The Recovery and Concentration of Spodumene Using Dense Media Separation
Total Page:16
File Type:pdf, Size:1020Kb
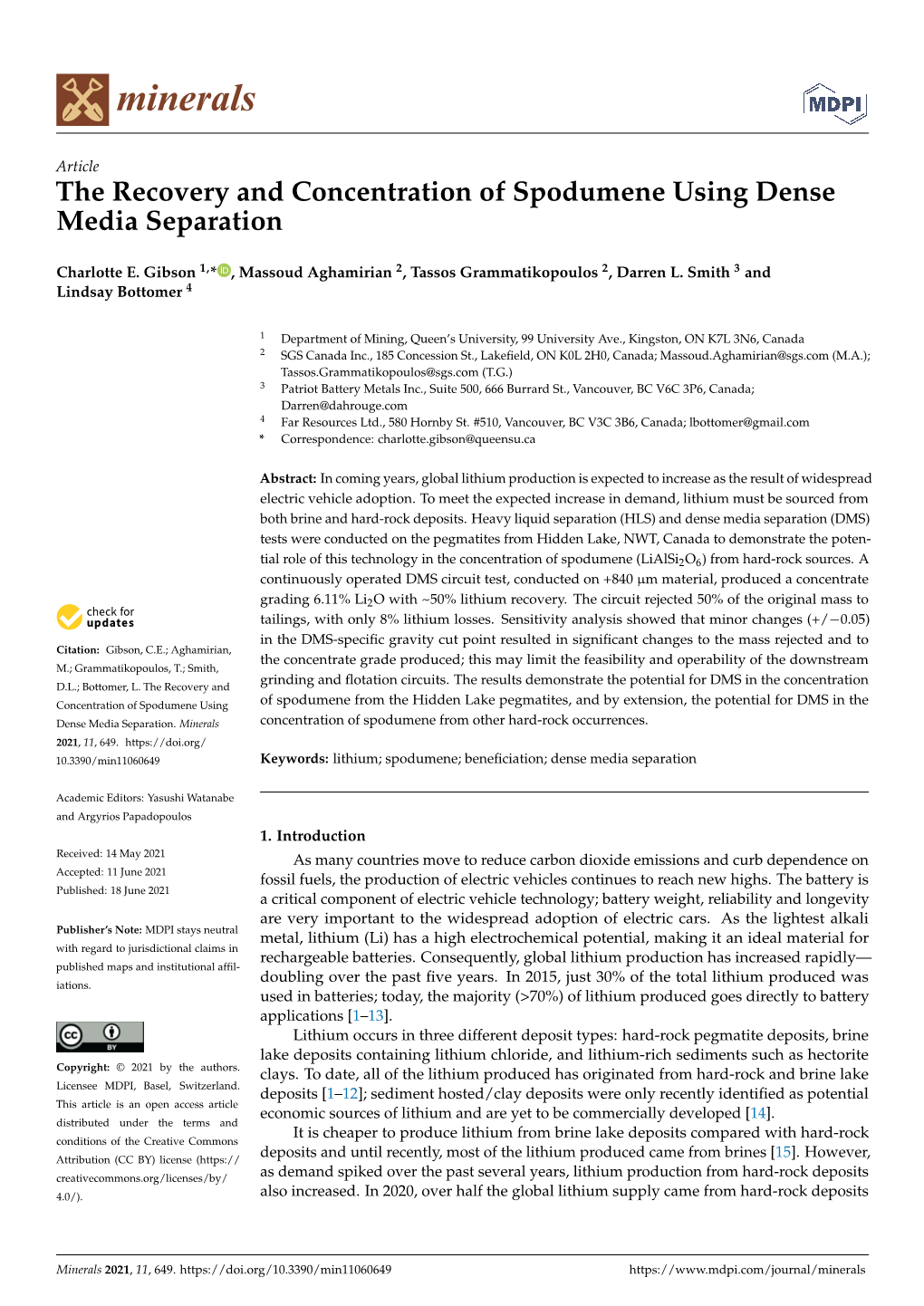
Load more
Recommended publications
-
Manufacturing Scalability Implications of Materials Choice in Inorganic Solid-State Batteries Abstract Context & Scale Intro
1 Manufacturing Scalability Implications of Materials Choice in Inorganic 2 Solid-State Batteries 3 Kevin J. Huang1, Gerbrand Ceder2, Elsa A. Olivetti1* 4 5 1Department of Materials Science & Engineering, MIT, Cambridge, MA 02139; 2Department of Materials 6 Science & Engineering, University of California Berkeley, Berkeley, CA 94720, USA 7 Abstract 8 The pursuit of scalable and manufacturable all-solid-state batteries continues to intensify, motivated by the 9 rapidly increasing demand for safe, dense electrical energy storage. In this Perspective, we describe the 10 numerous, often conflicting, implications of materials choices that have been made in the search for 11 effective mitigations to the interfacial instabilities plaguing solid-state batteries. Specifically, we show that 12 the manufacturing scalability of solid-state batteries can be governed by at least three principal 13 consequences of materials selection: (1) the availability, scaling capacity, and price volatility of the chosen 14 materials’ constituents, (2) the manufacturing processes needed to integrate the chosen materials into full 15 cells, and (3) the cell performance that may be practically achieved with the chosen materials and processes. 16 While each of these factors is, in isolation, a pivotal determinant of manufacturing scalability, we show that 17 consideration and optimization of their collective effects and tradeoffs is necessary to more completely 18 chart a scalable pathway to manufacturing. 19 Context & Scale 20 With examples pulled from recent developments in solid-state batteries, we illustrate the consequences of 21 materials choice on materials availability, processing requirements and challenges, and resultant device 22 performance. We demonstrate that while each of these factors is, by itself, essential to understanding 23 manufacturing scalability, joint consideration of all three provides for a more comprehensive understanding 24 of the specific factors that could impede the scale up to production. -
Alteration of Spodumene, Montebrasite and Lithiophilite In
American Mineralogist, Volume 67, pages 97-113, 1982 Alteration of spodumene,montebrasite and lithiophilite in pegmatites of the White PicachoDistrict, Arizona Davrp Lor.rooxrnNo DoNer-uM. Bunr Department of Geology Arizona State University Tempe, Arizona 85281 Abstract The crystallization sequence and metasomatic alteration of spodumene (LiAlSizOe), montebrasite(LiAIPO4(OH,F)), and lithiophilite (Li(Mn,Fe)PO+)are describedfor nine zoned lithium pegmatitesin the White Picacho district, Arizona. The observedcrystalliza- tion trends suggesta progressiveincrease in the activities of lithium species(spodumene follows microcline as the principal alkali aluminosilicate), as well as an increase in the activities of the acidic volatiles phosphorus and fluorine (montebrasite succeedsspodu- mene as the stableprimary lithium phase).Much of the lithiophilite occurs with columbite, apatite, beryl, zircon, and tourmaline in cleavelanditecomplexes that formed in part at the expenseof quartz-spodumenepegmatite. Fracture-controlledpseudomorphic alteration of the primary lithium minerals is widespread and apparently is the result of subsolidus reactionswith residualpegmatitic fluids. Spodumenehas been replacedby eucryptite, albite, and micas. Alteration products of montebrasite include low-fluorine secondary montebrasite,crandallite (tentative), hydroxylapatite, muscovite, brazilianite, augelite (tentative),scorzalite, kulanite, wyllieite, and carbonate-apatite.Secondary phases identi- fied in altered lithiophilite include hureaulite, triploidite, eosphorite, -
Research Article LITHIUM TETRABORATE PRODUCTION from the REACTION of BORIC ACID and LITHIUM CARBONATE USING CARBON DIOXIDE Ali Y
Sigma J Eng & Nat Sci 38 (3), 2020, 1121-1132 Sigma Journal of Engineering and Natural Sciences Sigma Mühendislik ve Fen Bilimleri Dergisi Research Article LITHIUM TETRABORATE PRODUCTION FROM THE REACTION OF BORIC ACID AND LITHIUM CARBONATE USING CARBON DIOXIDE Ali YALÇIN1, Mehmet GÖNEN*2 1Süleyman Demirel University, Dept. of Chemical Engineering, ISPARTA; ORCID: 0000-0002-8722-4159 2Süleyman Demirel University, Dept. of Chemical Engineering, ISPARTA; ORCID: 0000-0001-5780-4622 Received: 26.02.2020 Revised: 30.03.2020 Accepted: 22.05.2020 ABSTRACT In this study, the synthesis of lithium tetraborate in the presence of carbon dioxide (CO2) in an aqueous phase was investigated. A two-step process has been developed in the present study. The first step includes an aqueous phase reaction of lithium carbonate and boric acid in the presence of CO2 at different pressures. The second step involves the crystallization and thermal treating of the product obtained from step one at the temperatures between 300 and 400°C for 1 hour. Characterizations of the samples were performed by Fourier Transform Infrared Spectroscopy (FTIR), X-Ray Diffraction (XRD), Thermogravimetric Analysis (TGA) and Scanning Electron Microscopy (SEM). It was characterized that amorphous lithium tetraborate of Li2B4O7.3H2O was synthesized in the first step and then it was converted into Li2B4O7 in the second step. The use of CO2 as a modifying agent in lithium tetraborate synthesis has enhanced the dissolution rate of reactants that induced a fast-aqueous phase reaction. Keywords: Lithium tetraborate, boric acid, CO2, lithium carbonate, two-step process. 1. INTRODUCTION Lithium borates are important compounds that are used as specialty chemicals in the industry. -
Lithium in Lithium-Ion Batteries for Electric Vehicles
Office of Industries Working Paper ID-069 July 2020 Global Value Chains: Lithium in Lithium-ion Batteries for Electric Vehicles Gregory M. LaRocca Abstract Lithium is an essential material in the production of lithium-ion batteries (LIBs), which power electric vehicles. This paper examines the global value chain (GVC) for lithium as part of a series of working papers that map out the global sources of mining, refining, and value-added for the key LIB materials. Results show that few countries have economically viable resources of the upstream raw materials that supply the lithium GVC. Most lithium-rich ores are exported from Australia to China for processing, while most lithium brine concentrates are exported from Chile to South Korea, Japan, and China for processing. The large inflows of lithium to China support its dominant position in the downstream refining process, which is where the largest share of value-added occurs. Consequently, China is capturing the largest shares of value-added along the lithium GVC, despite lacking in resource endowment. Disclaimer: Office of Industries working papers are the result of the ongoing professional research of USITC staff and solely represent the opinions and professional research of individual authors. These papers do not necessarily represent the views of the U.S. International Trade Commission or any of its individual Commissioners. U.S. International Trade Commission Global Value Chains: Lithium in Lithium-ion Batteries for Electric Vehicles Gregory M. LaRocca Office of Industries U.S. International Trade Commission (USITC) July 2020 The author is staff with the Office of Industries of the U.S. -
Zinnwald Lithium Project
Zinnwald Lithium Project Report on the Mineral Resource Prepared for Deutsche Lithium GmbH Am St. Niclas Schacht 13 09599 Freiberg Germany Effective date: 2018-09-30 Issue date: 2018-09-30 Zinnwald Lithium Project Report on the Mineral Resource Date and signature page According to NI 43-101 requirements the „Qualified Persons“ for this report are EurGeol. Dr. Wolf-Dietrich Bock and EurGeol. Kersten Kühn. The effective date of this report is 30 September 2018. ……………………………….. Signed on 30 September 2018 EurGeol. Dr. Wolf-Dietrich Bock Consulting Geologist ……………………………….. Signed on 30 September 2018 EurGeol. Kersten Kühn Mining Geologist Date: Page: 2018-09-30 2/219 Zinnwald Lithium Project Report on the Mineral Resource TABLE OF CONTENTS Page Date and signature page .............................................................................................................. 2 1 Summary .......................................................................................................................... 14 1.1 Property Description and Ownership ........................................................................ 14 1.2 Geology and mineralization ...................................................................................... 14 1.3 Exploration status .................................................................................................... 15 1.4 Resource estimates ................................................................................................. 16 1.5 Conclusions and Recommendations ....................................................................... -
Ore Deposits
EARTH SCIENCES RESEARCH JOURNAL Earth Sci. Res. J. Vol. 20, No. 3 (September, 2016 ) : A1 - A10 ORE DEPOSITS Occurrence of Cr-bearing beryl in stream sediment from Eskişehir, NW Turkey Hülya Erkoyun and Selahattin Kadir * Eskişehir Osmangazi University, Deparment of Geological Engineering, TR−26480 Eskişehir, Turkey [email protected] [email protected] *corresponding author ABSTRACT Keywords: Beryl, Kaymaz, schist, SEM-EDX, IR. Beryl crystals are found within stream sediments transecting schists in the northeast of Eskişehir, western Anatolia. This paper studied the Eskişehir beryl crystals with optical microscopy, scanning electron microscopy (SEM-EDX), infrared spectroscopy (IR) and geochemical analyses. Beryl is accompanied by garnet, glaucophane, quartz, epidote, muscovite and chlorite in the stream sediments. The crystals are euhedral emerald (green gem beryl) and light bluish- green aquamarine, with ideal sharp IR bands. Wet chemical analysis of Eskişehir beryl yielded 61.28% SiO2, 15.13% Al2O3, 12.34% BeO, 0.18% Cr2O3, 1.49% MgO, 1.69% Na2O, 0.98% Fe2O3, and 0.008% V2O3, resulting in the formula (Al1.75Cr0.01Mg0.22Fe0.08)(Be2.90Si6.00)(Na0.32)O18. Large Ion Lithophile Elements (LILE) (barium, strontium), some transition metals (cobalt, except nickel) and High Field Strength Elements (HFSE) (niobium, zirconium, and yttrium) in stream sediments that are associated with beryl exhibited low content about metamorphic rocks. Beryl formation appears to be controlled by upthrust faults and fractures that juxtaposed them with Cr-bearing ophiolitic units and a regime of metasomatic reactions. Such beryl crystals have also been found in detrital sediments that are derived from the schists. Presencia de berilios relacionados con Cromo en corrientes sedimentarias de Eskisehir, noroeste de Turquía RESUMEN Cristales de berilio fueron encontrados en sedimentos de corrientes que atraviesan en esquistos en el noreste de Palabras clave: Berilio, Kaymaz, esquistos, Eskisehir, al oeste de Anatolia. -
Lithium 2017
2017 Minerals Yearbook LITHIUM [ADVANCE RELEASE] U.S. Department of the Interior September 2020 U.S. Geological Survey Lithium By Brian W. Jaskula Domestic survey data and tables were prepared by Annie Hwang, statistical assistant. In the United States, one lithium brine operation with an cobalt oxide and 2,160 kg of lithium-nickel-cobalt-aluminum associated lithium carbonate plant operated in Silver Peak, oxide (Defense Logistics Agency Strategic Materials, 2017). At NV. Domestic and imported lithium carbonate, lithium yearend 2017, the NDS held 540 kg of lithium-cobalt oxide and chloride, and lithium hydroxide were consumed directly 1,620 kg of lithium-nickel-cobalt-aluminum oxide. in industrial applications and used as raw materials for downstream lithium compounds. In 2017, lithium consumption Production in the United States was estimated to be equivalent to The U.S. Geological Survey (USGS) collected domestic 3,000 metric tons (t) of elemental lithium (table 1) [16,000 t production data for lithium from a voluntary canvass of the of lithium carbonate equivalent (LCE)], primarily owing to only U.S. lithium carbonate producer, Rockwood Lithium Inc. demand for lithium-based battery, ceramic and glass, grease, (a subsidiary of Albemarle Corp. of Charlotte, NC). Production pharmaceutical, and polymer products. In 2017, the gross weight and stock data collected from Rockwood Lithium were withheld of lithium compounds imported into the United States increased from publication to avoid disclosing company proprietary data. by 7% and the gross weight of exports increased by 29% from The company’s 6,000-metric-ton-per-year (t/yr) Silver Peak those in 2016. -
Global Lithium Sources—Industrial Use and Future in the Electric Vehicle Industry: a Review
resources Review Global Lithium Sources—Industrial Use and Future in the Electric Vehicle Industry: A Review Laurence Kavanagh * , Jerome Keohane, Guiomar Garcia Cabellos, Andrew Lloyd and John Cleary EnviroCORE, Department of Science and Health, Institute of Technology Carlow, Kilkenny, Road, Co., R93-V960 Carlow, Ireland; [email protected] (J.K.); [email protected] (G.G.C.); [email protected] (A.L.); [email protected] (J.C.) * Correspondence: [email protected] Received: 28 July 2018; Accepted: 11 September 2018; Published: 17 September 2018 Abstract: Lithium is a key component in green energy storage technologies and is rapidly becoming a metal of crucial importance to the European Union. The different industrial uses of lithium are discussed in this review along with a compilation of the locations of the main geological sources of lithium. An emphasis is placed on lithium’s use in lithium ion batteries and their use in the electric vehicle industry. The electric vehicle market is driving new demand for lithium resources. The expected scale-up in this sector will put pressure on current lithium supplies. The European Union has a burgeoning demand for lithium and is the second largest consumer of lithium resources. Currently, only 1–2% of worldwide lithium is produced in the European Union (Portugal). There are several lithium mineralisations scattered across Europe, the majority of which are currently undergoing mining feasibility studies. The increasing cost of lithium is driving a new global mining boom and should see many of Europe’s mineralisation’s becoming economic. The information given in this paper is a source of contextual information that can be used to support the European Union’s drive towards a low carbon economy and to develop the field of research. -
Spectral Evolution Lithium Exploration
spectral evolution Lithium Exploration Used in batteries, lighting and other technologically critical appli- cations, lithium is exceptionally light with a high specific heat capacity and high electrochemical potential. Lithium is typically recovered from brines or minerals in pegmatites. Finding poten- tial lithium deposits in pegmatites can involve identifying the minerals lepidolite and spodumene. With EZ-ID mineral identification software, the oreXpress, oreX- plorer and oreXpert can provide geologists with tools for identi- Ore sample from Australia fying and mapping potential lithium deposits in the field. The oreXpress is a high resolution/high sensitivity, field portable NIR spectrometer. Covering the full UV/VIS/NIR range from 350-2500nm, an oreXpress is lightweight and rugged with photo- diode array design for no moving optical parts. oreXpress allows a geologist to take spectra in the field within seconds so that a detailed mineral map can be constructed. Scans of a sample taken with an oreXpress and a contact probe can be analyzed on a lap- top using Spectral Evolution’s EZ-ID mineral identification soft- ware and matching to known samples from the USGS, SPECMin and GeoSPEC libraries. Identifying the mineral lepidolite using Spectral Evolution’s EZ-ID software In a sample from Australia, a lepidolite scan collected with the oreXpress and identified with EZ-ID shows a water feature at 1400nm, and absorption features at 2190nm and 2340nm that could indicate lepidolite or a short wavelength white mica. EZ-ID software matches the measured spectra (blue line) to a sample from the SPECMin library (red line) of lepidolite for possible identification. The second spectra shows absorption features at 550nm, 1400nm, 1910nm and 2220nm with a match to a spodumene Spodumene is a mineral associated with sample in the SPECMin library with a 0. -
Geology of the Pegmatites and Associated Rocks of Maine
DEPARTMENT OF THE INTERIOR UNITED STATES GEOLOGICAL SURVEY GEORGE OTIS SMITH, DIRECTOR BULLETIN 445 GEOLOGY OF THE PEGMATITES AND ASSOCIATED ROCKS OF MAINE INCLUDING FELDSPAR, QUARTZ, MICA, AND GEM DEPOSITS BY EDSON S. BASTIN WASHINGTON GOVERNMENT PRINTING OFFICE 1911 CONTENTS. Introduction.............................................................. 9 Definition of pegmatite...................................................... 10 Geographic distribution.................................................... 10 Geology.................................................................. 10 Bordering rocks....................................................... 10 Pegmatites in foliated rocks........................................ 11 General statement............................................ 11 Sedimentary foliates........................................... 11 Igneous foliates.....".......................................... 12 Pegmatites in massive granites.................................... 13 'Age.................................................................. 15 General character..................................................... 15 Mineral and chemical composition................................. 15 Mineral constituents.......................................... 15 Relative proportions of minerals............................... 18 Quartzose phases. ..............................^............. 18 Fluidal cavities............................................... 19 Sodium and lithium phases................................... 20 Muscovite -
Spodumene and Quartz Intergrowth – Textural and Genesis Point of View
Geophysical Research Abstracts Vol. 21, EGU2019-13404, 2019 EGU General Assembly 2019 © Author(s) 2019. CC Attribution 4.0 license. Spodumene and Quartz Intergrowth – Textural and Genesis Point of View Alexandre Lima and Filipa Dias Faculty of Sciences of University of Porto, Institute of Earth Sciences, Pole of University of Porto (Portugal) ([email protected]) The observation of spodumene quartz intergrowth both in the field and in microscopy is a common texture found in Lithium-rich pegmatites from different parts around the world. However, this texture may result from different environments of formation, it may be a primary texture or a secondary texture resultant from secondary reactions or posterior deformation. This study will approach the meaning of these terminologies and how different types of spodumene and quartz intergrowth can have similar textures but completely different conditions of formation. The amazing variety of textures and crystal morphologies in pegmatites are related to the crystal growth rate and to the degree of undercooling of the pegmatitic melt (the difference between the liquidus temperature and the actual temperature of the magma) resultant from non-equilibrium kinetic factors (Vernon, 2004; Webber and Simmons, 2007; London, 2008). The fact that pegmatites with symplectites of SQI originated from petalite seems to indicate that the rock after being solid still had some time at an elevated temperature to try to re-equilibrate its mineral phases while cooling down, indicating a low-to-moderate degree of undercooling. Another indication for its relatively low degree of undercooling is the lack of abundant textures reflecting a high degree of undercooling, such as skeletal, and radial crystals morphologies. -
Alkaline Process for Extracting Lithium from Spodumene
Alkaline Process for Extracting Lithium from Spodumene Paulo Braga1, Silvia França1, Reiner Neumann1, Mario Rodriguez2 and Gustavo Rosales2 1. Center for Mineral Technology (CETEM), Brazil 2. Laboratory of Extractive Metallurgy and Materials Synthesis, Universidad Nacional de Cuyo, Argentina ABSTRACT The growing market demand for lithium is mainly due to its use in the manufacture of batteries for electric or hybrid vehicles and portable equipment (cellphones, tablets, power tools, notebooks, etc.). Currently there is great interest in finding new sources of lithium and technologies for its utilization. Brazil has large lithium pegmatite reserves and spodumene is the most important commercially mined lithium mineral. There are two main routes to obtain lithium carbonate and lithium hydroxide from mineral concentrates. In the first - the acid process - the mineral concentrate is roasted, sulfated with sulfuric acid and leached with water. Soda ash is added to form lithium carbonate. In the second process - the alkaline one - the mineral concentrate is roasted with lime or limestone, forming a clinker which is leached with water, filtered and crystallized as lithium hydroxide monohydrate. In Brazil, only the acidic process is used, although lithium hydroxide is the product most in demand in the domestic market, used mainly by automotive lubricant manufacturers. Lithium hydroxide is the main product in the alkaline process. The processing of spodumene concentrate to produce lithium hydroxide via the alkaline process can provide advantages to the production process, especially by replacing expensive chemicals such as sulfuric acid and soda ash with products such as limestone or hydrated lime, which are produced domestically and have more affordable prices.