In 3,708,275 Camp, Jr
Total Page:16
File Type:pdf, Size:1020Kb
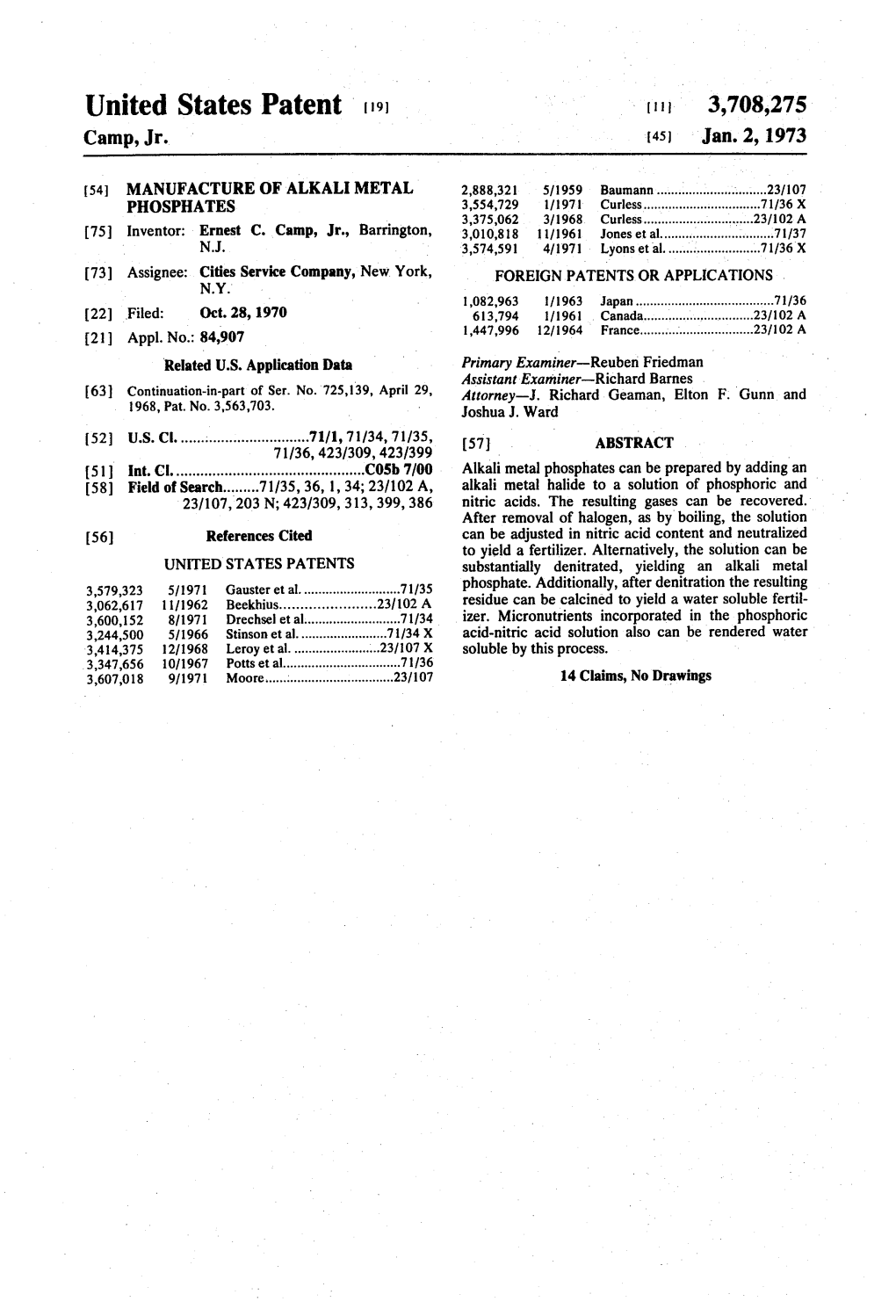
Load more
Recommended publications
-
A Review of the Patents and Literature on the Manufacture of Potassium Nitrate with Notes on Its Occurrence and Uses
UNITED STATES DEPARTMENT OF AGRICULTURE Miscellaneous Publication No. 192 Washington, D.C. July 1934 A REVIEW OF THE PATENTS AND LITERATURE ON THE MANUFACTURE OF POTASSIUM NITRATE WITH NOTES ON ITS OCCURRENCE AND USES By COLIN W. WHITTAKER. Associate Chemist and FRANK O. LUNDSTROM, Assistant Chemist Division of Fertilizer Technology, Fertilizer Investigationa Bureau of Chemistry and Soils For sale by the Superintendent of Documents, Washington, D.C. .....-..- Price 5 cents UNITED STATES DEPARTMENT OF AGRICULTURE Miscellaneous Publication No. 192 Washington, D.C. July 1934 A REVIEW OF THE PATENTS AND LITERATURE ON THE MANUFACTURE OF POTASSIUM NITRATE WITH NOTES ON ITS OCCURRENCE AND USES By COLIN W. WHITTAKER, associate chemist, and FRANK O. LUNDSTROM, assistant chemist, Division of Fertilizer Technology, Fertilizer Investigations, Bureau oj Chemistry and Soils CONTENTS Page Production of potassium nitrate —Contd. Page Processes involving dilute oxides of Introduction } nitrogen 22 Historical sketch 3 Absorption in carbonates, bicarbon- Statistics of the saltpeter industry 4 ates, or hydroxides 22 Potassium nitrate as a plant food 8 Conversion of nitrites to nitrates 23 Occurrence of potassium nitrate 9 Processes involving direct action of nitric Production of potassium nitrate 11 acid or oxides of nitrogen on potassium Saltpeter from the soil 11 compounds 23 In East India 11 Potassium bicarbonate and nitric In other countries 12 acid or ammonium nitrate 23 Chilean high-potash nitrate 13 Potassium hydroxide or carbonate Composting and -
(12) Patent Application Publication (10) Pub. No.: US 2002/0161249 A1 Mull Et Al
US 2002O161249A1 (19) United States (12) Patent Application Publication (10) Pub. No.: US 2002/0161249 A1 Mull et al. (43) Pub. Date: Oct. 31, 2002 (54) PREPARATION OF EPOXIDES FROM (21) Appl. No.: 09/792,390 ALKANES USING LANTHANDE-PROMOTED SILVER (22) Filed: Feb. 22, 2001 CATALYSTS Publication Classification (76) Inventors: Guido Mul, Nootdorp (NL); Marianna F. Asaro, Belmont, CA (US); Albert S. (51) Int. Cl." ............................................. C07D 301/02 Hirschon, Menlo Park, CA (US); (52) U.S. Cl. .............................................................. 549/534 Retri B. Wilson JR., Palo Alto, CA (57) ABSTRACT A process is provided for use in the conversion of alkanes Correspondence Address: into alkylene oxides, having particular utility in the conver REED & ASSOCATES Sion of propane to form propylene oxide, using a lanthanide 800 MENLO AVENUE promoted, Supported, Silver catalyst prepared via precipita SUTE 210 tion. A preferred embodiment uses Silver nitrate and MENLO PARK, CA 94025 (US) lanthanum nitrate to form the catalyst on a BaCO Support. Patent Application Publication Oct. 31, 2002 US 2002/0161249 A1 10 O 2000 4000 6000 Time (s) FIG. 1 US 2002/0161249 A1 Oct. 31, 2002 PREPARATION OF EPOXDES FROM ALKANES 0006 Catalysts composed of lanthanum carbonate and USINGLANTHANDE-PROMOTED SILVER chromium oxide have been shown to be active and Selective CATALYSTS at lower temperatures but have only been used in the oxidative dehydrogenation of isobutane, See Hoang et al. TECHNICAL FIELD (1997).J. Catal. 171:313. Carbonate-supported catalysts are currently used in ethylene epoxidation and often contain 0001. This invention relates generally to novel catalysts reduced Silver and an O-alumina carrier. -
Nano3,KNO3,Rbno3,Csno3)
id13369703 pdfMachine by Broadgun Software - a great PDF writer! - a great PDF creator! - http://www.pdfmachine.com http://www.broadgun.com ISSN : 0974 - 7524 Volume 8 Issue 4 Physical CCHHEEAnMM IndIIiaSSn TTJouRRrnaYYl Full Paper PCAIJ, 8(4), 2013 [140-145] Phase equilibria of alkali metal salt (NaNO3,KNO3,RbNO3,CsNO3) in system HOCH2CH(OH)CH2OH - H2O at various temperatures Zhang Hui-Ying1,2, Li Shu-Ni1, Zhai Quan-Guo1, Ou Yang-Miao2, Jiang Yu-Cheng1, Hu Man-Cheng1* 1Key Laboratory of Macromolecular Science of Shaanxi Province, School of Chemistry and Materials Science, Shaanxi ’an, Shaanxi, 710062, (CHINA) Normal University, Xi 2Department of Chemistry and Life Science, Hechi University, Yizhou,Guangxi, 546300, (CHINA) E-mail: [email protected]. ABSTRACT KEYWORDS By using a self-made research device for phase equilibrium, the equilib- Alkali metal nitrate; Glycerin; rium solubility of the saturation ternary system of NaNO3/KNO3/RbNO3/ °C Solubility; CsNO3 - HOCH2CH (OH)CH2OH - H2O at 35 and 45 was measured, and simultaneously the density and refractive index of this system was deter- Density; mined. The experimental results showed that, in all systems, with the Refractive index. increase of weight percentage of glycerol, the solubility and density of the salt in mixed solvent were reduced, while the refractive index was increased gradually. The solubility, refractive index and density data in all the saturation systems were fitted by the four-parameter empirical correlation equation. 2013 Trade Science Inc. - INDIA INTRODUCTION and refractive index, which aims to provide the neces- sary basic reference data for the separation and purifi- Crystallization, separation and purification can be cation of alkali metal nitrate. -
A Vibrational Study of a Selected Series of Matrix-Isolated Alkali-Metal Chlorate and Nitrate Salts
A VIBRATIONAL STUDY OF A SELECTED SERIES OF MATRIX-ISOLATED ALKALI-METAL CHLORATE AND NITRATE SALTS By NORMAN RAY SMYRL 11 Bachelor of Science West Texas State University Canyon, Texas 1969 Master of Science West Texas State University Canyon, Texas 1971 Submitted to the Faculty of t.he Graduate College of the Oklahoma State University in partial fulfillment of the requirements for the Degree of DOCTOR OF PHILOSOPHY December, 1973 Yk~i$ I q73l) S{;t'lv C.vp, ')._ OKLAHOMA STATE UNIVERSITY LIBRARY M.Af~ 14 1975 A VIBRATIONAL STUDY OF A SELECTED SERIES OF MATRIX-ISOLATED ALKALI-METAL CHLORATE AND NITRATE SALTS Thesis Approved: ,, Thesis Adviser 4~L1D-:Loe~ ,s); ~.2. ~ Dean of the Graduate College 902238 ii ACKNOWLEDGEMENTS Grateful acknowledgement is made to Dr. J. Paul Devlin, thesis director, for continuing assistance and guidance throughout this work. I would like to express my love and gratitude to my wife, Sherry, for her encouragement and understanding throughout my tenure in graduate school and for her patient assistance in the preparation of this manu script. I would also like to gratefully acknowledge the financial support during this work provided by the National Science Foundation and Oklahoma State University. Finally, I would like to thank Wayne Adkins and Heinz Hall for their aid in the design and repair of equipment utilized for this study. iii TABLE OF CONTENTS Chapter Page I. INTRODUCTION 1 Scope of the Problem. 1 Matrix Isolation. 3 Infrared Matrix Isolation. 3 Raman Matrix Isolation . 5 Chlorates .•......... 6 The Symmetry and Selection Rules for the Chlorate Anion .... -
The 70Th Southeastern Regional Meeting of the American Chemical Society October 31-November 3, 2018 Augusta, GA
The 70th Southeastern Regional Meeting of the American Chemical Society October 31-November 3, 2018 Augusta, GA Michael Bronikowski and Robert Lascola, Program Chairs WEDNESDAY MORNING Augusta Marriott at the Convention Center Estes A Chemistry Applications of Neutron Scattering Cosponsored by NUCL Financially supported by Shull Wollan Center – a Joint Institute for Neutron Sciences J. Z. Larese, Organizer, Presiding 8:00 Introductory Remarks. 8:15 1. Investigating phase transitions and structure changes under applied conditions with neutron scattering. C. Hoffmann, A.J. Schultz, C. Fancher 8:45 2. Upgraded diffractometer at HFIR, HB-2C: WAND2. M. Frontzek, K.M. Andrews, A.B. Jones, R. Whitfield, B. Chakoumakos, J. Fernandez-Baca 9:15 3. Adsorption of cycloalkanes on MgO (100), graphite and hexagonal boron nitride: A thermodynamic, modeling and neutron scattering study. F. Wahida, J.Z. Larese 9:35 4. Solution structure of an intramembrane aspartyl protease via small angle neutron scattering. R.L. Lieberman, S. Naing, R. Oliver, K.L. Weiss, V. Urban 9:55 Intermission. 10:15 5. Next-generation neutron vibrational spectroscopy of organic molecular crystals, cocrystals, and polymorphs: Applications for benchmarking density functional theory calculations. A. Sedova, A. Pandey 10:35 6. New insights on the nature of pressure induced amorphous ices. C.A. Tulk, J. Molaison, D. Klug, A. Makhluf, C. Manning 11:05 7. Probing the structures and dynamics of biological interfaces by neutron scattering. J. Majewski WEDNESDAY MORNING, 10/31/18 Augusta Marriott at the Convention Center Lamar C Frontiers in Nucleic Acid Chemistry J. T. Petty, Organizer, Presiding 8:00 Introductory Remarks. 8:05 8. -
The 70Th Southeastern Regional Meeting of the American Chemical Society
The 70th Southeastern Regional Meeting of the American Chemical Society October 31 - November 3, 2018 Augusta, GA Program 70th Southeastern Regional Meeting of the American Chemical Society Augusta Marriott at the Convention Center October 31 - November 3, 2018 Hosted by the ACS-Savannah River Section 2 SERMACS 2018 “Security Tomorrow Through Inovation Today” Augusta Marriott at the Convention Center, Augusta, Georgia General Co-Chairs’ Welcome On behalf of the Savannah River Section and the 2018 organizing committee, we want to welcome you to the 70th South- eastern Regional Meeting of the American Chemical Society (SERMACS 2018). With over 1140 abstracts, 46 exhibitors, and 34 graduate schools, this year’s meeting is definitely “Linking Chemistry in the Southeast” – to quote from our 2006 theme. Those of you visiting the Central Savannah River Area (CSRA) for the first time will find many exciting activities to explore. We have tried to promote the colloquialism that is the hallmark of regional meetings through a number of special events where you can meet and network amongst your colleagues from throughout the southeast, the nation, and 13 countries. Please join us for the ACS Division of Professional Relations (PROF) sponsored Trick-or-Treat Networking Reception in the Olmstead B Exposition Hall, for the National Historic Chemical Landmark (NHCL) Dedication and Reception at the SRS Heritage Museum in Aiken, SC, or the Fermentation Chemistry Social at the Savannah River Brewing Company, where you can dine at local Food Trucks, drink local brew, enjoy a tour of the brewery, and play some games. There are a number of new features at this year’s meeting. -
Ultra-Thin Mems Fabricated Tynodes for Electron Multiplication
Delft University of Technology Ultra-thin mems fabricated tynodes for electron multiplication Prodanovic, Violeta DOI 10.4233/uuid:1f889837-0d94-415c-8137-6065c0a44245 Publication date 2019 Document Version Final published version Citation (APA) Prodanovic, V. (2019). Ultra-thin mems fabricated tynodes for electron multiplication. https://doi.org/10.4233/uuid:1f889837-0d94-415c-8137-6065c0a44245 Important note To cite this publication, please use the final published version (if applicable). Please check the document version above. Copyright Other than for strictly personal use, it is not permitted to download, forward or distribute the text or part of it, without the consent of the author(s) and/or copyright holder(s), unless the work is under an open content license such as Creative Commons. Takedown policy Please contact us and provide details if you believe this document breaches copyrights. We will remove access to the work immediately and investigate your claim. This work is downloaded from Delft University of Technology. For technical reasons the number of authors shown on this cover page is limited to a maximum of 10. ULTRA-THIN MEMS FABRICATED TYNODES FOR ELECTRON MULTIPLICATION 537226-L-sub01-bw-Frodanovic Processed on: 29-10-2019 PDF page: 1 537226-L-sub01-bw-Frodanovic Processed on: 29-10-2019 PDF page: 2 ULTRA-THIN MEMS FABRICATED TYNODES FOR ELECTRON MULTIPLICATION Proefschrift ter verkrijging van de graad van doctor aan de Technische Universiteit Delft, op gezag van de Rector Magnificus prof. dr. ir. T.H.J.J. van der Hagen, voorzitter van het College voor Promoties, in het openbaar te verdedigen op dinsdag 19 november 2019 om 15:00 uur door Violeta PRODANOVIC´ Master of Science in Electrical Engineering and Computer Science, Universiteit van Belgrado, Belgrado, Servië, geboren te Zvornik, Joegoslavië. -
United States Patent Office Patented Feb
3,497,404 United States Patent Office Patented Feb. 24, 1970 1. 2 itate mixing with the magnesium powder. I have also 3,497,404 CAST FELARE COMPOSITION OF MAGNESUM found that these salt mixtures wet magnesium and hence DISPERSED IN A MATREX, MOSTLY SODIUM are specially easily mixed to form a uniform slurry. NTRATE The proportion of metal to oxidizer salt is between Ralph H. Hiltz, Pittsburgh, Pa., assignor to Mine Safety about 1 and 1.85 parts metal to each part salt, preferably Appliances Company, Pittsburgh, Pa., a corporation of between 1.25 and 1.50 to 1. Pennsylvania The flares are in use normally ignited at one end and No Drawing. Fied Jan. 28, 1969, Ser. No. 794,779 Int, C. C06d 1/10 burn lengthwise, the flare life depending on the rate at U.S. C. 149-17 4. Claims which the burning front proceeds lengthwise of the flare, O designated as linear burning rate. The linear burning rate can be substantially adjusted, suitably from 4-10 seconds per inch, by adjusting the proportion of magnesium to ABSTRACT OF THE DISCLOSURE Salt, the magnesium particle size and the amount of added Cast high-intensity illuminating flares contain a coarse salt. Burning rate decreases with increasing amounts of magnesium powder dispersed in a matrix of a solidified 5 magnesium up to about 60% by weight magnesium and salt melt containing principally sodium nitrate with a then increases with further increase in magnesium con minor amount of another alkali metal or alkaline earth tent. Increasing the amount of added salt decreases burn metal nitrate or nitrite. -
Microwave Enhancement of Energetic Materials Combustion Through Gas-Phase Flame Interactions
Iowa State University Capstones, Theses and Graduate Theses and Dissertations Dissertations 2020 Microwave enhancement of energetic materials combustion through gas-phase flame interactions Stuart James Barkley Iowa State University Follow this and additional works at: https://lib.dr.iastate.edu/etd Recommended Citation Barkley, Stuart James, "Microwave enhancement of energetic materials combustion through gas-phase flame interactions" (2020). Graduate Theses and Dissertations. 18277. https://lib.dr.iastate.edu/etd/18277 This Thesis is brought to you for free and open access by the Iowa State University Capstones, Theses and Dissertations at Iowa State University Digital Repository. It has been accepted for inclusion in Graduate Theses and Dissertations by an authorized administrator of Iowa State University Digital Repository. For more information, please contact [email protected]. Microwave enhancement of energetic materials combustion through gas-phase flame interactions by Stuart James Barkley A dissertation submitted to the graduate faculty in partial fulfillment of the requirements for the degree of DOCTOR OF PHILOSOPHY Major: Mechanical Engineering Program of Study Committee: Travis R Sippel, Major Professor James B Michael Shankar Subramaniam Theodore J Heindel Jiming Song The student author, whose presentation of the scholarship herein was approved by the program of study committee, is solely responsible for the content of this dissertation. The Graduate College will ensure this dissertation is globally accessible and will -
1 High Temperature Molten Salts for Solar Power Application Thomas
Chapter 20 in “Molten Salts Chemistry: From Lab To Applications”, edited by Lantelme, F. and Groult, H., Elsevier, 2013 https://doi.org/10.1016/B978-0-12-398538-5.00020-2 High temperature molten salts for solar power application Thomas Bauer1, Nicole Pfleger2, Doerte Laing2, Wolf-Dieter Steinmann2, Markus Eck2, Stefanie Kaesche3 1 German Aerospace Center (DLR), Institute of Technical Thermodynamics, Linder Höhe, 51147 Köln, Germany, [email protected] 2 German Aerospace Center (DLR), Institute of Technical Thermodynamics, Pfaffenwaldring 38-40, 70569 Stuttgart, Germany 3 Materials Testing Institute University of Stuttgart (MPA), Pfaffenwaldring 32, 70569 Stuttgart, Germany Abstract: Solar thermal power plants are a key technology for electricity generation from renewable energy resources. Thermal energy storage (TES) systems correct the mismatch between the solar supply and the power demand. TES makes it possible to meet the intermediate load profile with dispatchable power, a benefit that has a high value to power utilities and that gives concentrating solar power (CSP) technology an edge over photovoltaic and wind power. Hence, TES is a key technology for solar thermal energy utilization with growing present and future importance. This chapter focuses on material aspects of alkali nitrate salts. They include thermal properties, thermal decomposition processes, steel corrosion issues and phase diagrams of multicomponent salt systems. In addition, two CSP applications using molten nitrate salts as sensible and latent TES are discussed. Keywords: nitrates, nitrites, phase change materials (PCM), corrosion, heat transfer fluids, thermophysical properties, thermal decomposition, phase diagrams, multicomponent salt systems. 1 Chapter 20 in “Molten Salts Chemistry: From Lab To Applications”, edited by Lantelme, F. -
United States Patent (19) 11) Patent Number: 4,545,974 Thompson (45) Date of Patent: Oct
United States Patent (19) 11) Patent Number: 4,545,974 Thompson (45) Date of Patent: Oct. 8, 1985 (54) PROCESS FOR PRODUCING ALKALI METAL FERRATES UTILIZING HEMATITE OTHER PUBLICATIONS AND MAGNETTE Bailar et al., "Comprehensive Inorganic Chemistry', Pergamon Press, N.Y., vol. 3, 1973. 76 Inventor: John A. Thompson, Nassau, The Primary Examiner-H. T. Carter Bahamas Attorney, Agent, or Firm-Kenyon & Kenyon 57 ABSTRACT (21) Appl. No.: 590,567 Alkali metal iron (IV) and iron (VI) ferrates are pro duced by forming a particulate mixture of reactants (22 Filed: Mar. 16, 1984 including an alkali metal nitrogen oxygen compound and an iron material selected from the group of iron oxide, Fe2O3, Fe3O4 and an iron compound which self (51) Int. Cl." .............................................. C01G 49/00 reacts at a temperature less than about 1100° C. to form 52 U.S. Cl. .................................................... 423/594 Fe2O3. The mixture of reactants is subjected to a prede 58) Field of Search ......................................... 423/594 termined elevated temperature for a predetermined time duration sufficient to bring about a reaction be (56) References Cited tween the reactants which produces at least one of iron (IV) and iron (VI) ferrates. The molar ratio of alkali U.S. PATENT DOCUMENTS metal nitrogen oxygen compound to the iron material is 2,835,553 5/1958 Harrison et al. .................... 423/594 preferably in the range extending between about 4:1 and about 8:1. FOREIGN PATENT DOCUMENTS 1013272 1/1958 Fed. Rep. of Germany ...... 423/594 23 Claims, No Drawings 4,545,974 1. 2 duced in these methods are in solution and require a PROCESS FOR PRODUCING ALKAL METAL crystallization therefrom in order to avoid the obvious FERRATES UTILIZING HEMATITE AND handling, shipping and storage disadvantages associated MAGNETITE with aqueous solutions. -
CO2 Uptake and Cyclic Stability of Mgo-Based CO2 Sorbents Promoted with Alkali Metal Nitrates and Their Eutectic Mixtures
Research Collection Journal Article CO2 Uptake and Cyclic Stability of MgO-Based CO2 Sorbents Promoted with Alkali Metal Nitrates and Their Eutectic Mixtures Author(s): Dal Pozzo, Alessandro; Armutlulu, Andac; Rekhtina, Margarita; Abdala, Paula M.; Müller, Christoph R. Publication Date: 2019-02-25 Permanent Link: https://doi.org/10.3929/ethz-b-000327318 Originally published in: ACS Applied Energy Materials 2(2), http://doi.org/10.1021/acsaem.8b01852 Rights / License: In Copyright - Non-Commercial Use Permitted This page was generated automatically upon download from the ETH Zurich Research Collection. For more information please consult the Terms of use. ETH Library CO2 Uptake and Cyclic Stability of MgO-Based CO2 Sorbents Promoted with Alkali Metal Nitrates and Their Eutectic Mixtures Alessandro Dal Pozzo a,b, Andaç Armutlulu b, Margarita Rekhtina b, Paula M. Abdala, Christoph R. Müller b,* a Laboratory of Industrial Safety and Environmental Sustainability Department of Civil, Chemical, Environmental and Materials Engineering, Alma Mater Studiorum - Università di Bologna, via Terracini 28, 40131 Bologna, Italy b Laboratory of Energy Science and Engineering Department of Mechanical and Process Engineering, ETH Zürich, Leonhardstrasse 21, 8092 Zürich, Switzerland *Corresponding author. Tel.: +41 44 632 3440. E-mail address: [email protected] (Prof. Christoph Müller) ABSTRACT CO2 capture and storage (CCS) is a technological solution to stabilize or even reduce the atmospheric concentration of the greenhouse gas CO2, to mitigate climate change. In this context, MgO is a promising solid CO2 sorbent, as the energy penalty sorbent regeneration is comparatively small, but it requires the addition of promoters, typically alkali metal nitrates, to yield acceptable kinetics.