LNG Solutions in Action LNG Solutions in Action
Total Page:16
File Type:pdf, Size:1020Kb
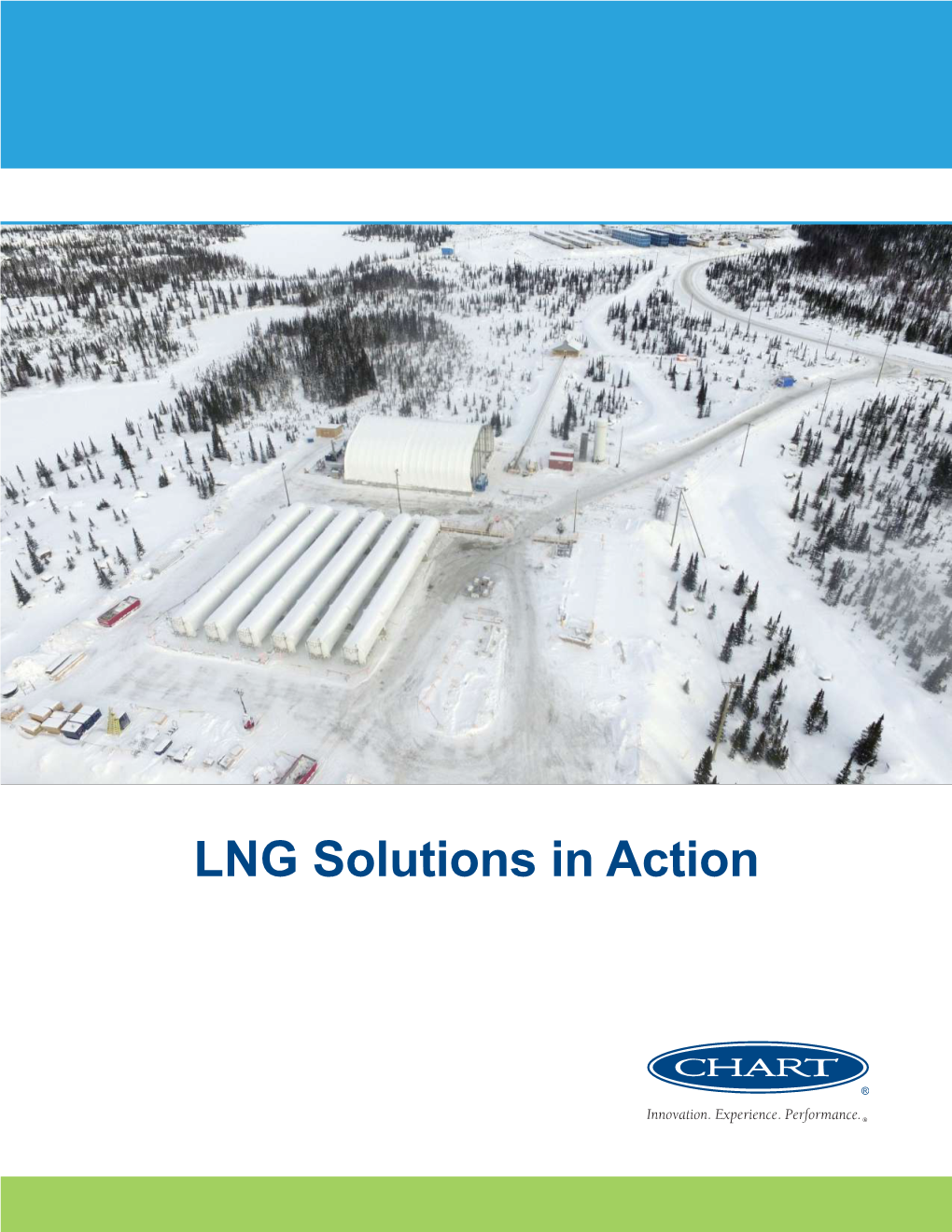
Load more
Recommended publications
-
Blending Hydrogen Into Natural Gas Pipeline Networks: a Review of Key Issues
Blending Hydrogen into Natural Gas Pipeline Networks: A Review of Key Issues M. W. Melaina, O. Antonia, and M. Penev NREL is a national laboratory of the U.S. Department of Energy, Office of Energy Efficiency & Renewable Energy, operated by the Alliance for Sustainable Energy, LLC. Technical Report NREL/TP-5600-51995 March 2013 Contract No. DE-AC36-08GO28308 Blending Hydrogen into Natural Gas Pipeline Networks: A Review of Key Issues M. W. Melaina, O. Antonia, and M. Penev Prepared under Task No. HT12.2010 NREL is a national laboratory of the U.S. Department of Energy, Office of Energy Efficiency & Renewable Energy, operated by the Alliance for Sustainable Energy, LLC. National Renewable Energy Laboratory Technical Report 15013 Denver West Parkway NREL/TP-5600-51995 Golden, Colorado 80401 March 2013 303-275-3000 • www.nrel.gov Contract No. DE-AC36-08GO28308 NOTICE This report was prepared as an account of work sponsored by an agency of the United States government. Neither the United States government nor any agency thereof, nor any of their employees, makes any warranty, express or implied, or assumes any legal liability or responsibility for the accuracy, completeness, or usefulness of any information, apparatus, product, or process disclosed, or represents that its use would not infringe privately owned rights. Reference herein to any specific commercial product, process, or service by trade name, trademark, manufacturer, or otherwise does not necessarily constitute or imply its endorsement, recommendation, or favoring by the United States government or any agency thereof. The views and opinions of authors expressed herein do not necessarily state or reflect those of the United States government or any agency thereof. -
Hydrogen Storage for Mobility: a Review
materials Review Hydrogen Storage for Mobility: A Review Etienne Rivard * , Michel Trudeau and Karim Zaghib * Centre of Excellence in Transportation Electrification and Energy Storage, Hydro-Quebec, 1806, boul. Lionel-Boulet, Varennes J3X 1S1, Canada; [email protected] * Correspondence: [email protected] (E.R.); [email protected] (K.Z.) Received: 18 April 2019; Accepted: 11 June 2019; Published: 19 June 2019 Abstract: Numerous reviews on hydrogen storage have previously been published. However, most of these reviews deal either exclusively with storage materials or the global hydrogen economy. This paper presents a review of hydrogen storage systems that are relevant for mobility applications. The ideal storage medium should allow high volumetric and gravimetric energy densities, quick uptake and release of fuel, operation at room temperatures and atmospheric pressure, safe use, and balanced cost-effectiveness. All current hydrogen storage technologies have significant drawbacks, including complex thermal management systems, boil-off, poor efficiency, expensive catalysts, stability issues, slow response rates, high operating pressures, low energy densities, and risks of violent and uncontrolled spontaneous reactions. While not perfect, the current leading industry standard of compressed hydrogen offers a functional solution and demonstrates a storage option for mobility compared to other technologies. Keywords: hydrogen mobility; hydrogen storage; storage systems assessment; Kubas-type hydrogen storage; hydrogen economy 1. Introduction According to the Intergovernmental Panel on Climate Change (IPCC), it is almost certain that the unusually fast global warming is a direct result of human activity [1]. The resulting climate change is linked to significant environmental impacts that are connected to the disappearance of animal species [2,3], decreased agricultural yield [4–6], increasingly frequent extreme weather events [7,8], human migration [9–11], and conflicts [12–14]. -
Storing Syngas Lowers the Carbon Price for Profitable Coal Gasification
Carnegie Mellon Electricity Industry Center Working Paper CEIC-07-10 www.cmu.edu/electricity Storing syngas lowers the carbon price for profitable coal gasification ADAM NEWCOMER AND JAY APT Carnegie Mellon Electricity Industry Center, Tepper School of Business, and Department of Engineering and Public Policy, 254 Posner Hall, Carnegie Mellon University, Pittsburgh, Pennsylvania 15213 Integrated gasification combined cycle (IGCC) electric power generation systems with carbon capture and sequestration have desirable environmental qualities, but are not profitable when the carbon dioxide price is less than approximately $50 per metric ton. We examine whether an IGCC facility that operates its gasifier continuously but stores the syngas and produces electricity only when daily prices are high may be profitable at significantly lower CO2 prices. Using a probabilistic analysis, we have calculated the plant-level return on investment (ROI) and the value of syngas storage for IGCC facilities located in the US Midwest using a range of storage configurations. Adding a second turbine to use the stored syngas to generate electricity at peak hours and implementing 12 hours of above ground high pressure syngas storage significantly increases the ROI and net present value. Storage lowers the carbon price at which IGCC enters the US generation mix by approximately 25%. 1 Carnegie Mellon Electricity Industry Center Working Paper CEIC-07-10 www.cmu.edu/electricity Introduction Producing electricity from coal-derived synthesis gas (syngas) in an integrated gasification combined cycle (IGCC) facility can improve criteria pollutant performance over other coal-fueled technologies such as pulverized coal (PC) facilities [1-5] and can be implemented with carbon capture and sequestration. -
Assessment of Innovative and Automated Freight Strategies and Technologies—Phase I Final Report
Technical Report Documentation Page 1. Report No. 2. Government Accession No. 3. Recipient's Catalog No. FHWA/TX-17/0-6837-1 4. Title and Subtitle 5. Report Date ASSESSMENT OF INNOVATIVE AND AUTOMATED FREIGHT February 2017 STRATEGIES AND TECHNOLOGIES—PHASE I FINAL REPORT 6. Performing Organization Code 7. Author(s) 8. Performing Organization Report No. Curtis Morgan, Jeffery Warner, Allan Rutter, Dahye Lee, C. James Report 0-6837-1 Kruse, Dong Hun Kang, Mario Monsreal, Jolanda Prozzi, Juan Carlos Villa, Jeffrey Borowiec, Leslie Olson, David Bierling, and Edwin Varela 9. Performing Organization Name and Address 10. Work Unit No. (TRAIS) Texas A&M Transportation Institute The Texas A&M University System 11. Contract or Grant No. College Station, Texas 77843-3135 Project 0-6837 12. Sponsoring Agency Name and Address 13. Type of Report and Period Covered Texas Department of Transportation Technical Report: Research and Technology Implementation Office March 2016 125 E. 11th Street 14. Sponsoring Agency Code Austin, Texas 78701-2483 15. Supplementary Notes Project performed in cooperation with the Texas Department of Transportation and the Federal Highway Administration. Project Title: Assessment of Innovative and Automated Freight Systems and Development of Evaluation Tools URL: http://tti.tamu.edu/documents/0-6837-1.pdf 16. Abstract Many innovative freight delivery strategies and technologies have been proposed to address the future freight needs of Texas’s growing population. Changes in both buying habits and a shift toward direct home package delivery threaten to dramatically change distribution patterns and increase the number of intercity and local delivery trucks on Texas Department of Transportation (TxDOT) roadways. -
Changing LNG Market Dynamics – Implications on Supply Security in the APEC Region
Changing LNG Market Dynamics – Implications on Supply Security in the APEC Region APEC Oil and Gas Security Studies | Series 17 APEC Energy Working Group September 2020 APEC Project: EWG 01 2020S Produced by Asia Pacific Energy Research Centre (APERC) Institute of Energy Economics, Japan Inui Building, Kachidoki 11F, 1-13-1 Kachidoki Chuo-ku, Tokyo 104-0054 Japan Tel: (813) 5144-8551 Fax: (813) 5144-8555 E-mail: [email protected] (administration) Website: http://aperc.or.jp/ For Asia-Pacific Economic Cooperation Secretariat 35 Heng Mui Keng Terrace Singapore 119616 Tel: (65) 68919 600 Fax: (65) 68919 690 Email: [email protected] Website: www.apec.org © 2020 APEC Secretariat APEC#220-RE-01.9 ISBN: 978-981-14-7794-2 OGSS Series 17 Changing LNG Market Dynamics – Implications on Supply Security in the APEC Region 3 | P a g e TABLE OF CONTENTS Table of Contents .......................................................................................................................... 3 Foreword ....................................................................................................................................... 6 Acknowledgements ....................................................................................................................... 7 Project coordinators .................................................................................................................. 7 Authors ...................................................................................................................................... 7 Editors -
NATURAL GAS STORAGE: Actions Needed to Assess Inspection
United States Government Accountability Office Report to Congressional Requesters October 2019 NATURAL GAS STORAGE Actions Needed to Assess Inspection Workload and Progress toward Safety Outcomes GAO-20-167 October 2019 NATURAL GAS STORAGE Actions Needed to Assess Inspection Workload and Progress toward Safety Outcomes Highlights of GAO-20-167, a report to congressional requesters Why GAO Did This Study What GAO Found About 400 natural gas storage sites In 2018, the U.S. Department of Transportation’s Pipeline and Hazardous are important to the U.S. natural gas Materials Safety Administration (PHMSA) set a goal for its natural gas storage system, providing about 30 percent of inspection program to inspect all approximately 400 natural gas storage sites the nation's energy. During a 2015 leak within 5 years, according to agency officials. PHMSA expected that all 25 eligible at a storage site near Los Angeles, states would help inspect sites, but only 10 states agreed to partner with the about 8,000 families were temporarily agency. As a result, the agency’s inspection workload increased by almost 60 relocated due to symptoms such as percent from when it set its goal, according to PHMSA data. Because of the migraines, nausea, and respiratory increase in its inspection workload over its preliminary estimate, PHMSA does problems. The leak raised concerns not have assurance that it has enough resources to meet its inspection goal. about health and safety risks from Furthermore, PHMSA has not used a workforce analysis to inform its budget other storage sites. In 2017, GAO recommended that PHMSA take requests. -
Update to Gas Storage Needed to Support Electricity Generation
Gas Storage Needed to Support Electricity Generation Prepared For The Utility Air Regulatory Group and the American Public Power Association An Update to Implications of Greater Reliance on Natural Gas for Electricity Generation (2010) June 2012 Update on Natural Gas Storage Needed to Support Electricity Generation Table of Contents Executive Summary ....................................................................................................................................... 3 Recent and Expected Additions to Storage .................................................................................................. 5 Generator Use of Storage ............................................................................................................................. 7 Use of Storage to Provide Reliability ............................................................................................................ 8 Generator Use of Storage for Imbalance Management ............................................................................. 10 Use of Storage to Provide Flexible Pipeline Services .................................................................................. 11 Competition for the Geology By Other Uses .............................................................................................. 14 Other Types of Storage May Increase in Relevance ................................................................................... 16 Final Thoughts ............................................................................................................................................ -
A Comparative Exergoeconomic Evaluation of the Synthesis Routes for Methanol Production from Natural Gas
applied sciences Article A Comparative Exergoeconomic Evaluation of the Synthesis Routes for Methanol Production from Natural Gas Timo Blumberg 1,*, Tatiana Morosuk 2 and George Tsatsaronis 2 ID 1 Department of Energy Engineering, Zentralinstitut El Gouna, Technische Universität Berlin, 13355 Berlin, Germany 2 Institute for Energy Engineering, Technische Universität Berlin, 10587 Berlin, Germany; [email protected] (T.M.); [email protected] (G.T.) * Correspondence: [email protected]; Tel.: +49-30-314-23343 Received: 30 October 2017; Accepted: 20 November 2017; Published: 24 November 2017 Abstract: Methanol is one of the most important feedstocks for the chemical, petrochemical, and energy industries. Abundant and widely distributed resources as well as a relative low price level make natural gas the predominant feedstock for methanol production. Indirect synthesis routes via reforming of methane suppress production from bio resources and other renewable alternatives. However, the conventional technology for the conversion of natural gas to methanol is energy intensive and costly in investment and operation. Three design cases with different reforming technologies in conjunction with an isothermal methanol reactor are investigated. Case I is equipped with steam methane reforming for a capacity of 2200 metric tons per day (MTPD). For a higher production capacity, a serial combination of steam reforming and autothermal reforming is used in Case II, while Case III deals with a parallel configuration of CO2 and steam reforming. A sensitivity analysis shows that the syngas composition significantly affects the thermodynamic performance of the plant. The design cases have exergetic efficiencies of 28.2%, 55.6% and 41.0%, respectively. -
Underground Storage of Natural Gas Storing Natural Gas the Same Way Nature Always Has… Deep Underground
UNDERGROUND STORAGE OF NATURAL GAS STORING NATURAL GAS THE SAME WAY NATURE ALWAYS HAS… DEEP UNDERGROUND Most of the natural gas used in Southern California travels from supply sources as far away as Texas and Canada. So, Underground storage is based on the simple in order to maintain a balance between supply and demand, premise that if an underground rock formation storage is a necessity. Without it, we might not always be held oil and natural gas securely for millions of able to meet our customers’ needs. years, it could continue to do under controlled Customer needs change by the season, by the day, and even conditions. by the hour. On a cold winter day, for example, residential customers can use seven times the amount of natural gas Extensive research and our experience have proven that used on an average summer day. this concept is sound. Depleted oil and natural gas fields Five decades ago, balancing customer demand meant relying offer ideal storage conditions because they are comprised on natural gas holding structures, which stood several stories of natural underground traps. Care is taken that the original high and resembled oil storage tanks. formation pressure of the field is not exceeded. These subterranean rock formations can be repeatedly refilled and In 1941 we introduced a new system to the Southwest: drawn from to meet the fluctuating needs of our customers. underground storage of natural gas. This system is based on the simple premise that if an underground rock formation When out of state pipelines can’t deliver enough natural held oil and natural gas securely for millions of years, it could gas to meet heavy demand, which might occur on a cold continue to do so under controlled circumstances. -
The Future of Gasification
STRATEGIC ANALYSIS The Future of Gasification By DeLome Fair coal gasification projects in the U.S. then slowed significantly, President and Chief Executive Officer, with the exception of a few that were far enough along in Synthesis Energy Systems, Inc. development to avoid being cancelled. However, during this time period and on into the early 2010s, China continued to build a large number of coal-to-chemicals projects, beginning first with ammonia, and then moving on to methanol, olefins, asification technology has experienced periods of both and a variety of other products. China’s use of coal gasification high and low growth, driven by energy and chemical technology today is by far the largest of any country. China markets and geopolitical forces, since introduced into G rapidly grew its use of coal gasification technology to feed its commercial-scale operation several decades ago. The first industrialization-driven demand for chemicals. However, as large-scale commercial application of coal gasification was China’s GDP growth has slowed, the world’s largest and most in South Africa in 1955 for the production of coal-to-liquids. consistent market for coal gasification technology has begun During the 1970s development of coal gasification was pro- to slow new builds. pelled in the U.S. by the energy crisis, which created a political climate for the country to be less reliant on foreign oil by converting domestic coal into alternative energy options. Further growth of commercial-scale coal gasification began in “Market forces in high-growth the early 1980s in the U.S., Europe, Japan, and China in the coal-to-chemicals market. -
Exergy Recovery During Liquefied Natural Gas Regasification
View metadata, citation and similar papers at core.ac.uk brought to you by CORE provided by Infoscience - École polytechnique fédérale de Lausanne 535 A publication of CHEMICAL ENGINEERING TRANSACTIONS VOL. 70, 2018 The Italian Association of Chemical Engineering Online at www.aidic.it/cet Guest Editors: Timothy G. Walmsley, Petar S. Varbanov, Rongxin Su, Jiří J. Klemeš Copyright © 2018, AIDIC Servizi S.r.l. ISBN 978-88-95608-67-9; ISSN 2283-9216 DOI: 10.3303/CET1870090 Exergy Recovery During Liquefied Natural Gas Regasification Using Methane as Working Fluid Francesca Belfiore*, Francesco Baldi, François Maréchal École Polytechnique Fédérale de Lausanne (EPFL Valis Wallis), SCI-STI-FM, Industrial Process and Energy Systems Engineering (IPESE), Rue de l’Industrie 17, Case postale 440, CH-1951 Sion, Switzerland [email protected] The increased concerns about the effect of human activities on the climate have pushed natural gas among the most obvious solutions for the transition to a low-carbon economy. The growing importance and volumes of liquefied natural gas for transportation over long distances come as a consequence of this tendency. The liquefaction of natural gas requires a high amount of energy that can be recovered during the re-gasification phase. In this paper, a novel approach for this purpose is presented, where the main feature is the use of a combination of Rankine and Brayton cycles while retaining natural gas as the only working fluid of the system. The proposed system is optimized for cost and exergy efficiency using a bi-level multi-objective optimization procedur e, where the master level is setup as a nonlinear optimization problem and solved using an evolutionary algorithm , while the slave level as a mixed integer-linear programming problem. -
Natural Gas Annual Questionnaire 2017-2021
NATURAL GAS ANNUAL QUESTIONNAIRE 2017-2021 AND HISTORICAL REVISIONS August 2018 Attached is the annual questionnaire for natural gas which provides for the submission of 2017-2021 data and historical revisions where applicable. Countries reporting to the IEA are requested to complete the questionnaire at the latest by 30 September. Earlier submissions are welcome. Countries reporting to Eurostat are requested to complete the questionnaire by 30 November (Regulation (EC) No 1099/2008 on energy statistics). Earlier submissions are welcome. Please send your questionnaire to: International Energy Agency (IEA/OECD), Energy Data Centre (the IEA will forward the data to the United Nations Economic Commission for Europe in Geneva). European Commission, Eurostat, Energy Statistics (for EU Member States, European Economic Area countries, EU Candidate Countries and Potential Candidates, Energy Community Contracting Parties) United Nations Statistics Division, Energy Statistics Section Transmission details are provided in the “Data communication procedures” section. ANNUAL GAS QUESTIONNAIRE Data communication procedures IEA 31-35, rue de la Fédération, 75739, Paris, Cedex 15, France Please complete data for your country on the Energy Validation Outlet: https://evo.iea.org Alternatively send the completed questionnaire in a CSV or Excel file as an e-mail attachment. to [email protected] For questions regarding the questionnaire, contact [email protected] * * * * * * * * * * * * * * * * * * * * * * * * * * * * * * * * * Eurostat European Commission – Eurostat, Unit E.5: Energy, L-2920 Luxembourg (for EU Member States, European Economic Area countries, EU Candidate Countries and Potential Candidates, Energy Community Contracting Parties) The completed MS Excel questionnaire should be transmitted via the Single Entry Point following the implementing procedures of EDAMIS (Electronic Data Files Administration And Management Information System): https://webgate.ec.europa.eu/edamis/ selecting the electronic data collection ENERGY_NTGAS_A.