US 2016/0183346A1 Hsing Et Al
Total Page:16
File Type:pdf, Size:1020Kb
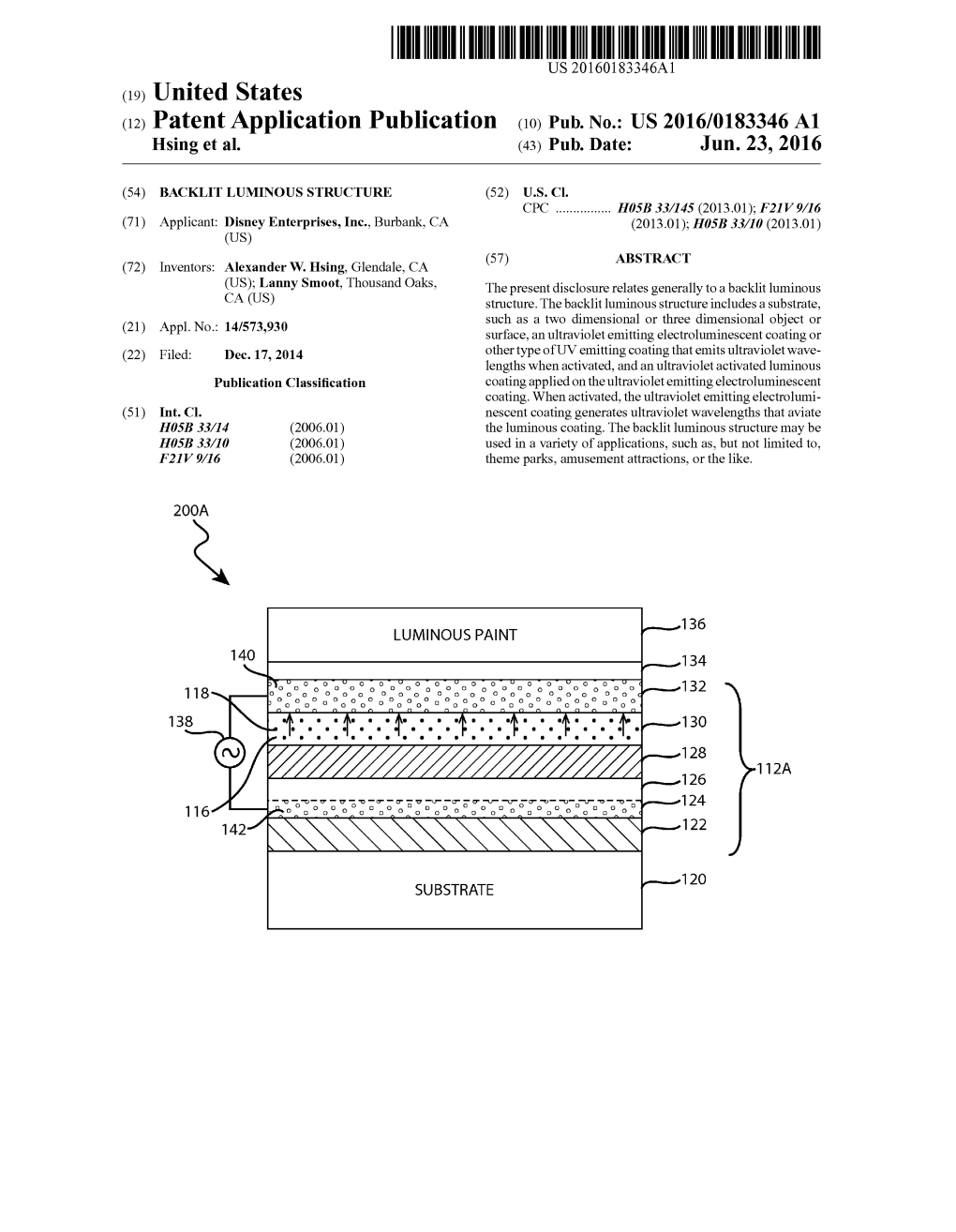
Load more
Recommended publications
-
Women's History Magazine Broadly As Possible
Women’s History Magazine Issue 48, AUTUMN 2004 Issn 1476-6760 Themed Issue: Science, Technology and Education Maria Rentetzi on The Case of the Radium Dial Painters Claire Jones on Grace Chisholm Young in Turn-of-Nineteenth-Century Germany Joyce Goodman on Technical Education, Female Emigration and Nation Building Hull 2004 Conference Report Launch of new WHN Book Prize Clare Evans Prize — Report on 2004 Award and Hypatia Announcement of of Alexandria 2005 Competition c. 370 - 415 Conference 2005 — Mathematician philosopher, Call for Papers teacher and inventor of mechanical devices. th 14 Conference of the Women’s History Network Women, Art and Culture: Historical Perspectives September 2nd- 4th 2005, Southampton Southampton Institute, Sir James Matthews Conference Centre, Southampton, Hants. Papers are welcomed on the following themes: Women and the visual arts; painting, sculpture, architecture, and the decorative arts. Women and the Arts and Crafts Movement/Home Decorating. Women and the performing arts. Women and the literary arts. Women as art objects/images of women. Women as mediators of culture. Women as collectors and benefactors. Plenary Speakers: Frances Borzello on 'Women Artists: Self Portraits' Marina Vaizey on '20th Century Women Collectors' Speakers, papers and a provisional programme will be posted at www.womenshistorynetwork.org as soon as they become available. Papers will be considered for special issues of: Women’s History Magazine & Women’s History Review. Abstracts of 200-300 words should be sent by 30/03/05 to: Dr Anne Anderson, FMAS, Southampton Institute, Southampton, S014 ORF. [email protected] Administrator: Dr. Joyce A. Walker (Women’s History Network) , Department of History, University of Aberdeen, Crombie Annexe, Meston Walk, Old Aberdeen, AB24 3FX E-mail: [email protected] The arrival of this Autumn's Women's History Magazine broadly as possible. -
Health & Hazardous Waste
HEALTH and HAZARDOUS WASTE A Practitioner's Guide to Patients' Environmental Exposures Volume 1, Number 3 Spring 1996 IONIZING RADIATION and Your Patient Ionizing radiation is energy that can damage tissue by disrupting either the cell or the molecules used or produced by the cell, such as DNA. Ionizing radiation can be produced by unstable radioactive elements which decay in order to reach a stable, non-radioactive molecular configuration. This occurs through the emission of radioactive particles or rays. Particles include alpha and beta radiation, and rays include gamma radiation and x-rays. When these particles or rays are emitted, the remaining product is another element which may also be radioactive. This daughter product, or progeny, will in turn emit particles or rays until ultimately a non-radioactive element is formed. Units of radiation measurement include the roentgen, gray, rad, curie, and becquerel, and their milli- and micro- derivatives. Radiation dose in humans is measured in rems or sieverts. Although sievert is the international unit, rem is the term more frequently used in the U.S., and will be used in this article. Rems and sieverts take into account both the quantity and the form of radiation in dose measurements. continued on page 2 Focus on: Focus on: WELSBACH AND GENERAL GAS MANTLE U.S. RADIUM SITES High Street and Alden Street Camden and Gloucester City Orange, Essex County, NJ Camden County, NJ Other affected areas Other affected areas "Vicinity" properties located near the plant, consisting of The contaminated properties include two former factories, approximately 300 residential and light industrial approximately 23 residential properties, 7 commercial properties within 9 city blocks of the site; properties, and 9 open areas. -
Dealing with Radiation Hazards: the Luminous Dial Project at the Canada Science and Technology Museum
Dealing with Radiation Hazards: The Luminous Dial Project at the Canada Science and Technology Museum Sue Warren Journal of the Canadian Association for Conservation (J. CAC), Volume 35 © Canadian Association for Conservation, 2010 This article: © Canada Science and Technology Museum, 2010. Reproduced with the permission of the Canada Science and Technology Museum. J.CAC is a peer reviewed journal published annually by the Canadian Association for Conservation of Cultural Property (CAC), 207 Bank Street, Suite 419, Ottawa, ON K2P 2N2, Canada; Tel.: (613) 231-3977; Fax: (613) 231- 4406; E-mail: [email protected]; Web site: http://www.cac-accr.ca. The views expressed in this publication are those of the individual authors, and are not necessarily those of the editors or of CAC. Journal de l'Association canadienne pour la conservation et la restauration (J. ACCR), Volume 35 © l'Association canadienne pour la conservation et la restauration, 2010 Cet article : © Musée des sciences et de la technologie du Canada, 2010. Reproduit avec la permission du Musée des sciences et de la technologie du Canada. Le J.ACCR est un journal révisé par des pairs qui est publié annuellement par l'Association canadienne pour la conservation et la restauration des biens culturels (ACCR), 207, rue Bank, Ottawa (Ontario) K2P 2N2, Canada; Téléphone : (613) 231-3977 ; Télécopieur : (613) 231-4406; Adresse électronique : [email protected]; Site Web : http://www.cac-accr.ca. Les opinions exprimées dans la présente publication sont celles des auteurs et ne reflètent pas nécessairement celles de la rédaction ou de l'ACCR. 9 Dealing with Radiation Hazards: The Luminous Dial Project at the Canada Science and Technology Museum Sue Warren Canada Science and Technology Museum, 1867 St. -
Chapter 2 Incandescent Light Bulb
Lamp Contents 1 Lamp (electrical component) 1 1.1 Types ................................................. 1 1.2 Uses other than illumination ...................................... 2 1.3 Lamp circuit symbols ......................................... 2 1.4 See also ................................................ 2 1.5 References ............................................... 2 2 Incandescent light bulb 3 2.1 History ................................................. 3 2.1.1 Early pre-commercial research ................................ 4 2.1.2 Commercialization ...................................... 5 2.2 Tungsten bulbs ............................................. 6 2.3 Efficacy, efficiency, and environmental impact ............................ 8 2.3.1 Cost of lighting ........................................ 9 2.3.2 Measures to ban use ...................................... 9 2.3.3 Efforts to improve efficiency ................................. 9 2.4 Construction .............................................. 10 2.4.1 Gas fill ............................................ 10 2.5 Manufacturing ............................................. 11 2.6 Filament ................................................ 12 2.6.1 Coiled coil filament ...................................... 12 2.6.2 Reducing filament evaporation ................................ 12 2.6.3 Bulb blackening ........................................ 13 2.6.4 Halogen lamps ........................................ 13 2.6.5 Incandescent arc lamps .................................... 14 2.7 Electrical -
The Radium Dial Painters: Workers’ Rights, Scientific Est Ting, and the Fight for Humane Treatment Elizabeth Richter
Hamline University DigitalCommons@Hamline Departmental Honors Projects College of Liberal Arts Spring 2018 The Radium Dial Painters: Workers’ Rights, Scientific esT ting, and the Fight for Humane Treatment Elizabeth Richter Follow this and additional works at: https://digitalcommons.hamline.edu/dhp Part of the History Commons Recommended Citation Richter, Elizabeth, "The Radium Dial Painters: Workers’ Rights, Scientific eT sting, and the Fight for Humane Treatment" (2018). Departmental Honors Projects. 74. https://digitalcommons.hamline.edu/dhp/74 This Honors Project is brought to you for free and open access by the College of Liberal Arts at DigitalCommons@Hamline. It has been accepted for inclusion in Departmental Honors Projects by an authorized administrator of DigitalCommons@Hamline. For more information, please contact [email protected], [email protected]. The Radium Dial Painters: Workers’ Rights, Scientific Testing, and the Fight for Humane Treatment Elizabeth Richter An Honors Thesis Submitted for partial fulfillment of the requirements for graduation with honors in History from Hamline University April 28, 2018 Abstract From the early 1910s through the Great Depression, the dial painting industry provided opportune jobs for young female workers. Dial painting jobs did not require many skills but were well-paying professions. These careers attracted many young women and girls to work there. However, unknown to the painters at the time, the radium that they were using to paint the dial faces was slowly poisoning them and would later cause major health defects. Many of these women that did not die directly from the radium developed various forms of cancer and radium poisoning, which led to many lawsuits. -
Card 2019.Pdf
CONTENTS FOR CREATIVITY AND HOBBY - Glow paint Acmelight for Hand Made and decor 1 - Glow paint Acmelight for textiles 2 - Glow paint Acmelight for tourism 3 - Glow paint Acmelight for fishing 4 - Glow paint Acmelight for flowers 5 - Fluorescent paint for creativity 6 - Fluorescent paint for textiles 7 - Fluorescent aqua makeup 8 FOR INTERIOR WORK - Luminous decorative plaster Acmelight Antic 9 FOR FINISHING WORK - Luminous decorative grout AcmeLight Grout 10 - Luminous interior paint Acmelight Interior 11 - Luminous exterior paint Acmelight Facade 12 - Luminous paint for swimming pools Acmelight Pool 13 - Luminous paint for metal Acmelight Metal 14 - Luminous paint for your car Acmelight Metal 15 - Luminous paint for your bike Acmelight Metal 16 - Luminous paint for concrete surfaces Acmelight Concrete 17 - Luminous paint for wood Acmelight Wood 18 - Luminous paint for plastic Acmelight Plastic 19 FOR SOUVENIRS AND ADVERTISING - Luminous paint for flower Acmelight Flower 20 - Luminous paint for textiles Acmelight Textile 21 - Luminous paint for film oracal Acmelight Oracal 22 - Luminous paint for glass Acmelight Glass Classic 23 - Luminous paint for glass and ceramics AcmeLight Glass Original 24 SAFETY SYSTEM - Luminous paint for safety systems Acmelight FES 25 - Luminous paint for metal safety systems Acmelight FES Metal 26 - Luminous paint for road marking AcmeLight Road 27 - Glow in the dark film FES 28 - Photoluminescent reflective tape 29 - Glowing in the dark helmet 30 READY PRODUCT - Glowing photopaper AcmeLight 31 - Glowing natural -
NRPB- Xxxx a Review of Consumer Products Containing Radioactive Substances in the European Union
NRPB- xxxx A Review of Consumer Products Containing Radioactive Substances in the European Union J Shaw, J Dunderdale and R A Paynter NRPB Occupational Services Department © National Radiological Protection Board Approval: Occupational Services Department Publication: Hospital Lane Cookridge ISBN Leeds LS16 6RW This NRPB report reflects understanding and evaluation of the current scientific evidence as presented and referenced in this document. CONTENTS 1 GENERAL INFORMATION 5 1.1 Introduction 5 1.2 Definitions, objectives and scope 5 1.3 Description of consumer products 7 1.3.1 Ionisation chamber smoke detectors (ICSD) 7 1.3.2 Radioluminous products 7 1.3.3 Fluorescent lamp starters 8 1.3.4 Electronic devices 8 1.3.5 Anti-static devices 8 1.3.6 Lightning preventors 9 1.3.7 Thoriated incandescent gas mantles 9 1.3.8 Thoriated lenses 9 1.3.9 Thoriated tungsten welding electrodes 9 1.3.10 Glassware, tableware, jewellery and ceramic tiles incorporating uranium 9 1.3.11 Dental products incorporating uranium 9 1.3.12 Irradiated gemstones 10 1.3.13 Antique products 10 1.4 Potential exposure routes 11 1.4.1 Ionisation chamber smoke detectors (ICSD) 11 1.4.2 Radioluminous products 11 1.4.3 Fluorescent lamp starters and other electronic devices 13 1.4.4 Lightning preventors 13 1.4.5 Anti-static devices 13 1.4.6 Thoriated incandescent gas mantles 13 1.4.7 Thoriated lenses 14 1.4.8 Thoriated tungsten welding electrodes 14 1.4.9 Glassware, tableware, jewellery and ceramic tiles incorporating uranium 14 1.4.10 Dental products incorporating uranium -
THE AMERICAN JOURNAL of CANCER a Continuation of the Journal of Cancer Research
THE AMERICAN JOURNAL OF CANCER A Continuation of The Journal of Cancer Research -__ No. VOLUMEXV OCTOBER,1931 ~____ 4 ~~ THE OCCURRENCE OF MALIGNANCY IN RADIO- ACTIVE PERSONS A GENERALREVIEW OF DATAGATHERED IN THE STUDYOF THE RADIUMDIAL PAINTERS,WITH SPECIALREFERENCE TO THE OCCURRENCEOF OSTEOGENICSARCOMA AND THE INTER-RELATIONSHIPOF CERTAINBLOOD DISEASES HARRISON S. MARTLAND, M.D. (From the Department of Pathology of the Newark City Hospital and the Ogice of the Chiej Medical Examiner of Essex COU~~!J,Newark, N. J.) It is the purpose of this paper to call attention to certain data which the writer has accumulated in the study of the radium dial painters which may have an important bearing on future research in the etiology of cancer and of certain obscure blood diseases. OCCUPATIONALPOISONING IN MANUFACTUREOF LUMINOUSWATCH DIALS The etiology, the general and special symptomatology, the pathology, toxicology, and prognosis of this new occupational disease were described by Martland and his associates in 1925 and 1926 (l),and the whole subject of the New Jersey cases was later reviewed by him in 1929 (2). In addition, important papers by Hoffman (3), Castle and the Drinkers (4), Flinn (5), St. George, Gettler and Muller (6), Schlundt, Flinn and Barker (7), and Barker and Schlundt (S), covering the nature of the exposure, factory inspections, methods of detection of radio-activity during life, and treatment have about completed the description of this new industrial hazard. The report of the U. S. Department of Labor (9) and the special 2435 2436 HARRISON S. MARTLAND survey of the U. S. Public Health Service (lo), both of which cover not only the New Jersey cases but those occurring in other states, give an excellent resume of the industrial hazard and complete the disease as an occupational one. -
Uranium in the History of Medicine
ISSN: 2689-4246 DOI: 10.33552/CTCMS.2019.01.000505 Current Trends in Clinical & Medical Sciences Review Article Copyright © All rights are reserved by Andrew Hague Uranium in the History of Medicine Fathi Habashi* Department of Mining, Laval University, Canada *Corresponding author: : Fathi Habashi, Department of Mining, Metallurgical and Materials Received Date: May 20 , 2019 Engineering, Laval University, Quebec City, Canada. Published Date: June 12, 2019 Abstract Joachimsthal in Saxony was an important silver mining district since the Middle Ages when around the 1770s production started to decrease and the mining town was about to become a ghost town. It was at that time that Martin Heinrich Klaproth (1743-1817) a pharmacist in Berlin who became later professor of chemistry at the Royal Mining Academy, discovered that the black mineral in the ore can be used to give glass a brilliant This discovery coincided with the discovery in 1781 of a new planet in the solar system by his compatriot William Herschel who had immigrated toyellow England color in with 1757 green and fluorescencecalled the planet when Uranus. added Henceto the moltenKlaproth batch. named He thewas new also metal convinced “uranium” that this to honormineral his must compatriot. have contained In 1789 a he new was metal. able to isolate a black heavy solid from the ore which he thought it to be the new metal. Since that time uranium started to play a dominant role in the history of medicine. Introduction when few years earlier silver was discovered. Further settlings in the neighborhood, Freiberg (1168) and Schneeberg (1446) are also known by their silver discoveries. -
PRESERVATION SNAPSHOT Radium Girls
PRESERVATION SNAPSHOT This monthly feature highlights National Register listings and eligible properties, tax act projects & compliance review success stories, as well as outstanding local efforts in New Jersey’s history. Radium Girls The Story of US Radium’s Superfund Site Orange, New Jersey US Radium Dial Painters, c. 1922 , Paint Application Building, 2nd floor Credit: Argonne National Laboratory At peak production during World War I, as many as 300 young women worked as ‘dial painters’ at their neighborhood US Radium Corporation plant in Orange, New Jersey. Seated at long benches on the second floor of the concrete Paint Application building with its large windows and skylights, they meticulously wielded minute brushes painting luminous paint on the numerals and hands of wrist watches and airplane cockpit dials. Within ten years, many would be dead. US Radium Corporation produced luminous paints and other radium products for military and medical purposes in Orange, NJ from 1917-1926. However, they operated with a dual set of health & safety standards. Their chemists and scientists were provided protective measures against exposure to the radioactive radium. The dial painters had no such measures in place. Nearly every surface inside their factory buildings sparkled with radioluminescence. Their supervisors told the dial painters the flavorless paint was perfectly safe, and encouraged them to “point” their camel hair brushes with their lips to keep a fine point. 1 Radium It was 1896 when Henri Becquerel discovered radium as a new element – Ra. Marie Curie and her husband, Pierre, jointly won the Nobel Prize with Becquerel in 1903 for their work on radioactivity. -
The Periodic Table of the Elements, in Pictures and Words
Alkali Earth Metals are reactive and readily form compounds but are not found free in nature. Their oxides are called alkali earths. In pure form, they are soft and somewhat brittle metals. elements.wlonk.com Solid The color of the symbol is Solid The color of the symbol is the color of the element in the color of the element in The Periodic Table Liquid its most common pure form. Liquid its most common pure form. Examples metallic solid Examples metallic solid Gas red liquid Gas red liquid of the Elements, at room colorless gas at room colorless gas in Pictures and Words temperature temperature Human Body Human Body H top ten elements by weight top ten elements by weight Noble Gases Alkali Earth Metals Nonmetals Alkali Metals Earth's Crust Earth's Crust Halogens Metalloids top eight elements by weight top eight elements by weight Magnetic Magnetic Transition Metals Poor Metals ferromagnetic at room temperature ferromagnetic at room temperature Noble Metals Noble Metals Superheavy Elements corrosion-resistant corrosion-resistant Radioactive Radioactive Rare Earth Metals all isotopes are radioactive all isotopes are radioactive Actinide Metals Only Traces Found in Nature Only Traces Found in Nature less than a millionth percent of earth's crust less than a millionth percent of earth's crust © 2005–2016 Keith Enevoldsen Never Found in Nature Never Found in Nature Creative Commons Attribution-ShareAlike 4.0 only made by people only made by people International License elements.wlonk.com elements.wlonk.com elements.wlonk.com Atoms Nucleus of Particles Solid The color of the symbol is Solid The color of the symbol is protons and +1 Proton the color of the element in the color of the element in neutrons its most common pure form. -
United States Patent Office Patented Ray 8, 1962 1
3,033,797 United States Patent Office Patented Ray 8, 1962 1. 2 100 grams of phosphor dispersed uniformly throughout 3,033,797 100 grams of tritiated plastic, the phosphor and plastic SELF-ILUMNOUS PANTS having the following physical characteristics: Felix R, De Leo, Needham, and Edward Shapiro, New toa, Mass., assignors, by mesae assiganents, to Leini (1) Density of plastic----------- 1.25 grams/cm.. nous Products. Corp., Boston, Mass, a corporation of (2) Density of phosphor--------- 4.00 grams/cm.3. Massachusetts (3) Volume of plastic----------- 100/125s 80 cm3. No Drawing. Fied Apr. 19, 1957, Ser. No. 653,733 (4) Volume of phosphor-------- 100/4.0=25 cm.. 3 Claims. Ci. 252-30.1) (5) Volume of paint------------. 105 cm.. This invention relates to a self-luminous paint and O The linear dimension of a cube having a volume of more particularly to a self-luminous paint comprising the 105 cm.3 is found to be 4.7 cm. radioactive isotope tritium. Consider now two cases, A and B. Heretofore self-luminous paints have been made using Case A: as the exciting agent a compound of radium. Generally Average diameter of phosphor particles is 1 micron the radium compound is in intimate admixture with the 5 (.0001 cm.). phosphor crystals and is not an integral part of the paint Volume of a single particle is 5.2x108 cm.. vehicle. Unfortunately radium is a particularly danger Weight of a single particle is 2.1X101 grams. ous form of radioactive material since when ingested by Number of phosphor particles is the body, it has a tendency to lodge in the bony struc 100/2.1.x10-12-4.8x1013 ture with its radiations causing serious damage to Sur rounding tissue.