US5109702.Pdf
Total Page:16
File Type:pdf, Size:1020Kb
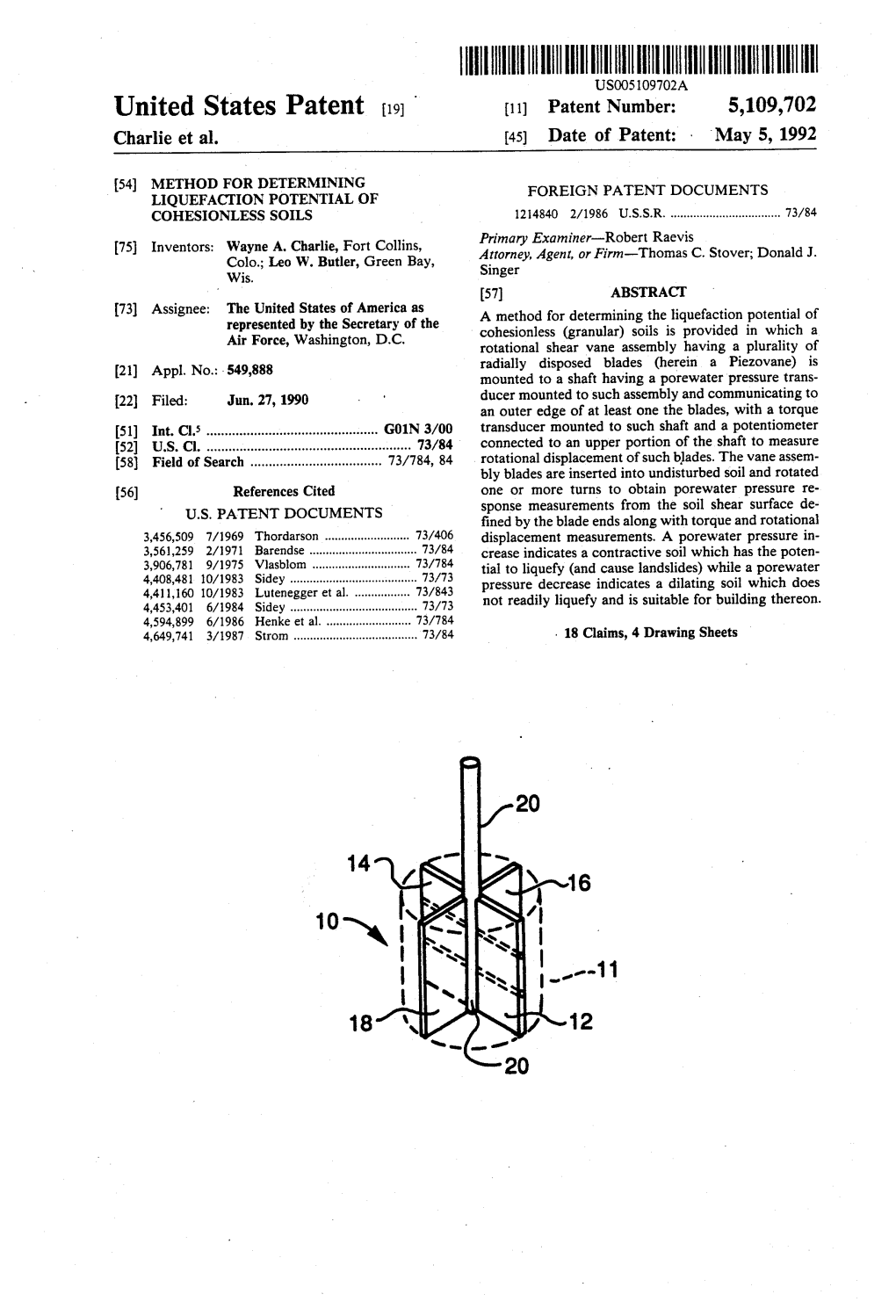
Load more
Recommended publications
-
A Qljarter Century of Geotechnical Researcll
A QlJarter Century of Geotechnical Researcll PUBLICATION NO. FHWA-RD-98-139 FEBRUARY 1999 1111111111111111111111111111111 PB99-147365 \c-c.J/t).:.. L~.i' . u.s. D~~~~~~~Co~~~~~erce~ Natronal_Tec~nical Information Service u.s. DepartillCi"li of Transportation Spnngfleld, Virginia 22161 Research, Development & Technology Turner-Fairbank Highway Research Center 6300 Georgetown Pike McLean, VA 22101-2296 FOREWORD This report summarizes Federal Highway Administration (FHW!\) geotechnical research and development activities during the past 25 years. The report incl!Jde~: significant accomplishments in the areas of bridge foundations, ground improvenl::::nt, and soil and rock behavior. A fourth category included important miscellaneous efrorts tl'12t did not fit the areas mentioned. The report vlill be useful to re~earchers and praGtitior,c:;rs in geotechnology. --------:"--; /~ /1 I~t(./l- /-~~:r\ .. T. Paul Teng (j Director, Office of Infrastructure Research, Development. and Technologv NOTiCE This document is disseminated under the sponsorship of the Department of Transportation in the interest of information exchange. The United States G~)\fernm8nt assumes no liahillty for its contt?!nts or use thereof. Thir. report dor~s not constiil)tl":: a standard, specification, or regu!p,tion. The; United States Government does not endorse products or n18;1ufaGturers, Traderrlc,rks or nianufacturers' narl1es appear in thi;-, report only bec:8'I)Se they arc considered essential to tile object of the document. Technical Report Documentation Page 1. Report No. 2. Government Accession No. 3. Recipient's Catalog No. FHWA-RD-98-139 4. Title and Subtitle 5. Report Date A Quarter Century of Geotechnical Research February 1999 6. Performing Organization Code ). -
Influence of Peripheral Velocity on Measurements of Undrained Shear Strength for an Artificial Soil
Estimated Time to Failure, t (minutes) f 104 1000 100 10 1 0.1 2.0 u0 /s Rate Effect Model u β = 0.10 β s /s = (v /v ) u u0 p p0 1.5 0.05 1.0 Typical 0.5 Typical Range of Range of Interest for Wave Interest for Reference Rate & Storm Loading Earthquake ~ 3.4 mm/min Loading Norm. Undrained Shear Strength, s Strength, Shear Undrained Norm. 0.0 0.0100 0.100 1.00 10.0 100 103 Peripheral Velocity, v (mm/min) p Symbol Reference Soil This Work Bentonite-Kaolinite Mix Perlow & Richards, 1977 San Diego Clay Wiesel, 1973 Ska Edeby Tortensson, 1977 Backebol Tortensson, 1977 Askim Schapery & Dunlap, 1978 Gulf Mexico INFLUENCE OF PERIPHERAL VELOCITY ON UNDRAINED SHEAR STRENGTH AND DEFORMABILITY CHARACTERISTICS OF A BENTONITE- KAOLINITE MIXTURE by Giovanna Biscontin and Juan M. Pestana Geotechnical Engineering Report No UCB/GT/99-19 November 1999 Revised in December 2000 GEOTECHNICAL ENGINEERING. Department of Civil and Environmental Engineering University of California, Berkeley ii TABLE OF CONTENTS LIST OF TABLES......................................................................................................................................................II LIST OF FIGURES....................................................................................................................................................II INFLUENCE OF PERIPHERAL VELOCITY ON MEASUREMENTS OF UNDRAINED SHEAR STRENGTH FOR AN ARTIFICIAL SOIL..............................................................................................................1 ABSTRACT .............................................................................................................................................................1 -
Kania, J.K., Sorensen, K.K., and Fellenius, B.H., 2020. Analysis of a Static Loading Test on an Instrumented CFA Pile in Silt and Sand
Kania, J.K., Sorensen, K.K., and Fellenius, B.H., 2020. Analysis of a static loading test on an instrumented CFA pile in silt and sand. International Journal of Geoengineering Case Histories, 5(3) 170-181. doi: 10.4417/IJGCH-05-03-03 Analysis of a Static Loading Test on an Instrumented Cased CFA Pile in Silt and Sand Jakub G. Kania, Ph.D., cp test a/s / Aarhus University, Vejle/Aarhus, Denmark; email: [email protected] Kenny Kataoka Sørensen, Associate Professor, Department of Engineering, Aarhus University, Aarhus, Denmark; email: [email protected] Bengt H. Fellenius, Consulting Engineer, Sidney, BC, Canada, V8L 2B9; email: [email protected] ABSTRACT: A static loading test was performed on an instrumented 630 mm diameter, 12.5 m long, cased continuous flight auger (CFA) pile. The soil at the site consisted of a 4.0 m thick layer of loose sandy and silty fill layer underlain by a 1.6 m thick layer of dense silty sand and sand followed by dense sand to depth below the pile toe level. The instrumentation comprised vibrating wire strain gages at 1.0, 5.8, 9.4, and 12.0 m depth. The pile stiffness (EA) was determined by the secant and tangent methods and used in back-calculating the distributions of axial load in the pile. A t-z/q-z simulation of the test was fitted to the load-movement distributions of the pile head, gage levels, and pile toe. The load-movement response for the shaft resistance was strain-hardening. The records indicated presence of residual force. -
Field Description of Soil and Rock
FIELD DESCRIPTION OF SOIL AND ROCK GUIDELINE FOR THE FIELD CLASSIFICATION AND DESCRIPTION OF SOIL AND ROCK FOR ENGINEERING PURPOSES NZ GEOTECHNICAL SOCIETY INC December 2005 NZ GEOTECHNICAL SOCIETY INC The New Zealand Geotechnical Society (NZGS) is Full members of the NZGS are affiliated to at least one the affiliated organisation in New Zealand of the of the following Societies: International Societies representing practitioners in Soil • International Society for Rock Mechanics (ISRM) Mechanics, Rock Mechanics and Engineering Geology. • International Society for Soil Mechanics and NZGS is also an affiliated Society of the Institution of Geotechnical Engineering (ISSMGE) Professional Engineers New Zealand (IPENZ). • International Society for Engineering Geology and The aims of the Society are: the Environment (IAEG). • To advance the study and application of soil Members are engineers, scientists, technicians, mechanics, rock mechanics and engineering geology contractors, students and others interested in the practice among engineers and scientists and application of soil mechanics, rock mechanics and • To advance the practice and application of these engineering geology. Membership details are given on disciplines in engineering the NZGS website www.nzgeotechsoc.org.nz. • To implement the statutes of the respective International Societies in so far as they are applicable in New Zealand. COVER PHOTOGRAPHS: MAIN: Incised bank, Waiwhakaiho River, New Plymouth (courtesy Sian France) UPPER LEFT: Basalt rock face, Mountain Road, Auckland (courtesy -
Old Rectory Court High Street Burwash East Sussex Geotechnical
Old Rectory Court High Street Burwash East Sussex Geotechnical Assessment Report Report No. R17-12510 November 2017 Report prepared for the benefit of: Ink Development Company Ltd Grosvenor House 125 High Street Croydon Surrey CR0 9XP Document Control Report Section Prepared By Approved By Factual Section Ryan Jones Stephen Atkinson BSc (Hons) FGS BSc FGS Geotechnical Assessment Stephen Atkinson Rebecca Webb BSc FGS BSc FGS Revisions Revision No. Revision Date Notes Limitations This report was prepared specifically for the Client’s project and may not be appropriate to alternative schemes. The copyright for the report and licence for its use shall remain vested in Ashdown Site Investigation Limited (the Company) who disclaim all responsibility or liability (whether at common law or under the express or implied terms of the Contract between the Company and the Client) for any loss or damage of whatever nature in the event that this report is relied on by a third party, or is issued in circumstances or for projects for which it was not originally commissioned. R17-12510 EXECUTIVE SUMMARY The following presents a summary of the main findings of the ground investigation. It is emphasised that no reliance should be placed on any individual point until the whole of the report has been read as other sections of the report may put into context the information contained herein. The proposed development is understood to comprise of the demolition of the existing property, ‘Old Rectory Court’, and the construction of four new 2-bedroom dwellings and a new apartment building comprising fifteen 1-bedroom flats, along with associated garden areas, soft landscaping, car parking and vehicular access. -
ASUC Underpinning and Mini Piling Guidelines
ASUC | Guidelines on Safe and ecient UNDERPINNING AND MINI PILING OPERATIONS 3rd Edition ASUC Underpinning & Subsidence Repair Techniques | Engineered Foundation Solutions | Retro Fit Basement Construction Kingsley House, Ganders Business Park , Kingsley, Bordon, Hampshire GU35 9LU Tel: +44 (0)1420 471613 www.asuc.org.uk ASUC ASUC is an independent trade association formed by a number of leading contractors to promote professional and technical competence within the underpinning industry. Members offer a comprehensive range of specialist domestic services in: underpinning and subsidence repair techniques, engineered foundation solutions and retrofit basement construction. Any contractor wishing to join ASUC must first undergo a technical, health & safety, insurance and financial audit and make a commitment to prescribed safety procedures. It publishes a number of useful documents on underpinning and related activities and a comprehensive directory of members all of which are freely available to download via the website. ASUC members offer 10 or 12 year, depending on the nature of the works, insurance backed latent defects guarantees. Main authors Rob Withers - ASUC Executive Director David Kitching – Stress UK Ltd Lewis O’Connor – Abbey Pynford Group Industry comments from Hurst Pierce and Malcolm Abbey Pynford Group Morcon Foundations Photographs and Diagrams Abbey Pynford Group Falcon Structural Repairs Ltd Force Foundations Ltd t/a Basement Force Kixx Ltd – Mike Darby Larsen Foundations Ltd Neil Foundations Ltd Patterson Construction -
Reference Test Procedure for Field Vane Tests
1 Reference test procedure for field vane tests Danish Geotechnical Society - Field Committee Revision 3 August 1999 (English translation September 2009 - In case of disagreement the Danish version applies) 1. INTRODUCTION This reference test procedure provides a guideline for execution of field vane tests in cohesive soils. A shear vane test determines the vane strength of the soil. Normally this indicates the undrained shear strength of the soil. 2. EQUIPMENT 2.1 General The vane probe consists of two blades mounted perpendicular to each other at the end of a cylindrical rod. The blades have rounded corners and sharpened edges. Just above the blades a ring is inserted to reduce the friction between the rod and the penetrated soil. Traditionally the torque on the rod is measured by a spring scale or a dial indicator spring connecting a fixed arm with the handle. It is this type of equipment that is described below. Alternatively, the measurement can be performed by a torque wrench. If a torque wrench is applied, it shall be verified that the level of accuracy and quality assurance complies with the description for the traditional equipment. Rod Friction reducer Cross-section A-A Direction of rotation Fig. 1. The vane probe. The figure shows a hand vane A A “deep vane” equipment is applied in the bottom of a borehole in connection with the execution of a geotechnical investigation boring. The “hand vane” equipment has a low weight and is designed for shallow tests. Different dimensions of the blades are used for measurements in cohesive soils with different strengths. -
Effect of Cementation on Cone Resistance in Sands: a Calibration Chamber Study
Louisiana State University LSU Digital Commons LSU Historical Dissertations and Theses Graduate School 1993 Effect of Cementation on Cone Resistance in Sands: A Calibration Chamber Study. Anand Jagadeesh Puppala Louisiana State University and Agricultural & Mechanical College Follow this and additional works at: https://digitalcommons.lsu.edu/gradschool_disstheses Recommended Citation Puppala, Anand Jagadeesh, "Effect of Cementation on Cone Resistance in Sands: A Calibration Chamber Study." (1993). LSU Historical Dissertations and Theses. 5687. https://digitalcommons.lsu.edu/gradschool_disstheses/5687 This Dissertation is brought to you for free and open access by the Graduate School at LSU Digital Commons. It has been accepted for inclusion in LSU Historical Dissertations and Theses by an authorized administrator of LSU Digital Commons. For more information, please contact [email protected]. INFORMATION TO USERS This manuscript has been reproduced from the microfilm master. UMI films the text directly from the original or copy submitted. Thus, some thesis and dissertation copies are in typewriter face, while others may be from any type of computer printer. The quality of this reproduction is dependent upon the quality of the copy submitted. Broken or indistinct print, colored or poor quality illustrations and photographs, print bleedthrough, substandard margins, and improper alignment can adversely affect reproduction. In the unlikely event that the author did not send UMI a complete manuscript and there are missing pages, these will be noted. Also, if unauthorized copyright material had to be removed, a note will indicate the deletion. Oversize materials (e.g., maps, drawings, charts) are reproduced by sectioning the original, begimiing at the upper left-hand corner and continuing firom left to right in equal sections with small overlaps. -
Downloaded from the Online Library of the International Society for Soil Mechanics and Geotechnical Engineering (ISSMGE)
INTERNATIONAL SOCIETY FOR SOIL MECHANICS AND GEOTECHNICAL ENGINEERING This paper was downloaded from the Online Library of the International Society for Soil Mechanics and Geotechnical Engineering (ISSMGE). The library is available here: https://www.issmge.org/publications/online-library This is an open-access database that archives thousands of papers published under the Auspices of the ISSMGE and maintained by the Innovation and Development Committee of ISSMGE. Proceedings of the XVII ECSMGE-2019 Geotechnical Engineering foundation of the future ISBN 978-9935-9436-1-3 © The authors and IGS: All rights reserved, 2019 doi: 10.32075/17ECSMGE-2019-0732 Design of bored piles in Denmark – a historical perspective Conception de pieux forés au Danemark - une perspective historique J. Knudsen COWI A/S and Aarhus University, Aarhus, Denmark K.K. Sørensen Aarhus University, Aarhus, Denmark J. S. Steenfelt, H. Trankjær COWI A/S, Kongens Lyngby / Aarhus, Denmark ABSTRACT: According to the Danish National Annex to Eurocode 7, part 1 (2015), Annex L the shaft resistance for a bored cast-in-place pile is limited to 30 per cent of the shaft resistance of the corresponding driven pile and the design toe resistance is limited to 1000 kPa unless recognised documentation allowing a larger bearing resistance is available. This principle has been enforced in Denmark (Code-requirement introduced in the Code of Practise for Foundations in 1977, with further adjustments regarding allowable toe resistance in 1984 and 1998) allegedly due to problems encountered in one or two un-documented case histories. This paper presents the historical aspects of the code-requirement as well as a case study on the results of recent full-scale static compression pile load tests on two bored piles performed on clay till in Nyborg, Denmark. -
Characterization of Glyben for Seismic Applications
Geotechnical Testing Journal, Vol. 31, No. 1 Paper ID GTJ100552 Available online at: www.astm.org M. H. T. Rayhani1 and M. H. El Naggar1 Characterization of Glyben for Seismic Applications ABSTRACT: Glyben is artificial clay that is prepared by mixing sodium bentonite powder and glycerin. It is used for laboratory tests and scale modeling for geotechnical applications. The mechanical properties of glyben depend on the bentonite and glycerin mix proportions. The shear strength, dynamic shear modulus, damping ratio, and Poisson’s ratio were evaluated for glyben samples prepared with different glycerin/bentonite ratios. Vane shear tests, T-bartests, hammer tests, and resonant column tests were conducted on glyben specimens and the shear strength and dynamic properties were evaluated considering a wide range of strain values and confining pressure. The measured glyben properties were compared with properties of natural cohesive soils to verify the range of applicability of glyben as a test bed material. It was found that glyben has the same range of strength and dynamic properties as soft to medium stiff clay. The trend of variation of the shear modulus and damping ratios of glyben is similar to that of natural clays. It is noted, however, that the damping ratio of glyben is higher than that of natural clays for shear strains below 0.01%. It was concluded that glyben can reasonably model the nonlinear behavior of natural soil under strong dynamic excitation. KEYWORDS: glyben clay, shear strength, shear modulus, damping ratio, resonant column Introduction constant shear strength behavior. Kenny and Andrawes (1997) car- ried out undrained triaxial and vane shear tests on glyben and dem- The measurement of dynamic soil properties is a crucial task in the onstrated that it behaves generally as a u =0 material under quick analysis of geotechnical earthquake engineering problems. -
Nipigon River Landslide, Ontario, Canada
Nipigon River Landslide, Ontario, Canada A. Abdelaziz, S. Besner, R. Boger, B. Fu, J. Deng, and A. Farina Presenter: Jian Deng, Ph.D, P.Eng Centre of Excellence for Sustainable Mining and Exploration, Lakehead University, Canada Contents • Introduction • Causes of landslide • Risk of further slide (Recommend measures to reduce future risks) • Stabilization measures • Conclusions and recommendations Nipigon River • Nipigon River is located on North shore of Lake Superior, Great Lakes in North America • Soils along the Nipigon River are products of glaciolacustrine and delta deposits consisting of sands and silts • Frequent small failures of natural and man-made slopes Outside sections of the river meanders Nipigon River Landslide 6 A massive landslide occurred on April 23, 1990 Involved 300,000 cubic meters of soil Extended almost 350 m inshore with a maximum width of approximately 290 m Caused soil to be pushed into the Nipigon River 300 m upstream and about the same distance downstream. The islands, formed by the soils pushed into the river, redirected the current and caused subsequent erosion on the west bank and further landslides on the south. A section of Trans Canada Pipeline was left unsupported Difficulties for water supply for Nipigon and Red Rock Adverse Economic and Environmental effects (fish habitat, etc.) Affected Parties • Ministry of Natural Resources • Ontario Hydro • TransCanada Pipelines • Bell Canada • Canadian National Railway • City of Nipigon • Town of Red Rock Water • Red Rock Indian Band Intakes • Domtar -
Field Testing Methods for Engineering Geological Investigations F. G. Bell L
Downloaded from http://egsp.lyellcollection.org/ by guest on September 29, 2021 Field testing methods for engineering geological investigations F. G. Bell l, J. C. Cripps 2 & M. G. Culshaw 3 1 Department of Geology and Applied Geology, University of Natal, King George V Avenue, Durban 4001, South Africa 2 Department of Geology, University of Sheffield, Beaumont Building, Brookhill, Sheffield, $3 7HF, UK Engineering Geology Research Group, British Geological Survey, Keywortb, Nottingham, NG12 5GG, UK Abstract. This paper discusses some of the more commonly used field testing methods used to determine various geotechnical parameters needed to classify soils and rocks in engineering terms and to provide engineering design values. The methods of performing, and the application of, various penetration, shear strength, plate loading, pressuremeter and dilatometer and permeablity tests are described. The use of geophysical methods to obtain, indirectly, mechanical parameter values is also discussed. Field testing and, to a lesser extent, geophysical frequently for the determination of the values of surveying are major sources of both qualititive and engineering design parameters. The techniques de- quantitative data relating to the ground conditions. In scribed include penetration tests, shear strength tests, spite of the fact that in most cases field testing is more loading tests, pressuremeter tests and permeability expensive to carry out than sampling and laboratory tests as well as geophysical methods. The discussion testing, it forms an