL ALLOYS IN PULSE ELECTROMAGNETIC FIELDS being a Thesis submitted for the Degree of Doctor of Philosophy, School of Engineering in the University of Hull by Theerapatt Manuwong, M.Eng, (Chulalongkorn University, Thailand) April 2015 Abstract __________________________________________________________ This research studies the evolution of solidification microstructures in applied external physical fields including in a pulse electric current plus a static magnetic field, and a pulse electromagnetic field. A novel electromagnetic pulse device and a solidification apparatus were designed, built and commissioned in this research. It can generate programmable electromagnetic pulses with tuneable amplitudes, durations and frequencies to suit different alloys and sample dimensions for research at university laboratory and at synchrotron X-ray beamlines. Systematic studies were made using the novel pulse electromagnetic field device, together with finite element modelling of the multiphysics of the pulse electromagnetic field and microstructural characterisation of the samples made using scanning electron microscopy, X-ray imaging and tomography. The research demonstrated that the Lorentz force and magnetic flux are the dominant parameters for achieving the grain refinement and enhancing the solute diffusion. At a discharging voltage from 120 V, a complete equaxied dendritic structure can be achieved for Al-15Cu alloy samples, the strong Lorentz force not only disrupts the growing direction of primary dendrites, it is also enough to disrupts the growing directions of primary intermetallic Al2Cu phases in Al-35Cu alloy, resulting a refined solidification microstructures. The applied electromagnetic field also has significant effect on refining the eutectic structures and promoting the solute diffusion in the eutectic laminar structure. -
Diamond-Like-Carbon Coated Dies for Electromagnetic Embossing
materials Technical Note Diamond-Like-Carbon Coated Dies for Electromagnetic Embossing Marius Herrmann 1,2,3,*, Björn Beckschwarte 1,3, Henning Hasselbruch 4, Julian Heidhoff 3,4, Christian Schenck 1,2,3, Oltmann Riemer 4 , Andreas Mehner 4 and Bernd Kuhfuss 1,2,3 1 Bremen Institute for Mechanical Engineering–Bime, University Bremen, 28359 Bremen, Germany; [email protected] (B.B.); [email protected] (C.S.); [email protected] (B.K.) 2 MAPEX Center for Materials and Processing, University Bremen, 28359 Bremen, Germany 3 University of Bremen, 28359 Bremen, Germany; heidhoff@iwt-bremen.de 4 Leibniz Institute for Materials Engineering–IWT, 28359 Bremen, Germany; [email protected] (H.H.); [email protected] (O.R.); [email protected] (A.M.) * Correspondence: [email protected]; Tel.: +49-0421-2186-4822 Received: 8 September 2020; Accepted: 29 October 2020; Published: 3 November 2020 Abstract: Electromagnetic forming is a high-speed process, which features contactless force transmission. Hence, punching operations can be realized with a one-sided die and without a mechanical punch. As the forces act as body forces in the part near the surface, the process is especially convenient for embossing microstructures on thin sheet metals. Nevertheless, the die design is critical concerning wear like adhesion. Several die materials were tested, like aluminum, copper as well as different steel types. For all die materials adhesion phenomena were observed. To prevent such adhesion an a-C:H-PVD (Physical Vapor Deposition)-coating was applied to steel dies (X153CrMoV12) and tested by embossing aluminum sheets (Al99.5). By this enhancement of the die adhesion was prevented. -
Investigation of Microscale Electromagnetic Forming Reid Vanbenthysen University of New Hampshire, Durham
University of New Hampshire University of New Hampshire Scholars' Repository Master's Theses and Capstones Student Scholarship Spring 2011 Investigation of microscale electromagnetic forming Reid VanBenthysen University of New Hampshire, Durham Follow this and additional works at: https://scholars.unh.edu/thesis Recommended Citation VanBenthysen, Reid, "Investigation of microscale electromagnetic forming" (2011). Master's Theses and Capstones. 644. https://scholars.unh.edu/thesis/644 This Thesis is brought to you for free and open access by the Student Scholarship at University of New Hampshire Scholars' Repository. It has been accepted for inclusion in Master's Theses and Capstones by an authorized administrator of University of New Hampshire Scholars' Repository. For more information, please contact [email protected]. INVESTIGATION OF MICROSCALE ELECTROMAGNETIC FORMING BY REID VANBENTHYSEN Baccalaureate of Science, University of New Hampshire, 2008 Submitted to the University of New Hampshire In Partial Fulfillment of The Requirements for the Degree of Master of Science in Mechanical Engineering May, 2011 UMI Number: 1498975 All rights reserved INFORMATION TO ALL USERS The quality of this reproduction is dependent upon the quality of the copy submitted. In the unlikely event that the author did not send a complete manuscript and there are missing pages, these will be noted. Also, if material had to be removed, a note will indicate the deletion. UMI Dissertation Publishing UMI 1498975 Copyright 2011 by ProQuest LLC. All rights reserved. This edition of the work is protected against unauthorized copying under Title 17, United States Code. uest ProQuest LLC 789 East Eisenhower Parkway P.O. Box 1346 Ann Arbor, Ml 48106-1346 This thesis has been examined and approved. -
A Uniform Pressure Electromagnetic Actuator for Forming Flat Sheets
A UNIFORM PRESSURE ELECTROMAGNETIC ACTUATOR FOR FORMING FLAT SHEETS DISSERTATION Presented in Partial Fulfillment of the Requirements for the Degree Doctor of Philosophy in the Graduate School of The Ohio State University By Manish Kamal, M.S. ***** The Ohio State University 2005 Dissertation Committee: Approved by Dr. Glenn S. Daehn, Adviser ________________________ Dr. David A. Rigney Adviser Dr. Yogeshwar Sahai Graduate Program in Materials Science and Engineering ABSTRACT Electromagnetic forming can lead to better formability along with additional benefits. The spatial distribution of forming pressure in electromagnetic forming can be controlled by the configuration of the actuator. A new type of actuator is discussed which gives a uniform pressure distribution in forming. It also provides a mechanically robust design and has a high efficiency for flat sheet forming. An analysis of the coil is presented that allows a systematic design process. Examples of uses of the coil are then presented, specifically with regards to forming a depression, embossing and cutting. Some practical challenges in the design of the coil are also addressed. This work emphasizes the approaches and engineering calculations required to effectively use this actuator. ii TO MY PARENTS iii ACKNOWLEDGMENTS With a deep sense of gratitude and indebtedness, I wish to record the relentless, timely and untiring guidance I received from Dr. Glenn Daehn. His energy and vast pool of ideas has been a source of constant inspiration. With thought provoking discussions and personal help made available by Dr. Daehn on this fascinating subject in general and the problem of the present investigation in particular, it has become possible for me to complete this dissertation. -
Study of the Industrial Precision Manufacturing and Metallic Alloys with Respect to Economic Considerations
MPRA Munich Personal RePEc Archive Study of the Industrial Precision Manufacturing and Metallic Alloys with Respect to Economic Considerations Saha Choudhuri and Jian Shi Bangladesh University of Engineering and Technology 5 January 2017 Online at https://mpra.ub.uni-muenchen.de/77481/ MPRA Paper No. 77481, posted 13 March 2017 14:26 UTC Study of the Industrial Precision Manufacturing and Metallic Alloys with Respect to Economic Considerations Saha Choudhuri, Jian Shi Bangladesh University of Engineering and Technology 1 Abstract In this report according to the research results and approaches that used, it is utilized and illustrated why these papers are suitable for this research. The best position for explaining topic is here, because for understanding better the concept and the area of research, it is necessary to write briefly at the beginning of the article about topic. It is attempted to design new piston (porous piston) not only to have a good resistance in mechanical properties but also provide lower weight comparing to the previous ones. The most important thing in this work is to be aware of the effect of vibration, vacuum and over pressure during investment casting which by this way we can produce porous structure. By using the existing results of several papers, we will attempt to cast porous piston and optimize it to have the best mechanical properties. As we know engine pistons are one of the most complex components among all automotive or other industry field components. The engine can be called the heart of the car and piston maybe considered the most important part of an engine.