(12) Patent Application Publication (10) Pub. No.: US 2014/0057512 A1 Matthews (43) Pub
Total Page:16
File Type:pdf, Size:1020Kb
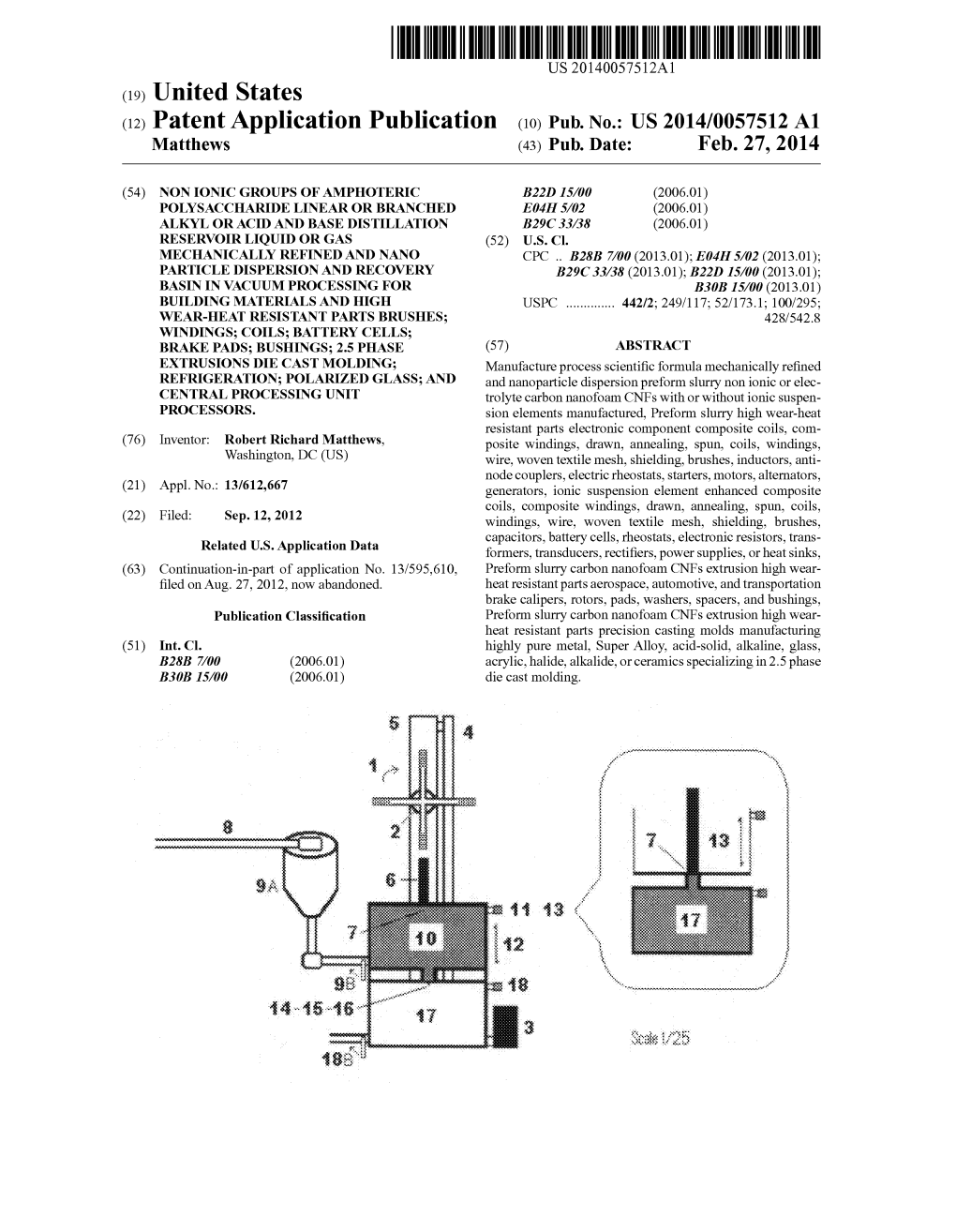
Load more
Recommended publications
-
A Study Into the Localized Corrosion of Magnesium Alloy Magnox Al-80
A Study into the Localized Corrosion of Magnesium Alloy Magnox Al-80 Ronald N. Clark‡*, James Humpage**, Robert Burrows*, Hugh Godfrey***, Mustufa Sagir****, Geraint Williams** ‡Corresponding author. E-mail: [email protected]. *National Nuclear Laboratory, Unit 102B, Sperry Way, National Nuclear Laboratory, Stonehouse, GL10 3UT, UK **Swansea University, Materials Research Centre, Bay Campus, Fabian Way, Crymlyn Burrows, Swansea, SA1 8EN, Wales, UK ***National Nuclear Laboratory, Workington Laboratory, Havelock Road, Derwent Howe, Workington, Cumbria, CA14 3YQ, UK ****Sellafield Limited, Hinton House, Birchwood Park Avenue, Risley, Warrington, Cheshire, WA3 6 GR, UK [email protected] [email protected] [email protected] [email protected] [email protected] ABSTRACT Magnesium (Mg) non-oxidizing alloy, known as Magnox, was historically used as a fuel cladding material for the first-generation of carbon dioxide (CO2) gas-cooled nuclear reactors in the UK. Waste Magnox is currently stored in cooling ponds, pending final disposal. The corrosion resistance of Mg and its alloys is relatively poor, compared to modern cladding materials such as zirconium (Zr) alloys, so it is important to have a knowledge of the chloride concentration/pH dependence on breakdown and localized corrosion characteristics prior to waste retrievals taking place. Our results show that Magnox exhibits passivity in high pH solutions, with charge transfer resistance and passive film thicknesses showing an increase with immersion time. When chloride is added to the system the higher pH maintains Magnox passivity, as shown through a combination of potentiodynamic and time-lapse/post corrosion imaging experiments. Potentiodynamic polarization of Magnox reveals a -229 mV-decade linear dependence of breakdown potential with chloride ion concentration. -
WATTS 04-2013 P1 PARC Management Team / Bestuurspan Aug
04-2013 WATTS Year 83 + 4m Monthly newsletter of the Pretoria Amateur Radio Club Maandelikse nuusbrief van die Pretoria Amateur Radio Klub. PARC, PO Box 73696, Lynnwood Ridge 0040, RSA web http://www.parc.org.za mail: [email protected] Bulletins: 145,725 MHz 08:45 Sundays/Sondae Relays: 1.840, 3.700, 7.066, 10.135, 14.235, 51.400, 438.825, 1297 MHz ZR6FD logo Activated frequencies are announced prior to bulletins Papier / Paper Drukwerk ZS6RH Swapshop: 2m and 7.066 MHz Live on-air after bulletins ZS6RH Bulletin repeats Mondays | herhalings : Maandae 2m 19:45 Another glimpse of the extensive facility operated by Iain-ZS5IE (more photos on QRZ.com) In this issue In hierdie uitgawe Next club events Fleamarkets at PMC Member news and activities Lede-nuus en Aktiwiteite Wed 1 May (public holiday) Sat 10 Aug Sat 7 Dec Technical Rig reviews Tegnies Club social at U.P. G7FEK limited space antenna Thursday 4 Apr 7pm Aluminium alloys Club committee meeting ● Page eight -- Bladsy agt Thursday 18 Apr 7pm WATTS 04-2013 p1 PARC Management team / Bestuurspan Aug. 2012 – Aug. 2013 Committee members Chairman, Contests Pierre Holtzhausen ZS6PJH [email protected] 012-655-0726 082-575-5799 Vice Chairman, SARL liason Fritz Sutherland ZS6SF [email protected] 012-811-3875 083-304-0028 Secretary, Clubs, Strategy Jean de Villiers ZS6ARA [email protected] 012-663-6554 083-627-2506 Treasurer, SARS Andre van Tonder ZS6BRC [email protected] 361-3292 082-467-0287 Rallies, Social Johan de Bruyn ZS6JHB [email protected] 012-803-7385 079-333-4107 Webmaster Graham Reid ZR6GJR [email protected] 083-701-0511 RAE, Bulletin co-ordinator Vincent Harrison ZS6BTY [email protected] 012-998-8165 083-754-0115 Repeaters, Technical Craig Symington ZS6RH [email protected] 081-334-6817 Technical, Kits. -
Gold in Antique Copper Alloys
Gold in Antique Copper Alloys Paul T. Craddock cent of either gold or silver would make to the appearance of Research Laboratory, The British Museum, London, U.K. the copper. However, although we can accept the story of its accidental discovery two centuries before Pliny's time as Lost continents, lost cities and fabulous materials from past apocryphal it is difficult to dismiss the latter's description of ages have a natural fascination for scholar and layman alike. its popularity with collectors and its high value in his own Since the Renaissance, men have sought examples of Corin- time. It would seem that in Pliny's day the term Corinthian thian Bronze, the precious alloy much extolled by antient Bronze was used to describe a group of alloys which were writers and have tried to establish its nature. As indicative of readily distinguished and appreciated, and for which attitudes towards it, Thomas Corayte (1) described the bronze collectors were willing to pay a high price. horses of San Marco in Venice as being 'a remarkable monu- The first step towards recognizing surviving examples of ment, four goodly brazen horses of Corinthian metal and this material was, of course, to have some idea of its fully as great as life' , apparently for no better reason than that appearance. Small quantities of gold and silver incorporated he thought such noble statuary demanded the most prized in copper are known to have a dramatic effect on the resulting bronze metal of them all. Further, in Pliny's 'Natural alloys if they are subsequently treated in a suitable manner. -
Elemental Metals Combiningscientific Facts with Medieval
Elemental Metals Copper Element: Earth, Water, Wood, Lightning, Metal Combiningscientific facts with medievalAvailability: Common folklore and New Age mysticism,Elemental Copper is an essential trace nutrient for animal and Metals provides you with information to helpplant life. It is also one of the most common metals and has excellent electrical conductivity, making it highly you customize weapons, armor, tools, and otheruseful for electronics. Copper resists corrosion from magical items. Each metal’s listing includes itswater, but is slowly oxidized in by oxygen in the air. relative availability, elemental affinities, and an Copper is the metal of choice when employing overview of its magical properties. Us as aemeralds into magical items. It has a strong affinity companion along withElemental Gemstones towith the gem, and conducts the gem’s power well. design your dream weapons, armor, or artifacts.Healing wands and staves are often made of copper. The combination of copper and emerald also cre- This product is designed to be usable withates potent charms to attract or protect wealth. any roleplaying system, however it will be of the most value when used with theKarma Role-Iron playing System. Element: Earth, Fire Availability: Common Iron is an abundant, heavy metal used in a wide range of items. It is perhaps the most important metal in civilization, because of its wide range of uses. Base metals are those metals that are most common and Iron is rarely used magically in anything but weap- easily available. But just because they are common andons and armor. It is too heavy to be a practical metal inexpensive, doesn’t mean they are not valuable tofor most jewelry or smaller magic items. -
Development of Filler Metals and Procedures for Vacuum Brazing Of
Development of Filler Metals and Procedures for Vacuum Brazing of Aluminum Several brazing filler metal compositions have been developed which offer significant improvements over existing compositions. They braze in vacuum at temperatures lower than normal flow temperatures and have equal or better flowability BY W. J. WERNER, G. M. SLAUGHTER AND F. B. GURTNER Introduction ry cleanliness levels under production vantages. As a single entity, it was This report documents work per conditions. The maximum allowable immediately more desirable from a formed toward the development of lag between cleaning and brazing was cleaning, assembling and material found to be 12 hours. handling standpoint. Metallurgically, new brazing filler metals for vacuum- 2 fluxless brazing (1 X 10~6 torr) C. S. Beuyukian developed tech the 4045 brazing filler metal with its certain aluminum alloys of interest to niques for vacuum or inert gas fluxless lower silicon content allowed greater the Army. The base metals under brazing of aluminum cold plates for latitude in processing parameters than consideration were alloys 6061, 2219, use in Apollo command modules. In did alloy No. 718. 7075 and 2024. Brazing filler metal this work, brazing filler metal No. 718 Finally, the workers at Aeronca, and No. 23 brazing sheet were evalu Inc. completed a study on inert gas flow temperatures needed for these 3 alloys encompass the temperature ated. Alloy No. 718 is nominally 88% brazing of aluminum in early 1967. range 900 to 1200F. Specifically, the aluminum, 12% silicon; No. 23 braz Their work was concerned with de contract called for the development of ing sheet is comprised of 6951 base velopment of high strength brazed alloys with flow temperatures of 950, alloy clad on one side with 4045 aluminum honeycomb structures 1000, and 1050F. -
Maec.19 70 (University of London) London
COMPLEX & INCREMENTAL STRESS CREEP OF A HIGH STRENGTH ALUMINIUM ALLOY AT ELEVATED TEMPERATURES (ALLOY: HIDUMINIUM RR58 SPECIFICATION DTD 731) by SURINDAR BAHADUR MATHUR Thesis presented in the Department of Mechanical Engineering for the Award of the Doctor of Philosphy in Mechanical Engineering of the University of London. Mechanical Engineering Department Imperial College of Science and Technology mAec.19 70 (University of London) London. ABSTRACT A theory for creep rates under complex and incremental stresses is deduced from experimental data concerning complex creep at elevated temperatures for the test material HIDUMINIUM RR 58 - Specification DID 731. The most important results are for tubular specimens tested at 150°C and 250°C under incremental loads. The analysis of results relates to steady state creep only. Modified relationships in stress equivalence and strain equivalence are proposed to account for thermal softening, polygonization, recrystallization and the resulting exaggerated flow in the direction of the applied shear. (The original equations are based on the hypothesis of Von Mises). A further relationship is suggested between the immediate total energy of distortion and the subsequent creep work rate. Results of the static tests and the results of the tests for creep behaviour under complex loading are presented and compared with the results of static torsion and simple incremental torsion creep tests on the basis of the proposed equations. An appendix describes the complex creep testing machine, furnace, extensometers -
Masters of Jade Book.Indb
TM BY M ICHAEL A. GOODWIN, ERIC M INTON, JOHN M ØRKE, NEALL R AEMONN P RICE, HOLDEN S HEARER, DEAN S HOMSHAK, CHARLES H. SPAULDING, AND R OBERT V ANCE 1 CREDITS Special Thanks: While this book deviates from Mana- Authors: Michael A. Goodwin, Eric Minton, John Mørke, cle and Coin, we nevertheless owe a debt to the vision Neall Raemonn Price, Holden Shearer, Dean Shomshak, of Geoffrey C. Grabowski, who used the Guild to show Charles H. Spaulding, and Robert Vance us Creation. I’d also like to thank Allison Cheek for her Developer: John Mørke with Holden Shearer good taste in movies, and for being my first reader. Also Editor: Stephen Lea Sheppard a big thanks to Liz Grushcow for her attention to detail. Creative Director: Rich Thomas Lastly to Michael Goodwin, who fought through pain to Art Direction and Layout: Brian Glass make his contribution to this book the best it could be. Artists: Tazio Bettin, Groundbreakers Studio and Melissa Uran Cover Art: Melissa Uran © 2012 CCP hf. All rights reserved. Reproduction without the written permission of the publisher is expressly forbidden, except for the purposes of reviews, and for blank character sheets, which may be reproduced for personal use only. White Wolf and Exalted are registered trademarks of CCP hf. All rights reserved. Scroll of Exalts, Scroll of Heroes, Scroll of Kings, Scroll of the Monk, Scroll of the Monk the Imperfect Lotus, Scroll of Fallen Races, the Manual of Exalted Power the Dragon-Blooded, the Manual of Exalted Power the Lunars, the Manual of Exalted Power the Sidereals, -
Microstructual Characteristics of Magnesium Metal Matrix Composites
University of Central Florida STARS Electronic Theses and Dissertations, 2004-2019 2012 Microstructual Characteristics Of Magnesium Metal Matrix Composites Dongho Shin University of Central Florida Part of the Materials Science and Engineering Commons Find similar works at: https://stars.library.ucf.edu/etd University of Central Florida Libraries http://library.ucf.edu This Masters Thesis (Open Access) is brought to you for free and open access by STARS. It has been accepted for inclusion in Electronic Theses and Dissertations, 2004-2019 by an authorized administrator of STARS. For more information, please contact [email protected]. STARS Citation Shin, Dongho, "Microstructual Characteristics Of Magnesium Metal Matrix Composites" (2012). Electronic Theses and Dissertations, 2004-2019. 2244. https://stars.library.ucf.edu/etd/2244 MICROSTRUCTUAL CHARACTERISTICS OF MAGNESIUM METAL MATRIX COMPOSITES by DONGHO SHIN B.S. Korea Military Academy, 2006 A thesis submitted in partial fulfillment of the requirements for the degree of Master of Science in the Department of Mechanical, Materials and Aerospace Engineering in the College of Engineering and Computer Science at the University of Central Florida Orlando, Florida Summer Term 2012 Major Professor: Yongho Sohn 1 © 2012 Dongho Shin ii ABSTRACT Magnesium (Mg) Metal matrix composites (MMCs) reinforced by ceramic reinforcements are being developed for a variety of applications in automotive and aerospace because of their strength-to-weight ratio. Reinforcement being considered includes SiC, Al2O3, Carbon fiber and B4C in order to improve the mechanical properties of MMCs. Microstructural and interfacial characteristics of MMCs can play a critical role in controlling the MMCs’ mechanical properties. This study was carried out to understand the microstructural and interfacial development between Mg-9wt.Al-1wt.Zn (AZ91) alloy matrix and several reinforcements including SiC, Al2O3, Carbon fibers and B4C. -
Aluminium Alloys Chemical Composition Pdf
Aluminium alloys chemical composition pdf Continue Alloy in which aluminum is the predominant lye frame of aluminum welded aluminium alloy, manufactured in 1990. Aluminum alloys (or aluminium alloys; see spelling differences) are alloys in which aluminium (Al) is the predominant metal. Typical alloy elements are copper, magnesium, manganese, silicon, tin and zinc. There are two main classifications, namely casting alloys and forged alloys, both further subdivided into heat-treatable and heat-free categories. Approximately 85% of aluminium is used for forged products, e.g. laminated plates, foils and extrusions. Aluminum cast alloys produce cost-effective products due to their low melting point, although they generally have lower tensile strength than forged alloys. The most important cast aluminium alloy system is Al–Si, where high silicon levels (4.0–13%) contributes to giving good casting features. Aluminum alloys are widely used in engineering structures and components where a low weight or corrosion resistance is required. [1] Alloys composed mostly of aluminium have been very important in aerospace production since the introduction of metal leather aircraft. Aluminum-magnesium alloys are both lighter than other aluminium alloys and much less flammable than other alloys containing a very high percentage of magnesium. [2] Aluminum alloy surfaces will develop a white layer, protective of aluminum oxide, if not protected by proper anodization and/or dyeing procedures. In a wet environment, galvanic corrosion can occur when an aluminum alloy is placed in electrical contact with other metals with a more positive corrosion potential than aluminum, and an electrolyte is present that allows the exchange of ions. -
Microstructual and Thermal Analysis of Aluminum-Silicon and Magnesium-Aluminum Alloys Subjected to High Cooling Rates
University of Windsor Scholarship at UWindsor Electronic Theses and Dissertations Theses, Dissertations, and Major Papers 2012 Microstructual and Thermal Analysis of Aluminum-Silicon and Magnesium-Aluminum Alloys Subjected to High Cooling Rates Paul Marchwica University of Windsor Follow this and additional works at: https://scholar.uwindsor.ca/etd Recommended Citation Marchwica, Paul, "Microstructual and Thermal Analysis of Aluminum-Silicon and Magnesium-Aluminum Alloys Subjected to High Cooling Rates" (2012). Electronic Theses and Dissertations. 5572. https://scholar.uwindsor.ca/etd/5572 This online database contains the full-text of PhD dissertations and Masters’ theses of University of Windsor students from 1954 forward. These documents are made available for personal study and research purposes only, in accordance with the Canadian Copyright Act and the Creative Commons license—CC BY-NC-ND (Attribution, Non-Commercial, No Derivative Works). Under this license, works must always be attributed to the copyright holder (original author), cannot be used for any commercial purposes, and may not be altered. Any other use would require the permission of the copyright holder. Students may inquire about withdrawing their dissertation and/or thesis from this database. For additional inquiries, please contact the repository administrator via email ([email protected]) or by telephone at 519-253-3000ext. 3208. Microstructual and Thermal Analysis of AlSi and MgAl Alloys Subjected to High Cooling Rates By Paul C. Marchwica A Thesis Submitted to the Faculty of Graduate Studies through the Department of Mechanical, Automotive and Materials Engineering in Partial Fulfillment of the Requirements for the Degree of Master of Applied Science at the University of Windsor Windsor, Ontario, Canada 2012 © 2012 P. -
What We Pay – Cash Gold Canada
What We Pay – Cash Gold Canada Gold prices today are near historic highs. Even scrap gold prices are soaring as the price of gold continues to climb. In order to make sure that you receive the best gold prices, make sure your gold buyer quotes the gold price per gram – this will ensure that you’re receiving the highest payout for your precious metals. The amount of money you earn for your gold, silver, and platinum depends on three factors: 1) Purity The higher the purity of your gold, the more it is worth. We’ll appraise your precious metals free of charge and let you know exactly how much they are worth prior to sending you a cheque. Let us remind you that once our specialists evaluate your items, we do not simply send you a cheque (like the competition), we will contact you with our best offer, and if you agree to the amount, we will immediately send you the money. Otherwise, we simply return your items no questions asked. 2) Weight Weight is also a factor. Heavier gold earns you more money. Again, we’ll tell you everything you need to know about your precious metals before proceeding. 3) Price Gold fluctuates in price according to market conditions. The price we offer is set by the market price for that day. Right now, gold is valued at record highs, so there has never been a better time to sell your used gold. Precious Metal Prices For Items Shipped To Us: The tables below list our current payment prices for gold jewelry ranging from 9Kt to 24Kt, dental gold , scrap gold , platinum jewelry , scrap platinum , sterling silverware , scrap silver , and American / Canadian coins shipped to us. -
Aluminum Alloy Weldability: Identification of Weld Solidification Cracking Mechanisms Through Novel Experimental Technique and Model Development
Dipl.-Ing. Nicolas Coniglio Aluminum Alloy Weldability: Identifi cation of Weld Solidifi cation Cracking Mechanisms through Novel Experimental Technique and Model Development BAM-Dissertationsreihe • Band 40 Berlin 2008 Die vorliegende Arbeit entstand an der BAM Bundesanstalt für Materialforschung und -prüfung. Impressum Aluminum Alloy Weldability: Identifi cation of Weld Solidifi cation Cracking Mechanisms through Novel Experimental Technique and Model Development 2008 Herausgeber: BAM Bundesanstalt für Materialforschung und -prüfung Unter den Eichen 87 12205 Berlin Telefon: +49 30 8104-0 Telefax: +49 30 8112029 E-Mail: [email protected] Internet: www.bam.de Copyright © 2008 by BAM Bundesanstalt für Materialforschung und -prüfung Layout: BAM-Arbeitsgruppe Z.64 ISSN 1613-4249 ISBN 978-3-9812354-3-2 Aluminum Alloy Weldability: Identification of Weld Solidification Cracking Mechanisms through Novel Experimental Technique and Model Development Dissertation zur Erlangung des akademischen Grades Doktor-Ingenieur (Dr.-Ing.) genehmigt durch die Fakultät für Maschinenbau der Otto-von-Guericke-Universität Madgeburg am 02.06.08 vorgelegte Dissertation von Dipl.-Ing. Nicolas Coniglio Thesis Committee: Prof. Dr.-Ing. A. Bertram Prof. Dr.-Ing. T. Böllinghaus Prof. C.E. Cross Prof. S. Marya Date of Examination: 23 October 2008 Abstract Abstract The objective of the present thesis is to make advancements in understanding solidification crack formation in aluminum welds, by investigating in particular the aluminum 6060/4043 system. Alloy 6060 is typical of a family of Al-Mg-Si extrusion alloys, which are considered weldable only when using an appropriate filler alloy such as 4043 (Al-5Si). The effect of 4043 filler dilution (i.e. weld metal silicon content) on cracking sensitivity and solidification path of Alloy 6060 welds are investigated.