&\S(1712; 2/Hi-4. 2
Total Page:16
File Type:pdf, Size:1020Kb
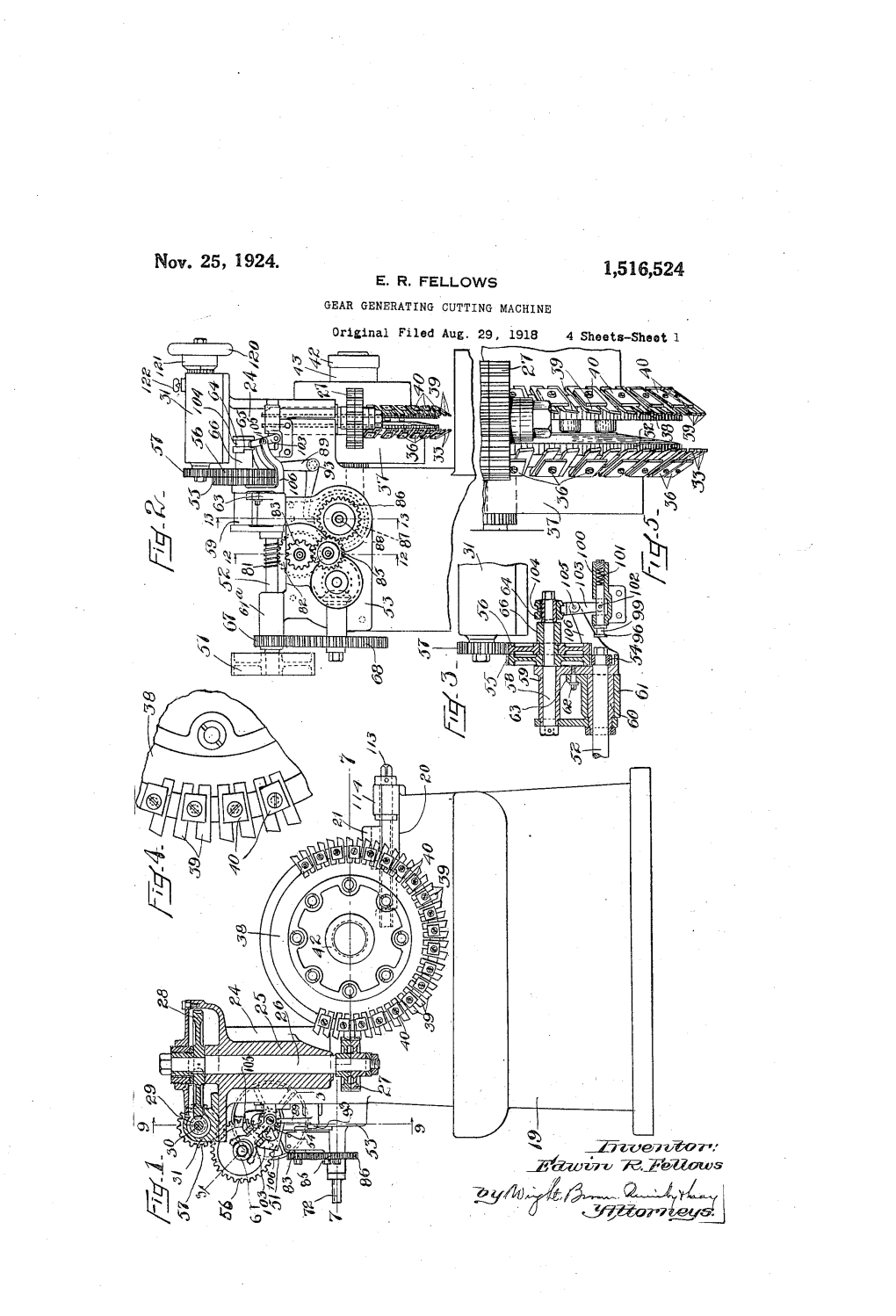
Load more
Recommended publications
-
Gear Cutting and Grinding Machines and Precision Cutting Tools Developed for Gear Manufacturing for Automobile Transmissions
Gear Cutting and Grinding Machines and Precision Cutting Tools Developed for Gear Manufacturing for Automobile Transmissions MASAKAZU NABEKURA*1 MICHIAKI HASHITANI*1 YUKIHISA NISHIMURA*1 MASAKATSU FUJITA*1 YOSHIKOTO YANASE*1 MASANOBU MISAKI*1 It is a never-ending theme for motorcycle and automobile manufacturers, for whom the Machine Tool Division of Mitsubishi Heavy Industries, Ltd. (MHI) manufactures and delivers gear cutting machines, gear grinding machines and precision cutting tools, to strive for high precision, low cost transmission gears. This paper reports the recent trends in the automobile industry while describing how MHI has been dealing with their needs as a manufacturer of the machines and cutting tools for gear production. process before heat treatment. A gear shaping machine, 1. Gear production process however, processes workpieces such as stepped gears and Figure 1 shows a cut-away example of an automobile internal gears that a gear hobbing machine is unable to transmission. Figure 2 is a schematic of the conven- process. Since they employ a generating process by a tional, general production processes for transmission specific number of cutting edges, several tens of microns gears. The diagram does not show processes such as of tool marks remain on the gear flanks, which in turn machining keyways and oil holes and press-fitting bushes causes vibration and noise. To cope with this issue, a that are not directly relevant to gear processing. Nor- gear shaving process improves the gear flank roughness mally, a gear hobbing machine is responsible for the and finishes the gear tooth profile to a precision of mi- crons while anticipating how the heat treatment will strain the tooth profile and tooth trace. -
Rexnord Gear Manufacturing Services Overview
Rexnord Gear Manufacturing Services Overview Rexnord Gear Manufacturing Services Rexnord Gear Manufacturing Services Overview Rexnord Gear Manufacturing Services is a full service supplier providing high-quality, custom precision spur & helical gearing and specialized gearboxes, serving the mining, energy, transit, construction, and industrial markets. Our custom solutions have helped customers for more than 60 years, demonstrating high performance and reliability on custom enclosed gear drives and loose precision gears with cost-effective solutions. As your single source custom gear and gearbox manufacturer, Rexnord Gear Manufacturing Services can offer you reduced complexity and inventory, improved lead time and efficiency, and state-of-the-art technical support and engineering. We have the necessary equipment that you need, all in one place. In-house heat treating, gear cutting and gear grinding capabilities and expertise ensure the highest level of precision is met for our customers’ most demanding gear applications. In addition, Rexnord has a full complement of precision gearing process capabilities for machining, turning, milling, drilling, broaching, key seating, OD/ID grinding, and balancing. ISO-certified, build-to-print manufacturing provides high-quality gearing and specialized gearboxes. Key features & benefits Gear Milling, Hobbing & Turning Gear Grinding • Spur & helical gears to 80” length and 60” • Spur & helical gears to 64” face width and 138” outer diameter outer diameter Heat Treating Housing Machining • In-house heat -
Grinding and Abrasives This Year
Gear Grinding4/26/043:54PMPage38 Ph t t f Gl C Gear Grinding 4/22/04 1:49 PM Page 39 Grinding Abrasivesand Flexibility and pro- Flexibility is seen in many of the newest model gear grind- ing machines. Several machine tool manufacturers (Kapp, ductivity are the key- Liebherr & Samputensili) now offer dedicated gear grinding machines that are capable of either generating grinding or words in today’s form grinding on the same machine, and the machines can use either dressable wheels or electroplated CBN wheels. On- grinding operations. machine dressing and inspection have become the norm. Automation is another buzzword in grinding and abrasives this year. Gear manufacturers are reducing their costs per Machines are becom- piece by adding automation and robotics to their grinding and deburring operations. ing more flexible as Productivity is being further enhanced by the latest grind- ing wheels and abrasive technology. Tools are lasting longer manufacturers look and removing more stock due to improvements in engineering and material technology. All of this adds up to a variety of possible solutions for the for ways to produce modern gear manufacturer. If your manufacturing operation includes grinding, honing, deburring, tool more parts at a sharpening or any number of other abrasive machining operations, today’s technology lower cost. What offers the promise of increased productivi- ty, lower costs and greater quality than ever before. used to take two By William R. Stott machines or more now takes just one. Photo courtesy of Gleason Corp. www.powertransmission.com • www.geartechnology.com • GEAR TECHNOLOGY • MAY/JUNE 2004 39 Gear Grinding 4/22/04 1:49 PM Page 40 ROTARY TRANSFER GRINDER other ground parts. -
Machining of Spur Gears Using a Special Milling Cutter
ISSN 1330-3651 (Print), ISSN 1848-6339 (Online) https://doi.org/10.17559/TV-20171120121636 Original scientific paper Machining of Spur Gears Using a Special Milling Cutter Piotr BORAL, Antun STOIĆ, Milan KLJAJIN Abstract: Spur gears have a wide application in the machine-building industry. Machining process primarily selected for these gears is hobbing method with modular hobs, or with Fellows cutters. Other methods which can be applied are profiling using the pull broaches, while the finishing can be done by gear shaving or grinding by the Maag, Niles or Reishauer methods. Moreover, in small (or unit) production, they may be formed using disc- or finger-type modular cutters. The article presents a method for cutting spur gears using a disc-type mill with a variable cutting plate profile. The influence of the number of blades of the presented milling cutter on the accuracy of the worked tooth profile was investigated. Keywords: disc-type milling cutter; gear machining; surface roughness 1 INTRODUCTION In numerous scientific research centres and manufacturing companies, gear analysis software is being The involute profile in spur gears is commonly used built to assist the design of the geometry and technology and practically adopted by all standards worldwide. The of toothed gears [14-17]. durability and good operating conditions of the toothed gears are largely influenced by the manufacturing accuracy and the structure and roughness of the cooperating surfaces [1-3]. These gears are manufactured using many profiling and hobbing methods [4-7]. They are machined chiefly by the hobbing method with modular hobs or Fellows cutters, or by gear shaving by the MAAG or Sunderland method – Fig. -
Gear Cutting
NO 02 HORN 20 20 SPECIAL FEATURE: GEAR CUTTING NEW BUILDING GEAR CUTTING PRODUCTS IN THE USA ABOUT US Tool by tool – Tooth by tooth 2020 innovations The HORN Group invests The HORN Group expands internationally DEAR READERS, The last few months have seen us living in extraordinary times that are shrouded in uncertainty and insecurity, and dominated by cautiousness. The measures implemented were – and remain – only right and proper. But that now makes it all the more important for us to turn our attention towards the future. COVID-19 has had an enormous impact on industry and many other sectors, with a good number of firms having been forced into adopting reduced working hours or, in some cases, even more extensive measures. In spite of everything, we are arguing for the quickest possible return to some semblance of normality. Our ability to supply our products has not been affected. Extensive pre- ventative measures have been put in place to ensure that your contacts can still be reached via the usual channels. Registered customers can also get hold of our products by visiting our online shop at eshop.phorn.de. This edition of “world of tools” covers a wide range of topics. As well as providing insights into the international activities of the HORN Group, we also showcase our capabilities in the area of gear production and illustrate everything a tool has to go through at our end before it is used by you. Our innovations are also featured here as usual, even though the major AMB (Stuttgart) and IMTS (Chicago) trade fairs could not take place in September in the normal format. -
Gear Cutting with Shaper
GEAR CUTTING With the Shaper by "Base Circle" IRST, let it be said that the method here of the machine and thus making the flats narrower. Fdescribed is not claimed to be original. In other words, the finer the feed of the machine, All that is claimed is that it does not appear to the better the result. Even with only a moderately be generally known to readers of THE MODEL fine feed, however, the results will be very much ENGINEER and that the writer has not come across better than those produced by the milling process any reference to such a method in print. with disc cutters. A disc cutter can, of course, The idea is to use a shaping machine (in the only be correct for one diametral pitch and one writer's case, a very old hand-operated machine) number of teeth. As a compromise, such cutters and to fit to it a mechanism on the lines of that are certainly sold to cover a range of teeth, but used in some types of gear-grinding machines, when so used, the resulting teeth are not correctly such as the " Maag " or older " Lees-Bradners " formed. to give a rolling motion to the gear blank while Using the suggested method, the cutter is a being cut. This method, being a true generating straightforward shaper tool, ground to the form method—right back to first principles—results of a rack tooth of the diametral pitch to be cut. in a correctly formed involute tooth. The sides are straight and inclined to the The curved sides of the tooth are made up of a centre-line at the same angle as the pressure series of small flats and the results can be made angle of the tooth—i.e., usually 14 1/2 deg. -
Your Gear Cutting Solution
YOUR GEAR CUTTING SOLUTION ONE TEAM, ONE GOAL YOUR GEAR CUTTING SOLUTION Fubri, on the edge of precision gear tool manufacturing since 85 years thanks to the strong motivation, flexibility and efforts of its team. We are careful in exceeding international quality standards thanks to its continuous improvement philosophy and ongoing investment plans. Fubri is today one of the few solutions on the market to offer thecomplete range of cutting tools: hobs, shapers, shaving tools and service. The special delivery service, FAST TRACK, developed to meet customer needs has enabled us to become the quickest hob manufacturer in the world. FAST TRACK HOBS TOP QUALITY HIGH PERFORMANCE GEAR HOBS FOR THE LATEST GENERATION OF HOBBING MACHINES Hobs for all automotive applications (shank type or bore type) Hobs for splines Hobs for chain sprockets Hobs for pulley hobs From MOD 0.8 to MOD 33 (DIA 20-300) Hobs for wormwheel Ext. Dia : from 20 mm to 300 mm Class A, AA, AAA, Agma standards HSS including hard-wearing materials such as MC90 Most uptodate coatings: TIN, ALCRONA, ALTENSA SHAPER AND SKIVING TOOLS One of the leading companies for production of shaper and skiving tools. Disc, EBB and shank type shaper cutters and skiving tools for the production of gears, splines, serrations, sprocket and other profiles in size mod. 0,2 up to 26,0 in all available tool steels as well as carbide and standard coatings. You will find also in our production range straight bevel generating tools, rack type cutters and chamfering tools. New developments allowing high speed synchronization between workpiece and tool enables the use of skiving tools. -
Advent Tool & Manufacturing Heller Machine Tools Dontyne Gears
GEAR SOLUTIONS MAGAZINE Your Resource for Machines, Services, and Tooling for the Gear Industry 2020 2020 BUYER’S GUIDE BUYER’S GUIDE MACHINES PROFILE HELLER MACHINE TOOLS SERVICES PROFILE DONTYNE GEARS TOOLING PROFILE ADVENT TOOL & MANUFACTURING NOVEMBER 2019 NOVEMBER 2019 gearsolutions.com www.toolink-eng.com 6595 Odell Place, Suite I Boulder, CO 80301 303-776-6212 COMPACT ROBOT MACHINE TENDING HOBBERS & SHAPERS INT/EXT WORM GRINDING GEAR GRINDERS GANTRY & STOCKER MACHINE TENDING GREAT IDEA! Precision Products for Gear Manufacturing www.toolink-eng.com 303-776-6212 Don’t Settle for Less The Phoenix® 280G Bevel Gear Grinding Machine is the industry benchmark for the ultra- fast production of high-quality automotive and light truck bevel gears. It’s reliable and easy to operate, available with high- speed loader, and can be directly networked through Gleason Closed Loop. www.gleason.com/280G © Gleason Corporation. All rights reserved. 2020 BUYER’S GUIDEWhen it comes to gear manufacturing, it’s not just about what you do, but also who you know. Identifying quality sources for equipment, services, and tooling is a critical component of your overall business plan, but it can be a time-consuming task. That’s why we publish the Gear Solutions Buyer’s Guide each year: to help you connect with the suppliers you need as well as to steer companies who require the machines, materials, products, and capabilities you provide. We have compiled the most complete source listing available and presented this information in a way that is accessible, convenient, -
Unit 1 Introduction to Tool Engineering and Management
Introduction to Tool UNIT 1 INTRODUCTION TO TOOL Engineering and ENGINEERING AND MANAGEMENT Management Structure 1.1 Introduction Objectives 1.2 Basics of Tool Engineering 1.3 Elements in Tool Engineering 1.3.1 Single Point Cutting Tool 1.3.2 Multi Point Cutting Tool 1.4 Types of Machine Tools 1.5 Operational Issues in Tool Engineering 1.6 Summary 1.7 Key Words 1.1 INTRODUCTION Tool engineering is a vital area of production engineering. It includes metal cutting, pressing, and various work holding devices. Metal cutting is the operation in which thin layer of metal is removed by wedge shaped tool. Metal cutting is commonly associated with industries like automotive, aerospace, home appliance, etc. The machining of metal and alloys play a crucial role in the range of manufacturing activities including ultra precision machining of extremely delicate components. Objectives After studying this unit, you should be able to • understand the basics of tool engineering, • classify the tooling and machine tools, and • recognise various types of operations performed on different machines. 1.2 BASICS OF TOOL ENGINEERING Machine tools are very important for any industrialised country because they hold a key position in the technology chain. Machine tools are needed to build the machines and parts with which capital goods and consumer goods of all kinds are manufactured, from cars to airplanes, from glasses to ball point pen. If the creative tool engineers and qualified skilled workers are constantly producing faster, better and more intelligent machine tools for the market, they are helping many industries. This means innovation in machine tool industry have a far-reaching and multiplicative impact. -
Fabrication of Directly Designed Gears with Symmetric and Asymmetric Teeth Alexander L
technical Fabrication of Directly Designed Gears with Symmetric and Asymmetric Teeth Alexander L. Kapelevich and Yuriy V. Shekhtman Introduction For Related Articles Search When compared with the traditional gear design approach — based on pre-selected, typically standard generating asymmetric rack parameters — the alternative Direct Gear Design (Ref.1) at www.geartechnology.com method provides certain advantages for custom, high-perfor- mance gear drives. Among them are increased load capacity; efficiency; length-of-service; reduced size and weight; noise/ vibrations; and cost. However, the manufacture of such non- standard gears requires custom tooling and certain alterations of known gear fabrication processes. This paper presents specifics of application main methods of gear fabrication, i.e. — form and generating machining (cutting and grinding); gear forming injection molding technology; net forging; powder metal (PM) processing; die casting; and wire EDM gear prototyping. It also describes tooling profile defini- tion, dependent upon the selected gear fabrication method. It presents the Genetic Molding Solution technique for compensa- tion of differential warpage and shrinkage for plastic injection molding tooling — that enables enhancement of gear accuracy and shortens the process development cycle. Table 1 Main machining processes used for spur and helical gears Type of process Type of tooling a Form Cutting Form disk or end mill cutter, broach, etc. Machining Grinding Grinding wheel Hob, shaper cutter, rack cutter, shaver Cutting Generating cutter Machining Grinding Grinding wheel CNC milling Cylinder or ball mill cutter Wire-cut EDM Wire Contour Machining Laser cutting Laser beam Water or water and abrasive media Water Jet cutting mixture stream b c Figure 2 Gear fly cutting schematics: a) top view; b) right view; c) Figure 1 Gear form machining: 1) gear profile; 2) tool profile. -
Precision Tools
Precision Tools Precision Tools Gear Cutting Tools & Broaches Pursuing advanced high-speed technology that is both user and environmentally friendly Since developing Japan's first broaching machine in the late 1920s, Fujikoshi has developed a variety of tools and machine tools to handle advancements in production systems. Fujikoshi continues to lead the way by developing machining systems that integrate tools and machines. Pursuing advanced high-speed technology that is both user and environmentally friendly Since developing Japan's first broaching machine in the late 1920s, Fujikoshi has developed a variety of tools and machine tools to handle advancements in production systems. Fujikoshi continues to lead the way by developing machining systems that integrate tools and machines. ndex Gear Cutting Tools Gear Cutting Comparison and Types 25 Broaches Design of Broach ools Guidance NACHI Accuracy of Gear Shaper Cutters 26 Technical Introduction Basic Design and Cutting Method 61 Materials and Coating of Gear Cutting Tools 5 Cutting Condition and Regrinding 27 Hard Broaches 45 Calculation of Pulling Load 62 Gear Cutting T Disk Type Shaper Cutters Type1Standard Dimensions 28 Broach for MQL 46 Face Angle and Relief Angle 63 Technical Introduction Disk Type Shaper Cutters Type2Standard Dimensions 30 Off-normal Gullet Helical Broach 47 Finished Size of Broaches 64 Hard Hobbing 6 Disk Type Shaper Cutters Type2Standard Dimensions 31 Micro Module Broaching 48 Helical Gear Shaper Cutters High Speed Dry Hobbing 7 Essential Points and Notice 65 Disk -
Experimental Simulation of Gear Hobbing Through a Face Milling Concept in CNC-Machine
Experimental simulation of gear hobbing through a face milling concept in CNC-machine SABA HOSEINI Degree project in Second cycle Stockholm, Sweden 2013 www.kth.se Powered by TCPDF (www.tcpdf.org) Experimental simulation of gear hobbing through a face milling concept in CNC-machine Author: Saba Hoseini Report No.: Kimab-2013-119 Swerea KIMAB Project No.: 265010 Date: 07.08.2013 Member program: MRC Materials in Machining i Abstract High-speed steels are the main material for cutting tools especially for producing gear boxes in the automotive industry. Cutting performance of high speed steel depends on their resistance to wear, their toughness and resistance to tempering at operating temperature. In this project, tool-life and wear type of cutting tools made of powder metallurgy high speed steel (PM-HSS) were investigated up to a flank wear width of 0.30 mm in different steels and cutting speeds. Hardness and cutting speed had a significant effect on tool-wear, tool-life and chip formation. More rake face wear was occurred by harder materials because of higher thermo- mechanical loading .Three indicators were used for representing tool life and to show the relation of cutting speed and hardness with cutting performance. Difference of tool life between the softest and the hardest steels was about two times. By increasing cutting speed in every work-material more number of passes was obtained. The required data were obtained experimentally by a 3-axis milling machine. This test method facilitates simulation of gear hobbing wear type in a less time-consuming way, compared to the other methods which have the same kinematics of real hobbing.