US5395981.Pdf
Total Page:16
File Type:pdf, Size:1020Kb
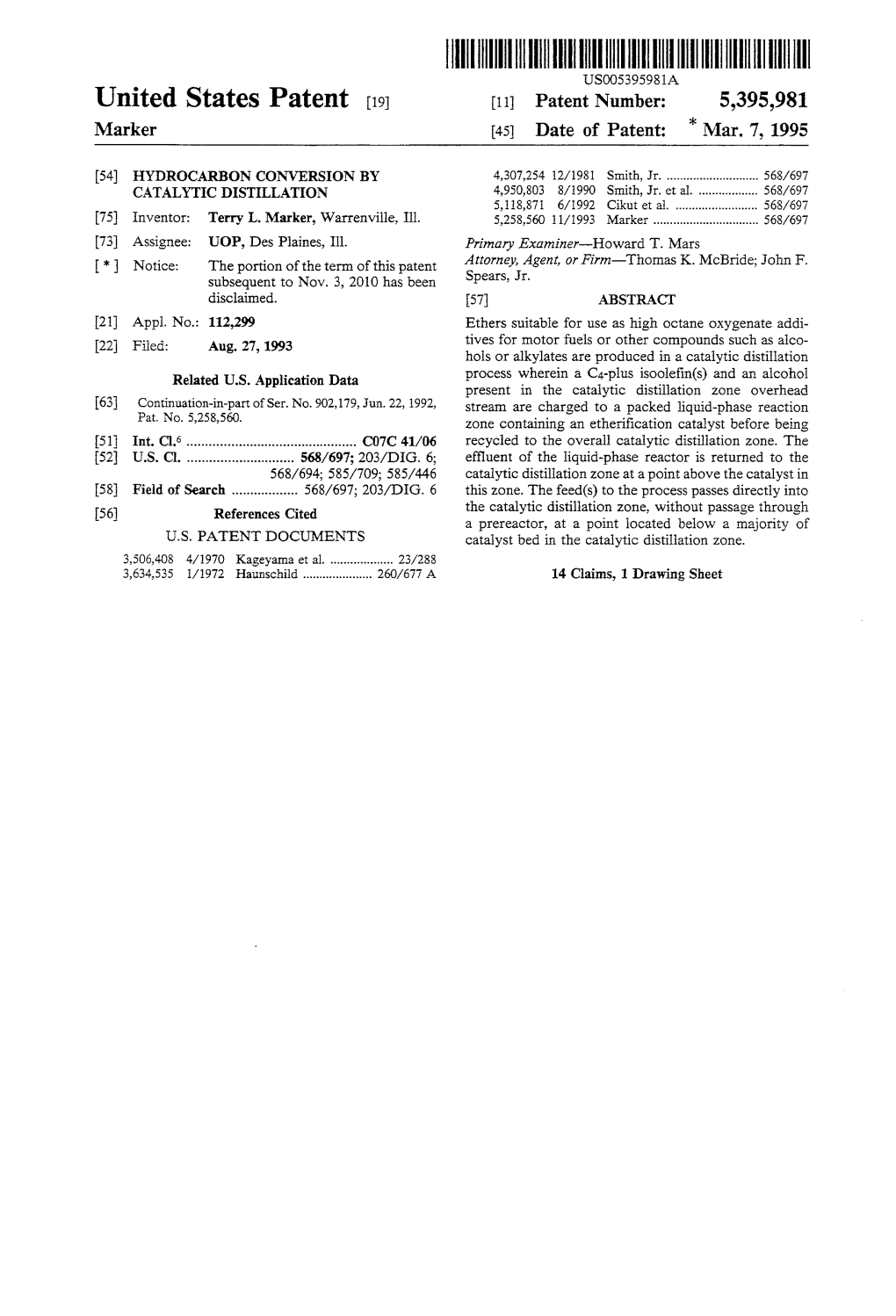
Load more
Recommended publications
-
Scale-Up of Reactive Distillation Columns with Catalytic Packings
SCALE-UP OF REACTIVE DISTILLATION COLUMNS WITH CATALYTIC PACKINGS Achim Hoffmann, Christoph Noeres, Andrzej Górak Department of Chemical Engineering, Dortmund University, 44221 Dortmund, Germany ABSTRACT The scale-up of reactive distillation columns with catalytic packings requires the knowledge of reaction kinetics, phase equilibrium and packing characteristics. Therefore, pressure drop, liquid holdup and separation efficiency have been determined for the catalytic packing MULTIPAK®. A new hydrodynamic model that describes the counter-current gas-liquid flow for the whole loading range and considers the influence of the column diameter has been implemented into a rate- based column model. Simulation results for the methyl acetate synthesis are compared with pilot plant experiments that cover a wide range of different process conditions. The experiments are in good agreement with the simulation results and confirm the applicability of the modelling approach for reactive distillation processes with catalytic packings. INTRODUCTION The combination of heterogeneously catalysed reaction and separation in one single process unit, known as catalytic distillation, is one of the most common applications of the multifunctional reactor concept [1]. In comparison to the conventional approach, where reaction and separation are carried out sequentially, catalytic distillation can considerably improve the process performance [2,3]. One of the advantages is the elimination of equipment for product recovery and recycling of unconverted reactants, which leads to savings in investment and operating costs. Catalytic distillation may also improve selectivity and mass transfer and avoid catalyst fouling [4]. Even if the invention of catalytic distillation dates back to 1966 [5], the number of processes in which catalytic distillation has been implemented on a commercial scale is still quite limited but the potential of this technique goes far beyond today’s applications [6]. -
NONLINEAR MODEL PREDICTIVE CONTROL of a REACTIVE DISTILLATION COLUMN by ROHIT KAWATHEKAR, B.Ch.E., M.Ch.E. a DISSERTATION IN
NONLINEAR MODEL PREDICTIVE CONTROL OF A REACTIVE DISTILLATION COLUMN by ROHIT KAWATHEKAR, B.Ch.E., M.Ch.E. A DISSERTATION IN CHEMICAL ENGINEERING Submitted to the Graduate Faculty of Texas Tech University in Partial Fulfillment of the Requirements for the Degree of DOCTOR OF PHILOSOPHY Approved Chairperson of the ConrnuS^ Accepted bean of the Graduate School May, 2004 ACKNOWLEDGEMENTS I am blessed with all nice people around me through out my life. While working on research project for past four years, many people have influenced my life and my thought processes. It is almost an impossible job to acknowledge them in a couple of pages or for that matter in limited number of words. I would like to express my sincere thanks to my advisor Dr. James B. Riggs for his financial support, guidance, and patience throughout the project. I would like to express my thanks to Dr. Karlene A. Hoo for her valuable graduate-level courses in the area of process control as well as for her guidance as a graduate advisor. I would also like to thank Dr. Tock, Dr, Leggoe, and Dr. Liman for being a part of my dissertation committee. My sincere thanks to Mr. Steve Maxner, my employer at the Vietnam Archive, for providing me the financial support during my last years of curriculum. I would like to take this opportunity to thank all the staff members and colleagues at Vietnam Archive for making me a part of their organization. A person, without her, this accomplishment would have been incomplete, is my wife, Gouri (Maaoo). -
345, 346, 349 Acid-Catalysed Dehydrat
733 Index a ALPO-18 catalyst 188, 280 ab initio calculations 377, 411, 412 aluminophosphate MeAPO-36 382 aberration-corrected electron microscopy aluminosilicates 382 (AC-TEM) 345, 346, 349 ammonia acid-catalysed dehydration 8 – absorption tower 585 –fructose 9,10 – adsorbed nitrogen 575, 576 acid-catalysed esterification 17 – Badische Anilin und Soda Fabrik (BASF) acrolein 690, 692 laboratories 569 acrylic acid 690 – BASF catalyst S6-10 570, 574 acrylonitrile 688–690 –CO2 removal 585 activation energy, chemisorption 101–104 – and copper catalyst 585 acyclic diene metathesis (ADMET) 413 – crystalline α-Fe phase 574 adiabatic reactors 516–518 – ex situ X-ray diffraction studies 574 adipic acid 697, 698, 700 – Fe catalysts 570 adsorbate 67 – high-temperature treatment 573 adsorption – in situ X-ray powder diffractometric studies – clean solids 71–74 574 –definition 67 – methanation 585 – energetics 113–126 – methane 585 – heterogeneous reactions 132–140, –N2 fixation 568 142–147, 151 – natural gas 583 – isotherms and isobars 79–88, 90–101 – nitrogen-containing compounds 568 – isotherms, kinetic principles 105–113 – oxidation 588–592 – microkinetics 147, 148, 152–154 – potassium 582 – mobility 126, 127 – potential-energy diagram 580 – ordered adlayers 74–76, 79 – primary reforming furnace 583 – physical, chemisorptions and precursor – process streams 585 states 67–70 – production 569 – surface reactions 127–129, 131, 132 – promoted iron catalyst composition 573 AES analysis see Auger electron spectroscopic – promoters 570 (AES) analysis 573 – reactor configurations 585–588 affinity coefficient 111 – reforming reactions 583 agostic interactions 49, 51 – Ru-based catalysts 570 Al2O3/CeO2/noble metal 385 – shift converters 583 algae biofuel challenge 13 – steam-reforming reactions 583 Algenol 13 – surface hydrogen 578–580 alkaline-earth oxides 430 – surface nitride 576–578 ALPO structure 384 – synthesis reactor 649 Principles and Practice of Heterogeneous Catalysis, Second Edition. -
Energy Technology Solutions
Welcome Dear Stakeholder, The economic challenges facing American industry today highlight the critical need Innovation is vital for innovative technology solutions that will increase productivity, sustainability, and competitiveness. At the Industrial Technologies Program (ITP), we work to to economic and identify promising innovations and accelerate their progress through the research and development pipeline. All of us at ITP are pleased to present this overview of environmental technologies from our research partnerships. sustainability in Partnership is key to our success. Our industrial partners help us identify and U.S. industry. pursue technology research opportunities that are too risky for industry to undertake alone —yet promise broad benefits across the manufacturing sector. This partnership approach has succeeded year after year in providing industry with technologies, tools, and practices to save energy and stimulate growth. Our products are actively making a difference by helping U.S. companies succeed in tough global markets. Since ITP’s inception, the program and its partners have successfully launched 220 new, energy-effi cient technologies and received 51 R&D 100 Awards. Collectively, these technologies and other program activities have cut carbon emissions by 206 million tons and saved 9.3 quadrillion British thermal units (Btu). We are proud to be serving American industry under the guidance of the U.S. Department of Energy’s (DOE’s) Offi ce of Energy Effi ciency and Renewable Energy. We invite you to learn more about -
United States Patent (19) [11] Patent Number: 4,978,807 Smith, Jr
United States Patent (19) [11] Patent Number: 4,978,807 Smith, Jr. (45) Date of Patent: Dec. 18, 1990 54 METHOD FOR THE PREPARATION OF 4,302,356 11/1981 Smith, Jr. ............................ 252A26 METHYL TERTARY BUTYLETHER E;e's Wy 2. : St.mith, Jr.im. ............................ :: 75) Inventor: Lawrence A. Smith, Jr., Bellaire, Tex. 4,439,350 3/1984 Jones, Jr. ............................ 502/527 e 4,443,559 4/1984 Smith, Jr. ............................ 502/527 73) Assignee: Chemical Rach & Licensing 4,475,005 10/1984 Paret ................................... 568/697 Company, Houston, Tex. 4,482,775 11/1984 Smith, Jr. ............................ 585/671 21 Appl. No.: 373,232 4,847,430 7/1989 Quang et al. ........................ 568/697 4,847,431 7/1989 Nocca et al. ........................ 568/197 22 FiledFiled: Jun . 29, 1989 Primary Examiner-Howard T. Mars Related U.S. Application Data Attorney, Agent, or Firm-Kenneth H. Johnson 62) Division of Ser. No. 328,487, Mar. 23, 1989. 57 ABSTRACT 51) Int. Cl. C07C 41/06 A method and apparatus for conducting a catalytic Yake a v on a a pae ea ao or so woo as we so as swo see was no as a O distillation process is provided which allows for main 52 U.S. C. ....................................203/DIG. 568/697; 6; 568/694;585/468 taining a liquid level in selected portions of the catalyst 58) Field of search.......sgs/697 bed.duction Three of methylparticular tertiary processes butyl disclosed ether, tertiary are the butyl pro (56) References Cited alcohol and cumene. A method for the production of U.S. PATENT DOCUMENTS methyl tertiary butyl ether by reaction of isobutene with methanol in a distillation reaction column is dis 4,089,752 5/1978 Hancock... -
Catalytic Distillation (CD) - Outline
Modern Methods in Heterogeneous Catalysis Research Fritz Haber Institute, Berlin, 14 November 2003 CatalyCatalytictic DistillationDistillation Kai Sundmacher1,2 1 Max-Planck-Institute for Dynamics of Complex Technical Systems Sandtorstraße 1, 39106 Magdeburg, Germany 2 Otto-von-Guericke-University Magdeburg, Process Systems Engineering Universitätsplatz 2, 39106 Magdeburg, Germany [email protected] Catalytic Distillation (CD) - Outline 3 Catalysts for Use in CD Processes 4 Modelling, Simulation, Experimental Validation 2 Fields of Application, CD Lecture Process Examples 5 Operational Process Behaviour 1 Basic Principles of CD CD Expert ! Modern Methods in Heterogeneous Catalysis Research Fritz Haber Institute, Berlin, 14 November 2003 Integration of Unit Operations in Multifunctional Reactors Raw Materials Main Products Recycle Physical Chemical/ Separation Separation Unit Biological Units for Units for Operations Units Reactants By-Products Multifunctional Multifunctional Reactors (e.g. Reactors (e.g. Fuel Cells) Reactive Mill) By-Products Multifunctional Reactors (Reactive Distillation / Absorption / Extraction / Adsorption Column) Possible Benefits from Multifunctional Reactor Concepts Synergetic interactions of chemical and physical unit operations may lead to: á increase of productivity from process intensification á increase of selectivity of reactions and/or separations á reduction of by-products and waste materials á more efficient (in situ) use of energy á inherent safety á improved environmental compatibility -
Novel Catalytic Reactive Distillation Processes for a Sustainable Chemical Industry
Topics in Catalysis https://doi.org/10.1007/s11244-018-1052-9 ORIGINAL PAPER Novel Catalytic Reactive Distillation Processes for a Sustainable Chemical Industry Anton A. Kiss1,2 © The Author(s) 2018 Abstract Reactive distillation (RD) is a great process intensification concept taking advantage of the synergy created when combin- ing (catalyzed) reaction and separation into a single unit, which allows the concurrent production and removal of products. This feat improves the productivity and selectivity, reduces the energy usage, eliminates the need for solvents, and leads to highly-efficient systems with improved sustainability metrics (e.g. less waste and emissions). This paper provides an over- view of the key features of RD processes, with emphasis on novel catalytic/reactive distillation processes that can make a difference at large scale and pave the way for a more sustainable chemical process industry that is more profitable, safer and less polluting. These examples include the production of: acrylic and methacrylic monomers, unsaturated polyesters resins, di-alkyl ethers, fatty esters, as well as other short alkyl esters (e.g. by enzymatic reactive distillation). The main drivers for such new RD applications are: economical (large reduction of costs and energy use), environmental (lower CO 2 emissions, no or reduced waste) and social (improved safety and health due to lower reactive content, reduced footprint and run away sensitivity). Hence RD technology strongly contributes to all three pillars of sustainability in the chemical process industry. Nonetheless, the potential of RD technology has not been fully tapped yet, and there is still undergoing research to improve it further by various means: e.g. -
Appendix 1 Pi Technologies Description and Review European Roadmap for Process Intensification Appendix 1 Appendix 1 European Roadmap for Process Intensification
Appendix 1 pi technologies description and review european roadmap for process intensification Appendix 1 Appendix 1 european roadmap for process intensification Introduction The state-of-the-art of PI worldwide has being identified through questionnaires to 70 experts, identifying patents (approximately 1,000), and a complete search for scientific publications including translation of Chinese and Japanese work. 72 PI technologies have been identified, of which 46 technologies have been described by globally-acknowledged experts in full “technology reports”. A description of these 72 technologies, and a review of the 46 reports by three Dutch experts can be found in this Appendix 1. Details are kept in a dedicated database which can be accessed through TU Delft and ECN. The 72 PI technologies are briefly described and illustrated here. For the 46 technologies for which a full “technology report” is available, a review has been prepared by the Review Panel, consisting of 3 Dutch process technology experts, Jacob Moulijn, Fons Meijs and Ben Stouthamer. The technologies that have not been reviewed by no means have a lower potential than those reviewed. Due to lack of resources and time constraints, it was not possible to finalize technology reports for all 72 technologies. The review panel has considered the potential benefits (energy efficiency, CO2 emission, etc.) of each technology only within the boundary of the process step in which it can be potentially implemented; benefits elsewhere in the process chain lie outside the scope of consideration. -
Real-Time Optimizing Nonlinear Control Applied to a Continuous Reactive Distillation Process
Preprints of the 18th IFAC World Congress Milano (Italy) August 28 - September 2, 2011 Real-Time Optimizing Nonlinear Control Applied to a Continuous Reactive Distillation Process Elrashid Idris ∗ Sebastian Engell ∗∗ ∗ Faculty of Bio-Chemical & Chemical Engineering, TU-Dortmund, 44227 Dortmund, Germany, ([email protected]). ∗∗ Faculty of Bio-Chemical & Chemical Engineering, TU-Dortmund, 44227 Dortmund, Germany, ([email protected]). Abstract: Chemical processes are usually operated under feedback control of critical operating conditions to maintain process safety, product quality and economic performance. Increasingly, linear model predictive is applied to these coupled multivariable control problems and in some cases the reference values are adapted infrequently by an optimization based as a rigorous nonlinear stationary plant model (RTO). However, in between these optimizations that plant may operate suboptimally due to the presence of disturbances. In recent years, it has been proposed to use nonlinear model-based optimization of the available degrees of freedom of a process over a finite moving horizon to integrate set-point optimization and feedback control (for a survey see Engell (2007)). In this paper we demonstrate the feasibility and the potential of the optimizing nonlinear control for a challenging example, a reactive distillation column. The performance of the controller is an economics-driven response since the profit function represents the main part of the objective criterion while the quality specifications as well as the physical limitations of the process were incorporated as optimization constraints. A performance comparison between the tracking controller and the optimizing nonlinear controller is also shown. Keywords: Reactive distillation, Non-linear model predictive control, Non-minimum phase behavior, Tracking and optimizing control, Static gain sign change. -
Simulation Study of a Reactive Distillation Process for the Ethanol Production J
A publication of CHEMICAL ENGINEERING TRANSACTIONS VOL. 69, 2018 The Italian Association of Chemical Engineering Online at www.aidic.it/cet Guest Editors: Elisabetta Brunazzi, Eva Sorensen Copyright © 2018, AIDIC Servizi S.r.l. ISBN 978-88-95608-66-2; ISSN 2283-9216 Simulation Study of a Reactive Distillation Process for the Ethanol Production J. Carlos Cárdenas-Guerraa,*, Susana Figueroa-Gerstenmaiera, J. Antonio Reyes- Aguileraa, Salvador Hernándezb aDepartamento de Ingenierías Química, Electrónica y Biomédica, Universidad de Guanajuato, Loma del Bosque No. 103, León, Gto., 37150, México bDepartamento de Ingeniería Química, Universidad de Guanajuato, Noria Alta s/n, Guanajuato, Gto., 36050, México [email protected] A simulation study of the effects of design and operating parameters under which optimal-stable steady states may occur in a reactive distillation process for synthesis of ethanol has been presented. The conceptual design of the reactive separation process is based on the element concept where the reactive driving force approach is employed. To validate the proposed design, steady state simulations using ASPEN PLUS® software package were accomplished, and a sensitivity analysis was done to establish the operating conditions of the process. The analysed parameters were as follows: i) the operating pressure and ii) the reflux ratio. The results showed that a new energy-efficient design with minimal energy requirements may be considered a viable technological alternative for ethanol synthesis. Also, this reaction-separation process allows to satisfy the design and operating constrains. This is, a novel reactive distillation process capable to increase the purity of the ethanol from a dilute solution, i.e., up to 30% ethanol in water under optimal operating conditions. -
Design and Application of a Catalytic Distillation Column
CATALYTIC DISTILLATION DESIGN AND APPLICATION OF A CATALYTIC DISTILLATION COLUMN by JOSIAS JAKOBUS (JAKO) NIEUWOUDT Thesis presented in partial ful…lment of the requirement for the Degree of MASTER OF SCIENCE IN ENGINEERING (CHEMICAL ENGINEERING) in the Department of Process Engineering at the UNIVERSITY OF STELLENBOSCH in co-operation with the UNIVERSITY OF CAPE TOWN CATALYSIS RESEARCH UNIT in the Department of Chemical Engineering SUPERVISORS University of Stellenbosch Dr. L.H. CALLANAN University of Cape Town A/Prof. K.P. MöLLER GRADUATION DATE DECEMBER 2005 i DECLARATION I, the undersigned, hereby declare that the work contained in this thesis is my own original work and that I have not previously in its entirety or in part submitted it at any university for a degree. __________________ 16th May 2005 J.J. Nieuwoudt Date ii iii SUMMARY Catalytic Distillation (CD) is a hybrid technology that utilizes the dynamics of si- multaneous reaction and separation in a single process unit to achieve a more compact, economical, e¢ cient and optimized process design when compared to the traditional multi-unit designs. The project goal (and key question) is (how) to design a cost-e¤ective, simple and accurate laboratory-scale continuous CD system that will su¢ ciently and accurately supply useful data for model validation. The system to be investigated is the continuous hydrogenation of an -ole…n C6 (1-hexene) feed stream to the corresponding alkane (n-hexane) product with simultaneous reactant/product separation. Hypothetically, a system can be constructured to determine whether hydrogenation will bene…t from the heat and mass transfer integration observed under CD conditions in terms of energy usage, temperature control and the catalyst’ssurface hydrogen concentration. -
Cyclic Distillation Technology - a New Challenger in Fluid Separations
823 A publication of CHEMICAL ENGINEERING TRANSACTIONS VOL. 69, 2018 The Italian Association of Chemical Engineering Online at www.aidic.it/cet Guest Editors: Elisabetta Brunazzi, Eva Sorensen Copyright © 2018, AIDIC Servizi S.r.l. ISBN 978-88-95608-66-2; ISSN 2283-9216 DOI: 10.3303/CET1869138 Cyclic Distillation Technology - A New Challenger in Fluid Separations Anton A. Kissa,b,*, Vladimir N. Maletac aThe University of Manchester, School of Chemical Engineering and Analytical Science, Centre for Process Integration, Sackville Street, The Mill, Manchester M13 9PL, United Kingdom b University of Twente, Sustainable Process Technology, PO Box 217, 7500 AE Enschede, The Netherlands c Maleta Cyclic Distillation LLC OÜ, Parnu mnt 130-38, 11317 Tallinn, Estonia [email protected] This paper provides a dual academic and industrial view on cyclic distillation. The cyclic mode of operation is based on separate phase movement (SPM) that can be achieved with specific internals. This leads to major advantages: increased column throughput, reduced energy requirements, and better separation performance (exceeding 200% Murphree efficiency). Next to the substantial theoretical developments in terms of process modeling and simulation, there have been also significant advances in the practical demonstration at pilot and large scale. All this contributed to a better understanding of the design, control and optimization of cyclic distillation processes, and to the development of more robust industrial solutions. The application range is now expanding to other areas, such as: oil refining, chemistry, petro-chemistry, pharmaceutics, biofuels and others. 1. Introduction Although considered by many professionals a mature field, distillation has enjoyed during the past decades a number of major enhancements based on process intensification: e.g.