Assembly Automation with Evolutionary Nanorobots and Sensor-Based Control Applied to Nanomedicine
Total Page:16
File Type:pdf, Size:1020Kb
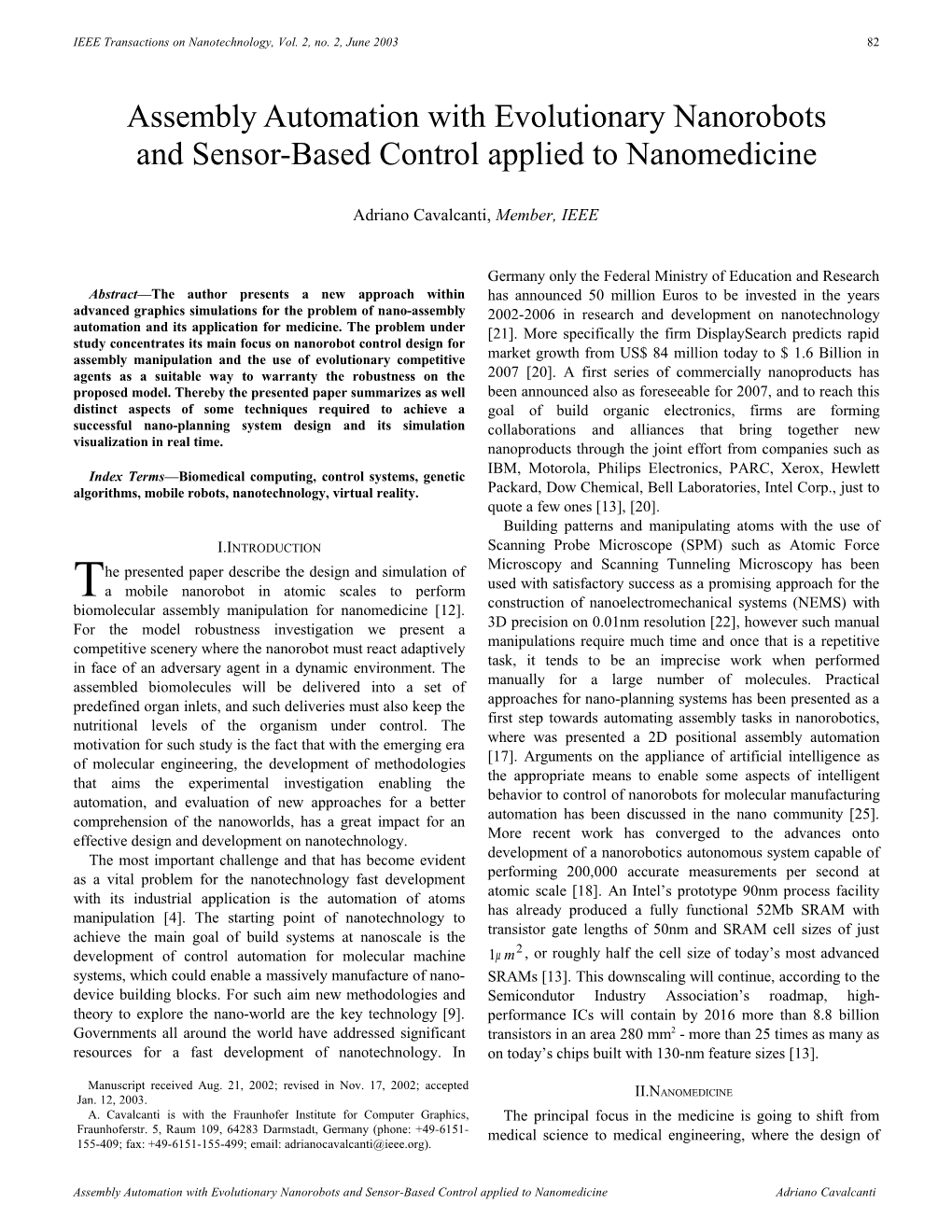
Load more
Recommended publications
-
Artificial Intelligence, Automation, and Work
Artificial Intelligence, Automation, and Work The Economics of Artifi cial Intelligence National Bureau of Economic Research Conference Report The Economics of Artifi cial Intelligence: An Agenda Edited by Ajay Agrawal, Joshua Gans, and Avi Goldfarb The University of Chicago Press Chicago and London The University of Chicago Press, Chicago 60637 The University of Chicago Press, Ltd., London © 2019 by the National Bureau of Economic Research, Inc. All rights reserved. No part of this book may be used or reproduced in any manner whatsoever without written permission, except in the case of brief quotations in critical articles and reviews. For more information, contact the University of Chicago Press, 1427 E. 60th St., Chicago, IL 60637. Published 2019 Printed in the United States of America 28 27 26 25 24 23 22 21 20 19 1 2 3 4 5 ISBN-13: 978-0-226-61333-8 (cloth) ISBN-13: 978-0-226-61347-5 (e-book) DOI: https:// doi .org / 10 .7208 / chicago / 9780226613475 .001 .0001 Library of Congress Cataloging-in-Publication Data Names: Agrawal, Ajay, editor. | Gans, Joshua, 1968– editor. | Goldfarb, Avi, editor. Title: The economics of artifi cial intelligence : an agenda / Ajay Agrawal, Joshua Gans, and Avi Goldfarb, editors. Other titles: National Bureau of Economic Research conference report. Description: Chicago ; London : The University of Chicago Press, 2019. | Series: National Bureau of Economic Research conference report | Includes bibliographical references and index. Identifi ers: LCCN 2018037552 | ISBN 9780226613338 (cloth : alk. paper) | ISBN 9780226613475 (ebook) Subjects: LCSH: Artifi cial intelligence—Economic aspects. Classifi cation: LCC TA347.A78 E365 2019 | DDC 338.4/ 70063—dc23 LC record available at https:// lccn .loc .gov / 2018037552 ♾ This paper meets the requirements of ANSI/ NISO Z39.48-1992 (Permanence of Paper). -
Detecting Automation of Twitter Accounts: Are You a Human, Bot, Or Cyborg?
IEEE TRANSACTIONS ON DEPENDABLE AND SECURE COMPUTING, VOL. 9, NO. X, XXXXXXX 2012 1 Detecting Automation of Twitter Accounts: Are You a Human, Bot, or Cyborg? Zi Chu, Steven Gianvecchio, Haining Wang, Senior Member, IEEE, and Sushil Jajodia, Senior Member, IEEE Abstract—Twitter is a new web application playing dual roles of online social networking and microblogging. Users communicate with each other by publishing text-based posts. The popularity and open structure of Twitter have attracted a large number of automated programs, known as bots, which appear to be a double-edged sword to Twitter. Legitimate bots generate a large amount of benign tweets delivering news and updating feeds, while malicious bots spread spam or malicious contents. More interestingly, in the middle between human and bot, there has emerged cyborg referred to either bot-assisted human or human-assisted bot. To assist human users in identifying who they are interacting with, this paper focuses on the classification of human, bot, and cyborg accounts on Twitter. We first conduct a set of large-scale measurements with a collection of over 500,000 accounts. We observe the difference among human, bot, and cyborg in terms of tweeting behavior, tweet content, and account properties. Based on the measurement results, we propose a classification system that includes the following four parts: 1) an entropy-based component, 2) a spam detection component, 3) an account properties component, and 4) a decision maker. It uses the combination of features extracted from an unknown user to determine the likelihood of being a human, bot, or cyborg. Our experimental evaluation demonstrates the efficacy of the proposed classification system. -
Design and Implementation of Home Automation System
DESIGN AND IMPLEMENTATION OF HOME AUTOMATION SYSTEM USING RASPBERRY PI A Project Presented to the Faculty of California State Polytechnic University, Pomona In Partial Fulfilment of the Requirements for the Degree Master of Science in Computer Science By Irwin Soni 2018 SIGNATURE PAGE PROJECT: DESIGN AND IMPLEMENTATION OF HOME AUTOMATION SYSTEM USING RASPBERRY PI AUTHOR: Irwin Soni DATE SUBMITTED: Spring 2018 Computer Science Department Dr. Yu Sun Project Committee Chair Computer Science Dr. Sampath Jayarathna Computer Science ii ACKNOWLEDGEMENT First and foremost, I would like to thank God for blessing me with such amazing people who have been there to support me in all that I have achieved. To my parents, who have filled my life with immense love, happiness and shaping me into the person I have become today. I would like to thank Dr. Yu Sun, my project advisor, for his selfless support and enlightening guidance. Working with Dr. Sun was such a valuable experience of learning computer science and life at the same time. I would also like to thank Dr. Sampath Jayarathna for his review, suggestions and encouragement. I would also like to thank my classmates for their companionship and friendship. iii ABSTRACT Home automation system achieved great popularity in the last decades as it increases the comfort and quality of life. Smartphone applications are used to control and monitor the home appliances using different types of communication techniques. As mobile devices continue to grow in popularity and functionality, the demand for advanced ubiquitous mobile applications in our daily lives also increases. The paper deals with the design and implementation of a flexible and low-cost Home Automation System for various mobile devices that leverages mobile technology to provide essential functionalities to our homes and associated control operations. -
Robots, Automation, and Employment: Where We Are
WORKING PAPER SERIES ROBOTS, AUTOMATION, AND EMPLOYMENT: WHERE WE ARE Lukas Wolters PhD Candidate MIT Political Science [email protected] MIT Work of the Future Working Paper 05-2020 Date: May 26, 2020 400 Main Street, E19-733, Cambridge, MA 02139 Robots, Automation, and Employment: Where We Are∗ Lukas Woltersy May 26, 2020 Introduction “Robots will destroy our jobs – and we’re not ready for it” titled The Guardian in early 2017.1 Headlines like this have become more and more common over the past couple of years, with newspapers and media outlets reporting that “the robots are coming! And they are going to take all our jobs,“2 asserting that “sometime in the next 40 years, robots are going to take your job,”3 and that “robots may steal as many as 800 million jobs in the next 13 years,”4 and proclaiming gloomy headlines such as “automation threatening 25% of jobs in the US,”5 and “robots to replace up to 20 million factory jobs by 2030.”6 While idea that technology can render human labor obsolete is not new, and concerns about technological unemployment go back at least to Keynes (1930; p. 3) who in 1930 wrote about potential unemployment “due to our discovery of means of economizing the use of labor outrunning the pace at which we can find new uses for labor,” the recent proliferation of reports warning about the potential effect of new technologies, particularly advances in machine learning and robotics, on employment stands out in terms of the number of jobs allegedly under threat of replacement by machines and obsolescence. -
History of Robotics: Timeline
History of Robotics: Timeline This history of robotics is intertwined with the histories of technology, science and the basic principle of progress. Technology used in computing, electricity, even pneumatics and hydraulics can all be considered a part of the history of robotics. The timeline presented is therefore far from complete. Robotics currently represents one of mankind’s greatest accomplishments and is the single greatest attempt of mankind to produce an artificial, sentient being. It is only in recent years that manufacturers are making robotics increasingly available and attainable to the general public. The focus of this timeline is to provide the reader with a general overview of robotics (with a focus more on mobile robots) and to give an appreciation for the inventors and innovators in this field who have helped robotics to become what it is today. RobotShop Distribution Inc., 2008 www.robotshop.ca www.robotshop.us Greek Times Some historians affirm that Talos, a giant creature written about in ancient greek literature, was a creature (either a man or a bull) made of bronze, given by Zeus to Europa. [6] According to one version of the myths he was created in Sardinia by Hephaestus on Zeus' command, who gave him to the Cretan king Minos. In another version Talos came to Crete with Zeus to watch over his love Europa, and Minos received him as a gift from her. There are suppositions that his name Talos in the old Cretan language meant the "Sun" and that Zeus was known in Crete by the similar name of Zeus Tallaios. -
Home Automation Planning Guide for Individuals with Autism
HOME AUTOMATION PLANNING GUIDE FOR INDIVIDUALS WITH AUTISM WRITTEN BY A.J. PARON-WILDES WHY HOME AUTOMATION? When caring for an individual with autism, many needs must be addressed, and even the best caregiver can miss something or not see an incident coming. Home automation can offer protective solutions that support and elevate human care. The most important thing to remember when designing for individuals with autism is that they do not experience the designed environment in the same way others do. They can have increased sensitivities that evoke strong reactions to environmental stimuli. Color, lighting, sounds, and smells all can trigger extreme responses. Having an understanding that many people with autism have either hypo or hyper sensory issues will help you design an environment that can foster increased independence and confidence. Below I outline four main areas of consideration when starting a new design project or retrofitting a home to aid a person with autism. SAFETY The number-one priority for families with an autistic child is safety. Many of us do not understand the inherit dangers of our built environment and the impact it can have on those with autism. Daily challenges can range from possible elopement—kids walking out the front door—to an inadequate understanding of systems and appliances—how does the stove turn on and off? Then, as children get older, safety concerns shift. Instead of preventing the child from leaving the house, you monitor if and when they get in: Did they get off the bus and make it in the house independently? Can you see if a stranger is at the front door? Many children with autism have a hard time with speech, or have no speech, so communicating on the phone is not effective. -
Industrial Robot
1 Introduction 25 1.2 Industrial robots - definition and classification 1.2.1 Definition (ISO 8373:2012) and delimitation The annual surveys carried out by IFR focus on the collection of yearly statistics on the production, imports, exports and domestic installations/shipments of industrial robots (at least three or more axes) as described in the ISO definition given below. Figures 1.1 shows examples of robot types which are covered by this definition and hence included in the surveys. A robot which has its own control system and is not controlled by the machine should be included in the statistics, although it may be dedicated for a special machine. Other dedicated industrial robots should not be included in the statistics. If countries declare that they included dedicated industrial robots, or are suspected of doing so, this will be clearly indicated in the statistical tables. It will imply that data for those countries is not directly comparable with those of countries that strictly adhere to the definition of multipurpose industrial robots. Wafer handlers have their own control system and should be included in the statistics of industrial robots. Wafers handlers can be articulated, cartesian, cylindrical or SCARA robots. Irrespective from the type of robots they are reported in the application “cleanroom for semiconductors”. Flat panel handlers also should be included. Mainly they are articulated robots. Irrespective from the type of robots they are reported in the application “cleanroom for FPD”. Examples of dedicated industrial robots that should not be included in the international survey are: Equipment dedicated for loading/unloading of machine tools (see figure 1.3). -
How Machines Are Affecting People and Places
EXECUTIVE SUMMARY and How machines are affecting people and places MARK MURO ROBERT MAXIM JACOB WHITON With contributions from Ian Hathaway January 2019 EXECUTIVE SUMMARY The power and prospect of automation and artificial intelligence (AI) initially alarmed technology experts for fear that machine advancements would destroy jobs. Then came a correction, with a wave of reassurances. Now, the discourse appears to be arriving at a more complicated, mixed understanding that suggests that automation will bring neither apocalypse nor utopia, but instead both benefits and stresses alike. Such is the ambiguous and sometimes-disembodied nature of the “future of work” discussion. Which is where the present analysis aims to help. Intended to clear up misconceptions on the subject of automation, the following report employs government and private data, including from the McKinsey Global Institute, to develop both backward- and forward-looking analyses of the impacts of automation over the years 1980 to 2016 and 2016 to 2030 across some 800 occupations. In doing so, the report assesses past and coming trends as they affect both people and communities and suggests a comprehensive response framework for national and state-local policymakers. 2 Metropolitan Policy Program at Brookings In terms of current trends, the report finds that: • Approximately 25 percent of U.S. employment (36 million jobs in 2016) will 1. Automation and AI will affect tasks in face high exposure to automation in the virtually all occupational groups in the future coming decades (with greater than 70 but the effects will be of varied intensity—and percent of current task content at risk of drastic for only some. -
Security Automation Best Practices
SECURITY AUTOMATION BEST PRACTICES A Guide to Making Your Security Team Successful with Automation TABLE OF CONTENTS Introduction 3 What Is Security Automation? 3 Security Automation: A Tough Nut to Crack 4 Prepare Your Security Organization for Success 6 Make a Choice: Build or buy? 8 Add Automation When the Time Is Right 10 Know Which Tasks Are Ideal for Automation 12 Testing Automation’s Capabilities 14 Implementing Security Automation 15 About Rapid7 16 Appendix 17 | Rapid7.com Security Automation Best Practices - 2 INTRODUCTION The best security postures are those that are built on efficiency and time-to-response. While processes make it possible to get a job done faster, creating ones that solve practical problems and result in measurable efficiency gains can be a time-consuming task, and without the expertise required to create and build them, they simply don’t get done. This is where security automation comes in. WHAT IS SECURITY AUTOMATION? Security automation streamlines a series of repetitive, manual tasks into cohesive and automated workflows. By plugging a set of tasks into an automated system (such as those involved in phishing investigations), security processes become: • More efficient • Less prone to human error With increased efficiency, better and faster decisions can be made, which in turn can improve your organization’s entire security posture. Even better, with repetitive and manual tasks taken care of by automation, security personnel can instead focus on more strategic work, which boosts their job satisfaction and ensures you’re retaining good talent. | Rapid7.com Security Automation Best Practices - 3 SECURITY AUTOMATION: A TOUGH NUT TO CRACK Historically, security automation has been difficult to implement, which is why many companies have yet to take advantage of it. -
SICX1020 THEORY of ROBOTICS and AUTOMATION (Common to EIE, E&C, ECE, ETCE, EEE & BIOMED)
SICX1020 THEORY OF ROBOTICS AND AUTOMATION (Common to EIE, E&C, ECE, ETCE, EEE & BIOMED) UNIT I BASIC CONCEPTS: History of Robot (Origin): 1968 Shakev, first mobile robot with vision capacity made at SRI. 1970 The Stanford Arm designed eith electrical actuators and controlled by a computer 1973 Cincinnati Milacron‘s (T3) electrically actuated mini computer controlled by industrial robot. 1976 Viking II lands on Mars and an arm scoops Martian soil for analysis. 1978 Unimation Inc. develops the PUMA robot- even now seen in university labs 1981 Robot Manipulators by R. Paul, one of the first textbooks on robotics. 1982 First educational robots by Microbot and Rhino. 1983 Adept Technology, maker of SCARA robot, started. 1995 Intuitive Surgical formed to design and market surgical robots. 1997 Sojourner robot sends back pictures of Mars; the Honda P3 humanoid robot, started in unveiled 2000 Honda demonstrates Asimo humanoid robot capable of walking. 2001 Sony releases second generation Aibo robot dog. 2004 Spirit and Opportunity explore Mars surface and detect evidence of past existence of water. 2007 Humanoid robot Aiko capable of ―feeling‖ pain. 2009 Micro-robots and emerging field of nano-robots marrying biology with engineering. An advance in robotics has closely followed the explosive development of computers and electronics. Initial robot usage was primarily in industrial application such as part/material handling, welding and painting and few in handling of hazardous material. Most initial robots operated in teach-playback mode, and replaced ‗repetitive‘ and ‗back-breaking‘ tasks. Growth and usage of robots slowed significantly in late 1980‘s and early 1990‘s due to ―lack of intelligence‖ and ―ability to adapt‖ to changing environment – Robots were essentially blind, deaf and dumb!.Last 15 years or so, sophisticated sensors and programming allow robots to act much more intelligently, autonomously and react to changes in environments faster. -
Artificial Intelligence Engineering for Cyborg Technology Implementation
Short Communication Robot Autom Eng J Volume 3 Issue 1 - May 2018 Copyright © All rights are reserved by Sadique Shaikh DOI: 10.19080/RAEJ.2018.03.555604 Artificial Intelligence Engineering for Cyborg Technology Implementation Sadique Shaikh* Institute of Management & Science (IMS), India Submission: April 01, 2018; Published: May 17, 2018 *Corresponding author: Sadique Shaikh Md, Institute of Management & Science (IMS), M.S, India, Email: Keywords: Artificial intelligence; Cyborg technology; Neuron command operating devices; Cyborg intelligence; Brain computer interfaces; CyborgAbbreviations: analysis design; Bionic organs; Medical robotics domains; Human biology Intelligence CAD: Cyborg Analysis Design; BCI: Brain Computer Interfaces; NCOD: Neuron Command Operating Devices; CI: Cyborg Introduction Modeling Cyborg analysis design (CAD) model A s hu m a n s l ive longer t her e i s a g r ow i ng ne e d for av a i l abi l it y of organs for transplant however shortage in donations necessitates the development of artificial alternatives with AI often called “Bionic”. Advances in medicine have led to the and heart-lung machines that are common implanted using availability of artificial blood, replacement joints, heart valves, AI for Bionic organs. One of the primary and utilitarian goals of artificial intelligence research is to develop machines with human-like intelligence. Great progress has been made since the start of AI as a field of study. One dominating research paradigm in AI has been based on the assumption that various aspects of human intelligence can be described and understood well enough to the extent that it can be simulated by computer programs through smart representational frameworks and generic reasoning mechanisms. -
Programmable Cloud Platform for Iot(Smart Home)
Programmable Cloud Platform for IoT(Smart Home) DashOS.net Co-founder, Braden Napier, Wayne Zhao [email protected] (408)421-9840 Market-Smart Home monitor and control • Target Dealer installed smart home market (instead of DIY market ) • We provides programmable cloud platform for home monitor and control. • Partner with installation dealers and hardware vendors to reach customers Problem and Our Solution Our Solution:Program home Problem of current smart automation rules on cloud, receive home control push notification, push to react Program home automation on Too hard to use! Smart Home Cloud Platform Trigger push 1.Find the app notification to 2. open app phone 3.find the button 4.click close light Find App, open app, find button, Click button Why cant I just walk there and turn off the light! Click “OK” Action! Example 1 Program Home Camera Detect automation in cloud: If motion Receive Push Choose action to motion in front camera, notification in perform send push notification phone Example 2 Program geo- Send push fencing on cloud: notification: confirm open If within 100 feet Open garage garage door of home, send door? push notification Our Solution-Smart Home Cloud OS User programs home automation rules on cloud platform DashOS.net Devices talk to Cloud using DashOS API (REST, Websocket, MQTT) • Partner with Home controller hardware vendor such as URC • Provide open API for home device to connect to DashOS cloud. (REST, Websocket, MQTT interface) User use push • Program the home automation in cloud platform. notification reaction to • User can use smart phone to monitor and control home device from control home anywhere devices Our Solution • We provide cloud platform for users to program home automation rules in the cloud.