The Underwater Application of Exothermic Welding
Total Page:16
File Type:pdf, Size:1020Kb
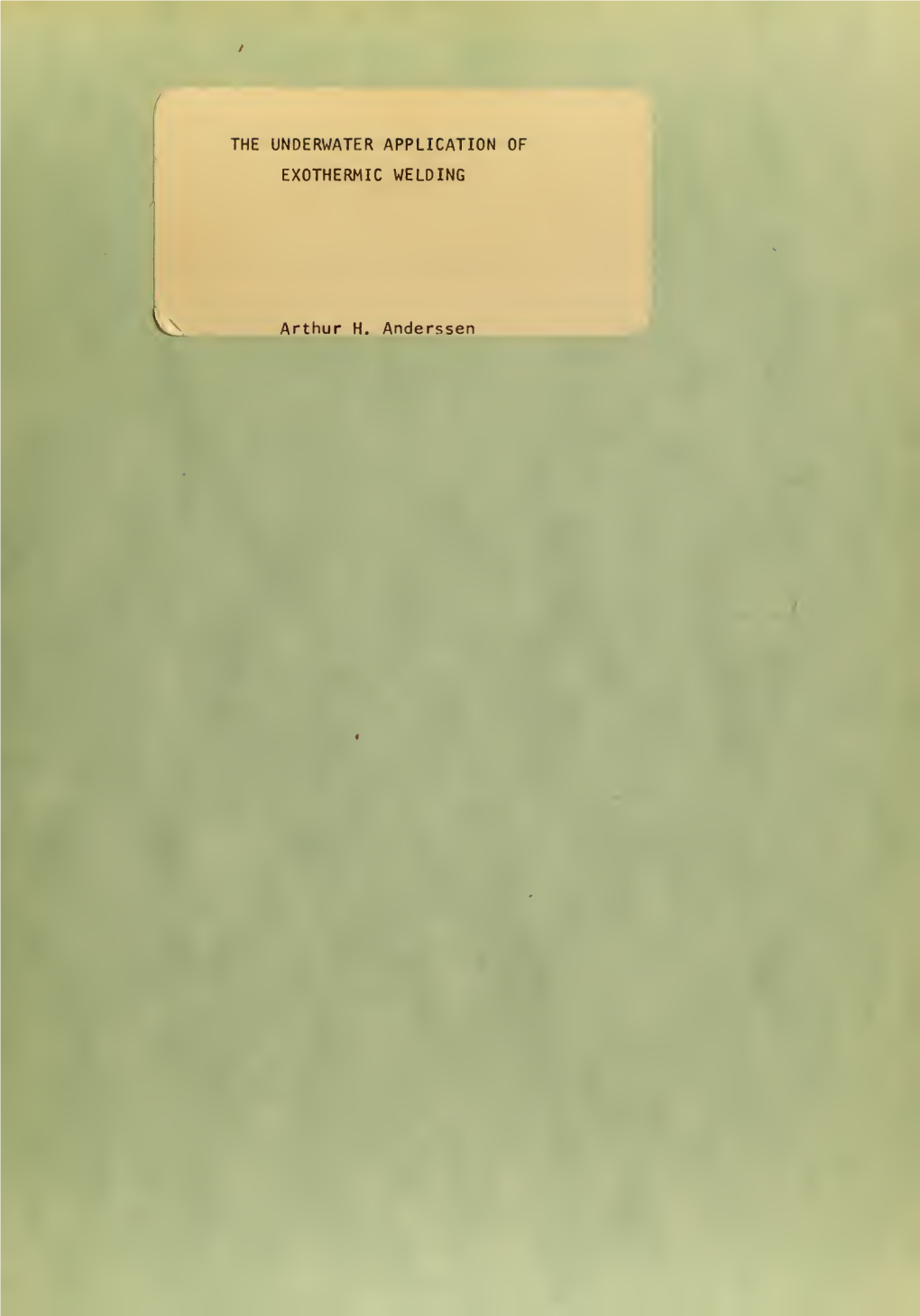
Load more
Recommended publications
-
Section 1 (Parts 1 - 4) of This Specification Includes Rail Welding by Electric Flash-Butt Welding Method
SECTION 05091 RAIL WELDING NOTE: Section 1 (Parts 1 - 4) of this specification includes rail welding by Electric Flash-Butt Welding method. Section 2 (Parts 5 - 8) of this specification includes rail welding by the Thermite Rail Welding method. SECTION 1 - ELECTRIC FLASH-BUTT WELDING PART 1 - GENERAL 1.01 SECTION INCLUDES A. The work specified in this section shall include the fabrication of continuous welded rail (CWR) strings by electric flash-butt welding, including testing, inspection, and qualification of welding and welders. B. The work specified in this section shall also include movement of rail from the manufacturer to the Contractor’s welding plant, from the welding plant to the welded string storage location and from the storage location to the final placement in track location. 1.02 RELATED SECTIONS A. Section 05651- General Track Construction B. Section 05652 - Ballasted Track Construction C. Section 05653 - Direct Fixation Track Construction D. Section 05656 - Running Rail 1.03 REFERENCES A. American Railway Engineering and Maintenance-of-Way Association (AREMA) Manual for Railway Engineering, Vol. I, Chapter 4, Specification for Fabrication of Continuous Welded Rail (latest addition). B. ASTM E18 C . ASTM E709 (replaced E109) D . ASTM E94 (replaced E142) E. ASTM E164 F . ASTM E709 (duplicate) G. AWS D1.1 1X0000 (11/07) 05091 - 1 H. USNRC Rules and Regulations, Title 10, Atomic Energy, Part 20. I. ASNT SNT-TC-1A Recommended Guidelines for Qualification and Certification of Non- Destructive Testing Personnel. 1.04 SUBMITTALS A. The Contractor shall submit procedures and documentation in accordance with the Section 01300 and as follows. -
General Disclaimer One Or More of the Following Statements May Affect This Document
General Disclaimer One or more of the Following Statements may affect this Document This document has been reproduced from the best copy furnished by the organizational source. It is being released in the interest of making available as much information as possible. This document may contain data, which exceeds the sheet parameters. It was furnished in this condition by the organizational source and is the best copy available. This document may contain tone-on-tone or color graphs, charts and/or pictures, which have been reproduced in black and white. This document is paginated as submitted by the original source. Portions of this document are not fully legible due to the historical nature of some of the material. However, it is the best reproduction available from the original submission. Produced by the NASA Center for Aerospace Information (CASI) MASSACHUSETTS INSTITUTE OF TEC'.-INOLOGY DEPARTMENT OF OCEAN ENGINEERING SEP 83 CAMBRIDGE. MASS. 02139 RECEIVED FAVUV wrw STI DEPI- , FINAL REPORT "Wo Under Contract No. NASW-3740 (M.I.T. OSP #93589) ON FEASIBILITY OF REMOTELY MANIPULATED WELDING IN SPACE -A STEP IN THE DEVELOPMENT OF NOVEL JOINING TECHNOLOGIES- Submitted to Office of Space Science and Applications Innovative Utilization of the Space Station Program Code E NASA Headquarters Washington, D.C. 20546 September 1983 by Koichi Masubuchi John E. Agapakis Andrew DeBiccari Christopher von Alt (NASA-CR-1754371 ZEASIbILITY CF RZ,1JTL": Y `84-20857 MANIPJLATED WELLINu iN SPAI.E. A STEP IN THE Uc.Y1;LuPdENT OF NUVLL Ju1NING Tkk ;HNuLUGIES Final Peport (c;dssachu6etts Irist. or Tccli.) U11CIds ibJ p HC Al2/Mk AJ 1 CSCL 1jI G:i/.i7 OOb47 i i rACKNOWLEDGEMENT The authors wish to acknowledge the assistance provided by M.I.T. -
Connector Theory and Application Connector Theory and Application a Guide to Connection Design and Specification
Connector Theory and Application Connector Theory and Application A Guide to Connection Design and Specification Revised 5th Edition Authored by: GARY DITROIA IEEE MEMBER BURNDY LLC 47 East Industrial Park Drive Manchester, NH 03109 USA RONALD LAI IEEE Life Senior Member ASME Life Member SAE Life Member Consultant to BURNDY LLC KENNETH WOO BURNDY LLC 47 East Industrial Park Drive Manchester, NH 03109 USA GAYLORD ZAHLMAN BURNDY LLC 47 East Industrial Park Drive Manchester, NH 03109 USA Connector Theory and Application - A Guide to Connection Design and Specification - Revised 5th Edition - 2 © BURNDY LLC, 2018 All rights reserved. Abstracting is permitted with credit to the source. Table of Contents Introduction 1.0 Theory of Connector Technology 1.1 Grounding (Earthing) and Bonding 1.1.1 Corrosion 1.1.2 Fault Current 1.1.3 Special Grounding Applications 1.1.4 Ground Connection Design 1.2 Substation 1.2.1 Distribution Substations 1.2.2 Conductors 1.2.3 Substation Connector Design 1.3 Underground Distribution 1.3.1 Design Objectives 1.3.2 Underground Secondary Networks 1.3.3 Special Considerations 1.3.4 Network Protection 1.4 Overhead 1.4.1 Thermal Expansion and Contraction 1.4.2 Mechanical Integrity 1.4.3 Dielectric Fundamentals 1.4.4 Corrosion 1.4.5 Performance Testing (ANSI C119.4) 1.5 Service Entrance 1.5.1 Secondary Conductor 1.5.2 Service Connectors 1.6 Telecommunication 1.6.1 Telecommunication Conductors 1.6.2 Telecommunication Connections 2.0 Connector Functions and Types 2.1 Functions 2.1.1 Tap 2.1.2 Terminal 2.1.3 Splice 2.2 Types of Connectors 2.2.1 Mechanical Connectors Connector Theory and Application - A Guide to Connection Design and Specification - Revised 5th Edition - © BURNDY LLC, 2018 All rights reserved. -
D49 Exothermic Welding System
EZGROUND GROUND ROD DRIVERS AND FLEXIBLE BRAID D49 — Exothermic welding system Earth points — Four-hole earth points Cat. no. A Hole size (in.) B (in.) C (in.) D (in.) E (in.) F (in.) 5 9 27 1 13 GPC110 4 x ⁄16 UNC x ⁄16 ⁄64 2 3 2 ⁄2 1 ⁄32 GPC111 As GPC110 with a pre-welded 20 in. long tail of 2/0 AWG PVC-insulated cable GPC110 Diagrams E D F C B A — Two-hole earth points Complete with front plate Cat. no. Conductor type B (in. dia.) C (in.) D (in.) E (in.) F (in.) 1 27 1 3 3 GPC115 1 in. x ⁄8 in. tape or 2/0 AWG cable ⁄64 2 3 ⁄8 2 ⁄16 1 ⁄4 GPC116 As GPC115 with a pre-welded 20 in. long tail of 2/0 AWG PVC-insulated cable 1 5 27 1 3 3 GPC120 1 in. x ⁄8 in. tape or ⁄16 in. dia. solid ⁄64 2 3 ⁄8 2 ⁄16 1 ⁄4 GPC125 GPC121 As PC120 with a pre-welded 20 in. long tail of 2/0 AWG PVC-insulated cable — Two-hole earth points Without front plate Cat. no. Conductor type B (in. dia.) C (in.) D (in.) E (in.) F (in.) 5 1 27 1 3 3 GPC115 – GPC120 GPC125 2 x ⁄16 UNC x ⁄2 ⁄64 2 3 ⁄8 2 ⁄16 1 ⁄4 GPC126 As PC125 with a pre-welded 20 in. long tail of 2/0 AWG PVC-insulated cable Diagrams D C E B F GPC116 – GPC121 D50 EZGROUND/FURSEWELD/BLACKBURN GROUNDING SYSTEMS — Exothermic welding system Earth points — One-hole earth points Cat. -
Cad Weld Type Exothermic Welding
MANUFACTURERS OF EXOTHERMIC WELD POWDER & GRAPHITE MOULDS Our company is a Manufacturer of Exothermic Weld Powder and Graphite Mould having more than 15 years’ experience. Our Firm is also well established organization in India, Dubai and overseas market and Manufactures and Export the following products: 01) Exothermic Weld Powder & Graphite Moulds (Factory situated in Gujrat – India.) 02) Copper Braided & Laminated Connectors (Factory situated in Mumbai - India) 03) Brass Parts Components, Accessories and Fittings (Factory situated in Gujrat – India.) We have earned good reputation amongst our international customers with our Quality Assurance, On time delivery and High Customer Satisfaction. To ensure consistent product quality, we work within a quality system that is approved with ISO 9001 – 2008, ISO 14000 and ISO 18000 certification. We manufacture all Products with CE & ROHS Compliance. Strict quality checks are carried out at different stages of manufacturing and only that material which passes stringent norms finds its way in the market around the Globe. We are also awarded GMP (Goods Manufacturing Practise) which assures that the products which we manufacture are of high quality and do not pose risk to our customer. Our vision The four pillars of our vision set out the long term direction for the company where we want to go and how we are going to get there: • We work to create a better future every day. • We help our customers feel good, have good and get more out of life with our brands and services that are good for them and good for others. • Whilst the company has ambitious plans for the future for its product range and its manufacturing abilities, our greatest objective will always be to maintain the highest level of quality assurance & service to the customer. -
Exothermic Welding Problems Compared to Clamped Ground Connections White Paper
Exothermic Welding Problems Compared to Clamped Ground Connections White Paper Contents Background Safety at work Quality earthing systems www.dehn-usa.com Exothermic Welding Problems Compared to Clamped Ground Connections White Paper This article discusses the advantages of DEHN clamping con- Safety nection grounding systems over exothermic weld connected As for the advantages of using clamping over exothermic weld, systems. safety has to be at the top of the list. The issues start with In order to describe the overwhelming advantages of using personal safety but quickly broaden into more complex job site clamping methods over exothermic weld methods, this article and materials handling difficulties as well. compares and contrasts the following key areas: The assembly process for a StSt clamping system consists of ¨ Safety mechanical fitting, alignment and then bolting connections. If the work pieces are misaligned, the fittings can be loosened, ¨ Assembly process adjusted and tightened to the final torque specifications. The ¨ Site and work preparation entire process of making the joint takes about the same time ¨ Job site safety analysis as replacing a bicycle tire. The assembly process is intrinsically ¨ Safety data sheet (SDS) repairable. The site work preparation includes all of the layout, ¨ Materials transportation measuring and trenching to place the metal grounding ma- terials into the soil, but that’s where the similarities between ¨ Quality welding and clamping end. ¨ Training Figure 1 depicts the typical layout for a bolted and clamped ¨ Inspection earth system before it is covered over with soil. ¨ Rework By contrast the assembly process for making exothermic weld connections includes the same material placement efforts, but ¨ Longevity needs more physical trench room to get the molds and joint ¨ Theft resistance in position. -
Exothermic Welding System Complying IEEE 837, Has Come Than That of the Conductor to Be Joined, the Weld Will up As a Robust Solution for These Problems
Exothermic Weld SYSTEM Complying IEEE 837, IEEE 80, NBC 2016, IS/IEC 62305 Electrical jointing or connection reliability is critical to the long-term integrity of the electrical system. Over the period of TECHNICAL FEATURES: time, due to ageing, less maintenance and changing weather conditions, the joints are becoming low performing joints as it Exothermic Weld connections form a solid bond around gets corroded or loosen due to temporary jointing techniques. the conductors assuring continuity. Standard exothermic weld has a cross-section greater An Exothermic Welding System complying IEEE 837, has come than that of the conductor to be joined, the weld will up as a robust solution for these problems. Today, Exothermic always remain cooler than the conductor under fault Welding is a globally accepted method to make reliable and conditions. safe connections between two or more conductors. This Superior electrcal conductiviy of the conductors technology is highly portable and does not require any external themselves. source of heat to make a joint offering in permanent molecular bonding among metallic conductors. Does not corrode, oxidize or degrade with time and is resistant to galvanic coupling. As per NBC:2016, IEEE 80:2013, BS 7430:2011, Able to withstand repeated electrical discharges. “An exothermic welding system is used for making electrical No environmental impact. connections of copper to copper, copper to steel or copper to cast iron for grounding and cathodic applications. An exothermic welded connection shall be suitable for exposure to the elements of direct burial in earth or concrete without LATEST CODES REFERENCES degradation over the lifetime of the grounding system.” NBC : 2016 IEEE 80 : 2013 Clause no. -
Metal Casting and Welding (17ME45A)
[METAL CASTING AND WELDING – 17M45-A] Metal Casting and Welding (17ME45A) Prepared by: Prof. Sachin S Pande Dept of Mechanical Engineering, SECAB I E T-586109 Page 1 [METAL CASTING AND WELDING – 17M35-A] METAL CASTING AND WELDING [AS PER CHOICE ASED CREDIT SYSTEM (CBCS) SCHEME] SEMESTER – III Subject Code 17 ME 35 A IA Marks 20 Number of Lecture Hrs / Week 04 Exam Marks 80 Total Number of Lecture Hrs 50 Exam Hours 03 CREDITS – 04 COURSE OBJECTIVE 1) To provide detailed information about the moulding processes. 2) To provide knowledge of various casting process in manufacturing. 3) To impart knowledge of various joining process used in manufacturing. 4) To provide adequate knowledge of quality test methods conducted on welded and casted components. MODULE -1 INTRODUCTION & BASIC MATERIALS USED IN FOUNDRY Introduction: Definition, Classification of manufacturing processes. Metals cast in the foundry-classification, factors that determine the selection of a casting alloy. Introduction to casting process & steps involved. Patterns: Definition, classification, materials used for pattern, various pattern allowances and their importance. Sand molding: Types of base sand, requirement of base sand. Binder, Additives definition, need and types Preparation of sand molds: Molding machines- Jolt type, squeeze type and Sand slinger. Study of important molding process: Green sand, core sand, dry sand, sweep mold, CO2 mold, shell mold, investment mold, plaster mold, cement bonded mold.Cores: Definition, need, types. Method of making cores, concept of gating (top, bottom, parting line, horn gate) and risering (open, blind) Functions and types. 10 hours MODULE -2 MELTING & METAL MOLD CASTING METHODS Melting furnaces: Classification of furnaces, Gas fired pit furnace, Resistance furnace, Coreless induction furnace, electric arc furnace, constructional features & working principle of cupola furnace. -
Exoweld Instruction Manual Digital
INSTRUCTION MANUAL A guide for the safe use of exothermic connections AN EASY GUIDE TO MAKING EXOTHERMIC CONNECTIONS The parameters and criteria set out in this handbook are based on the experience gained over the years of using Exoweld© products for installation work, as well as our ongoing research and development at our manufacturing plant, to develop better exothermic technology. The exothermic welding process is a simple, This bond will not loosen over time or deteriorate self-contained method of forming high quality with age. The connection’s current carrying electrical connections. The compact process capability is to that which it is being connected. In requires no external power or heat source, making other words, there is no increase in resistance in it completely portable. an exothermically welded connection as there is in most pressure connections. Connections are made inside a semi-permanent graphite mould, using the high temperature The majority of exothermic connections have at reaction of powdered copper oxide and aluminium. least twice the cross sectional area of the conductors being joined, and an equivalent or An exothermic connection is actually a molecular greater current carrying capacity. Because the bond formed between two metals such as connection is a fusion of high conductivity, high copper to copper, copper to steel and steel to copper content alloy, it will withstand repeated steel. Copper oxide and aluminium are combined fault currents, and will not loosen in the way that and ignited. The result is an exothermic reaction mechanical connections can. that produces molten, super-heated copper and aluminium oxide slag. -
Section 051200
Security Upgrade Contract # 2009-1117 SECTION 05 12 00 - STRUCTURAL STEEL FRAMING PART 1 - GENERAL 1.1 SUMMARY A. Section Includes: 1. Structural steel. 1.2 DEFINITIONS A. Structural Steel: Elements of structural-steel frame, as classified by AISC 303, "Code of Standard Practice for Steel Buildings and Bridges." 1.3 SUBMITTALS A. Shop Drawings: Show fabrication of structural-steel components. 1. Include details of cuts, connections, splices, camber, holes, and other pertinent data. 2. Include embedment drawings. 3. Indicate welds by standard AWS symbols, distinguishing between shop and field welds, and show size, length, and type of each weld. Show backing bars that are to be removed and supplemental fillet welds where backing bars are to remain. 4. Indicate type, size, and length of bolts, distinguishing between shop and field bolts. B. Paint Compatibility Certificates: From manufacturers of topcoats applied over shop primers, certifying that shop primers are compatible with topcoats. C. Mill test reports for structural steel, including chemical and physical properties. 1.4 QUALITY ASSURANCE A. Welding Qualifications: Qualify procedures and personnel according to AWS D1.1/D1.1M, "Structural Welding Code - Steel." B. Comply with applicable provisions of the following specifications and documents: 1. AISC 360. 2. RCSC's "Specification for Structural Joints Using ASTM A 325 or A 490 Bolts." 1.5 DELIVERY, STORAGE, AND HANDLING A. Store materials to permit easy access for inspection and identification. Keep steel members off ground and spaced by using pallets, dunnage, or other supports and spacers. Protect steel members and packaged materials from corrosion and deterioration. 1. Do not store materials on structure in a manner that might cause distortion, damage, or overload to members or supporting structures. -
Iron, Steel and Swords Script
Riveting, Soldering and Welding Plus Gluing and Screwing Joining in General So you have all kinds of steel pieces but not yet the object you want to make from that steel. Forging and casting can do a lot, but you can neither forge a big ship or a mechanical watch from a piece of steel, nor can you cast it. You must join your pieces, and joining is a major part of Materials Engineering. It is also a difficult part of Materials Engineering, even if we do not consider joined systems with moveable parts like gear wheels. If you think about it for a second, without joining you can't get very far. Even your flintstone arrow tip or axe head needed to be joined to the arrow shaft or some handle. While joining is obviously quite important for making all kinds of products, it is not clamorous and never easy. Non-metals you can join by simple means like sowing, tying with thread or twine or nailing. The ancient Egyptians actually sowed their large wooden boats together. But with wood you can also use nails (if you know how to make Illustration them) and the not-so-ancient Vikings indeed nailed their boats together. You use mortar for joining bricks and stones. This would be a huge topic by itself and I just mention it to point out that there are many ways for joining materials in general. So let's get a bit less general. In what follows I restrict myself mainly to the joining of metals. The major techniques available for joining are: Screwing (the metal) Riveting Welding Soldering Gluing Before I go onto details, let's ask ourselves a general question: What kind of mechanical properties can we expect from joined materials? To get a first idea, we simply imagine doing a tensile test on an "ideal" joined specimen like this Tensile Test for Joints The two joined metals might be of the same kind or of a different kind. -
Exothermicwelding Catalog
EXOTHERMICWELDING CATALOG Amiable Impex are the Manufacturer for Copper Bonded Rod and Importer, Supplier and Distributor of Exothermic Weld Powder and Accessories. We provide high quality Exothermic Weld Powder at reasonable rate with quickest lead time and fast response time. Amiable Impex was formedby 1) Mr. Ujjwal Shah (Having Experience of more than 15 years in Electrical Markets) Amiable Impex was founded with the goal of being at the forefront in the Electrical Metal Industry in both India and overseas for Copper Bonded Earth Rods and Exothermic Weld Powder and Accessories. Since our foundation, the company has grown through continuous development. As a company, Amiable always strives to set its own agenda, rather than pursuing the business as a follower of existing market leader. Our Style of work is unique which always suits our Customer. We believe in giving Quality Product in Quality Service at Goodprice. Amiable Impex endeavor to be a "more dynammic and competitive company" in order to respond appropriately to increasingly sophisticated and diverse customer requirements, and to provide superior value-added products through our innovation. We have very actively engaged in R&D activities to further improve of our product reliability and performance. Ourvision We have set the four pillars of our vision which set out the long term direction for our company Amiable Impex where we want to go and how we are going to get there: We work to create a better future every day. We help our customers feel good, have good and get more out of life with our brands and services that are good for them and good for others.