US5198189.Pdf
Total Page:16
File Type:pdf, Size:1020Kb
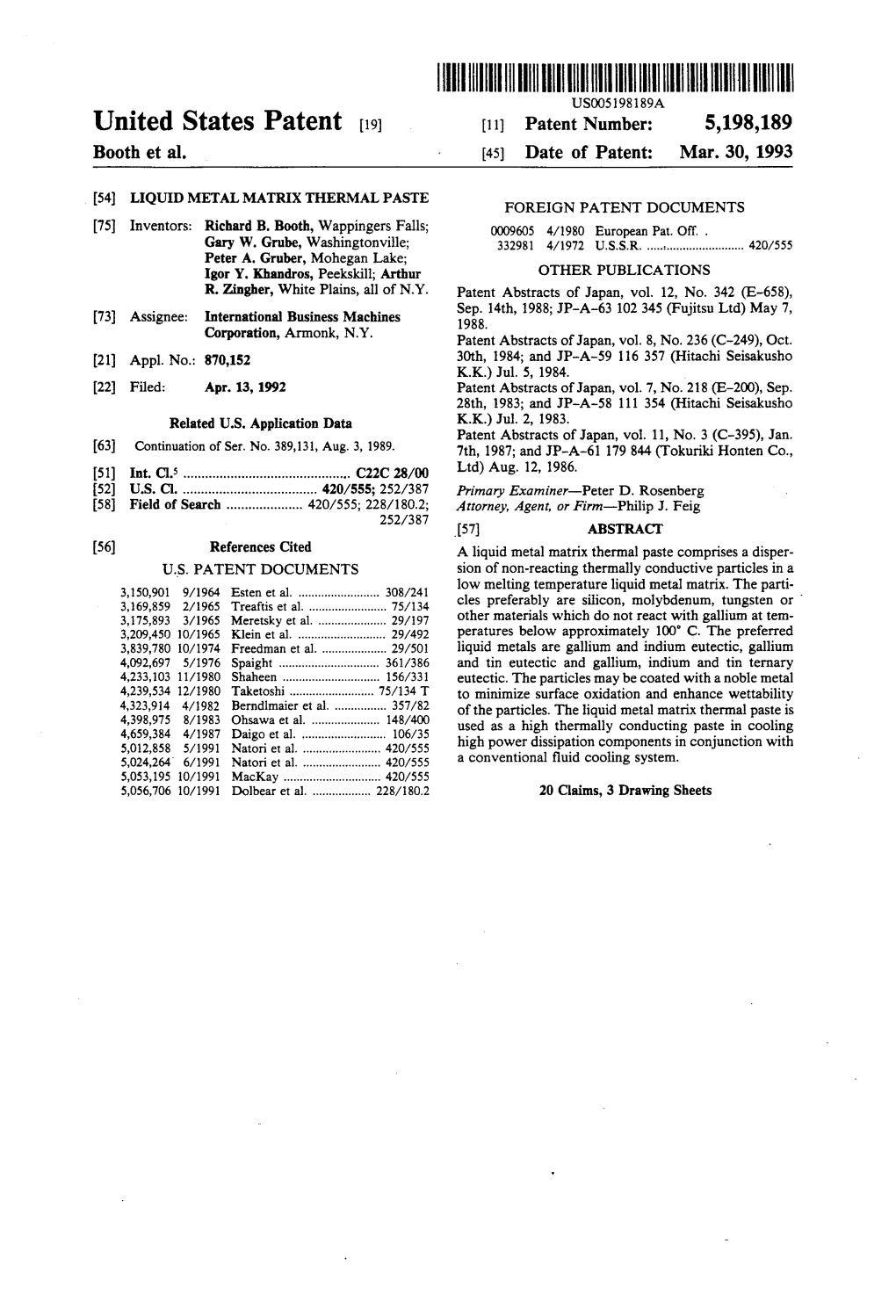
Load more
Recommended publications
-
UNIVERSITY of CALIFONIA SANTA CRUZ HIGH TEMPERATURE EXPERIMENTAL CHARACTERIZATION of MICROSCALE THERMOELECTRIC EFFECTS a Dissert
UNIVERSITY OF CALIFONIA SANTA CRUZ HIGH TEMPERATURE EXPERIMENTAL CHARACTERIZATION OF MICROSCALE THERMOELECTRIC EFFECTS A dissertation submitted in partial satisfaction of the requirements for the degree of DOCTOR OF PHILOSOPHY in ELECTRICAL ENGINEERING by Tela Favaloro September 2014 The Dissertation of Tela Favaloro is approved: Professor Ali Shakouri, Chair Professor Joel Kubby Professor Nobuhiko Kobayashi Tyrus Miller Vice Provost and Dean of Graduate Studies Copyright © by Tela Favaloro 2014 This work is licensed under a Creative Commons Attribution- NonCommercial-NoDerivatives 4.0 International License Table of Contents List of Figures ............................................................................................................................ vi List of Tables ........................................................................................................................... xiv Nomenclature .......................................................................................................................... xv Abstract ................................................................................................................................. xviii Acknowledgements and Collaborations ................................................................................. xxi Chapter 1 Introduction .......................................................................................................... 1 1.1 Applications of thermoelectric devices for energy conversion ................................... 1 -
Thermal Interface Material Catalog
Thermal Interface Materials One Company, Many Solutions www.boydcorp.com BC012021 Thermal Interface Materials TABLE OF CONTENTS Title Page Introduction . 2 Gap Fillers . 3 Gap Rubber Pads . 12 Graphite . 16 Phase Change Materials . 18 Tapes . 21 Thermal Epoxy. 24 Thermal Grease . 25 Lorem ipsum 1 BC012021 Thermal Interface Materials INTRODUCTION Thermal Interface Materials (TIMs) are a critical portion to any effective thermal management system as they transfer heat between solid surfaces. Boyd provides a full array of thermal interface materials, from soft materials like gap fillers, phase change materials, and thermal grease to less compliant materials like thermal rubber pads, films, and thermally conductive hardware. Our broad portfolio contains many options that include electrical isolating properties, adhesives, reinforcements, carriers, and a variety of hardnesses to meet varying application requirements. Boyd's engineering team is well-equipped to help you determine the best material to meet your project’s needs. We leverage our relationships with suppliers and our TIM expertise, developed from decades of tests and projects, to pick the material best suited for your application. Boyd’s precision converting and assembly expertise can custom fabricate and pre-apply Thermal Interface Materials on Aavid’s thermal management solutions like liquid cold plates or heat sinks. By providing complete, ready-to-install thermal Lorem ipsum management solutions, we help customers reduce assembly time and costs with a complete and integrated thermal solution. 2 BC012021 TECHNICAL DATASHEET Transtherm® Thermally Conductive Gap Filler TRANSTHERM® THERMALLY CONDUCTIVE GAP FILLERS Transtherm® Thermally Conductive Gap Fillers are soft, malleable interface materials with high thermal conductivity. Gap fillers are ideal for applications with significant distances between the heat source and cooling surface, varying component heights, high tolerance stack up variability, and uneven or rough surfaces. -
Noncuring Graphene Thermal Interface Materials for Advanced Electronics
FULL PAPER www.advelectronicmat.de Noncuring Graphene Thermal Interface Materials for Advanced Electronics Sahar Naghibi, Fariborz Kargar,* Dylan Wright, Chun Yu Tammy Huang, Amirmahdi Mohammadzadeh, Zahra Barani, Ruben Salgado, and Alexander A. Balandin* development of next generation of compact Development of next-generation thermal interface materials (TIMs) with high and flexible electronics.[1] The increase in thermal conductivity is important for thermal management and packaging computer usage and ever-growing depend- ence on cloud systems require better of electronic devices. The synthesis and thermal conductivity measurements methods for dissipating heat away from of noncuring thermal paste, i.e., grease, based on mineral oil with a mixture electronic components. The important of graphene and few-layer graphene flakes as the fillers, is reported. The ingredients of thermal management are the graphene thermal paste exhibits a distinctive thermal percolation threshold thermal interface materials (TIMs). Various with the thermal conductivity revealing a sublinear dependence on the filler TIMs interface two uneven solid surfaces loading. This behavior contrasts with the thermal conductivity of curing where air would be a poor conductor of heat, and aid in heat transfer from one medium graphene TIMs, based on epoxy, where superlinear dependence on the filler into another. Two important classes of TIMs loading is observed. The performance of the thermal paste is benchmarked include curing and noncuring composites. against top-of-the-line commercial thermal pastes. The obtained results show Both of them consist of a base, i.e., matrix that noncuring graphene TIMs outperforms the best commercial pastes in materials, and thermally conducting fillers. terms of thermal conductivity, at substantially lower filler concentration of Commonly, the studies of new fillers for the use in TIMs start with the curing epoxy- ϕ = 27 vol%. -
Classifying TIM Materials for Power LED Applications
Classifying and Understanding Thermal Interface Materials for Power LED Applications David L. Saums, Principal DS&A LLC Amesbury MA USA www.dsa-thermal.com IMAPS France 7th European Advanced Technology Workshop on Thermal Management and Micropackaging La Rochelle, France 1-2 February 2012 © Copyright 2012 DS&A LLC Selection of Thermal Interface Materials • Large number of different types of TIMs available from more than 100 vendors. • Many competing and similar materials • Reasons: . Very large number of different types of applications . Used in categories of electronic components and electronic systems today . Very widely different requirements for: • Performance: thermal, EOL reliability, gap-filling, compliancy, temperature tolerance • Application process needs • Function: electrically-conducting, electrically non-conducting, sealing, adhesion or fastening hardware required, other . Very different cost tolerance for different applications . Dielectric materials for electrically-live semiconductors – a less-common requirement . Very different manufacturing process requirements, given the wide range of types of application requirements . Extended product life and reliability requirements for critical applications IMAPS France 7th European ATW on Thermal Classifying and Understanding Thermal Interface Materials for Page 2 © Copyright 2012 DS&A LLC Management and Micropackaging Power LED Applications 1-2 February 2012 Selection of Thermal Interface Materials • Maximum performance is not the solitary method of selection for the “best” TIM. • Performance by what measure? . The answer to this question is driven by the application requirements. Choices: thermal, electrical, dielectric, gap-filling, dispensable, EOL reliability, more… • What are the primary drivers for TIM material thermal performance as a very generalized statement? 1. Clamping force applied: How much force is applied to a compliant form of TIM, to achieve the thinnest possible layer and maximum metal-to-metal contact. -
Electrolube Thermal Management Solutions
Thermal Management Solutions Created to perform when the heat is on Thermal Management Solutions • Silicone & Non-Silicone Pastes • RTVs and Bonding Products • Phase Change Materials • Encapsulation Resins • Silicone & Non-Silicone Gap Pads • 0.9 to 5.5W/m.K During use, some electronic components can generate significant amounts of heat. Failure to effectively dissipate this heat away from the component and the device can lead to reliability concerns and reduced operational lifetimes. Newton’s law of cooling states that the rate of loss Heat sinks have proven to be very effective over the of heat is proportional to the temperature difference years however in order to ensure full contact and between the body and its surroundings. Therefore, therefore maximum efficiency, thermal management as the temperature of the component increases and products are used alongside. reaches its equilibrium temperature, the rate of heat loss Metal surfaces, even when polished to a fine degree, per second will equate to the heat produced per second have a certain amount of roughness. It can therefore within the component. This temperature may be high be deduced that when two metal surfaces are placed enough to significantly shorten the life of the component together contact is not 100% and there will always or even cause the device to fail. It is in such cases that be an air gap between the two surfaces. The use of thermal management measures need to be taken. a thermal interface material (TIM) between such gaps The same considerations can be applied to a complete ensures complete contact between the two surfaces circuit or device which incorporates heat producing and in turn more efficient heat conductance. -
A Process, Structure, and Property Study of Gallium-Based Room Temperature Metallic Alloys Courtney Lyn Titus University of North Florida
UNF Digital Commons UNF Graduate Theses and Dissertations Student Scholarship 2019 A Process, Structure, and Property Study of Gallium-based Room Temperature Metallic Alloys Courtney Lyn Titus University of North Florida Suggested Citation Titus, Courtney Lyn, "A Process, Structure, and Property Study of Gallium-based Room Temperature Metallic Alloys" (2019). UNF Graduate Theses and Dissertations. 871. https://digitalcommons.unf.edu/etd/871 This Master's Thesis is brought to you for free and open access by the Student Scholarship at UNF Digital Commons. It has been accepted for inclusion in UNF Graduate Theses and Dissertations by an authorized administrator of UNF Digital Commons. For more information, please contact Digital Projects. © 2019 All Rights Reserved A Process, Structure, and Property Study of Gallium-based Room Temperature Metallic Alloys By Courtney Titus A thesis submitted to the School of Engineering in partial fulfillment of the requirements for the degree of Master’s of Science in Mechanical Engineering University of North Florida College of Computing, Engineering, and Construction April 2019 Unpublished work © Courtney Titus This Thesis titled A Process, Structure, and Property Study of Gallium-based Room Temperature Metallic Alloys is approved: Approved by the thesis committee: Date ____________________________ __________________ Dr. Stephen Stagon Thesis Advisor and Committee Chairperson ____________________________ __________________ Dr. Paul Eason ____________________________ __________________ Dr. Grant Bevill Accepted for the School of Engineering: ____________________________ __________________ Dr. Osama Jadaan Director of the School of Engineering Accepted for the College of Computing, Engineering, and Construction: ____________________________ __________________ Dr. William Klostermeyer Dean of the College Accepted for the University: ____________________________ __________________ Dr. John Kantner Dean of the Graduate School iii ACKNOWLEDGMENTS I would like to thank my advisor and committee chair, Dr. -
Experimenting and Simulating Thermoelectric Cooling of an LED Module
PAPER EXPERIMENTING AND SIMULATING THERMOELECTRIC COOLING OF AN LED MODULE Experimenting and Simulating Thermoelectric Cooling of an LED Module http://dx.doi.org/10.3991/ijoe.v11i4.4692 Mika Maaspuro Aalto University, Aalto, Finland Abstract — Use of a thermoelectric component (TEC) for an mounted on the hot side. TEC is a small size and a LED module cooling will be studied. The issue will be relative inexpensive component. Therefore TECs are approached by revealing the operation of a thermoelectric widely used in many applications. component known also as Peltier element, and the main equations describing its behaviour. An experimental setup TEC has some significant drawbacks. It does not fit well including an LED module, a TEC, an heatsink and a fan will be build. Heat dissipation and the electrical performance in high efficiency devices. Efficiency is related to figure- measurements of the hole experimental setup will be of-merit ZT, which for present day TEC is close to 1 [2]. conducted. The benefits and the limitations of TEC used in Efficiency is the highest at negligible output power level cooling, will be revealed. Cooling effect versus used but reduces at higher levels [3]. TEC generates Joule electrical power will be studied. 3D thermal simulations for heating according to its ohmic resistance and the electric the experimental setup using a FEM simulation software current which flows through it. This heat must be will be presented. Alternatively, a standard circuit simulator removed also by the HS or the HSF mounted on the TEC. will be used. A spice model, which imports TEC's Use of TEC as an active cooling device for LEDs has parameters from the data sheet, will be developed. -
Thermal Compound Selection Guide Silicone-Free Thermal Interface Material
Thermal Compound Selection Guide Silicone-Free Thermal Interface Material Thermal Interface Material (TIM) is any material used to enhance thermal coupling between two parts. TIM may be known by any number of names including thermal compound, thermal grease, thermal gel, heat sink compound, CPU grease, gap filler, and thermal paste. Each is formulated to provide an advantage in specific use conditions. Depending on the materials used, unit price varies from inexpensive to quite high for premium performance. When two surfaces are placed in contact, surface imperfections cause contact to occur at discrete points, with a relatively low percentage of the nominal area making contact. Thermal compounds are intended to conform to surfaces, filling in the space between discrete contact points. This creates an uninterrupted, thermally- conductive path between surfaces, delivering far better heat- carrying capacity than contact points alone. Mechanics of Heat Transfer Choosing the best thermal compound requires some understanding of the mechanics of heat transfer and how the thickness of the thermal compound layer, the bond line thickness, influences product choice. Bond line can be divided into three categories: • Low, at less than 75 μm • Medium, from 75 to 250 μm Thermal compound can be packaged in any size Nordson EFD syringe barrel or cartridge along with 6 oz jars and 1 and 5 gallon pails. • High, at greater than 250 μm There are two critical thermal performance characteristics: Thermal Conductivity (TC) and Thermal Resistance (TR). In low bond line applications, thermal resistance dominates performance. In high bond line applications, thermal conductivity dominates performance. In medium bond line there is a blended influence. -
Electrolube Thermal Management Solutions
Thermal Management Solutions Created to perform when the heat is on Thermal Management Solutions • Non-Silicone Pastes • Encapsulation Resins • Silicone Pastes • 0.9 to 3.4W/m.K • RTVs and Bonding Products During use, some electronic components can generate significant amounts of heat. Failure to effectively dissipate this heat away from the component and the device can lead to reliability concerns and reduced operational lifetimes. Newton’s law of cooling states that the rate of loss Heat sinks have proven to be very effective over the of heat is proportional to the temperature difference years however in order to ensure full contact and between the body and its surroundings. Therefore, therefore maximum efficiency, thermal management as the temperature of the component increases and products are used alongside. reaches its equilibrium temperature, the rate of heat loss Metal surfaces, even when polished to a fine degree, per second will equate to the heat produced per second have a certain amount of roughness. It can therefore within the component. This temperature may be high be deduced that when two metal surfaces are placed enough to significantly shorten the life of the component together contact is not 100% and there will always or even cause the device to fail. It is in such cases that be an air gap between the two surfaces. The use of a thermal management measures need to be taken. thermal interface material between such gaps ensures The same considerations can be applied to a complete complete contact between the two surfaces and in turn circuit or device which incorporates heat producing more efficient heat conductance. -
Thermal Interface Materials (TIM) for a Wide Product Range
Technical Explanation Revision: 03 Thermal Interface Issue date: 2019-09-25 Prepared by: Stefan Hopfe Materials Approved by: A.Wintrich Keyword: Thermal Interface Material, Thermal Paste, Grease, TIM, Phase Change Material 1. Introduction ............................................................................................................................... 1 Advantages .................................................................................................................................. 1 2. Technical Details ........................................................................................................................ 2 2.1 TIM Materials ........................................................................................................................ 2 2.2 Print pattern tolerances .......................................................................................................... 3 2.3 Surface specification for the heat sink ...................................................................................... 3 3. Qualification Tests ...................................................................................................................... 4 3.1 Typical qualification tests for shelf life of pre-printed modules inside blister .................................. 4 3.2 Typical qualification tests for reliability (module mounted on heat sink) ....................................... 4 3.3 Conclusion ........................................................................................................................... -
Comparison of Carbon Nanofiller-Based Polymer Composite Adhesives and Pastes for Thermal Interface Applications
This is a repository copy of Comparison of carbon nanofiller-based polymer composite adhesives and pastes for thermal interface applications. White Rose Research Online URL for this paper: http://eprints.whiterose.ac.uk/87916/ Version: Accepted Version Article: Raza, MA, Westwood, AVK and Stirling, C (2015) Comparison of carbon nanofiller-based polymer composite adhesives and pastes for thermal interface applications. Materials and Design, 85. 67 - 75. ISSN 0264-1275 https://doi.org/10.1016/j.matdes.2015.07.008 © 2015, Elsevier. Licensed under the Creative Commons Attribution-NonCommercial-NoDerivatives 4.0 International http://creativecommons.org/licenses/by-nc-nd/4.0 Reuse Unless indicated otherwise, fulltext items are protected by copyright with all rights reserved. The copyright exception in section 29 of the Copyright, Designs and Patents Act 1988 allows the making of a single copy solely for the purpose of non-commercial research or private study within the limits of fair dealing. The publisher or other rights-holder may allow further reproduction and re-use of this version - refer to the White Rose Research Online record for this item. Where records identify the publisher as the copyright holder, users can verify any specific terms of use on the publisher’s website. Takedown If you consider content in White Rose Research Online to be in breach of UK law, please notify us by emailing [email protected] including the URL of the record and the reason for the withdrawal request. [email protected] https://eprints.whiterose.ac.uk/ -
Heat Transfer Compound
Page 1 HTC Heat Transfer Compound HTC is a non-curing heat transfer paste, designed for use as a thermal interface material. It is recommended where the efficient and reliable thermal coupling of electronic components or heat dissipation between any surfaces are required. HTC is a non-silicone paste, suitable for applications where silicones are prohibited, thus avoiding issues with silicone and low molecular weight siloxane migration. • General purpose thermal management paste; cost effective heat dissipation • Based on a non-silicone oil; avoids issues with silicone and LMW siloxane migration • Good thermal conductivity; designed for use as a thermal interface material • Non-curing paste; allows simple and efficient rework of components if required Approvals RoHS-2 Compliant (2011/65/EU): Yes NATO Stock No. – EHTC10S: 6850-99-775-5881 NATO Stock No. – EHTC20S: 5835-99-775-5881 NATO Stock No. – EHTC35S: 5975-99-512-1473 Typical Properties Colour: White Base: Blend of synthetic fluids Thermo-conductive Component: Powdered metal oxides Density @ 20°C (g/ml): 2.04 Cone Penetration @ 20°C: 300 Viscosity @ 1rpm (Pa s): 202-205 Thermal Conductivity (Guarded Hot Plate): 0.9 W/m.K Thermal Conductivity (Heat Flow): 0.7 W/m.K (calculated) Temperature Range: -50°C to +130°C Weight Loss after 96 hours @ 100°C: <1.0% Permittivity @ 1 GHz: 4.2 Specific Resistance: 1 x 1014 Ohms/cm Dielectric Strength: 42 kV/mm Description Packing Order Code Shelf Life 2 ml Syringe HTC02S 48 months Heat Transfer Compound 10 ml Syringe HTC10S 48 months 20 ml Syringe HTC20S 48 months 35 ml Luer Lock Syringe HTC35SL 48 months 700 gram cartridge HTC700G 72 months 1 Kg Bulk HTC01K 72 months 12.5kg Bulk HTC12.5K 72 months 25 Kg Bulk HTC25K 72 months Page 2 Directions for Use Thermal pastes can be applied to the base and mounting studs of diodes, transistors, thyristors, heat sinks, silicone rectifiers and semi-conductors, thermostats, power resistors and radiators, to name but a few.