Acnation St03 PRODUCT N 225 Patent Application Publication Aug
Total Page:16
File Type:pdf, Size:1020Kb
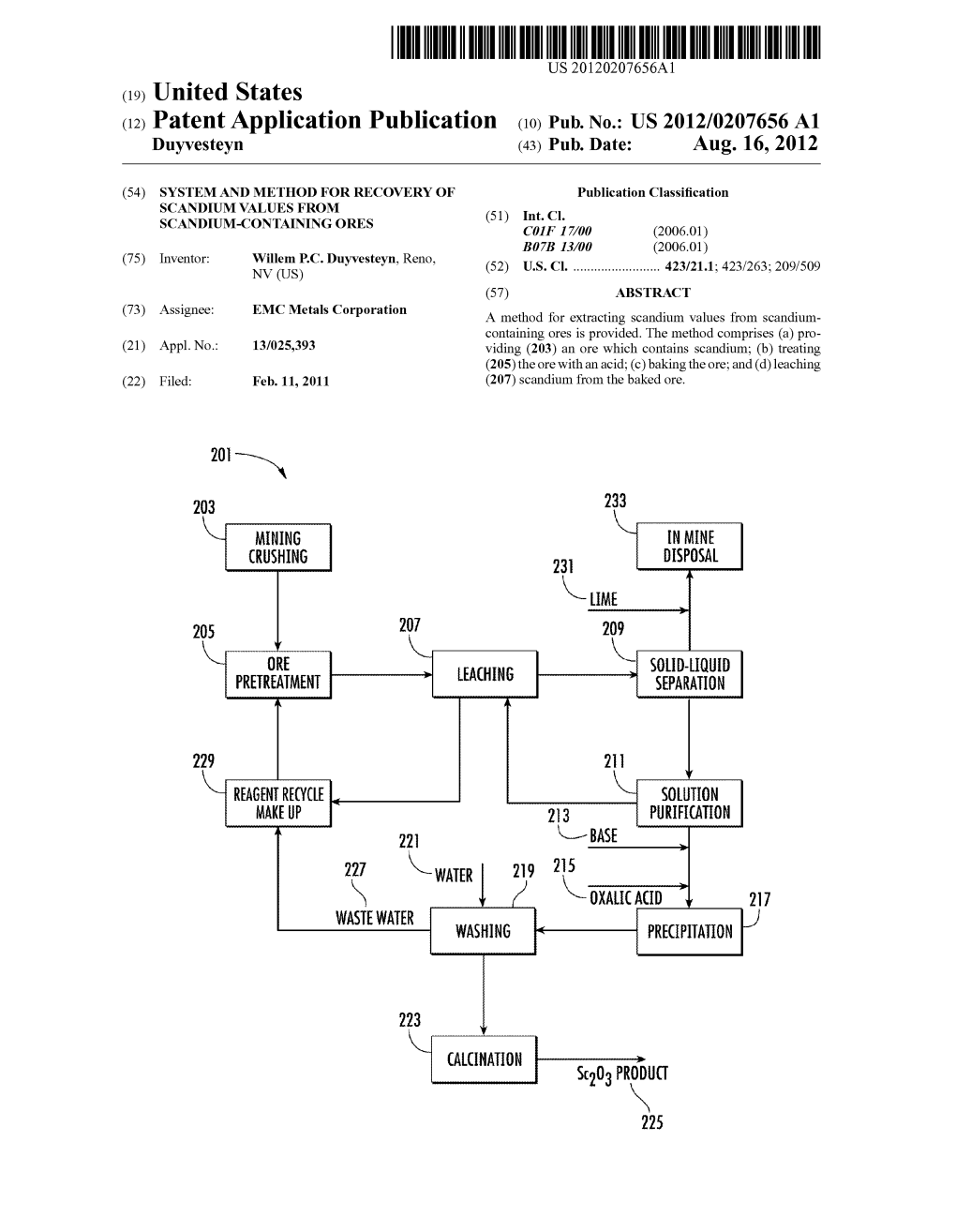
Load more
Recommended publications
-
Material Safety Data Sheet
LTS Research Laboratories, Inc. Safety Data Sheet Samarium fluoride ––––––––––––––––––––––––––––––––––––––––––––––––––––––––––––––––––––––––––––––––––––––––––––– 1. Product and Company Identification ––––––––––––––––––––––––––––––––––––––––––––––––––––––––––––––––––––––––––––––––––––––––––––– Trade Name: Samarium fluoride Chemical Formula: SmF3 Recommended Use: Scientific research and development Manufacturer/Supplier: LTS Research Laboratories, Inc. Street: 37 Ramland Road City: Orangeburg State: New York Zip Code: 10962 Country: USA Tel #: 855-587-2436 / 855-lts-chem 24-Hour Emergency Contact: 800-424-9300 (US & Canada) +1-703-527-3887 (International) ––––––––––––––––––––––––––––––––––––––––––––––––––––––––––––––––––––––––––––––––––––––––––––– 2. Hazards Identification ––––––––––––––––––––––––––––––––––––––––––––––––––––––––––––––––––––––––––––––––––––––––––––– Signal Word: Danger Hazard Statements: H302+H312: Harmful if swallowed or in contact with skin H331: Toxic if inhaled H315 Causes skin irritation H319 Causes serious eye irritation H335: May cause respiratory irritation Precautionary Statements: P261 Avoid breathing dust/fume/vapor P280: Wear protective gloves/protective clothing/eye protection/face protection P305+P351+P338: IF IN EYES: Rinse cautiously with water for several minutes. Remove contact lenses if present and easy to do – continue rinsing P304+P340: IF INHALED: Remove victim to fresh air and keep at rest in a position comfortable for breathing P405: Store locked up P501: Dispose of contents/container in accordance -
Wi Wuhwinwinwnwnh 136 047 Ths the E’Reparateqn Ame? Frgejeretes Of
WI WUHWINWINWNWNH 136 047 THS THE E’REPARATEQN AME? FRGEJERETES OF SOME SCANE‘JEUM CGfiAPQUflQS Thués far fire flowed; cf ML D. MICHEGAR SKATE CGLLEGE Road Fan‘s? Eéfiey W54? ', A" V «I V uni-1 numb-.- a:-—....-< . This is to certify that the thesis entitled The Preparation and Properties of Some Scandium Compounds presented bg heed Farrar Riley has been accepted towards fulfillment of the requirements for _P_hs_21_ degree in W Major prof ssor [7)3te Agril 22 , 1251+ LIBRARY Michigan State University PIACE IN RETURN BOX to remove this checkout from your record. TO AVOID FINES return on or before date due. MAY BE RECALLED with earlier due date if requested. DATE DUE DATE DUE DATE DUE 6/0I chlFIC/DateDue.p6&p.15 THE PREPARATION AND PROPERTIES OF SOME SCANDIUM COMPOUNDS BY REED FARRAR RILEY A THESIS Submitted to the School of Graduate Studies of Michigan State College of Agriculture and Applied Science in partial fulfillment of the requirements for the degree of DOCTOR OF PHILOSOPHY Department of Chemistry 1954 ACKNOWLEDGMENT The author wishes to express his gratitude to Professor L. L. Quill, for his considerate and able guidance of this work, and to Marjorie Riley for her patience and aid. ******* ***** ##1‘ * vr Lx I \-I I_\ 4—\ \_I \.I TABLE OF CONTENTS I. Introduction ............................. 1 II. Historical .............................. 2. III. Experimental ........ ................... 5 A. Oxalates ............................... 6 B. Fluorides ............................. 25 C. Trichloroacetates, Acetates and Carbonates .................... 35 Oxides, Hydroxides and Sulfates.. ....... 41 Polarographic Studies of Solutions Containing Scandium Salts ....... 48 IV. Summary ............................... 59 V. Bibliography ........................... 61 I. Introduction Since the discovery of scandium in the latter portion of the nineteenth century, work on this element has been both sporadic and limited, although, according to V. -
0.4 K, Losin-Ka Their A/VOAWAYS
Aug. 25, 1964 J. D. MOORE ETA 3,146,063 PROCESS FOR SEPARATING SCANDIUM FROM, MIXTURES CONTAINING SCANDIUM AND THORIUM WALUES Filed Jan. 3, 1961. "RECOVERY OF MINERAL VALUES." Acidified leoch Orgonic K OH Liquor Solvent (II) (14) EXTRACTION METATHESIS -Roffinole . (5) to Woste FILTER - Filtrote to Wostel (2) O LOOded HMO -- HC Ear UOs Loaded S-se -STRIPPING HCl to (16) Uronium Production KOs. ODATE PRECIPITATION NHF, HF -- (3) (7) X Thorium Precipitate SCANDUM-THORIUM. FTER 8& PRECIPITATION 4Th (OKIOI8HO (18) AqueousFluoride Solvent RecyRecycle his Neutralization Solution N - (3a) Sc - Th (19) FLTERFILTER Precipitate- FILTER Filtrate to Waste NHs Fitroe HC s (3b) (2O) NEUTRALIZATION HCOaaa-2?o (2) FLTER filtrate to Waste (3.c) - FILTER Titoniumis (22) Precipitote CACNE - HF lsco ar HsO. Sces INVENTORS, JAMES D. MOORE 8 A76 f By NORMAN N. SCHIFF 0.4 k, losin-ka their a/VOAWAYS - 3,146,063 United States Patent Office Patented Aug. 25, 1964 2 (NHF.HF) to precipitate and remove the thorium so 3,146,063 as to permit recycling of the organic solvent to the first PROCESS FOR SEPARAiNG SCANDUM FROM extraction operation previously described. Other mineral MIXTURES CONTAINING SCANDUM AND THORUM WALUES acid solutions of a fluoride salt may be used with the James D. Moore and Norman N. Schiff, Salt Lake City, proper amount of free fluoride. The insoluble thorium Utah, assignors to Vitro Corporation of America, New fluoride is removed by filtration while the soluble titani York, N.Y. um ion remains in solution. Filed Jan. 3, 1961, Ser. No. 80,260 According to the present invention, it has been dis 4 Claims. -
Scandium(III) Fluoride Safety Data Sheet M021201 According to Federal Register / Vol
Scandium(III) fluoride Safety Data Sheet M021201 according to Federal Register / Vol. 77, No. 58 / Monday, March 26, 2012 / Rules and Regulations Date of issue: 06/19/2018 Version: 1.0 SECTION 1: Identification 1.1. Identification Product form : Substance Substance name : Scandium(III) fluoride CAS No : 13709-47-2 Product code : M021-2-01 Formula : F3Sc Synonyms : Scandium trifluoride / Scandium fluoride Other means of identification : MFCD00016325 1.2. Relevant identified uses of the substance or mixture and uses advised against Use of the substance/mixture : Laboratory chemicals Manufacture of substances Scientific research and development 1.3. Details of the supplier of the safety data sheet SynQuest Laboratories, Inc. P.O. Box 309 Alachua, FL 32615 - United States of America T (386) 462-0788 - F (386) 462-7097 [email protected] - www.synquestlabs.com 1.4. Emergency telephone number Emergency number : (844) 523-4086 (3E Company - Account 10069) SECTION 2: Hazard(s) identification 2.1. Classification of the substance or mixture Classification (GHS-US) Acute Tox. 3 (Oral) H301 - Toxic if swallowed Acute Tox. 3 (Dermal) H311 - Toxic in contact with skin Acute Tox. 3 (Inhalation) H331 - Toxic if inhaled Skin Corr. 1C H314 - Causes severe skin burns and eye damage Eye Dam. 1 H318 - Causes serious eye damage STOT SE 3 H335 - May cause respiratory irritation Full text of H-phrases: see section 16 2.2. Label elements GHS-US labeling Hazard pictograms (GHS-US) : GHS05 GHS06 GHS07 Signal word (GHS-US) : Danger Hazard statements (GHS-US) -
Chemical Names and CAS Numbers Final
Chemical Abstract Chemical Formula Chemical Name Service (CAS) Number C3H8O 1‐propanol C4H7BrO2 2‐bromobutyric acid 80‐58‐0 GeH3COOH 2‐germaacetic acid C4H10 2‐methylpropane 75‐28‐5 C3H8O 2‐propanol 67‐63‐0 C6H10O3 4‐acetylbutyric acid 448671 C4H7BrO2 4‐bromobutyric acid 2623‐87‐2 CH3CHO acetaldehyde CH3CONH2 acetamide C8H9NO2 acetaminophen 103‐90‐2 − C2H3O2 acetate ion − CH3COO acetate ion C2H4O2 acetic acid 64‐19‐7 CH3COOH acetic acid (CH3)2CO acetone CH3COCl acetyl chloride C2H2 acetylene 74‐86‐2 HCCH acetylene C9H8O4 acetylsalicylic acid 50‐78‐2 H2C(CH)CN acrylonitrile C3H7NO2 Ala C3H7NO2 alanine 56‐41‐7 NaAlSi3O3 albite AlSb aluminium antimonide 25152‐52‐7 AlAs aluminium arsenide 22831‐42‐1 AlBO2 aluminium borate 61279‐70‐7 AlBO aluminium boron oxide 12041‐48‐4 AlBr3 aluminium bromide 7727‐15‐3 AlBr3•6H2O aluminium bromide hexahydrate 2149397 AlCl4Cs aluminium caesium tetrachloride 17992‐03‐9 AlCl3 aluminium chloride (anhydrous) 7446‐70‐0 AlCl3•6H2O aluminium chloride hexahydrate 7784‐13‐6 AlClO aluminium chloride oxide 13596‐11‐7 AlB2 aluminium diboride 12041‐50‐8 AlF2 aluminium difluoride 13569‐23‐8 AlF2O aluminium difluoride oxide 38344‐66‐0 AlB12 aluminium dodecaboride 12041‐54‐2 Al2F6 aluminium fluoride 17949‐86‐9 AlF3 aluminium fluoride 7784‐18‐1 Al(CHO2)3 aluminium formate 7360‐53‐4 1 of 75 Chemical Abstract Chemical Formula Chemical Name Service (CAS) Number Al(OH)3 aluminium hydroxide 21645‐51‐2 Al2I6 aluminium iodide 18898‐35‐6 AlI3 aluminium iodide 7784‐23‐8 AlBr aluminium monobromide 22359‐97‐3 AlCl aluminium monochloride -
Colossal Pressure-Induced Softening in Scandium Fluoride
PHYSICAL REVIEW LETTERS 124, 255502 (2020) Colossal Pressure-Induced Softening in Scandium Fluoride † † † Zhongsheng Wei ,1, Lei Tan ,1, Guanqun Cai ,1, Anthony E. Phillips ,1 Ivan da Silva ,2 Mark G. Kibble,2 and Martin T. Dove 3,4,* 1School of Physics and Astronomy, Queen Mary University of London, Mile End Road, London E1 4NS, United Kingdom 2ISIS Neutron and Muon Facility, Rutherford Appleton Laboratory, Harwell Campus, Didcot, Oxfordshire OX11 0QX, United Kingdom 3College of Computer Science, Sichuan University, Chengdu, Sichuan 610065, People’s Republic of China 4Department of Physics, School of Sciences, Wuhan University of Technology, 205 Luoshi Road, Hongshan district, Wuhan, Hubei 430070, People’s Republic of China (Received 2 April 2020; accepted 2 June 2020; published 25 June 2020) The counterintuitive phenomenon of pressure-induced softening in materials is likely to be caused by the same dynamical behavior that produces negative thermal expansion. Through a combination of molecular dynamics simulation on an idealized model and neutron diffraction at variable temperature and pressure, we show the existence of extraordinary and unprecedented pressure-induced softening in the negative thermal 0 expansion material scandium fluoride ScF3. The pressure derivative of the bulk modulus B, B ¼ ð∂B=∂PÞP¼0, reaches values as low as −220 Æ 30 at 50 K, and is constant at −50 between 150 and 250 K. DOI: 10.1103/PhysRevLett.124.255502 Just over 20 years ago a seminal paper on negative means that at high temperature the vibration of the bond thermal expansion in ZrW2O8 [1] marked the beginning of involves the bond stretching more than compressing, leading a new area in materials chemistry and physics that has led to to an increase in the average separation, as illustrated in the discovery of many materials whose phonon behavior Fig. -
The Elements.Pdf
A Periodic Table of the Elements at Los Alamos National Laboratory Los Alamos National Laboratory's Chemistry Division Presents Periodic Table of the Elements A Resource for Elementary, Middle School, and High School Students Click an element for more information: Group** Period 1 18 IA VIIIA 1A 8A 1 2 13 14 15 16 17 2 1 H IIA IIIA IVA VA VIAVIIA He 1.008 2A 3A 4A 5A 6A 7A 4.003 3 4 5 6 7 8 9 10 2 Li Be B C N O F Ne 6.941 9.012 10.81 12.01 14.01 16.00 19.00 20.18 11 12 3 4 5 6 7 8 9 10 11 12 13 14 15 16 17 18 3 Na Mg IIIB IVB VB VIB VIIB ------- VIII IB IIB Al Si P S Cl Ar 22.99 24.31 3B 4B 5B 6B 7B ------- 1B 2B 26.98 28.09 30.97 32.07 35.45 39.95 ------- 8 ------- 19 20 21 22 23 24 25 26 27 28 29 30 31 32 33 34 35 36 4 K Ca Sc Ti V Cr Mn Fe Co Ni Cu Zn Ga Ge As Se Br Kr 39.10 40.08 44.96 47.88 50.94 52.00 54.94 55.85 58.47 58.69 63.55 65.39 69.72 72.59 74.92 78.96 79.90 83.80 37 38 39 40 41 42 43 44 45 46 47 48 49 50 51 52 53 54 5 Rb Sr Y Zr NbMo Tc Ru Rh PdAgCd In Sn Sb Te I Xe 85.47 87.62 88.91 91.22 92.91 95.94 (98) 101.1 102.9 106.4 107.9 112.4 114.8 118.7 121.8 127.6 126.9 131.3 55 56 57 72 73 74 75 76 77 78 79 80 81 82 83 84 85 86 6 Cs Ba La* Hf Ta W Re Os Ir Pt AuHg Tl Pb Bi Po At Rn 132.9 137.3 138.9 178.5 180.9 183.9 186.2 190.2 190.2 195.1 197.0 200.5 204.4 207.2 209.0 (210) (210) (222) 87 88 89 104 105 106 107 108 109 110 111 112 114 116 118 7 Fr Ra Ac~RfDb Sg Bh Hs Mt --- --- --- --- --- --- (223) (226) (227) (257) (260) (263) (262) (265) (266) () () () () () () http://pearl1.lanl.gov/periodic/ (1 of 3) [5/17/2001 4:06:20 PM] A Periodic Table of the Elements at Los Alamos National Laboratory 58 59 60 61 62 63 64 65 66 67 68 69 70 71 Lanthanide Series* Ce Pr NdPmSm Eu Gd TbDyHo Er TmYbLu 140.1 140.9 144.2 (147) 150.4 152.0 157.3 158.9 162.5 164.9 167.3 168.9 173.0 175.0 90 91 92 93 94 95 96 97 98 99 100 101 102 103 Actinide Series~ Th Pa U Np Pu AmCmBk Cf Es FmMdNo Lr 232.0 (231) (238) (237) (242) (243) (247) (247) (249) (254) (253) (256) (254) (257) ** Groups are noted by 3 notation conventions. -
Periodic Table of Elements
The origin of the elements – Dr. Ille C. Gebeshuber, www.ille.com – Vienna, March 2007 The origin of the elements Univ.-Ass. Dipl.-Ing. Dr. techn. Ille C. Gebeshuber Institut für Allgemeine Physik Technische Universität Wien Wiedner Hauptstrasse 8-10/134 1040 Wien Tel. +43 1 58801 13436 FAX: +43 1 58801 13499 Internet: http://www.ille.com/ © 2007 © Photographs of the elements: Mag. Jürgen Bauer, http://www.smart-elements.com 1 The origin of the elements – Dr. Ille C. Gebeshuber, www.ille.com – Vienna, March 2007 I. The Periodic table............................................................................................................... 5 Arrangement........................................................................................................................... 5 Periodicity of chemical properties.......................................................................................... 6 Groups and periods............................................................................................................. 6 Periodic trends of groups.................................................................................................... 6 Periodic trends of periods................................................................................................... 7 Examples ................................................................................................................................ 7 Noble gases ....................................................................................................................... -
A System for the Qualitative Analysis for the Rare Elements by a Non-Sulfide Ches Me
Louisiana State University LSU Digital Commons LSU Historical Dissertations and Theses Graduate School 1957 A System for the Qualitative Analysis for the Rare Elements by a Non-Sulfide cheS me. Archie Oliver Parks Jr Louisiana State University and Agricultural & Mechanical College Follow this and additional works at: https://digitalcommons.lsu.edu/gradschool_disstheses Recommended Citation Parks, Archie Oliver Jr, "A System for the Qualitative Analysis for the Rare Elements by a Non-Sulfide cheS me." (1957). LSU Historical Dissertations and Theses. 220. https://digitalcommons.lsu.edu/gradschool_disstheses/220 This Dissertation is brought to you for free and open access by the Graduate School at LSU Digital Commons. It has been accepted for inclusion in LSU Historical Dissertations and Theses by an authorized administrator of LSU Digital Commons. For more information, please contact [email protected]. A SYSTEM FOR THE QUALITATIVE ANALYSIS FOR THE RARE ELEMENTS BY A NON-STTIFIDE SCHEME A Dissertation Submi tied to the Graduate Faculty of the V' isd me State Un;versity and Agricultural and Mechanical College in partial fulfillment of the recmirements for the degree of Doctor of Philosophy in The Department of Chorrj - '^ry by Archie Oliver Parks, Jr. B.S., Sul Ross State College, 19U2 .A., Southwest Texas State Teachers College, 1 August, 1957 ACKNOWLEDGMENT The author ie indebted to Dr. Philip W. West, under whose direction this work was carried out, for his patience, encouragement and assistance during the course of this investigation. He is also indebted to Dr. 3uddhadev Sen, Father W. J. Rimes, and to Mr. George Lyles for their encouragement and stimulating interest in the details of the work. -
Metal Fluorides Produced Using Chlorine Trifluoride Gas
Journal of Surface Engineered Materials and Advanced Technology, 2015, 5, 228-236 Published Online October 2015 in SciRes. http://www.scirp.org/journal/jsemat http://dx.doi.org/10.4236/jsemat.2015.54024 Metal Fluorides Produced Using Chlorine Trifluoride Gas Hitomi Matsuda1, Hitoshi Habuka1*, Yuuki Ishida2, Toshiyuki Ohno3 1Department of Chemical and Energy Engineering, Yokohama National University, Yokohama, Japan 2National Institute of Advanced Industrial Science and Technology, Tsukuba, Japan 3FUPET, Tsukuba, Japan Email: *[email protected] Received 12 September 2015; accepted 26 October 2015; published 29 October 2015 Copyright © 2015 by authors and Scientific Research Publishing Inc. This work is licensed under the Creative Commons Attribution International License (CC BY). http://creativecommons.org/licenses/by/4.0/ Abstract For developing coating materials, the fluorides of scandium, lanthanum, strontium, barium, mag- nesium and aluminum were produced from their oxides and chlorides by means of exposure to chlorine trifluoride gas at temperatures between room temperature and 700˚C. The metal chlo- rides could be easily fluorinated even at room temperature, while the metal oxides required tem- peratures higher than 300˚C. After the heating in ambient hydrogen at 1100˚C, the fluorides of lanthanum and barium showed very low weight losses at 1100˚C, although the weights of the other fluorides significantly decreased. These materials may work as protective films against corrosive and high temperature environments, particularly when using the chlorine trifluoride gas. Keywords Metal Fluoride, Metal Oxide, Chlorine Trifluoride, Synthesis, Coating Film Material 1. Introduction Chemical vapor deposition (CVD) can produce various high quality and functional material films [1]. In the CVD reactor, a film is formed not only on the substrate surface, but also on the surface of various reactor parts, such as the susceptor, gas distributor and exhaust. -
Supplementary Materials For
advances.sciencemag.org/cgi/content/full/5/11/eaay2748/DC1 Supplementary Materials for Entropic elasticity and negative thermal expansion in a simple cubic crystal David Wendt, Emil Bozin, Joerg Neuefeind, Katharine Page, Wei Ku, Limin Wang, Brent Fultz, Alexei V. Tkachenko, Igor A. Zaliznyak* *Corresponding author. Email: [email protected] Published 1 November 2019, Sci. Adv. 5, eaay2748 (2019) DOI: 10.1126/sciadv.aay2748 This PDF file includes: Supplementary Text Table S1. Scandium ionization energies, Ei(Sc) (45), and fluorine electron affinity, Ea(F) (49), used in eq. S28. Table S2. Frozen phonon calculation of the energy change as a function of the longitudinal (ΔE∥) and transverse (ΔE) fluorine displacement in ScF3. 11 Table S3. Parameters of an effective potential, Ux kx24 kx, for the longitudinal, 244 rr 0 u U|| , and transverse, U , r0 = 2.0Å fluorine displacement in ScF3. r0 r0 Table S4. The structural parameters of ScF3 obtained from Rietveld refinements of NOMAD data showing the standard uncertainty for the lattice spacing, a (measured in Å), and the atomic 2 mean square displacement parameters (measured in 0.01*Å ), isotropic for Sc (Uiso-Sc) and 2 anisotropic for F (Upar-F and Uperp-F, both measured in 0.01*Å ). Table S5. The structural parameters of ScF3 obtained from Rietveld refinements of NPDF data including parameters Rwp and Rp quantifying the goodness of the fit. Fig. S1. Electronic band structure in ScF3. Fig. S2. Effective potential of the fluorine ion in ScF3. Fig. S3. Selected plots of Rietveld refinement of structural parameters in ScF3. References (37–55) Supplementary Text Crystal structure and structural phase transition in ScF3 ScF3 crystallizes in a simple AMX3 cubic perovskite structure (Pm3m) with the A cations 10,12 36,37 absent (the ReO3 structure ). -
Scandium Quantification in Selected Inorganic and Organometallic Compounds
SCANDIUM QUANTIFICATION IN SELECTED INORGANIC AND ORGANOMETALLIC COMPOUNDS by Hlengiwe Thandekile Mnculwane A thesis submitted in fulfilment of the requirements for the degree of Magister Scientiae In the Faculty of Natural & Agricultural Sciences Department of Chemistry University of the Free State Bloemfontein Supervisor: Prof. W. Purcell Co-Supervisor: Dr. J. Venter January 2016 Declaration by candidate I hereby declare that the dissertation submitted here for the degree of Master in Science at the University of the Free State is my own original work and has not been previously submitted for academic examination towards any qualification at any other University. I further declare that all the sources that I have used or quoted have been indicated and acknowledged by means of complete references. Signature...................................................... Date............................................. Hlengiwe Thandekile Mnculwane Acknowledgements I hereby wish to thank God for being with me up to thus far and each and every person who contributed, directly or indirectly, to the completion and success of this study: Firstly, I am indebted to my supervisor, Prof. W Purcell for giving me the opportunity to further my academic career by accepting me as part of the Analytical chemistry group and for the guidance and patience throughout my study. To my Co-supervisor, Dr. J. Venter, thank you so much for the review of my work and for the recommendations and suggestions which greatly improved my thesis writing. To my colleagues, Dr. M. Nete, Dr. T. Chiweshe, S. Xaba, D. Nhlapho, M. Zidge, Dr S. Kumar, G. Malefo, Q. Vilakazi and L. Ntoi, I would like to say thank you very much for being so helpful and for providing such a friendly environment that was also conducive to carry out my project, and to P.