Motor Control Part 1 the Basics of Protection and Control
Total Page:16
File Type:pdf, Size:1020Kb
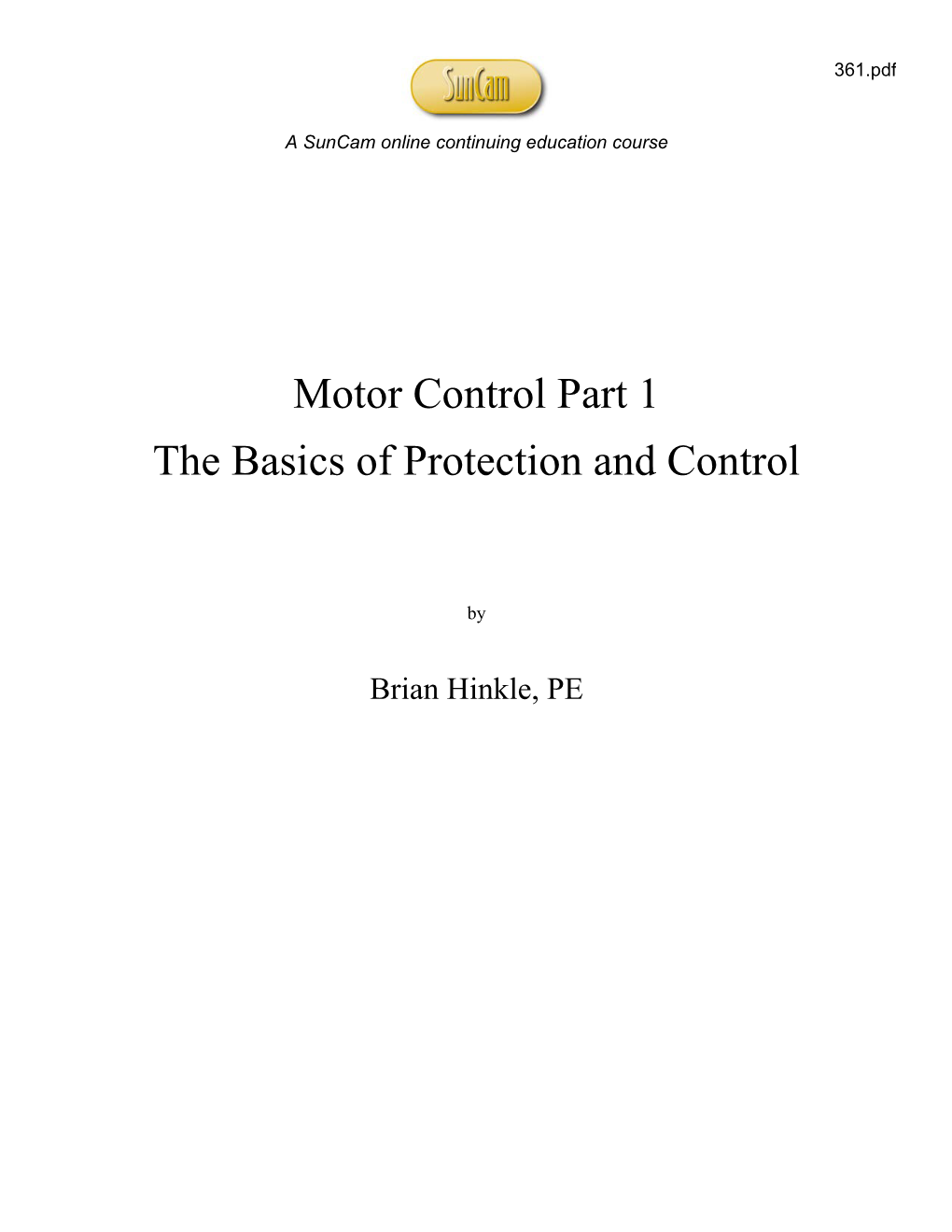
Load more
Recommended publications
-
ER2 Manual 125Kg – 5T
ER2 Series Electric Chain Hoist OM-ER2ZZZ-CEE-02 Original Instruction (125kg to 5t) (125kg Owner's Manual ER2 Series Electric Chain Hoist (125kg to 5t) Owner's Manual Hook Suspended Type (hoist only) : ER2 Motorized Trolley Type : ER2M Manual Trolley Type : ER2SP/ER2SG Global Website: kito.com KITO Europe GmbH Heerdter Lohweg 93, D-40549 Düsseldorf, Germany TEL: +49-(0)211-528009-00 FAX: +49-(0)211-528009-59 E-mail: [email protected] URL: http://www.kito.net/ To Customer • Thank you for purchasing KITO Electric Hoist (ER2). KITO corporation Tokyo Head Office: • Operators and maintenance engineers are requested to read this manual. SHINJUKU NS Building 9F, 2-4-1, Nishi-Shinjuku, Shinjuku-ku, Tokyo 163-0809, Japan After reading, please keep this manual at hand for future use. URL: http://kito.com/ • This product is designed considering the environment protection. The product contains none of six hazardous Head Office & Factory: substances specified by European RoHS Directives nor asbestos. 2000 Tsuijiarai Showa-Cho, Nakakoma-Gun, Yamanashi 409-3853, Japan URL: http://kito.com/ Utilizing 70% post-consumer recycled paper pulp Table of Contents DECLARATION OF CONFORMITY Introduction ............................................................................................2 Safety Precautions ................................................................................4 Chapter 1 Handling the Product ..........................................................7 Chapter 2 Inspection ..........................................................................63 -
Hitachi Electromagnetic Contactors & Switches
ELECTROMAGNETIC CONTACTORS AND SWITCHES CONTENTS ELECTROMAGNETIC CONTACTORS AND SWITCHES ................................................ 4 1. TYPES AND MODEL ARRANGEMENTS OF ELECTROMAGNETIC CONTACTORS AND SWITCHES ...................... 4 2. FEATURES OF NEW ELECTROMAGNETIC CONTACTORS AND SWITCHES (HS series) ............................ 5 3. FEATURES OF STANDARD TYPE ELECTROMAGNETIC CONTACTORS AND SWITCHES (H series) ...................... 7 4. RATINGS AND SPECIFICATIONS ....................................................... 10 4-1 Standard Models ........................................................... 10 4-2 Thermal Overload Relays ....................................................... 12 4-3 Electromagnetic Switches with 2E Thermal Overload Relay .................................... 14 4-4 DC Operated Electromagnetic Contactors .............................................. 16 4-5 Latched Electromagnetic Contactors ................................................ 18 4-6 Contactor Relays ........................................................... 20 5. STANDARD TYPE ELECTROMAGNETIC CONTACTORS AND SWITCHES .................................. 22 5-1 Coil Specifications ........................................................... 22 5-2 Performance .............................................................. 22 5-3 Application for the International Standards ............................................. 22 5-4 Normal Service Conditions ...................................................... 22 5-5 Selection ............................................................... -
Inc. Mercury & Solid State Contactors • Relays
,INC. MERCURY & SOLID STATE CONTACTORS • RELAYS • SWITCHES • LIQUID LEVEL CONTROL FLOATS Catalog X Courtesy of Steven Engineering, Inc.-230 Ryan Way, South San Francisco, CA 94080-6370-Main Office: (650) 588-9200-Outside Local Area: (800) 258-9200-www.stevenengineering.com GENERAL INFORMATION FEATURES AND SELECTION FACTORS GENERAL INFORMATION to prevent moisture damage and voltage breakdown through the Mercury Displacement Relays are all designed and built to meet the protective coating. most exacting demands of the industry. They have won their high The coils are wound on compact nylon bobbins and molded on place in the electrical field by doing the tough and tricky jobs that to the metal tube to provide minimum power loss. This allows for ordinary equipment could at best do in an uncertain manner. They low coil power required to actuate the contactor. This also enables have proven their ability to stand up to the most adverse conditions the units to handle high loads with minimum derating due to higher of temperature, dust and moisture, in all types of applications. All the ambient temperatures. care required for the manufacture of high-grade instruments is used Internal gasses prevent excessive arcing between the mercury and in the manufacture of the switches. All switch parts are specially the electrodes which enables the unit to function for millions of cycles cleaned, and contamination is avoided by use of tweezers, gloves, with very low contact resistance, and minimum deterioration of the etc., when making assemblies. internal parts. Contactors are hermetically sealed with high quality glass to metal Available in all standard coil voltages, in single, two, three and four seals. -
The Study on the Design of Low Voltage AC Contactor in the Electrical System and the Control Applications
4th International Conference on Mechatronics, Materials, Chemistry and Computer Engineering (ICMMCCE 2015) The Study on the Design of Low voltage AC Contactor in the Electrical System and the Control Applications Bao-ying Wang1,a 1Chongqing College of Electronic Engineering, Chongqing, 401331, China [email protected] Keywords: Electrical system; Low voltage AC contactor; Control; Design Abstract. The contactor is a kind of main circuit used to frequent connected and cut off and the large capacity control electronics, due to the AC and DC main circuit quickly cut off, and it can frequent switch the large current control circuit, so often be used to control motor, still can be used for machine tools, factory equipment and other electric power load control. Low voltage AC contactor is mainly used for on-off power electric equipment, can remote control the power devices, power on and off equipment to avoid personal injury. The low voltage AC contactor is mainly used for on-off power electric equipment, can remote control the power device, when the on and off equipment the power supply to avoid personal injury. The selection of AC contactor for the normal operation of the power equipment and power lines is Very important. This article puts forward the electrical design process when choosing low voltage AC contactor need to consider the main factors. Introduction The contactor can not only control of the circuit to connect and breaking also has the effect of release and protection. Contactor's main contact concatenated in the load circuit, used to load the large current in the circuit connected and breaking, after the contactor coil for electricity excitation, the smaller the excitation current can produce enough to touch the armature magnetic suction, drive the movable contact movement to perform the function of on and off. -
IEC Contactor Specifications
Technical Data Original Instructions IEC Contactor Specifications Bulletin Numbers 100/104-K, 100/104-C, 100/104S-C, 100/104-E, 100S-E, 100Q-C Topic Page Summary of Changes 2 Product Line Overview 3 IEC Contactors 3 Safety Contactors 4 100-K/104-K Miniature Contactors 5 Product Selection 5 Accessories 8 Specifications 11 Life-Load Curves 15 Approximate Dimensions 16 100-C/104-C, 100S-C/104S-C, 100Q-C Contactors 17 Product Selection—100-C/104-C Contactors 17 Product Selection—100S-C/104S-C Safety Contactors 22 Product Selection—100Q-C Capacitor-switching Contactors 30 Accessories 31 Renewal Parts 36 Specifications 38 Life-Load Curves 49 Approximate Dimensions 56 100-E/104-E, 100S-E/104S-E Contactors 59 Product Selection—100-E/104-E Contactors 59 Product Selection—100S-E Safety Contactors 62 Accessories 66 Renewal Parts 73 Specifications 75 Life-Load Curves 96 Approximate Dimensions 101 Additional Resources 113 Summary of Changes This publication contains the following new or updated information. This list includes substantive updates only and is not intended to reflect all changes. Topic Page Corrected pkg. qty. for mechanical interlocks 68 Corrected Cat. Nos. for mechanical latches 69 2 Rockwell Automation Publication 100-TD013J-EN-P - April 2021 Product Line Overview IEC Contactors Bulletin No. 100-K/104-K 100-C/104-C 100-E/104-E Screw Terminals (9…96 A), Thru-hole (116…2650 A) Spring Terminals (5…9 A) (9…16 A) — Max.Current Ie 12 A 97 A 2650 A Current Rating 5…12 A9…97 A9…2650 A • Panel mounting or mounting on 35 mm DIN • Mini-contactors -
IEC Contactor Specifications Bulletin Numbers 100/104-K, 100/104-C, 100/104S-C, 100/104-D, 100S-D, 100-G, 100Q-C
Technical Data IEC Contactor Specifications Bulletin Numbers 100/104-K, 100/104-C, 100/104S-C, 100/104-D, 100S-D, 100-G, 100Q-C Topic Page Product Line Overview 3 100-K/104-K Miniature Contactors 5 Coil Voltage Codes 5 Assignment of Contacts 6 Specifications 8 Life-Load Curves 12 Approximate Dimensions 14 100-C/104-C, 100S-C/104S-C, 100Q-C Contactors 15 Coil Voltage Codes 15 Assignment of Contacts 18 Specifications 25 Life-Load Curves 36 Maximum Operating Rates 42 Approximate Dimensions 46 100-D/104-D, 100S-D Contactors 51 Coil Voltage Codes 51 Specifications 53 Life-Load Curves 63 Approximate Dimensions 65 100-G Contactors 67 Coil Voltage Codes 67 Specifications 67 Life-Load Curves 73 Permissible Switching Rate 75 Approximate Dimensions 77 IEC Contactor Specifications Additional Resources These documents contain additional information concerning related products from Rockwell Automation. Resource Description Industrial Automation Wiring and Grounding Guidelines, publication 1770-4.1 Provides general guidelines for installing a Rockwell Automation industrial system. Product Certifications website, http://www.ab.com Provides declarations of conformity, certificates, and other certification details. You can view or download publications at http://www.rockwellautomation.com/literature/. To order paper copies of technical documentation, contact your local Allen-Bradley distributor or Rockwell Automation sales representative. 2 Rockwell Automation Publication 100-TD013E-EN-P - June 2015 Product Line Overview IEC Contactors Bulletin No. 100-K/104-K -
UNDERSTANDING ELECTRICAL SCHEMATICS Part 2
Refrigeration Service Engineers Society 1666 Rand Road Des Plaines, Illinois 60016 UNDERSTANDING ELECTRICAL SCHEMATICS Part 2 by Howard L. Pemper, CMS INTRODUCTION for example, shows both a normally open and a nor- mally closed single-pole, single-throw (SPST) switch. In this section, you will take a look at a packaged This type of switch either opens or closes one circuit. gas/electric system, which is a relatively complex Figure 1B shows a single-pole, double-throw (SPDT) heating and cooling unit. The wiring diagram for this switch. Again, only one circuit can be controlled at equipment is more difficult than those you studied in any given time, but in this case the switch has two dif- Part 1—but again, the schematic as a whole can be ferent “connected” positions, which means that it can simplified by breaking it down into its basic circuits. direct current to either of two paths. As you examine individual control circuits and the associated components that they operate, the overall diagram becomes easier to understand, as do the A. Single-pole, single-throw (SPST) various machine functions. The schematics in this section may include some symbols with which you are not familiar. For your convenience, many of the Normally closed (N/C) schematic symbols currently used and recognized by the HVAC/R industry are collected in Figure 16 at the end of this chapter. Normally open (N/O) SWITCH SYMBOLS B. Single-pole, double-throw (SPDT) Generally speaking, a wiring schematic shows the condition of a piece of equipment when there is no power being applied to the unit. -
Controls – Contactors and Contactor Assemblies
LV1_03.book Seite 1 Freitag, 25. Januar 2008 2:37 14 © Siemens AG 2008 Controls – Contactors and Contactor Assemblies 3/2 Introduction 3RH, 3TH Contactor Relays 3/69 3RH1 contactor relays, 4- and 8-pole 3RT, 3TB, 3TF Contactors 3/72 3RH14 latched contactor relays, 4-pole for Switching Motors 3/73 3TH4 contactor relays, 8- and 10-pole 3/5 General data 3/11 3RT10 contactors, 3-pole, 3 ... 250 kW 3/75 3TH2 contactor relays, 4- and 8-pole 3/26 3RT12 vacuum contactors, 3-pole, 3/78 3RH11 coupling relays for switching 110 ... 250 kW auxiliary circuits, 4-pole 3/27 3TF6 vacuum contactors, 3-pole, 335 ... 450 kW 3RT Coupling Relays 3/29 3TB5 contactors with DC solenoid system, 3/79 3RT10 coupling relays (interface), 3-pole, 55 ... 200 kW for switching motors, 3-pole, 3 ... 11 kW 3/30 3TF2 contactors, 3-pole, 2.2 ... 4 kW 3TX7, 3RS18 Coupling Relays 3RA13, 3RA14 Contactor Assemblies 3TX7 Coupling Relays, Narrow Design 3RA13 Reversing Contactor Assemblies 3/82 Relay couplers 3/32 3RA13 complete units, 3 ... 45 kW 3/84 Relay couplers with plug-in connection 3/37 Components for customer assembly 3/86 Semiconductor couplers 3RA14 Contactor Assemblies for 3RS18 Coupling Relays with Wye-Delta Starting Industrial Housing 3/40 3RA14 complete units, 3 ...75 kW 3/88 Relay couplers 3/47 Components for customer assembly 3TD, 3TE Contactor Assemblies LZS, LZX Plug-In Relays 3/48 3TD6 reversing contactor assemblies, 3/89 Relay couplers 335 kW 3TG10 Power Relays/Miniature 3/49 3TE6 contactor assemblies for wye-delta Contactors starting, 630 kW 3/96 4-pole, 4 kW 3RT, 3RH, 3TB, 3TC, 3TH, 3TK Contactors for Special Applications Accessories and Spare Parts 3RT14 Contactors for Switching Resistive For 3RT, 3RH Contactors and Loads (AC-1) Contactor Relays 3/50 3-pole, 140 .. -
Guidelines for Contactor Inspection and Maintenance ABB A/AF-Line
Manual Guidelines for Contactor inspection and maintenance ABB A/AF-line and EH/EK series Contactors The purpose of this manual is to provide guidance for correct selection and maintenance of contactors in in- dustrial installations to ensure a trouble free operation. This without increasing the overall cost. 2 ABB Contactor Manual | 1SFC101044M0201, rev B 1SFC101044M0201, rev B | ABB Contactor Manual 3 Contents Some general advice.......................................................4 Mechanical wear..............................................................5 Maintenance of contacts.................................................6 Interpreting levels of electrical contact wear AC-1............................................................................... 7 AC-2 ..............................................................................7 AC-3 ..............................................................................8 AC-4 ..............................................................................9 Changing main contacts, arc chutes and coils..............10 Trouble shooting..............................................................11 Spare parts and warranty claims....................................14 Contactor parts terminology...........................................15 1SFC101044M0201, rev B | ABB Contactor Manual 3 Some general advice 1. Choose correctly 3. Storage and climate • Nature of the duty Consider the immediate environment • Positioning of the contactor (variable temperatures, humidity, storage • Voltage -
Introduction Contactor Components
Introduction A contactor is an electrical device which is used for switching an electrical circuit on or off. It is considered to be a special type of relay. However, the basic difference between the relay and contactor is that the contactor is used in applications with higher current carrying capacity, whereas the relay is used for lower current applications. Contactors can be field mounted easily and are compact in size. Generally, these electrical devices feature multiple contacts. These contacts are in most cases normally open and provide operating power to the load when the contactor coil is energized. Contactors are most commonly used for controlling electric motors. There are various types of contactors, and each type has its own set of features, capabilities, and applications. Contactors can break current over a wide range of currents, from a few amperes to thousands of amperes, and voltages from 24 VDC to thousands of volts. In addition, these electrical devices come in varying sizes, from hand-held dimensions to sizes measuring a meter or yard on one side (approximately). The most common application area of the contactor is high-current load. Contactors are known for their capability to handle currents of over 5000 amperes and high power over 100 kW. Heavy motor currents produce arcs when being interrupted. These arcs can be reduced and controlled using a contactor. Contactor Components The following three are crucial components of the contactor: 1. Coil or Electromagnet: This is the most crucial component of a contactor. The driving force that is required to close the contacts is provided by the coil or electromagnet of the contactor. -
Contactors and Starters
Contactors and starters xStart series contactors xStart series 1 1.1 xStart series contactors 2 Mini contactor relays, contactor relay . 1 Contactors DIL . 1 1.2 xStart series overload relays Bimetal relay ZE, ZB, Z5 . 2 Overload relay ZW7 . 2 Electronic overload relays ZEB . 4 EMT6 thermistor overload relay for machine protection . 4 C441 overload and monitoring relay . 37 xStart series overload relays 1.3 xStart series motor-protective circuit-breakers Motor-protective circuit-breakers PKZ . 3 Motor-protective circuit-breakers PKE . 8 DC string circuit-breaker PKZ-SOL . 47 DC switch-disconnectors P-SOL, SOL . 47 1.4 Motor-starter combinations Motor-starter combinations . 1 Motor protective circuit breaker PKZ E Line series 2.1 E Line contactors Control relays XTRG . 1 Contactors XTCG . 6 2.2 E Line thermal overload relay Thermal overload relays XTOD/XTOG . 13 Motor-starter combinations E Line contactors E Line thermal overload relay 1 Mini contactor relays, contactor relay, contactors Continual operation requires high operational reliability in the components used. The DILM contactor achieves the best lifespan values in AC-3 applications and is ideal for heavy AC-4 jogging. Mini contactor relay DILE…,contactor relays, contactors up to 12 A AC-3 at 400 V • Compact dimensions for the highest packing densities • Extended performance range up to 5.5 kW at 400 V AC and DC contactor system DILM…, contactor relays, 3 pole contactors up to 170 A AC-3 at 400 V, 4 pole contactors up to 200 A AC-1 • Easier engineering through identical construction -
Full Voltage Contactors and Starters Catalog
Full Voltage Contactors and Starters Catalog 8502CT9701R11/20 Release date: 11/2020 www.se.com Legal Information The Schneider Electric brand and any trademarks of Schneider Electric SE and its subsidiaries referred to in this guide are the property of Schneider Electric SE or its subsidiaries. All other brands may be trademarks of their respective owners. This guide and its content are protected under applicable copyright laws and furnished for informational use only. No part of this guide may be reproduced or transmitted in any form or by any means (electronic, mechanical, photocopying, recording, or otherwise), for any purpose, without the prior written permission of Schneider Electric. Schneider Electric does not grant any right or license for commercial use of the guide or its content, except for a non-exclusive and personal license to consult it on an "as is" basis. Schneider Electric products and equipment should be installed, operated, serviced, and maintained only by qualified personnel. As standards, specifications, and designs change from time to time, information contained in this guide may be subject to change without notice. To the extent permitted by applicable law, no responsibility or liability is assumed by Schneider Electric and its subsidiaries for any errors or omissions in the informational content of this material or consequences arising out of or resulting from the use of the information contained herein. Schneider Electric, Mag-Gard, Modbus, Motor Logic, Spin Top, and TeSys are trademarks and the property of Schneider Electric SE, its subsidiaries, and affiliated companies. All other trademarks are the property of their respective owners.