Entropy Production and Mixed Convection Within Trapezoidal Cavity Having Nanofuids and Localised Solid Cylinder Muhamad S
Total Page:16
File Type:pdf, Size:1020Kb
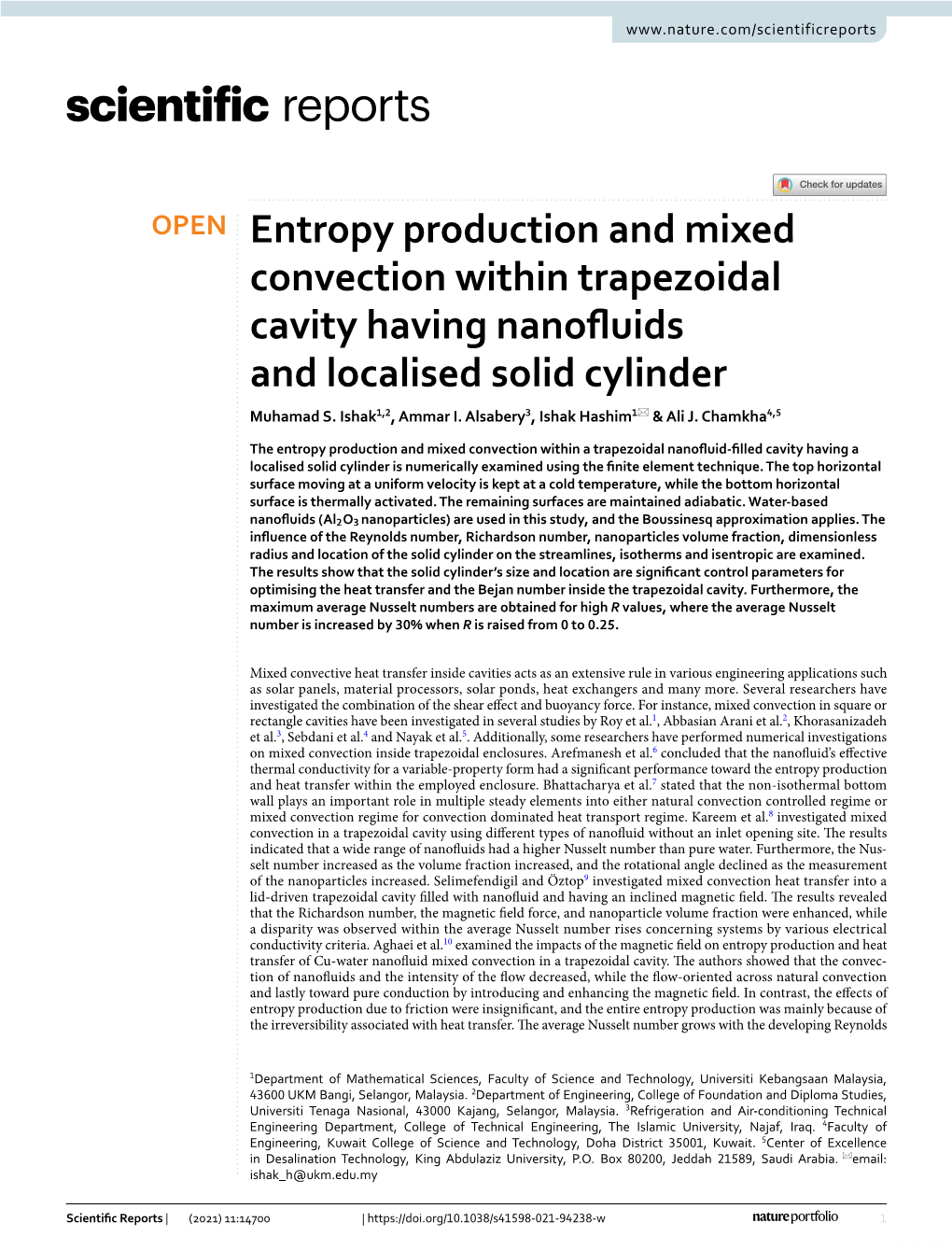
Load more
Recommended publications
-
The Effects of Vertical and Horizontal Sources on Heat Transfer
View metadata, citation and similar papers at core.ac.uk brought to you by CORE provided by Research Online University of Wollongong Research Online Faculty of Engineering and Information Faculty of Engineering and Information Sciences - Papers: Part B Sciences 2019 The effects of vertical and horizontal sources on heat transfer and entropy generation in an inclined triangular enclosure filled with non-Newtonian fluid and subjected ot magnetic field Zhixiong Li University of Wollongong, [email protected] Amin Shahsavar Kavian Niazi Abdullah Al-Rashed Pouyan Talebizadehsardari Follow this and additional works at: https://ro.uow.edu.au/eispapers1 Part of the Engineering Commons, and the Science and Technology Studies Commons Recommended Citation Li, Zhixiong; Shahsavar, Amin; Niazi, Kavian; Al-Rashed, Abdullah; and Talebizadehsardari, Pouyan, "The effects of vertical and horizontal sources on heat transfer and entropy generation in an inclined triangular enclosure filled with non-Newtonian fluid and subjected ot magnetic field" (2019). Faculty of Engineering and Information Sciences - Papers: Part B. 3789. https://ro.uow.edu.au/eispapers1/3789 Research Online is the open access institutional repository for the University of Wollongong. For further information contact the UOW Library: [email protected] The effects of vertical and horizontal sources on heat transfer and entropy generation in an inclined triangular enclosure filled with non-Newtonian fluid and subjected to magnetic field Abstract 2019 Elsevier B.V. Natural convection and entropy generation of a power-law non-Newtonian fluid in a tilted triangular enclosure subjected to a magnetic field was investigated. A part of the enclosure's right or left wall is at a high temperature while the top wall is cold. -
Analysis of Entropy Generation Between Porous Disks Due to Micropolar Fluid Flow with MHD Effect
The International Journal of Engineering and Science (IJES) ISSN (e): 2319 – 1813 ISSN (p): 23-19 – 1805 || Pages || PP 36-42 || 2020 || Analysis of Entropy Generation between porous disks due to Micropolar Fluid flow with MHD effect D. Srinivasacharya1, K. Hima Bindu2 1 Mathematics, National Institute of Technology, Warangal, Telangana, India 2 Mathematics, TSWRDCW Sircilla, Telangana, India Corresponding Author: D. Srinivasacharya --------------------------------------------------------ABSTRACT----------------------------------------------------------- This paper examines the magneto hydrodynamic flow of an electrically conducting micropolar fluid flow between parallel porous disks with constant uniform suction through the surface of the disks. The fluid is subjected to an external transverse magnetic field. The governing equations of the fluid flow are linearized using quasilinearization method and further, solved by the Chebyshev spectral collocation method. The numerical data for velocity, microrotation and temperature fields are used to evaluate entropy generation and Bejan number. It has been found that the entropy generation decreases with increase in Hartman number. Heat transfer irreversibility dominates at the lower and upper disks whereas fluid friction irreversibility dominates at the center of the parallel disks are observed from all Bejan number profiles. KEYWORDS;- Parallel disks, Micropolar fluid, Magnetic field, Entropy, Bejan number I. INTRODUCTION In most of the thermal systems, the thermal efficiency can be defined as a ratio of actual efficiency of thermal system to reversible thermal efficiency where the applied conditions are same. The fluid flow and heat transfer processes are intrinsically irreversible, which leads to increase entropy generation and useful energy destruction. Taking this into consideration, worldwide research is going on to reduce the entropy generation. Bejan [1] was the pioneer work on entropy generation. -
CONVECTION HEAT TRANSFER Other Books by Adrian Bejan
CONVECTION HEAT TRANSFER Other books by Adrian Bejan: Entropy Generation Through Heat and Fluid Flow, Wiley, 1982. Advanced Engineering Thermodynamics, Third Edition, Wiley, 2006. Thermal Design and Optimization, with G. Tsatsaronis and M. Moran, Wiley, 1996. Entropy Generation Minimization, CRC Press, 1996. Shape and Structure, from Engineering to Nature, Cambridge, 2000. Heat Transfer Handbook, with A. D. Kraus, eds., Wiley, 2003. Design with Constructal Theory, with S. Lorente, Wiley, 2008. Design in Nature, with J. P. Zane, Doubleday, 2012. Convection in Porous Media, with D. A. Nield, Fourth Edition, Springer, 2013. CONVECTION HEAT TRANSFER FOURTH EDITION Adrian Bejan J.A. Jones Distinguished Professor Duke University Durham, North Carolina Cover image: Courtesy of Adrian Bejan Cover design: John Wiley & Sons, Inc. This book is printed on acid-free paper. Copyright 2013 by John Wiley & Sons, Inc. All rights reserved Published by John Wiley & Sons, Inc., Hoboken, New Jersey Published simultaneously in Canada No part of this publication may be reproduced, stored in a retrieval system, or transmitted in any form or by any means, electronic, mechanical, photocopying, recording, scanning, or otherwise, except as permitted under Section 107 or 108 of the 1976 United States Copyright Act, without either the prior written permission of the Publisher, or authorization through payment of the appropriate per-copy fee to the Copyright Clearance Center, 222 Rosewood Drive, Danvers, MA 01923, (978) 750-8400, fax (978) 646-8600, or on the web at www.copyright.com. Requests to the Publisher for permission should be addressed to the Permissions Department, John Wiley & Sons, Inc., 111 River Street, Hoboken, NJ 07030, (201) 748-6011, fax (201) 748-6008, or online at www.wiley.com/go/permissions. -
Entropy Generation in Magnetohydrodynamic Mixed Convection Flow Over an Inclined Stretching Sheet
entropy Article Entropy Generation in Magnetohydrodynamic Mixed Convection Flow over an Inclined Stretching Sheet Muhammad Idrees Afridi 1, Muhammad Qasim 1, Ilyas Khan 2,*, Sharidan Shafie 3 and Ali Saleh Alshomrani 4 1 Department of Mathematics, COMSATS Institute of Information Technology, Park Road, Chak Shahzad, Islamabad 44000, Pakistan; [email protected] (M.I.A.); [email protected] (M.Q.) 2 Basic Engineering Sciences Department, College of Engineering, Majmaah University, Majmaah 11952, Saudi Arabia 3 Department of Mathematical Sciences, Faculty of Science, Universiti Teknologi Malaysia, 81310 UTM Johor Bahru, Johor 81310, Malaysia; [email protected] 4 Department of Mathematics, Faculty of Science, King Abdul Aziz University, Jeddah 21589, Saudi Arabia; [email protected] * Correspondence: [email protected]; Tel: +966-5-9477-0286 Academic Editors: Kevin H. Knuth, Brian Agnew and Eliodoro Chiavazzo Received: 5 July 2016; Accepted: 28 September 2016; Published: 28 December 2016 Abstract: This research focuses on entropy generation rate per unit volume in magneto-hydrodynamic (MHD) mixed convection boundary layer flow of a viscous fluid over an inclined stretching sheet. Analysis has been performed in the presence of viscous dissipation and non-isothermal boundary conditions. The governing boundary layer equations are transformed into ordinary differential equations by an appropriate similarity transformation. The transformed coupled nonlinear ordinary differential equations are then solved numerically by a shooting technique along with the Runge-Kutta method. Expressions for entropy generation (Ns) and Bejan number (Be) in the form of dimensionless variables are also obtained. Impact of various physical parameters on the quantities of interest is seen. Keywords: entropy generation; viscous dissipation; mixed convection; inclined stretching; Bejan number 1. -
Thermodynamic Analysis of Fe3o4nanofluid Flowing Through a Circular Tube
International Journal of Engineering and Advanced Technology (IJEAT) ISSN: 2249 – 8958, Volume-8 Issue-6, August 2019 Thermodynamic Analysis of Fe3O4Nanofluid Flowing Through A Circular Tube Praveena Devi N, Ch. Srinivasa Rao, K Kiran Kumar second law analysis is an efficient tool to find the suitability of Abstract: Present work is an experimental study of entropy the nanofluid in any thermal management system. It is to be generation of Fe3O4-water nanofluid flowing through a circular observed that, with nanofluids, thermal entropy generation tube. Flow is maintained in the turbulent region and tube is decreases whereas frictional entropy increases [ 3]. Bianco et exposed to constant heat flux along the length. Experiments are conducted to study the entropy generation rate for different al. [ 4] reported that at higher Reynolds number for minimum conditions such as particle volume concentrations varying from entropy generation, the most favorable nanoparticles 1% to 6% and also for the different Reynolds numbers varying concentration is low. Mahian et al.[5] in their studies on two from 6000 to 22000. Measured data from experimentation is co-rotating cylinders showed the possibility of minimizing the taken as input to calculate thermal entropy and frictional entropy entropy generation in the nanofluid with respect to the generation separately. Based on these thermal entropy and frictional entropy generation total entropy generation and Bejan nanoparticles concentration . number are calculated and results are analyzed. Experimentally, A customized experimental test rig is fabricated it is proved that the changes in the thermal and frictional entropy which represent different flow conditions (different Reynolds generations are converse, such a way that, as particle numbers) and different heat fluxes. -
Research Article Mathematical Analysis of a Reactive Viscous Flow Through a Channel Filled with a Porous Medium
Hindawi Publishing Corporation Journal of Mathematics Volume 2016, Article ID 1350578, 8 pages http://dx.doi.org/10.1155/2016/1350578 Research Article Mathematical Analysis of a Reactive Viscous Flow through a Channel Filled with a Porous Medium Samuel O. Adesanya,1 J. A. Falade,2 J. C. Ukaegbu,1 and K. S. Adekeye1 1 Department of Mathematical Sciences, Redeemer’s University, Ede, Nigeria 2Department of Physical Sciences, Redeemer’s University, Ede, Nigeria Correspondence should be addressed to Samuel O. Adesanya; [email protected] Received 19 July 2016; Accepted 14 November 2016 Academic Editor: Ghulam Shabbir Copyright © 2016 Samuel O. Adesanya et al. This is an open access article distributed under the Creative Commons Attribution License, which permits unrestricted use, distribution, and reproduction in any medium, provided the original work is properly cited. An investigation has been carried out to study entropy generation in a viscous, incompressible, and reactive fluid flowing steadily through a channel with porous materials. Approximate solutions for both velocity and temperature fields are obtained by using a rapidly convergent Adomian decomposition method (ADM). These solutions are then used to determine the heat irreversibility and Bejan number of the problem. Variations of other important fluid parameters are conducted, presented graphically, and discussed. 1. Introduction flux. Revellin et al. [8] addressed the thermal performance of adiabatic two-phase flow using two different methods. Studies on heat irreversibility in moving fluid find its rel- Hedayati et al. [9] utilized the thermodynamics analysis to evance in several geological, petrochemical, and industrial optimize flow on a nonstationary wedge. Butt and Ali [10] applications. -
2D Temperature Analysis of Energy and Exergy Characteristics of Laminar Steady Flow Across a Square Cylinder Under Strong Blockage
Entropy 2015, 17, 3124-3151; doi:10.3390/e17053124 OPEN ACCESS entropy ISSN 1099-4300 www.mdpi.com/journal/entropy Article 2D Temperature Analysis of Energy and Exergy Characteristics of Laminar Steady Flow across a Square Cylinder under Strong Blockage M. Ozgun Korukcu Department of Mechanical Engineering, University of Uludag, Gorukle, 16059 Bursa, Turkey; E-Mail: [email protected]; Tel.: +90-224-2941927; Fax: +90-224-2941903 Academic Editor: Marc A. Rosen Received: 10 March 2015 / Accepted: 7 May 2015 / Published: 12 May 2015 Abstract: Energy and exergy characteristics of a square cylinder (SC) in confined flow are investigated computationally by numerically handling the steady-state continuity, Navier-Stokes and energy equations in the Reynolds number range of Re = 10–50, where the blockage ratio (β = B/H) is kept constant at the high level of β = 0.8. Computations indicated for the upstream region that, the mean non-dimensional streamwise (u/Uo) and spanwise (v/Uo) velocities attain the values of u/Uo = 0.840→0.879 and v/Uo = 0.236→0.386 (Re = 10→50) on the front-surface of the SC, implying that Reynolds number and blockage have stronger impact on the spanwise momentum activity. It is determined that flows with high Reynolds number interact with the front-surface of the SC developing thinner thermal boundary layers and greater temperature gradients, which promotes the thermal entropy generation values as well. The strict guidance of the throat, not only resulted in the fully developed flow character, but also imposed additional cooling; such that the analysis pointed out the drop of duct wall (y = 0.025 m) non-dimensional temperature values (ζ) from ζ = 0.387→0.926 (Re = 10→50) at xth = 0 mm to ζ = 0.002→0.266 at xth = 40 mm. -
Entropy Generation Due to Heat and Fluid Flow in Backward Facing Step Flow with Various Expansion Ratios
Int. J. Exergy, Vol. 3, No. 4, 2006 419 Entropy generation due to heat and fluid flow in backward facing step flow with various expansion ratios Eiyad Abu-Nada Department of Mechanical Engineering, Hashemite University, Zarqa, 13115, Jordan E-mail: [email protected] Abstract: The present research investigated second law analysis of laminar flow over a backward facing step with various expansion ratios (ER). As Reynolds number (Re) increased the value of total entropy generation (Ns) increased. For smaller values of Re as the expansion ratio increased the value of Ns decreased. However, for higher values of Re as ER increased the value of Ns decreased but at smaller rates. The total Bejan number increased as the ER increased. At the bottom wall the minimum value of Ns occurred at the step location and the maximum value of Ns occurred inside the recirculation zone. Keywords: entropy generation; second-law analysis; separated flow; heat transfer. Reference to this paper should be made as follows: Abu-Nada, E. (2006) ‘Entropy generation due to heat and fluid flow in backward facing step flow with various expansion ratios’, Int. J. Exergy, Vol. 3, No. 4, pp.419–435. Biographical notes: Eiyad Abu-Nada is an Assistant Professor in the Department of Mechanical Engineering at the Hashemite University in Jordan. Recently he has assumed the position of Head of the Department. He joined the Department of Mechanical Engineering on February 2002. He got his PhD from New Mexico State University in Mechanical Engineering in 2001. His areas of research are entropy generation, viscous fluid flow, computational heat transfer, and flow in micro channels. -
Thermodynamic Analysis of Entropy Generation Minimization in Thermally Dissipating Flow Over a Thin Needle Moving in a Parallel Free Stream of Two Newtonian Fluids
entropy Article Thermodynamic Analysis of Entropy Generation Minimization in Thermally Dissipating Flow Over a Thin Needle Moving in a Parallel Free Stream of Two Newtonian Fluids Ilyas Khan 1, Waqar A. Khan 2, Muhammad Qasim 3 , Idrees Afridi 3 and Sayer O. Alharbi 4,* 1 Faculty of Mathematics and Statistics, Ton Duc Thang University, Ho Chi Minh City 700,000, Vietnam; [email protected] 2 Department of Mechanical Engineering, College of Engineering, Prince Mohammad Bin Fahd University, Al Khobar 31952, Saudi Arabia; [email protected] 3 Department of Mathematics, COMSATS University Islamabad (CUI), Park Road, Tarlai Kalan, Islamabad-455000, Pakistan; [email protected] (M.Q.); [email protected] (I.A.) 4 Department of Mathematics, College of Science Al-Zulfi, Majmaah University, Al-Majmaah 11952, Saudi Arabia * Correspondence: [email protected] Received: 21 November 2018; Accepted: 28 December 2018; Published: 16 January 2019 Abstract: This article is devoted to study sustainability of entropy generation in an incompressible thermal flow of Newtonian fluids over a thin needle that is moving in a parallel stream. Two types of Newtonian fluids (water and air) are considered in this work. The energy dissipation term is included in the energy equation. Here, it is presumed that u¥ (the free stream velocity) is in the positive axial direction (x-axis) and the motion of the thin needle is in the opposite or similar direction as the free stream velocity. The reduced self-similar governing equations are solved numerically with the aid of the shooting technique with the fourth-order-Runge-Kutta method. Using similarity transformations, it is possible to obtain the expression for dimensionless form of the volumetric entropy generation rate and the Bejan number. -
MHD Casson Fluid Flow Over a Stretching Sheet with Entropy Generation Analysis and Hall Influence
entropy Article MHD Casson Fluid Flow over a Stretching Sheet with Entropy Generation Analysis and Hall Influence Mohamed Abd El-Aziz 1 and Ahmed A. Afify 2,* 1 Department of Mathematics, Faculty of Science, King Khalid University, Abha 9004, Saudi Arabia; [email protected] 2 Department of Mathematics, Deanship of Educational Services, Qassim University, P.O. Box 6595, Buraidah 51452, Saudi Arabia * Correspondence: afi[email protected] Received: 3 May 2019; Accepted: 12 June 2019; Published: 14 June 2019 Abstract: The impacts of entropy generation and Hall current on MHD Casson fluid over a stretching surface with velocity slip factor have been numerically analyzed. Numerical work for the governing equations is established by using a shooting method with a fourth-order Runge–Kutta integration scheme. The outcomes show that the entropy generation is enhanced with a magnetic parameter, Reynolds number and group parameter. Further, the reverse behavior is observed with the Hall parameter, Eckert number, Casson parameter and slip factor. Also, it is viewed that Bejan number reduces with a group parameter. Keywords: MHD Casson fluid; slip factor; Hall current; entropy generation; Bejan number 1. Introduction The study of magnetohydrodynamic flows with Hall currents has evinced interest attributable to its numerous applications in industries, such as MHD power generators, Hall current accelerators, Hall current sensors, and planetary fluid dynamics. Sato [1] was the first author who investigated the impact of Hall current on the flow of ionized gas between two parallel plates. The influence of Hall current on the efficiency of an MHD generator was investigated by Sherman and Sutton [2]. -
Entropy Analysis for Boundary Layer Micropolar Fluid Flow
AIMS Mathematics, 5(3): 2009–2026. DOI: 10.3934/math.2020133 Received: 28 September 2019 Accepted: 09 February 2020 Published: 21 February 2020 http://www.aimspress.com/journal/Math Research article Entropy Analysis for boundary layer Micropolar fluid flow Paresh Vyas, Rajesh Kumar Kasana and Sahanawaz Khan* Department of Mathematics, University of Rajasthan, Jaipur-302004, India * Correspondence: Email: [email protected]; Tel: +01412708392. Abstract: This paper reports entropy generation analysis of radiative micropolar fluid flow in porous medium. The mathematical model depicting convective boundary layer flow due to a vertically moving infinite plate bounding the porous medium on one side is solved numerically. An implicit finite difference method together with Gauss elimination method is used. The numerically computed velocity and temperature fields are employed to analyze entropy. The plots for entropy generation number for various sets of parameters are drawn. It is found that entropy generation number Ns decreases with increasing values of heat sink parameter Q and radiation parameter N whereas it increases with increasing values of Grashoff number Gr, Brinkman number Br. The Bejan number shows pronounced variations for the parameters entering into the problem. Keywords: micropolar fluid; porous medium; entropy Mathematics Subject Classification: 74A15, 76D10, 76S05 Nomenclature: Be: Bejan number; Br: Brinkman number; c: specific heat at constant pressure; Ec: Eckert number; g: acceleration due to gravity; Gr: Grashoff number; -
A New Definition of Bejan Number THERMAL SCIENCE: Year 2012, Vol
Awad, M. M.: A New Definition of Bejan Number THERMAL SCIENCE: Year 2012, Vol. 16, No. 4, pp. 1251-1253 1251 A NEW DEFINITION OF BEJAN NUMBER by Mohamed M. AWAD Mechanical Power Engineering Department, Faculty of Engineering, Mansoura University, Mansoura, Egypt Short paper DOI: 10.2298/TSCI12041251A A new definition of Bejan number will be generated by replacing the thermal diffusivity with the mass diffusivity.For example, the Schmidt number is the mass transfer analog of the Prandtl number. For the case of Reynolds analogy (Sc = Pr = = 1), both current and new definitions of Bejan number are the same. This new defi- nition is useful and needed for diffusion of mass (mass diffusion). Key words: new definition, Bejan number, thermal diffusivity, mass diffusivity The Bejan numbers (Be) is named after Duke University Professor Adrian Bejan. It is used in fluid mechanics and heat transfer in general and represents the dimensionless pressure drop along a channel of length L. Historically, Bhattacharjee et al. [1] presented a systematic analysis of a pressure-driven wall jet. First, the researchers identified a model where the pres- sure gradient might become the dominant force in the wall boundary layer. They used numerical calculations to gain insight into the formation of the jet, and performed a simplified scale analy- sis for an idealized flow with favorable pressure gradient over a flat plate to identify the impor- tant non-dimensional groups. Using the scale analysis of the wall jet problem, they defined the dimensionless group: DPL2 Be = (1) mn where DP, L, m, and n are the pressure difference, the flow length, the dynamic viscosity, and the momentum diffusivity of the fluid, respectively.