Transit-Bus-Component-Tech-Forum
Total Page:16
File Type:pdf, Size:1020Kb
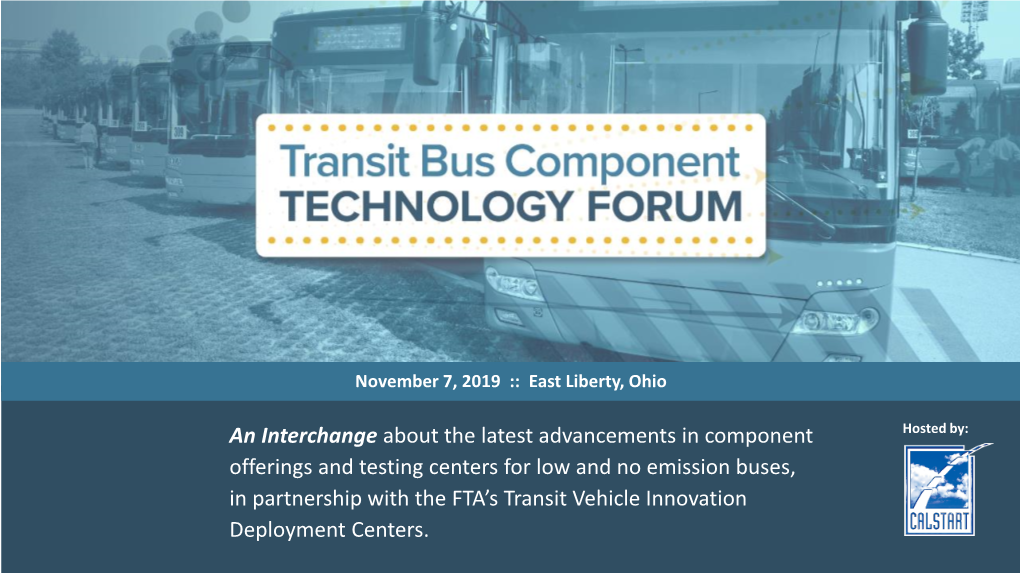
Load more
Recommended publications
-
The Mil-Spec Automotive M1 Specification Document 2020
SPECIFICATION DOCUMENT PROGRAM: THE MIL-SPEC AUTOMOTIVE M1 YEAR: 2020 M1 ESTABLISHED Mil-Spec Automotive creates re-envisioned vehicles that encompass the new era of adventure through 2015 exclusive utility and performance. We offer a distinct aesthetic that sets our work apart from the competition. Our team focuses on integrating relevant technology and products into a package that improves on proven platforms. THE 2020 MIL-SPEC M1 1 CHRIS VAN SCYOC ADAM MITCHELL IAN BROEKMAN President Chief Executive Officer Chief Innovation Officer & Co-Founder & Founder & Co-Founder THE 2020 MIL-SPEC M1 2 INTRODUCING The Mil-Spec Automotive M1 The MSA M1 is an evolution of the vehicle that our story began with, the Hummer H1. By expanding and improving on the Launch Edition program, we have created a re-imagined vehicle that establishes a new gold standard for current and future programs. FEATURING: Three Body Configuration Options 500 HP and 1000 Ft-Lbs Torque Revised Interior Design Including New Billet Components THE 2020 MIL-SPEC M1 3 MSA 2020 Components & Features THE 2020 MIL-SPEC M1 4 Components & Features AXLES TRANSFER CASE DRIVE TRAIN HORSEPOWER & TORQUE Independent, 12k rated half shafts Heavy duty, selectable Electronic, selectable 2wd/4wd system with fixed mounted differentials (4L-N-2H-4H push button engagement) *MSA proprietary heavy duty drive train 500hp & 1000 ft-lb configuration includes: re-designed constant velocity front and rear drive shafts, carrier bearings, motor mounts, and transmission *Values based on estimated crank horsepower -
Investigation on Static Stress Analysis of Portal Axle Gearbox
International Journal of Applied Engineering Research ISSN 0973-4562 Volume 13, Number 7 (2018) pp. 5244-5250 © Research India Publications. https://dx.doi.org/10.37622/IJAER/13.7.2018.5244-5250 Investigation on Static Stress Analysis of Portal Axle Gearbox Devan P D1, Senthilkumar K M2 & Arun K K3 Department of Mechanical Engineering, Kumaraguru College of Technology, Coimbatore, India. Abstract. gear failure. Due to cyclic loading, a pit is formed on the gear tooth surface and leads to surface failure. After a longer The paper deals with stress analysis of spur gear used in portal period, crack is initiated at root fillet. Tooth breakage occurs axle gearbox. Portal axle is a type of gearbox, especially used when the bending stress exceeds the maximum limit. in off-road vehicles. Gear teeth failure takes place due to excessive contact and bending stresses. Three different Contact stress is a kind of surface failure modes of the gear configurations of gear trains have taken for the analysis. Gear tooth due to repetitive fatigue load. In static analysis, entire trains are modeled and assembled in SOLIDWORKS and load is acting on the single tooth. In a dynamics analysis, analyzed in ANSYS workbench 14.5 software. Steel, Cast theses stresses at pitch circle is less than other areas [1]. Iron and Aluminium Alloy are taken as gear materials. In this Shuting Li [2] has develop an accurate analytical method to study, contact and bending stresses are theoretically calculated find out bending and contact stress of a spur gear tooth with using Hertzian theory and Lewi’s formula and simulated using the consideration of Mechanical, Assembly and Transmission finite element method (FEM). -
2018 MSA Launch Edition Standard Equipment + Optional Equipment
2018 MSA Launch Edition Standard Equipment + Optional Equipment Sheet (ORDER FORM) STANDARD LAUNCH EDITION $200,500 Interior: o Tri-Level Insulation System – This system protects against temperature, ambient noise, and vibration throughout the entire truck. o MSA Design LE Interior – Bespoke interior design developed in house and unique to the MSA LE program. o Standard MSA Design H1 Seats – Optional Comfort Package Available o MSA Design Re-Envisioned Interior Integrated Speakers and Controls Momo Prototipo Steering Wheel MSA Design Gauge Package LEFT to RIGHT – • Speed, RPM, Odometer (Trip Computer), Integrated Turn Signal Indicators • Voltage, Water Temp, Fuel Level, Oil Pressure • Boost, Trans Temp, EGT o Four Center Console Cup Holders o Driver and Passenger Safety Handles o Machined Steel Climate Control Knobs (Textured Black Coating) o Aircraft Grade Sun Visors o Standard MSA Water Resistant Upholstery Marine Grade Leather Moisture Resistant Tough Duck o MSA Design Identification Plate – Each vehicle comes with a plate that designates your serial number. o MSA Exclusive Audio Package – JL Audio Marine grade source unit with Sirius Satellite radio compatibility. This unit also has Bluetooth connectivity with an additional passenger control unit. o Outdoor Audio (Soft-top Configuration) - JL 9 Speaker Marine Grade Indoor Audio (Hard-top Configuration) – JL 9 Speaker Premium Audio System o MSA OEM Modernization Package – This package brings your Hummer H1 into the 21st century with modern components. o OEM Steering Column with Lighting/Wiper Controls o Electronic Transfer Case (GM Unit) o Modern Automatic Transmission Gear Selector o (Thumb Sensitive) Push Button Start o Remote Start/Vehicle Security System o Primary and Secondary Climate Control o Window Defrost System with Adjustable Vents o Front and Rear USB Outlets o Accessory Switch Panel (Located in Center Console) Exterior: o MSA Kevlar Body Coating – We coat the entire exterior of our LE’s with a tough durable Kevlar coating. -
Assembly Manual Introduction
MODEL 82016-4 6250 TRAXXAS WAY, McKINNEY, TEXAS 75070 1-888-TRAXXAS ASSEMBLY MANUAL INTRODUCTION Thank you for purchasing the all-new Traxxas TRX-4 builders may only need 4-5 hours to assemble this kit, while unassembled kit. The design of the TRX-4 instantly others may spend an entire weekend on it. You should obsoletes the status quo with greatly expanded features feel comfortable with taking as much time as needed to and versatility. The TRX-4 features the powerful Titan® 21T properly build and set up your model. 550 motor, waterproof electronics, and a smooth XL-5 HV 3s If you’ve been exploring the contents of your kit box, you’ve LiPo-capable electronic speed control. The game-changing noticed many bags of small parts. Open only one bag at a portal axles provide greater ground clearance while the time. To keep the parts organized, use small paper plates rigid steel frame eliminates chassis flex and allows you to or several large plastic plates with partitions to contain the navigate tough terrain. The new Canyon Trail 1.9 tires feature parts. Label the paper plates, and then pour the contents tuned foam inserts to deliver superior bite on rocky surfaces of the bags onto them. This puts the parts out in the open with convincing scale realism. In other words, we built it the where you can find them easily. The plates also prevent Traxxas way -- rugged, powerful, and ready to handle the small parts from rolling off the table. rigors of remote locations and all-day driving fun! Please read the text next to each diagram. -
WO 2015/097631 Al 2 July 2015 (02.07.2015) P O P C T
(12) INTERNATIONAL APPLICATION PUBLISHED UNDER THE PATENT COOPERATION TREATY (PCT) (19) World Intellectual Property Organization International Bureau (10) International Publication Number (43) International Publication Date WO 2015/097631 Al 2 July 2015 (02.07.2015) P O P C T (51) International Patent Classification: BZ, CA, CH, CL, CN, CO, CR, CU, CZ, DE, DK, DM, B60K 17/04 (2006.01) B60K 7/00 (2006.01) DO, DZ, EC, EE, EG, ES, FI, GB, GD, GE, GH, GM, GT, HN, HR, HU, ID, IL, IN, IR, IS, JP, KE, KG, KN, KP, KR, (21) International Application Number: KZ, LA, LC, LK, LR, LS, LU, LY, MA, MD, ME, MG, PCT/IB20 14/067 195 MK, MN, MW, MX, MY, MZ, NA, NG, NI, NO, NZ, OM, (22) International Filing Date: PA, PE, PG, PH, PL, PT, QA, RO, RS, RU, RW, SA, SC, 2 1 December 2014 (21 .12.2014) SD, SE, SG, SK, SL, SM, ST, SV, SY, TH, TJ, TM, TN, TR, TT, TZ, UA, UG, US, UZ, VC, VN, ZA, ZM, ZW. (25) Filing Language: English (84) Designated States (unless otherwise indicated, for every (26) Publication Language: English kind of regional protection available): ARIPO (BW, GH, (30) Priority Data: GM, KE, LR, LS, MW, MZ, NA, RW, SD, SL, ST, SZ, P1300754 23 December 201 3 (23. 12.2013) HU TZ, UG, ZM, ZW), Eurasian (AM, AZ, BY, KG, KZ, RU, TJ, TM), European (AL, AT, BE, BG, CH, CY, CZ, DE, (71) Applicant: RABA FUTOMU KFT. [HU/HU]; Martin it DK, EE, ES, FI, FR, GB, GR, HR, HU, IE, IS, IT, LT, LU, 1., H-9027 Gyor (HU). -
Suspension by Design
Version 5.114A June 2021 SusProg3D - Suspension by Design Robert D Small All rights reserved. No parts of this work may be reproduced in any form or by any means - graphic, electronic, or mechanical, including photocopying, recording, taping, or information storage and retrieval systems - without the written permission of the publisher. Products that are referred to in this document may be either trademarks and/or registered trademarks of the respective owners. The publisher and the author make no claim to these trademarks. While every precaution has been taken in the preparation of this document, the publisher and the author assume no responsibility for errors or omissions, or for damages resulting from the use of information contained in this document or from the use of programs and source code that may accompany it. In no event shall the publisher and the author be liable for any loss of profit or any other commercial damage caused or alleged to have been caused directly or indirectly by this document. Printed: June 2021 Contents 3 Table of Contents Foreword 0 Part 1 Overview 12 1 SusProg3D................................................................................................................................... - Suspension by Design 12 2 PC hardware................................................................................................................................... and software requirements 14 3 To run the.................................................................................................................................. -
Structural Analysis of Gear Train Design in Portal Axle Using Finite Element Modeling 1E
IJRMET VOL . 3, ISSU E 1, NO V - AP ri L 2013 ISSN : 2249-5762 (Online) | ISSN : 2249-5770 (Print) Structural Analysis of Gear Train Design in Portal Axle Using Finite Element Modeling 1E. Jayaram, 2M. Rambabu 1,2Dept. of Mechanical Engineering, Vitam Engineering College Visakapatnam, AP, India Abstract C. Finite Element Method (FEM) The portal axle is a gearbox that is specially designed for off-road The Finite Element Method (FEM) (its practical application driving conditions. It is installed between the wheel and the axle often known as Finite Element Analysis (FEA)) is a numerical shaft to give higher ground clearance to the vehicle. However, gear technique for finding approximate solutions to Partial Differential train design in portal axle is difficult to study comprehensively Equations (PDE) and their systems, as well as (less often) integral due to their relatively low cost and short product life cycle. In this equations. In simple terms, FEM is a method for dividing up a study, structural analysis of portal axle is simulated using Finite very complicated problem into small elements that can be solved Element Method (FEM). FEM static stress analysis is simulated on in relation to each other. FEM is a special case of the more general three different gear trains to study the gear teeth bending stress and Galerkin method with polynomial approximation functions. The contact stress behaviour of the gear trains. The single and double solution approach is based on eliminating the spatial derivatives pair gear teeth contact are also considered. Dynamic analysis is from the PDE. This approximates the PDE with carried out on above cases like modal & Harmonic. -
Don't Settle for Less Than the Best for Your Project!
Dynatrac™ axles are engineered like no others. These are large and small OEMs, demanding military, mining and other more than just upgrades. They are the ultimate axles, giving vehicle manufacturers. you the Confidence to Explore®! You can rest easy knowing that Dynatrac™ axles are built From our original Pro60™ to our popular ProRock44™, all with the best materials, processes and engineering available of our axles are 100-percent engineered, manufactured with more standard features than competitors. Each axle and assembled in the USA. Dynatrac™ has been the choice is inspected and measurements are checked a total of 117 of off-road racers and enthusiasts for over 20 years. Our different times before it’s shipped. expertise and high-quality products have also been used by Don’t settle for less than the best for your project! Dynatrac ProRock™ axle assemblies use a unique, patented design that delivers the best ground clearance in each category. From the ProRock44™ to the ProRock80®, there are no axle assemblies that are stronger, better engineered or offered in more configurations. And Dynatrac ProRock™ axles are 100% designed, manufactured and assembled in the USA with 100% new parts. More Ground Clearance ™ than a Dana 30! The Dynatrac ProRock44™ offers incredible strength and unmatched ground clearance in a small package. The ProRock44™ is full of uncompromised standard features like huge 3-inch-diameter, thick- wall axle tubes, unique US-made heavy-duty Pro44™ end forgings, thicker suspension brackets than stock and more. • The most ground clearance of any 44-based axle • Patented ProRock44™ design • Rock-proof nodular-iron Dynatrac™ diff cover included Available as a bolt-in assembly for the Jeep JK, TJ, XJ and • The strongest end forgings, made by Dynatrac™ in the other popular 4x4s. -
The New Unimog. Technical Data U 216 to U 530
The new Unimog. Technical data U 216 to U 530. Technical drawing of Unimog implement carrier BlueTec 6. Dimensions and weights. Models U 216 / U 218 U 318 U 423 U 427 / U 430 U 527 / U 530 Short Long Short Long Short Long Model type 405.090 405.104 405.105 405.125 405.110 405.125 405.202 405.222 A Wheelbase 2800 3000 3000 3600 3150 3600 3350 3900 B Vehicle height 2855 2845 2900 2900 2900 2900 2900 2900 B C Vehicle width 2200 2200 2200 2200 2200 2200 2300 2300 M D Track width 1794 1794 1734 1734 1734 1734 1828 1828 E Ground clearance 335 325 383 383 383 383 379 379 L F Vehicle length 4980 5155 5150 5755 5300 5755 5440 6215 K G1 Implement to axle centre 1145 1145 1142 1142 1142 1142 1142 1142 I J G2 Distance implement to 1363 1363 1363 1363 1363 1363 1363 1363 C steering wheel centre G1 A H H Rear overhang 860 840 840 840 840 840 840 1000 G2 I Ramp angle 27° 26° 30° 26° 30° 26° 28° 24° J Approach angle (front) 25° 27° 33° 33° 33° 33° 35° 35° K Departure angle (rear) 37° 37° 42° 42° 42° 42° 41° 35° N L Height of centre 825 815 873 873 873 873 869 869 trailer coupling M Height of platform 1357 1347 1407 1407 1407 1407 1435 1435 loading edge N Interior size tipper platform 2200 × 2075 × 400 2385 × 2075 × 400 2385 × 2075 × 400 2900 × 2075 × 400 2385 × 2075 × 400 2900 × 2075 × 400 2650 × 2200 × 400 3430 × 2200 × 400 (length × width × height) N Turning circle 12.6 m 13.7 m 13.7 m 16.5 m 14.3 m 16.5 m 15.1 m 16.9 m GVW (with optional extras) 10.0 t 11.0 t 13.8 t 14.0 t 14.0 t 14.0 t 16.5 t 16.5 t Maximum weight on front axle 5.2 t 5.5 t 6.9 t 7.0 t 7.0 t 7.0 t 7.5 t 7.5 t Maximum weight on rear axle 5.5 t 6.0 t 7.8 t 8.0 t 8.0 t 8.0 t 9.5 t 9.5 t E Vehicle dimensions in mm, tyres 365/80 R 20 (U 216 – U 318) or 365/85 R 20 (U 423 – U 530), partially loaded. -
EUROPEAN COMMISSION Brussels, XXX […](2017) XXX
EUROPEAN COMMISSION Brussels, XXX […](2017) XXX draft ANNEXES 7 to 11 ANNEXES to the Commission Regulation (EU) .../... implementing Regulation (EU) No 595/2009 of the European Parliament and of the Council as regards the determination of the CO2 emissions and fuel consumption of heavy-duty vehicles and amending Directive 2007/46/EC of the European Parliament and of the Council and Commission Regulation (EU) No 582/2011 EN EN ANNEXES to the Commission Regulation (EU) .../... implementing Regulation (EU) No 595/2009 of the European Parliament and of the Council as regards the determination of the CO2 emissions and fuel consumption of heavy-duty vehicles and amending Directive 2007/46/EC of the European Parliament and of the Council and Commission Regulation (EU) No 582/2011 ANNEX VII VERIFYING AXLE DATA 1. Introduction This Annex describes the certification provisions regarding the torque losses of propulsion axles for heavy duty vehicles. Alternatively to the certification of axles the calculation procedure for the standard torque loss as defined in Appendix 3 to this Annex can be applied for the purpose of the determination of vehicle specific CO2 emissions. 2. Definitions For the purposes of this Annex the following definitions shall apply: (1) “Single reduction axle (SR)” means a driven axle with only one gear reduction, typically a bevel gear set with or without hypoid offset. (2) “Single portal axle (SP)” means an axle, that has typically a vertical offset between the rotating axis of the crown gear and the rotating axis of the wheel due to the demand of a higher ground clearance or a lowered floor to allow a low floor concept for inner city buses. -
Download Mercedes Unimog U 4023 / U 5023 Technical Manual
Extreme off-road Unimog BlueTec 6 Technical Manual August 2014 issue Technical Manual Technical Manual for extreme off-road Unimog BlueTec 6 The present Technical Manual serves Unimog Sales as an advisory Part A document. In addition to the basic vehicle version, special equipment is also covered. Regarding the availability of standard and special equipment, Concept and sales reasoning please refer to the applicable price lists. Subject to technical modifications without notice. All rights reserved. Reprinting or reproduction in electronic form, including excerpts, is prohibited and requires the approval of Part B Mercedes-Benz Special Trucks. Technical data The latest changes and additions are available through our updates on the Extranet at: www.specialtrucks-extranet.com Daimler AG Mercedes-Benz Special Trucks Sales & Marketing August 2014 issue Mercedes-Benz Special Trucks 1 Contents Technical Manual Contents – Part A Overview of models and components ................................ 6 Transmission .......................................................................27 Main transmission ............................................................ 27 Product concept ................................................................... 7 Overview .......................................................................... 28 Unimog model series in comparison .................................. 7 Engine management ........................................................ 29 Extreme off-road capability ............................................... -
Design and Analysis of Portal Axle
IJSRD - International Journal for Scientific Research & Development| Vol. 7, Issue 10, 2019 | ISSN (online): 2321-0613 Design and Analysis of Portal Axle Omprakash Birajdar1 Harshal Lonkar2 1,2JSPM’s Rajarshi Shahu College of Engineering, Maharashtra, India Abstract— This project is related to the ground clearance and its toughness. Increased ground clearance is probably the V. CALCULATION main reason why serious off-roaders choose to fit portal axles to their vehicles. Hence we studied various gear arrangement A. Design- Since both gear are of same material, pinion is Weaker. for portal axle. Keywords: portal axle, Design of portal Axle, gear train 1) Design for Pinion design, Portal axle with spur & helical gear train Let, Number of teeth T1 = 24 ... Available standard I. INTRODUCTION So, module = m Diameter, D = T*m Portal axles (or portal gear) are an off-road technology where Velocity, v = πDN / 60 = 5275.2m the axle tube is above the center of the wheel hub and where Also W = (σ × C ) b.π.m.y …. (1) there is a reduction gearbox in the hub. This gives two t o v Tangential Tooth load advantages: ground clearance is increased, particularly =Wt = P/v … (2) beneath the low-slung differential housing of the main axles; = 55*1000/5275.2m = 10.43/m and secondly the hub gearing allows the axle half shafts to Where allowable stress = drive the same power but at reduced torque (by using higher σ = S / 3 = 150 MPa .. For Steel, S = 450 MPa shaft speed). This reduces load on the axle crown wheel and ut ut Velocity factor = differential.