Analysis Results of Micro-Particles Captu
Total Page:16
File Type:pdf, Size:1020Kb
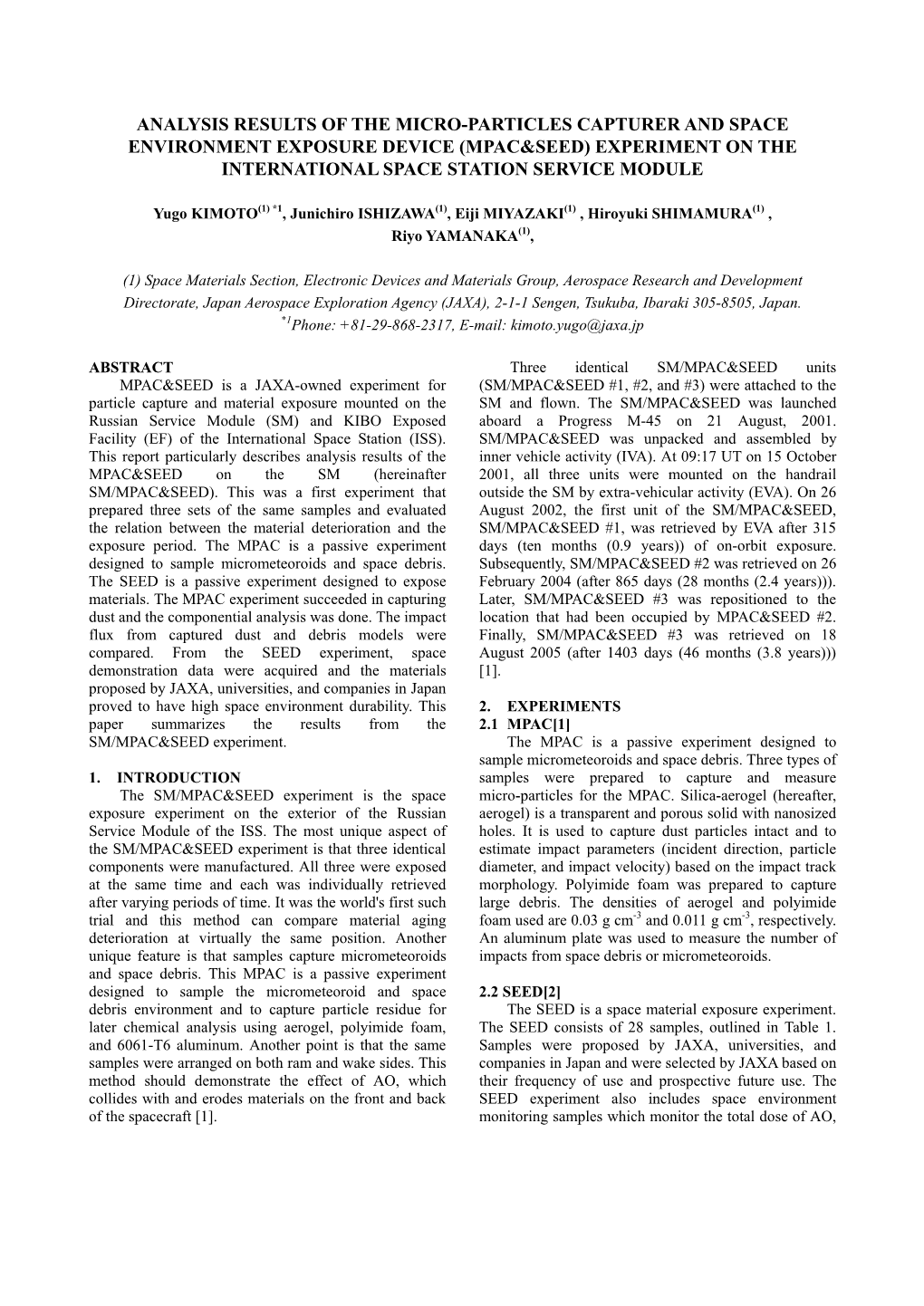
Load more
Recommended publications
-
Corporate Profile
2013 : Epsilon Launch Vehicle 2009 : International Space Station 1997 : M-V Launch Vehicle 1955 : The First Launched Pencil Rocket Corporate Profile Looking Ahead to Future Progress IHI Aerospace (IA) is carrying out the development, manufacture, and sales of rocket projectiles, and has been contributing in a big way to the indigenous space development in Japan. We started research on rocket projectiles in 1953. Now we have become a leading comprehensive manufacturer carrying out development and manufacture of rocket projectiles in Japan, and are active in a large number of fields such as rockets for scientific observation, rockets for launching practical satellites, and defense-related systems, etc. In the space science field, we cooperate with the Japan Aerospace Exploration Agency (JAXA) to develop and manufacture various types of observational rockets named K (Kappa), L (Lambda), and S (Sounding), and the M (Mu) rockets. With the M rockets, we have contributed to the launch of many scientific satellites. In 2013, efforts resulted in the successful launch of an Epsilon Rocket prototype, a next-generation solid rocket which inherited the 2 technologies of all the aforementioned rockets. In the practical satellite booster rocket field, We cooperates with the JAXA and has responsibilities in the solid propellant field including rocket boosters, upper-stage motors in development of the N, H-I, H-II, and H-IIA H-IIB rockets. We have also achieved excellent results in development of rockets for material experiments and recovery systems, as well as the development of equipment for use in a space environment or experimentation. In the defense field, we have developed and manufactured a variety of rocket systems and rocket motors for guided missiles, playing an important role in Japanese defense. -
Accomplishments Brochure for Printers
Foreword The Global Energy and Water Cycle Experiment (GEWEX) of the World Climate Research Programme (WCRP), sponsored by the World Meteorological Organization (WMO), the International Council for Science (ICSU), and the Intergovernmental Oceanographic Commission (IOC) of the United Nations Educational, Scientific and Cultural Organization (UNESCO), has amassed an out- standing record of accomplishments during the first phase of its planned program. From bringing hydrology, land surface, and atmospheric sciences communities together, to showing the impor- tance of understanding soil moisture/atmosphere and cloud/radiation interactions and their param- eterization within prediction models, GEWEX has been on the leading edge of science since its inception. Pulling together the global data sets necessary for validation of our predictive models and fostering direct applications with water resources user groups have also provided significant advances in climate research. This brochure provides just a sample of the numerous accomplishments that GEWEX has achieved during its build-up phase (Phase I). This prepares the stage for many more advances in Phase II, when the community will exploit the new fleet of environmental satellites and build upon the newly implemented model upgrades developed in Phase I. The authors would like to recognize the very critical support of national agencies in making this program possible. Although the list is very long, special recognition must be given to the U.S. National Aeronautics and Space Administration (NASA), the U.S. National Oceanic and Atmospheric Administration (NOAA), the Japan Aerospace Exploration Agency (JAXA), the Japanese Meteoro- logical Agency (JMA), the European Organization for the Exploitation of Meteorological Satellites (EUMETSAT), Meteo France, the German Association of Natural Resources, the European Space Agency (ESA), the European Community, the Meteorological Service of Canada, and the Natural Sciences and Engineering Research Council of Canada (NSERC). -
Hdtv) on Board Selene (Kaguya)
40th Lunar and Planetary Science Conference (2009) 2540.pdf RESULTS OF HIGH-DEFINITION TELEVSION SYSTEM (HDTV) ON BOARD SELENE (KAGUYA) . R. Honda1, J. Yamazaki2, S. Mitsuhashi2, J. Tachino3 , M. Yamauchi4, M. Shirao5, 1Kochi University, Akebono-cyo 2-5-1, Kochi, JAPAN, 780-8520 ([email protected]) , 2 NHK (Japan Broadcasting Corporation), 3 NHK En- gineering Service, 4 NHK Mito Broadcasting Station, 5Planetary Geological Society of Japan Introduction: High Definition Television System Imaging of the full Earth : HDTV’s primary ob- ( HDTV) on board KAGUYA/SELENE is the camera jective is to obtain the moving images of the “full” system composed of a wide angle camera (HDTV- Earth rising from the lunar horizon and setting to the WIDE) and a telephoto camera (HDTV-WIDE), that lunar horizon. We have succeeded in the acquisition aims to acquire the moving images of the moon and of these images on April 5 th and September 30 th in the Earth from the moon for the public outreach and 2008. Figure 2 shows a snapshot extracted from the the broadcasting. HDTV has succeeded in obtaining moving images of the full Earth rise from the lunar the moving images of the Earth rising from the moon South Pole obtained by HDTV-TELE on April 5th, and setting to the lunar horizon and other prominent 2008. These moving images are taken at the smallest features on the lunar surface. The data obtained frame rate among the four frame rates of 30fps, 15fps, amounts to 1.37 GB as of the end of November, 2008, 7.5dps, and 3.75fps . -
Securing Japan an Assessment of Japan´S Strategy for Space
Full Report Securing Japan An assessment of Japan´s strategy for space Report: Title: “ESPI Report 74 - Securing Japan - Full Report” Published: July 2020 ISSN: 2218-0931 (print) • 2076-6688 (online) Editor and publisher: European Space Policy Institute (ESPI) Schwarzenbergplatz 6 • 1030 Vienna • Austria Phone: +43 1 718 11 18 -0 E-Mail: [email protected] Website: www.espi.or.at Rights reserved - No part of this report may be reproduced or transmitted in any form or for any purpose without permission from ESPI. Citations and extracts to be published by other means are subject to mentioning “ESPI Report 74 - Securing Japan - Full Report, July 2020. All rights reserved” and sample transmission to ESPI before publishing. ESPI is not responsible for any losses, injury or damage caused to any person or property (including under contract, by negligence, product liability or otherwise) whether they may be direct or indirect, special, incidental or consequential, resulting from the information contained in this publication. Design: copylot.at Cover page picture credit: European Space Agency (ESA) TABLE OF CONTENT 1 INTRODUCTION ............................................................................................................................. 1 1.1 Background and rationales ............................................................................................................. 1 1.2 Objectives of the Study ................................................................................................................... 2 1.3 Methodology -
Status of GCOM-W and GOSAT-GW/AMSR3
The Advanced Microwave Scanning Radiometer 3 (AMSR3) Updates Misako Kachi, Hideyuki Fujii (JAXA Earth Observation Research Center) Marehito Kasahara, Kazuya Inaoka, Yasushi Kojima (JAXA GOSAT-GW Project Team) JAXA’s Earth Observation Satellite/Instrument Targets (JFY: Apr-Mar) 2014 2015 2016 2017 2018 2019 2020 2021 2022 2023 2024 2025 Disasters & Resources [Land and disaster monitoring] [Land and disaster monitoring] JERS1/OPS, SAR (1992-1998) ALOS-2 / PALSAR-2 ALOS-4/Advanced SAR ADEOS-I/AVNIR [Land and disaster monitoring] ALOS/AVNIR2, PALSAR (2006-2011) ALOS-3/Advanced Optical Climate System TRMM / PR [Precipitation 3D structure] with NASA •Water Cycle GPM / DPR ADEOS-II/AMSR (2003) with NASA [Wind, SST , water vapor, Aqua/AMSR-E (2002-2011 ) [Wind, SST , water vapor, rainfall] precipitation] GCOM-W / AMSR2 GOSAT-GW/AMSR3 •Climate change [Vegetation, aerosol, cloud, SST, ocean color] ADEOS-I/OCTS (1996-1997) GCOM-C / SGLI ADEOS-II/GLI (2003) [Cloud and aerosol 3D structure] EarthCARE / CPR with ESA [CO2, CH4] [CO2, CH4, CO] GOSAT / FTS, CAI GOAT-GW/TANSO-3 •Greenhouse gases with MOE For MOE [CO2, CH4, CO] with MOE GOSAT-2 Mission status: Completed On orbit Development History of Passive Microwave Observations • With experience of development and operation of MSR, JAXA developed 1st generation of AMSR (AMSR and AMSR-E) with large antenna size and C-band channels. AMSR-E continuous its science observation about 9.5-year, and its high capabilities enable to expand utilizations in operational and research areas. • 2nd generation of AMSR (AMSR2) was launched in 2012 and succeeds AMSR-E observations to establish its data utilization in various areas. -
MIT Japan Program Working Paper 01.10 the GLOBAL COMMERCIAL
MIT Japan Program Working Paper 01.10 THE GLOBAL COMMERCIAL SPACE LAUNCH INDUSTRY: JAPAN IN COMPARATIVE PERSPECTIVE Saadia M. Pekkanen Assistant Professor Department of Political Science Middlebury College Middlebury, VT 05753 [email protected] I am grateful to Marco Caceres, Senior Analyst and Director of Space Studies, Teal Group Corporation; Mark Coleman, Chemical Propulsion Information Agency (CPIA), Johns Hopkins University; and Takashi Ishii, General Manager, Space Division, The Society of Japanese Aerospace Companies (SJAC), Tokyo, for providing basic information concerning launch vehicles. I also thank Richard Samuels and Robert Pekkanen for their encouragement and comments. Finally, I thank Kartik Raj for his excellent research assistance. Financial suppport for the Japan portion of this project was provided graciously through a Postdoctoral Fellowship at the Harvard Academy of International and Area Studies. MIT Japan Program Working Paper Series 01.10 Center for International Studies Massachusetts Institute of Technology Room E38-7th Floor Cambridge, MA 02139 Phone: 617-252-1483 Fax: 617-258-7432 Date of Publication: July 16, 2001 © MIT Japan Program Introduction Japan has been seriously attempting to break into the commercial space launch vehicles industry since at least the mid 1970s. Yet very little is known about this story, and about the politics and perceptions that are continuing to drive Japanese efforts despite many outright failures in the indigenization of the industry. This story, therefore, is important not just because of the widespread economic and technological merits of the space launch vehicles sector which are considerable. It is also important because it speaks directly to the ongoing debates about the Japanese developmental state and, contrary to the new wisdom in light of Japan's recession, the continuation of its high technology policy as a whole. -
1999 EOS Reference Handbook
1999 EOS Reference Handbook A Guide to NASA’s Earth Science Enterprise and the Earth Observing System http://eos.nasa.gov/ 1999 EOS Reference Handbook A Guide to NASA’s Earth Science Enterprise and the Earth Observing System Editors Michael D. King Reynold Greenstone Acknowledgements Special thanks are extended to the EOS Prin- Design and Production cipal Investigators and Team Leaders for providing detailed information about their Sterling Spangler respective instruments, and to the Principal Investigators of the various Interdisciplinary Science Investigations for descriptions of their studies. In addition, members of the EOS Project at the Goddard Space Flight Center are recognized for their assistance in verifying and enhancing the technical con- tent of the document. Finally, appreciation is extended to the international partners for For Additional Copies: providing up-to-date specifications of the instruments and platforms that are key ele- EOS Project Science Office ments of the International Earth Observing Mission. Code 900 NASA/Goddard Space Flight Center Support for production of this document, Greenbelt, MD 20771 provided by Winnie Humberson, William Bandeen, Carl Gray, Hannelore Parrish and Phone: (301) 441-4259 Charlotte Griner, is gratefully acknowl- Internet: [email protected] edged. Table of Contents Preface 5 Earth Science Enterprise 7 The Earth Observing System 15 EOS Data and Information System (EOSDIS) 27 Data and Information Policy 37 Pathfinder Data Sets 45 Earth Science Information Partners and the Working Prototype-Federation 47 EOS Data Quality: Calibration and Validation 51 Education Programs 53 International Cooperation 57 Interagency Coordination 65 Mission Elements 71 EOS Instruments 89 EOS Interdisciplinary Science Investigations 157 Points-of-Contact 340 Acronyms and Abbreviations 354 Appendix 361 List of Figures 1. -
Allocation of Commercial Space Industry Components 1
May 2018 Allocation of Commercial S pace Industry Components A Virtual Think Tank (ViTTa)® Report Deeper Analyses Clarifying Insights Better Decisions Produced in support of the Strategic Multilayer Assessment (SMA) Office (Joint Staff, J39) www.NSIteam.com Allocation of Commercial Space Industry Components 1 Authors Dr. Belinda Bragg Dr. Sabrina Pagano Please direct inquiries to Belinda Bragg at [email protected] ViTTa® Project Team Dr. Allison Astorino-Courtois Sarah Canna Nicole Peterson Executive VP Principal Analyst Analyst Weston Aviles Dr. Larry Kuznar George Popp Analyst Chief Cultural Sciences Officer Senior Analyst Dr. Belinda Bragg Dr. Sabrina Pagano Dr. John A. Stevenson Principal Research Scientist Principal Research Scientist Principal Research Scientist Interview Team1 Weston Aviles Nicole Peterson Analyst Analyst Sarah Canna George Popp Principal Analyst Senior Analyst What is ViTTa®? NSI’s Virtual Think Tank (ViTTa®) provides rapid response to critical information needs by pulsing our global network of subject matter experts (SMEs) to generate a wide range of expert insight. For this SMA Contested Space Operations project, ViTTa was used to address 23 unclassified questions submitted by the Joint Staff and US Air Force project sponsors. The ViTTa team received written and verbal input from over 111 experts from National Security Space, as well as civil, commercial, legal, think tank, and academic communities working space and space policy. Each Space ViTTa report contains two sections: 1) a summary response to the question asked; and 2) the full written and/or transcribed interview input received from each expert contributor organized alphabetically. Biographies for all expert contributors have been collated in a companion document. -
Motorcycles, Spares and Memorabilia Bicester Heritage | 14 - 16 August 2020
The Summer Sale | Live & Online Including The Morbidelli Motorcycle Museum Collection Collectors’ Motorcycles, Spares and Memorabilia Bicester Heritage | 14 - 16 August 2020 The Summer Sale | Live & Online Including The Morbidelli Motorcycle Museum Collection Collectors’ Motorcycles, Spares and Memorabilia Hangar 113, Bicester Heritage, OX26 5HA | Friday 14, Saturday 15 & Sunday 16 August 2020 VIEWING SALE NUMBER MOTORCYCLE ENQUIRIES CUSTOMER SERVICES In light of the current government 26111 ON VIEW AND SALE DAYS Monday to Friday 8:30am - 6pm guidelines and relaxed measures +44 (0) 330 3310779 +44 (0) 20 7447 7447 we are delighted to welcome CATALOGUE viewing, strictly by appointment. £30.00 + p&p ENQUIRIES Please see page 2 for bidder All the lots will be on view at Ben Walker information including after-sale Bicester Heritage in our traditional +44 (0) 20 8963 2819 collection and shipment Hangar 113. We will ensure social BIDS ENQUIRIES INCLUDING [email protected] distancing measures are in place, VIEW AND SALE DAYS Please see back of catalogue with gloves and sanitiser available +44 (0) 330 3310778 James Stensel for important notice to bidders for clients wishing to view [email protected] +44 (0) 20 8963 2818 motorcycle history files. Please [email protected] IMPORTANT INFORMATION email: motorcycles@bonhams. LIVE ONLINE BIDDING IS The United States Government com or call +44 (0) 20 8963 2817 AVAILABLE FOR THIS SALE Bill To has banned the import of ivory to book an appointment. Please email [email protected] +44 (0) 20 8963 2822 into the USA. Lots containing with “Live bidding” in the subject [email protected] ivory are indicated by the VIEWING TIMES line no later than 6pm the day symbol Ф printed beside the Wednesday 12 August before the relevant auction Andy Barrett lot number in this catalogue. -
Introduction of NEC Space Business (Launch of Satellite Integration Center)
Introduction of NEC Space Business (Launch of Satellite Integration Center) July 2, 2014 Masaki Adachi, General Manager Space Systems Division, NEC Corporation NEC Space Business ▌A proven track record in space-related assets Satellites · Communication/broadcasting · Earth observation · Scientific Ground systems · Satellite tracking and control systems · Data processing and analysis systems · Launch site control systems Satellite components · Large observation sensors · Bus components · Transponders · Solar array paddles · Antennas Rocket subsystems Systems & Services International Space Station Page 1 © NEC Corporation 2014 Offerings from Satellite System Development to Data Analysis ▌In-house manufacturing of various satellites and ground systems for tracking, control and data processing Japan's first Scientific satellite Communication/ Earth observation artificial satellite broadcasting satellite satellite OHSUMI 1970 (24 kg) HISAKI 2013 (350 kg) KIZUNA 2008 (2.7 tons) SHIZUKU 2012 (1.9 tons) ©JAXA ©JAXA ©JAXA ©JAXA Large onboard-observation sensors Ground systems Onboard components Optical, SAR*, hyper-spectral sensors, etc. Tracking and mission control, data Transponders, solar array paddles, etc. processing, etc. Thermal and near infrared sensor for carbon observation ©JAXA (TANSO) CO2 distribution GPS* receivers Low-noise Multi-transponders Tracking facility Tracking station amplifiers Dual- frequency precipitation radar (DPR) Observation Recording/ High-accuracy Ion engines Solar array 3D distribution of TTC & M* station image -
EOS Data Products Handbook Volume 2 ACRIMSAT • ACRIM III
EOS EOS http://eos.nasa.gov/ ACRIMSAT • ACRIM III EOS Data Products EOSDIS http://spsosun.gsfc.nasa.gov/New_EOSDIS.html Aqua Handbook Data Products • AIRS Handbook • AMSR-E • AMSU-A • CERES • HSB • MODIS Volume 2 Jason-1 • DORIS • JMR • Poseidon-2 Landsat 7 • ETM+ Meteor 3M • SAGE III QuikScat • • SeaWinds QuikTOMS • TOMS Volume 2 Volume VCL • MBLA ACRIMSAT • Aqua • Jason-1 • Landsat 7 • Meteor 3M/SAGE III • QuikScat • QuikTOMS • VCL National Aeronautics and NP-2000-5-055-GSFC Space Administration EOS Data Products Handbook Volume 2 ACRIMSAT • ACRIM III Aqua • AIRS • AMSR-E • AMSU-A • CERES • HSB • MODIS Jason-1 • DORIS • JMR • Poseidon-2 Landsat 7 • ETM+ Meteor 3M • SAGE III QuikScat • SeaWinds QuikTOMS • TOMS VCL • MBLA EOS Data Products Handbook Volume 2 Editors Acknowledgments Claire L. Parkinson Special thanks are extended to NASA Goddard Space Flight Center Michael King for guidance throughout and to the many addi- tional individuals who also pro- Reynold Greenstone vided information necessary for the completion of this second volume Raytheon ITSS of the EOS Data Products Hand- book. These include most promi- nently Stephen W. Wharton and Monica Faeth Myers, whose tre- mendous efforts brought about Design and Production Volume 1, and the members of the Sterling Spangler science teams for each of the in- Raytheon ITSS struments covered in this volume. Support for production of this For Additional Copies: document, provided by William EOS Project Science Office Bandeen, Jim Closs, Steve Gra- Code 900 ham, and Hannelore Parrish, is also gratefully acknowledged. NASA/Goddard Space Flight Center Greenbelt, MD 20771 http://eos.nasa.gov Phone: (301) 441-4259 Internet: [email protected] NASA Goddard Space Flight Center Greenbelt, Maryland Printed October 2000 Abstract The EOS Data Products Handbook provides brief descriptions of the data prod- ucts that will be produced from a range of missions of the Earth Observing System (EOS) and associated projects. -
A Note from the Co-Chairs SPECIAL ISSUE Satellite Retrievals Of
Issue No. 35 March 2007 Taipei TAIWAN R.O.C. POSTAGE PAID NEWSLETTER LICENCE NO.N285 IGAC Core Project Office RESEARCH CENTER FOR ENVIRONMENTAL CHANGE of the International Global Atmospheric Chemistry Project ACADEMIA SINICA 128 Academia Rd. Sect. 2 P.O. Box 1-55 NanKang Taipei, 11529 Taiwan A Note from the IGAC Co-chairs: Phil Rasch and Kathy Law This newsletter provides an introduction to satellite-based instruments in use for assessing A Note from the tropospheric constituent distributions, and it highlights how these satellite observations Co-Chairs have contributed to rapid developments in our understanding of tropospheric chemistry. Examples include the quantification of emissions, improved estimates of radiative forcing, observation of long-range transport on regional to continental scales, and air quality characterization. Increasing concern over changes taking place in the Earth system due to human activities makes it critical that we understand how these data can be used to SPECIAL ISSUE understand the Earth system. We hope that this summary can provide a glimpse into the Printed on Recycled Paper many available opportunities for exploiting these data. The use of satellite remote sensing, especially for tropospheric applications, is a fairly Please Recycle after Use! Satellite new field. Like the very first picture of Earth taken from space, the images from these Retrievals instruments provide, at a glance, an unprecedented and inspiring world-view. They are of both illustrative of specific events (e.g. pollution sources, fires, and transport pathways) and useful for quantitative studies (e.g. inversions for source emission estimates). However, Tropospheric for quantitative applications, there is a significant learning curve to using the data with Chemistry appreciation of its strengths and limitations, especially when trying to compare or integrate the data with models or in-situ measurements.